机械设计外文文献翻译、中英文翻译、外文翻译
机械设计中英文外文翻译文献
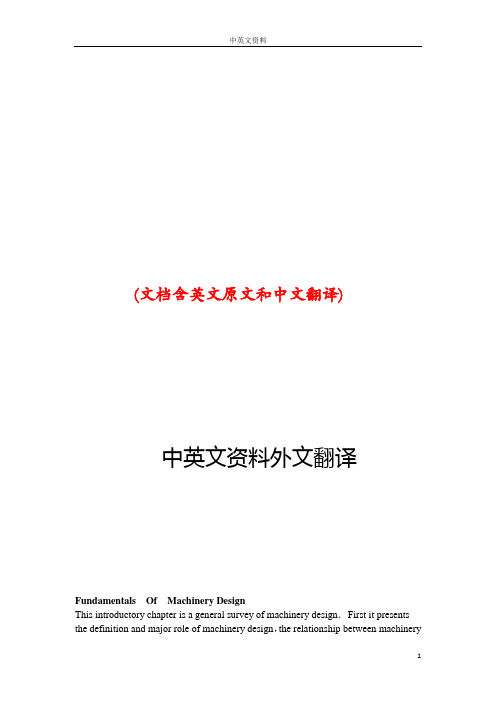
(文档含英文原文和中文翻译)中英文资料外文翻译Fundamentals Of Machinery DesignThis introductory chapter is a general survey of machinery design.First it presents the definition and major role of machinery design,the relationship between machineryand its components.Then it gives an overview of machinery design as a fundamental course and outlines a general procedure of machinery design followed by all the engineers.Finally, it lists the contents of the course and the primary goals to be achieved.1.1 The role of machinery designMachinery design is to formulate all engineering plan.Engineering in essence is to utilize the existing resources and natural law to benefit humanity.As a major segment of engineerin,machinery design involves a range of disciplines in materials,mechanics,heat,flow,control,electronics and production.Although many hightechnologies are computerized and automated,and are rapidly merged into Our daily life,machines are indispensable for various special work that is difficult or impracticable to be carried out by human.Moreover,machinery can significantly improve efficiency and quality of production,which is crucial in current competitive global market.In the modern industrialized world,the wealth and living standards of a nation are closely linked with their capabilities to design and manufacture engineering products.It can be claimed that the advancement of machinery design and manufacturing can remarkable promote the overall level of a country’s industrialization.Those nations,who do not perform well in design and manufacture fields,are not competitive in world markets.It is evident that several countries that used to be leaders in the design and manufacturing sectors until the l 960s and the1 970s had,by the l990s,slipped back and lost their leadership.On the contrary, our Country is rapidly picking up her position in manufacturing industry since the l 9 80s and is playing a more and more vital role in the global market.To accelerate such an industrializing process of our country, highly skilled design engineers having extensiveknowledge and expertise are needed.That is why the course of machinery design is of great significance for students of engineering.The course of machinery design is considerable different from those background subjects in science and mathematics.For many students,it is perhaps one of their basic professional engineering courses concerned with obtaining solutions to practical problem s.Definitely these solutions must clearly represent an understanding of the underlying science,usually such an understanding may not be sufficient,empirical knowledge or engineering judgement has to be also involved.Furthermore,due to be professional nature of this subject,most design problems may not have one right solution.Nevertheless it is achievable to determine a better design from all feasible solutions.1.2 Machinery and componentsA state-of-the-art machine may encompass all or part of mechanical,electrical,control,sensor,monitoring and lubricating sub—systems.Intermsof the functions of those parts,the machine can also be viewed to be comprised of power,transmission,execution and control/manipulation parts.Regardless of the complexity, however,the major functional part may be still the mechanical system.Forconvenience of analysis,the mechanical system can be decomposed int0.mechanisms that are designed to execute some specific tasks.And the mechanism can be further decomposed into mechanical components.In this sense,the mechanical components are the fundamental elements of machinery.On the whole,mechanical components can be classified as universal and special components.Bolts,gear and chains are the typical examples of the universal components which can be used extensively in different machines across various industrial sectors.Turbine blades,crankshaft and aircraft propeller are the examples ofthe special components,which Can be used extensively in different machines across various industrial sectors.turbine blades,crankshaft and aircraft propeller arethe examples of the special components,which are designed for some specific purposes.In addition to this,if a number of components are manufactured,assembled and even equipped as an individual system,e.g.leaf spring setin a vehicle,it is also termed as a mechanical part.A good machine definitely requires quality individual components.Thus,the design of components is very important.When designing a machine,on the otherhand,engineers invariably find that requirements and constraints of its components areinterrelated.As a local portion,the component is expected to play a certain role on the machine and therefore must be appropriately restrained by the whole system.The design of a gear drive in a speed—reducer,for instance,depends upon not only the strength and stiffness,but also the space available for the gears in the shaft and relation with other transmission drive.This means that the design of the mechanical components inevitably requires a whole view in the whole system.Due to relationship between a machine and its components,the process of machinery design usually covers interconnected designs of machine,parts,and components.Any modification and adjustment in one component may considerably affect the designs of other components or parts.To present the best possible design solution,the iteration of evaluation,analysis and optimization across all the process seem indispensable.1.3 Overview of machinery designThis course is primarily concerned with the design of specific components of machines or mechanical systems.Competence in this area is basic to the consideration and synthesis of complete machines and systems in subsequent courses and professional practice.It Can be seen that even the design of a single bolt or spring needs the designer’s thorough understanding of the principles and methods ofmachinery design together with empirical information,good judgment and even a degre3e of ingenuity in order to produce the best product for the society today.It is natural that designing engineers give first consideration to the functional and economic aspects of new products or devices.Machinery design needs to ensure safetyand reliability in a prescribed lifetime.To address such a problem conventionally,the technical consideration of the mechanical component design is largely centered around two main areas of concerns:(1) strength-stiffness-stability criteria involving the bulk of a solid member and (2) surface phenomena including friction,lubrication,weal7,and environmental deterioration.However,in comparison with such relatively straightforward computations as stress and deflection,the design determination of safety and reliability is likely to be an elusive and indefinite matter,complicated by psychological and sociological factors.It must be kept in mind that safety and reliability are inherently relative to each other,and the value judgmentsmust be made with regard to trade—offs between safety,reliability,cost,weight,and soforth.On the other hand,a practical design needs to reflect clearly manufacturability and economy to make sure of the lowest cost as well as the least consumption of energy and materials.Otherwise,the products or devices designed will be of no further engineering or commercial interests.Nowadays,the simultaneous considerations of manufacturing and assembly factors phases including design,manufacturing,inspection,asassembly and other is considered in such a parallel fashion that the quality and cost arebest satisfied concurrently.In addition to these traditionally technological and economic considerations fundamental to the design and development of mechanical components and systems,the modern engineers have become increasingly concerned with the broader considerations of sustainability,ecology,aesthetics,ergonomics,maintainability,andoverall quality of life.It is clear that a greater than ever engineering effort is being recently devoted to broader considerations relating to the influences of engineered products on people as well as on the environment.The following is a list of general factors for engineers to consider in the design process,which from a different viewpoint shows us a panoramic picture with regard to the design-related activities and tasks.(1) Cost of manufacturing.Will the selling price be competitive? Are there cheaper ways of manufacturing the machine? Could other materials be used? Are any special tools,dies, jigs,or fixtures needed? Can it easily be inspected? Can the workshop produce it? Is heat treatment necessary? Can parts be easily welded?第4页Cost of operation.Are power requirements too large? What type of fuelwill be used? Will operation cost be less expensive?(3) Cost of maintenance.Are all parts easily accessible? Are access panels needed? Can common tools be used? Can replacement parts be available?(4) Safety features.Is a suitable factor of safety used? Does the safety factor meet existing codes? Are fuses,guards,and/or safety valves used? Are shear pins needed? Is there any radiation hazard? Any overlooked ”stress raiser”? Are there any dangerous fumes?(5) Packaging and transportation.Can the machine be readily packaged for shipping without breakage? Is its size suitable to parcel post regulations, freight car dimensions,or trailer truck size? Are shipping bolts necessary? Is its center of gravity in a desirable location?(6) Lubrication.Does the system need periodic checking? Is it automatic? Isit a sealed system?(7) Materials.Are chemical,physical,and mechanical properties suitable to its use? Is corrosion a factor? Will the materials withstand impact? Is thermal or electrical conductivity important? Will high or low temperatures present any problem? Will design stress keep parts reasonable in size?(8) Strength.Have dimensions of components been carefully calculated? Have all the load cases be taken into account? Have the stress concentrations been carefully considered? Has the fatigue effect be computed?(9) Kinematics.Does it provide necessary motion for moving parts? Are rotational speeds reasonable? Could linkages replace cams? What will be the best choice,the belts,chains or gears? Is intermittent motion needed?(10) Styling.Does the color have eye appeal? Is the sharp desirable? Is the machine well proportioned? Are the calibrations on dials easily read? Are the controls easy to operate?(11) Drawings.Are standardized parts used? Are the tolerances realistic? Is the surface finish over-specified? Must the design conform to any standards?(12) Ergonomics.Has the operator of the equipment been considered? Are the controls conveniently located to avoid operator fatigue? Are knobs,grab bars,hand wheels,levers,and dial calibrations of proper size to fit the average operator?1.4 A general procedure of machinery designWhatever design tasks the designers are expected to complete,theyalways,consciously or unconsciously,follow the similar process which goes as follows:(1)Studies of feasibilityAfter understanding the product functions,operational conditions,manufacturing constraints and key technologies,go on to uncover existing solutions to some similar problems so as to clarify the design tasks,understand the needs,present the major functional parameters and evaluate design tasks,proposal of design aims,and feasibility analysis.(2) Conceptual design of configurationAccording to the design of tasks and functional parameter,designs need to extensively search for various feasible configurations and alternatives.Forconvenience,usually,the system can be analyzed comprehensively by decomposing itinto power sources,transmission and work mechanisms.A great effort needs to be devoted to the analysis and synthesis of these different parts.For example,the power source may be selected from motor,engine and turbine.Each power source may have a range of power and kinematical parameters .Similarly, power trains may have numerous optionsavailable,e.g.belts,chains,gears,worm gears and many other drives.Obviously selecting an appropriate configuration would guarantee the Success of the whole design and the quality of the products.To make a best possible decision,an iterative process is normally required to select,analyze,compare and evaluate different configurations.At this stage,the goals involve sketching of configuration,determination of kinematical mechanisms,and evaluation of functional parameter(power and kinematics).(3)Detailed technical designBased on the design of configuration and parameters,a number ofassembly and component drawings will be completed to reflect the detaileddesign including kinematics,power,strength,stiffness,dynamics,stability,fatigue and SO on.Consideration should also be given to manufacturingfactors by presenting structural details,materials,and both geometricand dimensional tolerances.This part of work will also be carried out ina repeated process in drawings,calculation,evaluation and modificationuntil a best possible design is achieved.The goal at this stage is tocomplete assembly and component drawings,structural details,design calculations and detailed technical documentations.(4)Modification of designAfter the design is completed,a prototype is usually made for a more realistic physical assessment of the design quality.This will help correct any drawback or fault that may be overlooked or neglected during the design process.At this stage,the goal is to correct the design imperfection,test the potential manufacturing or assembly flaws and refine /improve design.1.5 Contents and tasks of the courseThe course Machinery Design will cover the following contents:(1)Preliminaries.the fundamental principles of machinery andComponents design,design theory,selection of materials,structure,friction,wear and lubrication.(2)Connection.sand.joints.thread.fasteners,keys,rivets,welds,bonds .and adhesive and interference joints.(3)Transmission.screws,chains,belts,gears,worms,bevel.gearsAnd helical gears.(4)Shaft.system.rolling—contact.bearings,slidingbearings,clutches,couplings,shafts,axles and spindles.(5)Other part s.springs,housings and frame s.The course centers on engineering design of mechanical components andis in a category of fundamental methodology and procedure.It is notfeasible or realistic for the students to become involved in the detaileddesign considerations associated with all machine components.Instead,the textbook has its main focus on some typical components and parts.However,the methodologies and procedures to be developed in this course can beextended to more design cases.For this reason,an emphasis will be laidon the methods and procedure s over the course so that the student s willgain a certain competence in applying these skills and knowledge todesigning more mechanical components.As a professional fundamental course,it will help students to acquirea sol id knowledge of mechanical design and engineering awareness.More specifically,the course will help to develop the students’ competence inthe following facets:Competence of creative design and solving practical problem;Competence of team work as well as professional presentation and communications:Competence of apprehending the design principles andregulations,synthesizing the knowledge to develop new designs:Competence of engineering research as well as using designcode s,handbooks,standards and references:Competence of doing experiments to solve problem in the design oftypical components:Competence of understanding newly introduced technological as well aseconomic codes to update the knowledge of machinery design.It is worth noticing that the course will also integrate a number ofpreceding relevant subjects at the university—level ,including mathematics ,physics,electronics,chemistry,solid mechanics,fluid mechanics,heat transfer,thermodynamics,computin9,and so forth.It will combine the knowledge about science and professional skills to solve some practical engineering problems,which will significantly advance students’ competence and enlarge their vision to the professional engineers.It should be pointed out that skills and experience could beacquired only by a great deal of practice——hour after monotonous hour ofit.It is acknowledged universally that nothing worthwhile in life canbe achieved without hard work,often tedious,dull and monotonous,and engineering is no exception.机械设计的基本原则这个导言章节是对机械设计的一个纵览。
机械设计过程外文文献翻译、中英文翻译

附录英文Machine design processThe machine is the organization with other components combinations, transforms,the transmission or using the energ,the strength or the movementexample for the beneficial use has the engine.the turbine wheel,the vehicles.the hoist,the printer,the washer and the movie camera Many is suitable tbr themachine design principle and the strength law also is suitable to is not thegenuine machine finished product.the driven wheel hub and the file cabinet tothe measuring appl iance and the nuclear pressure vessel.”Machine designt thisterminology compared to”machine design”more generalized,it including machine design.But regarding certain instruments.1ike uses to determine hot,the mobile line and the volume thermal energy as well as the fluid aspect question needs alone to consider.But when machine design must consider themovement and the structure aspect question as well as preserved and the sealstipulation.In the mechanical engineering domain and all that project domainapplication machine design,all need such as mechanism and so on the svdtch,cam,valve,vessel and mixer.The design beginning tO being true or the imagination need.The existing instrument possibly needs in the durability,the efficiency,the weight,the speedor the cost performs to improve.]he possible need new instrument tO completebefore made the function by the person.1ike t was abundant Assembly or maintenance.After the goal completely or partially determines,the design nextstep is the idea carl complete needs the ffmction the organization and its thearrangement for this,the free hand drawing schematic diagram value is enormous,it not only takes a person idea the recording and the auxiliary.methodwhich if the other people discusses,moreover especially is suitable for with ownidea exchange,also needs to concern as the creative mentality stimulant to thepart widespread knowledge,because a new machine frequently by knew very well each kind of components rearrange or the replace become,perhaps changedthe size and the material.Regardless of after idea process or,a designer callcarry on fast either the sketchy computation or the analysis determines thegeneral size and the feasibility.After about need or may use the spatial meteidea determination,may start according to the proportion picture schematicdiagram.When several components approximate shapes and several sizes come out,the analysis was allowed truly to start.The analysis goal lies in enable it to havesatisfying or the superior performance,as well as will seek the best proportionand the size under the smallest weight security and the durability and thecompetitive cost designer for each essential load bearing section,as well asseveral components intensities balance then choice material and processingmethod.These important goals only have through only then may obtain based on the mechanism analysis,like about reacting force and friction most superioruse principie of statics;About inertia,acceleration and energy principle ofdynamics:About stress and deflection material elasticity and intensity principle;About material physical behavior principle;About lubrication and water poweractuation hydromechanics principle.The analysis may identical engineer whicharranges by the idea machinery do,or makes the analysis in the big company bythe independent analysis department or the research group the result,possibleneed new arrangement and new size.No matter is officially does orunofficialdoes,supposes Japan is relapse and the cooperation process.the analysis staffmay play the role to all stages but not merely is he stage.Some design criteriaIn this part,some people suggested carries on the analysis using the creative manner,this kind of analysis may cause the significant improvement aswell as to the spare product idea and the consummation,the product functionmore.more economical,is perhaps more durable. The creation stage does notneed is at first and the independent stage.Alttlough the analysis staff possiblycertainlv is not responsible for the entire design,but he not meyely is can fromthe numeral proposc wants question correct answer which he soIVes,not merelyis Droduces the stress value,the size or the work limit. He may propose a morewidespread opinion,in order to improvement standard or plan. Because beforethe analysis or in the analysis process,he can familiar install and its the workingcondition.he is in an idea to prepare chooses the plan the rantage Poinl.Best hecan propose the suggestion transfigure eliminates the moment of force or thestress concentration,but was not the permission constructs has the blgsectlonand the excessively many dynamic loads organization should better be he discards his careful desi{;n but is not afterwards saw the machinery discarded.In order to stimulate the creative thought,below suggested designs thepersonnel and the analysis staff uses the criterion.The first 6 criteria especially are suitable for the analysis staff,although he possibly involves to possesses this l o items.1.Creatively the use needs the physical performance and the control doesnot need.2.Knows the practical load and its the importance.3.D00s not consider the function load in advance.4.Invents the more advantageous loading environment.5.Provides the minimurn weight the most advantageous stress distributionand the rigidity.6.uses the fundamental equation computation proportion and causes thesize optimization.7.The selection material obtains the perlbrmance combination.8.In between spare parts and integrated components carefid choice. 9.Revisions functional design adapts the production process and reduces thecost.10.In the consideration assembly causes the part pintpointing and mutuallydoes not disturb.Designs the personnel to have in such domain,like the statics,the inematics,dynamics and the materials mechanics have the good accomplishment,in addition.but also must familiar make the material and themanufacture craft.Designs the personnel to have to be able to combine allcollrelations the fact,carries on teaches Wei.the manufacture schematic diagramand the charting comes the manufacture request totransmit the workshop. Any product design one of first step of work is the choice uses in to makeeach part the material.Today design personnel may obtain innumerably.When choice,the product function,the outward appearance,the material cost and theproduction cost very are all important.Before any computation must carefullyappraise the material the performance.It is the necessary careful computation toguarantee the design the validity The computation ever does not appear on thechart,but is saved by ten each kind of reason.Once any part expires,had makeclear when is designing at first this had the flaw the components has made any;Moreover,。
变速箱壳体机械加工工艺设计外文文献翻译、中英文翻译、外文翻译

Gearbox shell machining process design《Manufacturing Engineering and Technology—Machining》Mechanical Industry Press In March 2004, version 1 p560—564(Serope kalpakjian)(Steven R.Schmid)AbstractGearbox shell is a more complex structure of spare parts box, its high precision, complex process, and the processing quality will affect the overall performance engine, so it has become the engine manufacturer's focus parts one.Machining process planning must guarantee the machining quality of parts, to meet the technical requirements stipulated in drawings, at the same time should also have high productivity and efficiency. Therefore, machining process planning design is an important work, requires designers must have a rich experience in production practice and wide range of mechanical manufacturing technology basic theory knowledge. In the specified procedure, should according to the production of parts and the existing equipment conditions, taking the processing quality into account, productivity and economy requirements, after repeated analysis and comparison, to determine the optimal or the best solution.1.Technical Characteristics of the gearbox shellThe gearbox shell process features are: the structure of complex shape; processing plane, more than holes; uneven wall thickness and stiffness is low; processing of high precision typical of box-type processing part. The main processing of the surface of cylinder block top surface, the main bearing side, cylinder bore, the main and camshaft bearing bore holes and so on, they will directly affect the machining accuracy of the engine assembly precision and performance, mainly rely on precision equipment, industrial fixtures reliability and processing technology to ensure the reasonableness.2.The gearbox shell process design principles and the basisDesign Technology program should be to ensure product quality at the same time, give full consideration to the production cycle, cost and environmental protection; based on the enterprises ability to actively adopt advanced process technology and equipment, and constantly enhance their level of technology. Gearbox shell machining process design should follow the following basic principles: 2.1 The selection of processing equipmentThe principle of selection adopted the principle of selection adopted the principle of combining rigid-flexible, processing each horizontal machining center is located mainly small operations with vertical machining center, the key process a crank hole, cylinder hole, balancer shaft hole High-speed processing of high-precision horizontal machining center, an upper and lower non-critical processes before and after the four-dimensional high-efficiency rough milling and have a certain adjustment range of special machine processing;2.2 Concentration process principleFocus on a key process in principle process the body cylinder bore, crankshaft hole, Balance Shaft hole surface finishing and the combination of precision millingcylinder head, using a process focused on a setup program to complete all processing elements in order to ensure product accuracy The key quality processes to meet the cylinder capacity and the relevant technical requirements;3.The gearbox shell machining process design the main contentGearbox shell complex structure, high precision, arge size, is thin-walled parts, there are a number of high precision plane and holes. Engine block machining process characteristics; mainly flat and the hole processing, processing of flat generally use planing, milling methods such as processing, processing of hole used mainly boring, processing and multi-purpose drilling holes. As the cylinder complex structure. so how to ensure that the mutual position of the surface processing precision is an important issue.3.1 The selection of blankGearbox shell on the materials used are generally gray cast iron HT150,HT200,HT250,there is also cast aluminum or steel plate, this engine block using high-strength alloy cast iron. Cylinder in the processing prior to aging treatment in order to eliminate stress and improve the rough casting mechanical properties. Improve the rough accuracy, reduction of machining allowance, is to improve the automated production line system productivity and processing quality of the important measures. As the foreign box-type parts of rough quality and high precision, and its production-line system has been implemented directly on the blank line, not only eliminating the need for blank check device also saves the rough quality problems due to waste of machining time, increase overall efficiency. Therefore, the refinement of rough is to improve the productivity of the most promising way out. For the engine block production line, can be rough in parts on-line pre-milling six face, removing most of the margin, to facilitate direct on-line parts.3.2 Machining process selection and processing of the benchmarkChoose the right processing technology base is directly related to the processing quality can ensure the parts. Generally speaking, process benchmarking can be divided into coarse and fine reference base.3.2.1 Coarse reference baseThe baseline for the on-line thick rough ,which is particularly important the choice of benchmark crude, if crude benchmark choice unreasonable, will the uneven distribution of machining allowance, processing and surface offsets, resulting in waste. In the cylinder production line, we have adopted for the coarse side of the base;3.2.2 Fine reference baseRefined the base of this box for the engine block parts, the general use of "side two sales "for a full range of uniform benchmarks, For the longer automated production positioning. In the gearbox shell of the process, we have adopted to the side, bottom and the spindle hole positioning, in the processing center on the process.3.3 Machining Processing Stages and processes of the arrangementsOften a part of many apparent need for processing, of course, the surface machining accuracy are different. Processing of high precision surface, often afterrepeated processing; As for the processing of the surface of low precision, only need to go through one or two on the list. Thus, when the development process in order to seize the "processing high precision surface, "this conflict, the reasonable arrangement processes and rational division stage of processing. Arrange the order of the principle of process is: after the first coarse refined, the first surface after the hole, the first benchmark other. In the engine block machining, the same should follow this principle.3.3.1 roughing stage engine block machining processThe arrangements for roughing process, to fully carry out rough rough, trim most of the margin in order to ensure production efficiency;3.3.2 semi-finishing phase of the engine block machiningIn order to ensure the accuracy of the middle of some important surface processing, and arrange some semi-finishing operations, will be required accuracy and surface roughness of the surface of the middle of some processing to complete, while demanding the surface of semi-finished, to prepare for future finishing;3.3.3 The finishing stageThe finishing stage of requiring high accuracy and surface roughness of the surface processing; 3.3.4 secondary processingSecondary processing such as small surface screw holes, you can finish of the major surface after the one hand, when the workpiece deformation process little impact at the same time also reduced the rejection rate;In addition,if the main surface of a waste,these small the surface will not have to be processed,thus avoiding a waste of man-hours.However,if the processing is very easy for a small surface bumps the main surface,it should be placed on a small surface finish prior to the main surface finishing;3.3.5 make proper arrangements for secondary processesMake proper arrangements for secondary processes such as product inspection process,in part roughing stage,the key process before and after processing,spare parts all the processing has been completed,should be appropriate arrangements. Stage of processing division,has the following advantages:First,it can take measures to eliminate the rough workpiece after the stress,to ensure accuracy; second,finishing on the back,and will not damage during transport the surface of the workpiece has been processed;again,first roughing the surface defects can be detected early and promptly deal with rough,do not waste working hours.But most small parts,do not sub very thin.3.4 The gearbox shell surface of the main processing and secondary processes3.4.1 Plane processingPlane processing at present, the milling of engine blocks is the primary means of planar processing,domestic milling feed rate is generally 300-400mm/min,and foreign 2000-4000mm/min milling feed rate compared to far cry,to be on increasing,therefore,improve the milling feed rate,reduce overhead time is to improve the productivity of the major means of finishing a number of plane engine block when the milling feed rate to reach 2399mm/min,greatly improved efficiency; Top surface of the cylinder milling is a key process in the process,the flatnessrequirements for 0.02/145mm,the surface roughness of Ra1.6um.Processing in the cylinder,the use of side and spindle bearing bore positioning,top,bottom and middle vagay only aperture while processing used in the processing line outside of the knife device can better meet the engine block machining accuracy;3.4.2 General holes MachiningGeneral holes Machining holes in general are still using the traditional processing of drilling,expansion,boring,reaming,tapping and other craft approach. Issues in the design process of specific programs,use of coated cutting tools,cutting tools and other advanced tools within the cooling,and using a large flow of cooling systems,greatly improving the cutting speed,improved productivity;3.4.3 Deep hole processingDeep hole processing of the traditional processing method is used to grade twist drill feed,low efficiency of their production,processing and quality is poor.The deep hole in the engine block processing,the use of gun drilling process;3.4.4 CleaningCleaning is divided into wet cleaning and dry cleaning.Machining cylinder automatic production line using a large flow of wet cleaning;3.4.5 DetectionDetect points outside the line detection and line detection of two kinds. Quality inspection in the engine block,according to the actual situation with lines outside the detection,the main use of coordinate measuring machine integrated measurements of the cylinder,each 200 samples 1-5 pieces,each class random one.变速箱壳体机械加工工艺设计摘自:《机械工程与技术(机加工)》(英文版)机械工业出版社2004年3月第1版美国卡卡尔帕基安·施密德摘要变速箱壳体是变速器机零件中结构较为复杂的箱体零件,其精度要求高,加工工艺复杂,并且加工加工质量的好坏直接影响发动机整个机构的性能,因此,它成为各个发动机生产厂家所关注的重点零件之一。
机械设计专业外文文献翻译

机械设计专业外文文献翻译general。
however。
materials that are easy to machine have high machinability。
while those that are difficult to machine have low XXX。
microstructure。
and mechanical properties。
as well as the XXX。
material。
and wear resistance.XXX factors。
cutting speed。
feed rate。
and depth of cut also play XXX the amount of heat generated in the cutting zone and decreasing the time that the cutting tool is in contact with the XXX。
at high cutting speeds。
tool wear and cutting forces can increase。
which can ce tool life and surface finish quality.Feed rate and depth of cut also XXX the amount of material that is removed and the forces that are generated during cutting。
Higher feed rates and deeper cuts can improve material removal rates。
but they can also increase cutting forces and heat n。
which can ce tool life and surface finish quality.Overall。
机械设计毕业设计外文文献翻译中英文对照塑料模具CAD集成技术

机械设计毕业设计外文文献翻译中英文对照:塑料模具CAD集成技术毕业设计外文文献翻译毕业设计题目摇控器面板注塑模设计翻译题目The molding tool CAD gathers the technique专业机械设计制造及其自动化姓名班级机械A0731学号指导教师机械与材料工程学院二O一O年十一月[K.P. Rao and K. Sivaram: J. Mater. Proc. Technol., 1993, vol. 37, pp.295-318.]毕业论文(设计)外文翻译课题名称:塑料模具CAD集成技术内容提要:通过分析计算机辅助注射模设计和制造的各个环节中共享的技术和信息,本文揭示了注射模CAD的集成技术的根本内涵,并提出了它的研究热点和趋势。
引言模具CAD集成技术是一项重要的模具先进制造技术, 是一项用高技术改造模具传统技术的重要关键技术。
从六五计划开始,我国有许多模具企业采用CAD 技术, 特别是近年, CAD技术的应用越来越普遍和深入, 大大缩短了模具设计周期,提高了制模质量和复杂模具的制造能力。
然而, 由于许多企业对模具CAD集成技术认识不足, 投资带有盲目性, 不能很好地发挥作用,造成了很大的浪费。
本文就塑料模具CAD集成技术及其应用发表一些观点, 供大家参考。
1、塑料模具CAD集成技术塑料模具的制造, 包括塑料产品的造型设计、模具的结构设计及分析、模具的数控加工铣削、电加工、线切割等、抛光和配试模以及快速成形制造等。
各个环节所涉及的CAD单元技术有:造型和结构设计CAD、产品外形的快速反求RE、结构分析与优化设计CAE、辅助制造CAM、加工过程虚拟仿真SIMULATION、产品及模具的快速成形RP、辅助工艺过程CAPP和产品数据管理技术PDM等。
塑料模具CAD集成技术,? 就是把塑料模具制造过程所涉及的各项单元技术集成起来, 统一数据库和文件传输格式, 实现信息集成和数据资源共享, 从而大大缩短模具的设计制造周期, 提高制模质量。
机械类外文文献及翻译
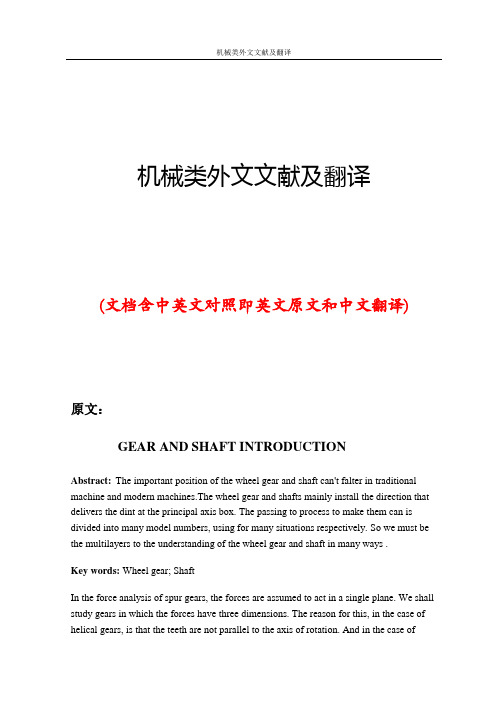
机械类外文文献及翻译(文档含中英文对照即英文原文和中文翻译)原文:GEAR AND SHAFT INTRODUCTIONAbstract:The important position of the wheel gear and shaft can't falter in traditional machine and modern machines.The wheel gear and shafts mainly install the direction that delivers the dint at the principal axis box. The passing to process to make them can is divided into many model numbers, using for many situations respectively. So we must be the multilayers to the understanding of the wheel gear and shaft in many ways .Key words: Wheel gear; ShaftIn the force analysis of spur gears, the forces are assumed to act in a single plane. We shall study gears in which the forces have three dimensions. The reason for this, in the case of helical gears, is that the teeth are not parallel to the axis of rotation. And in the case ofbevel gears, the rotational axes are not parallel to each other. There are also other reasons, as we shall learn.Helical gears are used to transmit motion between parallel shafts. The helix angle is the same on each gear, but one gear must have a right-hand helix and the other a left-hand helix. The shape of the tooth is an involute helicoid. If a piece of paper cut in the shape of a parallelogram is wrapped around a cylinder, the angular edge of the paper becomes a helix. If we unwind this paper, each point on the angular edge generates an involute curve. The surface obtained when every point on the edge generates an involute is called an involute helicoid.The initial contact of spur-gear teeth is a line extending all the way across the face of the tooth. The initial contact of helical gear teeth is a point, which changes into a line as the teeth come into more engagement. In spur gears the line of contact is parallel to the axis of the rotation; in helical gears, the line is diagonal across the face of the tooth. It is this gradual of the teeth and the smooth transfer of load from one tooth to another, which give helical gears the ability to transmit heavy loads at high speeds. Helical gears subject the shaft bearings to both radial and thrust loads. When the thrust loads become high or are objectionable for other reasons, it may be desirable to use double helical gears. A double helical gear (herringbone) is equivalent to two helical gears of opposite hand, mounted side by side on the same shaft. They develop opposite thrust reactions and thus cancel out the thrust load. When two or more single helical gears are mounted on the same shaft, the hand of the gears should be selected so as to produce the minimum thrust load.Crossed-helical, or spiral, gears are those in which the shaft centerlines are neither parallel nor intersecting. The teeth of crossed-helical fears have point contact with each other, which changes to line contact as the gears wear in. For this reason they will carry out very small loads and are mainly for instrumental applications, and are definitely not recommended for use in the transmission of power. There is on difference between a crossed heli : cal gear and a helical gear until they are mounted in mesh with each other. They are manufactured in the same way. A pair of meshed crossed helical gears usually have the same hand; that is ,a right-hand driver goes with a right-hand driven. In the design of crossed-helical gears, the minimum sliding velocity is obtained when the helix angle areequal. However, when the helix angle are not equal, the gear with the larger helix angle should be used as the driver if both gears have the same hand.Worm gears are similar to crossed helical gears. The pinion or worm has a small number of teeth, usually one to four, and since they completely wrap around the pitch cylinder they are called threads. Its mating gear is called a worm gear, which is not a true helical gear. A worm and worm gear are used to provide a high angular-velocity reduction between nonintersecting shafts which are usually at right angle. The worm gear is not a helical gear because its face is made concave to fit the curvature of the worm in order to provide line contact instead of point contact. However, a disadvantage of worm gearing is the high sliding velocities across the teeth, the same as with crossed helical gears.Worm gearing are either single or double enveloping. A single-enveloping gearing is onein which the gear wraps around or partially encloses the worm.. A gearing in which each element partially encloses the other is, of course, a double-enveloping worm gearing. The important difference between the two is that area contact exists between the teeth of double-enveloping gears while only line contact between those of single-enveloping gears. The worm and worm gear of a set have the same hand of helix as for crossed helical gears, but the helix angles are usually quite different. The helix angle on the worm is generally quite large, and that on the gear very small. Because of this, it is usual to specify the lead angle on the worm, which is the complement of the worm helix angle, and the helix angle on the gear; the two angles are equal for a 0-deg. Shaft angle.When gears are to be used to transmit motion between intersecting shaft, some of bevel gear is required. Although bevel gear are usually made for a shaft angle of 0 deg. They may be produced for almost any shaft angle. The teeth may be cast, milled, or generated. Only the generated teeth may be classed as accurate. In a typical bevel gear mounting, one of the gear is often mounted outboard of the bearing. This means that shaft deflection can be more pronounced and have a greater effect on the contact of teeth. Another difficulty, which occurs in predicting the stress in bevel-gear teeth, is the fact the teeth are tapered.Straight bevel gears are easy to design and simple to manufacture and give very good results in service if they are mounted accurately and positively. As in the case of squr gears, however, they become noisy at higher values of the pitch-line velocity. In these cases it is often go : od design practice to go to the spiral bevel gear, which is the bevel counterpart of thehelical gear. As in the case of helical gears, spiral bevel gears give a much smoother tooth action than straight bevel gears, and hence are useful where high speed are encountered.It is frequently desirable, as in the case of automotive differential applications, to have gearing similar to bevel gears but with the shaft offset. Such gears are called hypoid gears because their pitch surfaces are hyperboloids of revolution. The tooth action between such gears is a combination of rolling and sliding along a straight line and has much in common with that of worm gears.A shaft is a rotating or stationary member, usually of circular cross section, having mounted upon it such elementsas gears, pulleys, flywheels, cranks, sprockets, and other power-transmission elements. Shaft may be subjected to bending, tension, compression, or torsional loads, acting singly or in combination with one another. When they are combined, one may expect to find both static and fatigue strength to be important design considerations, since a single shaft may be subjected to static stresses, completely reversed, and repeated stresses, all acting at the same time.The word “shaft” covers numerous v ariations, such as axles and spindles. Anaxle is a shaft, wither stationary or rotating, nor subjected to torsion load. A shirt rotating shaft is often called a spindle.When either the lateral or the torsional deflection of a shaft must be held to close limits, the shaft must be sized on the basis of deflection before analyzing the stresses. The reason for this is that, if the shaft is made stiff enough so that the deflection is not too large, it is probable that the resulting stresses will be safe. But by no means should the designer assume that they are safe; it is almost always necessary to calculate them so that he knows they are within acceptable limits. Whenever possible, the power-transmission elements, such as gears or pullets, should be located close to the supporting bearings, This reduces the bending moment, and hence the deflection and bending stress.Although the von Mises-Hencky-Goodman method is difficult to use in design of shaft, it probably comes closest to predicting actual failure. Thus it is a good way of checking a shaft that has already been designed or of discovering why a particular shaft has failed in service. Furthermore, there are a considerable number of shaft-design problems in which the dimension are pretty well limited by other considerations, such as rigidity, and it is only necessary for the designer to discover something about the fillet sizes, heat-treatment,and surface finish and whether or not shot peening is necessary in order to achieve the required life and reliability.Because of the similarity of their functions, clutches and brakes are treated together. In a simplified dynamic representation of a friction clutch, or brake, two in : ertias I and I traveling at the respective angular velocities W and W, one of which may be zero in the case of brake, are to be brought to the same speed by engaging the clutch or brake. Slippage occurs because the two elements are running at different speeds and energy is dissipated during actuation, resulting in a temperature rise. In analyzing the performance of these devices we shall be interested in the actuating force, the torque transmitted, the energy loss and the temperature rise. The torque transmitted is related to the actuating force, the coefficient of friction, and the geometry of the clutch or brake. This is problem in static, which will have to be studied separately for eath geometric configuration. However, temperature rise is related to energy loss and can be studied without regard to the type of brake or clutch because the geometry of interest is the heat-dissipating surfaces. The various types of clutches and brakes may be classified as fllows:. Rim type with internally expanding shoes. Rim type with externally contracting shoes. Band type. Disk or axial type. Cone type. Miscellaneous typeThe analysis of all type of friction clutches and brakes use the same general procedure. The following step are necessary:. Assume or determine the distribution of pressure on the frictional surfaces.. Find a relation between the maximum pressure and the pressure at any point. Apply the condition of statical equilibrium to find (a) the actuating force, (b) the torque, and (c) the support reactions.Miscellaneous clutches include several types, such as the positive-contact clutches, overload-release clutches, overrunning clutches, magnetic fluid clutches, and others.A positive-contact clutch consists of a shift lever and two jaws. The greatest differences between the various types of positive clutches are concerned with the design of the jaws. To provide a longer period of time for shift action during engagement, the jaws may be ratchet-shaped, or gear-tooth-shaped. Sometimes a great many teeth or jaws are used, and they may be cut either circumferentially, so that they engage by cylindrical mating, or on the faces of the mating elements.Although positive clutches are not used to the extent of the frictional-contact type, they do have important applications where synchronous operation is required.Devices such as linear drives or motor-operated screw drivers must run to definite limit and then come to a stop. An overload-release type of clutch is required for these applications. These clutches are usually spring-loaded so as to release at a predetermined toque. The clicking sound which is heard when the overload point is reached is considered to be a desirable signal.An overrunning clutch or coupling permits the driven member of a machine to “freewheel” or “overrun” bec ause the driver is stopped or because another source of power increase the speed of the driven. This : type of clutch usually uses rollers or balls mounted between an outer sleeve and an inner member having flats machined around the periphery. Driving action is obtained by wedging the rollers between the sleeve and the flats. The clutch is therefore equivalent to a pawl and ratchet with an infinite number of teeth.Magnetic fluid clutch or brake is a relatively new development which has two parallel magnetic plates. Between these plates is a lubricated magnetic powder mixture. An electromagnetic coil is inserted somewhere in the magnetic circuit. By varying the excitation to this coil, the shearing strength of the magnetic fluid mixture may be accurately controlled. Thus any condition from a full slip to a frozen lockup may be obtained.齿轮和轴的介绍摘要:在传统机械和现代机械中齿轮和轴的重要地位是不可动摇的。
机械设计类英文文献及翻译

The Sunflower Seed Huller and Oil PressBy Jeff Cox-- from Organic Gardening, April 1979, Rodale PressIN 2,500 SQUARE FEET, a family of four can grow each year enough sunflower seed to produce three gallons of homemade vegetable oil suitable for salads or cooking and 20 pounds of nutritious, dehulled seed -- with enough broken seeds left over to feed a winter's worth of birds.The problem, heretofore, with sunflower seeds was the difficulty of dehulling them at home, and the lack of a device for expressing oil from the seeds. About six months ago, we decided to change all that. The job was to find out who makes a sunflower seed dehuller or to devise one if none were manufactured. And to either locate a home-scale oilseed press or devise one. No mean task.Our researches took us from North Dakota -- hub of commercial sunflower activity in the nation -- to a search of the files in the U.S. Patent Office, with stops in between. We turned up a lot of big machinery, discovered how difficult it is to buy really pure, unrefined vegetable oils, but found no small-scale equipment to dehull sunflowers or press out their oil. The key to success, however, was on our desk the whole time. In spring 1977, August Kormier had submitted a free-lance article describing how he used a Corona grain mill to dehull his sunflower seeds, and his vacuum cleaner exhaust hose to blow the hulls off the kernels. A second separation floated off the remaining hulls, leaving a clean product. We'd tried it, but because some kernels were cracked and the process involved drying, we hadn't been satisfied. Now we felt the best approach was to begin again with what we learned from Mr. Kormier and refine it.Staff Editor Diana Branch and Home Workplace Editor Jim Eldon worked with a number of hand- and electric-powered grain mills. While the Corona did a passable job, they got the best results with the C.S. Bell #60 hand mill and the Marathon Uni Mill, which is motor-driven. "I couldn't believe my eyes the first time I tried the Marathon," Diana says. "I opened the stones to 1/8th inch, and out came a bin full of whole kernels and hulls split right at the seams. What a thrill that was!"She found that by starting at the widest setting,and gradually narrowing the opening, almost every seed was dehulled. The stones crack the hulls open, then rub them to encourage the seed away from the fibrous lining. The Bell hand mill worked almost as well. "As long as the stones open at least as wide as the widest unhulled seed, any mill will work," she says.Because the seed slips through the mill on its flat side, grading is an important step to take before dehulling. We made three sizing boxes. Thefirst is 1/4-inch hardware cloth [wire screen]. The second is two layers of1/4-inch cloth, moved slightly apart to narrow the opening in one direction, and the third is two layers of screen adjusted to make a still-smaller opening. Since the smallest unhulled seeds are about the size of the largest hulled kernels, the grading step prevents these undersized seeds from passing through unhulled. Processed together at a closer setting, the smallest seeds hulled out.Jim Eldon's workshop is littered with strange-looking pieces of apparatus. They represent initial attempts to build a workable winnowing box, using Kormier's vacuum exhaust idea for a source of air. Jim, Fred Matlack and Diana finally made a box with a Plexiglas front, through which they could observe what was happening.They cut a hole in the back of the box with a sliding cover to regulate the air pressure, and fiddled with various arrangements of baffles. The result was a stream of hulls exiting through one hole while the kernels fell to the bottom of the box. Now they were ready to try a five-pound sample of unhulled sunflower seeds to see how much they could recover.The five pounds were graded and dehulled, then winnowed. We got about one hull for every ten kernels in the final, winnowed product. These are easily picked out. They usually contain kernels still held behind the fibrous strings of the hull. Their weight prevents them from blowing out with the empty hulls. We found that bug-eaten seeds do blow away with the chaff, which was a bonus for cleanliness of the final product. Toss the hulls to the birds, who will find broken seeds among them.Starting with 80 ounces of unhulled seed, we ended up with 41-1/4 ounces of edible whole seeds, 1.8 ounces of damaged seeds suitable for animal feed, and 36.6 ounces of hulls. It took us about an hour. Notbad.Sunflower seeds store perfectly in the hulls, but they deteriorate more rapidly when shelled out. The grain mill dehuller and winnowing box give the gardener a way to have the freshest possible seeds for eating at all times of the year. With the construction of one more piece of equipment -- the oil press -- he can have absolutely fresh, unrefined, polyunsaturated sunflower oil for salads, mayonnaise and cooking.Most light, refined vegetable oils have been extracted using hexane, a form of naphtha. The oil is then heated to boil off the hexane. Lye is dumped into it. It's washed with steam, then heated to remove odors and taste before being laced with preservatives and stabilizers. It may feel oily in the mouth, but you might as well taste air. No so with fresh-made sunflower oil -- it's deliciously yet subtly nutty in flavor, adding unsurpassed flavor to salads.There's good reason to believe that sunflower oil may become the #1 vegetable oil in the U.S. in a few years. It's already #1 in health-conscious Europe. Corn oil has already caught on here for health reasons, and sunflower oil is so much better. Sunflower oil's 70 percent polyunsaturate is just under safflower, with corn oil bringing up the rear with 55 percent. And sunflowers yield 40 percent oil, soybeans only 20 percent.Our oil press isrelatively simple, but it must be welded together. Check the construction directions for details. The press consists of a welded tubular frame which accepts a three-ton hydraulic jack. You may already have one. If not, it can be purchased at most auto and hardware stores for about $16. A metal canister with holes drilled in its sides and one end welded shut holds the mashed sunflower seeds. A piston is inserted in the canister and then inverted and slipped over a pedestal on the frame. The jack is set in place, and the pressure gradually increased over half an hour. The oil drips from the sides of the canister into a tray -- the bottom of a plastic jug slipped over the pedestal works fine -- which empties the oil into a cup. You can filter the oil with a coffee filter to remove pieces of seed and other fine particles that would burn if the oil were used for cooking. If it's for salads or mayonnaise, there's no need to filter it.We first tried using "confectionary" sunflower seeds for oil. These are the regular eating kernels we're used to seeing. They give less than half as much oil as the oilseed types of sunflower. Although you can use confectionary types such as MAMMOTH RUS- SIAN for oil, don't expect to get more than an ounce and a half from a pound of seed. Oilseed produces three or more ounces of oil from a pound of seed and is well worth planting along with confectionary-type seeds. Oilseed has another big advantage -- to prepare it, you can put the whole, unhulled seed into a blender and whiz it until it forms a fine meal, while confectionary seeds must be dehulled first. The entire sequence of grading, dehulling and winnowing is avoided with oilseed.Oil types produce about a tenth of a pound of seed per head in commercial production. Gardeners, with their better soil and care, invariably do better than that. Our conservative estimate is that 1,280 plants will be enough for three gallons of oil. Spaced one foot apart in rows two feet apart, 1,280 oilseed plants will take a space 40-by-56 feet, or 80-by-28 if you want a more rectangular patch to face south.We worked in pound batches, since the canister just holds one pound of mash. After blending, we heated it to 170 degrees F. (77 deg C) by placing it in a 300-degree F. (149 deg C) oven and stirring it every five minutes for 20 minutes. Heating gets the oil flowing and doubles the yield of oil. In case you're wondering,"cold-pressed" oils sold commercially are also heated, and some are subjected to the entire chemical process. The term has no firm meaning within the industry, according to the literature we've surveyed.Heating does not change the structure of fats. It will not turn polyunsaturated fats into saturated fats. In fact, Dr. Donald R. Germann in his book, "TheAnti-Cancer Diet", says that "... an unsaturated fat must be heated to high temperatures -- above 425 degrees F. or 200 degrees C. -- at least 8 or 10 times before any shift toward saturation occurs..." Dean C. Fletcher, Ph.D., of the American Medical Association Department of Foods and Nutrition in Chicago, says, "It's true that either high temperature or repeated heatingdoes change the nature of some of the unsaturated oil molecules. (But) the flavor of the oil changes as these chemical changes occur, spoiling its taste. This effect is probably more profound than any of the physiological changes the altered oil might produce within the body."From 500 gm. of heated mash, we pressed 89 gm. of oil, 89 percent of the entire amount available and twice as much as we could press from unheated oil! The decision is up to you whether or not to heat the mash, but that extra 50 percent seems like an awful lot, especially when the whole technique is so labor intensive. The oil should be stored in the refrigerator, and it's probably best to use it within a month, since it has no preservatives. Mayonnaise made with such fresh oils should be kept refrigerated and used within two weeks. The leftover cake, still containing 50 percent of its oil, is a nutritious addition to your dishes, and makes excellent feed for animals or winter birds. Store the pressed cake in the freezer.We're talking then about a sunflower patch with two kinds of plants -- confectionary such as MAMMOTH RUSSIAN and oilseed such as PEREDOVIK. The oilseed plants should be grown 12 inches apart in rows two feet apart. Four average confectionary heads yield about a pound of unhulled seed. You'll need about 35 pounds of unhulled seed, or 140plants-worth, to yield 20 pounds of hulled kernels, about what a family of four will use in a year. That many plants can be grown in an area 26-by-10 feet. That's 260 square feet. Put that together with the 2,240 square feet for the oilseed sunflowers, and you need a patch about 2,500 square feet -- 25 100-foot rows -- to keep yourself supplied year-round with super nutrition and unsurpassable taste.Winnowing Machine For Sunflower SeedsThe winnowing machine operates on the age-old principle of blowing the chaff away from the heavy grain with a controlled current of air.The unit uses a household or shop-type vacuum cleaner for its air supply. A vacuum cleaner was used as a power source because it can supply a large volume of air over an extended period of time, and most homes and farms have a vacuum cleaner.A cloth bag has been attached to the chaff chute to catch the chaff as it is separated from the seed. The bag allows the hulls to be collected and greatly reduces the amount of waste material normally blown into the air by conventional systems.The unit has been constructed in such a way that the cloth bag and cleaner box can be placed inside the seed box, making a compact package for storage.Tools Required1. Table Saw2. Drill Press3. Band Saw4. Saber SawProcedure (cleaner box)1 . Cut out the two sides of the cleaner box from 1/4-inch plywood.2. Cut out the six interior pieces of the cleaner box from 3/4 x 3-1/2-inch select pine.3. Assemble the cleaner box elements with glue and nails.4. Cut four 1/4-inch square strips of pine four inches long.5. Glue the strips around the end of the chaff chute.6. Sand all surfaces and edges.7. Finish with clear lacquer finish.Procedure (seed box)1. Cut two pieces of pine /34" x 5 /12 x 15 inches for the sides.2. Cut two pieces of pine 3/4 x 5-1/2 x inches for the top and bottom.3. Plow a /14 x 1/4 groove for the front and back panels in all four pieces.4. Rip the top board to 5 inches so that the front panel can slide into the grooves in the side boards.5. Rabbet both ends of each 15-inch side piece to accept the top and bottom boards.6. Drill a hole in the left side board 2-1/2 inches from the top. The size of the hole is determined by the vacuum cleaner hose fitting.7. Cut a 3-1/4 x 4 inch hole in the top 1/2 inch from the right end. This hole will accept the cleaner box.8. Cut two pieces of pine for the baffle.9. Drill two 1-inch holes in the bottom of the baffle box.10. Cut a piece of 1/4 x 8-1/2 x 14 inch plywood for the back panel.11. Cut a 3-inch hole, centered 1-7/8 inches from the top and left sides of the plywood back.12. Assemble the sides, baffles, top, bottom, and back panel with glue and nails.13. Cut an 8-7/16 x 15-3/4-inch piece of Plexiglas for the front.14. Cut a one-inch radius on the top corners of the front.and sand the edges.15. Drill a one-inch thumb hole centered 7/8 inch from the top edge.16. Cut a 3-1/2-inch disk of 1/4-inch plywood for the vent cover.17. Drill a 3/16-inch hole 3/8 inch from the edge of the disk.18. Mount the disk over the vent with a #10 x 1-inch screw.19. Sand all surfaces and edges of the, box.20. Finish with clear lacquer finish.MaterialsCleaner Box2 -- 7-3/4 x 7-1/2 x 3/4" plywood (sides)6 -- 3/4 x 3-1/2 x 24" for all members (baffles)4 -- 1/4 x 1/4 x 4" pine (chute cleats)22 -- 1" x 18 ga. headed nailsWhite vinyl glueClear lacquer finishSeed Box2 -- 3/4' x 5-1/2 x 15" select pine (sides)2 -- 3/4 x 5-1/2 x 8-1/2" select pine (top and bottom)1 -- 3/4 x 3-1/2 x 4-1/2" select pine (baffle)1 -- 3/4 x 4-1/2 x 4-1/2" select pine (baffle)1 -- 1/4 x 8-1/2 x 14" plywood (back)1 -- 1/4 x 3-1/2" dia. plywood (control valve)1 -- 1/4' x 8-7/16 x 15-1/4" Plexiglas (front)1 - #10 x 1" flat head screw18 - 4d finish nailsWhite vinyl glueClear lacquer finish1 -- 17 x 31" cloth laundry bagSunflower Seed Oil PressThe press was designed so that homesteaders can produce sunflower oil from their own seeds. The oil can be pressed as is or heated to 170 degrees F., which doubles oil yield.Both methods require the seed to be ground to fine powder. If you are pressing the oil seed variety, a meat grinder or electric blender will do an excellent job of grinding the seed. The confectionary type of seed will require the seed to be hulled and winnowed before it is ground. A food mill with the stones set at the coarse setting can be used to accomplish this step. The ground kernels are placed in the cylinder with the piston closing the bottom portion of the cylinder.The cylinder is mounted in the press frame and a three-ton hydraulic jack is used to supply the pressure.Because of the great pressures created by the hydraulic jack, it is important that the frame be properly constructed and firmly mounted to the work surface before the pressing operation begins. The following instructions can be given to a welder.Tools Required1. Power Hacksaw2. Metal Band Saw3. Metal Lathe4. Drill Press5. Belt or Disk Grinder6. Arc Welder7. Hand ClampsProcedure (Frame)1. Cut two pieces of 1-3/4" O.D. x 1-3/8" I.D. x 24-1/2 inch long tubing for the uprights.2. Cut one piece of 1-3/4" O.D. x 1-3/8" I.D. x 6-1/2 inch long tubing for the center tube.3. Cut one 3/4" x 2-3/4 x 5-1/2 inch steel bar for the top cross member.4. Cut two pieces of 1-3/4 x 1-3/4 x 8 inch angle iron for the base members.5. Drill two 9/32-inch holes in each base member 1/2 inch from the outer edges.6. Weld the base members, tubes and cross member together as per the drawing.7. Grind all edges to remove any burrs.8. Paint the frame.9. If a mounting board is desired, cut a piece of pine 1-1/4 x 6-1/2 x 12 inches long.10. Center the frame on the board and mark the location of the four mounting holes.11. Drill four 7/8-inch holes 1/4-inch deep to accept the T-nuts.12. Drill four 5/16-inch holes through the mounting board using the same centers created by the 7/8-inch holes.13. Round the edges of the base and sand all surfaces.14. Install four 1/4-20 T-nuts.15. Finish the base with clear lacquer finish.16. Assemble the base to the frame using four 1/4-20 x 1-1/4-inch round head bolts.Procedure (Cylinder)1. Cut a piece of 3-1/2" O.D. x 3-1/4" I.D. tubing 5-3/8 inches long.2. Face both ends on the lathe.3. Cut out a 3-1/2-inch round disk from 1/4-inch plate steel.4. Weld the disk to one end of the tube.5. Drill a series of 3/32-inch holes around the side of the tube on 1/2-inch centers.6. Remove all burrs on the inside and outside of the tube.Procedure (Piston)1. Cut out a 3-3/8-inch disk of 1/4-inch plate steel.2. Cut a 1-3/8" O.D. x 1-1/8" I.D. piece of tubing 1-1/8 inches long.3. Face both ends of the tube.4. Weld the tube in the center of the 3-3/8-inch disk. All welds should be made on the inside of the tube.5. Mount the piston in the lathe and turn the disk to fit the inside diameter of the cylinder. This will be about 3-15/64 inches in diameter.6. Remove any sharp edges.Procedure (Collector Ring)1. Cut the bottom out of a one-gallon plastic bottle. The cut line should be approximately 1-1/2 inches from the bottom of the bottle.2. Make a 1/8 x 1 inch slot at one edge of the bottom outside ring. This will allow the oil to pour into a receiving cup.3. Cut a 1-3/4-inch hole in the center of the bottom, so that the unit will fit over the center tube in the frame.MaterialsFrame2 -- 1-3/4 O.D. x 1-3/8 I.D. x 24-1/2" long H.R.S. (frame tubes)1 -- 1-3/4 O.D. x 1-3/8 I.D. x 6-1/2 inch long H.R.S. (center tube)1 -- 3/4 x 2-3/4 x 5-1/2" flat bar H.R.S. (top cross member)2 -- 1-3/4 x 1-3/4 x 8" angle iron H.R.S. (base members)1 -- 1-1/4 x 6-1/2 x 12" #2 white pine (wood base)4 -- 1/4-20 x 1-1/4 R.H. mounting bolts4 -- 1/4-20 T-nutsBlack enamel for frame (finishing material)Clear lacquer finish for wood base3 -- 1/8" dia. welding rodsCylinder1 -- 1/4 x 3-1/2" dia. C.R.S. disk (top)1 -- 3-1/2 O.D. x 3-1/4 I.D. C.R.S. tube (cylinder)1 -- 1/8 dia. welding rodPiston1 -- 1/4 x 3-3/8 D.A. C.R.S. disk (piston top)1 -- 1-1/4 O.D. x 1 I.D. x 1" long H.R.S. (piston tube)1 -- 1/8 dia. welding rodCollector Ring1 -- Bottom from a one-gallon plastic bottle (oil collector ring)葵花籽脱壳机和油压机由Jeff考克斯-从有机园艺,1979年4月,罗代尔新闻2,500平方尺,一个四口之家每年可以长到足以产生三种葵花籽国产蔬菜沙拉或烹调油和20磅的营养丰富,适合脱皮加仑种子 - 与遗留养活一个冬天的产值,破碎的种子鸟类。
机械外文文献及翻译
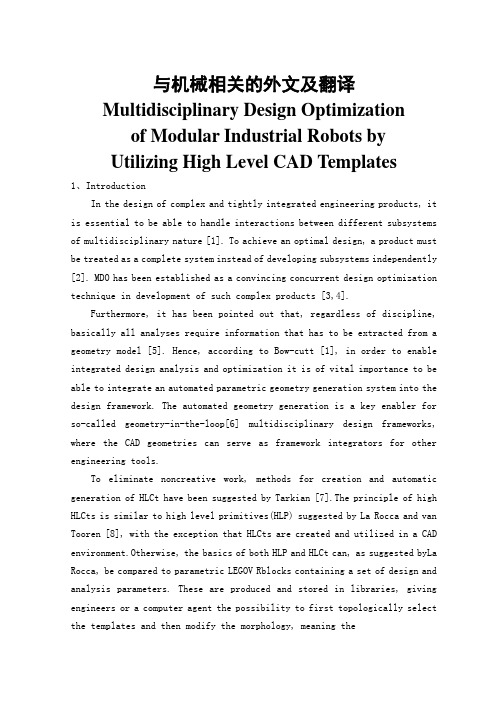
与机械相关的外文及翻译Multidisciplinary Design Optimization of Modular Industrial Robots by Utilizing High Level CAD Templates1、IntroductionIn the design of complex and tightly integrated engineering products, it is essential to be able to handle interactions between different subsystems of multidisciplinary nature [1]. To achieve an optimal design, a product must be treated as a complete system instead of developing subsystems independently [2]. MDO has been established as a convincing concurrent design optimization technique in development of such complex products [3,4].Furthermore, it has been pointed out that, regardless of discipline, basically all analyses require information that has to be extracted from a geometry model [5]. Hence, according to Bow-cutt [1], in order to enable integrated design analysis and optimization it is of vital importance to be able to integrate an automated parametric geometry generation system into the design framework. The automated geometry generation is a key enabler for so-called geometry-in-the-loop[6] multidisciplinary design frameworks, where the CAD geometries can serve as framework integrators for other engineering tools.To eliminate noncreative work, methods for creation and automatic generation of HLCt have been suggested by Tarkian [7].The principle of high HLCts is similar to high level primitives(HLP) suggested by La Rocca and van Tooren [8], with the exception that HLCts are created and utilized in a CAD environment.Otherwise, the basics of both HLP and HLCt can, as suggested byLa Rocca, be compared to parametric LEGOV Rblocks containing a set of design and analysis parameters. These are produced and stored in libraries, giving engineers or a computer agent the possibility to first topologically select the templates and then modify the morphology, meaning theshape,of each template parametrically.2、Multidisciplinary Design FrameworkMDO is a “systematic approach to design space exploration”[17], the implementation of which allows the designer to map the interdisciplinary relations that exist in a system. In this work, the MDO framework consists of a geometry model, a finite element(FE) model, a dynamic model and a basic cost model. The geometry model provides the analysis tools with geometric input. The dynamic model requires mass properties such as mass, center of gravity, and inertia. The FE model needs the meshed geometry of the robot as well as the force and torque interactions based on results of dynamic simulations.High fidelity models require an extensive evaluation time which has be taken into account. This shortcoming is addressed by applying surrogate models for the FE and the CAD models. The models are briefly presented below. 2.1 High Level CAD Template—Geometry ModelTraditionally, parametric CAD is mainly focused on morphological modifications of the geometry. However, there is a limit to morphological parameterization as follows:•The geometries cannot be radically modified.•Increased geometric complexity greatly increases parameterization complexity.The geometry model of the robot is generated with presaved HLCts, created in CATIA V5. These are topologically instantiated with unique internal design variables. Topological parameterization allows deletion, modification, and addition of geometricelements which leads to a much greater design space captured.Three types of HLCts are used to define the industrial robot topologically; Datum HLCt which includes wireframe references required for placement for the Actuator HLCTs and Structure HLCts, as seen Fig.2.Fig. 2 An industrial robot (left) and a modular industrial robot(right) The names of the references that must be provided for each HLCt instantiation are stored in the knowledge base (see Appen-dix A.4), which is searched through by the inference engine. In Appendix A, pseudocode examples describes how the references are retrieved and how they are stored in the knowledge base.The process starts by the user defining the number of degrees of freedom (DOF) of the robot (see Fig. 3) and is repeated until the number of axis (i) is equal to the user defined DOF.In order to instantiate the first Structure HLCt, two Datum and two actuator instances are needed. References from the two Datum instances help orienting the structure in space, while the geometries of the actuator instances, at both ends of the link, are used to construct the actuator attachments, as seen in Figs. 2 and 3. For the remaining links, only one new instance of both datum and actuator HLCts are required, since the datum and actuator instances from adjacent links are already available.Appendix A.2 shows a pseudocode example of an instantiation function. The first instantiated datum HLCt is defined with reference to the absolute coordinate system. The remaining datum HLCt instances are placed in a sequential order, where the coordinate system of previous instances is used as reference for defining the position in space according to user inputs (see also AppendixA.3). Furthermore, the type of each actuator and structure instance is user defined.Fig. 3 The high level CAD template instantiation process Since it is possible to create new HLCts in the utilized CAD tool, the users are not forced to merely choose from the templates available. New HLCts can be created, placed in the database and parametrically inserted into the models.2.2 Dynamic ModelThe objective of performing dynamic simulation of a robot is to evaluate system performance, such as predicting acceleration and time performance, but it also yields loads on each actuated axis, needed for actuator lifetime calculations and subsequent stress analysis based on FE calculations. Thedynamic model in the outlined framework is developed in Modelica using Dymola, and it constitutes a seven-axis robot arm based on the Modelica Standard library [18].The dynamic model receives input from the geometry model,as well as providing output to the FE model, which is further described in Sec. 2.3. However, to better understand the couplings between the models, the Newton –Euler formulation will be briefly discussed. In this formulation, the link velocities and acceleration are iteratively computed, forward recursivelyWhen the kinematic properties are computed, the force and torque interactions between the links are computed backward recursively from the last to the first link2.3 FE Surrogate ModelTo compute the structural strength of the robot, FE models for each robot link is created utilizing CATIA V5, see Fig. 4. For each HLCt, mesh and boundary conditions are manually preprocessed in order to allow for subsequent automation for FE-model creation. The time spent on preprocessing each FE-model is thus extensive. Nonetheless, the obtained parametric FE-model paves way for automated evaluation of a wide span of concepts. Each robot link is evaluated separately with the load conditions extracted from the dynamicmodel. The force (fi-11and fi) and torque (ţi-1and ti) are applied on the surfaceswhere the actuators are attached.2.4 Geometric Surrogate Models.Surrogate models are numerically efficient models to determine the relation between inputs and o utputs of a model [19]. The input variables for the proposed application are the morphological variables thickness and link height as well as a topological variable actuator type. The outputs of the surrogate models are mass m, Inertia I, and center of gravity ri,ci.To identify the most suitable type of surrogate model for the outlined problem, a range of surrogate models types are created and evaluated using 50 samples. The precision of each surrogate model is compared with the values of the original model with 20 new samples. The comparison is made using the relative average absolute error (RAAE) and relative maximum absolute error (RMAE) as specified by Shan et al. [20], as well as the normalized root mean square error (NRMSE), calculated as seen in Eq. (3). All precision metrics are desired to be as low as possible, since low values mean that the surrogate model is accurateThe resulting precision metrics can be seen in Appendix B and the general conclusion is that anisotropic kriging [21], neural networks [22], and radialbasis functions [23] are the most promising surrogate models. To investigate the impact of increasing number of samples, additional surrogate models of those three are fitted using 100 samples, and the results compiled in Appendix B. The resulting NRMSEs for 50 and 100 samples for anistotropic kriging, neural networks, and radial basis functions can be seen in Fig.5. The figures inside the parentheses indicate the number of samples used to fit the surrogate models.Fig. 5 Graph of the NRMSEs for different surrogate models,fitted using 50 and 100 samplesAccording to Fig. 5, anisotropic kriging outperforms the other surrogate models and the doubling of the number of samples usedfor fitting the surrogate model increases the precision dramatically.2.5 FE Surrogate ModelsFor generating FE surrogate models, the anisotropic kriging was also proven to be the most accurate compared to the methods evaluated in Sec. 2.4. Here, one surrogate model is created for each link. Inputs are thickness,actuators, force (fi-11and fi) and torque (ţi-1and ti). The output for eachsurrogate model is maximum stress (MS).A mean error of approximately 9% is reached when running 1400 samples for each link. The reason for the vast number of samples, compared to geometry surrogate models, has to do with a much larger design space.利用高水平CAD模板进行模块化工业机器人的多学科设计优化1 介绍指出,除了规则,基本上所有的分析都需要信息,而这些信息需要从一个几何模型中提取。
- 1、下载文档前请自行甄别文档内容的完整性,平台不提供额外的编辑、内容补充、找答案等附加服务。
- 2、"仅部分预览"的文档,不可在线预览部分如存在完整性等问题,可反馈申请退款(可完整预览的文档不适用该条件!)。
- 3、如文档侵犯您的权益,请联系客服反馈,我们会尽快为您处理(人工客服工作时间:9:00-18:30)。
外文原文:Mechanical designAccording to user requirements of special mechanical working principle, structure, movement, power and energy transmission, various parts of the material and shape size, lubrication methods for design, analysis and calculation and mechanical designTranslate them into a specific description to be made based on the workingprocess. Mechanical design is an important part of mechanical engineering, machinery is produced in the first step, is to determine the mechanical properties of the main factors. Mechanical design goal is: in various limited conditions (such as materials, processing ability, theory and calculation method of design of the best machinery ), i.e. to make optimization design. Optimization design to consider the many requirements, generally : the best performance, the minimum cost, the minimum size and weight, use the reliability, minimum consumption and the minimum environmental pollution. These requirements are often contradictory, but their relative importance for the mechanical type and use vary. The designer's task is to weigh up one thing against another according to the specific circumstance, take all factors into consideration, make the design of the mechanical optimal comprehensive technical and economic effect. In the past, optimization design depends on the designer's knowledge, experience and vision. As the base of mechanical engineering theory and the value engineering, systems analysis and other new disciplines in the development, manufacture and use of technical economy the accumulation of data, as well as computer application, optimize gradually abandon the subjective judgment and rely on scientific computing. In the service of different industry different machinery, application of different working principle, requires a different function and characteristic. Industrial machinery design, especially the whole and the entire system of mechanical design, must be attached to the relevant industrial technology to form an independent discipline. So the design of agricultural machinery, mining machinery, textile machinery, automobile design design design, ship design, design of pump, compressor, turbine design, engine design, machine design, professional mechanical design branch. However, many of these professional design and many common technologies, such as the analysis and synthesis of mechanisms, and can analysis and calculation, engineering materials, strength of materials, transmission, lubrication, sealing, and standardization, reliability, process optimization. In addition, there are research design work of the inherent law and the rationality of the design methods and steps of the new design methodology. The mechanical design of the general technology and rational design methodology brings together into an independent, comprehensive mechanical design is mechanical engineering practice and education workers are working hard.A machine quality basically depends on the quality of design. Manufacturing process on the quality of the machine the role, essence is to realize the design requiredquality. Therefore, the machine's design phase is the key decision machine. Mechanical designThe discussion of the design process refers only to the narrow sense of technical design process. It is a creative process, but also a try best to use the successful experience of the job. Be well to the inheritance and innovation to combine, in order to design a high quality machine. As a complete machine, it is a complex system. To improve the design quality, must have a scientific design program. Although it is not possible for a list of valid in all cases only program, but, according to the long term experience, a machine design process basically can be as shown in Table 2- 1. 1for each stage are respectively brief description. ( a ) the planning stage in accordance with the production or life presents the need to design new machines, the planning stage is a stage of preparation. At this time, to design the machines only a vague notion. In the planning stages, to deal with the design of the machine needs to do the full investigation and analysis. Through the analysis, to further clarify the machine the function that should have, and for the subsequent decision proposed by the environmental, economic, and processing time and other aspects of the identified constraints. Based on this, clearly written assignments on the overall requirements and design details, finally forms the design task book, as the stage summary. The design task book generally should include : the machine function, economy and environmental protection estimates, manufacturing requirements with respect to roughly estimate, basic requirements, and completed the task of design is expected duration. At this point, the requirements and conditions in general can only give a reasonable range, but not the exact number. For example can be used must meet the requirements, minimum requirements, hoping to reach the requirements shall be identified.( two) scheme design stage the stage of design play a key role. In this one phase is also fully demonstrated the design work have multiple solutions ( solution ) features. The function of the machine analysis, is to design of the proposed machine function must meet the requirements of the minimum requirements, and hope to achieve the requirements of comprehensive analysis, namely, these functions can be realized, a number of features with no contradiction, can substitute each other. Finally determines the functional parameters, as the basis for further design. In this step, want appropriate processing need and possibility, the ideal and the reality, development goals and the goals may arise between the contradictory problem. To determine the functional parameters, then propose possible solutions, which is made possible by the plan. Seek solution, according to the driving part, a transmission part and execution part are respectively discussed. , more commonly used method is to first from the operative portion began to discuss. Discuss machine execution part, the first is about the working principle of selection. For example, the design and manufacture of screw machine, its working principle can be used in the cylindrical blank by turning thread approach, can also be used in the cylindrical blanks with thread rolling die rolling thread approach. It puts forward two kinds of different working principles. Its working principle is different, of course, the design of the machine will fundamentally different. Special is to be stressed, must continue to research and development of newworking principle. It is an important way of the development of design technology. According to the different working principle, can develop a variety of different execution mechanism scheme. For example, only the thread cutting, can use the workpiece can only rotate and tool for linear motion to the cutting thread ( such as in lathe cutting thread ), also can make the workpiece is fixed and the cutter to rotate and move to the cutting thread ( such as die processing thread ). That is to say, even for the same kind of work principle, also may have several different structural schemes. The original motivation scheme also can have multiple choice. Because of the power supply of the universality and the electric drive technology development, it can be said that the vast majority of the fixed mechanical is preferred choice as prime mover part of motor. The original motivation for transport, the main thermal engineering machinery and agricultural machinery. Even with the motor as the motive, there are both AC and DC selection, high speed and low speed selection. The transmission part of the scheme is more complicated and diverse. For the same transmission task, by a variety of institutions and different body combination to complete. Therefore, if the prime mover Part IV, said the number of possible schemes, N2and N3respectively representing the transmission part and the execution part number of possible schemes, then the machine the overall number of possible schemes of Ni x N2x N3. The above is only on the machine is composed of three main parts to discuss the. Sometimes, also considering the configuration assistant system, in this regard, books no longer discuss. In so many programmes, technically feasible only a few. On the several feasible solutions, from technology and economy and environmental protection and other aspects of a comprehensive evaluation. Evaluation of the method are many, now with economic evaluation for example omitted description. According to the economic evaluation, it is necessary to take into account the design and manufacture of economy, should cost taken into account when using economy. If the machine structure is more complex, its design and manufacture cost is relatively increased, but its function will be more complete, productivity is higher, so the use of economy is also good. In turn, the structure is relatively simple, the function is not complete machinery, design and manufacturing cost is less, but the use of cost will increase. Evaluation of structural scheme design and manufacturing economy, can also be used to represent the cost of unit efficiency. For example, the unit output power cost, unit cost. Machine evaluation, but also on the machine reliability analysis, the reliability as an evaluation index. From the point of view of reliability, the blind pursuit of complex structure is often not wise. Generally speaking, the system is more complex, then the system reliability is lower. In order to improve the reliability of complex systems, it is necessary to increase the parallel system, which will inevitably increase the cost of the machine. The environmental protection is also design must be carefully considered important aspects. Have a bad effect on the environment of the technical scheme, must detailed analysis, and puts forward the technical maturity of the solution. Through the evaluation, the final decision, according to determine a next step technology design of the schematic diagram or kinematic diagram of mechanism. In the program design phase, to correctly handle the relationship between reference and innovation. Similar machines ought to draw lessons from the successful precedent,originally weak and inconsistent with the current task demands of the part should be improved or changed. We should not only actively innovation, against conservative and copy the original design, but also against a novelty and reasonable original experience abandoned the two wrong tendencies.( three) the technical design stage design goal was to generate assembly sketches and assembly sketches. The sketch design identified the components and parts of the form and basic size, including connections between components, spare, parts of the form and basic size. The final drawing parts drawing, parts and assembly drawings and assembly drawings. In order to determine the main parts of the basic size, must do the following:1) the kinematic design of machines. According to determine the structure scheme, determine the driver parameters ( power, speed, linear speed etc. ). Then do the kinematics calculation, thereby determining the motion components of movement parameters ( speed, velocity, acceleration ). 2) the machine dynamics calculation. Combined with the structure and motion parameters, calculation of the main part of the load size and characteristics. The calculated load, the part is designed, which is applied to parts of the nominal ( or nominal ) load. 3) parts of the working capability design. The known major parts by the nominal load size and characteristics, can be zero, parts of the preliminary design. The designs are based on the ability to work standards, should be zero, parts of the general failure situation, job characteristics, environmental conditions and reasonably develop, generally have the strength, stiffness, vibration, life criterion. Through calculation and comparison, then decided to spare, parts of the basic size. 4) assembly sketches and general assembly sketch design. According to the main components, the basic size, design a component assembly sketches and assembly sketches. The sketch of all parts of the shape and size of the structured design. In this step, need good coordination among the various parts of the structure and size, to consider a comprehensive design of zero, parts of the process of the structure, so that all the parts have the most reasonable configuration. 5) the main parts of the check. There are some parts, in the above third ) step due to the specific structure of undetermined, difficult to conduct detailed work capacity calculation, we can only do a preliminary calculation and design. In the draw assembly design and assembly sketches, all parts of the structure and size are known, the mutually abutting the relations between components also known as. Only then, can be more accurately determined action on the part of load, decisions affecting parts working ability detail factor. Only on this condition, it can and must be for something important or shape and stress condition of complex parts for accurate calculation of. According to the check results, repeatedly modify parts of the structure and size, until satisfied. In the technical design of the various steps in, nearly thirty or forty years with the development of the optimization design technology, more and more shows it can make the selection of structural parameters to achieve the best capacity. Some new numerical method, such as finite element method, can make previously difficult to quantitative calculation problems in obtaining excellent approximation calculation results. For a few very important, the structure is complex and expensive parts, where necessary, must use the model test method to the design, namely according to the preliminary design drawings to create a model, through the experiment, to find out theweak parts of the structure or the redundant section size, thus enhance or reduce the modification to the original design, finally achieving the perfect degree. Mechanical reliability theory for the technical design stage, according to the viewpoint of reliability design of zero, parts of structure and its parameters to make it meet the requirement of reliability evaluation, put forward the improvement design is proposed, which can further improve the quality of machine design. These new design methods and concepts, shall, should be applied in the design and promotion, make get corresponding development. Sketch design completed, according to the sketch has identified parts of basic size, design parts drawing. At this time, there are still a large number of parts structure details to be examined and determined. Design work plan, full consideration should be given to the processing of parts and assembly process, parts during machining process and processing after completion of the inspection requirements and implementation methods. Some details of the arrangement if the parts work ability was worth considering influence, must go back to check the work ability. Finally draw out in addition to the standard outside of all parts of the map. According to the final shape of the parts of the structure and size, to draw the part and assembly drawings and assembly drawings. Through this work, can check out the detail drawings may be hidden in the size and structural errors. People regard this work popularly called paper assembly.( four) the preparation of technical documents phase technology file types, commonly used in the machine design brochures, manuals, and other standard parts list. Design calculation specification, should include the scheme selection and technical design all the conclusions of the content. Preparation for users of machine instructions, should introduce the users machine performance parameters, operation methods, daily maintenance and simple repair method, spare parts catalog. Other technical documents, such as inspection single, purchased parts list, acceptance, as needed and not be compiled. ( five) the computer application in mechanical design with the development of computer technology, the computer in the mechanical design has been increasingly widely used, and there have been many efficient design, analysis software. It can be used in the design phase of projects, can be of different includes large and complex project structural strength, stiffness and dynamic characteristics of precision analysis. At the same time, also in the computer to build virtual prototype, using virtual prototype simulation to verify the design, which realizes the design phase fully assess the feasibility of the design. Can say, the computer technology in machinery design promotion has already changed mechanical design process, it enhances the design quality and efficiency advantages is difficult to estimate. The above briefly introduced the machine design program. Broadly speaking, in the machine manufacture process, appear likely at any time due to technical reasons for modifying the design condition. If you want to modify, should follow certain procedures. Machine factory, should have planned to carry out investigation; in addition, users in the use of the process will also give the design or manufacture sector feedback problems. Design department according to these information, through the analysis, it is also possible for the original design was modified, even remodel. These work, although generalized also belong to design program components, butbelongs to another level of problems, this book will not discuss its specific content. But as design worker, should have a strong sense of social responsibility, to my vision extends into the manufacture, use and waste utilization of total process, repeated constantly improve the design, in order to make the quality of the machine to continue to improve, to better meet the needs of production and lifeAt the beginning of the design before, must make the design task. When the design task is more complex, using three general stages of design, the preliminary design, technical design and working drawing design; when the task is relatively simple, such as the simple mechanical model design, general machinery inherited design or variant design, it will start a design to achieve technical design depth, after review, modification and approval to do working drawing design, and become two stage design. In the three stage design in the preliminary design stage, design of the main steps of : determining the working principle and basic structure, motion design, main spare parts, drawing design, preliminary master plan, the preliminary design review. In the design phase, the main steps are: according to the review comments to modify the design, design of all parts, drawing the new general plan, technical design review. In working drawing design stage, according to the review comments to modify the design, draw all the working drawings and make all technical documents. For the mass or mass production of products, but also shape design. In the design of each step, may be found in the previous step some decided not reasonable, it need to fold back in front of that step, modify the irrational decisions, redo the subsequent design work. 1, making design task it is the preparatory work of the design. Design task is based on the user orders, the market needs and the new research results. Design departments application technology and market information, to be listed options, comparing its advantages and disadvantages, and business departments and users together, formulates the reasonable design target. The new design is particularly important. The goal of the task error will be caused serious damage to the economy, even with the overall failure. 2, determine the working principle and basic structure types such as design task did not make specific provision, designed the first step is to determine the overall program, that is determined by the application of the working principle and the structure types. Such as the design of high power marine diesel engine, the first to determine the two stroke, double action, crosshead, low-speed diesel engine, or by four stroke, single function, medium speed diesel engine. Another example is designed for crushing rock crushing machinery, we must first determine the using extrusion and bending as the main role of the jaw crusher or gyratory crusher, or used to shock as the main role of the single rotor or double rotor impact crusher. 3, exercise design scheme is determined, then the need to apply the mechanism knowledge, choose appropriate institutions in order to obtain the desired motion scheme. The above mentioned jaw crusher on the movable jaw plate to swing into the crushing chamber rock by extrusion, bending and splitting the role and broken, and the swing jaw plate can adopt a double elbow board mechanism of simple swinging, or using a single elbow board mechanism of complex oscillation. In the new design, may need to be integrated with a new mechanism to obtain the required movement, this is often a difficult job. Therefore, designers commonly applied as faras possible the existing and mature mechanism is proposed for sports program. 4, structure design and draw the preliminary general motion design, designers began to carry on the structural design, calculation of the main part of the force, strength, shape, size and weight, and the mapping of the main components, sketch. Then if found out that selection of structure is not feasible, we must adjust or modify structure. At the same time also should be considered a possible cause overheating, excessive wear or vibration part. In this step, the designer through sketching will find each part of the shape, size, such as the proportion of contradiction. In order to enhance or improve certain aspects, may weaken or deterioration on the other hand. Then we must weigh up one thing against another, coordination, in order to achieve the best effect. Sketch by repeatedly revise that initial satisfaction, will be able to draw the preliminary master plan and estimated cost. A preliminary layout strictly according to scale, selection of sufficient view and section. 5, preliminary review of the initial layout drawing, the need to please the type of machinery has experience in the design, manufacture and use of personnel as well as the user or commissioned to design the delegate of the unit to conduct a preliminary examination. A review of results such as that is not designed ( such as weight, volume big, cost is too high, the reliability of structure is the doubt ), shall be to exercise design, and even to other working principle and basic structure. In most cases, to take certain measures to improve design. 6, technology design according to the preliminary examination opinions, to modify the design, and the mapping of all parts and components. On the main parts and components for accurate stress analysis, according to the analysis results of modified parts of the shape, size and other details, and the provisions of material and heat treatment. Determine the machining accuracy of the parts and components and assembly of the assembly conditions. Complete lubrication design, electrical design ( drive and control ). Redraw the map, some important and production machinery can sometimes produce model. Will complete the technical design submitted second review 7, draw working drawings according to second review comments made last modified, can draw formal part drawing, assembly drawing and assembly drawing, writing a parts list, wearing parts list, use the guide and other technical documents. Design responsible person should pay attention to coordinate the parts between the size, check the coupling between tolerance, review some parts of the strength and stiffness. Complete the parts after the start to check the drawings, it is very important work. After careful proofreading to ensure smooth processing assembly drawings. The most reliable method of proofreading is based on drawing good parts drawing heavy draw a general assembly drawing, all contradictions will be shown. In the detail drawing but also the need for two tasks: one is the process of audit, the convenient processing of the parts and the manufacturing cost is reduced the two is the standard audit, so that parts of structure, size, tolerance, heat treatment technology and standard and general parts conform to the standard. 8, trial production and designed for single or small batch production machinery, through the steps to complete the design drawings can be put into production. For batch or lot production machinery, before formal production prototype system to test, function test and identification of, by, then by batch process batch production. In batch production in the problems may also needto design corresponding modification, become available for formal production by using modular design.The design of mechanical parts with many constraints, design criteria design should meet the constraint condition. 1, technical performance standards technical performance includes the function of products, manufacturing and operation status of all property, refers to the static performance, dynamic performance is also used to refer to. For example, the product can transfer power, efficiency, service life, strength, stiffness, friction resistance, wear resistance, thermal stability, vibration characteristics. Technical performance criterion refers to the relevant technical performance to meet the stipulated requirements. For example, the vibration will generate additional dynamic load and stress, especially when the frequency is close to the mechanical systems or parts of the natural frequency, resonance phenomenon will occur, then the amplitude will increase sharply, may lead to the parts and even whole system rapidly damage. Vibration stability criterion is limiting the mechanical systems or parts of the vibration parameters, such as frequency, amplitude, noise in the provisions of the scope of the permit. And as the machine when the fever may cause thermal stress, thermal strain, even will cause thermal damage. Thermal characteristics of guidelines is to restrict the various related thermal parameters ( such as the thermal stress, thermal strain, temperature rise ) in the specified range. 2, standardization and design of mechanical products related to the main standard generally are: the concept of Standardization: involved in the design process of the terminology, symbols, units of measurement shall be in accordance with the standard; objective form standardization: parts, raw materials, equipment and energy structure, size, performance, should be uniform choice. Methods: standardized operation method, measurement method, test method etc should be according to the relevant provisions. Standardization in the entire design process all behavior, must meet the requirements for standardization. Has been released and the design of mechanical parts related standard, from the scope of application of speaking, can be divided into national standards, industry standards and enterprise standards for three grade. From the use of mandatory, can be divided into must be performed and recommended the use of the two kind. 3: reliability, reliability standards for products or components within the prescribed conditions, the expected life to finish regulation function of theprobability of Reliability criterion refers to design products, components or parts should be able to meet the requirements of the reliability requirements in 4, the safety criterion for safety of machinery parts including: Security: defined in terms of external load and within a specified period of time, such as fracture parts not excessive deformation, excessive wear and without loss of stability and so on. Machine safety: a machine to ensure that the required conditions of trouble, can normally achieve functional requirements. Work safety: refers to the operation personnel protection guarantee the safety of humanand health of body and mind. Environmental security: refers to the machines to the surrounding environment and people do not cause the pollution and harmDesign methodology to design thinking to rational process, so that the design can follow certain logic, so that more designers can make good design. It generally。