氯乙烯合成工艺设计
化工PVC各工段工艺流程
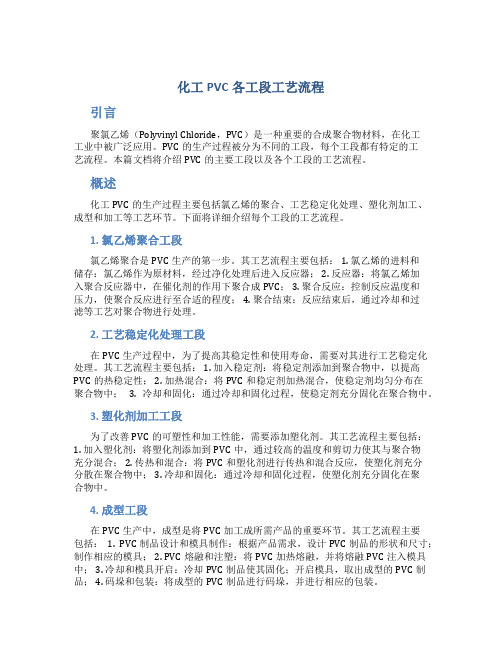
化工PVC各工段工艺流程引言聚氯乙烯(Polyvinyl Chloride,PVC)是一种重要的合成聚合物材料,在化工工业中被广泛应用。
PVC的生产过程被分为不同的工段,每个工段都有特定的工艺流程。
本篇文档将介绍PVC的主要工段以及各个工段的工艺流程。
概述化工PVC的生产过程主要包括氯乙烯的聚合、工艺稳定化处理、塑化剂加工、成型和加工等工艺环节。
下面将详细介绍每个工段的工艺流程。
1. 氯乙烯聚合工段氯乙烯聚合是PVC生产的第一步。
其工艺流程主要包括: 1. 氯乙烯的进料和储存:氯乙烯作为原材料,经过净化处理后进入反应器; 2. 反应器:将氯乙烯加入聚合反应器中,在催化剂的作用下聚合成PVC; 3. 聚合反应:控制反应温度和压力,使聚合反应进行至合适的程度; 4. 聚合结束:反应结束后,通过冷却和过滤等工艺对聚合物进行处理。
2. 工艺稳定化处理工段在PVC生产过程中,为了提高其稳定性和使用寿命,需要对其进行工艺稳定化处理。
其工艺流程主要包括: 1. 加入稳定剂:将稳定剂添加到聚合物中,以提高PVC的热稳定性; 2. 加热混合:将PVC和稳定剂加热混合,使稳定剂均匀分布在聚合物中; 3. 冷却和固化:通过冷却和固化过程,使稳定剂充分固化在聚合物中。
3. 塑化剂加工工段为了改善PVC的可塑性和加工性能,需要添加塑化剂。
其工艺流程主要包括:1. 加入塑化剂:将塑化剂添加到PVC中,通过较高的温度和剪切力使其与聚合物充分混合; 2. 传热和混合:将PVC和塑化剂进行传热和混合反应,使塑化剂充分分散在聚合物中; 3. 冷却和固化:通过冷却和固化过程,使塑化剂充分固化在聚合物中。
4. 成型工段在PVC生产中,成型是将PVC加工成所需产品的重要环节。
其工艺流程主要包括:1. PVC制品设计和模具制作:根据产品需求,设计PVC制品的形状和尺寸;制作相应的模具; 2. PVC熔融和注塑:将PVC加热熔融,并将熔融PVC注入模具中; 3. 冷却和模具开启:冷却PVC制品使其固化;开启模具,取出成型的PVC制品; 4. 码垛和包装:将成型的PVC制品进行码垛,并进行相应的包装。
年产10万吨氯乙烯工艺设计项目设计方案

设计方案项目背景:氯乙烯是一种重要的有机化工原料,广泛应用于塑料、橡胶、涂料、农药等多个领域。
我国是全球最大的氯乙烯生产和消费国家之一,但生产设备老化、能耗高等问题制约了其可持续发展。
因此,本设计方案旨在设计一套年产量为10万吨的氯乙烯工艺,利用先进的技术和设备,提高产能和能源利用效率。
设计方案:1.原料准备:该工艺采用乙烯和氯气为原料,通过氯化反应生成氯乙烯。
乙烯和氯气作为主要原料需要在储罐中储存,并通过气体管道输送至反应箱进行反应。
为确保原料的供给稳定和安全,需要设计合适的储存和输送系统,并设置相应的自动控制和安全设备。
2.反应过程:该工艺采用常压氯化法进行氯化反应。
乙烯和氯气通过催化剂在反应箱中进行氯化反应生成氯乙烯。
为提高反应效率和选择性,需要选择合适的催化剂和反应条件,并设计适当的反应器结构和控制系统。
同时,需要考虑废气处理和安全措施,避免有毒气体泄漏和环境污染。
3.分离和提纯:反应产生的气体混合物需要经过分离和提纯才能得到纯净的氯乙烯产品。
首先通过冷凝和压缩将气体混合物转化为液体,然后采用分离技术如蒸馏、吸附等进行分离和提纯。
分离后的氯乙烯产品需要经过后续的脱水、脱色等工艺步骤,得到满足市场要求的产品。
4.能源回收利用:为提高能源利用效率,该工艺设计考虑了能源回收利用系统。
具体包括废热回收、废气回收等。
废热回收可以通过余热锅炉进行,将废热转化为蒸汽等能源进行再利用;废气回收可以通过气体分离和净化系统,将有价值的气体组分进行回收利用。
5.自动控制系统:为确保生产过程的稳定和安全,该工艺设计采用自动控制系统进行全面控制。
通过传感器和仪表对关键工艺参数进行监测和控制,自动化地调节反应条件、制备工艺等,提高生产效率和产品质量。
同时,系统还需要具备报警、故障诊断等功能,保证生产的安全和可靠性。
6.安全环保措施:该工艺设计重点考虑安全和环保问题。
针对反应过程中有毒气体的泄漏和排放,需要设计相应的密封装置和废气处理系统,降低对环境和人体的影响。
年产10万吨氯乙烯工艺设计项目设计方案

年产10万吨氯乙烯工艺设计项目设计方案第一章绪论1.1聚氯乙烯1.1.1聚氯乙烯性质和用途⑴常温常压下,氯乙烯(vinyl chloride ,CH2=CHCI是无色气体,具有微甜气味,微溶于水,溶于烃类,醇,醚,氯化溶剂和丙酮等有机溶剂中,氯乙烯沸点-13.9 C,易聚合,并能与乙烯、丙烯、醋酸乙烯酯,偏二氯乙烯、丙烯腊、丙烯酸酯等单体共聚,而制得各种性能的树脂,加工成管材、面膜、塑料地板、各种压塑制品、建筑材料、涂料和合成纤维等。
近年来世界和中国聚氯乙烯树脂消耗比例分别见表 1.1和表1.2。
表1.1近年来世界聚氯乙烯树脂消耗比例品种比例/% 品种比例/%管材33 薄膜片材13 PVC 护墙板8 PVC 地板地砖 3硬薄膜和片材8 软合成皮革 3制吹塑制品 5 制电线电缆8品其他 6 品其他13合计60 合计40表1.2近年来中国聚氯乙烯树脂消耗比例品种比例/% 品种比例/%管材14 薄膜片材11 PVC 护墙板18 PVC 地板地砖8硬薄膜和片材15 软合成皮革7制吹塑制品 5 制电线电缆 4品其他 5 品其他13合计57 合计431.2 氯乙烯VC1.2.1 氯乙烯在国民经济中的地位和作用自1835 年法国化学家V.Regnault 首先发现了氯乙烯,于1838年他又观察到聚合体,这就是最早的聚氯乙烯。
聚氯乙烯自工业化问世至今,六十多年来仍处不衰之势。
占目前塑料消费总量的29%以上。
到上世纪末,聚氯乙烯树脂大约以3%的速度增长。
这首先是由于新技术不断采用,产品性能亦不断地得到改进,品种及牌号的增加,促进用途及市场的拓宽。
其次是制造原料来源广、制造工艺简单。
产品质量好。
在耐燃性、透明性及耐化学药品性能方面均较其它塑料优异。
又它是氯碱行业耗“氯”的大户,对氯碱平衡起着举足轻重的作用。
从目前世界主要聚氯乙烯生产国来说:一般耗用量占其总量的20〜30%。
特别是60 年代以来,由于石油化工的发展,为聚氯乙烯工业提供廉价的乙烯资源,引起了人们极大的注意,因而促使氯乙烯合成原料路线的转换和新制法以及聚合技术不断地更新,使聚氯乙烯工业获得迅猛的发展。
氯乙烯合成工艺设计
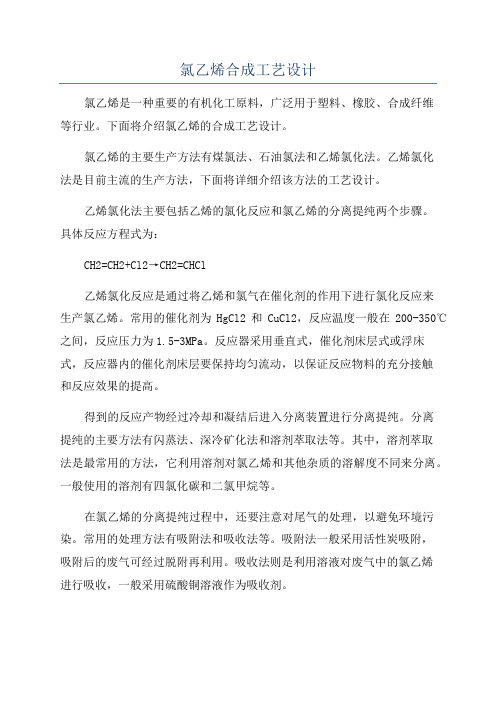
氯乙烯合成工艺设计氯乙烯是一种重要的有机化工原料,广泛用于塑料、橡胶、合成纤维等行业。
下面将介绍氯乙烯的合成工艺设计。
氯乙烯的主要生产方法有煤氯法、石油氯法和乙烯氯化法。
乙烯氯化法是目前主流的生产方法,下面将详细介绍该方法的工艺设计。
乙烯氯化法主要包括乙烯的氯化反应和氯乙烯的分离提纯两个步骤。
具体反应方程式为:CH2=CH2+Cl2→CH2=CHCl乙烯氯化反应是通过将乙烯和氯气在催化剂的作用下进行氯化反应来生产氯乙烯。
常用的催化剂为HgCl2和CuCl2,反应温度一般在200-350℃之间,反应压力为1.5-3MPa。
反应器采用垂直式,催化剂床层式或浮床式,反应器内的催化剂床层要保持均匀流动,以保证反应物料的充分接触和反应效果的提高。
得到的反应产物经过冷却和凝结后进入分离装置进行分离提纯。
分离提纯的主要方法有闪蒸法、深冷矿化法和溶剂萃取法等。
其中,溶剂萃取法是最常用的方法,它利用溶剂对氯乙烯和其他杂质的溶解度不同来分离。
一般使用的溶剂有四氯化碳和二氯甲烷等。
在氯乙烯的分离提纯过程中,还要注意对尾气的处理,以避免环境污染。
常用的处理方法有吸附法和吸收法等。
吸附法一般采用活性炭吸附,吸附后的废气可经过脱附再利用。
吸收法则是利用溶液对废气中的氯乙烯进行吸收,一般采用硫酸铜溶液作为吸收剂。
除了反应和分离提纯步骤外,还要对生产过程中产生的废水、废热等进行处理利用,以达到资源综合利用和环境保护的目的。
总结起来,氯乙烯的合成工艺设计主要包括乙烯氯化反应和氯乙烯的分离提纯两个步骤,其中乙烯氯化反应通过催化剂的作用将乙烯和氯气进行氯化反应,分离提纯则通过溶剂萃取法将氯乙烯和其他杂质进行分离。
在生产过程中还要注意对废气、废水和废热的处理利用。
正确设计和优化各个环节的操作条件和流程,能够提高产量、品质和能源利用率,降低生产成本和环境污染,实现可持续发展。
年产16万吨氯乙烯合成工艺设计

年产16万吨氯乙烯合成工艺设计1. 引言氯乙烯是一种重要的有机化工原料,广泛应用于塑料、合成橡胶、溶剂等行业。
本文旨在设计一种年产16万吨氯乙烯的合成工艺,以满足市场需求并提高生产效率。
2. 工艺概述合成工艺的概述如下:1.原料准备:主要原料包括乙烯、氯气和催化剂。
2.反应装置:采用流动床反应器,具有较高的热传导和负载能力。
3.反应步骤:氯气与乙烯在催化剂作用下发生氯化反应,生成氯乙烯。
4.分离纯化:通过多级凝馏和萃取等工艺对氯乙烯进行纯化。
5.产品储存和包装:将纯化后的氯乙烯储存于贮罐中,并进行相应的包装以便于运输和销售。
3. 反应装置设计3.1 流动床反应器流动床反应器是当前工业生产中常用的反应器类型之一,由于其具有优良的热传导和负载能力,适用于氯乙烯的合成反应。
流动床反应器的设计要点如下:•反应器材料:选择耐腐蚀性能好、热传导性能高的不锈钢。
•反应器结构:采用垂直式结构,方便气体和液体的流动,并且易于维护和清洗。
•热交换器:在反应器内部设置热交换器,提高反应器的热效率,减少能量损失。
•自动控制系统:采用先进的自动控制系统,实时监测反应器的温度、压力等参数,保证反应的稳定进行。
4. 反应步骤与工艺条件4.1 氯化反应氯化反应是合成氯乙烯的关键步骤,该反应基于氯气与乙烯的化学反应。
反应方程式如下:C2H4 + Cl2 -> C2H3Cl + HCl氯化反应的工艺条件如下:•温度:反应温度为300-500摄氏度。
•压力:反应压力为1-5兆帕。
•催化剂:采用氯化汞作为催化剂,具有较高的活性和选择性。
4.2 分离纯化分离纯化工艺的目的是将氯乙烯从反应产物中分离出来,以提高氯乙烯的纯度和质量。
分离纯化工艺包括多级凝馏和萃取等步骤:•多级凝馏:通过不同的温度和压力条件,将乙烯、氯乙烯和其他杂质分离出来。
•萃取:采用特定的溶剂将残留的杂质进一步去除,提高氯乙烯的纯度。
5. 安全防护措施在氯乙烯合成工艺中,涉及到氯气和高温高压条件,因此必须采取必要的安全防护措施,以防止事故发生,保证生产安全。
年产10万吨聚氯乙烯生产工艺设计

聚氯乙烯(Polyvinyl Chloride,简称PVC)是一种用途广泛的塑料材料,其年产量也相对较大。
本文将对年产10万吨聚氯乙烯的生产工艺进行设计,并将工艺步骤进行详细介绍。
1.原料准备2.氯乙烯制备利用氯气和乙烯进行反应,生成氯乙烯。
这一步需要精确控制反应的温度、压力和氯乙烯生成的速率,以确保反应的高效性和安全性。
3.聚合反应将氯乙烯和引发剂引入聚合反应器中进行聚合反应。
聚合反应器需要具备良好的搅拌和加热功能,以确保反应均匀进行且能高效完成。
聚合反应的时间和温度控制至关重要,以确保所得的聚合物的分子量和物性符合要求。
4.分离和净化将聚合反应产生的混合物进行分离和净化。
这一步主要包括聚合物的沉淀、过滤、洗涤等操作,以去除杂质和未反应的原料。
5.干燥和造粒将净化后的聚合物颗粒进行干燥处理,以去除水分和挥发性杂质,同时将其熔融并通过造粒机构成颗粒状的聚氯乙烯。
颗粒的大小和形状对后续的加工工艺和产品质量有关联。
6.真空除气将造粒后的聚氯乙烯通过真空除气设备进行处理,去除颗粒中的气体和挥发性成分,以确保产品的稳定性。
7.制品加工将除气处理后的聚氯乙烯颗粒进行制品加工。
常见的制品加工方式包括挤出、注塑、吹塑等。
通过这些加工方式,可以将聚氯乙烯颗粒制成板材、管材、型材等不同形状和尺寸的产品。
8.产品测试和质量控制对最终产品进行测试,检查其物理、力学、热学等性能指标,确保产品质量达到要求。
并建立质量控制体系,对每批产品进行检验和记录,以便进行溯源和质量追踪。
9.废弃物处理对生产过程中产生的废弃物进行处理和回收利用。
这些废弃物包括回收的聚氯乙烯颗粒、废水、废气等,应根据地方环保要求进行合理的处理。
综上所述,年产10万吨聚氯乙烯的生产工艺设计包括原料准备、氯乙烯制备、聚合反应、分离和净化、干燥和造粒、真空除气、制品加工、产品测试和质量控制以及废弃物处理等主要步骤。
在每一步骤中,都需要精确控制工艺参数、确保产品质量和安全性。
氯乙烯生产工艺介绍
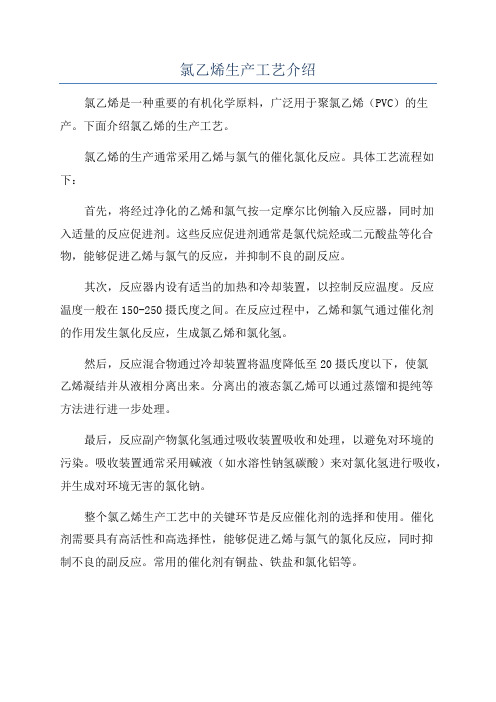
氯乙烯生产工艺介绍氯乙烯是一种重要的有机化学原料,广泛用于聚氯乙烯(PVC)的生产。
下面介绍氯乙烯的生产工艺。
氯乙烯的生产通常采用乙烯与氯气的催化氯化反应。
具体工艺流程如下:首先,将经过净化的乙烯和氯气按一定摩尔比例输入反应器,同时加入适量的反应促进剂。
这些反应促进剂通常是氯代烷烃或二元酸盐等化合物,能够促进乙烯与氯气的反应,并抑制不良的副反应。
其次,反应器内设有适当的加热和冷却装置,以控制反应温度。
反应温度一般在150-250摄氏度之间。
在反应过程中,乙烯和氯气通过催化剂的作用发生氯化反应,生成氯乙烯和氯化氢。
然后,反应混合物通过冷却装置将温度降低至20摄氏度以下,使氯乙烯凝结并从液相分离出来。
分离出的液态氯乙烯可以通过蒸馏和提纯等方法进行进一步处理。
最后,反应副产物氯化氢通过吸收装置吸收和处理,以避免对环境的污染。
吸收装置通常采用碱液(如水溶性钠氢碳酸)来对氯化氢进行吸收,并生成对环境无害的氯化钠。
整个氯乙烯生产工艺中的关键环节是反应催化剂的选择和使用。
催化剂需要具有高活性和高选择性,能够促进乙烯与氯气的氯化反应,同时抑制不良的副反应。
常用的催化剂有铜盐、铁盐和氯化铝等。
此外,工艺中还需要注意安全问题。
氯乙烯是一种具有毒性和高燃烧性的物质,对工人的生命和健康构成一定的威胁。
因此,在生产过程中需要严格控制反应温度和压力,保证设备和操作的安全性。
综上所述,氯乙烯的生产工艺主要包括乙烯与氯气的催化氯化反应、冷却和凝析、分离和提纯以及氯化氢的吸收和处理等环节。
工艺的主要挑战是催化剂的选择和使用,以及安全控制。
通过科学合理的工艺设计和严格的操作管理,可以实现高效、安全、环保的氯乙烯生产。
氯乙烯工艺设计范文

氯乙烯工艺设计范文氯乙烯是一种非常重要的有机化学原料,广泛应用于塑料制品、橡胶制品、合成纤维、涂料、医药和农药等领域。
本文将探讨氯乙烯的工艺设计及其工艺流程。
氯乙烯的工艺设计主要包括原料选择、反应器设计、分离装置设计以及工艺流程优化等方面。
首先,原料选择。
氯乙烯的主要原料是乙烯和氯气。
乙烯是一种广泛存在于石油和天然气中的重要烃类化合物,而氯气则可通过电解食盐水或电解氯化钠来制备。
在原料选择时,需要考虑乙烯和氯气的纯度以及供应的可靠性和成本因素。
其次,反应器设计。
氯乙烯的主要制备方法是通过氯化乙烯反应。
该反应通常是在高温下进行,并利用催化剂促进反应速率。
反应器的设计要考虑到反应速率、温度和压力的控制以及产物的分离等因素。
分离装置设计是氯乙烯工艺设计的关键一步。
氯乙烯的主要杂质是氯化乙烯和1,2-二氯乙烷。
分离装置的设计要考虑到这些杂质的物理性质和沸点,并采取合适的分离方法,如精馏、冷凝和吸收等。
最后,对氯乙烯的工艺流程进行优化是提高生产效率和产品质量的关键。
在工艺流程中,可以采用节能措施和改进操作条件来减少能耗和排放。
此外,还可以进行废气处理和废水处理,以减少对环境的污染。
总的来说,氯乙烯工艺设计是一个复杂而关键的过程。
通过合理选择原料、合适的反应器设计、优化的分离装置和工艺流程,可以实现高效生产氯乙烯,并提高产品质量和减少环境污染。
在实际应用中,还需要与相关部门合作,遵守相关法规和标准,确保工艺的安全和可持续发展。
- 1、下载文档前请自行甄别文档内容的完整性,平台不提供额外的编辑、内容补充、找答案等附加服务。
- 2、"仅部分预览"的文档,不可在线预览部分如存在完整性等问题,可反馈申请退款(可完整预览的文档不适用该条件!)。
- 3、如文档侵犯您的权益,请联系客服反馈,我们会尽快为您处理(人工客服工作时间:9:00-18:30)。
氯乙烯合成工艺设计一、氯乙烯的性质与用途1. 常温常压下,氯乙烯(vinyl chloride,CH2=CHCl)是无色气体,具有微甜气味,微溶于水,溶于烃类,醇,醚,氯化溶剂和丙酮等有机溶剂中,氯乙烯沸点-13.9℃,易聚合,并能与乙烯、丙烯、醋酸乙烯酯,偏二氯乙烯、丙烯腊、丙烯酸酯等单体共聚,而制得各种性能的树脂,加工成管材、面膜、塑料地板、各种压塑制品、建筑材料、涂料和合成纤维等[1]。
氯乙烯的物理性质见下表[2]:2. 氯乙烯是易燃易爆物质,与空气混合能形成爆炸性混合物,高温或遇明火能引起燃烧或无抑制剂时可发生剧烈聚合。
在氯乙烯与空气的混合物中加入氮气或二氧化碳可使爆炸范围变窄,减少爆炸危险。
危险性类别:第2.1类易燃气体,禁忌物是强氧化剂,灭火方式是切断电源,灭火剂用雾状水、二氧化碳、泡沫,泄漏应急处理:迅速撤离泄露污染区人员至上风处并进行隔离,严格限制出入,切断火源,应急处理人员戴好正压式呼吸器,尽可能切断泄漏源[3]。
[2]3. 由于光和热可引发氯乙烯单体聚合,故存储时应避免日晒,常温下存储应加入阻聚剂(如对苯二酚)防止其自聚,一般以液体状态存储和运输[1]。
4. 氯乙烯在工业上的主要应用时生产聚氯乙烯树脂,故常称其为氯乙烯单体(VCM)所谓聚氯乙烯树脂是一类由氯乙烯单体衍生的均聚物和共聚物,其中氯乙烯占树脂组分质量的50%,因此VCM的生产质量和成本直接影响到聚氯乙烯树脂的质量和成本。
目前用于制造聚氯乙烯树脂的氯乙烯约占其产量的96%,VCM的需求量和产量在很大程度上取决于聚氯乙烯树脂的需求量。
聚氯乙烯为五大和成树脂之一,由于其价廉易得、应用广泛,因此需求量和产量逐年上升。
氯乙烯是离分子材料工业的重要单体,产量很大,还可用于合成1,1,2-三氯乙烷和1,1-二氯乙烯等。
故氯乙烯的生产在基本有机化学工业中占有重要的地位[7]。
二、氯乙烯生产工艺简介氯乙烯是1835年由法国人V.Regnault首先在实验室中制得,他用氢氧化钾的乙醇溶液处理二氯乙烷得到了氯乙烯。
1902年,Biltz 将二氯乙烷进行热分解也可制得氯乙烷。
1911年,kiatte和Rollett 利用乙炔和氯化氢催化加成反应合成了氯乙烯。
1913年,Griesheim -Elektron用氯化汞作催化剂,使氯乙烯合成技术进一步发展。
1931年,德国首先实现了氯乙烯的工业化生产,原料是乙炔和氯化氢,催化剂是氯化汞。
20世纪50年代以前,氯乙烯主要采用电石乙炔和氯化氢制得,即电石乙炔法。
其生产流程简单,副反应少,产品纯度高。
它具有设备、工艺简单,投资低,可以小规模经营的特点。
但由于汞催化剂有毒,不利环境保护,且生产电石要消耗大量电能,以后由于电力和焦炭提价,电石价格大幅度提高,严重影响到氯乙烯的生产。
之后出现了原料的部分转换,产生了联合法和烯炔法。
石油化工的迅速发展给氯乙烯工业带来了重大影响。
1955-1958年,道化学公司首先将以电石乙炔为原料的路线转变为以乙烯为原料的工艺路线,建成一套氧氯化法生产氯乙烯的工业装置。
氧氯化法的成功,不仅使制造氯乙烯的原料从乙炔完全转变为乙烯,而且为平衡氧氯化法制造氯乙烯打下了基础[8]。
2.1用乙烯和氯气为他原料合成氯乙烯,要经过两步反应,第一步是乙烯与氯气加成生成1,2-二氯乙烷(EDC),第二步是EDC裂解脱氯化氢生成氯乙烯。
这种方法仅有一半的氯气用于生产氯乙烯,另一半变成氯化氢,排放浪费大量的氯资源污染环境。
因此如何利用副产物氯化氢时氯化工业必须解决的技术经济问题[1]。
2.2联合法是将氯化氢用于与乙炔反应+=≡CH=+→CHClCHCHClCHCH2222此法的优点是利用已有的电石资源和乙炔生产装置,迅速提高氯乙烯的生产能力,因此,在电石原料向石油系原料变换的初期,曾有不少工厂采用,但是,这种方法不能完全摆脱电石原料,只是一种暂时的方法[1]。
联合法流程示意图2.3烯炔法是由石脑油得到乙烯和乙炔裂解气,不经分解直接氯化生产氯乙烯,是对联合法的改进,这种方法摆脱了电石原料,省去了分离乙炔和乙烯的费用,但技术复杂,投资较高,成本较高[1]。
2.4平衡氧氯化法[1]由乙烯氧氯化合成二氯乙烷的反应,虽然在1922年就已经提出,但利用此反应制备氯乙烯的技术,是在20世纪50年代才开始实验室研究工作,至60年代初开始工业化,并逐渐取代联合法。
乙烯氧氯化反应的成功开发,解决了氯化氢的利用问题,使以乙烯和氯气为原料生产氯乙烯的方法显出极大地优越性。
乙烯氧氯化生产氯乙烯包括两个反应,第一个反应时乙烯在铜催化剂存在下与氯化氢进行氧氯化反应生成EDC ,第二个反应是EDC 裂解脱氯化氢生成氯乙烯。
由乙烯氧氯化法的俩个化学计量式可知,每生产1mol 二氯乙烷需要消耗2mol 氯化氢,而1mol 二氯乙烷裂解只生产1 mol 氯化氢,氯化氢的需要量和产生量不平衡,伴有净得氯化氢消耗。
若将氧氯化法与乙烯直接氯化过程结合在一起,两过程所产生的二氯乙烷一并进行裂解得到氯化氢,则可平衡氯化氢,即为平衡氧氯化法。
该法由乙烯、氯气和氧气生产氯乙烯,整个工艺过程既不产生氯化氢,也不消耗氯化氢。
平衡氧氯化法包括三个反应:第一个反应是乙烯与氯气进行氯化反应生成EDC;第二个反应是乙烯与氯化氢和氧进行氧氯化反应生产EDC ;第三个反应时EDC 裂解脱氯化氢生成氯乙烯。
该方法的物料平衡式为:OH CHCl CH O Cl CH CH OH Cl CH Cl CH O HCl CH CH 222222222240~22022222/122/12+=→++=+-−−−→−++=该方法是目前世界公认的技术经济较合理的方法,全世界93%以上的氯乙烯是采取平衡氧氯化法生产的。
三、电石乙炔法生产氯乙烯工艺[4]。
3.1 我国由于乙烯资源匮乏,煤碳资源相对丰富,电石原料易得,为电石乙炔法的发展创造了较大的利润空间,因此氯乙烯的生产以电石乙炔法为主,氯乙烯原料路线相对比较落后。
3.2 乙炔与氯化氢反应机理 乙炔与氯化氢加成得氯乙烯kJ CHCl CH HCl CH CH 8.1242+=→+≡加成反应是在气相中进行。
虽然从热力学分析此反应很有利,但由于反应速度慢,因此必须在催化剂存在下进行。
工业上采用的催化剂是HgCI 2/活性炭,其活性随Hgcl 2含量的增高而增大,一般HgCl 2含量为10-20%。
该催化剂的主要缺点是活性稳定性较差。
据研究,当反应温度<140℃时,活性基本稳定。
但温度低,反应速度太慢,乙炔转化率低。
反应温度高于140℃,催化剂就出现明显的失活,并随温度的升高而加剧。
使催化剂失活的主要原因是活性组分HgCl 2的升华。
当温度高于200℃时,就会有大量HgCl 2升华而使催化剂的活性迅速下降故反应温度的控制十分重要,工业上一段控制在160-180℃,HgCl 2蒸汽压与温度关系如下图。
也有使用(氯化汞-氯化钡)/活性炭作催化剂,据报道此类复合催化剂活性和选择性都很高,并可以减少HgCl 2的升华现象,而使稳定性得到改善。
据研究乙炔在HgCl 2/活性炭催化剂上与氯化氢加成的反应机理可能为吸附空位-------**+=→+**⇔*+CHCl CH H C HCl HCl HCl 222C 2H 2/HCl 的摩尔比对催化剂的活性和反应选择性也有影响。
当用量比大时,过量的乙炔会与催化剂活性组分HgCl 2作用,生成1,2-二氯乙烯,并使HgCl 2转化为Hg 2C12或甚至析出汞。
Hg 2C12和汞都无催化作用,从面使催化剂的活性下降。
因此C 2H 2/HCI 摩尔比不宜过大。
但太小也会降低反应选择性,因为过量的HCl 会与氯乙烯进一步发生加成反应而生成1,1-二氯乙烷。
一般采用HCl 略为过量。
232CHCl CH HCl Cl CH CH →+-=3.3 乙炔气相加氯化氢制氯乙烯工艺流程乙炔加氯化氢是放热反应,局部过热会影响催化剂的寿命,因此必须及时地移出反应热。
工业上常采用多管式的固定床氯化反应器,管内盛放催化剂,干燥和已净化的乙炔和氯化氢的混合气自上而下地通过催化剂层进行反应。
管外用加压热水循环进行冷却。
由于受到热点温度的限制,乙炔空速也受到限制。
要充分发挥床层催化剂的效率,就必须使整个床层温度都接近最佳的允许温度。
采取分段进气、分段冷却和适当调整催化剂活性等方法,可使床层温度分布得到改善,乙炔空速可以提高,因而催化剂的生产能力也可以显著提高。
乙炔加氯化氢制氯乙烯的工艺流程如图所示。
乙炔可由电石水解得到,经净化和干燥后与干燥的HCl以1:1.05-1.1的比例混和进入反应器进行加成反应,乙炔转化率可达99%左右,副产物1,1-二氯乙烷的生成量约为1%左右。
自反应器出来的气体产物中除含有产物氯乙烯和副产物1,1-二氯乙烷外,还含有5-10%HCl,和少量未反应的乙炔。
反应气经水洗和碱洗除去HCl等酸性气体,并用固体KOH进行干燥,再经冷却冷凝得粗氯乙烯冷凝液。
粗氯乙烯先经冷凝蒸出塔脱去溶于其中的乙炔等气体后,至氯乙烯塔进行积储,除去1,l-二氯乙烷等高沸点杂质,塔顶蒸出产品氯乙烯贮于低温贮槽。
四、电石乙炔法中电石渣的处理[6]1. 电石渣一直都是电石法制取氯乙烯的生产者最烦恼的问题。
电石渣由于含有大量的氢氧化钙固体,具有强烈的碱性,并含有较高的硫化物,以及其它微量的杂质。
此外,电石渣作为副产物,在数量上却大大超过产品聚氯乙烯树脂。
根据生产经验,每生产一吨树脂,可以得到含固量5~15%的电石渣浆9~15吨,或含固量50%的干渣3~5吨。
因此,若对电石渣不予处理而直接排放,必将造成极大的污染,成为聚氯乙烯工厂最大的“三废”。
1963年冬季,美国在肯塔基州路易斯维尔城的某广,堆积二十多年的、面积为5万多平方米、高度达30多米的电石渣,发生了大崩溃,吞没本厂和邻近的炼油广,污染了俄亥俄河,付出了极大的代价。
目前,多数工厂只将发生器排出的电石渣浆经过一级沉降分离,对干渣进行利用。
而将分离后的沉清水直接排放,这是不妥当的,因为沉清水即使达到“眼见不混”,其pH值也高达14,硫化物含量等都超过国家的“三废”排放标难,因此有必要对电石渣浆沉清水进行中和及脱硫处理。
2.综合利用处理电石渣,一般来说,发生器排出的电石渣浆经过初步澄清分离后,可以得到含水45~60%的所谓干渣,以及“眼见不混”(含固量约500毫克/升)的澄清水。
根据各厂的经验,这两部分都可以综合利用,现分述如下。
(1)干渣多数利用其氢氧化钙(消石灰)组分①加煤渣制作砖块或大型砌块;②作铺设地坪、道路的材料;③工业或农业的中和剂;④代替石灰水用于生产漂白液和漂白粉;⑤代替石灰水用于生产氯仿;⑥代替石灰水用于生产三氯乙烯;⑦代替石灰生产水泥;⑧最近己试制成功一种质深、强度高的粉煤灰加气混凝土砌块,它是由电石渣、粉煤渣、石灰、石膏、水泥和废气为原科制成,可用于高层建筑施工。