可靠性维修性标准
产品可靠性与可维护性评估

产品可靠性与可维护性评估产品的可靠性和可维护性是制造商和消费者关心的重要指标。
可靠性指产品在规定条件下连续工作所需的时间和性能稳定性,而可维护性则是指产品在出现故障时进行维修和保养所需的时间和难度。
本文将探讨如何评估产品的可靠性和可维护性,并提供相关的方法和工具。
一、可靠性评估方法1. 故障率评估故障率是评估产品可靠性的重要指标之一。
它描述了在特定时间和条件下产品出现故障的概率。
常用的故障率计算方法包括可靠性预测模型和可靠性增长模型。
可靠性预测模型一般基于历史故障数据和可靠性理论,通过统计分析和模拟计算来预测产品的故障率。
可靠性增长模型则是指通过产品在运行中不断收集的故障数据来估计故障率。
2. 评估产品寿命产品寿命是产品可靠性的重要指标之一。
评估产品寿命时,可以考虑多种因素,如材料质量、工艺技术、环境条件等。
通过实验室测试和实际使用中数据的收集,可以确定产品的寿命分布函数,并计算出平均寿命和可靠度。
3. 可靠性验证在产品开发过程中,进行可靠性验证是必要的一步。
可靠性验证通过实际测试和验证,检验产品是否符合设计要求和用户需求。
常用的可靠性验证方法包括加速寿命试验、可靠度增长试验和可靠性确认试验。
其中,加速寿命试验通过加速产品的工作条件来提前暴露潜在的故障,以评估产品的可靠性。
可靠度增长试验则通过长时间运行和收集故障数据来验证产品的可靠性。
而可靠性确认试验则是通过对已修复故障产品进行再测试,以确保产品已修复并符合可靠性要求。
二、可维护性评估方法1. 故障诊断与分析故障诊断与分析是评估产品可维护性的重要手段之一。
通过对产品故障进行诊断和分析,可以确定故障原因和解决方法。
常用的故障诊断与分析方法包括故障树分析、故障模式与影响分析和故障树分析等。
2. 维修性评估维修性评估是评估产品可维护性的关键环节之一。
它包括维修时间、维修难度、维修工具和维修手册等方面的评估。
通过对维修过程的模拟和分析,可以评估产品的维修性,并提出相应的改进措施。
可靠性试验标准
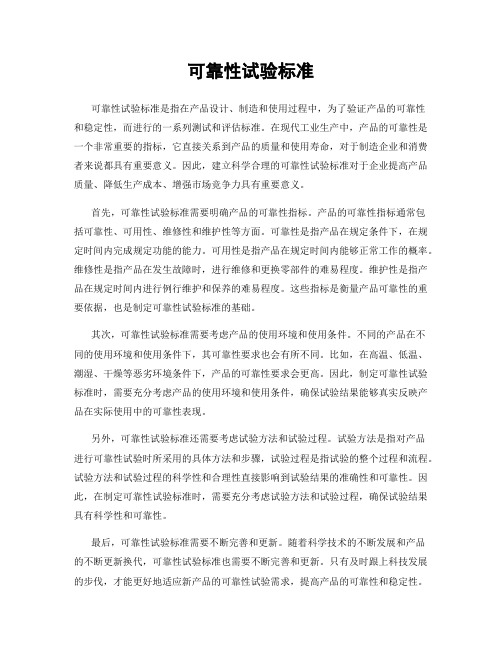
可靠性试验标准可靠性试验标准是指在产品设计、制造和使用过程中,为了验证产品的可靠性和稳定性,而进行的一系列测试和评估标准。
在现代工业生产中,产品的可靠性是一个非常重要的指标,它直接关系到产品的质量和使用寿命,对于制造企业和消费者来说都具有重要意义。
因此,建立科学合理的可靠性试验标准对于企业提高产品质量、降低生产成本、增强市场竞争力具有重要意义。
首先,可靠性试验标准需要明确产品的可靠性指标。
产品的可靠性指标通常包括可靠性、可用性、维修性和维护性等方面。
可靠性是指产品在规定条件下,在规定时间内完成规定功能的能力。
可用性是指产品在规定时间内能够正常工作的概率。
维修性是指产品在发生故障时,进行维修和更换零部件的难易程度。
维护性是指产品在规定时间内进行例行维护和保养的难易程度。
这些指标是衡量产品可靠性的重要依据,也是制定可靠性试验标准的基础。
其次,可靠性试验标准需要考虑产品的使用环境和使用条件。
不同的产品在不同的使用环境和使用条件下,其可靠性要求也会有所不同。
比如,在高温、低温、潮湿、干燥等恶劣环境条件下,产品的可靠性要求会更高。
因此,制定可靠性试验标准时,需要充分考虑产品的使用环境和使用条件,确保试验结果能够真实反映产品在实际使用中的可靠性表现。
另外,可靠性试验标准还需要考虑试验方法和试验过程。
试验方法是指对产品进行可靠性试验时所采用的具体方法和步骤,试验过程是指试验的整个过程和流程。
试验方法和试验过程的科学性和合理性直接影响到试验结果的准确性和可靠性。
因此,在制定可靠性试验标准时,需要充分考虑试验方法和试验过程,确保试验结果具有科学性和可靠性。
最后,可靠性试验标准需要不断完善和更新。
随着科学技术的不断发展和产品的不断更新换代,可靠性试验标准也需要不断完善和更新。
只有及时跟上科技发展的步伐,才能更好地适应新产品的可靠性试验需求,提高产品的可靠性和稳定性。
总之,可靠性试验标准是产品质量管理的重要环节,对于提高产品的可靠性和稳定性具有重要意义。
设备维修可靠性评分表

设备维修可靠性评分表1. 背景设备维修可靠性评分表是用于评估设备维修工作质量的工具。
通过对设备维修过程中的关键指标进行评分,可以对设备维修可靠性进行客观、全面的评估,帮助改进维修流程和提高设备维修质量。
2. 评分指标2.1 故障现象描述评分标准:根据故障现象的描述,评估是否准确和清晰。
评分范围为1-5分,5分表示描述准确、清晰,1分表示描述不准确、模糊。
2.2 维修方案制定评分标准:评估维修方案是否科学、合理,并考虑到设备的特性和维修的成本。
评分范围为1-5分,5分表示方案科学、合理,1分表示方案不科学、不合理。
2.3 维修工具和设备评分标准:评估维修工具和设备是否适用于维修工作,并是否充分准备。
评分范围为1-5分,5分表示工具和设备适用、充分准备,1分表示工具和设备不适用、准备不充分。
2.4 维修过程操作规范评分标准:评估维修过程中的操作是否规范、符合要求。
评分范围为1-5分,5分表示操作规范、符合要求,1分表示操作不规范、不符合要求。
2.5 维修效果验证评分标准:评估维修后设备是否能够正常工作,并进行必要的检测和验证。
评分范围为1-5分,5分表示设备正常工作、验证完善,1分表示设备不能正常工作、未进行验证。
3. 总分计算与分级根据上述评分指标的得分,将各项得分相加,得出总分。
总分根据以下规则进行分级:- 总分大于等于18分:维修可靠性极高。
- 总分大于等于15分小于18分:维修可靠性良好。
- 总分大于等于12分小于15分:维修可靠性一般。
- 总分小于12分:维修可靠性较低。
4. 使用方法使用设备维修可靠性评分表时,根据实际情况对每个评分指标进行评估,并记录得分。
然后根据总分进行分级,以评估维修可靠性的水平。
根据评估结果,可以分析维修过程中的问题,并采取相应的措施进行改进。
5. 注意事项- 评分应该客观、公正,避免主观因素影响评估结果。
- 评分过程中应根据实际情况进行评估,避免凭空臆测或情绪化评价。
可靠性维修性标准术语
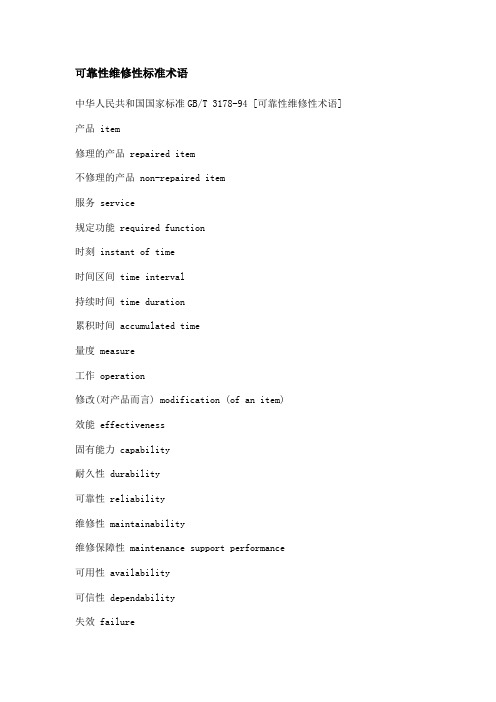
可靠性维修性标准术语中华人民共和国国家标准GB/T 3178-94 [可靠性维修性术语] 产品 item修理的产品 repaired item不修理的产品 non-repaired item服务 service规定功能 required function时刻 instant of time时间区间 time interval持续时间 time duration累积时间 accumulated time量度 measure工作 operation修改(对产品而言) modification (of an item)效能 effectiveness固有能力 capability耐久性 durability可靠性 reliability维修性 maintainability维修保障性 maintenance support performance可用性 availability可信性 dependability失效 failure致命失效 critical failure非致命失效 non-critical failure误用失效 misuse failure误操作失效 mishandling failure弱质失效 weakness failure设计失效 design failure制造失效 manufacture failure老化失效;耗损失效 ageing failure; wear-out failure突然失效 sudden failure渐变失效;漂移失效 gradual failure; drift failure灾变失效 cataleptic failure关联失效 relevant failure非关联失效 non-relevant failure独立失效 primary failure从属失效 secondary failure失效原因 failure cause失效机理 failure mechanism系统性失效;重复性失效 systematic failure; reproducible failure 完全失效 complete failure退化失效 degradation failure部分失效 partial failure故障 fault致命故障 critical fault非致命故障 non-critical fault重要故障 major fault次要故障 minor fault误用故障 misuse fault误操作故障 mishandling fault弱质故障 weakness fault设计故障 design fault制造故障 manufacturing fault老化故障;耗损故障 ageing fault; wear-out fault程序敏感故障 programme-sensitive fault数据敏感故障 data-sensitive fault完全故障;功能阻碍故障 complete fault; function-preventing fault 部分故障 partial fault持久故障 persistent fault间歇故障 intermittent fault确定性故障 determinate fault非确定性故障 indeterminate fault潜在故障 latent fault系统性故障 systematic fault故障模式 fault mode故障产品 faulty item差错 error失误 mistake工作状态 operating state不工作状态 non-operating state待命状态 standby state闲置状态;空闲状态 idle state; free state不能工作状态 disable state; outage外因不能工作状态 external disabled state不可用状态;内因不能工作状态 down state; internal disabled state可用状态 up time忙碌状态 busy state致命状态 critical state维修 maintenance维修准则 maintenance philosophy维修方针 maintenance policy维修作业线 maintenance echelon; line of maintenance维修约定级 indenture level (for maintenance)维修等级 level of maintenance预防性维修 preventive maintenance修复性维修 corrective maintenance受控维修 controlled maintenance计划性维修 scheduled maintenance非计划性维修 unscheduled maintenance现场维修 on-site maintenance; in sits maintenance; field maintenance 非现场维修 off-site maintenance遥控维修 remote maintenance自动维修 automatic maintenance逾期维修 deferred maintenance基本的维修作业 elementary maintenance activity维修工作 maintenance action; maintenance task修理 repair故障识别 fault recognition故障定位 fault localization故障诊断 fault diagnosis故障修复 fault correction功能核查 function check-out恢复 restoration; recovery监测 supervision; monitoring维修的实体 maintenance entity影响功能的维修 function-affecting maintenance妨碍功能的维修 function-preventing maintenance减弱功能的维修 function-degrading maintenance不影响功能的维修 function-permitting maintenance维修时间 maintenance time维修人时 MMH; maintenance man-hour实际维修时间 active maintenance time预防性维修时间 preventive maintenance time修复性维修时间 corrective maintenance time实际的预防性维修时间 active preventive maintenance time 实际的修复性维修时间 active corrective maintenance time 未检出故障时间 undetected fault time管理延迟(对于修复性维修) administrative delay后勤延迟 logistic delay故障修复时间 fault correction time技术延迟 technical delay核查时间 check-out time故障诊断时间 fault diagnosis time故障定位时间 fault localization time修理时间 repair time工作时间 operating time不工作时间 non-operating time需求时间 required time无需求时间 non-required time待命时间 standby time闲置时间 idle time; free time不能工作时间 disabled time不可用时间 down time累积不可用时间 accumulated down time外因不能工作时间 external disabled time; external loss time 可用时间 up time首次失效前时间 time to first failure失效前时间 time to failure失效间隔时间 time between failures失效间工作时间 operating time between failures恢复前时间 time to restoration; time to recovery使用寿命 useful life早期失效期 early failure period恒定失效密度期 constant failure intensity period恒定失效率期 constant failure rate period耗损失效期 wear-out failure period瞬时可用度 instantaneous availability瞬时不可用度 instantaneous unavailability平均可用度 mean availability平均不可用度 mean unavailability渐近可用度 asymptotic availability稳态可用度 steady-state availability渐近不可用度 asymptotic unavailability稳态不可用度 steady-state unavailability渐近平均可用度 asymptotic mean availability渐近平均不可用度 asymptotic mean unavailability平均可用时间 mean up time平均累积不可用时间 mean accumulated down time可靠度 reliability瞬时失效率 instantaneous failure rate平均失效率 mean failure rate瞬时失效密度 instantaneous failure intensity平均失效密度 mean failure intensity平均首次失效前时间 MTTFF; mean time to first failure 平均失效前时间 MTTF; mean time to failure平均失效间隔时间 MTBF; mean time between failures平均失效间工作时间 MOTBF; mean operating time between failure 失效率加速系数 failure rate acceleration factor失效密度加速系数 failure intensity acceleration factor维修度 maintainability瞬时修复率 instantaneous repair rate平均修复率 mean repair rate平均维修人时 mean maintenance man-hour平均不可用时间 MDT; mean down time平均修理时间 MRT; mean repair timeP-分位修理时间 P-fractile repair time平均实际修复性维修时间 mean active corrective maintenance time 平均恢复前时间 MTTR; mean time to restoration故障识别比 fault coverage修复比 repair coverage平均管理延迟 MAD; mean administrative delayP-分位管理延迟 P-fractile administrative delay平均后勤延迟 MLD; mean logistic delayP-分位后勤延迟 P-fractile logistic delay验证试验 compliance test测定试验 determination test实验室试验 laboratory test现场试验 field test耐久性试验 endurance test加速试验 accelerated test步进应力试验 step stress test筛选试验 screening test时间加速系数 time acceleration factor维修性检验 maintainability verification维修性验证 maintainability demonstration观测数据 observed data试验数据 test data现场数据 field data基准数据 reference data冗余 redundancy工作冗余 active redundancy备用冗余 standby redundancy失效安全 fail safe故障裕度 fault tolerance故障掩盖 fault masking预计 prediction可靠性模型 reliability model可靠性预计 reliability prediction可靠性分配 reliability allocation; reliability apportionment故障模式与影响分析 FMEA; fault modes and effects analysis故障模式影响与危害度分析 FMECA; fault modes, effects and criticality analysis故障树分析 FTA; fault tree analysis应力分析 stress analysis可靠性框图 reliability block diagram故障树 fault tree状态转移图 state-transition diagram应力模型 stress model故障分析 fault analysis失效分析 failure analysis维修性模型 maintainability model维修性预计 maintainability prediction维修树 maintenance tree维修性分配 maintainability allocation; maintainability apportionment 老练 burn in可靠性增长 reliability growth可靠性改进 reliability improvement可靠性和维修性管理 reliability and maintainability management可靠性和维修性保证 reliability and maintainability assurance可靠性和维修性控制 reliability and maintainability control可靠性和维修性大纲 reliability and maintainability programme可靠性和维修性计划 reliability and maintainability plan可靠性和维修性审计 reliability and maintainability audit可靠性和维修性监察 reliability and maintainability surveillance设计评审 design review真实的 true预计的 predicted外推的 extrapolated估计的 estimated固有的 intrinsic; inherent 使用的 operational平均的 meanP-分位 P-fractile瞬时的 instantaneous稳态的 steady state。
制造工艺中的产品可靠性与维修性
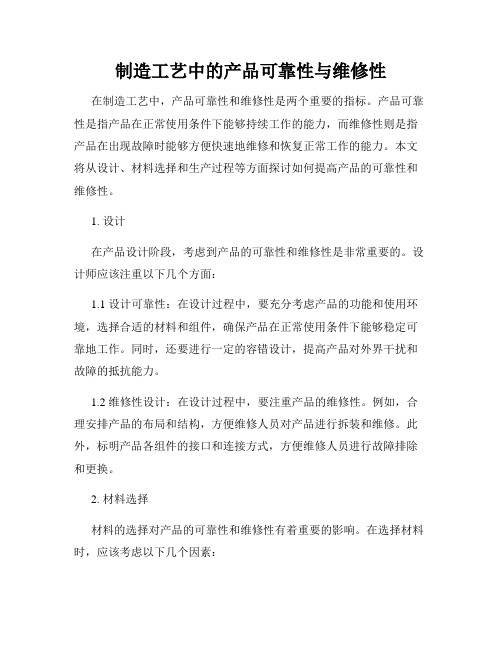
制造工艺中的产品可靠性与维修性在制造工艺中,产品可靠性和维修性是两个重要的指标。
产品可靠性是指产品在正常使用条件下能够持续工作的能力,而维修性则是指产品在出现故障时能够方便快速地维修和恢复正常工作的能力。
本文将从设计、材料选择和生产过程等方面探讨如何提高产品的可靠性和维修性。
1. 设计在产品设计阶段,考虑到产品的可靠性和维修性是非常重要的。
设计师应该注重以下几个方面:1.1 设计可靠性:在设计过程中,要充分考虑产品的功能和使用环境,选择合适的材料和组件,确保产品在正常使用条件下能够稳定可靠地工作。
同时,还要进行一定的容错设计,提高产品对外界干扰和故障的抵抗能力。
1.2 维修性设计:在设计过程中,要注重产品的维修性。
例如,合理安排产品的布局和结构,方便维修人员对产品进行拆装和维修。
此外,标明产品各组件的接口和连接方式,方便维修人员进行故障排除和更换。
2. 材料选择材料的选择对产品的可靠性和维修性有着重要的影响。
在选择材料时,应该考虑以下几个因素:2.1 材料的质量和可靠性:选择质量可靠的材料,能够降低产品的故障率和维修率。
通过与供应商建立长期合作关系,确保材料的质量和稳定性。
2.2 材料的可维修性:选择易于维修和更换的材料,能够提高产品的维修性。
例如,选择模块化设计的组件,方便维修人员对故障组件进行更换,而不需要对整个产品进行维修。
3. 生产过程在生产过程中,严格控制工艺流程和质量管理,可以有效提高产品的可靠性和维修性。
3.1 工艺流程管理:制定详细的工艺流程和操作规范,确保每个环节都按照标准进行操作。
此外,建立质量检测点,对每个生产环节进行监控和检测,及时发现并解决问题。
3.2 质量管理:建立完善的质量管理体系,包括质量管理人员的培训和技能提升,建立质量评估和反馈机制。
通过不断改进和优化质量管理,提高产品的可靠性和维修性。
4. 用户培训与支持除了以上的工艺措施,产品的用户培训和支持也是提高产品可靠性和维修性的重要环节。
机械设计中的可靠性与维修性分析
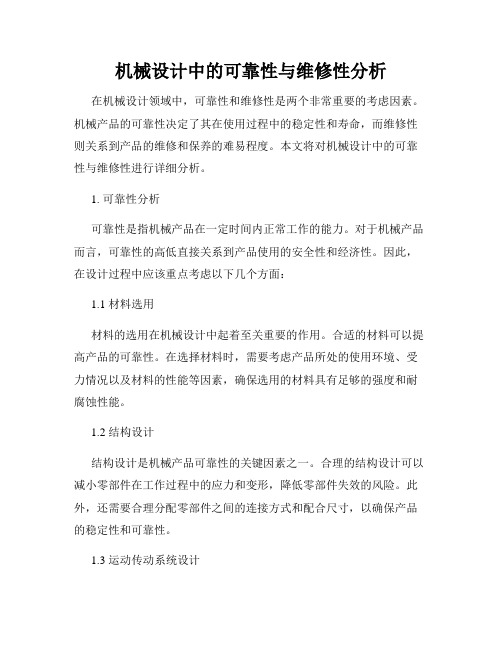
机械设计中的可靠性与维修性分析在机械设计领域中,可靠性和维修性是两个非常重要的考虑因素。
机械产品的可靠性决定了其在使用过程中的稳定性和寿命,而维修性则关系到产品的维修和保养的难易程度。
本文将对机械设计中的可靠性与维修性进行详细分析。
1. 可靠性分析可靠性是指机械产品在一定时间内正常工作的能力。
对于机械产品而言,可靠性的高低直接关系到产品使用的安全性和经济性。
因此,在设计过程中应该重点考虑以下几个方面:1.1 材料选用材料的选用在机械设计中起着至关重要的作用。
合适的材料可以提高产品的可靠性。
在选择材料时,需要考虑产品所处的使用环境、受力情况以及材料的性能等因素,确保选用的材料具有足够的强度和耐腐蚀性能。
1.2 结构设计结构设计是机械产品可靠性的关键因素之一。
合理的结构设计可以减小零部件在工作过程中的应力和变形,降低零部件失效的风险。
此外,还需要合理分配零部件之间的连接方式和配合尺寸,以确保产品的稳定性和可靠性。
1.3 运动传动系统设计运动传动系统是机械产品中常见的关键组成部分。
在设计过程中,需要根据产品的工作要求和使用寿命,选择合适的传动方式和传动元件。
同时,还需要注意传动链路的设计,减小传动效率损失和传动误差,提高产品的可靠性。
2. 维修性分析维修性是指机械产品在出现故障或需要保养时能够方便、快捷地进行维修和保养的能力。
良好的维修性设计可以减少产品的停机时间和维修成本,提高设备的可用性。
以下是维修性设计的一些重要考虑因素:2.1 模块化设计模块化设计是提高产品维修性的有效手段之一。
将机械产品分解为多个独立的模块或部件,每个模块可以独立进行维修或更换。
这样在出现故障时只需要更换具体的模块而无需对整个产品进行维修,大大缩短了维修时间。
2.2 易损部件设计针对机械产品中容易出现故障的部件,设计时可以采用易损部件的形式。
易损部件可以在出现故障时方便地进行更换,减少了维修的难度和成本。
同时,还可以提供易损部件的备件,进一步提高产品的可用性。
可靠性等级的划分标准
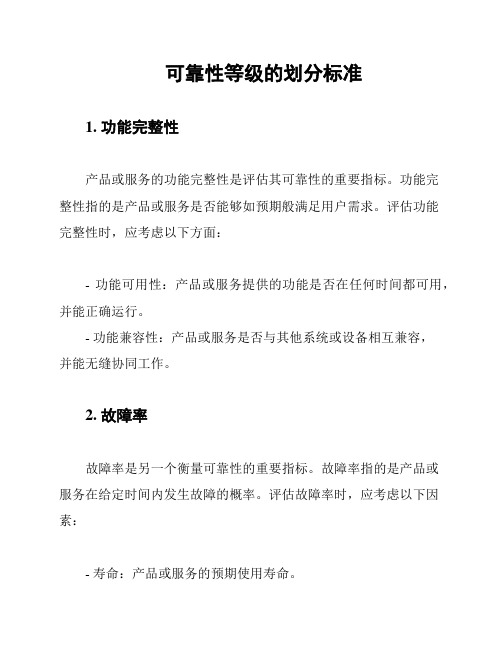
可靠性等级的划分标准
1. 功能完整性
产品或服务的功能完整性是评估其可靠性的重要指标。
功能完
整性指的是产品或服务是否能够如预期般满足用户需求。
评估功能
完整性时,应考虑以下方面:
- 功能可用性:产品或服务提供的功能是否在任何时间都可用,并能正确运行。
- 功能兼容性:产品或服务是否与其他系统或设备相互兼容,
并能无缝协同工作。
2. 故障率
故障率是另一个衡量可靠性的重要指标。
故障率指的是产品或
服务在给定时间内发生故障的概率。
评估故障率时,应考虑以下因素:
- 寿命:产品或服务的预期使用寿命。
- 维修时间:当产品或服务发生故障时,维修或恢复正常运行所需的时间。
3. 可维护性
可维护性是指产品或服务在发生故障时的易修复程度。
评估可维护性时,应考虑以下要素:
- 维修性:产品或服务是否容易维修,并且能够快速恢复正常运行。
- 维护成本:维修或保养产品或服务所需的成本(如人力、材料、时间等)。
4. 数据安全性
数据安全性是评估可靠性的另一个重要因素,特别适用于涉及敏感信息的产品或服务。
评估数据安全性时,应考虑以下要素:
- 数据保密性:产品或服务是否能保护用户数据不被未授权访问。
- 数据完整性:产品或服务是否能确保数据不被篡改或丢失。
根据以上要素,企业可以综合考虑确定适合自身产品或服务的可靠性等级。
企业可以定义不同的可靠性等级,如高可靠性、中可靠性和低可靠性,以满足不同用户需求。
> 注意:本文档所提供的划分标准仅供参考,具体的可靠性等级划分标准应根据企业的实际情况进行调整。
gjb2225a-2008标准
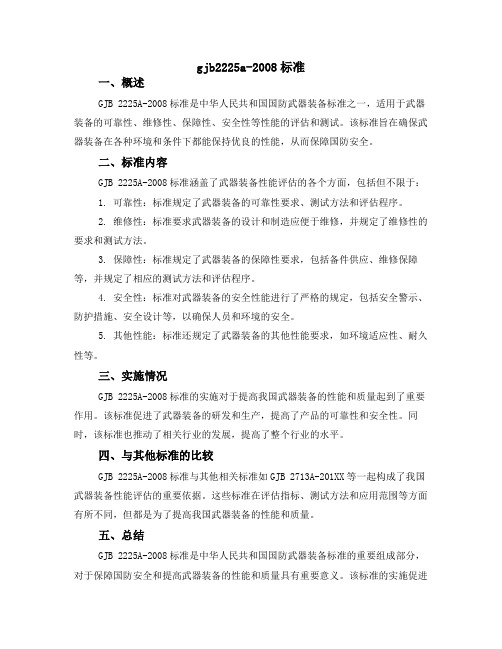
gjb2225a-2008标准一、概述GJB 2225A-2008标准是中华人民共和国国防武器装备标准之一,适用于武器装备的可靠性、维修性、保障性、安全性等性能的评估和测试。
该标准旨在确保武器装备在各种环境和条件下都能保持优良的性能,从而保障国防安全。
二、标准内容GJB 2225A-2008标准涵盖了武器装备性能评估的各个方面,包括但不限于:1. 可靠性:标准规定了武器装备的可靠性要求、测试方法和评估程序。
2. 维修性:标准要求武器装备的设计和制造应便于维修,并规定了维修性的要求和测试方法。
3. 保障性:标准规定了武器装备的保障性要求,包括备件供应、维修保障等,并规定了相应的测试方法和评估程序。
4. 安全性:标准对武器装备的安全性能进行了严格的规定,包括安全警示、防护措施、安全设计等,以确保人员和环境的安全。
5. 其他性能:标准还规定了武器装备的其他性能要求,如环境适应性、耐久性等。
三、实施情况GJB 2225A-2008标准的实施对于提高我国武器装备的性能和质量起到了重要作用。
该标准促进了武器装备的研发和生产,提高了产品的可靠性和安全性。
同时,该标准也推动了相关行业的发展,提高了整个行业的水平。
四、与其他标准的比较GJB 2225A-2008标准与其他相关标准如GJB 2713A-201XX等一起构成了我国武器装备性能评估的重要依据。
这些标准在评估指标、测试方法和应用范围等方面有所不同,但都是为了提高我国武器装备的性能和质量。
五、总结GJB 2225A-2008标准是中华人民共和国国防武器装备标准的重要组成部分,对于保障国防安全和提高武器装备的性能和质量具有重要意义。
该标准的实施促进了相关行业的发展,提高了整个行业的水平。
在未来的发展中,我们应该继续关注国际标准和先进技术,不断完善和提升我国武器装备的性能和质量。
- 1、下载文档前请自行甄别文档内容的完整性,平台不提供额外的编辑、内容补充、找答案等附加服务。
- 2、"仅部分预览"的文档,不可在线预览部分如存在完整性等问题,可反馈申请退款(可完整预览的文档不适用该条件!)。
- 3、如文档侵犯您的权益,请联系客服反馈,我们会尽快为您处理(人工客服工作时间:9:00-18:30)。
可靠性维修性标准
GJB450A-2004装备可靠性工作通用要求
GJB368A-1994装备维修性大纲
GJB900-1990系统安全性通用大纲
GJB3872 装备综合保障通用要求
GJB2547 装备测试性大纲
GJB4239 装备环境工程通用要求
GJB1909 装备可靠性维修性保障性要求论证
GJB3206-1998技术状态管理
GJB 5000 军用软件研制能力成熟度模型
可靠性---产品在规定的条件下和规定的时间内,完成规定的功能的能力。
基本可靠性:
产品在规定的条件下,无故障的持续时间或概率。
基本可靠性费用产品对维修人力的要求,确定基本可靠性参数时应统计产品的所有寿命单元和所有的故障。
任务可靠性
国家军用标准要求组织按GJB450A和GJB368A标准的要求建立可靠性工作系统负责可靠性和维修性管理,进行可靠性和维修性分析,开展可靠性和维修性设计,进行可靠性和维修性试验、验证和评
估等工作。
为了确定和达到产品的可靠性要求而开展的一系列的技术和管理活动称为可靠性工程。
可靠性工程活动涉及到装备全寿命过程的各阶段,目的是确保新研制和改型的装备达到可靠性要求,保证和提高现役装备的可靠性水平,满足装备战备完好性和任务成功性要求,降低保障资源要求,减少全寿命周期费用。
维修性---产品在规定的条件下和规定的时间内,按规定的程序和方法进行维修时,保持和恢复到规定状态的能力。
GJB368A-1994装备维修性大纲标准规定的维修性工作的目标是确保研制、生产或改进的装备达到规定的维修性要求,以提高装备的战备完好性和任务成功性、减少对维修人力及其资源的要求,降低全寿命费用,并为装备全寿命管理提供必要的信息。
标准规定了12个工作项目:
101制定维修性工作计划
102对转承制方和供方的监督和控制
103维修性工作评审
104建立数据收集、分析和纠正措施系统
201建立维修性模型
202维修性分配
203维修性设计
204故障模式及影响分析--维修性信息
205维修性分析
206维修性设计准则
207为详细的维修保障计划和保障性分析准备输入
301维修性和测试性验证
维修性常用指标:
平均修复时间MTTR
维修活动平均直接维修工时DMMH/MA
重要部件更换时间
测试性---产品能及时并准确地确定其状态(可工作、不可工作或性能下降),并隔离其内部故障的一种设计特性。
GJB2547< 装备测试性大纲标准>规定的测试性工作内容:1制定测试性工作计划
2制定诊断方案和测试性要求
3进行测试性设计
4评审测试性工作
5验证测试性要求
测试性常用指标:
故障检测率
故障隔离率
虚警率
保障性---装备的设计特性和计划的资源满足平时战备和战时使用要求的能力。
GJB3872 <装备综合保障通用要求>标准规定综合保障的主要任务:
1、确定装备系统的保障性要求
2、在装备的设计过程中进行保障性设计
3、规划并及时研制所需的保障资源
4、建立经济而有效的保障系统,使装备获得所需的保障
GJB3872 <装备综合保障通用要求>标准规定工作项目:
5.1综合保障的规划与管理
1、制定综合保障计划。
2、制定综合保障工作计划。
3、综合保障评审。
4、转承制方和供应方的监督与控制。
5.2规划保障
1、规划使用保障
2、规划维修
5.3研制与提供保障资源
5.4装备系统的部署保障
5.5保障性试验和分析
安全性---不发生事故的能力。
事故---造成人员伤亡、职业病、设备损坏或财产损失的一个或
一系列意外的事件。
危险---可能导致事故的状态。
危险可能性---产生某一危险的事件的总的可能性。
危险严重性---对某种危险可能引起的事故可信的最严重程度的估计。
风险—用危险的可能性和危险的严重性表示的发生事故的
可能程度。
组织按GJB900标准的要求进行安全性分析,识别危险源,控制不安全因素,开展安全性设计、试验、验证和评估,保证人员、设备、产品安全。
GJB900-1990《系统安全性通用大纲》要求的工作项目:(27个)系统安全性工作项目实施表
GC----仅设计更改时适用
S----根据需要选用
NA----不适用
设施的安全性工作项目实施表(略)
环境适应性---装备(产品)在其寿命期预计可能遇到的各种环境下能实现其所有预定功能和性能和(或)不被破坏的能力。
GJB450A-2004装备可靠性工作通用要求标准规定了32个工作项目:
可靠性建模-----建立产品各单元之间的可靠性逻辑关系及数学模型。
可靠性分配-----将可靠性定量要求分配到低层次的产品。
比例分配法
可靠性预计-----提供产品定量的可靠性信息,估计固有的可靠性水平,以确定是否能够达到规定的要求。
故障模式、影响及危害分析(FMECA)----通过自上而下方法,分析产品中每一个潜在的故障模式、原因及其影响的严酷度等级并根据故障模式影响的严酷度及其发生的频率进行危害性分析。
功能分析(或飞行事件保证链分析)
潜通路分析
最坏情况分析
结构力学分析
可靠性设计方法:
冗差设计、热设计、电磁兼容设计、环境适应性设计、降额设计、冗余设计
技术状态管理
按GJB3206-1998技术状态管理的要求,策划和实施技术状态管理活动。
技术状态管理活动应从方案阶段开始,在产品设计和开发、采购、生产、试验、安装、服务、使用直至产品处置的全寿命周期内,应能准确清楚地表明产品的技术状态,
技术状态标识
技术状态控制
技术状态纪实
技术状态审核
技术状态基线:在技术状态项目研制过程中的某一特定时刻,被正式确认并被作为今后研制、生产活动基准的技术文件。
分:功能基线
分配基线
产品基线
计算机软件
软件配置
在软件生存周期各阶段产生的各种形式和各种版本的文档、程序、数据及环境的集合。
软件配置项
为了配置管理的目的而作为一个单位来看待的软件成分,通常为软件配置中的一个元素。
软件配置管理
为保证软件配置项的完整性和正确性,在整个软件生存周期内应用配置管理的过程。
软件开发库
在软件生存周期中,存放软件配置项的集合。
软件受控库
在软件生存周期中,存放已通过测试或评审且作为阶段性产品的软件配置项的集合。
软件产品库
在软件生存周期中,存放已定型(鉴定)且供交付、生产、检验验收的软件配置项的集合。
需求分析—概要设计—详细设计---软件实现—软件测试—软件验收--交付,全过程实施严格的工程化管理。
标准化
制定工程项目标准化大纲,确定选用标准范围和开展产品标准化工作,并对设计和开发过程中产品标准化大纲进行评审、贯彻实施和监督检查。
风险分析
标准要求对产品实现各阶段都应进行风险分析和评估,形成各阶段风险分析文件,并提供给顾客。
这里讲的风险主要是指对在规定的费用、进度和技术的约束条件下,不能实现项目目标的可能性及所
导致的后果的一种度量。
在对产品实现过程进行策划时,应考虑到产品实现过程中可能出现的风险,并对风险分析和评估工作做好安排。
风险分析和评估包括:识别哪些产品单元存在风险?风险发生的概率有多大、后果如何?以便找出关键的风险事件,有针对性地采取应对措施。
可靠性、维修性、测试性工作项目
续2
GJB1406 产品质量保证大纲要求
其中M---强烈推荐,通常要求采用C---根据具体情况而采用
NA----不采用。