CC复合材料性能参数
(整理)CC复合材料的制备及方法.
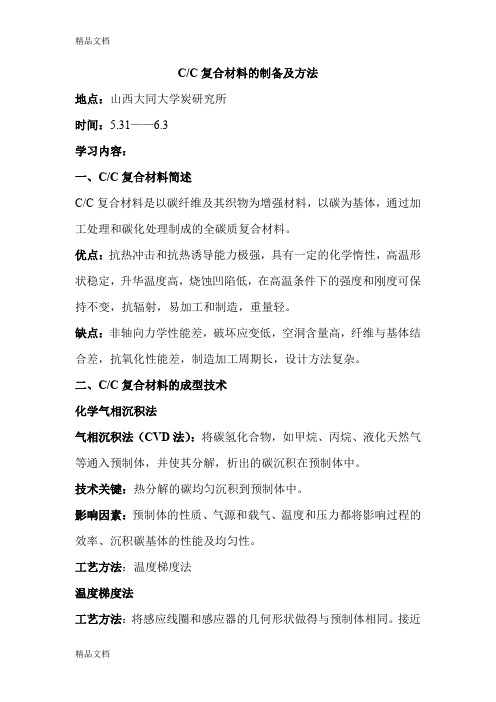
C/C复合材料的制备及方法地点:山西大同大学炭研究所时间:5.31——6.3学习内容:一、C/C复合材料简述C/C复合材料是以碳纤维及其织物为增强材料,以碳为基体,通过加工处理和碳化处理制成的全碳质复合材料。
优点:抗热冲击和抗热诱导能力极强,具有一定的化学惰性,高温形状稳定,升华温度高,烧蚀凹陷低,在高温条件下的强度和刚度可保持不变,抗辐射,易加工和制造,重量轻。
缺点:非轴向力学性能差,破坏应变低,空洞含量高,纤维与基体结合差,抗氧化性能差,制造加工周期长,设计方法复杂。
二、C/C复合材料的成型技术化学气相沉积法气相沉积法(CVD法):将碳氢化合物,如甲烷、丙烷、液化天然气等通入预制体,并使其分解,析出的碳沉积在预制体中。
技术关键:热分解的碳均匀沉积到预制体中。
影响因素:预制体的性质、气源和载气、温度和压力都将影响过程的效率、沉积碳基体的性能及均匀性。
工艺方法:温度梯度法温度梯度法工艺方法:将感应线圈和感应器的几何形状做得与预制体相同。
接近感应器的预制体外表面是温度最高的区域,碳的沉积由此开始,向径向发展。
温度梯度法的设备如下图:三、预制体的制备碳纤维预制体是根据结构工况和形状要求,编织而成的具有大量空隙的织物。
二维编织物:面内各向性能好,但层间和垂直面方向性能差;如制备的氧化石墨烯和石墨烯三维编织物:改善层间和垂直面方向性能;如热解炭四、C/C的基体的获得C/C的基体材料主要有热解碳和浸渍碳两种。
热解碳的前驱体:主要有甲烷、乙烷、丙烷、丙烯和乙烯以及低分子芳烃等;大同大学炭研究所使用的是液化天燃气。
浸渍碳的前驱体:主要有沥青和树脂五、预制体和碳基体的复合碳纤维编织预制体是空虚的,需向内渗碳使其致密化,以实现预制体和碳基体的复合。
渗碳方法:化学气相沉积法。
基本要求:基体的先驱体与预制体的特性相一致,以确保得到高致密和高强度的C/C复合材料。
化学气相沉积法制备工艺流程:碳纤维预制体→通入C、H化合物气体→加热分解、沉积→C/C复合材料。
cc复合材料

(3)涂层与基体碳之间要能良好结合,形 成较高的结合强度,对多层涂层来说, 各层之间也要有良好的结合强度,以免 分层或脱落;
(4)涂层与基体、涂层的各层之间的热膨 胀系数要尽可能接近,避免在较大的热 应力作用下涂层出现裂纹或剥落;
碳/碳复合材料
碳/碳复合材料的端头帽 碳/碳复合材料加工件
1.碳碳复合材料特性及性能
1.1碳碳复合材料特性 C/C复合材料是新材料领域中重点研究和开发 的一种新型超高温材料,它具有以下显著特 点:
(1)密度小(<2.0 g/cm ),仅为镍基高温合金的 1/4,陶瓷材料的1/2,这一许多结构或装备 要求轻型化至关重要。
3.1内部抗氧化技术 该化技术是从两方面来解决C/C 复合材料的
抗氧化问题。 (1)改进纤维的抗氧化问题。纤维抗氧化性能 的提高手段有两种,一是提高纤维的石墨化度, 从而提高纤维的抗氧化性;另一种方法是在纤 维的表面进行涂层,使纤维得到保护。
(2)提高C/C 材料基体的抗氧化性。可以通过 加入氧化抑制剂的方法来提高C/C 材料基体的 抗氧化性,如加入含磷化合物等,通过磷与氧 的作用,使氧失去氧化活性,从而达到抗氧化 的目的,但效果并不理想。另外一种方法是在 基体中加入抗氧化组分,如重金属、陶瓷等可 以提高C/C 复合材料的抗氧化性;还可以在基 体中加入有机硅、有机钛等,使基体C被SiC和 TiC取代,也可达到抗氧化的目的。
2.1.2 热梯度式(差温式)CVD技术 将热梯度式CVD技术应用于碳刹车盘的制备, 其基本思路是在碳盘工件的径向(而不是厚度
方向)形成温度梯度,并通过压差使碳源气逆 温度梯度定向流动,从而提高了增密速度。并 研究了温度、气氛压力及其流量等参数对CVD 增密过程的影响。发现当温度、气氛压力搭配 合理时,热梯度式CVD增密效果大大优于均温 式,总致密时间仅为相应均温式的1/3。若在差 温式CVD基础上实现差温-差压式CVD可进一步 改善CVD增密效果。
CC复合材料
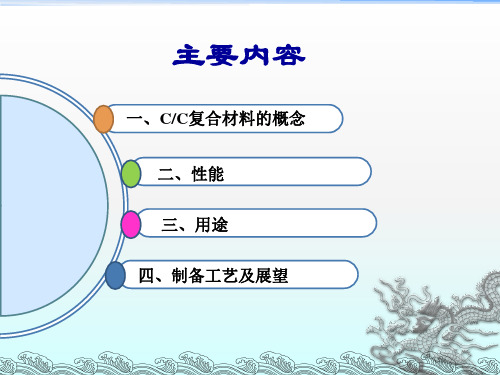
用于叶片和活塞, 可明显减轻重量, 提高燃烧室的温度, 大幅度提高热效率。
涡轮发动机
4.内燃发动机
发动机活塞和活塞环; 高性能密封材料
C/C复合材料因其密度低、优异的摩 擦性能、热膨胀率低,从而有利于控 制活塞与汽缸之间的空隙,目前正在 研究开发用其制活塞。
浸渍热固 性树脂
碳化、 墨化
通入HC化 合物气体
加热分解、 沉积
化学气相沉积法
C/C复 合材料
立式化学气相沉积炉
C/C复合材料的展望
今后将以结构C/C复合材料为主,向功能和多功能C/C复 合材料发展;
在编制技术方面:由单向朝多向发展; 机械针织技术方面:由简单机械向高度机械化、微机化
和计算机程控全自动化发展; 应用方面:由先进飞行器向普通航空和汽车、非航天高
C/C复合材料的用途
1.刹车领域的应用
C/C复合材料刹车盘的实验性研究于上世纪1973年第一次用于飞 机刹车。一半以上的C/C复合材料用做飞机刹车装置。
1.重量轻、耐温高 2.比热容比钢高2. 5 倍 3.同金属刹车相比可节省40 % 的结构重量 4.碳刹车盘的使用寿命是金属的5~7倍 5.刹车力矩平稳,刹车时噪声小
C/C复合材料在偏光下 的三种基本显微结构
C/C复合材料的性能
1.高温性能好:耐烧蚀 (3000℃ );耐高温(升华温度 3800℃);强度随温度的升高不降反升的独特性能,使其作为 高性能发动机热端部件和使用于高超声速飞行器热防护系统。 2.低比重、高比强、高比模、低热膨胀系数。 3.耐热冲击、耐烧蚀、耐含固体微粒燃气的冲刷。 4.质量轻,密度为1.65-2.0g/cm3,仅为钢的四分之一。
炭炭复合材料
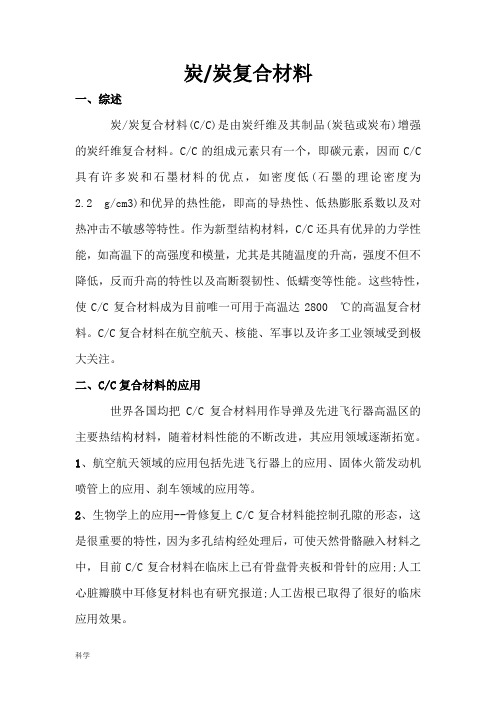
炭/炭复合材料一、综述炭/炭复合材料(C/C)是由炭纤维及其制品(炭毡或炭布)增强的炭纤维复合材料。
C/C的组成元素只有一个,即碳元素,因而C/C 具有许多炭和石墨材料的优点,如密度低(石墨的理论密度为2.2 g/cm3)和优异的热性能,即高的导热性、低热膨胀系数以及对热冲击不敏感等特性。
作为新型结构材料,C/C还具有优异的力学性能,如高温下的高强度和模量,尤其是其随温度的升高,强度不但不降低,反而升高的特性以及高断裂韧性、低蠕变等性能。
这些特性,使C/C复合材料成为目前唯一可用于高温达2800 ℃的高温复合材料。
C/C复合材料在航空航天、核能、军事以及许多工业领域受到极大关注。
二、C/C复合材料的应用世界各国均把C/C复合材料用作导弹及先进飞行器高温区的主要热结构材料,随着材料性能的不断改进,其应用领域逐渐拓宽。
1、航空航天领域的应用包括先进飞行器上的应用、固体火箭发动机喷管上的应用、刹车领域的应用等。
2、生物学上的应用--骨修复上C/C复合材料能控制孔隙的形态,这是很重要的特性,因为多孔结构经处理后,可使天然骨骼融入材料之中,目前C/C复合材料在临床上已有骨盘骨夹板和骨针的应用;人工心脏瓣膜中耳修复材料也有研究报道;人工齿根已取得了很好的临床应用效果。
三、性能(1)物理性能有耐酸、碱和盐的化学稳定性,其比热容大,热导率随石墨化程度的提高而增大,线膨胀系数随石墨化程度的提高而降低等优越性能。
(2)力学性能炭纤维长度方向的力学性能比垂直方向高出几十倍,C/C复合材料的拉伸强度大于270 MPa,单向高强度C/C复合材料可达700 MPa以上。
(3)热学及烧蚀性能C/C复合材料导热性能好、热膨胀系数低,因而热冲击能力很强,不仅可用于高温环境,而且适合温度急剧变化的场合。
其比热容高,这对于飞机刹车等需要吸收大量能量的应用场合非常有利。
四、制备(1)液相浸渍工艺液相浸渍工艺是制备C/C复合材料的一种主要工艺。
碳碳复合材料

碳/碳复合材料摘要:C/ C 复合材料是目前新材料领域重点研究和开发的一种新型超高温热结构材料, 密度小、比强度大、线膨胀系数低( 仅为金属的1/ 5~ 1/ 10) 、热导率高、耐烧蚀、耐磨性能良好。
特别是C/ C 复合材料在1 000℃~ 2 300℃时强度随温度升高而升高, 是理想的航空航天及其它工业领域的高温材料[ 1~ 7]。
C/ C 复合材料是具有优异耐高温性能的结构与功能一体化工程材料。
它和其它高性能复合材料相同,是由纤维增强相和基体相组成的一种复合结构, 不同之处是增强相和基体相均由具有特殊性能的纯碳组成[8.9]。
关键词:C/C复合材料发展高性能成型加工化学沉积航空航天易氧化1.碳/碳复合材料的发展C/C复合材料的首次出现是于1958年在Chance Vought航空公司实验室偶然得到的,当测定C纤维在一有机基体复合材料中的含量时,由于实验过程中的失误,有机基体没有被氧化,反而被热解,得到了C基体,结果发现这种复合材料具有结构特征,因而C/C复合材料就诞生了。
C/C复合材料技术在最初十年间发展的很慢,到六十年代末期,才开始发展成为工程材料中新的一员,自七十年代,在美国和欧洲得到很大发展,推出了C 纤维多向编织技术,高压液相浸渍工艺及化学气相浸渍法(CVI),有效地得到高密度的C/C复合材料,为其制造、批量生产和应用开辟了广阔的前景。
八十年代以来,C/C复合材料的研究极为活跃,前苏联、日本等国也都进去这一先进领域,在提高性能、快速致密化工艺研究及扩大应用等方面取得很大进展。
2.碳/碳复合材料的特征C/ C 复合材料具有低密度、高强度、高比模、低烧蚀率、高抗热震性、低热膨胀系数、零湿膨胀、不放气、在2 000℃以内强度和模量随温度升高而增加、良好的抗疲劳性能、优异的摩擦磨损性能和生物相容性( 组织成分及力学性能上均相容) 、对宇宙辐射不敏感及在核辐射下强度增加等性能[10.11],尤其是C /C 复合材料强度随温度的升高不降反升的独特性能,使其作为高性能发动机热端部件和使用于高超声速飞行器热防护系统具有其它材料难以比拟的优势[12]。
碳碳(C、C)复合材料介绍(ppt 38页)
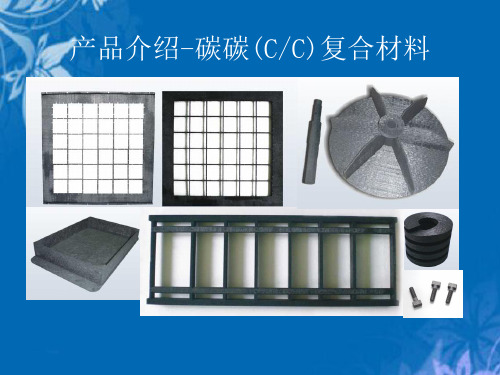
连续高温炉在设计和制造使更多的选择并使用标 准品。 与耐热刚的联接板不同,C/的联接板没有热变性, 使用寿命长,可以降低托盘的更换频率,减少驴子 维修次数,提高生产效率。 此外,由于托盘本身重量的降低,保温性能的提 高,降低了搬送设备的负荷,并且大幅降低了能源 损耗。
耐热材料领域-炉内材料-保温材
和“石墨”比较 和“陶瓷”比较
更高的强度 更好的韧性,不易破碎
更好的韧性,不易破碎 不易粘结(不会胶合) 耐热冲击性好 容易加工
和“树脂”比较
良好的耐热性 良好的耐腐蚀性 高的耐摩擦性
C/C复合材料应用领域介绍
耐热材料领域
C/C复合材料 C/C金属复合材料
优良的耐热性能及低重量,可作为金属热处理过程中的工具,如烧制垫 板,料盒,以及高温炉内耐温材料。可以提高成品率及生产效率
摩擦材料领域
根据先进的制造技术,制造出的优良的耐磨产品,可用作夹具,刹车 片,火车导电架的滑板等等。
高机械性能领域
C/C复合材料和 C/CMC产品集质量轻,耐热好,热膨胀小,高强度, 高弹性等优点于一身,可满足产业界多种多样的需要。
耐热材料领域
➢产品在2000℃~2500℃下生产而成,遇热变形的状况不会发生。 ➢同时,为了使产品达到更好的耐热冲击性,产品经过了反复的热处理。 ➢产品的密度为1.6~1.7g/cm3, 产品重量是耐热钢的1/4。 ➢因为碳素纤维经过强化处理,强度是原来石墨材料的3~5倍,产品掉落也不会产生损伤。
对于连续高温炉,一般其设计和制造都会采用标准品。 当炉内运送重物时,一般会采用薄钢板。 C/C复合材料与原来的耐热刚质辊棒相比,其不同之处在 于C/C耐热性能高,不需要进行水冷。因此可以提高炉内的 保温性。并且避免水冷系统漏水的问题。 同时,由于C/C材料几乎没有热变性,可以大幅降低维修 的次数,提高生产效率。 C/C辊棒本身质量轻,能够减少炉内20~50%的能量损耗。
C复合材料
度工艺等三种基本工艺方法(图11 – 6):
图 11 – 6 碳碳复合材料的CVD(CVI)工艺示意图
2) – 1 等温工艺
将预成型体置于均温CVD(CVI)炉中,导入碳 氢化合物气体,控制炉温和气体的流量和分压以控 制反应气体和生成气体在孔隙中的扩散,以便得到 均匀的 沉积。为了防止孔隙的过早封闭,应使反应 沉积速率低于扩散速率。这样沉积速率将非常缓慢。 为了提高制品的致密度,需要在沉积一定时间后, 对制品机加工,除去已封闭的外表面,然后再进行 沉积。如此循环,整个工艺需要长达数百上千小时 的时间。 等温工艺的优点是可以生产大型构件,并同时 可在一炉中装入若干件预成型体进行沉积。
1 – 2 基体碳
典型的基体碳有热解碳(CVD碳)和浸渍碳化碳。 前者是由烃类气体的气相沉积而成;后者是合成树 脂或沥青经碳化和石墨化而得。 1) CVD碳: 主要以来原料有甲烷、丙烷、丙烯、乙炔、天然 气等碳氢化合物。 CH4(g) C (s)+ 2H2(g) 沉积根据不同的沉积温度可获得不同形态的碳, 在950 ~ 1100C为热解碳;1750 ~ 2700C 为热解 石墨。
2) – 4 其它工艺
(4)直热式CVI工艺 直热式CVI工艺具有均匀、快速的特点。其原理 是在冷壁炉内,预制体直接通电被加热,在预制体 的每根纤维周围都产生了微弱电磁场,样品被整体 加热。再加上辐射与对流,在样品中产生了反向热 梯度,导致从内到外热沉积反应。特别是在脱氢/聚 合反应中形成的自由基有顺磁性,容易被带电纤维 所吸引,能快速地进行表面动力学反应,使沉积速 率明显加快。使用这种技术只需几个小时就能制备 出通常4-5个月才能制备的材料,而价格仅是目前均 热法的1/3 – 1/4 。
碳纤维预制成型体经过浸渍树脂或沥青等浸渍剂后, 经预固化,再经碳化后获得的基体碳。浸渍剂选择 原则如下; (1)碳化率(焦化率):碳化率高的浸渍剂可提 高效率,减少浸渍次数。 (2)粘度:要求粘度适当,易于浸渍剂浸渍到预 制成型体中。 (3)热解碳化时能形成张开型的裂缝和空隙,以 利于多次浸渍,形成致密的碳/碳复合材料。 (4)碳化后收缩不会破坏预制成型体的结构和形 状。 (5)形成的显微结构有利于碳/碳复合材料的性能。
无机复合材料第六章——碳碳复合材料
8
1、力学性能——与碳材料的对比
C/C复合材料的力学性能在室温和高温下都明显高于 基体的碳材料。
9
2、摩擦性能
碳/碳的高温摩擦性能稳定;刹车时吸收动能高,能 显著提高飞机制动性能;密度低,并能显著减轻飞机刹 车装置的重量。
◆ 摩擦系数:0.2-0.3
高温下稳定。飞机制动过程中,刹车盘整体温度达500℃,而表面最 高温度可达1500℃以上。
从第四次循环浸渍碳化开始,则每次复合材料的密度增 加相对较慢。
为了减少浸渍-碳化次数,提高浸渍碳化效率和改善复 合材料的性能,一般采用真空压力浸渍工艺,形成了压 力浸渍碳化工艺(PIC, Pressure Impregnation Carbonization)。并且在沥青液态浸渍-碳化工艺中得 到应用。
预制体; 高温和HIP下,沥青中挥发分进
行碳化,同时防止沥青流出预 制体; HIPIC一次需1~3天。
54
4、CVD/CVI工艺
沥青、树脂浸渍-碳化与CVD裂解碳填充孔隙的区别
55
C/C复合材料CVD/CVI工艺的种类主要有:
等温 (Isothermal)法; 压力梯度 (Pressure gradient)法; 温度梯度(Thrmal gradient)法; 化学液气相沉积法(Chemical Liquid Vapour
49
PIC工艺与在1大气压下浸渍-碳化工艺 对复合材料密度影响
50
◆ 沥青液态浸渍-碳化工艺
沥青液态浸渍-碳化工艺与树脂有相似之处,但根据 沥青的特性,也有不同之处。主要是沥青软化点低;熔化 后粘度低易浸渍;含有较多的低分子量芳香族分子可以在 压力下热解转化为碳;碳化后基体沥青碳易石墨化等。
CC复合材料
三 制备工艺
制备碳/碳复合材料主要步骤为: 预制体成型 → 致密化处理 → 最终高温热处理
3.1
预制体成型 • 在进行预制体成型前,根据所设计复合 材料的应用和工作环境来选择纤维种类和 编织方式.例如 ,对重要的结构选用高强度、 高模量纤维.对要求导热系数低的则选用低 模量炭纤维 ,如粘胶基炭纤维 成型方法为用短纤维增强: (1) 压滤法; (2) 喷涂法; (3) 热压法; (4) 浇注法 用连续长纤维增强: (1) 预浸布层压、 铺压、 缠绕等做成层压板、 回转体和异 形薄壁结构; (2) 编织技术.
3.4
常规化学气相沉积方工艺(等温法)仍有许多不足: 由于受到气相扩散速率和表面反应速率的制约 , 在一个较窄的工艺条件下进行.因此 ,对沉积炭显 微组织的选择余地有限 ,得到的通常为光滑层(S L)组织 ,要想提高沉积炭温度 ,以得到粗糙层(RL) 炭 ,则又易形成表面的气孔堵死 ,以及表层和里层 的密 度差提高[6 ].同时 ,等温 CVI制备碳/碳复合材料 周期长(约 1 000 - 1 500 h) 、 原料气利用率低 ( < 5 %) ,需要数次石墨化和机加工 ,需用大量高 能耗的贵重设备 ,成本很高
CC复合材料
目录
• 定义 • 性能 • 制备工艺 • 发展前景及用途
一 定义
•
碳/碳复合材料是复合材料 的一种 ,它是以碳为基体 ,由 碳纤维或其制品(碳纤维的高 强度 ,具有良好的机械性能、 耐 热性、 耐腐蚀性、 磨擦减振特 性及热、电传导特性等特点.而 且 ,其质轻 ,比强度和比弹性模 量都很高 ,更重要的是这种材料 随着温度的升高(可达2 200 ℃) 其强度不降低 ,甚至比室温条件 下还高。
(7) 制作热压模具和超塑性加工模具.在陶瓷和粉未冶金 生产中采用碳/碳复合材料制作热压模 具 ,可减少模具厚度 ,缩短加热周期 ,节约能源和提高产 量;用碳/碳复合材料制作钛合金超塑性加工模 具 ,因其低膨胀性和钛合金的相容性 ,可提高成型效率 , 并减少成型时钛合金的折叠缺陷. (8) 制作加热元件.与传统的石墨发热体强度低、 脆 ,加工与运输困难相比 ,碳/碳复合材料的强度 高 ,韧性好 ,可减少发热体体积 ,扩大工作区. (9) 作高温真空炉内衬材料 ,以及化工防腐蚀管道 及零部件等
CC复合材料与金属连接及接头力学性能测试
©
性 ,防止钎料熔化渗入 ; 然后将钎料以焊膏的形式涂
在复合材料的表面 ,在真空条件下加热 至 980℃,保
温 5 m in,所得接头强度远远高于母材强度 。值得指
出的是 ,这种钎料还适合连接低密度 的 C /C 复合材
料与钢或者陶瓷。
人们发现 , Ti、Zr等过渡元素 ,具有很强的化学活 泼性 ,在液态时能与碳元素 发生反应 [ 3] 。添加少许
通过焊前对cc复合材料表面改性即在cc复合材料表面扩渗沉积一3m的金属梯度层ni使它们之间形成扩散层再沉积一层mpa的真空下用银基或者镍基钎料填充焊缝只需在800850的温度保温15min就可以得到剪切强度为48mpa的钎焊接头相对于镍基或者钛基钎料来说银基钎料具有更低的钎焊温度
C /C复 合 材 料 与 金 属 连 接 及 接 头 力 学 性 能 测 试
张 雷 曲文卿 庄鸿寿
(北京航空航天大学机械工程及自动化学院 ,北京 100083)
文 摘 对 C / C复合材料与铜合金的真空钎焊方法进行了介绍 ,着重列出了近年来出现的活性钎料及相 关的焊接工艺参数 ,并将 ⅥB 元素对 C / C复合材料表面的改性效果作了对照 ; 介绍了银基活性钎料连接 C / C 复合材料与钛合金技术 ,对该过程钎料和母材相互扩散机理做了描述 ;概述了 C /C 复合材料和铝合金、镍和不 锈钢金属的粘结及钎焊工艺 ,列出了 C / C复合材料与金属接头的剪切强度 、冲击热应力等的测试方法。
活性元素制成 的活性钎料 , 可以直接 润湿 C /C 复合
材料的表面并完成与其他金属的连接 。采用活性金
属钎料钎焊需要在真空炉或高纯度惰性气氛中进行 ,
通常一次即可完成钎焊连接 。
近年来 ,银基 、铜基活性钎料已经开始商业生产 ,
- 1、下载文档前请自行甄别文档内容的完整性,平台不提供额外的编辑、内容补充、找答案等附加服务。
- 2、"仅部分预览"的文档,不可在线预览部分如存在完整性等问题,可反馈申请退款(可完整预览的文档不适用该条件!)。
- 3、如文档侵犯您的权益,请联系客服反馈,我们会尽快为您处理(人工客服工作时间:9:00-18:30)。
C/C复合材料性能参数
C/C热场材料与石墨热场材料性能对比
C/C复合材料具有质量轻、损伤容限高、强度高等突出特点,用作热场与石墨产品比较,具有以下突出优点:
(1) C/C复合材料用作热场产品,大幅度延长产品使用寿命减少更换部件的次
数,从而提高设备的利用率,减少维修成本。
(2) 用作拉晶砖的坩埚时,由于石英坩埚对石墨坩埚产生较大的膨胀应力作用,石墨坩埚只好做成多瓣,或在坩埚上开热膨胀槽.而使用C/C复合材料热场产品由于不用开热膨胀槽,可以做成一个整体,可以在石英坩埚内获得更均匀的热场,可以提高成品率,而且可以避免“漏硅”事故造成的损失,据统计一次“漏硅”事故造成的设备、材料方面的损失超过10万元。
(3) C/C复合材料用作热场产品时,现有设备具有固定的,而由于C/C复台材料具有优异的性能,与石墨产品相比,可以做得更薄,从而可以利用现有设备生产尺寸更长、更大直径的产品,可节约大量新设备投资费用。
(4) 在拉制大直径的产品时,石墨热场产品成型困难,如果要制造超大大直径的石墨热场零部件其制造成本加工成本都很高,而由于C/C复合材料具有优异的性能,目前国外拉制大直径的产品时,较多地采用了C/C复合材料热场产品(5) 石墨热场产品在反复高温热震条件下易产生裂纹,微裂纹的存在改变了其热传导性能,使加热时石墨加热器的功率与硅熔体的温度场发生变化,将影响拉晶的效率和拉出的晶体的质量和品质。
而使用C/C复合材料热场产品可以克服这个缺点。
(6) C/C复合材料用作热场产品时,导热系数比石墨热场产品低很多,用做隔热保温材料隔热保温效果好,可以节约大量的电能,节省大量的电费开支,可有效的降低单(多)晶硅生产厂家的生产成本,随着全球能源供应的紧张,单(多)晶硅生产作为高耗能行业,能源消耗的降低具有较大的经济和社会意义。