第五章挤出成型第二节挤出成型工艺
(整理)食品机械05第五章面食品成型机
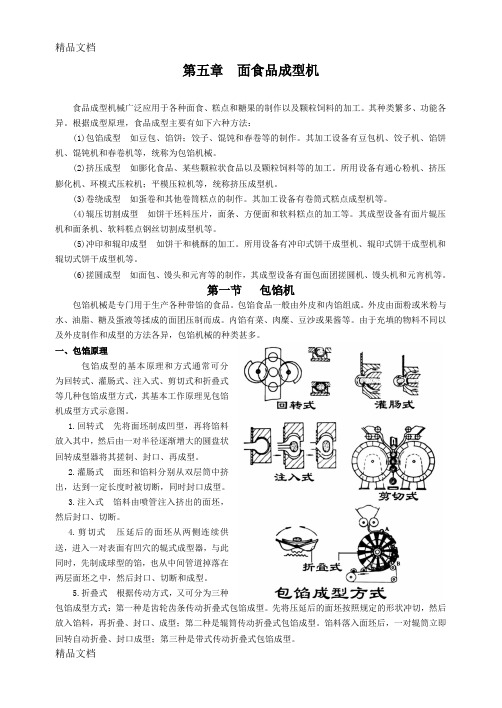
第五章面食品成型机食品成型机械广泛应用于各种面食、糕点和糖果的制作以及颗粒饲料的加工。
其种类繁多、功能各异。
根据成型原理,食品成型主要有如下六种方法:(1)包馅成型如豆包、馅饼;饺子、馄饨和春卷等的制作。
其加工设备有豆包机、饺子机、馅饼机、馄钝机和春卷机等,统称为包馅机械。
(2)挤压成型如膨化食品、某些颗粒状食品以及颗粒饲料等的加工。
所用设备有通心粉机、挤压膨化机、环模式压粒机;平模压粒机等,统称挤压成型机。
(3)卷绕成型如蛋卷和其他卷筒糕点的制作。
其加工设备有卷筒式糕点成型机等。
(4)辊压切割成型如饼干坯料压片,面条、方便面和软料糕点的加工等。
其成型设备有面片辊压机和面条机、软料糕点钢丝切割成型机等。
(5)冲印和辊印成型如饼干和桃酥的加工。
所用设备有冲印式饼干成型机、辊印式饼干成型机和辊切式饼干成型机等。
(6)搓圆成型如面包、馒头和元宵等的制作,其成型设备有面包面团搓圆机、馒头机和元宵机等。
第一节包馅机包馅机械是专门用于生产各种带馅的食品。
包馅食品一般由外皮和内馅组成。
外皮由面粉或米粉与水、油脂、糖及蛋液等揉成的面团压制而成。
内馅有菜、肉糜、豆沙或果酱等。
由于充填的物料不同以及外皮制作和成型的方法各异,包馅机械的种类甚多。
一、包馅原理包馅成型的基本原理和方式通常可分为回转式、灌肠式、注入式、剪切式和折叠式等几种包馅成型方式,其基本工作原理见包馅机成型方式示意图。
1.回转式先将面坯制成凹型,再将馅料放入其中,然后由一对半径逐渐增大的圆盘状回转成型器将其搓制、封口、再成型。
2.灌肠式面坯和馅料分别从双层筒中挤出,达到一定长度时被切断,同时封口成型。
3.注入式馅料由喷管注入挤出的面坯,然后封口、切断。
4.剪切式压延后的面坯从两侧连续供送,进入一对表面有凹穴的辊式成型器,与此同时,先制成球型的馅,也从中间管道掉落在两层面坯之中,然后封口、切断和成型。
5.折叠式根据传动方式,又可分为三种包馅成型方式:第一种是齿轮齿条传动折叠式包馅成型。
挤出成型工艺—挤出成型原理(塑料成型加工课件)
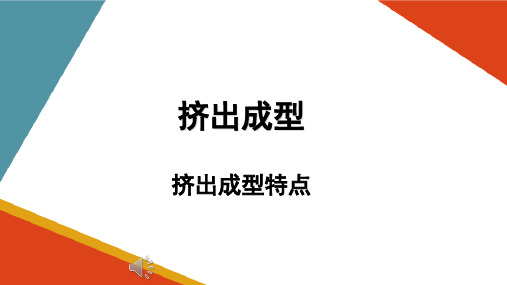
二、挤出成型过程
既有混合过 程,也有成 型过程
树脂原料 加热黏流 塑料熔体
助剂
混合过程
加压 挤出连续体
一定规格的 制品
切割 成型连续体
冷却定型
成型过程
以 管 材 挤 出 原料 成型为例
挤出连续体
熔体
定型连续体
制品
三、挤出成型特点
1. 可以连续化生产,生产效率高。 2. 设备自动化程度高,劳动强度低。 3. 生产操作简单,工艺控制容易。 4. 原料适应性强,适用大多数热塑性树脂和少数热固性 树脂。 5. 可生产的产品广泛,同一台挤出机,只要更换不同的 辅机,就可以生产不同的制品。
挤出成型
挤出成型特点
一、挤出成概述
挤出成型又叫挤出模塑,是利用加热使塑料熔融塑化成 为流动状态,然后在机械力(螺杆或柱塞的挤压)的作用下, 使熔融塑料通过一定形状的口模制成具有恒定截面连续的制 品,适用于绝大部分热塑性树脂和部分热固性树脂。
除了用于挤出造粒、染色、树脂掺和等共混改性,还可用于塑 料薄膜、网材、带包覆层的产品、截面一定、长度连续的管材、板 材、片材、棒材、打包带、单丝和异型材等塑料制品的生产。
料表面接近或达到黏流温度,表面发黏。
要求:输送能力要稍高于熔融段和均化段。
2. 压缩段 (熔融段)
位置:螺杆中部一段。 作用:输送物料,使物料受到热和剪切作用熔 融塑化,并进一步压实和排出气体。 特点:物料逐渐由玻璃态转变为粘流态,在熔 融段末端物料为粘流态。 要求:螺杆结构逐渐紧密,使物料进一步压实。
(3)横流(环流) 由垂直于螺棱方向的分速
度引起的使物料在螺槽内产生翻 转运动。对生产能力没有影响, 但能促进物料的混合和热交换。
(4)漏流 由机筒与螺棱间隙处形成的
挤出机和挤出成型工艺

挤出成型工艺和挤出机1.挤出成型工艺1.1 挤出成型工艺:在挤出机中通过加热、加压而使物料以流动状态持续通过口模(即机头)成型的方式称挤出成型或挤塑。
是塑料重要的成型方式之一。
1.2 挤出成型的特点:①设备本钱低,制造容易,投资少,上马快。
②生产效率高,挤出机的单机产量较高,产率一般在几千克~5吨/小时。
③持续化生产。
能制造任意长度的薄膜、管、片、板、棒、单丝、异型材和塑料与其他材料的复合制品等。
④生产操作简单,工艺控制容易,易于实现自动化。
占地面积小,生产环境清洁,污染少。
⑤能够一机多用。
挤出机也能进行混合、造粒。
1.3 挤出成型可分为两个阶段:第一阶段是使固态塑料变成粘性流体(即塑化),并在加压情形下,使其通过特殊形状的口模,而成为截面与口模形状相仿的持续体。
第二阶段则是用适当的处置方式使挤出的持续体失去塑性状态而变成固体,即取得所需制品。
1.4 挤出成型工艺分类:干法(熔融法)—通过加热使塑料熔融成型①塑化方式湿法(溶剂法)—用溶剂将塑料充分软化成型(CN、CA及纺丝)持续式:螺杆式挤出机,借助螺杆旋转产生的压力和剪切力,使物料充分塑化和均匀混合,通过口模而成型,可进行连续生产。
②加压方式间歇式:柱塞式挤出机,借助柱塞压力,将事先塑化好的物料挤出口模而成型。
仅用于粘度特别大,流动性极差的塑料。
如:PTFE,成型温度下,粘度为1010~1014泊(一般熔融塑料的粘度范围为102~108泊);HUMWPE等。
柱塞可提供很大的压力,但形状不能太复杂,不能加分流梭。
间歇式生产。
2. 挤出设备塑料的挤出,绝大多数都是热塑性塑料,而且又是采用持续操作和干法塑化的。
故在设备方面多用螺杆式挤出机。
螺杆式挤出机有单、双(或多螺杆)之分。
大部份用单螺杆挤出机,只是粉料,RPVC 95%以上都用双螺杆挤出机。
2.1 单螺杆挤出机2.1.1 单螺杆挤出机的组成:由传动系统、加料系统、挤压系统、机头和口模和加热与冷却系统等组成。
第五章挤出成型(六讲)精品PPT课件
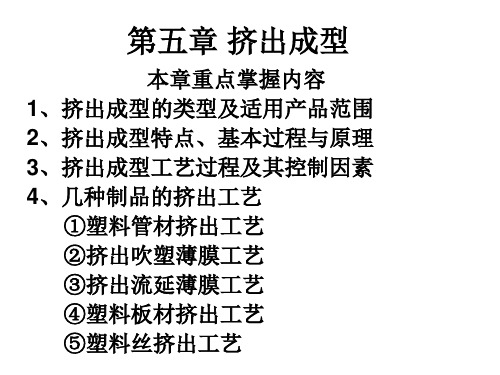
• (1)管材的挤出(P101 图 5-8)
挤出成型的主要原料有: PVC 、 PE 、 PP 、 ABS 、 PA 、 PC 等。
1、管材挤出过程
挤管成模型前头准有备: 直通式
机筒预热
加热塑化
挤出成型
偏移式(转定角径式)所用挤水出槽机冷,却应根据管材直牵引径和所需切割挤或收卷
直角式管材一般出不量需、后原处料品理种确定。同时考虑扩大再 2、挤出设备及生装产置的需要。
T ↓ , η↑ ,机头压力 ↑ ,制品致密,形状稳定, 易出现离模膨胀效应,
T ↓↓ ,塑化差,质量差。 转速 n ↑ ,剪切 ↑ ,利于塑化, η↓ ,但料筒中物 料的压力 ↑ 。
3 、定型和冷却 (同时进行)
• 管材、异型材 —— 独立的定型装置 板材、片材——压辊定型 薄膜、单丝、线缆包覆 —— 无需定型装置,直接冷却定 型。 定型方法: 管材:定径套(外径定型、内径定型) 原理:管坯内外形成压力差。使管外紧贴于套内壁冷却。 冷却速度: 硬质塑料:慢些,以避免内应力。软质塑料、结晶塑料: 快些。 (熔体粘度低)
和干燥。
干燥要求加:热器
热 风
一般塑料:水份
<
热
0.5%风
热
干燥高温下易鼓水风解机 的塑料,干燥如尼龙(
系
统纶(
PET )等:水份 过滤器
< 系统
0.03%
预热和干燥的方式:
PA
)、风 烘涤
料 斗
烘箱、烘房,可抽真空干燥,热风干燥。
热风除湿系统
加热系统
2 、塑化挤出
Байду номын сангаас• 挤出成型是连续成型工艺,关键是初期的 调整,要调整到正常挤出。 主要调整:
挤出成型工艺分析ppt

挤出成型工艺的历史与发展
1 2 3
起源
挤出成型工艺起源于19世纪末期,最初用于生 产硬质管材和型材。
发展
随着技术的不断进步,挤出成型工艺逐渐应用 于生产各种形状和用途的制品,如软管、薄膜 、发泡制品等。
未来趋势
随着科技的进步,挤出成型工艺将不断向高效 、节能、环保的方向发展,同时探索新的应用 领域和市场。
解决方案:为避免气泡问题,挤出成型过程中可以 采取以下措施
1. 提高塑料熔体的温度,使气体更容易从熔体 中逸出。
2. 控制好挤出机的转速和牵引速度,使塑料熔 体保持稳定的流动状态。
3. 在制品设计时增加排气孔或改变排气结构, 使气体更容易从制品中排出。
制品尺寸不稳定
总结词:制品尺寸不稳定是挤出成型工艺中的另一个问 题,主要是由于挤出机、模具和冷却系统等因素导致的 。 解决方案:为提高制品尺寸稳定性,可以采取以下措施
常用挤出吹塑机。
工艺流程
将挤出造粒后的塑料颗粒加热至 熔融状态,通过吹塑模具吹制成 中空制品。
吹塑工艺参数
包括温度、压力、吹胀比等,需根 据不同产品要求进行优化。
成型后处理
冷却定型
吹塑后的制品需进行冷却定型 ,以去除内应力,提高制品稳
定性。
制品修饰
如切除飞边、修整等。
检验入库
对制品进行质量检验,合格品 入库。
解决方案
为避免塑料降解,挤出成型过程中应 控制好加热温度和时间,避免过度加 热和长时间暴露在高温环境下。同时 ,选择质量好的塑料原材料,并保持 挤出机内部清洁。
制品变形
总结词
详细描述
解决方案
制品变形是挤出成型工艺中的另一个 常见问题,主要是由于制品冷却不均 匀或受力不均匀导致的。
挤出成型工艺
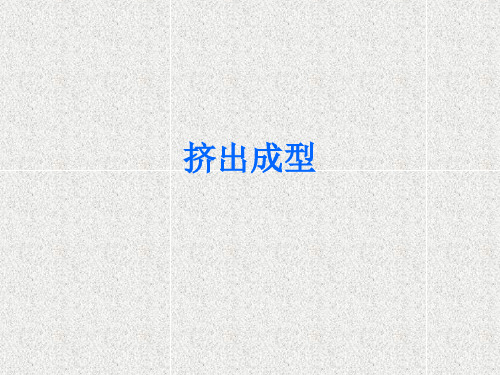
双金属料筒:为了既能满足料筒 对材质的要求,又能节省贵重材 料,不少料筒在一般碳素钢或铸 钢的基体内部镶一合金钢衬套。
IKV料筒:提高固体输送率 1、料筒加料段内壁开设纵向沟 槽; 2、将加料段靠近加料口处的一 段料筒内壁做成锥形; 3、强制冷却加料段料筒
螺杆
• 120销钉螺杆
• 250大螺杆
• 压片机双锥螺杆
• 锥双压片
• 锥形双螺杆
• 锥形双螺杆35-90
螺杆结构参数 螺杆直径
D—螺杆外径 d—螺杆根径 螺杆直径是一个重要参量,它在一定意义上表征挤出机挤
出量的大小。 D↑,加工能力↑。挤出机生产率∝D2
我国挤出机标准所规定的螺杆直径系列为:30、45、65、 (85)90、(115)120、150、200。 螺杆直径的大小一般根据所加工制品的断面尺寸、加工 塑料的种类和所要求的生产率来确定。
单螺杆的长径比有一个由小到大的发展趋势,50年代一般为
18—20,60年代为25—28,目前为30左右。
压缩比(2—5)
作用:是将物料压缩,排除气体,建立必要的压力,保证物 料到达螺杆末端时有足够的致密度。 几何压缩比:螺杆加料段第一个螺槽与均化段最后一个螺槽 的容积比: 物理压缩比:物料加工之前的松密度与均化段熔体密度之比。 设计原则:应使几何压缩比大于物理压缩比 获得压缩比的方法:等距变深螺槽、等深不等距螺槽、不等 深不等距螺槽、锥形螺杆等方法。其中等距不等深螺槽的办
螺杆长径比
螺杆的长径比是螺杆的重要参数之一。若将它与螺杆转数
联系起来考虑,在一定意义上也表示螺杆的塑化能力和塑化 质量。
1)长径比加大后,螺杆的长度增加,塑料在料筒中停留的 时间长,塑化得更充分更均匀,故可以保证产品质量。 2) 在此前提下,可以提高螺杆的转数.从而提高挤出量。
挤出成型培训资料

片材车间内部学习教材目录第一节 概 述第二节 挤出成型基本工艺流程第三节 挤出成型原辅材料基础知识第四节 挤出成型过程的工艺控制第五节 挤出成型的辅助加工第六节 挤出产品的后续加工第一节 概 述挤出成型是在挤出成型机中,塑料被加热、加压,通过一定形状的模具成型,然后经冷却定型、拉伸(也有不经过拉伸的)、卷取(或切割)成为具有一定截面形状的制品。
一条挤出生产线由两部分组成。
第一部分是将塑料熔融挤到料筒末端的过程,第二部分是将已经塑化好的塑料熔体经过模头成型,再经过定型装置定型,再经过牵引、切断、或修整等工序而成为制品的过程。
在塑料加工领域中,挤出成型是应用最广泛的一种成型方法,与其他成型方法相比,具有如下优点:①设备制造容易,成本低;②可以连续化生产,生产效率高;③设备的自动化程度高,劳动强度低;④生产操作简单,工艺控制容易;⑤挤出产品均匀,密实,质量高;⑥对原料的适应性强,不仅大多数的热塑性塑料可以用语挤出成型,而且少数的热固性塑料也能适应;⑦所生产的产品广泛,可一机多用,同一台押出机,只要更换辅机,就可以生产出不同的制品或半成品;⑧生产线的占地面积小,而且生产环境清洁。
当然,挤出成型也有缺点:①不能生产三维尺寸的产品;②制品往往需要二次加工。
由于挤出成型的优点突出,因此,挤出成型在塑料加工行业中具有举足轻重的地位,热塑性塑料的95%可用螺杆式挤出机生产。
作为挤出成型工程技术人员及技术工人,必须掌握塑料熔体的基本性质。
只有掌握了塑料熔体的基本性质,才能对挤出成型过程中的各种控制有理论上的依据,减少实际生产中的盲目性,减少调试时间。
第二节 挤出成型基本工艺流程塑料挤出成型产品包括塑料挤出造粒技术、塑料管件/管材的挤出生产技术、塑料薄膜挤出吹塑生产、流延薄膜与双向拉伸薄膜生产技术、塑料板材/片材挤出生产技术、合成纤维与塑料丝挤出生产技术以及塑料异形材挤出生产技术等内容,本教材只介绍塑料板材/片材挤出生产工艺基础知识。
第5章+挤出成型2
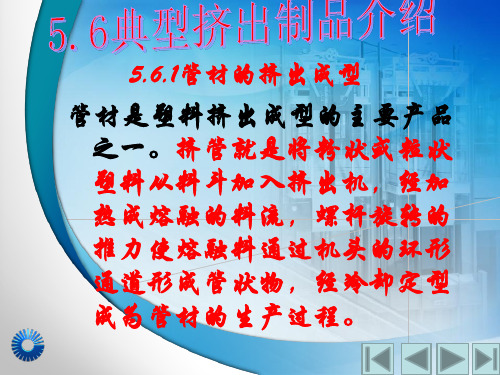
1.2挤出过程之牵引
牵引装置
4.牵引装置
橡胶带式:适合50-150mm管 滚轮式:<100m管 履带式:二履带、三履带、四履带和六履带,适合各种管。
5.6.1.2挤出过程之牵引
履带式牵引排列方式
履带的排列
a-六条履带 b-二条履带 c-三条履带 1-履带 2-塑料管材
挤出过程之牵引 履带式牵引机实物照片
5.6.1管材的挤出设备
机头附件:
分流器(鱼雷头)将圆柱形料流变为薄环状并 便于进一步加热塑化。大型分流器内设加热器, 支架用以支承分流器及芯棒,同时使料流分束 以加强搅拌,小型分流器与芯棒做为一体
5.6.1管材机头种类
(直通式、直角式、旁侧式和筛孔板式) 1)直通式 熔体在机头中流动方向与螺杆轴向一致,结 构简单易制造;适于PVC,PE,PA
当吹塑材料为结晶塑料薄膜时管膜刚离开模头时是透明的至一定的高度由于冷却而结晶固化变得不透明浑浊浑浊与透明的交界线被称1适当提高或降低加工温度对固体输送率没有影响2机头压力大小对单螺杆挤出机的单位时间产量无关3在异向旋转双螺杆中物料是以正位移原理向前强制输送与螺杆与物料的摩擦系数无关因此输送效率是极4由于同向平行双螺杆转动而反复强迫物料转向使物料受到较好的剪切混合效果这种螺杆具有很好的自洁作用一般用于混料造粒
管材挤出成型常见故障的排查
拉破或拉断 故障分析及排除方法: 如果牵引过程中,管壁上产生小洞,主要是由于冷却定 型环的供水太少。应适当增加供水量。 若管壁上拉出大洞,主要是由于压缩空气供气量太 大。应合理调节压缩空气供给量。 若牵引太快,管材容易拉断。应合理控制牵引速度。
5.6.1管材的挤出成型流程实物图
牵引 切割 挤出机
5.6.1管材的挤出设备(机头、 1 机头:
- 1、下载文档前请自行甄别文档内容的完整性,平台不提供额外的编辑、内容补充、找答案等附加服务。
- 2、"仅部分预览"的文档,不可在线预览部分如存在完整性等问题,可反馈申请退款(可完整预览的文档不适用该条件!)。
- 3、如文档侵犯您的权益,请联系客服反馈,我们会尽快为您处理(人工客服工作时间:9:00-18:30)。
转速过快导致的问题
出模膨胀加大和口模内流动的不稳定,使制品表面 质量下降
并且可能会出现因冷却时间过短造成的制品变形、 弯曲
转速过低,挤出速率过慢,物料在机筒内受热
时间变长,会造成物料降解,使制品物理力学
性能下降。
5.2.3 挤出压力
(1)作用
①克服因螺杆槽深度的变化,过滤板、过滤网 和口模等产生料流阻力,即使塑料物理状态 发生变化。 ②使塑件均匀密实。 压力波动
不良影响:
塑件局部疏松,表面不平,弯 曲等。
5.2.4 冷却与牵引
(1)冷却 ① 空气冷却 ② 水冷却
冷却速率过块
易造成残余应力过大,尤其是硬质塑料
冷却速率过慢
生产效率低,塑件变形,尤其是软质塑料
5.2.4 冷却与牵引
牵引速度可与挤出速度相当。牵引速度与挤出速 度的比值称牵引比,其值必须等于或大于1。 (1)牵引
机头
(1) 加料段(固体输送段)温度设定
加料段在挤出 机中的作用 温度设定原则 (1) 不宜太高,影响物料在此段输送;也不宜
高效率输送 固体物料
预热物料
太低,螺杆受力过大或卡死
(2) 一般接近粘流温度,由低到高按梯度排列。
(2) 熔融段(压缩段)温度设定
熔融塑化 物料 压缩物料、排出 空气
熔融段在挤出 机中的作用
一般要求熔融段的温度比粘流温度高15-20℃,以 保证物料的有效熔融。
(2) 熔融段(压缩段)温度设定
A填充料,(提供强剪切使填充物,充分分散),熔融段 高出基料熔点10~20℃(尽量提高),使物料充分熔融均 匀分布。 B阻燃料,其温度要偏低,尽可能降低。 C合金料,以两组熔融温度为依据,同时考虑组分比 例及组分热敏性等
第五章
挤出成型
第二节 挤出成型工艺
塑料挤出成型工艺流程
挤出过程 在螺杆中 熔融塑化 机头口 模挤出
加料
牵引 切割
定型 冷却
5.2 挤出成型工艺
挤出温度 螺杆转速(时间和剪切) 压力(由温度和螺杆转速控制)
冷却和牵引
5.2 挤出成型工艺
5.2.1挤出温度
低温
中温
段
目的: ①消除塑件尺寸变化值。 ②对塑件进行适当的拉伸, 提高塑件质量。
(2)牵引
正常
牵引速度略大于挤出速度
非正常
牵引速度过大
影响: 塑件的厚度、直径减小,纵向抗 断裂强度增高,扯断伸长率降低
本节小结
(1)理解塑料挤出过程的工艺流程 (2)掌握塑料挤出时螺杆各段温度如何设定 (3)掌握螺杆转速的快慢对挤出过程有何影响
5.2.2 螺杆转速与挤出速度
挤出速度是指单位时间内由挤出机头和 口模中挤出的塑化好的物料量或塑件长 度,它表征着挤出生产能力的高低。
(1)影响因素
①机头、螺杆和料筒的结构 ②螺杆转速
③加热冷却系统结构
④塑料性能
转速增加优势
机筒内物料的压力增加,挤出速率增加 强化对物料的剪切,提高料温,降低熔体粘度, 有利于物料的充分混合与均匀塑化。
谢谢大家
(4) 机头(口模)温度
温度偏低
物料塑化不良,熔体粘度增大,机头压力上 升,制品压得较密实,产品形状稳定性好 加工较困难,离模膨胀较严重,产品表面 较粗糙 挤出机背压增加,设备负荷 加大; 温度过低时物料不能有效塑化,不但产品无 法成型,还会造成设备损坏。
口模段温度影响
口模温度的设定除需考虑所用塑料的配方体系外,还应 考虑制品截面的几何形状,其基本原则为 (1)断面复杂、截面积大、壁厚及拐角部位温度应 较高。 (2)断面简单、截面积小、壁薄的部位温度应较低。 (3)断面对称、厚薄均匀处口模与 芯模温差应较小。
(3) 均化段(计量段)温度设定
均化段在挤出 机中的作用 熔融塑化 物料
为机头提供 稳定的熔体
温度设定原则
温度比熔融段温度略高,一般为粘流温度以上 20-30℃,
(4) 机头(口模)温度
机头是机筒与口模之间的过渡部分,其温度控制的 合理与否会影响到产品质量和产量。
机头温度偏高
有利于物料进入口模 挤出物的尺寸稳定性差,制品收缩率增加; 严重时还会引起跑料,产品出现气泡、产 品发黄、物料分解等弊端,导致挤出生产不 能正常进行;