数控系统主轴
数控机床主轴控制_图文
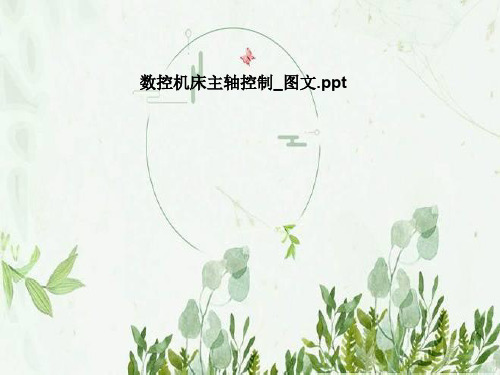
5.1.3高速主轴的设计
表5-1铝合金在切削实验中切削速度和表面粗糙度的关系
转速/r﹒min-1 进给量 /mm﹒min-1
10000 20000 30000 40000
1000 2000 3000 4000
切削速度 /m﹒min-1 785 1570 2356 3142
Ra/μm
0.56 0.46 0.32 0.32
5.2.1主轴直流电动机
图5-11
直流主轴电动机结构示意图
5.2.2、直流主轴驱动控制系统
数控机床常用的直流主轴驱动系统的原理框图如图5-13所示。
(图5-13) 直流主轴驱动系统原理图
实际直流电机的电刷和换向片:
直流电机的基本结构
电机模型的各组成部件
固有机械特性
称为理想空载转速
V2 W1
n
U1
U2
W2 V1
三相绕组基波合成磁动势——旋转磁动势
交流电机三相对称绕组, 通入三相对称电流,磁动势是三相 的合成磁动势。
取U相绕组轴线位置作为空间坐标原点、以相序的方向作为 x的参考方向、U相电流为零时作为时间起点,则三相基波磁动 势为:
三相的合成磁动势:
可见:三相合成磁动势也是一个圆形旋转磁动势。
(4)励磁回路方程
(5)气隙磁通
。U 。
I Ia
M Ea
。 Uf 。
Φ
5.2.2、直流主轴驱动控制系统
1调磁调速回路 图5-13的上半部分为励磁控制回路,由于主轴电动
机功率通常较大,且要求恒功率调速范围尽可能大 ,因此,一般采用他励电动机,励磁绕组与电枢绕 组相互独立,并由单独的可调直流电源供电。
2、交流主轴驱动系统
5.1.2主轴变速方式
数控车床主轴定位故障原因及维修方法

数控车床主轴定位故障原因及维修方法数控车床主轴定位故障原因及维修方法数控车床主轴是数控车床的核心部件,负责驱动工件进行切削加工。
然而,有时候主轴的定位会出现故障,导致加工精度下降,甚至无法正常工作。
本文将探讨数控车床主轴定位故障的原因,并提供一些常见的维修方法。
1. 主轴定位故障的原因:1.1 主轴轴承故障:主轴轴承是支撑主轴的重要部件,如果轴承出现磨损、松动或损坏,会导致主轴定位不准确。
常见的原因包括润滑不良、使用时间过长、过度负载或工作环境恶劣等。
1.2 主轴螺纹松动:主轴和主轴螺套之间的螺纹连接如果松动,会导致主轴的定位不稳定。
这可能是由于螺纹未拧紧、螺纹磨损或螺纹螺母松动等原因造成的。
1.3 电机控制系统故障:数控车床主轴是由电机驱动的,如果电机控制系统出现故障,如电机驱动器故障、电源问题或连接线路松动等,都可能导致主轴定位不准确。
2. 维修方法:2.1 检查和更换主轴轴承:首先,需要检查主轴轴承的状态。
如果发现轴承存在磨损、松动或损坏的情况,应及时更换新的轴承。
此外,定期进行轴承的润滑也是必要的,可以减少轴承的磨损。
2.2 检查和紧固主轴螺纹连接:检查主轴和主轴螺套之间的螺纹连接,确保其紧固度。
如果发现连接松动,可以使用适当的工具进行拧紧。
如果螺纹磨损严重,建议更换新的螺纹部件。
2.3 检查和修复电机控制系统:检查电机控制系统,确保电机驱动器和电源正常工作。
如果发现故障,需要修复或更换故障部件。
同时,还应检查相关连接线路,确保连接牢固。
需要注意的是,维修数控车床主轴定位故障需要有专业的技术人员进行操作,因为涉及到机械和电气方面的知识。
此外,定期的保养和维护也是预防主轴定位故障的重要举措,可以延长数控车床的使用寿命,并提高加工精度。
新代数控主轴定位参数

新代数控主轴定位参数一、引言随着制造业的发展,新代数控主轴定位参数成为了越来越重要的话题。
在传统的数控机床中,主轴定位参数是通过手动调整来实现的。
然而,在新代数控机床中,主轴定位参数是通过自动化系统来实现的。
这种自动化系统可以提高生产效率和质量,并减少操作员的劳动强度。
二、什么是新代数控主轴定位参数新代数控主轴定位参数是指在数控机床中,用于确定主轴位置和方向的一组参数。
这些参数包括:角度误差、径向误差、偏心误差、圆度误差等。
这些误差会影响到加工件的精度和表面质量。
三、新代数控主轴定位参数如何测量1. 角度误差测量角度误差可以通过旋转台和激光干涉仪来测量。
首先,在旋转台上安装一个激光干涉仪,然后将旋转台旋转一周,并记录下每个角度下激光干涉仪所测得的距离值。
最后,通过计算得出每个角度下的角度误差。
2. 径向误差测量径向误差可以通过径向跳动检测器来测量。
径向跳动检测器是一种可以检测主轴径向跳动的设备,它可以通过感应器和信号处理器来检测主轴的径向运动。
通过对信号进行处理,可以得到主轴的径向误差。
3. 偏心误差测量偏心误差可以通过离心试验机来测量。
离心试验机是一种可以模拟主轴偏心运动的设备,它可以通过旋转试验样品来模拟主轴在不同偏心位置下的运动状态。
通过对试验数据进行处理,可以得到主轴的偏心误差。
4. 圆度误差测量圆度误差可以通过圆度检测仪来测量。
圆度检测仪是一种可以检测加工件圆度误差的设备,它可以通过感应器和信号处理器来检测加工件表面的形状变化。
通过对信号进行处理,可以得到加工件表面的圆度误差。
四、新代数控主轴定位参数如何调整1. 角度误差调整角度误差可以通过调整机床床身和导轨间隙、调整主轴安装位置、调整主轴前后端面的距离等方式来调整。
2. 径向误差调整径向误差可以通过更换主轴轴承、调整主轴支撑结构、调整主轴前后端面的距离等方式来调整。
3. 偏心误差调整偏心误差可以通过更换主轴轴承、调整主轴支撑结构、增加平衡质量等方式来调整。
数控机床主轴的几种结构形式

数控机床主轴的几种结构形式
作者: 日期:
n
数控机床的主轴部件包括主轴、主轴的支承轴承和安装在主轴上的传动零件等。
主轴部件是机床的重要部件,其结构的先进性已成为衡量机床水平的标志之一。
由于数控机床的转速高、功率大,并且在加工过程中不进行人工调整,因此要求主轴部件具有良好的回转精度、结构刚度、抗振性、热稳定性、耐磨性和精度的保持性。
对于具有自动换刀装置的数控机床,为了实现刀具在主轴上的自动装卸和夹紧,还必须有刀具的自动夹紧装置、主轴准停装置等。
机床主轴的端部一般用于安装刀具、夹持工件或夹具。
在结构上,应能保证定位准确、安装可靠、连接牢固、装卸方便,并能传递足够的扭矩。
目前,主轴端部的结构形状都已标准化,图i所示为几种机床上通用的结构形式。
(a)数控车床主轴端部(b)铣、镗类机床主轴端部(c)外圆磨床砂轮主轴端部
(d)内圆磨床砂轮主轴端部(e)钻床与普通镗床锤杆端部(f)数控镗床主轴端部
图1机床主轴的几种结构形式。
数控机床主轴结构
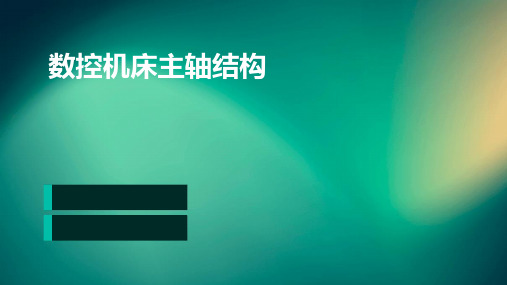
材料优化
结构形状优化
轴承配置优化
选用高性能材料,如合 金钢、陶瓷等,提高主
轴的刚度和耐磨性。
通过改变主轴的形状和 尺寸,优化其刚度和质 量分布,提高动态性能。
合理选择和配置轴承, 提高主轴的旋转精度和
稳定性。
冷却与润滑优化
改进冷却和润滑系统, 降低主轴温升和摩擦磨
损,提高使用寿命。
案例分析:某型号数控机床主轴设计
发展历程及现状
发展历程
随着数控技术的不断发展,主轴结构 经历了从简单到复杂、从低速到高速 、从低精度到高精度的演变过程。
现状
目前,数控机床主轴结构已经实现了 高速化、高精度化、高刚性化、高可 靠性化等目标,满足了现代制造业对 高效率、高质量加工的需求。
市场需求与应用前景
市场需求
随着制造业的快速发展,数控机床主轴的市场需求不断增长。特别是在汽车、 航空航天、模具等高端制造领域,对高精度、高效率的主轴需求尤为迫切。
维护效果
经过维护后,数控机床主轴的发热和振动问题得到了有效解决,主轴运 转恢复正常。此次维护不仅提高了设备的稳定性和加工精度,也延长了 设备的使用寿命。
06 主轴结构发展趋势与展望
技术创新方向
高速、高精度主轴技术
通过优化主轴结构、提高制造精度和采用先进的控制策略,实现 主轴的高速、高精度运转,满足高端数控机床的加工需求。
致。
主轴振动
可能是主轴动平衡不良、轴承磨 损或主轴电机故障等原因引起。
主轴转速不稳定
可能是主轴电机故障、电源电压 不稳定或控制系统故障等原因造
成。
维护保养方法与建议
定期检查主轴轴承预紧力, 确保其在合适范围内。
定期检查主轴动平衡,如 有必要,进行动平衡调整。
FANUC数控系统主轴参数

FANUC数控系统主轴参数1. 主轴转速(Spindle Speed)主轴转速是指主轴每分钟旋转的圈数,通常以转/分钟(rpm)为单位。
FANUC数控系统通常具有高精度的主轴调速系统,可以根据加工要求调节主轴转速,以满足不同工件材料和加工方式的需求。
2. 主轴加速度(Spindle Acceleration)主轴加速度是指主轴从静止状态加速到设定转速时所需的时间。
在精密加工中,主轴加速度的快慢对加工质量、工件表面质量和主轴寿命都有重要影响。
FANUC数控系统通常具有大范围的主轴加速度调节功能,可以根据不同工艺要求进行调整。
3. 主轴减速度(Spindle Deceleration)主轴减速度是指主轴从设定转速减速到静止状态所需的时间。
主轴减速度的合理设置可以保证主轴停止后位置的精度,减少工件因主轴停转而产生的负面影响。
FANUC数控系统通常具有调整主轴减速度的功能,可以根据工件的要求和机床性能进行调整。
4. 主轴定位精度(Spindle Positioning Accuracy)主轴定位精度是指主轴停止后,在指定位置能够保持的精度。
在高精度加工中,主轴定位精度对工件的加工精度至关重要。
FANUC数控系统通常具有高精度的主轴定位控制系统,可以保证主轴在停止后的位置精度。
5. 主轴控制方式(Spindle Control Mode)主轴控制方式是指主轴的启停和转速控制方式。
FANUC数控系统通常具有多种主轴控制方式,如手动控制、自动控制、远程控制等。
不同的主轴控制方式可以满足不同的加工需求。
6. 主轴力矩(Spindle Torque)主轴力矩是指主轴旋转时所产生的力矩。
主轴力矩的大小决定了机床能够承受的加工负荷,对于大型工件的加工尤为重要。
FANUC数控系统通常可以根据加工要求调整主轴力矩,以适应不同的工作情况。
7. 主轴冷却方式(Spindle Cooling Method)主轴冷却方式是指主轴散热的方式。
机床数控系统的组成
机床数控系统的组成机床数控系统是现代机床的核心技术之一,它由多个组成部分构成,共同实现对机床的自动化控制和加工操作。
本文将从硬件和软件两个方面介绍机床数控系统的组成。
一、硬件组成1.主轴驱动系统:主轴驱动系统是机床数控系统的核心部分,它负责控制主轴的转速和运动方向。
主轴驱动系统通常由伺服电机、减速器、编码器等组成,通过对电机的控制,实现对主轴的精确控制。
2.进给驱动系统:进给驱动系统用于控制工件在加工过程中的运动轴向,包括直线进给轴和旋转进给轴。
直线进给轴通常由伺服电机、滚珠丝杠等组成,用于控制工件的直线运动;旋转进给轴通常由伺服电机、齿轮传动等组成,用于控制工件的旋转运动。
3.运动控制卡:运动控制卡是机床数控系统的核心控制器,它负责接收数控指令,并将其转换为电信号,通过与主轴驱动系统和进给驱动系统的配合,实现对机床的精确控制。
运动控制卡通常具备高速数据处理能力和多个输入输出接口,以满足机床复杂加工过程的控制需求。
4.传感器:传感器是机床数控系统的重要组成部分,用于实时监测机床的运行状态和工件加工过程中的各种参数。
常见的传感器包括位置传感器、力传感器、温度传感器等,它们通过与运动控制卡的连接,将采集到的数据反馈给数控系统,以实现对机床的自动化调节和控制。
5.人机界面:人机界面是机床数控系统与操作人员之间的交互界面,用于输入加工参数、监视加工过程和显示加工结果等。
人机界面通常由触摸屏、键盘、显示器等组成,操作人员可以通过它们与数控系统进行交互,并实时了解机床的工作状态。
二、软件组成1.数控系统软件:数控系统软件是机床数控系统的核心程序,它负责解释和执行数控指令,控制机床的运动和加工过程。
数控系统软件通常由操作系统、驱动程序、插补算法等组成,它们共同实现对机床的高精度控制和加工操作。
2.加工程序:加工程序是机床数控系统的另一重要组成部分,它是由一系列数控指令组成的程序,用于描述工件的加工路径和加工过程。
FANUC数控系统主轴参数
FANUC数控系统主轴参数以FANUC-Oi(M 型) 数控系统为例, 介绍主轴齿轮换档参数的合理应用。
1 齿轮换档方式A如图1 所示, 主轴的3 个档位所对应的主轴电动机最高限定速度是相同的。
例如XH756 卧式加工中心, 主轴低档的齿轮传动比为11:108, 中档的齿轮传动比为11:36, 高档的齿轮传动比为11:12; 机械设计要求主轴低档时的转速范围是O-458r/min, 中档的转速范围是459-1375r/min, 高档的转速范围是1376-4125r/min, 主轴电动机的最低速度限定为150r/min。
主轴电动机给定电压为1OV 时, 对应的主轴电动机速度为6000r/min。
通过计算可知各个档位的主轴电动机最高转速相同,均为4500r/min。
此时参数应设定如下:参数N0.3736( 主轴速度上限,Vmax=4095 ×主轴电动机速度上限/指令电压10V 的主轴电动机速度) 设定为4095 × 4500/6000=3071。
参数N0.3735( 主轴速度下限,Vmax=4095 ×主轴电动机速度下限/ 指令电压为10V 的主轴电动机速度) 设定为4095 × 150/6000=102。
参数N0.3741( 指令电压1OV 时对应的主轴速度A, 低档) 设定为6000 × 11/108=611。
参数N0.3742( 指令电压10V 时对应的主轴速度B, 中档) 设定为6000 × 11/12=1833 。
参数N0.3743( 指令电压10V 时对应的主轴速度C, 高档) 设定为6000 × 11/12=5500 。
按照以上参数设定, 该机床速度范围合理覆盖, 并在PMC 程序中自动判别, 合理选择档位。
2 齿轮换档方式B如图2 所示, 主轴的3 个档位所对应的主轴电动机最高限定速度是不同的。
例如主轴低档齿轮传动比为11:108, 主轴中档齿轮传动比为260:1071, 主轴高档齿轮传动比为169: 238, 而机械设计要求主轴低档的转速范围是O-401r/min, 主轴中挡的转速范围是402-1109r/min, 主轴高档的转速范围是1110-3000r/min。
FANUC数控系统主轴参数
FANUC数控系统主轴参数1.主轴转速参数:主轴转速是指主轴每分钟旋转的转数,通常以转/分为单位。
在FANUC数控系统中,可以通过参数设置来调整主轴转速,并且可以根据加工要求进行多级转速调节。
主轴转速参数对于机床的切削效率、加工质量和工件加工尺寸等方面起着重要作用。
2.主轴加减速时间参数:主轴加减速时间是指主轴从零速度加速到设定转速所需的时间,或者从设定转速减速到零速度所需的时间。
在FANUC数控系统中,可以通过设置参数来调整主轴的加减速时间,以满足不同的加工需求和切削条件。
3.主轴最大转矩参数:主轴最大转矩是指主轴所能输出的最大转矩。
在机床加工过程中,有些加工工艺需要较大的主轴转矩来完成,因此主轴最大转矩参数对于选择合适的切削条件和保证切削质量非常重要。
4.主轴径向定位精度参数:主轴径向定位精度是指主轴在旋转过程中的径向定位误差。
在金属切削加工中,主轴径向定位精度对于保证工件加工尺寸的精度非常重要。
在FANUC数控系统中,可以通过调整参数来优化主轴径向定位精度。
5.主轴轴向定位精度参数:主轴轴向定位精度是指主轴在旋转过程中的轴向定位误差。
对于需要进行轴向移动或轴向定位的加工工艺,主轴轴向定位精度对于保证加工质量和工件的准确位置非常关键。
6.主轴行程参数:主轴行程是指主轴在轴向运动中的有效行程范围。
在FANUC数控系统中,可以通过参数设置来限制主轴的行程范围,以防止机床意外超出行程范围导致故障或意外损坏。
总结起来,FANUC数控系统主轴参数包括主轴转速、主轴加减速时间、主轴最大转矩、主轴径向定位精度、主轴轴向定位精度和主轴行程参数等。
这些参数对于保证机床的切削效率、加工质量和工件加工尺寸有着重要作用,并且可以通过FANUC数控系统的参数设置来进行调整和优化。
数控原理与系统第6章主轴驱动及控制
第6章 主轴驱动及控制
为 此 , 可 选 用 额 定 功 率 7.4KW 、 额 定 转 速
1500r/min的主轴电动机,在1/2额定电压下无
级变速驱动主轴,工作特性曲线如图6.6所示。
在 750r/min ~ 6000r/min 整 个 范 围 内 ,
Pmax=3.7KW , 在 750r/min 以 下 ,
频器调速时,其调速特性无法与直流电动机相
比, 因此必须采用矢量变频控制技术。
第6章 主轴驱动及控制
由于采用矢量变频控制技术后,交流
电动机与直流电动机的数学模型极为相似,
因而以直流主轴电动机为例来分析其调速特
性, 其模型结构如图6.1所示。
根据直流电动机的工作原理可得
Ua Ia Ra E
E Cen M C M Ia KIt
第6章 主轴驱动及控制
P, M
转矩特性曲线 功率特性曲线
O1
2
h
图6.2 主轴电机的工作特性曲线
第6章 主轴驱动及控制
6.1.3 CNC与主轴驱动装置的连接 下面以日本安川(YASKAWA)VA-626MT
型主轴驱动装置为例讲解CNC与主轴驱动装置 的连接,图6.3所示为其内部原理框图, CNC装 置与该主轴驱动装置的连接如图6.4所示。
第6章 主轴驱动及控制
本章导读
本章主要介绍主轴驱动装置的特性与连接
方法、主轴分段无级调速控制、主轴准停控制
等内容。通过本章的学习,了解数控机床对主
轴的要求,熟悉主轴驱动装置的一般连接方法,
掌握主轴调速、准停控制方法。
第6章 主轴驱动及控制
6.1 概 述
数控机床的主轴驱动和进给驱动有很大的
差别。主轴的运动通常是旋转运动,以调速和
- 1、下载文档前请自行甄别文档内容的完整性,平台不提供额外的编辑、内容补充、找答案等附加服务。
- 2、"仅部分预览"的文档,不可在线预览部分如存在完整性等问题,可反馈申请退款(可完整预览的文档不适用该条件!)。
- 3、如文档侵犯您的权益,请联系客服反馈,我们会尽快为您处理(人工客服工作时间:9:00-18:30)。
10000r/min以上。
数控系统主轴
四、常用的主轴驱动系统介绍
n 1、FANUC(法那科)公司主轴驱动系统 n 目前三个系列交流主轴电动机为: n S系列电动机,额定输出功率范围1.5~37KW; n H系列电动机,额定输出功率范围1.5~22KW; n P系列电动机,额定输出功率范围3.7~37KW。
数控系统主轴
5、伺服主轴驱动系统
n
伺服主轴驱动系统具有响应快、速度
高、过载能力强的特点,还可以实现定向
和进给功能,当然价格也是最高的,通常
是同功率变频器主轴驱动系统的2--3倍以
上。伺服主轴驱动系统主要应用于加工中
心上,用以满足系统自动换刀、刚性攻丝、
主轴C轴进给功能等对主轴位置控制性能要
求很高的加工。
n 1PH5和1PH6两个系列的交流主轴电动机,功率范围为 3~100KW。驱动装置为6SC650系列交流主轴驱动装置 或6SC611A(SIMODRIVE 611A)主轴驱动模块,主 回路采用晶体管SPWM变频器控制的方式,具有能量再生 制动功能。另外,采用为处理器80186可进行闭环转速、 转矩控制及磁场计算,从而完成矢量控制。同过选件实现 C轴进给控制,在不需要CNC的帮助下,实现主轴的定位 控制。
数控系统主轴
6、电主轴
n
电主轴伺服,也可以
不要驱动器。电主轴由于电机和主轴合二
为一,没有传动机构,因此,大大简化了
主轴的结构,并且提高了主轴的精度,但
是抗冲击能力较弱,而且功率还不能做得
太大,一般在10KW以下。由于结构上的优
势,电主轴主要向高速方向发展,一般在
数控系统主轴
3、DANFOSS(丹佛斯)公司系列 变频器
n
目前应用于数控机床上的变频器系列
常用的有:VLT2800,可并列式安装方式,
具有宽范围配接电机功率:0.37KW-
7.5KW 200V/400;VLT5000,可在整个
转速范围内进行精确的滑差补偿,并在
3ms内完成。在使用串行通讯时,VLT
数控系统主轴
3、普通笼型异步电动机配通用变频 器
n
目前进口的通用变频器,除了具有
U/f曲线调节,一般还具有无反馈矢量控制
功能,会对电动机的低速特性有所改善,
配合两级齿轮变速,基本上可以满足车床
低速(100—200转/分钟)小加工余量的
加工,但同样受最高电动机速度的限制。
这是目前经济型数控机床比较常用的主轴
数控系统主轴
二、数控机床对主轴驱动系统的要 求
n
机床主轴的工作运动通常是旋转运动,数
控机床通常通过主轴的回转与进给轴的进给实现
刀具与工件的快速的相对切削运动。
1、调速范围宽并实现无极调速
2、恒功率范围要宽
3、具有4象限驱动能力
4、具有位置控制能力
5、具有较高的精度与刚度,传动平稳,噪音低。
6、良好的抗振性和热稳定性
n
可以实现主轴的无级调速,主轴电动机只有
工作在约500转/分钟以上才能有比较满意的力矩
输出,否则,特别是车床很容易出现堵转的情况,
一般会采用两挡齿轮或皮带变速,但主轴仍然只
能工作在中高速范围,另外因为受到普通电动机
最高转速的限制,主轴的转速范围受到较大的限
制。
n 这种方案适用于需要无级调速但对低速和高速都 不要求的场合,例如数控钻铣床。国内生产的简 易型变频器较多。
数控系统主轴
2020/11/21
数控系统主轴
数控机床主传动系统是用 来实现机床主运动的,它将主 电动机的原动力变成可供主轴 上刀具切削加工的切削力矩和 切削速度。典型数控机床主传 动系统外观如左图。
数控系统主轴
§ 6.1概述
n
数控机床的主轴驱动系统也就是主传动系统,
它的性能直接决定了加工工件的表面质量,因此,
驱动系统。
数控系统主轴
4、专用变频电动机配通用变频器
n 中档数控机床主要采用这种方案,主轴传 动两挡变速甚至仅一挡即可实现转速在 100—200r/min左右时车、铣的重力切削。 一些有定向功能的还可以应用与要求精镗 加工的数控镗铣床,若应用在加工中心上, 还不很理想,必须采用其他辅助机构完成 定向换刀的功能,而且也不能达到刚性攻 丝的要求。
数控系统主轴
三、 不同类型的主轴系统的特点和 使用范围
n 1、普通笼型异步电动机配齿轮变速箱
n
这是最经济的一种方法主轴配置方式,
但只能实现有级调速,由于电动机始终工
作在额定转速下,经齿轮减速后,在主轴
低速下输出力矩大,重切削能力强,非常
适合粗加工和半精加工的要求。
数控系统主轴
2、普通笼型异步电动机配简易型变 频器
5000对每条指令的响应时间为0.1ms,可
使用任何标准电机与VLT 5000匹配。
数控系统主轴
4、HITACHI(日立)公司系列变频 器
n
HITACHI公司的主轴变频器应用于数控机
床上通常有:L100系列通用型变频,额定输出功
率范围为0.2KW-7.5KW, V/f 特性可选恒转矩
/降转矩,可手动/自动提升转矩,载波频率
在数控机床的维修和维护中,主轴驱动系统显得
很重要。
一、概述
主轴驱动系统也叫主传动系统,是在系统
中完成主运动的动力装置部分。主轴驱动系统通 过该传动机构转变成主轴上安装的刀具或工件的 切削力矩和切削速度,配合进给运动,加工出理 想的零件。它是零件加工的成型运动之一,它的 精度对零件的加工精度有较大的影响。
该公司交流主轴驱动系统的特点为:①采用为处 理器控制技术,进行矢量计算,从而实现最佳控 制。②主回路采用晶体管PWM逆变器,使电动机 电流非常接近正弦波性。③具有主轴定向控制、 数字和模拟输入接口等功能。
数控系统主轴
2、SIEMENS(西门子)公司主轴 驱动系统
n SIEMENS公司生产的直流主轴电动机有1GG5、1GF5、 1GL5和1GH5四个系列,与这四个系列电动机配套的 6RA24、6RA27系列驱动装置采用晶闸管控制。
0.5HZ-16HZ连续可调。日立 SJ100系列变频器,
是一种矢量型变频,额定输出功率范围为
0.2KW-7.5KW,载波频率在0.5HZ-16HZ内连
续可调 ,加减速过程中可分段改变加减速时间 ,
可内部/外部启动直流制动;日立 SJ200/300系
列变频器,额定输出功率范围为0.75KW-
132KW,具有2台电机同时无速度传感器矢量控