挤出成型技术
挤出成型技术

度成正比。阻力愈小,挤出量受压力的影响愈大。
精品课件
挤出机的发展
发展方向: 高速、高效、提高自动化水平、 多品种多规格、研制特殊用途 和新型挤出机等方向发展。
精品课件
挤出—拉幅成型,双轴拉伸薄膜 (3)产品形状多样 (4)设备简单,投资少,占地面积小
精ቤተ መጻሕፍቲ ባይዱ课件
2 挤出成型基本过程
(1)塑化:在挤出机内将固体塑料加热并依靠塑料之间 的内摩擦热使其成为粘流态物料。 (2)成型:在挤出机螺杆的旋转推挤作用下,通过具有 一定形状的口模,使粘流态物料成为连续的型材。 (3)定型:用适当的方法,使挤出的连续型材冷却定型 为制品。
根据流动分析,影响挤出机生产能力的是正流、逆流、漏 流,横流对挤出量没有影响 挤出机的生产能力表示为
Qv=Qv,D -Qv,p -精品Q课v件,L
影响挤出机生产率的因素 1.机头压力 当机头压力△p=0 可获最大挤出量
当机头口模封闭时无挤出量 机头最大压力降
精品课件
2 螺杆转速 机头和螺杆的尺寸一定时,挤出量与螺杆转速 成正比。
作用:将塑化均匀的物料在均化段螺槽和机头回压作用下 进一步搅拌塑化均匀,并定量定压的通过机头口模挤出成 型。一般无压缩作用。
精品课件
4 螺杆的形式 •普通螺杆:
采用等距变深、等深变距、变深变距螺槽 •高效专用螺杆:
L/ DS 大、熔融效率低、塑化混合均匀
精品课件
机头和口模
(1)使粘流态物料从螺旋运动变为平行直线运动,并稳 定地导入口模而成型
精品课件
料筒
作用:输送、塑化、压缩 工作温度:180-290℃ 压力:≤55MPa 设有分段加热和冷却装置 制造材料:耐磨、耐腐蚀、高强度的合金钢等 料筒除了可以用45号钢、40Cr、38CrMoAL外,还可以 用铸钢和球墨铸铁制造。带衬套的加料段可以用优质 铸铁制成。
挤出成型法名词解释

挤出成型法名词解释
挤出成型法是一种常见的塑料加工方法,也被称为挤塑或挤压成型。
它是利用
挤出机将熔化的塑料物料通过模具挤出,使其成型为所需的截面形状。
这种方法在塑料加工领域应用广泛,可以生产出各种形状复杂的塑料制品,如管材、板材、型材等。
挤出成型法的工作原理是通过将塑料颗粒或粉末加热熔化,然后将熔化的塑料
物料送入挤出机的螺杆筒内。
在螺杆的旋转作用下,熔化的塑料物料被压缩、混合、加热,最终在机筒出口处通过模具挤出,形成所需的截面形状。
挤出机通常由进料装置、加热装置、螺杆和机筒、模具、冷却装置等部件组成。
挤出成型法具有生产效率高、成型精度高、生产成本低等优点。
它适用于生产
各种截面形状的塑料制品,且可以通过更换模具实现生产不同形状和尺寸的产品。
此外,挤出成型法生产的制品表面光滑、一致性好,可以满足各种工业和民用领域的需求。
在挤出成型法中,塑料的选择、挤出机的参数调节、模具设计等因素都会影响
成型制品的质量和性能。
因此,在实际生产中,需要根据具体的产品要求和生产条件,合理选择塑料材料、挤出机型号和参数,设计合理的模具,确保生产出符合要求的塑料制品。
总的来说,挤出成型法是一种常用的塑料加工方法,具有广泛的应用前景。
通
过不断的技术改进和创新,挤出成型法将能够更好地满足不同行业的生产需求,为塑料制品的生产和应用提供更加便捷、高效的解决方案。
挤出成型可以生产哪些制品

挤出成型可以生产哪些制品在现代制造业中,挤出成型技术是一种广泛应用于各种行业的生产工艺。
通过挤出成型,可以生产出各种形状复杂的制品,从日常生活用品到工业零部件,应用范围非常广泛。
以下是挤出成型可以生产的一些制品及其应用领域:1. 塑料制品挤出成型是塑料制品生产中最常用的方法之一。
通过将塑料颗粒加热熔化后挤压出模具,可以生产出各种形状的塑料制品,如塑料管道、塑料板材、塑料型材等。
这些制品在建筑、工程、家居等领域有着广泛的应用,如水暖管道、地板材料、窗框等。
2. 金属制品除了塑料制品,挤出成型还可以用于生产金属制品。
通过将金属坯料加热后挤压形成所需的截面形状,可以生产出各种金属型材,如铝合金窗框、钢管、铜杆等。
这些金属制品广泛应用于建筑、汽车、航空航天等领域。
3. 橡胶制品挤出成型也是生产橡胶制品的重要方法之一。
通过将橡胶混合料加热后挤压出模具,可以生产出各种橡胶制品,如密封条、橡胶管件、橡胶密封圈等。
这些橡胶制品在汽车、机械、电子等领域有着重要的应用,起着密封、减震、保护等功能。
4. 食品制品除了工业制品,挤出成型还可以应用于食品加工领域。
通过挤出成型可以生产出各种形状的食品制品,如糖果、巧克力、面包等。
这些食品制品在食品加工业中有着重要的地位,提高了生产效率,丰富了产品种类。
5. 纤维制品挤出成型也可以用于生产纤维制品,如人造棉、合成纤维等。
通过挤出成型可以实现纤维的连续生产,生产出各种纤维制品,如纺织品、绳索、过滤材料等。
这些纤维制品在纺织、建筑、环保等领域有着广泛的应用。
总的来说,挤出成型技术在各种行业的生产中都有着重要的应用,可以生产出各种形状、材质的制品,广泛满足了市场需求。
随着科技的不断发展,挤出成型技术也在不断创新和完善,将为更多行业带来更高效、环保、优质的制造解决方案。
塑料挤出成型技术
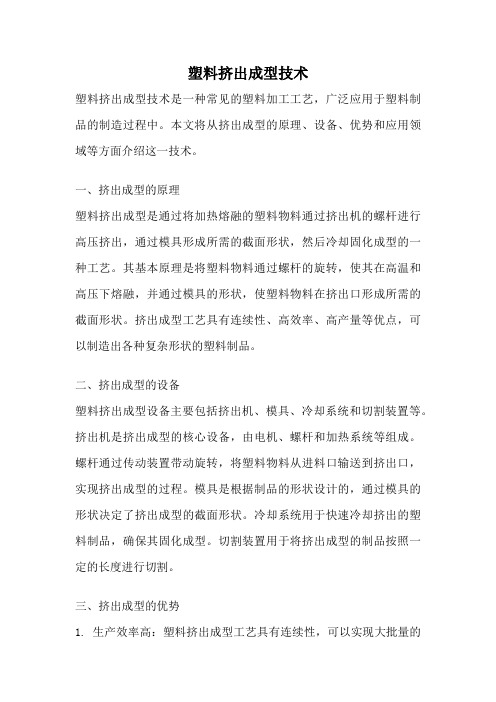
塑料挤出成型技术塑料挤出成型技术是一种常见的塑料加工工艺,广泛应用于塑料制品的制造过程中。
本文将从挤出成型的原理、设备、优势和应用领域等方面介绍这一技术。
一、挤出成型的原理塑料挤出成型是通过将加热熔融的塑料物料通过挤出机的螺杆进行高压挤出,通过模具形成所需的截面形状,然后冷却固化成型的一种工艺。
其基本原理是将塑料物料通过螺杆的旋转,使其在高温和高压下熔融,并通过模具的形状,使塑料物料在挤出口形成所需的截面形状。
挤出成型工艺具有连续性、高效率、高产量等优点,可以制造出各种复杂形状的塑料制品。
二、挤出成型的设备塑料挤出成型设备主要包括挤出机、模具、冷却系统和切割装置等。
挤出机是挤出成型的核心设备,由电机、螺杆和加热系统等组成。
螺杆通过传动装置带动旋转,将塑料物料从进料口输送到挤出口,实现挤出成型的过程。
模具是根据制品的形状设计的,通过模具的形状决定了挤出成型的截面形状。
冷却系统用于快速冷却挤出的塑料制品,确保其固化成型。
切割装置用于将挤出成型的制品按照一定的长度进行切割。
三、挤出成型的优势1. 生产效率高:塑料挤出成型工艺具有连续性,可以实现大批量的生产,提高生产效率。
2. 制品质量稳定:挤出成型的制品形状稳定,尺寸精确,质量可靠。
3. 适用范围广:挤出成型工艺适用于各种塑料,可以制造出各种形状的制品,如管材、板材、型材等。
4. 设备投资少:相对于其他塑料加工工艺,挤出成型设备投资较少,生产成本较低。
5. 可塑性强:挤出成型的塑料物料可根据需要选择,可以加入各种填充剂、增强剂等,增加塑料的性能。
四、挤出成型的应用领域塑料挤出成型技术广泛应用于建筑、包装、汽车、电子、家电等行业。
在建筑行业中,挤出成型制造的塑料管材、型材、板材等被广泛应用于室内装饰、给排水系统、电线电缆等方面。
在包装行业中,挤出成型用于制造各种塑料包装盒、瓶子、袋子等。
在汽车行业中,挤出成型的塑料制品用于汽车内饰、外饰等部件。
在电子和家电行业中,挤出成型的塑料制品用于电线电缆的保护管、电器外壳等。
挤出成型定义

挤出成型定义
挤出成型是一种常见的加工工艺,通常适用于塑料、橡胶等材料的加工制造过程。
在挤出成型过程中,原料经过加热融化,然后通过一个特定形状的模具,使之产生连续且具有相同截面形状的成型产品。
这种加工方式具有高效、低成本和高质量等优势,被广泛应用于生产各种塑料制品,如管材、板材、型材等。
挤出成型的过程可以分为预处理、挤出成型和后处理三个阶段。
首先是预处理阶段,原料经过干燥、混合等处理,以保证挤出成型的质量稳定和良好。
接着是挤出成型阶段,原料在高温、高压下被挤出模具,形成连续的型材,这个阶段需要控制好的温度、压力和挤出速度等参数,以确保产品的准确尺寸和表面光洁。
最后是后处理阶段,挤出成型出来的产品可能需要冷却、切割、挤出料头等处理,以得到最终的产品。
在挤出成型过程中,模具的设计是至关重要的一环。
不同形状的模具会影响挤出产品的截面形状和尺寸,因此需要根据产品的需求精确设计模具。
同时,挤出机的性能也会直接影响产品的质量,挤出机需要稳定的温度控制、压力控制和挤出速度调节,以确保产品的一致性和稳定性。
挤出成型技术的发展也在不断创新和完善中。
随着材料科学和机械工艺的不断进步,挤出成型技术越来越智能化和自动化,使得生产效率更高、产品质量更稳定。
同时,新材料的应用也拓展了挤出成型的领域,如生物可降解塑料、复合材料等,使得挤出产品更加环保和功能多样化。
总的来说,挤出成型作为一种常见的加工工艺,在塑料工业和橡胶工业中具有重要的地位。
通过不断的技术创新和工艺改进,挤出成型技术将会更加精密、智能化,为工业生产带来更多便利和效益。
1。
塑料挤出成型技术
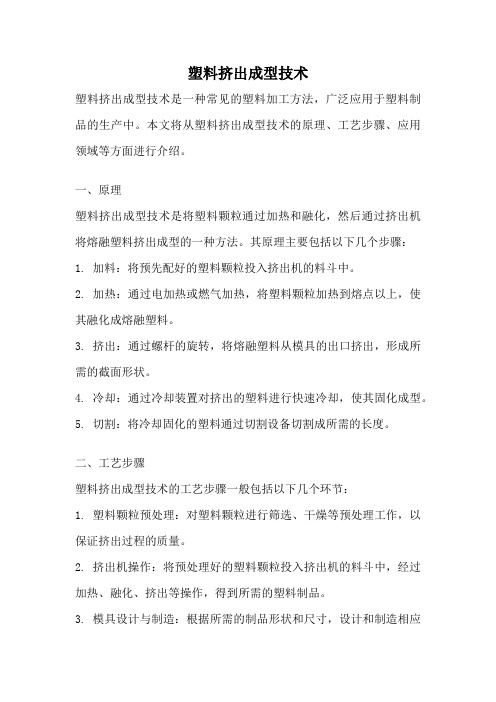
塑料挤出成型技术塑料挤出成型技术是一种常见的塑料加工方法,广泛应用于塑料制品的生产中。
本文将从塑料挤出成型技术的原理、工艺步骤、应用领域等方面进行介绍。
一、原理塑料挤出成型技术是将塑料颗粒通过加热和融化,然后通过挤出机将熔融塑料挤出成型的一种方法。
其原理主要包括以下几个步骤:1. 加料:将预先配好的塑料颗粒投入挤出机的料斗中。
2. 加热:通过电加热或燃气加热,将塑料颗粒加热到熔点以上,使其融化成熔融塑料。
3. 挤出:通过螺杆的旋转,将熔融塑料从模具的出口挤出,形成所需的截面形状。
4. 冷却:通过冷却装置对挤出的塑料进行快速冷却,使其固化成型。
5. 切割:将冷却固化的塑料通过切割设备切割成所需的长度。
二、工艺步骤塑料挤出成型技术的工艺步骤一般包括以下几个环节:1. 塑料颗粒预处理:对塑料颗粒进行筛选、干燥等预处理工作,以保证挤出过程的质量。
2. 挤出机操作:将预处理好的塑料颗粒投入挤出机的料斗中,经过加热、融化、挤出等操作,得到所需的塑料制品。
3. 模具设计与制造:根据所需的制品形状和尺寸,设计和制造相应的模具。
4. 挤出成型:将熔融塑料从模具的出口挤出,形成所需的截面形状。
5. 冷却与固化:通过冷却装置对挤出的塑料进行快速冷却,使其固化成型。
6. 切割与包装:将冷却固化的塑料通过切割设备切割成所需的长度,并进行包装。
三、应用领域塑料挤出成型技术广泛应用于各个领域的塑料制品生产中,例如:1. 建筑行业:生产塑料管道、塑料板材、塑料薄膜等建筑材料。
2. 包装行业:生产塑料袋、塑料瓶、塑料容器等包装制品。
3. 汽车行业:生产汽车零部件,如塑料车门、塑料仪表盘等。
4. 家电行业:生产电视机外壳、冰箱内胆等家电配件。
5. 日用品行业:生产塑料梳子、塑料杯子、塑料衣架等日用品。
总结:塑料挤出成型技术是一种常见的塑料加工方法,通过加热和融化塑料颗粒,然后通过挤出机将熔融塑料挤出成型。
该技术具有工艺简单、生产效率高、适用范围广等优点,被广泛应用于各个领域的塑料制品生产中。
挤出成型的工艺过程
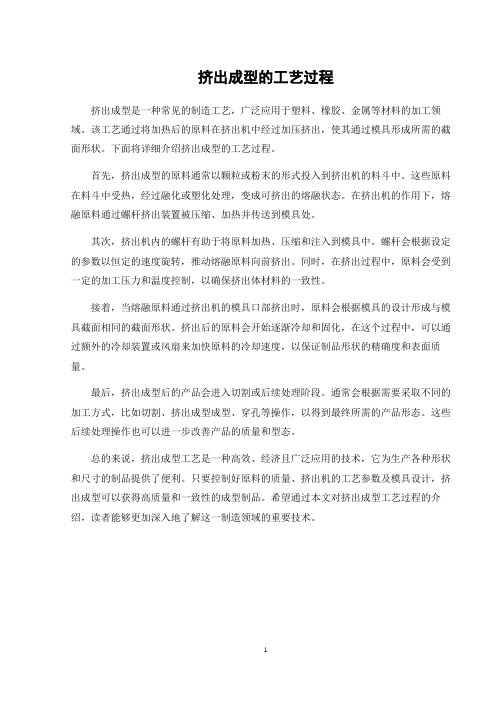
挤出成型的工艺过程
挤出成型是一种常见的制造工艺,广泛应用于塑料、橡胶、金属等材料的加工领域。
该工艺通过将加热后的原料在挤出机中经过加压挤出,使其通过模具形成所需的截面形状。
下面将详细介绍挤出成型的工艺过程。
首先,挤出成型的原料通常以颗粒或粉末的形式投入到挤出机的料斗中。
这些原料在料斗中受热,经过融化或塑化处理,变成可挤出的熔融状态。
在挤出机的作用下,熔融原料通过螺杆挤出装置被压缩、加热并传送到模具处。
其次,挤出机内的螺杆有助于将原料加热、压缩和注入到模具中。
螺杆会根据设定的参数以恒定的速度旋转,推动熔融原料向前挤出。
同时,在挤出过程中,原料会受到一定的加工压力和温度控制,以确保挤出体材料的一致性。
接着,当熔融原料通过挤出机的模具口部挤出时,原料会根据模具的设计形成与模具截面相同的截面形状。
挤出后的原料会开始逐渐冷却和固化,在这个过程中,可以通过额外的冷却装置或风扇来加快原料的冷却速度,以保证制品形状的精确度和表面质量。
最后,挤出成型后的产品会进入切割或后续处理阶段。
通常会根据需要采取不同的加工方式,比如切割、挤出成型成型、穿孔等操作,以得到最终所需的产品形态。
这些后续处理操作也可以进一步改善产品的质量和型态。
总的来说,挤出成型工艺是一种高效、经济且广泛应用的技术,它为生产各种形状和尺寸的制品提供了便利。
只要控制好原料的质量、挤出机的工艺参数及模具设计,挤出成型可以获得高质量和一致性的成型制品。
希望通过本文对挤出成型工艺过程的介绍,读者能够更加深入地了解这一制造领域的重要技术。
1。
《挤出成型技术》课件
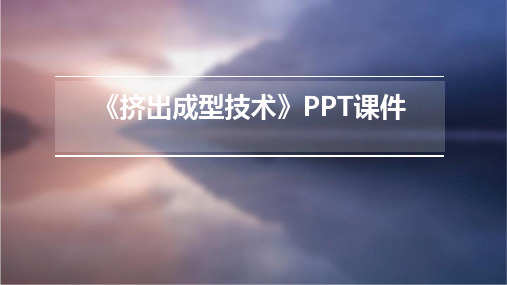
根据制品形状和尺寸进行结构设计,确保制品成型质量、提高生产 效率。
冷却系统
设计合理的冷却系统,控制模具温度,减小制品成型后的收缩率。
挤出成型设备的操作与维护
01
操作规程
制定严格的设备操作规程,确保 操作人员熟悉设备性能和安全操 作要求。
维护保养
02
03
故障排除
定期对设备进行维护保养,检查 各部件磨损情况,及时更换易损 件。
高分子材料在挤出成型技术中的优势在于其可塑性强、加工温度低、成型周期短 等,使得制品具有轻量化、高强度、耐腐蚀等优良性能。同时,高分子材料在挤 出成型过程中易于实现自动化和智能化生产,提高了生产效率和产品质量。
新型挤出成型技术的研发与推广
随着科技的不断发展,新型挤出成型技术不断涌现,如微孔塑料挤出技术、异型截面管材挤出技术、 反应挤出技术等。这些新型技术的研发和应用,极大地丰富了挤出成型制品的种类和性能,满足了不 同领域的需求。
挤出成型技术的应用领域
挤出成型技术广泛应用于塑料加工行业,如管材、型材、薄膜、板材等产品的生产 。
除了塑料加工行业,挤出成型技术还应用于橡胶、陶瓷、玻璃纤维等材料的加工。
随着科技的发展,挤出成型技术的应用领域不断扩大,如3D打印技术的出现,使得 挤出成型技术也可以用于制造个性化的定制产品。
02
挤出成型设备
挤出成型工艺的控制要素
温度控制
温度是挤出成型工艺的重要控制要素之一,包括 机筒温度、模具温度等。温度的控制直接影响着 塑料的塑化和产品质量。
速度控制
速度控制包括挤出速度、注射速度等,它影响着 产品的产量和质量。合理地调整速度参数,可以 提高生产效率和产品质量。
压力控制
压力也是挤出成型工艺的重要控制要素之一,包 括挤出压力、注射压力等。压力的控制对于塑料 的流动性和产品的致密性至关重要。
- 1、下载文档前请自行甄别文档内容的完整性,平台不提供额外的编辑、内容补充、找答案等附加服务。
- 2、"仅部分预览"的文档,不可在线预览部分如存在完整性等问题,可反馈申请退款(可完整预览的文档不适用该条件!)。
- 3、如文档侵犯您的权益,请联系客服反馈,我们会尽快为您处理(人工客服工作时间:9:00-18:30)。
料筒 作用:输送、塑化、压缩 工作温度:180-290℃ 压力:≤55MPa 设有分段加热和冷却装置 制造材料:耐磨、耐腐蚀、高强度的合金钢等 料筒除了可以用45号钢、40Cr、38CrMoAL外,还可以 用铸钢和球墨铸铁制造。带衬套的加料段可以用优质 铸铁制成。
螺杆
(1)作用:输送、挤压、剪切
挤出机的发展
发展方向: 高速、高效、提高自动化水平、
多品种多规格、研制特殊用途
和新型挤出机等方向发展。
机 头和 口 模
螺杆
料筒
加料 装置
传 动 装 置
加料装置及作用 • 有些加料斗还配备真空装置或加热装置,以便防止物料从空 气中吸收水分。有些料斗有振动搅拌器,并能自动上料与加 料。 • 料斗底部有冷却夹套,防止“架桥”。
• 主要是指料斗,大多数设备用的加料斗是圆锥形的,其容量
至少要求能容纳1h的用料。底部有截断装置,以便调整和切 断料流。侧面有玻璃视镜和标定计量的装置。
3 螺杆几何尺寸 生产率qv ∝螺杆直径 D2 正流qvD ∝ 螺槽深度H qvp ∝ H3
4 物料温度 温度的变化直接影响物料的粘度,从我们前面推导出的公式 来看,Q与η 无关。 在机头和口模尺寸不变的情况下,粘度大的物料,螺杆对其 产生的压力高: 结论:Q与温度T也无关。 实际上,T的变化相当于影响了均化段的长度。 5 机头口模的阻力 物料流动时受到阻力,大体上与口模的截面积成反比,与 长度成正比。阻力愈小,挤出量受压力的影响愈大。
(5)螺旋角 θ =10°-30° • 定义:螺纹与螺杆横截面之间的夹角 • θ 大,挤出机的生产能力提高,但螺杆对塑料的 剪切挤压作用减小 • θ =10°-30° • 实验证明: • θ =30°适合细粉状物料;均化段的挤出产率 提高 • θ =15°适合方块状物料 • θ =17°适合圆柱状物料 • 常用螺杆的θ =17.7°
(6)螺杆与料筒的间隙 δ δ 大,生产效率低,剪切作用小,不利于热传导,
不利于物料的熔融和混合
δ 小,剪切作用大,容易引起物料热力学降解 小直径螺杆δ =0.005 DS 大直径螺杆δ =0.002 DS δ =0.1-0.65mm
3
螺杆的作用
• 连续稳定地运输(固体、熔体)
• 熔融、塑化(固体→熔体)
2
挤出成型基本过程
(1)塑化:在挤出机内将固体塑料加热并依靠塑料之间 的内摩擦热使其成为粘流态物料。 (2)成型:在挤出机螺杆的旋转推挤作用下,通过具有 一定形状的口模,使粘流态物料成为连续的型材。 (3)定型:用适当的方法,使挤出的连续型材冷却定型 为制品。
挤出成型工艺流程
加料——在螺杆中熔融塑化——机头口模挤出
根据流动分析,影响挤出机生产能力的是正流、逆流、漏 流,横流对挤出量没有影响 挤出机的生产能力表示为 Qv=Qv,D -Qv,p - Qv,L
影响挤出机生产率的因素
1.机头压力 当机头压力△p=0 可获最大挤出量
当机头口模封闭时无挤出量 机头最大压力降
2 螺杆转速 机头和螺杆的尺寸一定时,挤出量与螺杆转速 成正比。
回,再进行下一次操作,挤出机对物料没有搅拌混合作用。
挤出机能够产生较大的压力,一般来说,其操作是间歇进 行,物料的塑化程度和均匀性不如螺杆式挤出机,因此应用 范围受限制。适用于聚四氟乙烯,超高相对分子质量聚乙烯 等塑料的挤出。
螺杆式挤出机
借助螺杆旋转时螺纹所切作用,促进物料的塑
挤出成型原理
根据塑料在挤出机中的物理状态变化和流动 行为,建立了 • 固体输送理论 • 熔化理论 • 熔体输送理论
(1)正流Qv,D 塑料熔体在料筒和螺杆之间沿着螺槽方向朝机头方向的流 动。它是由旋转螺杆的挤压所造成的,其体积流量用Qv,D
表示。
(2)逆流Qv,p 其流动方向与正流相反,它是由机头、多孔板、过滤板 等阻力引起的压力梯度所造成,又称为压力倒流,其体积
造粒及塑料的共混改性等。 • 橡胶挤出——压出 合成纤维——螺杆挤出纺丝 塑料挤出——主要以热塑性塑料为主
1
挤出成型的特点
(1)操作简单,工艺易控,可连续化、工业化、自动化生产,
生产效率高、应用范围广。
(2)挤出—吹塑成型,中空吹塑制品 挤出—拉幅成型,双轴拉伸薄膜 (3)产品形状多样 (4)设备简单,投资少,占地面积小
(3)螺杆的压缩比A 定义:加料段第一个螺槽容积:均化段最后一个螺槽 容积,表示物料通过螺杆的全过程被压缩的程 度一般是2-5 获得方法:采用等距变深、等深变距、变深变距螺槽 (4)螺槽深度H 决定塑料的塑化及挤出效率 小:剪切速率高,利于传热和塑化,但挤出生产效率低 热敏性塑料——深槽螺杆 热稳定性较高、熔体粘度低——浅槽螺杆 H1≥0.1 DS H3=0.02-0.06 DS
螺杆直径D:Db—螺杆外径 Ds—螺杆根径 D —螺杆平均直径 螺杆长度L:L —螺杆有效工作部分长度 L1—加料段长度 L2—压缩段长度 L= L1 + L2 + L3 L3—均化段长度 螺杆长径比L/D
2
螺杆的几何参数
(1) 螺杆直径DS 外径:30-300mm之间,常见:60-150mm (2) 螺杆的长径比 一般15-25,以25居多,最大可达45 小:对塑料的混合和塑化不利 大:改善塑料的温度分布,混合均匀,减少挤出时的漏流 和逆流,提高挤出机的生产能力;适应性强,可用于多种塑料 的挤出。 过大:热敏性塑料因受热时间太长而容易分解,螺杆的自 重增加,制造和安装都困难,挤出机的功率消耗增大。
流率以Qv,p表示。
(3)横流Qv,T 它是熔体沿着垂直于螺纹壁的流动,它使物料在螺槽内产 生翻转运动,而形成环流。它对挤出量的影响可忽略,但 对挤出过程中熔体的混合和热交换作用却很大。
(4)漏流Qv,L 由于压力梯度在螺杆与料筒间隙处所形成的倒流,其方向 是沿着螺杆的轴向,其体积流率Qv,L表示。
粗滤器、过滤网
作用:使物料流由旋转运动变为直线运动,阻止杂质和
未塑化物料通过并增加料流背压,使制品更加密
实。其中粗滤器还起支撑过滤网的作用,但在挤 出硬聚氯乙烯等粘度大而稳定性差时,一般不用 过滤网。
其它辅助设备 挤出机辅助设备大致可分为以下三类: (1)挤压前物料处理的设备(如预热、干燥等)。 一般用于吸湿性塑料。干燥设备有烘箱或沸腾干燥器等。 有的干燥设备直接设置在加料斗上。 ( 2 )挤出物的处理设备如用作冷却、牵引、卷取、切断和 检验设备。 ( 3 )控制生产条件的设备指各种控制仪表,如温度控制器、 电动机启动装置、电流表、螺杆转数表和测定机头压力的 装置等。
4
螺杆的形式
• 普通螺杆: 采用等距变深、等深变距、变深变距螺槽 • 高效专用螺杆: L/ DS 大、熔融效率低、塑化混合均匀
机头和口模
(1)使粘流态物料从螺旋运动变为平行直线运动,并稳
定地导入口模而成型
(2)产生回压,使物料进一步均化,提高制品质量 (3)产生必要的成型压力,获得结构密实和形状准确的 制品
(2)用耐热、耐腐蚀、高强度的合金钢制作
(3)表面高硬度、高光洁度 (4)转速10-120 rpm、无级变速
1 螺杆的结构
如下图
H2 S H1
θ
计量段 L 3
压料段 L 2 螺杆长度 L D e S 螺杆直径 螺棱宽度 螺距
加料段 L 1
H1 H2 θ
加料段螺槽深度 计量段落槽深度 螺旋角
表征螺杆结构的基本参数
挤出成型加工技术
主要内容
概述 单螺杆挤出机基本结构及作用 挤出成型原理 挤出机的发展
概述
• 挤出成型是使高聚物熔体(或粘性流体)在挤出 机的螺杆 或柱塞的挤压作用下通过一定形状的口模而连续成型,制品 为具有恒定断面形状的连续型材。 • 用于挤出塑料制品,如管材、片材、各种异型材以及塑料和
其它材料的复合物等,也常用于塑料的着色、混炼、塑化、
——定型——冷却——牵引——切割(卷曲)
3
挤出成型设备 螺杆式挤出机 连续成型,用途最多。 柱塞式挤出机 间歇成型,一般不用。
螺杆式挤出机
单螺杆 双螺杆 多螺杆
单螺杆挤出机 双螺杆挤出机 行星螺杆挤出机
其中以单螺杆最常用,也较为简单。
柱塞式挤出机 借助柱塞的推挤压力,将事先塑化好的或由挤出机料筒加 热塑化的物料从机头口模挤出成型的。物料被挤完后柱塞退
• 混合、均化(温度、组成分布均匀)
• 增压—有利于排气、传热,使制品密实
(1) 加料段L1(固体输送段) 作用:加热送来的物料并输送到压缩段 (2) 压缩段L2(熔融段) 作用:挤出和剪切加料段送来的物料,加热物料使其转变 为熔融体,赶走塑料中的空气及其它挥发成分,增大塑料 的密度。 无定形塑料,熔融温度范围宽,渐变螺杆 结晶型塑料,熔融温度范围窄, 突变螺杆 (3) 均化段(计量段) 作用:将塑化均匀的物料在均化段螺槽和机头回压作用下 进一步搅拌塑化均匀,并定量定压的通过机头口模挤出成 型。一般无压缩作用。
化和均匀分散,同时使挤出过程连续进行,因此可以提 高挤出制品的质量和产量。适用于绝大多数热塑性塑料 的挤出。
单螺杆挤出机基本结构及作用
• 传动系统 • 挤出系统——挤出成型系统的关键部分 加料装置、料筒、螺杆、机头、口模 • 加热系统:采用电阻丝加热,也可电感应加热, 蒸汽或油加热。 • 冷却系统:空冷或水冷,其作用是防止进料口处 的物料过热发粘,出现搭桥现象,使 物料供料不足。另外在紧急停车时, 避免物料过热降解。