催化剂制备方法大全
催化剂的制备方法与成型技术简汇

催化剂的制备方法与成型技术简汇催化剂是一种能够加速化学反应速率的物质。
制备催化剂的方法和成型技术有很多种,下面将对其中的几种方法进行简要介绍。
一、沉积法沉积法是一种将活性物质沉积在惰性载体表面的制备方法。
常用的沉积方法有浸渍法、喷涂法、浸涂法和胶体分散法等。
浸渍法是将载体浸泡在溶液中或涂覆溶液于载体上,使溶液中的活性物质被吸附在载体表面。
喷涂法是将溶液或悬浮液喷雾到载体表面,使活性物质均匀分布在载体上。
浸涂法是将活性物质直接浸涂到载体表面,形成厚度均匀的涂层。
胶体分散法是通过胶体分散剂将活性物质分散在溶剂中,然后将溶剂蒸发使活性物质沉积在载体表面。
二、溶胶凝胶法溶胶凝胶法是一种利用溶胶凝胶化学反应将活性物质沉淀在载体表面的制备方法。
首先将一种或多种金属盐或金属有机化合物溶解在溶剂中,形成溶胶。
然后通过加入沉淀剂、酸性或碱性物质,使溶胶逐渐凝胶化为凝胶。
最后通过热处理或其他方法将凝胶转化为坚硬的复合材料。
三、热分解法热分解法是利用热分解反应将金属有机物转化为金属颗粒的制备方法。
首先将金属有机化合物溶解在溶剂中,然后通过加热使其发生热分解反应,生成金属颗粒。
最后将金属颗粒与载体混合并经过处理,得到催化剂。
四、物理吸附法物理吸附法是利用物理相互作用力将活性物质吸附在载体表面的制备方法。
常见的物理吸附方法有气相吸附、液相吸附和固相吸附等。
气相吸附是将活性物质蒸发或加热生成气体,然后将气体吸附到载体表面。
液相吸附是将活性物质溶解在溶剂中,将溶液浸泡到载体中,使溶质被吸附到载体表面。
固相吸附是将活性物质粉末均匀覆盖在载体表面,通过物理吸附力使活性物质吸附在载体上。
成型技术常用的有压制法、浇注法和喷涂法等。
压制法是将混合活性物质和载体的粉末通过压制设备进行压缩,形成规定形状和尺寸的催化剂块。
浇注法是将活性物质和载体的混合物溶解在溶剂中,然后将溶液倒入制模器中,通过凝固、干燥等过程形成坚硬的催化剂块。
喷涂法是将活性物质和载体的混合物溶解在溶剂中,然后通过喷枪将溶液喷到基底上,形成均匀的涂层。
化学反应中催化剂的制备方法

化学反应中催化剂的制备方法化学反应中催化剂是一个极其重要的组成部分,它能够促进反应速度,降低所需要的温度及压力,降低反应活化能等。
在化学工业中,催化剂是不可或缺的组成部分,对于一些复杂的反应而言,催化剂也是非常关键的。
那么,如何制备催化剂呢?催化剂的制备方法有很多种,不同的反应需要不同的催化剂,因此催化剂的制备方法也各不相同。
下面,我们将从三个方面来讨论催化剂的制备方法。
一、物理化学法制备催化剂物理化学法是制备催化剂的常用方法之一。
它通过改变催化剂的表面结构,改变催化剂的形貌、形态,来达到提高催化剂效率的目的。
比如,采用热处理、电化学方法、物理吸附等方法可以制备出具有均匀孔径、大比表面积等特点的催化剂。
这种方法制备出来的催化剂具有高效、稳定、易于再生等优点,被广泛应用于各种化学反应中。
二、化学合成法制备催化剂化学合成法是一种较为常用的制备催化剂的方法。
它利用化学反应的原理,采用一定的方法及工艺条件来合成催化剂。
这种方法可以得到具有特定功能的催化剂,可以对催化剂进行定制,使其具有其他传统制备方法所不具备的性质。
例如,在金属催化剂的制备中,常常采用化学还原、溶胶-凝胶等方法。
这些方法不仅可以得到纳米尺寸的催化剂,还可以通过添加不同的催化剂过渡金属、调控反应条件等方法得到具有特定性质的催化剂。
三、生物制备法制备催化剂除了物理化学法和化学合成法以外,生物制备法也是一种较为新颖的催化剂制备方法。
生物体内合成各种酶类可以作为参考,设计合成人工酶,以替代催化剂,来实现反应过程的加速,降低催化剂对环境的污染等目的。
生物制备法中,核壳结构的金属纳米粒子成功应用于大量的催化反应中,例如,银纳米颗粒,由于具有特殊的光学性质,已经成功应用于光催化反应中。
生物制备法制备的催化剂,不仅性能稳定,而且具有良好的环保性和可再生性,因此受到越来越多的关注和研究。
总之,催化剂是化学反应中不可或缺的重要组成部分,催化剂的制备方法也是很多的。
催化剂制备的20类38种方法
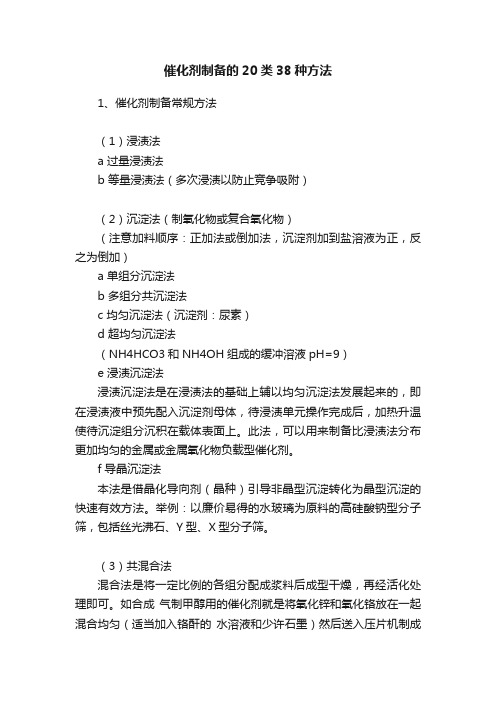
催化剂制备的20类38种方法1、催化剂制备常规方法(1)浸渍法a 过量浸渍法b 等量浸渍法(多次浸渍以防止竞争吸附)(2)沉淀法(制氧化物或复合氧化物)(注意加料顺序:正加法或倒加法,沉淀剂加到盐溶液为正,反之为倒加)a 单组分沉淀法b 多组分共沉淀法c 均匀沉淀法(沉淀剂:尿素)d 超均匀沉淀法(NH4HCO3和NH4OH组成的缓冲溶液pH=9)e 浸渍沉淀法浸渍沉淀法是在浸渍法的基础上辅以均匀沉淀法发展起来的,即在浸渍液中预先配入沉淀剂母体,待浸渍单元操作完成后,加热升温使待沉淀组分沉积在载体表面上。
此法,可以用来制备比浸渍法分布更加均匀的金属或金属氧化物负载型催化剂。
f 导晶沉淀法本法是借晶化导向剂(晶种)引导非晶型沉淀转化为晶型沉淀的快速有效方法。
举例:以廉价易得的水玻璃为原料的高硅酸钠型分子筛,包括丝光沸石、Y型、X型分子筛。
(3)共混合法混合法是将一定比例的各组分配成浆料后成型干燥,再经活化处理即可。
如合成气制甲醇用的催化剂就是将氧化锌和氧化铬放在一起混合均匀(适当加入铬酐的水溶液和少许石墨)然后送入压片机制成圆柱形,在100 oC烘2h即可。
(4)热分解法硝酸盐、碳酸盐、甲酸盐、草酸盐或乙酸盐。
(5)沥滤法制备骨架金属催化剂的方法,Raney 镍、铜、钴、铁等。
(6)热熔融法合成氨催化剂Fe-K2O-Al2O3;用磁铁矿Fe3O4、KNO3和Al2O3高温熔融而得。
(7)电解法用于甲醇氧化脱氢制甲醛的银催化剂,通常用电解法制备。
该法以纯银为阳极和阴极,硝酸银为电解液,在一定电流密度下电解,银粒在阴极析出,经洗涤、干燥和活化后即可使用。
(8)离子交换法NaY制HY(9)滚涂法和喷涂法(10)均相络合催化剂的固载化(11)金属还原法(12)微波法(13)燃烧法(高温自蔓延合成法)常用尿素作为燃烧机(14)共沸蒸馏法通过醇和水的共沸,改变沉淀的形貌、孔结构。
2、催化剂制备新技术(1)溶胶-凝胶法(水溶液Sol-gel法和醇盐Sol-gel法)a 胶体凝胶法(胶溶法)胶体凝胶法是通过金属盐或醇盐完全水解后产生无机水合金属氧化物,水解产物与胶溶剂(酸或碱)作用形成溶胶,这种溶胶转化成凝胶是胶粒聚集在一起构成网络,胶粒间的相互作用力是静电力(包括氢键)和范德华力。
化学催化剂的制备方法

化学催化剂的制备方法化学催化剂在各个领域中都扮演着重要的角色,例如在工业化生产、环境保护和能源转化等方面。
制备高效的催化剂对于提高反应效率和产品选择性至关重要。
本文将介绍几种常见的化学催化剂制备方法。
一、沉积法沉积法是制备催化剂常用的方法之一。
通过在载体上制备沉积层,可以增加催化剂的活性和选择性。
常用的沉积法包括浸渍法和气相沉积法。
浸渍法是将载体浸泡在催化剂溶液中,使催化剂沉积于载体表面。
这种方法具有操作简单、适用范围广的优点。
气相沉积法则是利用气体反应生成沉积物,常见的气相沉积方法有化学气相沉积和物理气相沉积。
二、共沉淀法共沉淀法是通过共沉淀过程制备催化剂。
通常将两个或多个金属盐溶液混合,在适当的条件下发生沉淀反应,生成催化剂。
这种方法可以调控催化剂的成分以及晶体结构,从而影响催化剂的性能。
三、溶胶-凝胶法溶胶-凝胶法是利用溶胶和凝胶的特性,在溶胶阶段形成固体凝胶,并通过热处理生成催化剂。
这种制备方法具有成本低、适用范围广的特点。
四、微乳液法微乳液法是一种在溶胶和凝胶形成前,通过适当的界面活性剂和助剂形成的稳定微乳液中制备催化剂。
这种方法能够控制催化剂的形貌和粒径,从而影响催化剂的活性和选择性。
五、溶胶自组装法溶胶自组装法是一种制备催化剂的较新方法。
通过选择具有亲疏水性的功能分子,在溶液中自组装形成乳液,进而生成催化剂。
这种制备方法能够调控催化剂的孔径和分散度,提高催化剂的性能。
六、共沉淀-还原法共沉淀-还原法是一种通过先共沉淀生成前驱体,再进行还原处理制备催化剂的方法。
这种方法能够调控催化剂的成分和晶体结构,从而影响催化剂的活性和选择性。
在使用以上制备方法时,还可以通过调控反应条件、添加助剂等手段进一步改善催化剂的性能。
此外,还可以采用纳米材料制备方法来制备纳米尺度的催化剂,提高效率和选择性。
总之,化学催化剂的制备方法多种多样,每种方法都有其适用范围和特点。
通过合理选择制备方法和优化制备条件,可以制备出高效、高选择性的催化剂,促进各领域的化学反应。
制备工业催化剂的方法

制备工业催化剂的方法工业催化剂是指用于促进或加速化学反应的物质,广泛应用于许多生产过程中,如炼油、化工、能源等。
制备工业催化剂的方法有很多种,下面将介绍几种常见的制备方法。
一、沉淀法沉淀法是制备工业催化剂的常用方法之一、该方法通过在溶液中加入还原剂使金属离子还原成金属颗粒,然后沉淀得到催化剂。
该方法简单易行,适用于大规模生产。
二、浸渍法浸渍法是指将载体浸入金属溶液中,使金属离子被载体吸附,并通过热处理将金属还原成金属颗粒。
浸渍法可使金属颗粒分散均匀,催化剂活性较高。
三、沉积法沉积法是将金属源溶于溶剂中,然后将溶液喷洒在载体表面,通过烘干和热处理将金属还原成金属颗粒,从而制备催化剂。
该方法适用于制备高活性催化剂。
四、共沉淀法共沉淀法是将金属源和载体溶解在同一溶剂中,通过调节条件使金属沉淀到载体表面,再进行热处理得到催化剂。
共沉淀法制备的催化剂具有高分散性和高活性。
五、焙烧法焙烧法是将金属前驱体或金属盐溶于溶剂中,通过热处理使金属变得稳定且易于使用,然后得到催化剂。
焙烧法制备的催化剂适用于高温条件下的反应。
六、溶胶-凝胶法溶胶-凝胶法是将金属前驱体溶于溶剂中,通过加热使其形成溶胶,然后通过凝胶化得到凝胶,在热处理过程中形成催化剂。
该方法制备的催化剂具有高度分散性和活性。
七、离子交换法离子交换法是将金属离子与载体接触,通过离子交换反应将金属离子固定在载体上,形成催化剂。
离子交换法制备的催化剂具有高度分散性和稳定性。
综上所述,制备工业催化剂的方法有很多种,选择适当的制备方法取决于催化剂的要求和实际应用。
通过不断研究和创新,制备高效、高分散性和高稳定性的工业催化剂对促进化工和工业生产的发展具有重要作用。
催化剂制备方法
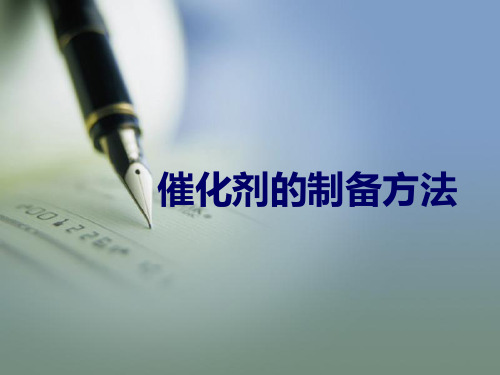
关于浸渍时间的几种情况:
1)活性组分在孔壁的吸附速率快于扩散速率,导致活 性组分吸附在孔口(时间或活性组分浓度不够);
2)浸渍后过滤,静臵,吸附的活性成分重新解吸,通
过再分配实现均匀分布(不立刻干燥); 3)浸渍后不过滤,载体外活性成分不断扩散至孔道内, 实现均匀分布(增加浸渍时间)。
3)浸渍前载体的状态 载体状态不同使组分在载体内部 的分布不均匀,且当浸渍液浓度愈 大,不均匀性愈显著。在同样浓度 的浸渍液条件下,干燥载体内浸渍 组分的分布比湿载体时均匀。
匀 pH稳定 多组分同时 沉淀 沉淀均 匀
(5)pH值 沉淀法中常用碱性物质作沉淀剂,沉 淀物的生成在相当大的程度上受溶液的 pH值得影响
沉淀方法的分离 1)单组分沉淀法 单组份沉淀法是通过沉淀剂与一种特 殊组分溶液作用以制备单一组分沉淀物 的方法。 例:氧化铝的制备 碱法:Al3+ + OH- Al2O3· nH2O 酸法:AlO2- + H3O+ Al2O3· nH2O
浸渍法的影响因素: 1)盐浓度盐、铵盐、有 机酸盐(乙酸盐、乳酸盐)
浸渍液浓度:
催化剂中活性组分含量(以氧化物计)
a
VpC 1 VpC
100%
浸渍液浓度(以氧化物计),g/ml
载体比孔容,ml/g
2)浸渍时间: t=2η/δx x2/r 渗透时间与粘度系数、表面张力、孔径 和粒度有关 在氧化铝上浸渍含Ni化合物
2.分子筛的制备 制备分子筛主要通过混合液成胶、晶化、洗 涤、成型及活化等步骤。以下介绍影响分子筛 制备的几个因素。 (1)硅铝比。不同型号的分子筛有其固定的硅铝 比,如A型为2.0左右。 (2)基数。基数是指反应物料中氧化铝的摩尔浓 度。A型为0.2-0.3mol/L. (3)碱度。指晶化过程中,反应液中所含碱的浓 度,一般以Na2O的摩尔度表示。 (4)晶化温度和晶化时间。一般规律是,高温晶 化需时短,低温晶化需时长。 (5)成胶温度。一般情况下,温度越高越易成胶。
催化剂制备方法及应用
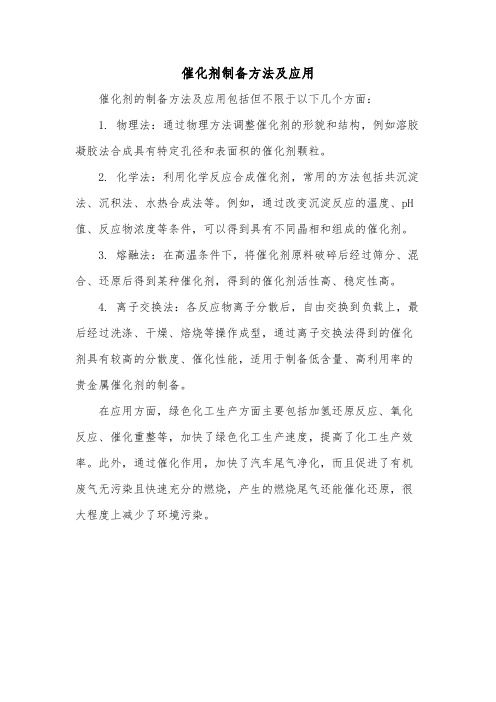
催化剂制备方法及应用
催化剂的制备方法及应用包括但不限于以下几个方面:
1. 物理法:通过物理方法调整催化剂的形貌和结构,例如溶胶凝胶法合成具有特定孔径和表面积的催化剂颗粒。
2. 化学法:利用化学反应合成催化剂,常用的方法包括共沉淀法、沉积法、水热合成法等。
例如,通过改变沉淀反应的温度、pH 值、反应物浓度等条件,可以得到具有不同晶相和组成的催化剂。
3. 熔融法:在高温条件下,将催化剂原料破碎后经过筛分、混合、还原后得到某种催化剂,得到的催化剂活性高、稳定性高。
4. 离子交换法:各反应物离子分散后,自由交换到负载上,最后经过洗涤、干燥、焙烧等操作成型,通过离子交换法得到的催化剂具有较高的分散度、催化性能,适用于制备低含量、高利用率的贵金属催化剂的制备。
在应用方面,绿色化工生产方面主要包括加氢还原反应、氧化反应、催化重整等,加快了绿色化工生产速度,提高了化工生产效率。
此外,通过催化作用,加快了汽车尾气净化,而且促进了有机废气无污染且快速充分的燃烧,产生的燃烧尾气还能催化还原,很大程度上减少了环境污染。
催化剂制备方法

浸渍法的影响因素: 1)盐浓度:
➢ 活性组分金属的易溶盐 —— 硝酸盐、铵盐、有机 酸盐(乙酸盐、乳酸盐)
➢ 浸渍液浓度:
催化剂中活性组分含量(以氧化物计)
a VpC 100% 1 VpC
载体比孔容,ml/g 浸渍液浓度(以氧化物计),g/ml
2)浸渍时间: t=2η/δx x2/r
渗透时间与粘度系数、表面张力、孔径 和粒度有关
Al2O3·nH2O
(2)共沉淀法
共沉淀法是将催化剂所需的两个或两 个以上组分同时沉淀的一个方法。
注意:
各金属盐、沉淀剂浓度、介质pH值、 加料方式等条件件必须满足各个组分同 时沉淀的要求
共沉淀时是否可形成复合碳酸盐的金属
金属
Al
Mg
Ca
Zn
Cu
是
否
否
是
Fe
是
是
否
否
Ni
是
是
否
否
Zn
是
否
否
×
Mg
二、沉淀法制备催化剂举例
1.Al2O3的制备(单组分沉淀剂)
多数情况下都是先制备氧化铝的水合物, 然后将其转化为Al2O3。水合氧化铝一 般有四种:α-Al2O3.3H2O-水氧铝αAl2O3.H2O-水软铝石、βAl2O3.3H2O-拜尔石、βAl2O3.H2O-水硬铝石。
A、α-Al2O3.H2O的制备
在交换过程中,根据交换离子的种类和 交换度的不同,需要注意交换温度、交 换浓度等因素。
分子筛上的离子交换过程:
分子筛的化学组成:
Mn+·[(Al2O3)p·(SiO2)q]·wH2O M 是n价碱金属、碱土金属阳离子,特 别是钠离子。p, q, w分别是氧化硅、氧 化铝、结晶水的分子数。通过改变这些 变数和分子筛晶胞内四面体的排列组合 (链状、层状、多面体等)可以衍生各 种类型分子筛。
- 1、下载文档前请自行甄别文档内容的完整性,平台不提供额外的编辑、内容补充、找答案等附加服务。
- 2、"仅部分预览"的文档,不可在线预览部分如存在完整性等问题,可反馈申请退款(可完整预览的文档不适用该条件!)。
- 3、如文档侵犯您的权益,请联系客服反馈,我们会尽快为您处理(人工客服工作时间:9:00-18:30)。
催化剂的制备方法与成型技术总结应用化学系1202班王宏颖2012080201催化剂的制备方法与成型技术一、固体催化剂的组成:固体催化剂主要有活性组分、助剂和载体三部分组成:1.活性组分:主催化剂,是催化剂中产生活性的部分,没有它催化剂就不能产生催化作用。
2.助剂:本身没有活性或活性很低,少量助剂加到催化剂中,与活性组分产生作用,从而显著改善催化剂的活性和选择性等。
3.载体:载体主要对催化活性组分起机械承载作用,并增加有效催化反应表面、提供适宜的孔结构;提高催化剂的热稳定性和抗毒能力;减少催化剂用量,降低成本。
目前,国内外研究较多的催化剂载体有:SiO2,Al2O3、玻璃纤维网(布)、空心陶瓷球、有机玻璃、光导纤维、天然粘土、泡沫塑料、树脂、活性炭,Y、β、ZSM-5分子筛,SBA-15、MCM-41、LaP04等系列载体。
二、催化剂传统制备方法1、浸渍法(1)过量浸渍法(2)等量浸渍法(多次浸渍以防止竞争吸附)2、沉淀法(制氧化物或复合氧化物)(注意加料顺序:正加法或倒加法,沉淀剂加到盐溶液为正,反之为倒加)(1)单组分沉淀法(2)多组分共沉淀法(3)均匀沉淀法(沉淀剂:尿素)(4)超均匀沉淀法(NH4HCO3和NH4OH组成的缓冲溶液pH=9)(5)浸渍沉淀法浸渍沉淀法是在浸渍法的基础上辅以均匀沉淀法发展起来的,即在浸渍液中预先配入沉淀剂母体,待浸渍单元操作完成后,加热升温使待沉淀组分沉积在载体表面上。
此法,可以用来制备比浸渍法分布更加均匀的金属或金属氧化物负载型催化剂。
(6)导晶沉淀法本法是借晶化导向剂(晶种)引导非晶型沉淀转化为晶型沉淀的快速有效方法。
举例:以廉价易得的水玻璃为原料的高硅酸钠型分子筛,包括丝光沸石、Y型、X型分子筛。
3、共混合法混合法是将一定比例的各组分配成浆料后成型干燥,再经活化处理即可。
如合成气制甲醇用的催化剂就是将氧化锌和氧化铬放在一起混合均匀(适当加入铬酐的水溶液和少许石墨)然后送入压片机制成圆柱形,在100 o C烘2h即可。
4、热分解法硝酸盐、碳酸盐、甲酸盐、草酸盐或乙酸盐。
5、沥滤法制备骨架金属催化剂的方法,Raney 镍、铜、钴、铁等。
6、热熔融法借高温条件将催化剂的各个组分熔合成为均匀分布的混合体、氧化物固体溶液或合金固体溶液,以制取特殊性能的催化剂。
一些需要高温熔炼的催化剂都用这种方法。
主要用于氨合成熔铁催化剂、费-托合成催化剂、兰尼骨架催化剂等的制备。
熔炼温度、环境气氛、冷却速度或退火温度对产品质量都有影响。
固体溶液必须在高温下才能形成,熔炼温度显得特别重要。
提高熔炼温度,还能降低熔浆的粘度,加快组分间的扩散。
采用快速冷却工艺,让熔浆在短时间内迅速淬冷,一方面可以防止分步结晶,维持既得的均匀性;另一方面可以产生内应力,得到晶粒细小的产品。
退火温度对合金的相组成影响较大, 例如,在Ni-Al合金中NiAl3和Ni2Al3的组成与退火温度有关,提高温度会增加Ni2Al3的含量。
沥滤(溶出)Ni-Al合金中的Al组分时,碱液的浓度、浸溶时间、浸溶温度对骨架镍的粒子大小、孔结构、比表面、催化活性均有影响。
如:合成氨催化剂Fe-K2O-Al2O3;用磁铁矿Fe3O4、KNO3和Al2O3高温熔融而得。
7、电解法用于甲醇氧化脱氢制甲醛的银催化剂,通常用电解法制备。
该法以纯银为阳极和阴极,硝酸银为电解液,在一定电流密度下电解,银粒在阴极析出,经洗涤、干燥和活化后即可使用。
8、离子交换法此法用离子交换剂作载体,以反离子的形式引入活性组分,制备高分散、大表面的负载型金属或金属离子催化剂,尤其适用于低含量、高利用率的贵金属催化剂制备,也是均相催化剂多相化和沸石分子筛改性的常用方法。
如:NaY 制HY9、滚涂法和喷涂法将活性组分粘浆置于可摇动的容器中,无孔载体小球布于其上,经过一段时间的滚动,活性组分便逐渐粘附在载体表面。
为了提高涂布效果,有时还要添加粘结剂。
由于活性组分容易剥离,滚涂法已不常用。
10、均相络合催化剂的固载化11、金属还原法12、微波法13、燃烧法(高温自蔓延合成法)常用尿素作为燃烧机14、共沸蒸馏法通过醇和水的共沸,改变沉淀的形貌、孔结构。
三、催化剂制备新技术1、溶胶-凝胶法(水溶液Sol-gel 法和醇盐Sol-gel 法)金属醇盐醇水水解聚合胶溶剂解胶陈化溶胶(1)胶体凝胶法(胶溶法)胶体凝胶法是通过金属盐或醇盐完全水解后产生无机水合金属氧化物,水解产物与胶溶剂(酸或碱)作用形成溶胶,这种溶胶转化成凝胶是胶粒聚集在一起构成网络,胶粒间的相互作用力是静电力(包括氢键)和范德华力。
(2)聚合凝胶法(分子聚合法)聚合凝胶法通过金属醇盐控制水解,在金属上引入OH 基,这些溶胶转化成凝胶时,在介质中继续缩合,靠化学键形成氧化物网络。
两种方法的区别在于加入水量的不同,注意事项:1)水的加入量;2)醇的加入量;3)水解温度;4)胶溶剂加入量 2、超临界技术1)气凝胶催化剂的制备(超临界干燥)2)超临界条件下的催化反应能够改进反应的传质、传热性能,改进产物的分离过程3)用于因结焦、积垢和中毒而失活催化剂的再生。
具有温度低、不发生局部过热现象的特性,从而有效地防止催化剂的烧结失活。
3、纳米技术(1)固相合成法1)物理粉碎法(又称为机械研磨法或机械合金化法)采用超细磨制备超微粒,很难使粒径小于100 nm。
2)固相反应法该法利用金属化合物的固相反应或热分解制备超细微粒,但其粉末易固结,还需再次粉碎,不易制备100 nm以下的超细粉,粒子形状也较难控制。
3)大塑性变形法(100-200 nm)在大塑性变形过程中,材料产生剧烈塑性变形,导致位错增殖、运动、湮灭、重排等一系列过程,晶粒不断虚化达到纳米量级。
i 等通道挤压ii 压力扭转方式4)非晶晶化法(卢柯)该法将非晶材料(可通过熔体激冷、机械研磨、溅射等获得)作为前驱体材料,通过适当的晶化处理(如退火、机械研磨、辐射等)来控制晶体在非晶固体内形核、生长,而使材料部分或完全地转化为具有纳米尺度晶粒的多晶材料。
根据晶化过程和产物可分为多晶型晶化、共晶型晶化等。
5)表面纳米化法(卢柯)该法是将材料的表层晶粒细化至纳米量级而集体仍保持原粗晶状态。
根据材料表层纳米晶的形成方式,表面纳米化分为如下三种类型:i 表面涂层或沉积纳米化(基于不同的涂层和沉积技术,如PVD、CVD、等离子体方法)ii 表面自生纳米化(通过机械变形或热处理使材料表面变成纳米结构,而保持材料整体成分或相组成不变)iii 混合纳米化在表面纳米层形成后进一步通过化学、热或冶金方法,产生于基体不同化学成分或不同相的表面纳米层。
基于纳米表层材料的高活性和快扩散特性,采用混合纳米化技术可使常规难于实现的化学过程,如催化、扩散和表面化合等反应变得容易进行。
(2)气相合成法该法是将高温的蒸气在冷阱中冷凝或在衬底上沉积和生长出低维纳米材料的方法,可利用各种前驱气体或采用加热的方法使固体蒸发成气体以获得气源。
加热方法可采用电阻加热或采用高频感应、等离子体、电子束、激光加热等各种方法。
1)物理气相沉积法PVD制备纳米粉体1-10 nm。
(在充有低压高纯惰性气体的真空容器中进行,可通过调节蒸发的温度和惰性气体的压力等参数控制纳米粉体的粒径。
)2)化学气相沉积法CVD气态原材料导入到一个反应室内,然后发生化学反应,形成一种新的材料,沉积到晶片表面上。
图:用硅烷在单晶硅表面CVD制多晶硅的原理过程示意图(3)液相合成法液相法制备纳米材料的特点,是先将材料所需成分溶解在液体中形成均相溶液,然后通过反应沉淀得到所需组分的前驱物,再经过热分解得到所需物质。
1)沉淀法2)溶胶凝胶法(分为水溶液Sol-gel法和醇盐Sol-gel法)3)水热/溶剂热合成4)微乳液法[反相微乳液即油包水型(W/O型)]当胶束内部的水或油池的体积增大,使液滴的尺寸远大于表面活性剂分子的单层厚度时,则称这种胶束为溶胀胶束或微乳液,胶团的直径可在几纳米至100 nm之间调节。
由于化学反应被限制在胶束中进行,因此微乳液可作为纳米材料的纳米级反应器。
根据水、油和表面活性剂的性质和加入量的不同,微乳液中的胶束可以自组装成不同的纳米结构。
表面活性剂的选择和加入量是形成微乳液的关键。
助表面活性剂通常为醇类,如正丁醇、正戊醇等。
制备微乳液的方法主要有两种:1)Schulman法,将烃、水、乳化剂混合均匀,向其中滴加醇使混合液突然变得透明;2)Shah法,将烃、醇、乳化剂混合均匀向其中滴加水至系统突然变得透明,即获得微乳液。
5)电解沉积法(电化学沉积法)(4) 模板合成(自组装、纳米印刷术)软模板主要应用于介孔或多孔材料的自组装,合成物的结构与模板的有序孔结构或胶体晶结构相同。
表面活性剂和嵌段共聚物的液晶体系、胶体颗粒和乳液液滴等均属于软模板体系。
硬模板则通常指多孔的薄膜或厚膜,如微孔沸石分子筛、介孔分子筛、多孔的Si和高分子膜、具有有序孔洞阵列的Al2O3膜以及金属膜等皆属于硬模板。
(5)成膜技术1)固态粒子烧结法(将无机粉体分散成悬浮液,成型制成生坯,干燥烧结制陶瓷膜或金属膜)2)溶胶凝胶法(浸涂制膜)3)薄膜沉积法用溅射、离子镀、金属镀及气相沉积等方法,将膜料沉积在载体上制造薄膜的技术。
4)阳极氧化法阳极氧化法是目前制备多孔Al2O3膜的重要方法之一。
该法的特点是,制得的膜的孔径是同向的,几乎互相平行并垂直于膜表面,这是其他方法难以达到的。
5)相分离-沥滤法相分离-沥滤法可以制备微孔玻璃膜、复合微孔玻璃膜和微孔金属膜。
6)水热法分子筛膜的合成(6)微晶化技术微晶一般是指粒径介于1-100μm的晶体粉末,也因粉体比表面积大,化学活性高,成为制造催化剂或载体的重要原料。
主要制备技术为下面两类:1)急冷技术2)烧结技术包括常规烧结和特殊条件下的烧结,比如冲击波烧结。
(可用爆炸)冲击波烧结是利用激波产生的瞬间高压、高温,使具有一定松散度(或孔隙率)的粉体发生烧结的方法。
由于激波压缩伴随着材料很强的绝热塑性畸度和颗粒间的摩擦,从而大大地影响了颗粒变形特性和温度的分布规律,以及相伴发生的物理-化学现象。
(7)主体-客体组装技术涉及主客体化学和超分子化学。
四、催化剂成型技术催化剂的几何外形和几何尺寸,对流体阻力、气流速度、床层温度梯度分布、浓度梯度分布等都有影响。
为了充分发挥它的催化潜力,应当选择最优的外形和尺寸,这就需要选择最合适的成型方法。
能形成凝胶的物质,可以制成微球或小球;塑性较好的粘浆或粉末容易挤条或压片;有延展性的金属或合金有时编织成丝网。
对于一个工业多相催化剂来说,必须具备以下几个方面的性能:(1)活性好;(2)选择性高;(3)活性稳定,寿命长;(4)适宜的物化性质(孔体积、孔径、孔径分布及比表面等);(5)必要的强度(压碎强度、磨损强度);(6)适当的形状(粒径或粒度分布);以上催化剂使用性能的每一项都与催化剂的成型方法有关。