汽车变截面钢板弹簧的设计计算
汽车钢板弹簧设计计算1

#DIV/0! #DIV/0! #DIV/0!! #DIV/0! #DIV/0! #DIV/0!
#DIV/0! #DIV/0! #DIV/0! #DIV/0! #DIV/0! 0 #DIV/0! #DIV/0! #DIV/0! #DIV/0!
1
14)(1-μi-1)↑3Ki 12)*13)
15)Bi 14)+1 16)ξi=Bi-αi-2*Ci-2 n=6,ξn=ξ6
2.钢板弹簧总成刚 度C=6EIn/ln↑3/ξ
n (N/mm)
1)刚度差(C实-C 理)/C实*100 (%) 2)钢板弹簧总成挠 度fc=2*Pn/C (mm) 3)钢板弹簧的固有 频率N (Hz)=16/fc ↑0.5 (1.3~2.3Hz)
0
#DIV/0! #DIV/0! #DIV/0! #DIV/0! #DIV/0! #DIV/0! #DIV/0! 0 #DIV/0! #DIV/0! #DIV/0! #DIV/0! #DIV/0! #DIV/0!
0 -0.1889 -0.13115 #DIV/0! #DIV/0! #DIV/0! #DIV/0!
47 #DIV/0!
#DIV/0! #DIV/0! #DIV/0! #DIV/0! #DIV/0! #DIV/0! #DIV/0! #DIV/0! #DIV/0! #DIV/0! #DIV/0! #DIV/0! #DIV/0! #DIV/0! #DIV/0! #DIV/0!
45
#DIV/0! ###### ###### #DIV/0!
2.065591 #DIV/0! #DIV/0! #DIV/0! #DIV/0!
#DIV/0! #DIV/0! #DIV/0!
4.A(L/2,(n0-1)h↑ 3),B(S/2,nh↑3)两 点直线方程: (x-x1)/(x1x2)=(y-y1)/ (y1-y2) 即:x=ay+b x1=L/2 x2=S/2 a=(x1-x2)/(y1y2) b=x1-(x1-x2) *y1/(y1-y2) 5.求各片的弦长Li (xi)圆整为尾数为 1)最短片L1 L2 (单边) L3 L4 L5 L6 L7 L8 L9 L10 L11 L12 L13 L14 L15 n=6,Ln=L6
少片变截面钢板弹簧的设计计算

少片变截面钢板弹簧的设计计算钢板弹簧是一种常见的机械弹簧,在各种机械和设备中得到广泛应用。
它由在轴线方向上并排排列的一系列弯曲的钢板组成,呈螺旋状。
当外力作用于弹簧时,它会发生形变,具有很好的弹性回复能力,是一种具有重要机械性能的弹簧。
一、设计计算1、弹簧基本要素弹簧基本要素包括钢带材料、外直径、内直径、圈数、导程、自由长度和加工工艺。
其中材料是决定弹簧机械性能的关键要素。
通常钢板弹簧采用碳素钢、合金钢等材料,其弹性模量会随材料强度的提高而增大。
2、弹簧设计弹簧的设计需要考虑弹簧的工作条件,计算外力的大小、方向、作用点等,从而确定弹簧材料的选择、外径、圈数等要素。
弹簧设计需要考虑以下几个方面:(1)弹簧的工作负荷:根据机械设备的工作条件和要求确定弹簧承受的最大负荷,以此作为设计的起点。
(2)弹簧的外径和内径:根据弹簧材料、工作负荷和工作环境等要素来确定弹簧的外径和内径大小。
(3)弹簧的圈数和导程:弹簧的圈数和导程直接决定了其刚度和变形量,需要根据实际需求来设计,避免过强或过松。
(4)弹簧自由长度:弹簧自由长度也会影响到其机械性能,需要根据实际工作环境来确定。
二、样例下面以一种常见的钢板弹簧为例,介绍其设计和计算过程。
1、材料选择假设需要设计一种碳素钢的钢板弹簧,采用SWO-A钢带材,其具有以下机械性能:屈服强度:235MPa弹性模量:210GPa泊松比:0.3材料密度:7.85g/cm³2、外径和内径的确定假设弹簧的最大工作负荷为500N,弹簧碳素钢钢带的工作应力取90%时,最大弹簧应变量ρs应该小于σ/2E,即(υ-Dw)/Dw≥0.08。
可根据此公式,确定外径Dw=20mm。
根据设计要求,弹簧的圈数为8,导程为3mm。
当弹簧材料确定且弹簧固定长度生成后,利用弹簧方程(Fs=kρs)推导,得到弹簧直径Di=17.9mm。
3、根据内径、外径和圈数确定性能参数内直径ID=Di-2t,弹簧导程l0=π(Di+Dw)/2,自由长度L0=l0*(n-1)+2*ra+ra-ra*υ/Dw。
钢板弹簧设计说明书
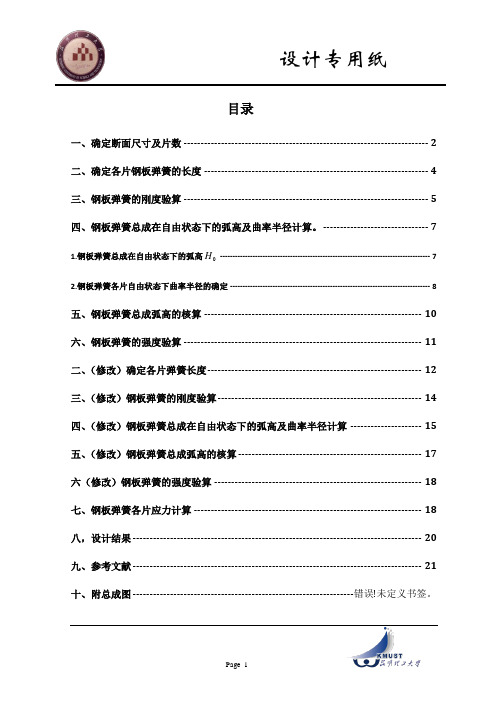
目录一、确定断面尺寸及片数 ------------------------------------------------------------------------ 2二、确定各片钢板弹簧的长度 ------------------------------------------------------------------ 4三、钢板弹簧的刚度验算 ------------------------------------------------------------------------ 5四、钢板弹簧总成在自由状态下的弧高及曲率半径计算。
------------------------------- 7H ------------------------------------------------------------------------------------ 71.钢板弹簧总成在自由状态下的弧高02.钢板弹簧各片自由状态下曲率半径的确定 -------------------------------------------------------------------------------- 8五、钢板弹簧总成弧高的核算 ---------------------------------------------------------------- 10六、钢板弹簧的强度验算 ---------------------------------------------------------------------- 11二、(修改)确定各片弹簧长度--------------------------------------------------------------- 12三、(修改)钢板弹簧的刚度验算 ------------------------------------------------------------ 14四、(修改)钢板弹簧总成在自由状态下的弧高及曲率半径计算 --------------------- 15五、(修改)钢板弹簧总成弧高的核算 ------------------------------------------------------ 17六(修改)钢板弹簧的强度验算 ------------------------------------------------------------- 18七、钢板弹簧各片应力计算 ------------------------------------------------------------------- 18八,设计结果 ------------------------------------------------------------------------------------- 20九、参考文献 ------------------------------------------------------------------------------------- 21十、附总成图 ----------------------------------------------------------------- 错误!未定义书签。
某微车的少片变截面钢板弹簧结构设计分析与验证

( ) = n d [ 1 …t (
d f l 、 用 负 号 ) 由式 ( 9 ) 乘 n减 式 ( 1 0 )得
d ( d , J 、 )= —
) ] ( 用 正 号 ,
( 1 0 )
( 上接第 6 6页 )
6 结 论
( 1 1 )
由 上述 结果 对 比可 知 ,刚 度 、强 度 的结 果 均 比较 接 近 ,台 架耐 久 试 验 也 满 足 了 8万 次 断 裂 的标 准 要 求 。耐 久 性 反 映 了 强
( 2 )辅具结构简单 ,一般 中小型机 械厂都可 以自制 ; ( 3 )辅具可 实现车 间现 场 随 时测量 ,准确 可靠 ,轻巧 耐
用 ,完 全 满 足 生产 现 场 测 量 要 求。
d ( d ) = , n 一 d [ 1 + c 。 t (
d , J 、 用负号 ) 的尺寸 m : ,则
明 了该 设 计 方法 的可 行 性 。
文中主要利用材料力学的简单基础公式对板 簧进行理论计 式 ( 1 2 ) 中 :A d ( △ d 』 J 、 )为被测 圆锥大 、小端直径 ;
n d ( d )为大 ( 小 ) 标 准 圆柱 直径 。
算 ,并未涉及经验之类的系数 ,相对很多其他计算 方法较 为简 洁 明了。并通过 C A E分析验证与台架验证 ,该板簧的理论计算 得 以认证。这一套设计开发流程 ,比较完善地将理论 与实 际结
式 ( 1 1 ) 中 :n可 以取 为 任 意 值 ,在 此 ,笔 者 取 大 、 小标 准 圆 柱 直 径 之 比 ,即 n= n d / d ,代 入式 ( 4) 后 可 得
d ( d , j 、 )= 。 ( 1 2 )
汽车变截面钢板弹簧的设计计算

汽车变截面钢板弹簧的设计计算东风汽车工程研究院 陈耀明 2006年5月前 言少片变截面钢板弹簧在我国已有多年的制造和使用经验,特别是大、中型客车,采用者相当广泛。
然而,涉及变截面簧的设计计算方法,虽然二十几年前悬架专委会曾做过一些介绍,但资料零散、重复、不完整,尤其是比较常用的加强型变截面簧,资料反而欠缺。
撰写本文的目的,就是为悬架设计者提供变截面簧的比较完整的设计计算资料,主要是刚度计算公式和应力分布计算方法。
变截面簧轮廓线包括梯形和抛物线形两大类,每类又含有根部、端部加厚,或只有根部加厚,或都不加厚等几种变型。
这样,可以说几乎所有的变截面簧轮廓线都可在本文找到计算公式。
此外,本文还介绍了各种轮廓线的选型原则以及若干设计经验等,可供设计人员参考。
附录中列出已有资料中的一些计算公式,并证明了它们和本文公式的一致性。
本文的式(1)~(3)引自日本资料“自动车用重型钢板弹簧”,其它公式(6)~(15)是笔者近期重新推导出来的。
当然,有一些和过去推导出来的公式完全一致。
一、 纵截面为梯形的变截面弹簧这种弹簧的轧锥部分(3l ~4l 段)为梯形,而根部和端部都将厚度增大,称为加强型变截面簧,见图1。
图1为四分之一椭圆钢板弹簧,其刚度计算公式为:654321αααααα+++++=EK ----------------(1)若对称地扩展成为半椭圆钢板弹簧,其总刚度为:6543212αααααα+++++=EK ----------------(2)若弹簧由若干等长、相同轮廓线的叠片所组成,则其合成的总成刚度为:6543212αααααα+++++=nEK ----------------(3)式中 )/(10058.225mm N E ×=为弹性模数n 弹簧片数,单片弹簧1=n313114bt l =α⎥⎦⎤⎢⎣⎡++−+−+−−=1221112121221122212211132ln 223)(22212t t t Al t t l A t Al t t l A t Al t bA α )(43233323l l bt −=α ⎥⎦⎤⎢⎣⎡++−+−+−−=2322322223233223232223234ln 223)(22212t t t Bl t t l B t Bl t t l B t Bl t bB α ⎥⎦⎤⎢⎣⎡++−+−+−−=3423432324244324242234335ln 223)(22212t t t Cl t t l C t Cl t t l C t Cl t bC α )(43536346l l bt −=α而 1212l l t t A −−=3423l l t t B −−=4534l l t t C −−=其中 b 弹簧宽度实际应用中,有些弹簧的轮廓线有所简化,见图2,其刚度计算式也有所变化: 1、增厚转折点急剧变化,2型。
汽车变截面钢板弹簧的优化设计

′ Pmax = max{P 1, P 2} = m •
则制动时: σ t max =
G l + ϕCC • 2 2l
(17) (18)
Pmaxl m′G (l + ϕ CC ) = W0 4W0 Pmax l Fx m ′G (l + ϕC C ) m ' Gϕ + = + W0 bh1 4W0 bh1 L2 + ϕ h g L2
P1 FX
驱动时: σ t max =
(19)
式中:m/为轴荷再分配系数,制动时: m ′ = Ga 为汽车总载荷,N;hg 为汽车重心高度, mm;La 为轴距,mm;L2 为汽车后轴中心线 至重心的距离,mm;G 为轴荷,N;l 为钢 板弹簧的主片半长 l=l1,mm;Cc 为弹簧固定 点至路面的距离,mm; ϕ 为路面附着系数, 取 ϕ =0.8;W0 为弹簧的总截面系数:
设Hale Waihona Puke 技术汽车变截面钢板弹簧的优化设计
赵 云 郑财权
(福州大学机械工程学院) 摘 要:本文对各片不等长变截面钢板弹簧进行了研究,按质量最小为目标函数建立了钢板弹簧优化设计的数学模型,
并利用 Visual Basic6.0 高级语言采用复合形法开发了优化计算程序。通过实例设计计算表明,用该优化计算程序进行设 计,可使汽车钢板弹簧的质量比原设计减少 33.3~43.2%。 关键词:变截面钢板弹簧 优化 设计
C=
η
(1) BB
2ξ ,N/mm (1) P2 / P1 − η BA
(5)
式中:ξ为修正系数,由于梁弯曲理论是基于等截面梁建立的,用它计算变截面梁的变形,其结果是 近似的;另一方面,实际生产的弹簧其截面形状并不是理想的矩形。因此计算总成刚度时引入一个修 正系数ξ,经验取ξ= 0.9~0.92;η ij(k) 为变形系数,mm/N,表示第 k 片由于 j 处单位作用力所产生 的 I 处的挠度;Pk 为片端力,N。 由梁弯曲理论,可推得变形系数 η ij(k)为:
汽车钢板弹簧的设计
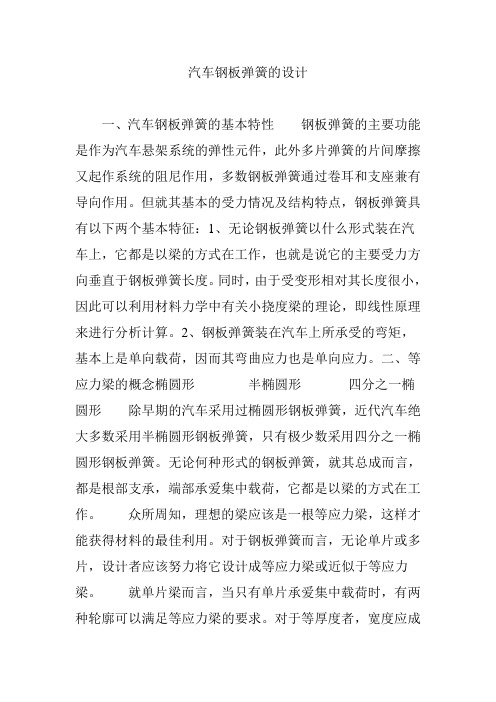
汽车钢板弹簧的设计一、汽车钢板弹簧的基本特性钢板弹簧的主要功能是作为汽车悬架系统的弹性元件,此外多片弹簧的片间摩擦又起作系统的阻尼作用,多数钢板弹簧通过卷耳和支座兼有导向作用。
但就其基本的受力情况及结构特点,钢板弹簧具有以下两个基本特征:1、无论钢板弹簧以什么形式装在汽车上,它都是以梁的方式在工作,也就是说它的主要受力方向垂直于钢板弹簧长度。
同时,由于受变形相对其长度很小,因此可以利用材料力学中有关小挠度梁的理论,即线性原理来进行分析计算。
2、钢板弹簧装在汽车上所承受的弯矩,基本上是单向载荷,因而其弯曲应力也是单向应力。
二、等应力梁的概念椭圆形半椭圆形四分之一椭圆形除早期的汽车采用过椭圆形钢板弹簧,近代汽车绝大多数采用半椭圆形钢板弹簧,只有极少数采用四分之一椭圆形钢板弹簧。
无论何种形式的钢板弹簧,就其总成而言,都是根部支承,端部承爱集中载荷,它都是以梁的方式在工作。
众所周知,理想的梁应该是一根等应力梁,这样才能获得材料的最佳利用。
对于钢板弹簧而言,无论单片或多片,设计者应该努力将它设计成等应力梁或近似于等应力梁。
就单片梁而言,当只有单片承爱集中载荷时,有两种轮廓可以满足等应力梁的要求。
对于等厚度者,宽度应成三角形,对于等宽度者,厚度为抛物线形状。
当然,从理论上讲,只要截面系数沿片长方向与弯矩成比例变化,都可以成为等应力梁。
然而汽车上几乎没有采用同时变厚又变宽的弹簧。
上述轮廓线只是对弯曲应力而言,实际上钢板弹簧端部受剪切强度的要求以及卷耳的存在,第一种轮廓只能是在三角形端部加上等宽的矩形或整个宽度成为梯形,而第二种轮廓只能是抛物线端部接上一段等厚度的矩形或厚度按梯形变化的梁。
为了简化轧制工艺,对于等宽度者,可用梯形代替抛物线。
此外,根部也设计成为平直的,便于与支承座贴合,也就是说,或者由梯形和根部、端部为矩形的三段直线构成。
所以,在实际应用上,只能把弹簧设计成为近似的等应力梁。
由于结构上的原因,没有人在汽车上采用等厚度变宽度的单片钢板弹簧,但等宽度变厚度的单片钢板弹簧早就得到实际的应用。
汽车钢板弹簧的性能计算和试验

汽车钢板弹簧的性能计算和试验首先,汽车钢板弹簧的性能主要包括以下几个方面。
1.抗压性能:汽车钢板弹簧需要承受车身的重力和不同路况下的载荷,因此需要具备良好的抗压性能。
这主要取决于材料的强度和设计的结构形式。
2.弹性模量:汽车钢板弹簧必须具备足够的弹性,以便在受到压力后能够恢复原状,保持悬挂系统的正常工作状态。
3.疲劳寿命:汽车钢板弹簧在长期使用的过程中,需要承受反复加载和卸载的作用,容易发生疲劳断裂。
因此,提高弹簧的疲劳寿命是非常重要的,需要选择耐疲劳性能好的材料和合理的结构设计。
其次,汽车钢板弹簧的计算主要包括以下几个方面。
1.材料选择:根据汽车钢板弹簧所需的强度和弹性模量,选择合适的材料。
常用的材料有碳素钢和合金钢等。
2.结构设计:根据汽车的荷载情况和悬挂系统的要求,设计合适的弹簧结构。
包括弹簧片的长度、宽度、厚度以及弹簧片的叠放方式等。
3.刚度计算:根据汽车的质量、弹簧的刚度系数以及悬挂系统的要求,计算出合适的弹簧刚度。
刚度计算可通过弹簧公式和有限元分析等方法进行。
最后,汽车钢板弹簧的试验主要包括以下几个方面。
1.负荷试验:对汽车钢板弹簧进行加荷试验,测试其承受负荷的能力。
这通常包括静态负荷试验和动态负荷试验两种。
2.疲劳试验:通过反复加载和卸载的试验,测试汽车钢板弹簧的疲劳寿命。
疲劳试验通常包括弯曲疲劳试验和循环疲劳试验。
3.刚度试验:通过施加不同荷载,测量弹簧的变形量和对应的载荷,计算出弹簧的刚度系数。
在试验过程中,需要遵循相关的试验标准和方法,确保试验结果的准确性和可靠性。
综上所述,汽车钢板弹簧是汽车悬挂系统中不可或缺的元件,其性能、计算和试验的合理设计和有效实施,对于保证汽车悬挂系统的稳定性、舒适性和安全性具有重要的意义。
- 1、下载文档前请自行甄别文档内容的完整性,平台不提供额外的编辑、内容补充、找答案等附加服务。
- 2、"仅部分预览"的文档,不可在线预览部分如存在完整性等问题,可反馈申请退款(可完整预览的文档不适用该条件!)。
- 3、如文档侵犯您的权益,请联系客服反馈,我们会尽快为您处理(人工客服工作时间:9:00-18:30)。
由于前簧往往比较薄,制动力又很大,端部加厚措施是必要的。
8
4、 有效长度的选取 由于变截面簧根部很厚,U 形螺栓相对单薄,特别是加垫之后,实际上是夹不死它。也就是说,U 形
螺栓跨距内的那段无效长度往往是有效的。因此,设计时要根据根部厚度及夹紧结构,来确定无效长度系 数。
−
t2 )
l2 ≤ x ≤ l3 , t(x) = t2 = const
l3 ≤ x ≤ l4
,
t(x)
=
t2
+
x ( l4
− l3 − l3
)(t3
−
t2 )
l4 ≤ x ≤ l5
,
t(x)
=
t3
+
x ( l5
− l4 − l4
)(t 4
−
t3 )
l5 ≤ x ≤ l6 , t(x) = t4 = const
--------------(10)
k′
= η1
⋅k
=1+
(2η1
− 1)λ32
−
2η1 (λ1
3
⋅ λ2 ) 2
+ η1 ⋅η η2
⋅ λ13
若对称地扩展成为半椭圆钢板弹簧,其总刚度为:
-----(11)
K = 6EI3 k ⋅l3
--------------(12)
若弹簧由若干等长、相同轮廓线的叠片所组成,则其合成的总成刚度为:
2、 没有加厚,为一般轮廓断面,3 型。
这时, l1 = l2 = 0 ,α1 = 0 ;
t1 = t2 ,α 2 = 0 ;
l4 = l5 ,t3 = t4 , α5 = 0 。
将α 3 ,α 4 ,α 6 代入式(1)~(3)求解。
3、 端部没有平直段(非卷耳端、短轧锥),4 型。
这时, l1 = l2 = 0 ,α1 = 0 ;
3
W (x) 计算断面的断面系数
n 弹簧片数
断面系数为:
W (x) = b ⋅ t(x)2 6
----------------(5)
式中 t(x) 沿片长变化的厚度
b 弹簧宽度
当 0 ≤ x ≤ l1 , t(x) = t1 = const
l1 ≤ x ≤ l2
,
t(x)
=
t2
+
( l2 l2
−x − l1 )(t1
同样,化简后可得
k = 1 + λ32 −η ⋅ λ13
=
1
+
λ32
(1
−
1 η
)
--------------(15)
对于抛物线的变截面簧,仍然可以采用式(4)、(5)来计算沿片长的应力分布,只是在抛物线区 段,厚度的变化规律有所不同,即:
当 0 ≤ x ≤ l1 , t(x) = t1 ( 或 t2 ) = const
优质的材料和轧制工艺,使表面缺陷减少或减轻,也就可以选取抛物线形,让较多材料承受较高 应力,以减轻重量。反之,材质与工艺较差者,宜选用梯形轮廓线。 2、 根部加强
对于板簧根部较厚(20mm 以上),且 U 形螺栓夹紧装置不是特别强,尤其是根部加有软垫者,应该采 用加厚措施。否则,由于夹不死,最大弹簧应力恰好处在中心孔位置上。加上该孔有应力集中,其结果是 在中心孔处早期断裂。除了中心孔要倒角以减小应力集中外,加厚并取消软垫或改为硬垫是最有效措施。 简单说,大中型客、货车的变截面簧根部应加厚。 3、 端部加强
附录中列出已有资料中的一些计算公式,并证明了它们和本文公式的一致性。本文的式(1)~(3) 引自日本资料“自动车用重型钢板弹簧”,其它公式(6)~(15)是笔者近期重新推导出来的。当然,有 一些和过去推导出来的公式完全一致。 一、 纵截面为梯形的变截面弹簧
这种弹簧的轧锥部分( l3 ~ l4 段)为梯形,而根部和端部都将厚度增大,称为加强型变截面簧,见
=
t0
(
x l
)
1 2
=
t2
(
x l1
)
1 2
图中所标尺寸定义如下:
---------------(6)
l1 端部加强(平直)段长度
t1 端部加强段厚度
t2 端部平直段与抛物线交点处的厚度
l2 根部加强(平直)段距端点长度
t4 根部加强段厚度
4
t3 根部平直段与抛物线交点处的厚度 l 端点至根部总长度
所以,选用什么样的轮廓线,取决于两个因素: (1) 最大应力处在什么部位。
如果最大应力位于根部(根部不加厚、加软垫或夹紧装置不是很强),那么轧锥部分可选用抛物 线形,以获得较好的材料利用率,且可降低刚度。这种选择多数用在轿车或轻型车的悬架上。
相反,大中型客车或货车,往往根部要加厚,最大应力点不在根部,而是在轧锥段。这时选用梯 形轮廓较合适,使最大应力局限在极值点的小区域,碰上缺陷的概率较低,使寿命提高。 (2) 弹簧材料和轧制工艺的优劣。
请注意,此处所取惯性矩不是根部惯性矩,而是平直段与抛物线交点处的断面惯性矩。这样选取只
是为了方便与其它轮廓线的计算公式对比。
当然,若算式(7)要选取根部惯性矩来计算也是可以的,但挠度系数要相应改变。
Θ
I3
=
I4 η1
,代入式(7),得
K = 3EI 4 = 3EI 4 η1 ⋅ k ⋅ l 3 k′ ⋅ l 3
对于 2 型弹簧,在根部和端部厚度有突变,该位置之应力也有突变。
二、 纵截面为抛物线形状的变截面弹簧
这种弹簧的轧锥部分( l1 ~ l2 )为抛物线形状,该抛物线的顶点在端点(集中载荷作用点),而根部
和端部都将厚度增大,以满足结构强度的要求,见图 3。该抛物线函数为:
t(x)
=
t3
(
x l2
)
1 2
众所周知,在抛物线区段,应力分布是均等的,即为等应力的。从理论上讲,这种轮廓线似乎是最 理想的,其材料利用率是最高的。然而,从另一方面看,亦即从“比例尺效应”的理论看,等应力分布并 不一定是理想的设计。
大家知道,材料疲劳损伤、断裂都是从表面缺陷引发的,而由于材质或工艺上的原因,材料表面总 有缺陷存在。如果结构上高应力区所占的比例大,缺陷处在高应力点的概率就高,因此该结构就会出现早 期损坏,即寿命降低。相反,如果高应力区所占比例小,缺陷碰到高应力点的概率就低得多,该结构的寿 命就会高得多。这就是所谓的“比例尺效应”。
−
2(λ1
3
⋅ λ2 ) 2
+η
⋅ λ13
Θη = (t3 )3
,又 t2
=
(
l1
)
1 2
=
(
λ1
)
1 2
t2
t3 l2
λ2
∴η
=
( λ2
)
3 2
λ1
3
,η ⋅ λ13 = (λ1 ⋅ λ2 ) 2
且η 2 = ( λ2 )3 代入上式,化简后得 λ1
6
k
=
1 η1
(1 −
λ32
)
+
2λ32
−η
⋅ λ13
图 1。图 1 为四分之一椭圆钢板弹簧,其刚度计算公式为:
K=
E
α1 +α2 +α3 +α4 +α5 +α6
----------------(1)
若对称地扩展成为半椭圆钢板弹簧,其总刚度为:
1
K=
2E
α1 + α2 +α3 +α4 + α5 + α6
----------------(2)
若弹簧由若干等长、相同轮廓线的叠片所组成,则其合成的总成刚度为:
根据我们经验,对于总质量达 15 吨的大中型客、货车,其板簧无效长度系数甚至可取零,即全长有 效。对于中、轻型车,可取 0.2 左右,而不像多片簧取 0.4~0.5。
当然,应在试制后对样品进行测试,再来核对该系数。 5、 横截面的断面参数计算
变截面簧的理论分析和公式计算,都是将横截面当为矩形的。实际上,弹簧片轧制时侧边都自然地 形成圆角。所以按矩形断面来计算惯性矩、断面系数和断面积,结果都偏大。即,算出的刚度偏大,应力 偏小。可以有两种方法进行修正: (1) 计算断面参数时考虑圆角的影响。例如,认定圆角半径等于片厚,则:
2(t1 − Al1 ) t2
+
A 2 l12
− 3t12 + 2t1 Al1 2t12
+
ln
t2 t1
⎤ ⎥ ⎦
α3
=
4
bt
3 2
(l33
−
l
3 2
)
α4
=
12 bB 3
⎡ ⎢
2t
2
Bl3
⎣
−
t
2 2
2t
2 3
− B 2l32
+
2(t 2
− Bl3 ) t3
+
B 2l32
−
3t
2 2
+
2t2 Bl3
t1 = t2 ,α 2 = 0 ;
l3 = 0 ,α3 = 0 ;
l4 = l5 ,t3 = t4 ,α5 = 0 。
将α 4 ,α 6 代入式(1)~(3)求解。
从图 1 可见,沿片长的应力分布为:
σ = P⋅x n ⋅W (x)
---------------(4)
式中 P 端部负荷 x 端部至计算断面距离
B = t3 − t2 l4 − l3
C = t4 − t3 l5 − l4