三效蒸发器CAD图说明修改版
三效蒸发器CAD图说明修改版

三效连续蒸发结晶器设备表序号设备规格型号数量备注1 预热器4套2 一效加热室2套3 一效分离室2套4 二效加热室2套5 二效分离室2套6 三效加热室2套7 三效分离室2套8 冷凝水罐2台9 冷凝器2台10 液位自控阀6套11 汽水分离罐4台12 进料泵2台流量8m3/h,扬程40m,功率5.5kw13 出料泵2台流量3m3/h,扬程30m,功率2.2kw14 强制循环泵2台流量1350m3/h,扬程1.5m,功率22kw15 逆流泵4台流量5m3/h,扬程25m,功率2.2kw16 冷凝水泵2台流量8m3/h,扬程25m,功率4kw17 真空泵2台2SK-6,功率11kw18 温度检测计8套19 流量检测计2套20 压力检测计8套21 浓度检测计1套22 减压阀1个该三效蒸发结晶系统主要是为了从盐酸酸洗废液中回收氯化亚铁晶体和盐酸。
工作原理主要是根据氯化氢易于挥发和易溶于水的特性,以及氯化亚铁在盐酸溶液中溶解度的规律,采用蒸汽加热蒸发浓缩工艺,使酸洗废液中的盐酸和铁盐分离。
蒸发产生的含HCl的气体经适当冷凝分离得到18%左右的热稀盐酸,可循环使用。
含高浓度铁盐的酸洗废液浓缩到一定浓度后经后续工艺获取氯化亚铁的结晶体。
该三效蒸发结晶系统中,废酸原液与蒸汽的流向相反,属于逆流模式。
盐酸酸洗废液在加热蒸发浓缩过程中温度较高,盐酸腐蚀性很强,采用耐高温和换热系数较高的非金属材质的石墨内衬加热室和分离室,使设备腐蚀程度大为降低,可有效延长设备的使用寿命,降低酸洗废液处理过程设备运行维护费用。
该系统结构包括有预热器1a、预热器1b、第一效加热室2、第一效分离室3、第二效加热室4、第二效分离室5、第三效加热室6、第三效分离室7、冷凝水罐8、冷凝器9、液位自控阀10、汽水分离罐11、进料泵01、出料泵02、强制循环泵03、逆流泵04、05、冷凝水泵06、真空泵07、温度检测计、流量检测计、压力检测计、浓度检测计、减压阀和管道。
三效蒸发器工艺流程图

三效蒸发器工艺流程图
三效蒸发器是一种用于浓缩溶液的设备,其工艺流程图如下所示:
首先,原始溶液从进料口进入蒸发器,经过预热器预热后,进
入第一效蒸发器。
在第一效蒸发器中,溶液受热蒸发,产生蒸汽,
而未蒸发的溶液则成为下一级蒸发器的进料。
接着,蒸汽通过蒸汽分离器分离出来,成为蒸汽产物。
而在蒸
汽分离器中,溶液则继续蒸发,直至浓缩到一定程度。
浓缩后的残
液从下部排出,成为下一级蒸发器的进料。
最后,蒸汽产物通过冷凝器冷凝成液体,而液体则被收集起来,成为浓缩后的产物。
而残液则通过残液排出口排出系统。
三效蒸发器工艺流程图清晰展示了溶液在蒸发器中的浓缩过程,通过多级蒸发,能够充分利用热能,提高浓缩效率。
同时,蒸汽产
物的回收也能够减少能源消耗,降低生产成本。
三效蒸发器工艺流程图的设计考虑了热能的传递和利用,使得
溶液能够在设备内充分蒸发浓缩,达到预期的浓缩效果。
同时,蒸汽产物的回收利用也是工艺流程图的重要设计要素,能够提高能源利用效率,减少能源浪费。
总的来说,三效蒸发器工艺流程图清晰地展示了溶液在设备内的蒸发浓缩过程,通过多级蒸发和蒸汽产物的回收利用,能够提高浓缩效率,降低生产成本,是一种高效节能的浓缩设备。
含盐废水三效强制循环蒸发器调试操作规范PDF
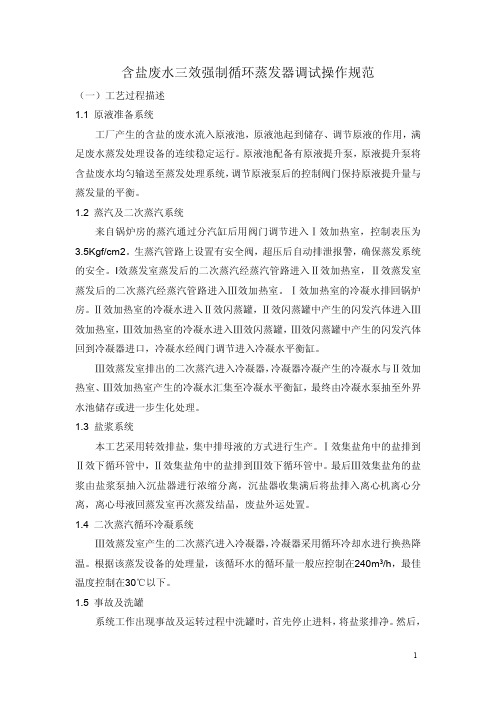
含盐废水三效强制循环蒸发器调试操作规范(一)工艺过程描述1.1原液准备系统工厂产生的含盐的废水流入原液池,原液池起到储存、调节原液的作用,满足废水蒸发处理设备的连续稳定运行。
原液池配备有原液提升泵,原液提升泵将含盐废水均匀输送至蒸发处理系统,调节原液泵后的控制阀门保持原液提升量与蒸发量的平衡。
1.2蒸汽及二次蒸汽系统来自锅炉房的蒸汽通过分汽缸后用阀门调节进入Ⅰ效加热室,控制表压为3.5Kgf/cm2。
生蒸汽管路上设置有安全阀,超压后自动排泄报警,确保蒸发系统的安全。
I效蒸发室蒸发后的二次蒸汽经蒸汽管路进入Ⅱ效加热室,Ⅱ效蒸发室蒸发后的二次蒸汽经蒸汽管路进入Ⅲ效加热室。
Ⅰ效加热室的冷凝水排回锅炉房。
Ⅱ效加热室的冷凝水进入Ⅱ效闪蒸罐,Ⅱ效闪蒸罐中产生的闪发汽体进入Ⅲ效加热室,Ⅲ效加热室的冷凝水进入Ⅲ效闪蒸罐,Ⅲ效闪蒸罐中产生的闪发汽体回到冷凝器进口,冷凝水经阀门调节进入冷凝水平衡缸。
Ⅲ效蒸发室排出的二次蒸汽进入冷凝器,冷凝器冷凝产生的冷凝水与Ⅱ效加热室、Ⅲ效加热室产生的冷凝水汇集至冷凝水平衡缸,最终由冷凝水泵抽至外界水池储存或进一步生化处理。
1.3盐浆系统本工艺采用转效排盐,集中排母液的方式进行生产。
Ⅰ效集盐角中的盐排到Ⅱ效下循环管中,Ⅱ效集盐角中的盐排到Ⅲ效下循环管中。
最后Ⅲ效集盐角的盐浆由盐浆泵抽入沉盐器进行浓缩分离,沉盐器收集满后将盐排入离心机离心分离,离心母液回蒸发室再次蒸发结晶,废盐外运处置。
1.4二次蒸汽循环冷凝系统Ⅲ效蒸发室产生的二次蒸汽进入冷凝器,冷凝器采用循环冷却水进行换热降温。
根据该蒸发设备的处理量,该循环水的循环量一般应控制在240m3/h,最佳温度控制在30℃以下。
1.5事故及洗罐系统工作出现事故及运转过程中洗罐时,首先停止进料,将盐浆排净。
然后,将蒸发罐中的卤水排到母液原液池中,将蒸发设备中的母液排净。
洗罐水用冷凝水储池的水,洗罐完毕后,将洗罐水排掉,初次洗罐水排入原液池,排空蒸发罐后,首先将部分母液通过原液泵进入蒸发罐,然后通过原液泵补充加入原液,使蒸发罐中的液位满足工艺要求。
三效连续蒸发结晶器设计

三效连续蒸发结晶器(技术方案)总目录一、工艺说明:二、工作过程中料液的流动:三、工作过程中蒸汽的流动:四、工作过程中冷凝水的流动:伍、设备材质选择:六、浓缩介质:七、整套系统流程方框图:八、设备主要工作技术参数:九、配套设备主要技术特点:一、工艺说明:(1)生蒸汽进入Ⅰ效加热器作为热源,对Ⅰ效内的物料进行加热;Ⅰ效分离室内的物料经过蒸发产生二次蒸汽,进入Ⅱ效加热器作为热源对Ⅱ效内的物料进行加热;Ⅱ效分离室内的物料经过蒸发产生二次蒸汽,进入Ⅲ效加热器作为热源对Ⅲ效内的物料进行加热。
(2)本装置相关的技术特点是:将具有强化传热、防垢性能优良的沸腾蒸发。
针对本装置而言,由于采用的是外循环传热蒸发方式,物料在管束中的流向本身就是自下而上的,就可以达到强制循环的目的,这样的能耗很低,也降低了蒸发器的运行成本。
本装置的原理可以广泛用于盐卤、芒硝、烧碱、亚硫酸钠、硫酸锰、氯化纳、氯化钙、氧化铝、硫酸铵、氯化铵等溶液的沸腾蒸发结晶工艺。
(3)本工艺采用了国内外最先进的蒸发工艺技术,具有蒸发速度快,物料受热时间短,物料不易结焦与结污垢,设备便于清洗。
物料可直接在蒸发器内热结晶,能耗低,操作方便,维修频率低,占地面积小等优点。
带液位自动控制装置蒸发器的工艺流程简述:开启真空泵抽真空、打开冷却水进口阀门,整套蒸发器在-0.090Mpa真空状态下开始工作,开启原料液进料泵,使物料经预热通过液位控制阀进入第Ⅰ效分离室,笫Ⅰ效分离室内物料液位在进料泵的作用下升高;笫Ⅰ效分离室内物料液位升高的同时,笫Ⅱ效分离室内物料在负压差作用下通过液位控制阀被吸入第Ⅱ效分离室,第Ⅱ效分离室内物料液位升高;同理第Ⅲ效分离室内物料液位升高。
Ⅰ、Ⅱ、Ⅲ效分离室内物料在液位控制阀的作用下,各效分离室、结晶器内的物料液位被设定在适当的参数范围内,并达到设计液位。
此时,开启生蒸汽阀门,使生蒸汽进入蒸发器进行物料蒸发,生蒸汽和多次产生的二次蒸汽与物料进行热效交换后,物料中的水份不断被汽化成水蒸汽蒸发,而生蒸汽或二次蒸汽在进行换热后凝结成冷凝水。
(完整版)硫酸钠三效结晶蒸发器介绍及调试
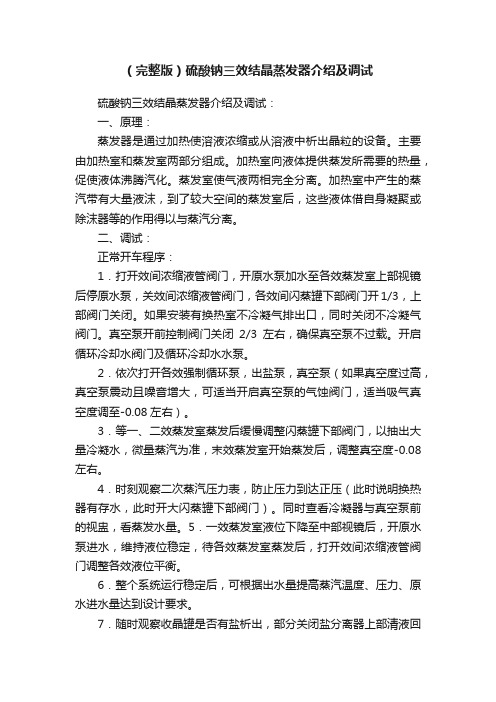
(完整版)硫酸钠三效结晶蒸发器介绍及调试硫酸钠三效结晶蒸发器介绍及调试:一、原理:蒸发器是通过加热使溶液浓缩或从溶液中析出晶粒的设备。
主要由加热室和蒸发室两部分组成。
加热室向液体提供蒸发所需要的热量,促使液体沸腾汽化。
蒸发室使气液两相完全分离。
加热室中产生的蒸汽带有大量液沫,到了较大空间的蒸发室后,这些液体借自身凝聚或除沫器等的作用得以与蒸汽分离。
二、调试:正常开车程序:1.打开效间浓缩液管阀门,开原水泵加水至各效蒸发室上部视镜后停原水泵,关效间浓缩液管阀门,各效间闪蒸罐下部阀门开1/3,上部阀门关闭。
如果安装有换热室不冷凝气排出口,同时关闭不冷凝气阀门。
真空泵开前控制阀门关闭2/3左右,确保真空泵不过载。
开启循环冷却水阀门及循环冷却水水泵。
2.依次打开各效强制循环泵,出盐泵,真空泵(如果真空度过高,真空泵震动且噪音增大,可适当开启真空泵的气蚀阀门,适当吸气真空度调至-0.08左右)。
3.等一、二效蒸发室蒸发后缓慢调整闪蒸罐下部阀门,以抽出大量冷凝水,微量蒸汽为准,末效蒸发室开始蒸发后,调整真空度-0.08左右。
4.时刻观察二次蒸汽压力表,防止压力到达正压(此时说明换热器有存水,此时开大闪蒸罐下部阀门)。
同时查看冷凝器与真空泵前的视盅,看蒸发水量。
5.一效蒸发室液位下降至中部视镜后,开原水泵进水,维持液位稳定,待各效蒸发室蒸发后,打开效间浓缩液管阀门调整各效液位平衡。
6.整个系统运行稳定后,可根据出水量提高蒸汽温度、压力、原水进水量达到设计要求。
7.随时观察收晶罐是否有盐析出,部分关闭盐分离器上部清液回流阀,使整个盐分离器及收晶罐处于正压状态,便于盐分的排出;勤于观察,做到随时排盐防止堵塞。
8.三效硫酸钠晶体浓度达到15%以后,开启离心机,分离的硫酸钠固体排至储料池,滤液回到滤水罐。
滤水罐满后自动开启抽液泵,将滤水罐内的液体送至三效蒸发器。
正常停车程序:首先关闭蒸汽进口控制阀门,蒸发工序先将蒸发室内盐浆尽量排出,然后将加热蒸汽放空;把各罐内料液经事故管排放到原液罐,然后将原液罐内的原液打入各罐,开动循环泵。
化工原理设计说明书-三效并流蒸发器
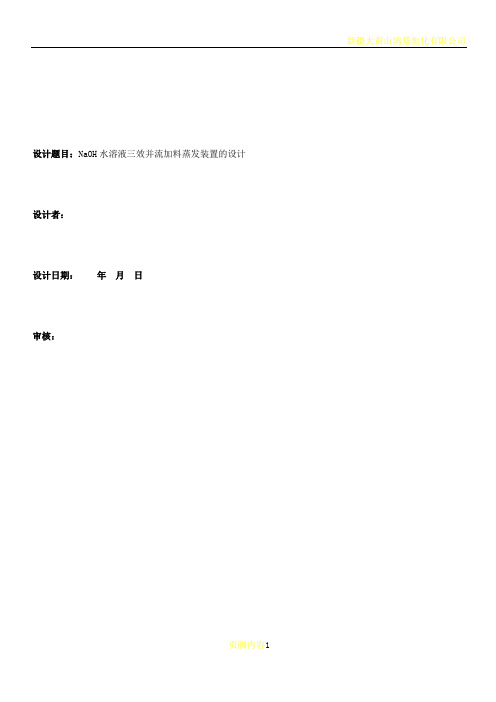
设计题目:NaOH水溶液三效并流加料蒸发装置的设计设计者:设计日期:年月日审核:2009级化工单元操作课程设计任务书一、设计题目NaOH水溶液三效并流加料蒸发装置的设计二、设计任务及操作条件1.处理能力 3.96×104吨/年NaOH水溶液2.设备形式中央循环管式蒸发器3.操作条件(1) NaOH水溶液的原料液浓度为5%。
完成液浓度为25%,原料液温度为第一效沸点温度,原料液比热为3.7KJ(kg·℃),各效蒸发器中溶液的平均密度为:ρ1=1014kg/m3,ρ2=1060 kg/m3,ρ3=1239 kg/m3;(2)加热蒸气压强为500kPa(绝压),冷凝器压强为15 kPa(绝压):(3)各效蒸发器的总传热系数:K1=1500W/(m2·℃),K2=1000W/(m2·℃),K3=600W/(m2·℃);(4)各效蒸发器中页面的高度:1.5m;(5)各效加热蒸气的冷凝液均在饱和温度下下排出,假设各效传热面积相等,并忽略热损失;(6)每年按330天计算,每天24小时运行。
三、设计项目(1)设计方案简单,对确定的工艺流程及蒸发器形式进行简要论述;(2)蒸发器的工艺计算,确定蒸发器的传热面积;(3)蒸发器的主要结构尺寸设计;(4)绘制NaOH水溶液三效并流加料蒸发装置的流程及蒸发器设备工艺简图;(5)对本设计的评述1目录(一)蒸发器的形式、流程、效数论证..................(二)工艺计算......................................(三)蒸发器主要工艺尺寸的设计计算..................(四)设计感想......................................(五)设计图纸......................................2(一)蒸发器的形式、流程、效数论证1.蒸发器的形式:中央循环管式2.蒸发器的流程:三效并流加料3.效数论证:在工业中常用的加热方式有直接加热和间接加热。
三效蒸发器工艺流程图
三效蒸发器工艺流程图三效蒸发器工艺流程图三效蒸发器是一种高效利用热能的分离设备,广泛应用于化工、制药、食品等工业领域。
下面是一篇700字的三效蒸发器工艺流程图的介绍。
三效蒸发器工艺流程图如下:输入原料:进料泵将原料送入蒸发器系统中。
一效加热:原料进入一效加热器,通过蒸汽加热提高其温度,同时与一效蒸发器中的蒸发液接触,进行传热和物质传递,使得一效蒸发器中的蒸发液蒸发。
一效蒸发:一效蒸发器中的蒸发液暴露在低压蒸汽的条件下,形成蒸气和浓缩液。
浓缩液通过一效蒸发器的排污阀排出,而蒸汽则通过一效凝结器冷凝为蒸汽。
蒸汽压缩:蒸汽经过一效凝结器后进入一效蒸发器,通过蒸发器中的蒸发液与低温热物料接触传热,同时压缩蒸气,使其温度和压力升高。
二效加热:二效加热器中的蒸汽与二效蒸发器中的蒸发液进行传热和物质传递,使得二效蒸发器中的蒸发液继续蒸发。
二效蒸发:二效蒸发器中的蒸发液也暴露在低压蒸汽的条件下,形成蒸气和浓缩液。
浓缩液通过二效蒸发器的排污阀排出,而蒸汽则通过二效凝结器冷凝为蒸汽。
蒸汽压缩:蒸汽经过二效凝结器后进入二效蒸发器,通过蒸发器中的蒸发液与低温热物料接触传热,同时压缩蒸汽,使其温度和压力升高。
三效加热:三效加热器中的蒸汽与三效蒸发器中的蒸发液进行传热和物质传递,使得三效蒸发器中的蒸发液继续蒸发。
三效蒸发:三效蒸发器中的蒸发液也暴露在低压蒸汽的条件下,形成蒸气和浓缩液。
浓缩液通过三效蒸发器的排污阀排出,而蒸汽则通过三效凝结器冷凝为蒸汽。
蒸汽压缩:蒸汽经过三效凝结器后进入三效蒸发器,通过蒸发器中的蒸发液与低温热物料接触传热,同时压缩蒸汽,使其温度和压力升高。
产品收集:三效蒸发器系统中的蒸汽通过除气器除去水蒸气中的杂质和少量蒸发液,然后通过冷凝器冷凝为液体,最后由产物泵将产物送至收集罐中。
废物处理:三效蒸发器系统中的排污阀排出的浓缩液经过处理后,可用于再利用或排放。
整个三效蒸发器工艺流程图中,通过多级蒸发和压缩的方式,能够有效利用热能,提高设备的能效,同时还能够对原料进行分离浓缩,得到高纯度的产物和节约能源的排放。
三效错流蒸发器开关机说明书
三效蒸发器使用说明书湖北中原楚天蒸发器有限公司目录一、设备特点 (3)二、技术参数 (3)三、工作原理 (3)四、试车 (4)五、液位自动控制 (7)六、安装与调整 (7)七、维修和保养 (8)八、问题解决方案 (8)一、设备特点:通过对物料性质的了解,我公司采用了三效错流蒸发器,其特点是具有比较高的传热性能,能耗较低,适合浓缩粘度较大,有晶体的物料。
强制循环式蒸发器是一种高效多程循环型蒸发设备,它具有传热效率高、温差损失小、物料加热时间短、不易腐蚀材料、适合处理粘度较高,有结晶体的物料。
二、技术参数三、工作原理:蒸发器的工作原理:通过热交换将稀浓度废水中的大部分水分蒸发(汽化)掉,以提高废水的浓度,直至达到要求的浓度,从各效排出。
四、试车1)试车前的准备为确保试车顺利和安全,需要作好如下准备工作:(1)全面系统地检查设备安装的正确性、安全性和精密度。
重点是泵的安装、蒸发器的垂直度。
(2)组织试车人员进行一次设备的学习,熟悉设备的流程,结构、性能、操作规程和操作注意事项。
(3)准备好试车记录本,并明确记录内容和要求。
(4)设备内做彻底冲洗。
(5)检查各效进料电动阀启闭是否正常。
(重点)2)试车注意事项及要求(1) 设备的投料运转过程中不允许中断物料。
(2) 用水冷却的泵,必须在给水后方可开动,并应保证要求的水压,运行过程中不能断水。
保证各泵有充足的冷却密封水供应。
(重点)(3) 严格执行操作规程,认真作好记录。
(4)水试完毕应达到要求的工艺数据。
(6)水试必须重复两次以上方可投料试车。
(7)为防止蒸发、加热管壁挂水垢,试车(生产)中应该尽可能地使用蒸汽冷凝水运转和冲洗。
(8)因紧急事故停车时,首先讯速关闭蒸汽阀(切断蒸汽),然后及时将物料排出。
3)试车步骤:部件试运转——水试车——物料试车(1)部件试运转系指配备的各泵的运转。
(2)水试车。
水试车是以水代替物料的操作过程。
检查设备各法兰,阀门,管道有没有漏气,漏水的现象。
含盐三效强制循环蒸发器
含盐三效强制循环蒸发器公司内部编号:(GOOD-TMMT-MMUT-UUPTY-UUYY-DTTI-博特蒸发器项目名称:100t/d含盐三效强制循环蒸发器设计能力:蒸发量4032kg/h客户单位:邯郸富美环保科技有限公司设计单位:石家庄博特环保科技有限公司设计编码:BTHB-141217-03设计日期:2014年12月17日一、公司简介石家庄博特环保科技有限公司是一家致力于工业疑难废水处理技术开发及相应配套设备生产和销售的高科技环保企业,拥有一流的工业疑难废水处理技术和设备。
自公司成立以来,博特环保成功地帮肋客户解决了很多的环境治理难题,为当地的环境污染治理发挥了重要作用;公司的工业疑难废水处理技术与设备在钢铁、化工、医药、纺织、煤化工、石油等行业拥有众多的使用业绩。
公司与北京航空航天大学、北方设计研究院、河北科技大学等大学和科研机构建立了密切的合作关系,同时聘请了一批具有丰富实际经验的高级工程师,形成了博特环保公司的技术核心,为公司的产品的研发、设计提供技术支持,为公司的发展奠定了坚实的技术基础。
公司在石家庄设有产品研发中心、技术服务中心和设备销售中心。
并拥有标准的设备加工生产中心,可以生产和调试自主知识产权设备,并对进口的设备的进行组装和测试。
公司严格按照ISO9001国际质量管理体系认证、IS O14001国际环境管理体系认证的要求进行设备的生产和销售,为客户创造最大的社会和经济价值。
科研成果产品:废水蒸发结晶设备、废水蒸发浓缩设备、降膜蒸发器、强制循环蒸发器、 MVR蒸发器等。
二、工艺及蒸发器选择1.物料分析:处理量100吨/天,含钠盐钾盐为4%。
2.性质分析:氯化钠溶解度3.蒸发器类型:设计方案针对含盐废水,采用三效顺流强制循环蒸发装置。
盐溶液都属于蒸发结晶,因此蒸发器采用抗盐析、抗结疤堵管能力强的强制循环蒸发器。
4.本蒸发器特点:1.结构紧凑、占地面积小2.蒸汽耗量低,浓缩比大3.管内受热均匀,传热系数高4. 连续出料,液位与所需浓度可实现自控(根据客户需要)5.工艺描述:5.1原液准备系统工厂产生的含氯化钠的废水流入原液池,原液池起到储存、调节原液的作用,满足废水蒸发处理设备的连续稳定运行。
三效蒸发器操作说明书
三效蒸发器操作说明书 Document number:WTWYT-WYWY-BTGTT-YTTYU-2018GT*************有限公司三效蒸发结晶装置操作说明书一、安全事项警告:1.本装置电气控制柜内部严禁进水或受潮。
2.操作人员必须严格按照本公司所提供的操作说明操作。
3.操作人员必须具备基本的电气常识和机械常识,并经过培训考核合格后才能操作。
4.严禁在无介质的状态下运转本装置。
5.严禁在介质蒸发干后,继续运转。
6.操作人员在操作之前应该注意到本装置的警示标志。
7.本装置安装有报警装置,一旦发现异常,立刻按照程序处理。
安全注意事项1.请牢记停止开关的位置,以便出现异常时可以立即停机;2.无论进行何种保养,检查,调整,请务必关闭机台及主开关;3.停电时请关闭主电源开关。
安全标志1.在机台上必要的地方张贴防止事故的警告等的安全标志,并请务必遵守标志中显示的注意事项;2.请勿剥除机台上所附的警告等安全标志,若标志丢失或因污损等原因使其无法辩认时,请与本公司联系并设法替换。
二、设备基本组成详见三效蒸发装置竣工图(PID图)。
三、操作说明开车前的检查、准备工作:1.操作人员必须事先经过培训后才能操作该设备,并遵循操作说明书的要求;2.检查设备各法兰,阀门,管道有没有漏气,漏水的现象;3.检查各泵的油位是否充足,应在二分之一处;4.启动密封水泵,保证各泵有充足的冷却密封水供应;5.提前确认相关连接部分,蒸汽系统、冷却水系统、配电室等,蒸汽、电、冷却水、原水正常情况下开车;6.开机前确保主电源正常,设备电源在接通状态。
所有阀门在设定的开关状态,仪表正常工作;7.开机前确认浓缩装置原水池液位,浓缩装置物料槽在高液位时可以进行处理。
如不在设定液位时,需要处理,必须随时掌握处理进度;8.本设备实现自动化,执行一键开机运行,设备按设置程序自动运行。
自动时,执行以下操作:1.首次启动时需要往真空泵补水,。
若真空泵之前有运行过,则无需再次补水。
- 1、下载文档前请自行甄别文档内容的完整性,平台不提供额外的编辑、内容补充、找答案等附加服务。
- 2、"仅部分预览"的文档,不可在线预览部分如存在完整性等问题,可反馈申请退款(可完整预览的文档不适用该条件!)。
- 3、如文档侵犯您的权益,请联系客服反馈,我们会尽快为您处理(人工客服工作时间:9:00-18:30)。
三效连续蒸发结晶器设备表
序号设备规格型号数量备注
1 预热器4套
2 一效加热室2套
3 一效分离室2套
4 二效加热室2套
5 二效分离室2套
6 三效加热室2套
7 三效分离室2套
8 冷凝水罐2台
9 冷凝器2台
10 液位自控阀6套
11 汽水分离罐4台
12 进料泵2台流量8m3/h,扬程40m,功
率5.5kw
13 出料泵2台流量3m3/h,扬程30m,功
率2.2kw
14 强制循环泵2台流量1350m3/h,扬程1.5m,
功率22kw
15 逆流泵4台流量5m3/h,扬程25m,功
率2.2kw
16 冷凝水泵2台流量8m3/h,扬程25m,功
率4kw
17 真空泵2台2SK-6,功率11kw
18 温度检测计8套
19 流量检测计2套
20 压力检测计8套
21 浓度检测计1套
22 减压阀1个
该三效蒸发结晶系统主要是为了从盐酸酸洗废液中回收氯化亚铁晶体和盐酸。
工作原理主要是根据氯化氢易于挥发和易溶于水的特性,以及氯化亚铁在盐
酸溶液中溶解度的规律,采用蒸汽加热蒸发浓缩工艺,使酸洗废液中的盐酸和铁盐分离。
蒸发产生的含HCl的气体经适当冷凝分离得到18%左右的热稀盐酸,可循环使用。
含高浓度铁盐的酸洗废液浓缩到一定浓度后经后续工艺获取氯化亚铁的结晶体。
该三效蒸发结晶系统中,废酸原液与蒸汽的流向相反,属于逆流模式。
盐酸酸洗废液在加热蒸发浓缩过程中温度较高,盐酸腐蚀性很强,采用耐高温和换热系数较高的非金属材质的石墨内衬加热室和分离室,使设备腐蚀程度大为降低,可有效延长设备的使用寿命,降低酸洗废液处理过程设备运行维护费用。
该系统结构包括有预热器1a、预热器1b、第一效加热室2、第一效分离室3、第二效加热室4、第二效分离室5、第三效加热室6、第三效分离室7、冷凝水罐8、冷凝器9、液位自控阀10、汽水分离罐11、进料泵01、出料泵02、强制循环泵03、逆流泵04、05、冷凝水泵06、真空泵07、温度检测计、流量检测计、压力检测计、浓度检测计、减压阀和管道。
预热器1所用的热源为生蒸汽冷凝水和第三效二次蒸汽,节省了原料预热的能耗,缩短了蒸发的时间,使热能的利用率得到提高。
经过预热器1预热后的原液与蒸汽流向相反依次进入第三效加热室6和第三效分离室7组成的外加热循环蒸发系统、第二效加热室4和第二效分离室5组成的外加热循环蒸发系统、第一效加热室2、第二效分离室3和强制循环泵PMP03组成的外加热强制循环蒸发系统,得到氯化亚铁浓缩液。
氯化亚铁浓缩液制备成的氯化亚铁晶体采用编织袋包装,便于长距离运输,可直接使用作为电镀的原料、印染的煤染剂、陶瓷的着色剂等,也可经深加工生产三氯化铁、聚合氯化铁等高效水处理药剂以及铁系颜料、铁氧体等高附加值化工产品。
生蒸汽是整个系统的初始热源,生蒸汽进入第一效加热室2前先要经过流量和P1压力检测计的检测,并且在进入系统前还需通过减压阀控制。
第一效分离室3的上部设有二次蒸汽管与第二效加热室4连通,第一效加热室2下端外接了冷凝水管与预热器1a相通,利用第一效生蒸汽换热后温度较高冷凝水对废酸原液进行预热。
第二效分离室5的上部设有二次蒸汽管与第三效加热室6连通,第二效加热室4下端外接了冷凝水管与汽水分离罐11a相通,通过罐11a的作用使第二效加热器4外排的冷凝水汽水分离,蒸汽进入第三效加热器6,冷凝水则最终进入冷凝水罐8。
第三效分离室7的上部设有二次蒸汽管与预热器1b连通,使余热得到更充分的利用。
第三效加热室6下端外接了冷凝水管与汽水分离罐11b相通,通过罐11b的作用使第三效加热器6外排的冷凝水汽水分离,蒸汽进入预热器1b,冷凝水则最终进入冷凝水罐8。
最终经过三效蒸发系统蒸发出的水和氯化氢气体进入冷凝器9冷凝而成18%左右的稀盐酸,基本基本不含氯化亚铁,因而纯度较高。
如流程图所示,从盐酸酸洗废液中回收氯化亚铁浓缩液和稀盐酸的处理系统是这样实现的,分为以下物料和蒸汽—冷凝水两个流程:
1、物料流程:
废酸原液通过进料泵PMP01依次进入预热器1b和预热器1a后,再进入第三效分离室7,第三效分离室7和第三效加热室6之间之间设有往复连通管道,形成一个循环蒸发系统,当料液经过循环加热达到一定的蒸发温度后,在第三效分离室7内完成气液分离。
第三效浓缩液由逆流泵PMP05打到第二效分离室5,第二效分离室5和第二效加热器4之间设有往复连通管道,也形成一个循环蒸发系统,当料液经过循
环加热达到一定的蒸发温度后,在第二效分离室5完成气液分离。
第二效浓缩液再由逆流泵PMP04打到第一效分离室3,为降低加热室和分离室结晶和堵塞现象,第一效分离室3和第一效加热室2之间设有强制循环泵PMP03形成一个强制循环蒸发系统,,待浓度检测计检测到浓缩液达到饱和浓度要求后,在由出料泵PMP02将浓缩液回收后进入后续工艺收集氯化亚铁晶体。
2、蒸汽—冷凝水流程:
生蒸汽先通过减压阀进入第一效加热室2加热物料后,第一效加热室2内的冷凝水进入预热器1a给废酸原液提供预热。
第一效加热室2中出来的第一效热物料在第一效分离室3内气液分离,产生第一效二次蒸汽和第一效浓缩液。
第一效二次蒸汽则通过二次蒸汽管进入第二效加热室4。
第二效加热室4中出来的第二效热物料在第二效分离室5内气液分离,产生第二效二次蒸汽和第二效浓缩液。
在第二效加热室4内产生的冷凝水进入汽水分离罐11a,罐11a分离出的蒸汽随第二效分离室5内产生的第二效二次蒸汽进入第三效加热室6,罐11a内汽水分离后的冷凝水经过罐11b最终进入冷凝水罐8。
第二效二次蒸汽则通过二次蒸汽管进入第三效加热室6。
第三效加热室6中出来的第三效热物料在第三效分离器7内气液分离,产生第三效二次蒸汽和第三效浓缩液。
在第三效加热室6内产生的冷凝水进入汽水分离罐11b,罐11b分离出的蒸汽进入预热器1b给废酸原液预热,罐11b内汽水分离后的冷凝水进入冷凝水罐8。
第三效分离器7中蒸发出的含有氯化氢和水蒸气的第三效二次蒸汽通过二次蒸汽管进入预热器1b给废酸原液预热,可节省原料预热的能耗。
最终从预热器1b出来的蒸汽进入冷凝器9冷凝,冷凝的蒸汽液化与来自汽水分离罐11的冷凝水混合后成为稀盐酸,经由冷凝水泵PMP06排出。