汽轮机隔板裂纹的分析及焊修复
汽轮机隔板裂纹的分析及焊修复

汽轮机隔板裂纹的分析及焊修复汽轮机隔板裂纹的分析及焊修复1裂纹产生原因分析1.1铸钢浇注性能不好汽轮机隔板材料ZG20CrMo中Cr元素的质量分数较大,在浇注时,其液态金属的流动性不好,充满铸型的能力较差。
此外,铸钢件单件的体积大、重量大,影响铸钢件在浇注时的成型能力。
因此ZG20CrMo铸钢件本身就存在较多的铸造缺陷,如气孔、砂眼、疏松、缩孔,在运行中,这些缺陷随时会发展成裂纹。
1.2结构复杂汽轮机隔板结构复杂,造成局部刚性小,结构的刚性不均匀,在工艺加工时,必然出现应力分布不均匀,形成严重的应力集中现象。
由于铸钢件的结构特点,在浇注时极易产生不同类型的铸造缺陷,如气孔、砂眼、疏松、缩孔,这些缺陷在运行中还会扩展成裂纹。
铸钢件的结构刚性大,焊接后的残余应力水平高。
这类材料的焊接性又不好,在补焊过程中,工艺不合理,极易产生裂纹,促使铸钢件原有的铸造缺陷诱发成裂纹。
由于结构形状的复杂,焊后残余应力分布不均匀,造成局部地方变形不均匀,扩大了整体的变形量,而隔板是配合件,具有严格的形状和尺寸要求,这给补焊带来很大的困难。
2铸钢裂纹补焊方案的选择珠光体铸钢件的常规补焊工艺有两种:采用奥氏体耐热钢焊条的冷补焊方案和采用珠光体钢焊条的热补焊方案。
2.1奥氏体耐热不锈钢焊条冷补焊2.1.1冷补焊工艺的优点冷补焊的焊缝金属是奥氏体组织,焊接过程中不发生相变,且焊缝的塑性和韧性较好,因此可不预热,也不需焊后热处理,简化了补焊工艺,避免铸钢件受到过大的热作用,从而减小被焊件的应力和变形;奥氏体组织对氢有较大的溶解度,可避免焊缝产生氢致裂纹,减少珠光体组织的近缝区产生氢致裂纹的可能;奥氏体组织的缺口敏感性比珠光体组织低,即使焊缝内部有裂纹也不易扩展;奥氏体组织焊缝金属的屈强比小于珠光体组织的,因而在应力作用下,必然产生塑性变形,从而使应力得到松弛,避免了结构的破坏。
2.1.2冷补焊存在的缺点a) 补焊近缝区的淬硬问题冷补焊时近缝区的冷却速度较大,最高可达120 ℃/s,在补焊的近缝区不可避免地产生淬硬组织。
某汽轮机铸铁隔板螺栓孔开裂修复案例研究
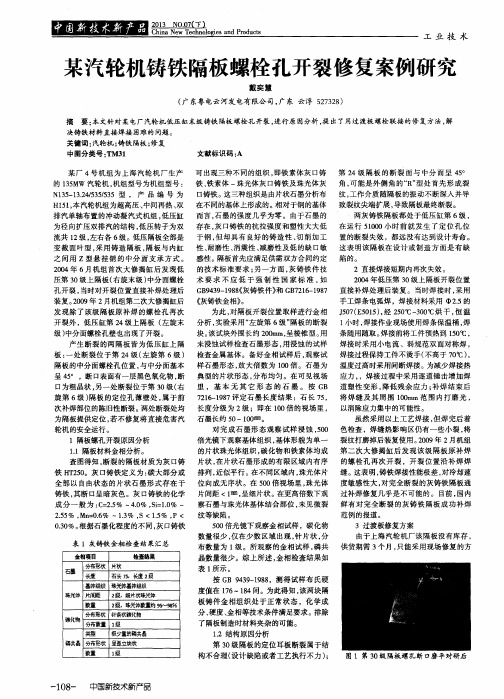
流共 1 2级 , 左 右各 6 级。 低压 隔 板全 部是 于钢 , 但却具有 良好 的铸造性 、 切削加工 置 的断 裂失 效 ,都 远 没有 达 到设 计 寿 命 。 变截面叶型 , 采用铸造隔板 , 隔板 与 内缸 性 、 耐磨 性 、 消 震性 、 减 磨 性 及低 的缺 口敏 这 表 明该 隔板 在 设 计 或 制 造 方 面 是 有 缺 之 间 用 z型悬 挂 销 的 中分 面 支 承 方式 。 感性 。 隔板首先应满足供需双方合同约定 陷 的 。 2 0 0 4年 6月 机组 首 次 大 修 揭 缸 后 发 现低 的技术标准要求 ; 另一方面 , 灰铸铁件技 压第 3 0 级 上 隔板 ( 右旋 末级 ) 中分 面 螺栓 术 要 求 不 应 低 于 强 制 性 国 家 标 准 , 如 2 直接 焊接 短期 内再 次失 效 。 2 0 0 4 年低 压 第 3 0 级 上 隔板 开裂 位 置
2 Q Q : Q 2 ( 王) C h i n a N e w T e c h n o l o g i e s a n d P r o d u c t s
工 业 技 术
某汽轮机铸铁隔板螺栓 孔开裂修复案例研究
戴 奕 慧
( 广 东粤 电云 河发 电有限公 司, 广东 云浮 5 2 7 3 2 8 )
文献 标识 码 : A
某 厂 4号机 组 为 上海 汽轮 机 厂 生产 可出现三种不同的组织 , 即铁素体灰 口铸 第 2 4级 隔 板 的断 裂 面 与 中分 面 呈 4 5 。
铁 索体 一珠 光体 灰 口铸 铁 及珠 光 体 灰 角 , 可能 是 外 侧 角 的 “ R ” 型 处 首 先 形 成 裂 的1 3 5 M W 汽 轮机 , 机 组 型号 为机 组 型号 : 铁、 口铸铁 。 这 三种组 织是 由片状石 墨 分析 布 纹 , 工 作介 质 随 隔板 的振 动不 断深 入 并 导 相 对 于钢 的基 体 致 裂纹 尖端 扩 展 , 导 致隔 板最 终 断裂 。 H1 5 1 , 本 汽 轮机 组 为超 高压 、 中间再 热 、 双 在 不 同的基 体 上形 成 的。 排汽单轴布置的冲动凝汽式机组 , 低压缸 而 言 , 石 墨 的强 度 几乎 为 零 。 由于 石 墨 的 两灰铸铁隔板都处于低压缸第 6级 , 为 径 向扩压 双 排 汽 的结 构 , 低压 转 子 为双 存在 , 灰 口铸 铁 的抗 拉 强 度 和塑 性 大大 低 在 运 行 5 1 0 0 0小 时前 就发 生 了 定 位 孔 位
600MW机组汽轮机隔板裂纹的原因分析及处理措施
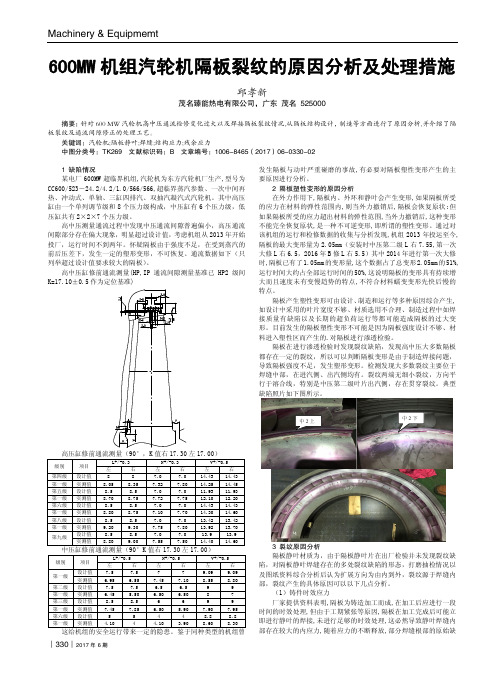
中2上
中2下
高压缸修前通流测量(90°,K 值右 17.30 左 17.00)
级别
项目
L+/-0.3
左
右
N+/-0.3
左Hale Waihona Puke 右V+/-0.5
左
右
第四级 设计值
8
8
7.0
7.0
14.43 14.43
第一级 实测值 8.05
8.35
7.32
7.80
14.25
14.45
第五级 设计值
8.5
8.5
7.0
7.0
11.93 11.93
第一级 实测值 4.10
4
4.10
3.90
8.60
8.30
这给机组的安全运行带来一定的隐患。鉴于同种类型的机组曾
︱330︱2017 年 6 期
3 裂纹原因分析 隔板静叶材质为,由于隔板静叶片在出厂检验并未发现裂纹缺 陷,对隔板静叶焊缝存在的多处裂纹缺陷的形态,打磨抽检情况以 及图纸资料综合分析后认为扩展方向为由内到外,裂纹源于焊缝内 部,裂纹产生的具体原因可以以下几点分析。 (1)铸件时效应力 厂家提供资料表明,隔板为铸造加工而成,在加工后应进行一段 时间的时效处理,但由于工期紧张等原因,隔板在加工完成后可能立 即进行静叶的焊接,未进行足够的时效处理,这必然导致静叶焊缝内 部存在较大的内应力,随着应力的不断释放,部分焊缝根部的原始缺
发生隔板与动叶严重碰磨的事故,有必要对隔板塑性变形产生的主 要原因进行分析。
2 隔板塑性变形的原因分析 在外力作用下,隔板内、外环和静叶会产生变形,如果隔板所受 的应力在材料的弹性范围内,则当外力撤销后,隔板会恢复原状;但 如果隔板所受的应力超出材料的弹性范围,当外力撤销后,这种变形 不能完全恢复原状,是一种不可逆变形,即所谓的塑性变形。通过对 该机组的运行和检修数据的收集与分析发现,机组 2013 年投运至今, 隔板的最大变形量为 2.05mm(安装时中压第二级 L 右 7.55,第一次 大修 L 右 6.5,2016 年 B 修 L 右 5.5)其中 2014 年进行第一次大修 时,隔板已有了 1.05mm 的变形量,这个数据占了总变形 2.05mm 的 51%, 运行时间大约占全部运行时间的 50%,这说明隔板的变形具有持续增 大而且速度未有变慢趋势的特点,不符合材料蠕变变形先快后慢的 特点。 隔板产生塑性变形可由设计、制造和运行等多种原因综合产生, 如设计中采用的叶片宽度不够、材质选用不合理、制造过程中如焊 接质量有缺陷以及长期的超负荷运行等都可能造成隔板的过大变 形。目前发生的隔板塑性变形不可能是因为隔板强度设计不够、材 料进入塑性区而产生的.对隔板进行渗透检验。 隔板在进行渗透检验时发现裂纹缺陷,发现高中压大多数隔板 都存在一定的裂纹,所以可以判断隔板变形是由于制造焊接问题, 导致隔板强度不足,发生塑形变形。检测发现大多数裂纹主要位于 焊缝中部,在进汽侧、出汽侧均有。裂纹两端无细小裂纹,方向平 行于溶合线,特别是中压第二级叶片出汽侧,存在贯穿裂纹。典型 缺陷照片如下图所示。
330MW机组汽轮机高压外缸内壁裂纹焊接修复工艺word精品文档6页
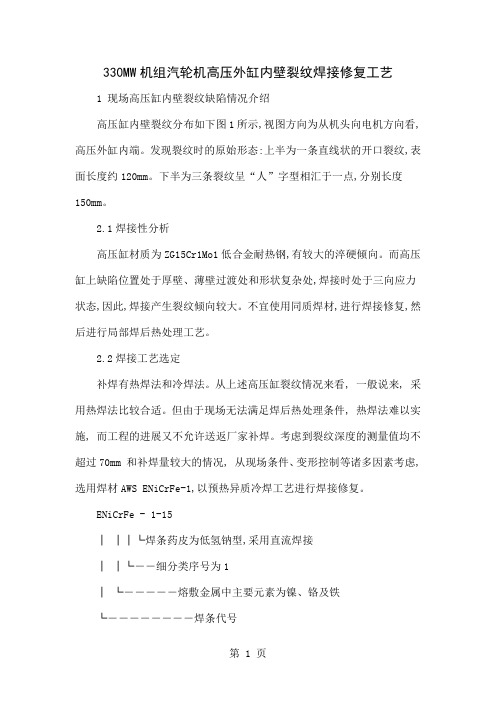
330MW机组汽轮机高压外缸内壁裂纹焊接修复工艺1 现场高压缸内壁裂纹缺陷情况介绍高压缸内壁裂纹分布如下图1所示,视图方向为从机头向电机方向看,高压外缸内端。
发现裂纹时的原始形态:上半为一条直线状的开口裂纹,表面长度约120mm。
下半为三条裂纹呈“人”字型相汇于一点,分别长度150mm。
2.1焊接性分析高压缸材质为ZG15Cr1Mo1低合金耐热钢,有较大的淬硬倾向。
而高压缸上缺陷位置处于厚壁、薄壁过渡处和形状复杂处,焊接时处于三向应力状态,因此,焊接产生裂纹倾向较大。
不宜使用同质焊材,进行焊接修复,然后进行局部焊后热处理工艺。
2.2焊接工艺选定补焊有热焊法和冷焊法。
从上述高压缸裂纹情况来看, 一般说来, 采用热焊法比较合适。
但由于现场无法满足焊后热处理条件, 热焊法难以实施, 而工程的进展又不允许送返厂家补焊。
考虑到裂纹深度的测量值均不超过70mm 和补焊量较大的情况, 从现场条件、变形控制等诸多因素考虑,选用焊材AWS ENiCrFe-1,以预热异质冷焊工艺进行焊接修复。
ENiCrFe - 1-15│ ││└焊条药皮为低氢钠型,采用直流焊接│ │└――细分类序号为1│ └―――――熔敷金属中主要元素为镍、铬及铁└――――――――焊条代号AWS ENiCrFe-1的抗拉强度617 MPa,延伸率42%,冲击值89J(-196℃),适合于Inconel对接,或Inconel和低合金钢、不锈钢等异材焊接。
其焊缝组织为奥氏体组织,它在焊接热循环过程中不发生相变,不要求预热(或低温预热)和焊后热处理,简化了施工工艺,减小热作用范围及工件的变形量、残余应力。
同时奥氏体组织塑性高,对氢的溶解度较大,从而有很好的抗裂性能。
焊材线膨胀系数同母材线膨胀系数接近,工作状态因材质不同而产生的附加应力较小;Ni含量高,奥氏体组织稳定性好,可防止碳的扩散,减少融合区碳迁移的不利因素。
同时AWS ENiCrFe-1焊缝金属使用温度范围广,可在-196~980℃范围内使用,完全满足高压缸工作要求温度范围。
500MW汽轮机低压缸隔板裂纹原因分析及处理
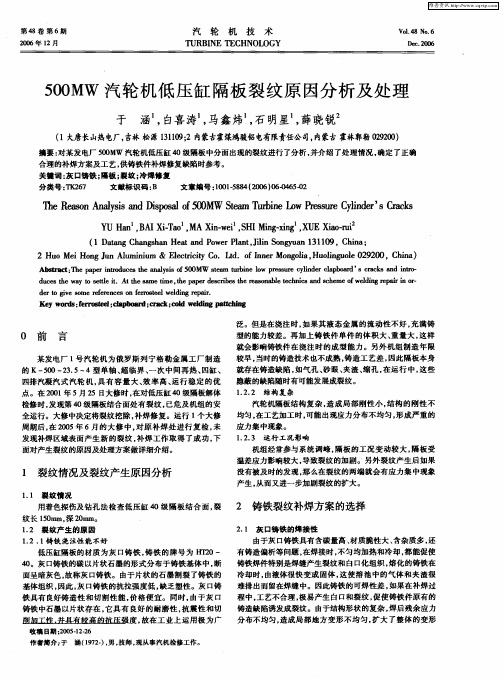
汽轮机隔板结 构复杂 , 造成 局部 刚性小 , 结构 的 刚性 不 均匀 , 在工艺加工时 , 可能 出现应力分 布不均匀 , 形成严重 的 应力集 中现象 。
12 3 运 行 工 况 影 响 ..
机组 经常参与系统 调峰 , 隔板 的工况 变动较 大 , 隔板受 温差 应力影 响较大 , 导致裂纹的加剧 。另外 裂纹产生后如果 没有被及 时的发现 , 那么在裂纹的两端就会 有应 力集 中现象
泛 。但是在浇注时 , 如果 其液态 金属 的流动性 不好 , 充满 铸
0 前
言
某发 电厂 1 号汽 轮机 为俄 罗斯 列宁格 勒金 属工厂 制造 的 K一 0 2 . 50— 3 5—4型单轴 、 临界 、 超 一次 中间再 热 、 四缸 、
四排汽凝汽 式汽 轮机 , 有 容量 大 、 具 效率 高 、 行稳 定 的优 运
于 涵 白喜涛 马鑫炜 石 明星 薛晓锐 , , , ,
( 1大唐长山热电厂, 松源 110 ; 吉林 3192内蒙古霍煤鸿骏铝电有限责任公司, 内蒙古 霍林郭勒 090 ) 220
摘要 : 对某发 电厂 5 0 W 汽轮机低压缸 4 0M 0级隔板 中分面出现的裂纹进行 了分析 , 并介绍 了处理情况 , 确定 了正确 合理的补焊方案及工艺 , 供铸铁件补焊修 复缺 陷时参考 。
维普资讯
第 4 卷 第 6期 8
20 0 6年 l 2月
汽
轮
机
技
术
Vo.8 N 6 14 o.
De . O 6 c2 0
兀பைடு நூலகம் BI EC R NE I HN O OL GY
50 0 MW 汽 轮 机低 压缸 隔板 裂 纹 原 因分 析 及处 理
N40—42型汽轮机汽封座裂纹焊接修复技术应用

N40—42型汽轮机汽封座裂纹焊接修复技术应用摘要:本文针对N40-42型汽轮机上、下缸汽封座在运行中产生裂纹的原因进行分析;对母材的可焊性、焊接方法及材料的选择、焊接变形与残余应力控制进行分析;对在现场进行的焊接工艺进行了详细叙述,此工艺对现场修复大型珠光体耐热钢具有修复效率高,成本低,焊工劳动条件好,对减少汽轮机上、下缸汽封座的应力和变形具有较高的实用价值。
关键词:焊条电弧焊冷焊法;裂纹;锤击前言我厂#1汽轮机工作压力为4.2Mpa,蒸汽温度为460℃,机组在运行中发出金属磨擦声和震动,停机检查发现汽轮机上、下缸汽封座有27处深浅不一,长短不等的纵向裂纹,最长的裂纹约300mm、深36mm。
为尽快恢复机组运行,采用现场挖补处理。
1.裂纹产生原因我们针对汽封座产生裂纹原因进行综合分析:一是汽轮机在运行过程中汽转子发生前窜与汽封座产生摩擦温度剧升,致使汽封局部半溶化状态,造成汽封座局部材料强度降低产生裂纹;二是汽封座表面受到汽室温度与摩擦形成温差,使局部产生较大应力,同时受汽转子前后窜动撞击,形成裂纹。
2.可焊性分析2.1母材的分析2.1.1母材的可焊性差汽封座材质为ZG20GrMo,属珠光体耐热钢,运行温度460℃,工作压力为4.2Mpa。
碳当量在0.41~0.66﹪之间,厚度为800mm,拘束度大。
因而,补焊区不仅需要足够的强度,还要一定的高温性能和疲劳强度。
2.1.2焊接变形因汽封座和汽缸是一个整体,焊后变形最大挠度不得超过0.5mm,径向和轴向的线变形不超过1.0mm。
因而,如何降低焊后残余应力,防止焊缝产生淬硬组织,是必须解决的问题。
2.1.3焊缝综合性能机组需经常停机、启动或瞬间增减负荷,补焊区不仅处于高温条件下工作,而且处在交变热应力作用下工作。
因此,要求焊缝必须具有一定的抗热疲劳性能和高温稳定等性能。
2.2焊接方法选择汽封座补焊的困难是如何防止产生裂纹、夹渣、未熔合和应力变形等缺陷,选择正确的焊接方法尤为重要。
汽轮机旋转隔板裂纹缺陷处理
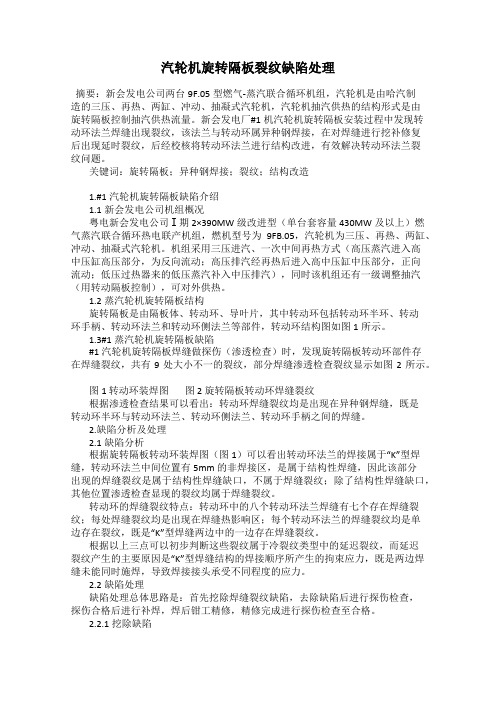
汽轮机旋转隔板裂纹缺陷处理摘要:新会发电公司两台9F.05型燃气-蒸汽联合循环机组,汽轮机是由哈汽制造的三压、再热、两缸、冲动、抽凝式汽轮机,汽轮机抽汽供热的结构形式是由旋转隔板控制抽汽供热流量。
新会发电厂#1机汽轮机旋转隔板安装过程中发现转动环法兰焊缝出现裂纹,该法兰与转动环属异种钢焊接,在对焊缝进行挖补修复后出现延时裂纹,后经校核将转动环法兰进行结构改进,有效解决转动环法兰裂纹问题。
关键词:旋转隔板;异种钢焊接;裂纹;结构改造1.#1汽轮机旋转隔板缺陷介绍1.1新会发电公司机组概况粤电新会发电公司Ⅰ期2×390MW级改进型(单台套容量430MW及以上)燃气蒸汽联合循环热电联产机组,燃机型号为9FB.05,汽轮机为三压、再热、两缸、冲动、抽凝式汽轮机。
机组采用三压进汽、一次中间再热方式(高压蒸汽进入高中压缸高压部分,为反向流动;高压排汽经再热后进入高中压缸中压部分,正向流动;低压过热器来的低压蒸汽补入中压排汽),同时该机组还有一级调整抽汽(用转动隔板控制),可对外供热。
1.2蒸汽轮机旋转隔板结构旋转隔板是由隔板体、转动环、导叶片,其中转动环包括转动环半环、转动环手柄、转动环法兰和转动环侧法兰等部件,转动环结构图如图1所示。
1.3#1蒸汽轮机旋转隔板缺陷#1汽轮机旋转隔板焊缝做探伤(渗透检查)时,发现旋转隔板转动环部件存在焊缝裂纹,共有9处大小不一的裂纹,部分焊缝渗透检查裂纹显示如图2所示。
图1 转动环装焊图图2 旋转隔板转动环焊缝裂纹根据渗透检查结果可以看出:转动环焊缝裂纹均是出现在异种钢焊缝,既是转动环半环与转动环法兰、转动环侧法兰、转动环手柄之间的焊缝。
2.缺陷分析及处理2.1缺陷分析根据旋转隔板转动环装焊图(图1)可以看出转动环法兰的焊接属于“K”型焊缝,转动环法兰中间位置有5mm的非焊接区,是属于结构性焊缝,因此该部分出现的焊缝裂纹是属于结构性焊缝缺口,不属于焊缝裂纹;除了结构性焊缝缺口,其他位置渗透检查显现的裂纹均属于焊缝裂纹。
浅析汽轮机高压缸盖裂纹产生的原因及焊接修复工艺
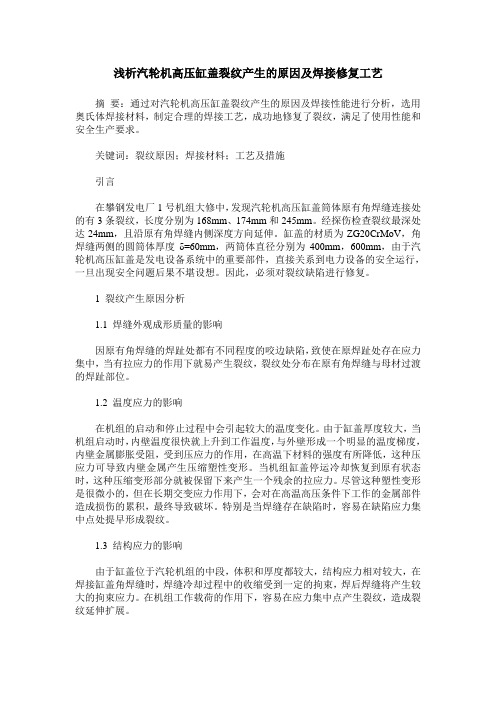
浅析汽轮机高压缸盖裂纹产生的原因及焊接修复工艺摘要:通过对汽轮机高压缸盖裂纹产生的原因及焊接性能进行分析,选用奥氏体焊接材料,制定合理的焊接工艺,成功地修复了裂纹,满足了使用性能和安全生产要求。
关键词:裂纹原因;焊接材料;工艺及措施引言在攀钢发电厂1号机组大修中,发现汽轮机高压缸盖筒体原有角焊缝连接处的有3条裂纹,长度分别为168mm、174mm和245mm。
经探伤检查裂纹最深处达24mm,且沿原有角焊缝内侧深度方向延伸。
缸盖的材质为ZG20CrMoV,角焊缝两侧的圆筒体厚度δ=60mm,两筒体直径分别为400mm,600mm,由于汽轮机高压缸盖是发电设备系统中的重要部件,直接关系到电力设备的安全运行,一旦出现安全问题后果不堪设想。
因此,必须对裂纹缺陷进行修复。
1 裂纹产生原因分析1.1 焊缝外观成形质量的影响因原有角焊缝的焊趾处都有不同程度的咬边缺陷,致使在原焊趾处存在应力集中,当有拉应力的作用下就易产生裂纹,裂纹处分布在原有角焊缝与母材过渡的焊趾部位。
1.2 温度应力的影响在机组的启动和停止过程中会引起较大的温度变化。
由于缸盖厚度较大,当机组启动时,内壁温度很快就上升到工作温度,与外壁形成一个明显的温度梯度,内壁金属膨胀受阻,受到压应力的作用,在高温下材料的强度有所降低,这种压应力可导致内壁金属产生压缩塑性变形。
当机组缸盖停运冷却恢复到原有状态时,这种压缩变形部分就被保留下来产生一个残余的拉应力。
尽管这种塑性变形是很微小的,但在长期交变应力作用下,会对在高温高压条件下工作的金属部件造成损伤的累积,最终导致破坏。
特别是当焊缝存在缺陷时,容易在缺陷应力集中点处提早形成裂纹。
1.3 结构应力的影响由于缸盖位于汽轮机组的中段,体积和厚度都较大,结构应力相对较大,在焊接缸盖角焊缝时,焊缝冷却过程中的收缩受到一定的拘束,焊后焊缝将产生较大的拘束应力。
在机组工作载荷的作用下,容易在应力集中点产生裂纹,造成裂纹延伸扩展。
- 1、下载文档前请自行甄别文档内容的完整性,平台不提供额外的编辑、内容补充、找答案等附加服务。
- 2、"仅部分预览"的文档,不可在线预览部分如存在完整性等问题,可反馈申请退款(可完整预览的文档不适用该条件!)。
- 3、如文档侵犯您的权益,请联系客服反馈,我们会尽快为您处理(人工客服工作时间:9:00-18:30)。
汽轮机隔板裂纹的分析及焊修复
1裂纹产生原因分析
1.1铸钢浇注性能不好
汽轮机隔板材料ZG20CrMo中Cr元素的质量分数较大,在浇注时,其液态金属的流动性不好,充满铸型的能力较差。
此外,铸钢件单件的体积大、重量大,影响铸钢件在浇注时的成型能力。
因此ZG20CrMo铸钢件本身就存在较多的铸造缺陷,如气孔、砂眼、疏松、缩孔,在运行中,这些缺陷随时会发展成裂纹。
1.2结构复杂
汽轮机隔板结构复杂,造成局部刚性小,结构的刚性不均匀,在工艺加工时,必然出现应力分布不均匀,形成严重的应力集中现象。
由于铸钢件的结构特点,在浇注时极易产生不同类型的铸造缺陷,如气孔、砂眼、疏松、缩孔,这些缺陷在运行中还会扩展成裂纹。
铸钢件的结构刚性大,焊接后的残余应力水平高。
这类材料的焊接性又不好,在补焊过程中,工艺不合理,极易产生裂纹,促使铸钢件原有的铸造缺陷诱发成裂纹。
由于结构形状的复杂,焊后残余应力分布不均匀,造成局部地方变形不均匀,扩大了整体的变形量,而隔板是配合件,具有严格的形状和尺寸要求,这给补焊带来很大的困难。
2铸钢裂纹补焊方案的选择
珠光体铸钢件的常规补焊工艺有两种:采用奥氏体耐热钢焊条的冷补焊方案和采用珠光体钢焊条的热补焊方案。
2.1奥氏体耐热不锈钢焊条冷补焊
2.1.1冷补焊工艺的优点
冷补焊的焊缝金属是奥氏体组织,焊接过程中不发生相变,且焊缝的塑性和韧性较好,因此可不预热,也不需焊后热处理,简化了补焊工艺,避免铸钢件受到过大的热作用,从而减小被焊件的应力和变形;奥氏体组织对氢有较大的溶解度,可避免焊缝产生氢致裂纹,减少珠光体组织的近缝区产生氢致裂纹的可能;奥氏体组织的缺口敏感性比珠光体组织低,即使焊缝内部有裂纹也不易扩展;奥氏体组织焊缝金属的屈强比小于珠光体组织的,因而在应力作用下,必然产生塑性变形,从而使应力得到松弛,避免了结构的破坏。
2.1.2冷补焊存在的缺点
a) 补焊近缝区的淬硬问题
冷补焊时近缝区的冷却速度较大,最高可达120 ℃/s,在补焊的近缝区不可避免地产生淬硬组织。
这种高硬度、低塑性的淬硬层约有1 mm宽,给补焊接头的性能带来不利影响。
b) 奥氏体焊缝金属σ相析出脆化
奥氏体焊缝金属长期在高温下运行,将有σ相析出。
σ相是Fe和Cr的金属间化合物,性脆而硬。
它的析出物一般分布在奥氏体晶粒的边界处,使奥氏体焊缝的韧性下降。
有资料表明,18Cr8Ni奥氏体焊缝金属在高温下长期运行1 000 h,由于σ相析出,使焊缝的韧性变化幅度很大,最低韧性值降至原韧性值的10%左右。
c) 奥氏体焊缝金属与珠光体母材之间的碳扩散问题
奥氏体焊缝与珠光体母材间的合金含量相差十分悬殊,特别是Cr元素的质量分数相差更大,构成了母材的碳向焊缝扩散的条件,从而在近缝区母材侧出现脱碳层,铁素体晶粒长大,强度下降,在机组启停的热循环过程中,沿脱碳层产生热疲劳裂纹而破坏。
d) 接头产生的附加应力
奥氏体与珠光体的线膨胀系数不同,在今后的运行中,由于温度的变化,及起停的热循环过程中,在接头的界面将产生附加热应力,随着这种热循环次数的增加,热应力变化将引起接
头的热疲劳破坏。
2.2珠光体耐热钢焊条的热补焊
热补焊工艺由于补焊填充材料与铸钢件材料基本一致,在高温运行条件下,不会出现冷补焊时存在的σ相析出等问题,补焊接头的性能稳定。
但是,热补焊工艺复杂,需对隔板进行预热和焊后热处理,由于附加加热次数的增加,大大增加了铸钢件补焊的残余变形量。
而隔板有一定的尺寸要求,因此在热补焊过程中严格控制变形是非常必要的。
热补焊虽然采取了许多工艺措施,但实践表明,用热焊方法补焊的焊缝,应力水平仍是较高的,有时接近母材的屈服极限,又由于珠光体组织的焊缝塑性和韧性均较奥氏体焊缝差。
为减少应力水平,补焊过程中应严格控制预热温度、热处理温度和层间温度,尽量减小焊接应力,改善焊缝组织。
为了保证补焊后焊缝组织的性能,避免冷焊带来的不稳定性,我们决定采用珠光体耐热钢焊条的热补焊工艺。
3焊接性分析
给水泵汽轮机隔板体材质ZG20CrMo,以Cr, Mo为主要合金元素的珠光体耐热钢, 其化学成分和力学性能见表1。
珠光体耐热钢由于含碳及合金元素较多,焊缝及热影响区容易出现淬硬组织,当焊件刚性较大及接头应力大时,容易产生冷裂纹,应进行焊前预热与焊后热处理,以减小焊接残余应力从而减少冷裂纹的产生。
但是,铸件现场补焊的工件体积大、结构复杂,很难对补焊处进行常规的充分预热和焊后热处理。
由于工件结构刚性大,拘束度大,局部补焊时产生的焊接拘束应力较大,同时冷却速度大,散热快,难于用局部加热的方法来控制焊接时的冷却速度,预热、焊接和焊后热处理都可能造成变形等种种特点,给补焊工作增加很大的难度。
使用奥氏体不锈钢焊条对此类铸件进行冷补焊虽然能解决上述部分问题,但焊缝与母材是异种金属结合,存在着熔合区脆性过渡层、熔合线两侧碳迁移、线膨胀系数不同等问题,补焊区域的长期安全运行受到影响,因此决定采用同质焊材补焊。
同质补焊必须同时充分考虑工件的体积、结构、刚性、冷却等多种因素的组合,采用适当的焊接工艺参数、预热和后热温度、冷却速度等才能保证补焊工作的成功。
邹一汽机石凯。