生产线动作及时间分析
生产线平衡,解决瓶颈工序是关键

第1页共1页
格式为 Word 版,下载可任意编辑
生产线平衡,解决瓶颈工序是关键
生产线平衡是对生产的全部工序进行平均化,调整作业负荷,使各作业时 间尽可能相近。生产线平衡的目的是消除作业间不平衡的效率损失、以及生 产过剩,使企业达到生产效率的最大化。具体来说是: 1、提高作业员及设备工装的工作效率; 2、减少单件产品的工时消耗,降低成本(等同于提高人均产量); 3、减少工序的在制品,真正实现"一个流'; 4、在平衡的生产线基础上实现单元生产,提高生产应变能力,对应市场变 化,实现柔性生产系统; 5、通过平衡生产线可以综合应用到程序分析、动作分析、规划(Layout) 分析、搬运分析、时间分析等全部 IE 手法,提高全员综合素质。 要达到生产线平衡,实现生产效率最大化,首先要做的就是找出生产线瓶颈 工序,对瓶颈问题加以解决。如果不解决生产瓶颈,那么各工位作业时间不 等所造成的时间损失将会成为生产现场的一大工时浪费。 平衡率改善的基本原则是通过调整工序的作业内容来使各工序作业时间接 近或减少这一偏差。实施时可遵循以下方法: 1.首先应考虑对瓶颈工序进行作业改善,作业改善的方法,可参照程序分析 的改善方法及动作分析、工装自动化等 IE 方法与手段; 2.将瓶颈工序的作业内容分担给其它工序; 3.增加各作业员,只要平衡率提高了,人均工序,重新排布生产工序,相对来讲在作业内容较多的情况下容 易拉平衡; 5.分解作业时间较短的工序,把该工序安排到其它工序当中去。生产线平衡 指南主要包括生产线平衡的相关定义、生产线平衡的意义、工艺平衡率的计 算、生产线平衡的改善原则和方法。 我们在对生产线进行分析时,首先要订定生产线的各工程顺序,填入生产流 动平衡表内,测算好各工序实质作业时间,清点各工序作业人数,将每位员 工的工作时间做好记录,找出分配的实质时间最高的工序,按照不平衡损失 =(最高 DM*合计人数)-(各工序时间的合计)的公式计算不平衡损失,最终找 出不平衡点进行改善。 在对生产线进行改善时,我们重点需要改善的是瓶颈工序,无论是将其他工 序多余人手调遣到瓶颈工序,还是雇佣更多人员,还是合并、分解工序,只 要是适合企业实际状况的手段我们都可以采纳。要知道,瓶颈工序制约着整 个生产线的效率,要实现生产线平衡,达到生产效率最大化,就必须突破瓶 颈,否则其他工序的生产效率再高也是枉然。半成品没有任何作用,只有生 产线平衡率提高了,才能提高人均产量,单位产品的成本也随之下降,生产 效率提高,随之而来的是企业利润的提高。
工业工程的七大手法

七大手法之三 — 流程法
15
现场作业改善方法
对象 设备布置
制程改善
着眼点
具体手法手段
适. ✓ 原则11: 工作抬椅高度适当舒适 ✓ 原则12: 尽量以足踏/夹具替代手之工作. ✓ 原则13: 尽可能将二种工具合并.
七大手法之二 —动改法
✓ 原则15: 依手指负荷能力分配工作.
手别 手指別 能力顺序
左手
右手
小无中食食中无小
87531246
✓ 原则16: 手柄接触面尽可能加大 ✓ 原则17: 操作杆应尽可能少变更姿势.
七大手法有哪些?
1.防错法 如何避免做错事情,使工作第一次就做好的,精神能够具 体实现. 2.动改法 改善人体动作的方式,减少疲劳使工作更为舒适、更有 效率,不要蛮干. 3.流程法 研究探讨牵涉到几个不同工作站或地点之流动关系,藉 以发掘出可资改善的地方.
4.五五法 借着质问的技巧来发掘出改善的构想. 5.人机法 研究探讨操作人员与机器工作的过程,藉以发 掘出可资改善的地方. 6.双手法 研究人体双手在工作时的过程,藉以发掘出可 资改善之地方. 7.抽查法 借着抽样观察的方法能很迅速有效地了解问 题的真象.
✓ 5>. 顺序原理: 避免工作之顺序或流程前后倒置,可依编号 顺序排列,可以减少或避免错误的发生.
✓ 6>. 隔离原理: 藉分隔不同区域的方式,来达到保护某些地 区,使不能造成危险或错误的现象发生.隔离原理亦称保护 原理.
✓ 7>. 复制原理: 同一件工作,如需做二次以上,最好采用“复 制”方式来达成,省时又不错误.
✓ 3.三大分类为:
Hale Waihona Puke 大手法之二 — 动改法✓ 1>. 有关于人体动用方面之原则,共包含8项.
工业工程动作分析之mod法

对MOD法的改进建议
01
引入人工智能技术
利用人工智能技术进行自动化评 估和计算,减少人为因素对评估 结果的影响。
02
拓展适用范围
03
持续优化经验公式
研究如何将MOD法应用于更广 泛的工业工程领域,提高其适用 性和普适性。
根据实际应用反馈,不断优化 MOD法的经验公式,提高其精 度和可靠性。
05
案例分析
MOD法经过多年的发展和改进,形成了许多不同的版本和变体,
03
但其核心思想和方法仍然保持一致。
MOD法的基本原则
01
分解原则
将复杂的动作序列分解为简单的操 作单元,便于分析和优化。
优化原则
不断优化操作单元和流程,消除浪 费和瓶颈,提高生产效率。
03
02
标准化原则
通过标准化操作单元和流程,提高 生产效率和产品质量。
分析历史生产数据和市场预测,制定 更为合理的生产计划和目标。
运用MOD法对生产排程进行优化,合 理安排作业顺序和资源配置。
通过实时监控和调整生产计划与排程, 确保生产过程的顺利进行,提高生产 效率和资源利用率。
谢谢观看
预测生产能力
通过MOD法分析生产线的生产能力,预测未来一段时间内的生产 能力和负荷情况,为生产计划和排程提供依据。
04
MOD法的优势与局限性
MOD法的优势
简单易行
MOD法是一种简单易行的 动作分析方法,适用于各 种工业工程领域,便于初 学者快速掌握。
全面性
MOD法能够全面分析作业 过程中涉及的所有动作要 素,包括基本动作、辅助 动作和无效动作。
MOD法通过将每个动作分解为最小的 操作单元,并评估每个操作单元所需 的时间和人力,来识别生产过程中的 瓶颈和浪费。
LE
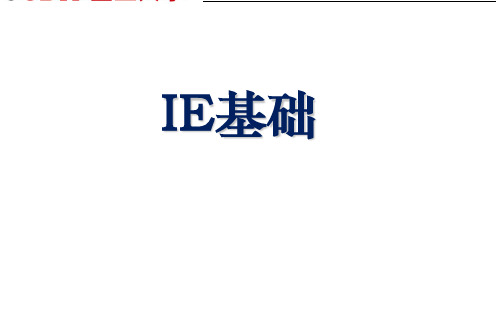
IE基础SBTI中国精益研究中心1.效率2.人工效率3.动作经济原则4.动作分析5.线平衡效率的定义:效率=产出投入人工效率人工效率的定义:人工效率==备注:单件流生产线标准工时=瓶颈工序标准工时×作业员配置数量有效人工工时产出总人工工时投入标准工时×产出良品数量总人工工时投入动作经济原则基本原则I 减少动作II 同步动作III 缩短动作V 轻松动作出发点作业员是否需要寻找,挑选,调整方向,定位的动作作业员是否有等待,持有动作作业员是否有不必要的大动作,能否降低动作范围,强度能否减少限制性动作动作方法的原则1.去掉不必要的动作2.减少眼睛的动作3.考虑两个以上的动作组合1.动作同时开始并同时结束2.让双手同时向相反或相对方向动作1.以最适宜的身体部位进行动作,优先使用手指,再手臂,再身体动作。
2.以最短距离进行动作1.尽量使动作没有限制2.利用重力或其他力量进行动作3.利用惯力或反弹力进行动作4.使动作方向及其变换很顺畅操作场所的原则1.将材料或工具放在作业员身边,距离其使用点最近的位置2.将材料或工具放在易于使用的状态,使之不需要寻找,挑选,定向,定位3.将材料和工具按照使用顺序摆放,包括型号更换作业顺序调整位置,以使双手能同时作业以作业不受妨碍为前提,尽量缩小作业空间将作业位置调整到最合适的高度工装夹具及机器的原则1. 使用合适的容器,使得材料和零部件易于拿取,增强作业员动作重复性2.将两种以上的工具合为一体3.使用安装简单的工装夹具4.用1个动作完成机器操作1.对需长时间持有的物品使用支撑架2.对简单操作及需要力量的操作,使用可以应用脚,腿的器具机构3.研制能够同时使用双手的夹具1.取料,送料使用利用重力的器具2.调整机器的操作位置,以便能以最适宜的身体部位进行操作1.为了限制一定的运动路线而使用夹具或导向2.调整手握部位,使其易握3.使用易见且易安装的夹具4.使机器的移动方向与操作方向一致5.使工具轻便易用类别序号名称文字符号Therblig符号例:拿起桌上的铅笔写字色彩符号符号注释第1类1空手(动)Transport EmptyR交盘的形状伸出的(伸向放铅笔的地方)OliveGreen2抓住GraspG抓住物品的形状握住铅笔Dark Red 3搬运MoveM在盘里放东西的形状把铅笔拿过来Green4松手Release loadRL把盘翻过来的形状放下铅笔GarmineRed5定位于PositionP物品搁在手指尖上的形状把笔类放在特定的位置上Blue6组合AssembleA组合的形状套上铅笔直帽VioletLight7使用UseU杯口朝上放置的形状写字(使用铅笔)Pureple 8分解DisassembleDA从组合物上取下一根的形状摘掉笔帽VioletLight类别序号名称文字符号Therblig符号例:拿起桌上的铅笔写字色彩符号符号注释第2类9寻找SearchSH用眼睛寻找物品的形状找一下铅笔在什么地方Black10选择SelectST指明所选物品的形状从数支铅笔中选出一支合适的Grey Light 11检查InspectI凸透镜的形状查看一下字写得如何BurntOchre12预定位置PrepositionPP立着的保龄球瓶的形状调整握笔的姿势,以便容易书写Sky Blue 13考虑PlauPN手托在脑袋上思考的形状考虑写什么样的字Brown第3类14保持HoldH物品被磁铁吸住的形状一直拿着铅笔GoldOchre 15无可避免的延误UnavoidableUD人被绊倒的形状因停电而无法写字,手闲住等待YellowOchre 16休息RestRE人坐在椅子上的形状累了休息一下Orange 17可避免的延误Avoidable DelayAD人睡着了的形状不写字,眼睛看着别处LemonYellow改善点左手右手改善点作业要素动作要素动作要素/Therbling符号作业要素动作要素动作分析改善重点:1.能否省掉这个动作1.这个动作是否不必要2.可否将两个以上的动作要素合成一个3.右手的动作能否用左手完成?动作范围能否缩小4.作业区的配置能否改变5.通过脚完成的动作能否改变2.能否去掉“空手”?能否更容易?1.动手的动作和后面的抓住动作能否同时进行2.物品如放在近处,能否缩短动作距离3.能否将手的动作从上下动作改为水平动作?3.“抓住”的动作能否更容易一些1.物品的形状能否变得更好抓一些(变小,变大)2.能否改变物品的位置和方向,使物品更好拿3.能否改变放置物品的容器,便于更容易拿取4.能否使用夹具,以便更容易抓取物品动作分析改善重点:4.能否省去“搬运”能否使之更容易完成1.搬运动作能否变为滑行或使用传送带2.能否用夹具自动的送出3.能否使物品存放处离作业区更近一些4.抓住物品的动作,能否调整物品的方向和角度,是物品更容易抓取5.工具能否吊放在作业者的近处6.能否使用夹具使搬运更容易完成5.能否省去“确定位置”?能否使之更容易完成1.能否装上定子或导轨2.能否改变持物的方法3.能否去掉物品的棱角,改变其形状6.能否省去“组装”,“分解”能否使之更容易完成1.能否改变物品的设计和组装方法2.能否使部品更光滑动作分析改善重点:7.能否让“使用”更容易1.工夹具的大小,形状,重量能否改变2.拿工夹具的方法和位置能否改变3.能否将两个以上的工夹具组合到一起8.能否省去“放下”的动作?能否使之更容易完成1.能否经常拿到手里2.能否改变放下的位置3.能否使用夹具,以便更容易放下4.能否在伸手的过程中放下5.能否边用一只手放下加工物品,另一只手拿起另一件部品9.“检查”能否更容易的进行1.能否与样本进行比较2.能否用计测器和测定用具测定3.能否同时查看表里两面4.能否一次检查数件动作分析改善重点:10.能否省掉“找”“找出”“选择”?能否使之更容易完成1.能否预先确定好物品的放置处2.能否将物品的放置标准化,使选择变得没必要3.能否在不作业区放置不必要的物品4.能否改变物品的颜色及形状5.物品没有按照作业的顺序放置吗11.能否省去“准备”1.放置物品时能否考虑避免准备动作2.吊挂工具时能否考虑避免准备动作3.能否制作合适的工具箱,以便使后面的动作更容易进行12.能否省去“保持”能否使之更容易进行1.能否不使用保持用的夹具2.能否改变保持物的位置,方向,形状,重量3.能否改变保持动作的方向及方法动作分析改善重点:13.“不可避免的延迟”能否消除1.能否用双手进行作业2.能否担任其他工作14.“可避免的延迟”能否消除1.延误的原因是否已经弄清2.有无消除的方法线平衡率公式:线平衡率=备注:生产线为单件流生产线,用上面公式。
工厂Layout局部优化四种操作方法

工厂Layout局部优化四种操作方法如果是局部的LAYOUT改善, 你要考虑的是设备的布局还是装配线的布局,这两者有一些区别的, 做物料供给的话,首先要区分你做的是内物流还是外物流,更多的从VSM角度来改善。
01.方法一1、P-Q分析,确定生产的品种与规格;2、产品族分析;3、工艺分析,确定生产顺序;4、规划生产线的作业品种和确定节拍;5、预计各工序的工时;6、重新设定作业区域和位置(更多的以场地面积来考虑);7、设定节拍管理;8、设定“安咚" ;9、做产线员工作业熟练度测试,再次评测工时;10、线平衡,作业组合;11、设定标准库存;12、然后就要做TWI的JI了。
做局部的物料供给: 基本为一个小型的拉动系统。
1、对WIP做调查,了解现场的配套情况;2、现场物料的尺寸、包装、器具做调查;3、对物料进行ABC分析;4、对投料频度及时间的明确化和维持管理(这时候往往要重新设定物料的标准,包罗路径,时间,容器,有条件的话可以用看板卡等) ;5、工位器具的改进;6、设定空器具、空托盘的返还流程。
(如果有看板卡的话,别忘记了看板卡) 。
02.方法二第一步:了解产品、产品工艺流程图、车间平面布置图;第二步:绘制生产系统图;第三步:工艺改善、设备改善,条件成熟构建生产线(单元流或一个流方式);第三步:构建以车间为单位的店铺、容器、物流车、物流通道;第四步:根据改善绘制改善后的车间布局图、车间搬运方式及路径图;第五步:绘制改善后的生产系统图。
03.方法三在施耐德电气使用一种叫LADM(Line Architecture Design Methodology)的方法,非常系统,大致的思路为:1、明确客户的需求和内部企业的目标,确定生产线的产能规划,计算T akt Time。
2、明确约束条件(质量的、空间的、设备的等),通过系统的方法研究工艺流程和操作,并以Tmu为时间单位进行动作分析。
3、以Takt Time作为生产和物流的契约,研究物流和信息流。
生产线快速切换的七大技巧(一)

生产线快速切换的七大技巧(一)
技巧一:并行操作
所谓的平行作业就是指两个人以上共同从事切换动作。
平行作业最容易马上获得缩短内作业时间的效果。
由一个人慢条斯理地从事切换动作,也许需耗1小时才能完成。
若能由两人共同作业,也许会在40分钟或20分钟就能完成。
那么整个切换时间就由原先的1小时减为20分钟至40分钟之间。
而在平行作业中所需的人工时间或许会增多、不变、减少,都不是所要考虑的重点。
因为,缩短了切换的时间所获得的其他效果远大于人工成本的部分,此点是一般人较容易忽视的。
在从事平行作业时,两人之间的配合动作必须演练熟练,尤需注意安全,不可因为疏忽而造成意外伤害。
生产线平衡分析与改善答案
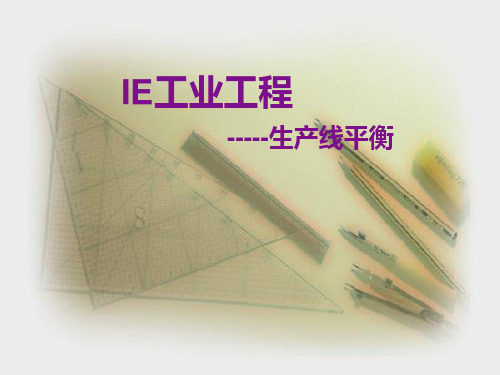
2020/3/2
14
三、流水生产线平衡的设计方法
3、 单品种流水线平衡方法 ● 案例:生产线平衡分析案例
2020/3/2
15
三、流水生产线平衡的设计方法
3、 单品种流水线平衡方法
● 案例:生产线平衡分析案例
由表一可知A、B、C、D四个工序每小时产量处于不平衡的状态, 整体生产线的产量受限于C工序,每小时只能产出209.09个,其 他的工序的产出高于209.09个,只会堆积在生产线上而造成半成 品库存积压,而D工序更将因为C工序的产量,而形成时间的等 候。
若对C工序进行动作分析研究,将部分工作分配给闲置的B、D两工序, 则将有助于一产平衡率由64.17%提高至96.25%。产能比30分钟生产一 个成品,提高到20分钟生产一个成品,产能提高50% .
2020/3/2
24
三、流水生产线平衡的设计方法
③生产线平衡率的计算:
若评估上述两方案,对瓶颈工序C进行动作分析的生产线平 衡改善方案较增加作业资源的生产线平衡改善方案的效果为 佳(无须增加一个工位)
2、 流水线平衡设计的准备工作
● 进行产品和零件的分类 ● 改进产品和零件的结构,使之适合流水生产 ● 审查和修改工艺规程 ● 收集整理设计工作所需要的资料
2020/3/2
11
三、流水生产线平衡的设计方法
3、 单品种流水线平衡方法 ① 确定流水生产的节拍 当流水线的运输批量等于1的情况下,节拍按下式计算:
IE工业工程
-----生产线平衡
课 程 内容
生产线平衡 一、生产线平衡的概述 二、流水生产线概述 三、生产线平衡的设计 四、生产线平衡的方法及改善原则 5、案例分析
2020/3/2
2
基础工业工程动作分析

第 六 章 动 作 分 析
锡钎焊作业动素分析表
左手
动素
右手
分析要点
伸到工件处
抓起工件 成品堆放处
放开 等待 等待 移动 对准电路板 作业 放回焊丝 等待 等待
1
2 3 4 5 6 7 8 U 9U 10 11 12
伸到工件处
抓起工件 移动工件到锡钎焊处
放开 伸手到处
握取 移动电烙铁 对准电路板(定位) 锡焊丝作业(使用) 锡焊丝作业(使用) 移动电烙铁 放开电烙铁
1.3 动作分析的目的
第
六
➢(1)了解操作者身体各部分的动作顺序和方
章
法。
➢(2)了解以两手为中心的人体各部位是否能
动
尽可能同时动作,是否相互联系。
作
➢(3)明确各种动作的目的,动作过程中的必
分
要动作和不必要动作
析
➢ (4)了解在必要的作业动作中两手的平衡。
1.4 动作分析的用途
第
六
➢ (1)为减轻作业疲劳、提高工作效率而找出动作存在的
法.
➢ (7)提高能细微分析动作和判断动作好坏的动作意识。
2.1 观察作业动作的方法
第
六
目视动作观察法
章
➢动素分析法
动
作
影像动作观察法
分
析
➢慢速摄影分析
➢常速影像分析
2.2 动作分析的方法
第
六
方法
目的
分析对象
优点
缺点
章
能用最小
的单位分
动 作 分 析
目 视 动 作 观 察 法
人体各部分 在固定的作业 析动作,
等待
1.2 动作分析的定义
- 1、下载文档前请自行甄别文档内容的完整性,平台不提供额外的编辑、内容补充、找答案等附加服务。
- 2、"仅部分预览"的文档,不可在线预览部分如存在完整性等问题,可反馈申请退款(可完整预览的文档不适用该条件!)。
- 3、如文档侵犯您的权益,请联系客服反馈,我们会尽快为您处理(人工客服工作时间:9:00-18:30)。
六、程序研究建立之要点
A.五大步骤:如何改进工作程序,整个工作能够取消
(1) 选择:选择凡能很快而容易获得下列各种情形者
◇ 使工作更为安全 ◇使工作更为容易
◇ 减少现有之动作 ◇取消各种困难
选择工作最需要改善者先予改善,避免发生不安不快
(2)记录:不要听见臆测与传闻,要亲自实地观察每一动作
◇ 取得工作人员之合作 ◇注视工作如何进行的
何时做?
为何在那时候做?
有无其他更好之时间?
谁做?
为什么那个人做?
有无其他更好之人员?
如何做?
为何要那样做?
有无其他更好之方法?
(4)建立:如能注意动作,就可以节省时间
◇ 复阅各种已得意见,记下各种可能改善趋向
◇ 剔除不必要之动作
◇ 合并动作节省搬运
◇ 调整布置节省搬运
◇ 改变次序,避免复杂与重复
(二)工作位置之安排 1.工具物料之放置应各有固定处所,养成良好习惯 2.工具物料应放置于规定位置,以将物料尽量送至靠近工人 4.工具、物料及控制器位于最大工作区域范围内,且应尽量靠 近工人工作场所 5.物料及工具应依最佳之动作次序排列 6.应尽量使用“自动落下”或“弹出”装置,使操作人不必用 手处理完成工作 7.应有适当之照明设备,坐椅之形式及高度应符合规定,使工 作者保持良好之姿态,工作处所及座位之高度亦应适量,务 使坐力均宜。 8.工作处所之颜色应与工作物之颜色衬托,以减少眼睛疲劳。 9.尽量避免以手握持工作物,应以夹具或足踏器具代替之。 10.可能时,应将两件或两件以上之工具合拼在一起。 11.当每一手指均有其特定工作时(如打字),应依其本能分担 工作。 12.曲柄及大起子之握柄,与手之接触面愈大愈佳,尤以使用大 力之手柄最为需要。 13.机器上杠杆、十字杆及手轮之位置,应能使工作者极少变动 其姿态,且能利用机械之最大能力。
◇ 联系各有关人员与您共同研究改进
◇ 通知并说服各有关人员使他们一致乐于参与工作,并愿接
受改变
◇ 训练各使用人员熟悉新方法
◇ 注意对各有关人员之利益
B.工作改善程序与应革除之观念 工作简化之五大步骤 ◇ 选择拟改进的工作 ◇ 记录工作之内容 ◇ 分析工作内容 ◇ 研拟改进方案 ◇ 拟立改进之工作方法 ◇ 付诸实施
生产线动作及时间分析
A.动作分析程序图:列出后分析距离时间分析 操作○ 运送 待料 D 检验 库存
B.经济动作原则: (一)人体之利用: 1.两手应同时开始及完成动作 2.除了休息时间外,两手不应同时动作 3.两臂之动作应对称,方向相反,且同时动作 4.手和身体之动作等级以尽量用最低级而能使工作满意为宜 5.应利用动量助月,但当需使用肌肉之力制止时,则应将运动 量减至最低限度。 6.连续之曲线运动较含有方向突变动甚巨艮进直线运动为佳。 7.“弹道”(即自由摆动)动作较有限制或受控制之运动迅速, 容易及准确。 8.动作应尽可能轻松、自然、保持节奏,尤其重复动作更不可 缺少韵律。 9.工作应作妥善安排,使眼睛之动作局限一悦目之范围。
C.革除不良之十大观念 ◇ 要消除错误的话,要注意就行 ◇ 因为工作忙,所以发生稍微错误是难免 ◇ 发生不良品也会在检查时检查出,故稍发生不良好没关系 ◇ 因为产品之零件品种繁多,所以混入好是不得已 ◇ 作业有变异是由于经验之差异,故是无可奈何之事 ◇ 虽有作业指导书,但只要用自己容易做之方法就行 ◇ 这种方法与程序之变更不必向上级报告 ◇ 作业虽有困难之点,但也不必提案 ◇ 虽然有标准样品,但已经很熟悉,所以不必去看
◇ 简化剩余之动作
◇ 使新方法安全,作新方法之程序图
何事
剔除 剔除不必要动作是改善最高之原则
何地何时何人 合并 合并必要之动作节省办事手续
排列 排列必要之动作工作成线办事有序
如何
简化 简化必要之动作节省人力时间设备
(5)实施:能为他人设想,要消除对改变之猜疑与恐惧
◇ 附建议书
◇ 选择最适当之时机提出建议
虽有日常检查单,
◇ 图解现行方法
◇注意记下技巧及困难之地方
试找出:a、现在做的是什么 b、在何处做
c、在何时做
d、谁做
e、如何做
(3)分析:找出真实——不是判断!不是托词
◇ 首先质疑 ◇必要时,再质疑其他工作,记下所有之意见
完成了什么? 是否必要?为什么? 有无其他更好之成就?
何处做?
为何在那里做?
有无其他更好之地方?