热轧板带钢生产压下规程设计
1250热轧板带轧制规程设计

1250热轧板带轧制规程设计一、前言热轧板带是金属材料加工过程中常用的一种形式,具有广泛的应用领域。
为了保证产品质量和生产效率,制定一套科学合理的热轧板带轧制规程非常重要。
本文将介绍一种热轧板带轧制规程设计,旨在优化生产流程,提高生产效率。
二、制定背景以钢材为例,热轧板带是制造厚度在4.5mm及以下的钢材的重要工艺步骤。
因此,制定一套适用于厚度为4.5mm及以下的热轧板带轧制规程,对于提高钢材生产效率、保证产品质量起到重要作用。
三、规程设计要点1.轧制工艺设计:根据产品要求和材料特性,确定轧制工艺,包括轧制温度、轧制次数和轧制速度等。
轧制温度应根据材料的硬度和塑性选定,轧制次数和轧制速度应根据材料的厚度和要求的成品尺寸来确定。
2.设备选择与调试:根据热轧板带的设备和生产工艺要求,选购适当的轧机、辅助设备和检测设备。
同时,进行设备的调试和优化,保证轧制工艺的稳定和精确性。
3.质量控制:制定合理的质量控制方案,包括质量检测、质量评价和质量监控。
采用合适的检测工具,如超声检测、硬度检测等,对产品进行质量检测。
对于不合格品,进行返修或者剔除,以提高产品质量。
4.生产计划与调度:制定合理的生产计划和调度方案,根据市场需求和设备运行情况,合理安排生产任务。
及时调整生产计划和调度,以确保生产效率和产品质量。
5.工艺优化和持续改进:根据生产实践和市场需求,对热轧板带轧制规程进行优化和改进。
通过改变工艺参数,提高生产效率和产品质量。
同时,积极引进先进的生产工艺和设备,不断进行技术创新和改进。
四、总结与展望热轧板带轧制规程是保证产品质量和提高生产效率的重要手段。
本文提出了一种针对厚度为4.5mm及以下热轧板带的轧制规程设计。
通过制定合理的轧制工艺、选择适当的设备、实施质量控制、优化生产计划和调度,并进行工艺优化和持续改进,可以提高生产效率和产品质量,满足市场需求。
展望未来,可以进一步研究和发展轧制工艺和设备,提高轧制效率和产品质量,进一步提高热轧板带的应用范围和市场竞争力。
热轧板带钢轧制规程设计

热轧板带钢轧制规程设计一、引言热轧板带钢是一种广泛应用于工业领域的金属材料,其性能的稳定性和质量的优越性对产品的质量和使用寿命至关重要。
因此,热轧板带钢的制造过程需要遵循一定的规程和标准,以确保产品质量的稳定性。
本文将介绍一个热轧板带钢的轧制规程设计。
二、设计目标本轧制规程的设计目标是制定一套科学合理的生产工艺和操作规程,以确保热轧板带钢的质量和性能达到预期要求。
具体的设计目标包括:1.确定合适的轧制温度和轧制速度,以确保给定的产品尺寸和机械性能的要求。
2.设计适当的冷却方式,以确保产品在冷却过程中达到理想的组织结构。
3.确定合适的轧制压力和辊缝尺寸,以确保产品的形状和尺寸的精度。
4.设计适当的轧制工艺和操作规程,以确保生产过程的稳定性和可控性。
5.设计合适的质量检验方法和标准,以确保产品的质量符合要求。
三、设计思路本轧制规程的设计思路是在充分了解产品需求和原材料性能基础上,通过迭代优化的方式确定最佳的轧制工艺和操作规程。
具体的设计思路包括:1.通过分析产品的尺寸要求、力学性能要求和成分要求等,确定轧制温度和轧制速度的范围。
根据产品的板厚和钢种,选择适当的温度和速度条件,以满足产品的性能要求。
2.设计合适的冷却方式,以确保产品在冷却过程中达到理想的组织结构。
根据产品的厚度和形状,选择适当的冷却方式,并确定冷却速度、冷却介质等参数。
3.确定合适的轧制压力和辊缝尺寸,以确保产品的形状和尺寸的精度。
通过分析产品的厚度、宽度和长度要求,选取合适的辊缝尺寸,并确定合适的轧制压力。
4.设计合适的轧制工艺流程和操作规程,以确保生产过程的稳定性和可控性。
根据产品的尺寸和性能要求,确定轧制的工艺流程,并设计详细的操作规程。
5.设计合适的质量检验方法和标准,以确保产品的质量符合要求。
制定合适的质量检验方法和标准,进行产品的质量检验和评价。
四、设计步骤1.分析产品需求和原材料性能,确定轧制温度和轧制速度的范围。
2.设计合适的冷却方式,确定冷却速度和冷却介质。
课程设计压下规程

(1)概述制定压下规程的方法很多,一般为经验法和理论法两大类。
经验方法是参照现有类似轧机行之有效的实际压下规程(经验资料)进行压下分配及校核计算。
理论方法就是从充分满足前述制定的轧制规程的原则要求出发,按预设的条件通过数学模型计算或图表方法,以求最佳的轧制规程。
这是理想和科学的方法。
通常在板带生产中制订压下规程的方法和步骤为:1)根据原料、产品和设备条件,在咬入能力允许的条件下,按经验分配各道次压下量,这包括直接分配各道次绝对压下量或压下率、确定各道次压下量分配率()及确定各道次能耗负荷分配比等各种方法;2)制定速度制度,计算轧制时间并确定逐道次轧制温度;3)计算轧制压力、轧制力矩及总传动力矩;4)校核轧辊等部件的强度和电机过载过热能力;5)按前述制订轧制规程的原则和要求进行必要的修正和改进。
(2)限制压下量的因素限制压下量的因素:金属塑性、咬入条件、轧辊强度及接轴叉头等的强度条件、轧制质量。
最大咬入角与轧制速度的关系见表2-1。
表2-1 最大咬入角与轧制速度的关系轧制速度0 0.5 1.0 1.5 2.0 2.5 3.5/m/s最大咬入角/0 25 23 22.5 22 21 17 11(3)道次压下量的分配规律道次压下量通常有两种分配规律。
1)中间道次有最大的压下量,开始道次受到咬入条件的限制,同时考虑到热轧的破鳞作用及坯料的尺寸公差等,为了留有余地,给予小的压下量。
以后为了充分利用钢的高温给予大的压下量。
随着轧件温度下降,轧制压力增大,压下量逐渐减小。
最后为了保证板形采用较小的压下量,但这个压下量又必须大于再结晶的临界变形量,以防止晶粒过粗大,如图2-1(a)所示。
2)压下量随道次逐渐减小? 压下量在开始道次不受咬入条件限制,开轧前除鳞比较好,坯料尺寸比较精确,因此轧制一开始就可以充分利用轧件的高温采用大的压下量,以后随轧件温度的下降压下量逐渐减少,最后1~2道次为保证板形采用小的压下量,须大于再结晶的临界变形量,如图2-1(b)所示。
H68(Y)热轧压下规程

18.09
5 44 33 11.00 25.00 16.67 462.05 466.58 464.32 4.53 20659 27278 10.91 10.00 20.91 9.22 773.78 3.60 16.03 757.75 765.77 68.37 31747 90.00 10.45 0.80 0.30 1.15 24.84 28.57 1.23 35.11 1119.99 0.44 67.39 2.42 0.80 3.22 5.39 16.45 2.01 681.50 2250.00 2500 8.597 0.91 540 0.004 29.54 2.91 639.10 150.32 105.98 90.00
32 轧制压力 P
KN
33 力臂系数x
34 轧制力矩MZ
KN*m
35 轧辊轴承中附加摩擦力矩Mf1 KN*m
36 传动机构中附加摩擦力矩Mf2 KN*m
37 摩擦力矩 Mf
KN-m
38 空转力矩 M0
KN-m
39 静力矩Mc
KN-m
40 等效力矩M'
10^4N-m
41 计算电机功率N
KW
42 选择电机功率N
2500 8.597 0.91 540 0.004 155.15 33.76
13.03
4 63 44 19.00 30.16 20.11 454.87 462.05 458.46 7.18 14656 20659 8.26 10.00 18.26 12.12 784.73 3.60 10.95 773.78 779.26 89.86 41198 90.00 9.88 0.85 0.29 1.12 24.85 28.57 1.20 34.43 1429.53 0.58 149.01 3.09 1.75 4.84 11.92 34.09
金属压力加工车间设计之热轧板带钢轧制规程设计(56页)
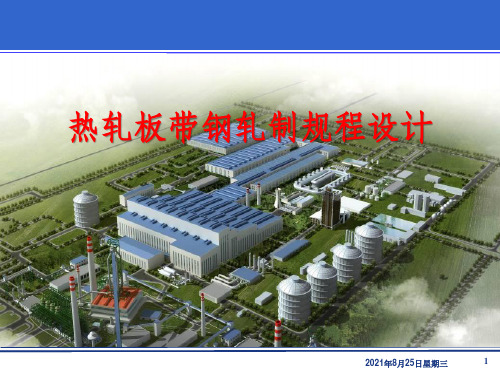
在校核粗轧机咬 入能力时,取机 架最大压下量的 那道次进行,精 轧F1~F3可取 F1较核,F4~ F7可取F4校核.
热轧带钢时,最大咬入角一般为15°~20°,低速轧制时为20°, 所以上述咬入角符合条件,咬入能力满足。
2021年8月25日星期三
19
3 速度制度设计-粗轧速度制度
粗轧为可逆式轧制,一般采用梯形速度图
38.1
34.8
16.76 9.69 6.00
7.07 9.69
3.69 6.00
2.09 3.91
F5 30.2 3.91 1.18 2.73
F6 24.6 2.73 0.67 2.06
F7 12.5 2.06 0.26 1.8
2021年8月25日星期三
18
2 咬入能力校核
压下量与咬入角的关系
h D (1 cos ) cos 1 h
No 轧制力能参数校核
Yes 压下规程、速度规程等
最终确定
结束
2021年8月25日星期三
2
压力加工车间设计课程
➢ 初始压下规程设计 ➢ 咬入能力校核 ➢ 速度制度设计 ➢ 轧制温度计算 ➢ 道次变形程度计算 ➢ 道次轧制力和轧制力矩计算
2021年8月25日星期三
3
压力加工车间产线概况
生产工艺流程
SF 2 4 9.69 1 2 0.25
7.07 400
0.13
SF3
3.69 4 6.00
1
1 2 0.25
3.69 400
0.12
SF 4
4
2.09 3.91
1
1 2 0.25
2.09 375
0.11
SF5
4
热轧窄带钢压下规程设计

201224050120河北联合大学轻工学院课程设计题目:12mm热轧窄带钢压下规程设计专业:金属材料工程班级:12轧钢学生姓名:赵凯指导老师:李硕日期:2015年12月3日目录1 任务要求 (3)1.1 任务要求 (3)1.2 原料及产品规格 (3)2 压下规程设计 (3)2.1 产品规格 (3)2.2 设计原则 (3)2.3 粗精轧道次,分配压下量 (4)2.3.1轧制道次的确定 (4)2.3.2 粗轧机组压下量分配 (4)2.3.3 精轧机组的压下量分配 (5)2.4 咬入能力的校核 (6)2.5 计算轧制时间 (6)2.5.1 粗轧速度制度 (6)2.5.2 精轧速度制度 (7)2.5.3 各道轧件速度的计算 (8)2.6 轧制压力的计算 (9)2.6.1 粗轧温度的确定 (9)2.6.2 精轧机组温度确定 (10)2.6.3 粗轧段轧制力计算 (10)2.6.4 精轧段轧制力计算 (13)2.7 轧辊强度校核 (14)2.7.1 支撑辊弯曲强度校核 (15)2.7.2 工作辊的扭转强度校核 (16)3 设计总结 (19)一、设计任务1、任务要求(1)、产品宽度1650mm,厚度12mm(2)、简述压下规程设计原则(3)、选择轧机型式和粗精轧道次,分配压下量(4)、校核咬入能力(5)、计算轧制时间(6)、计算轧制力(7)、校核轧辊强度2、坯料及产品规格依据任务要求典型产品所用原料:坯料:板坯厚度:120mm钢种:Q235最大宽度:300mm长度:7m产品规格:厚度:12mm板凸度:6错误!未找到引用源。
坯料单重:2t二、压下规程设计1、产品宽度300mm,厚度12mm2、设计原则压下规程设计的主要任务就是要确定由一定的板坯轧成所要求的板、带产品的变形制度,亦即要确定所需采用的轧制方法、轧制道次及每道次压下量的大小,在操作上就是要确定各道次辊缝的位置(即辊缝的开度)和转速。
因而,还要涉及到各道次的轧制速度、轧制温度及前后张力制度及道次压下量的合理选择,因而广义地来说,压下规程的制定也应当包括这些内容。
热轧板带钢轧制规程设计PPT课件

考虑轧辊与轧件之间的摩擦和张力等因素,计算轧制力矩,保证轧 制过程的稳定性。
速度制度设计
轧制速度
根据设备能力和生产节奏确定轧制速度,提高生产效率。
卷取速度
与轧制速度相匹配,保证带钢卷取整齐、紧密。
加速和减速
在轧制过程中适当进行加速和减速操作,以调整带钢厚度和板形。
张力制度设计
张力设定
01
热轧板带钢轧制规程设 计ppt课件
目录 CONTENT
• 热轧板带钢轧制概述 • 热轧板带钢轧制设备介绍 • 热轧板带钢轧制工艺参数设计 • 热轧板带钢质量控制与检测 • 热轧板带钢轧制过程自动化技术
应用 • 热轧板带钢轧制规程设计实践案
例分析
01
热轧板带钢轧制概述
热轧板带钢定义与分类
定义
热轧板带钢是指通过高温加热后 ,在轧机上经过多道次连续轧制 而成的具有一定厚度、宽度和长 度的钢板或钢带。
基于轧机刚度、轧辊磨损、热膨胀等因素,建立精确的厚度设定 模型。
厚度自动控制(AGC)
采用测厚仪对带钢实际厚度进行实时测量,通过AGC系统对轧机进 行调整,确保厚度精度。
厚度变化趋势预测
利用历史数据和机器学习算法,对带钢厚度变化趋势进行预测,提 前采取控制措施。
宽度控制方法与策略
1 2
宽度设定模型
预测控制
基于历史数据和当前状态,预测 未来一段时间内热轧板带钢生产 过程的发展趋势,提前采取控制 措施,确保生产过程的稳定性和 产品质量。
智能化技术在热轧板带钢生产中的应用展望
机器学习算法应用
通过机器学习算法对历史数据进行分析和学习,挖掘潜在规律并应用于生产过程优化和质量控制 。
智能感知与决策支持
热轧带钢压下规程设计
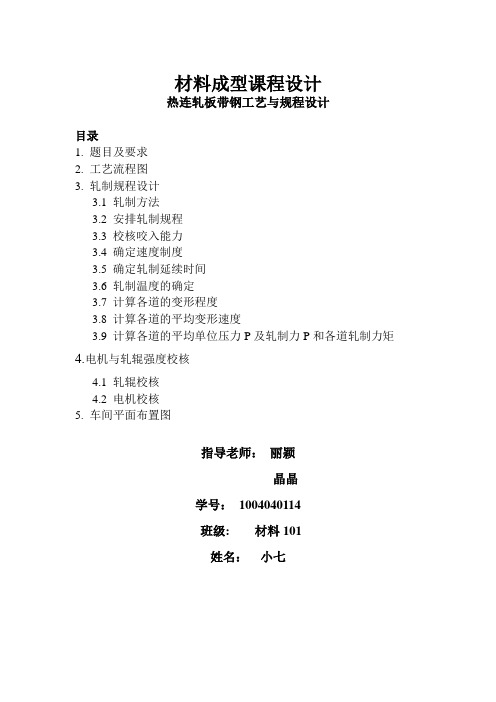
材料成型课程设计热连轧板带钢工艺与规程设计目录1. 题目及要求2. 工艺流程图3. 轧制规程设计3.1 轧制方法3.2 安排轧制规程3.3 校核咬入能力3.4 确定速度制度3.5 确定轧制延续时间3.6 轧制温度的确定3.7 计算各道的变形程度3.8 计算各道的平均变形速度3.9 计算各道的平均单位压力P及轧制力P和各道轧制力矩4.电机与轧辊强度校核4.1 轧辊校核4.2 电机校核5. 车间平面布置图指导老师:丽颖晶晶学号:1004040114班级: 材料101姓名:小七(1)题目及要求1) 设计题目已知原料规格为300×2500×12000mm,钢种为Q345,产品规格为20×3000mm。
2)Q345的产品技术要求(1)碳素结构钢热轧板带产品标准(GB912-89),尺寸、外形、重量及允许偏差应符合 GB-709-88标准钢板长度允许偏差公称厚度钢板长度长度允许偏差>4-16≤2000 +10 >2000-6000 +25 >6000 +30切边钢板宽度允许误差公称厚度宽度宽度允许偏差>4-16 ≤1500 +10>1500 +15(2)牌号、化学成分及机械性能:低合金结构钢1)碳素结构钢热轧板带产品标准(GB912-89)2)力学性能:综合力学性能良好,低温性能亦可,塑性和焊接性良好,用做中低压容器、油罐、车辆、起重机、矿山机械、电站、桥梁等承受动荷的结构、机械零件、建筑结构、一般金属结构件,热轧或正火状态使用,可用于-40℃以下寒冷地区的各种结构。
3)表面质量:表面要缺陷少,需要平整,光洁度要好。
(2)工艺流程图1)工艺流程坯料→加热→除鳞→定宽→粗轧→(热卷取→开卷)→精轧→冷却→剪切→卷取2)绘制工艺简图3)确定轧制设备粗轧机:二辊、四辊轧辊的主要参数的确定(辊身直径D 、辊身长度L )决定板带轧机轧辊尺寸时,应先确定辊身长度L,然后再根据强度、刚度和有关工艺条件确定其直径D。
- 1、下载文档前请自行甄别文档内容的完整性,平台不提供额外的编辑、内容补充、找答案等附加服务。
- 2、"仅部分预览"的文档,不可在线预览部分如存在完整性等问题,可反馈申请退款(可完整预览的文档不适用该条件!)。
- 3、如文档侵犯您的权益,请联系客服反馈,我们会尽快为您处理(人工客服工作时间:9:00-18:30)。
攀枝花学院学生课程设计(论文)题目:6×1700㎜热轧带钢精轧压下规程设计学生姓名:乔红林学号:201111102049 所在院(系):材料工程学院专业:材料成型及控制工程班级: 2011级压力加工班指导教师:肖玄职称:助教2014年10 月13 日攀枝花学院教务处制攀枝花学院本科学生课程设计任务书摘要压下规程设计的主要任务就是要确定由一定的板坯轧成所要求的板、带产品的变形制度,亦即要确定所需采用的轧制方法、轧制道次及每道次压下量的大小,在操作上就是要确定各道次辊缝的位置(即辊缝的开度)和转速。
因而,还要涉及到各道次的轧制速度、轧制温度及前后张力制度及道次压下量的合理选择,从而达到充分发挥设备能力,提高产量和质量,并使操作方便,设备安全的目的。
本课题设计了6×1700㎜热轧带钢精轧压下规程制定。
事实证明影响热轧带钢成品质量的主要因素有坯料缺陷、轧制温度、轧制张力、轧辊磨损及表面粗糙度等,而该课程设计任务就是采用合理压下规格以提高热轧带钢的产量和质量。
关键词压下规程设计,轧制,热轧带钢目录摘要 (IV)1 设计任务 (2)1.1设计任务 (2)1.2坯料及产品规格 (2)2 设计方案 (3)2.1产品规格 (3)2.2设计原则 (3)3 压下规程设计 (4)3.1精轧道次,分配压下量 (4)3.1.1轧制道次的确定 (4)3.1.2精轧机组的压下量分配 (5)3.2咬入能力的校核 (6)3.3计算轧制时间 (6)3.3.1精轧速度制度确定 (6)3.3.2各道轧件速度的计算 (7)3.4轧制压力的计算 (8)3.4.1精轧机组温度确定 (8)3.4.2精轧段轧制力计算 (8)3.5轧辊强度校核 (9)3.5.1支撑辊弯曲强度校核 (9)3.5.2工作辊的扭转强度校核: (11)4 结论 (12)参考文献 (15)1 设计任务1.1设计任务6×1700㎜热轧带钢精轧压下规程制定。
1.2坯料及产品规格依据任务要求典型产品所用原料:坯料:板坯厚度:120mm钢种:Q235最大宽度: 1700mm长度:5m产品规格:厚度:6mm板凸度:7坯料单重:8.07t2 设计方案2.1产品规格产品宽度1700mm, 厚度6mm,凸度7μm。
2.2设计原则压下规程设计的主要任务就是要确定由一定的板坯轧成所要求的板、带产品的变形制度,亦即要确定所需采用的轧制方法、轧制道次及每道次压下量的大小,在操作上就是要确定各道次辊缝的位置(即辊缝的开度)和转速。
因而,还要涉及到各道次的轧制速度、轧制温度及前后张力制度及道次压下量的合理选择,因而广义地来说,压下规程的制定也应当包括这些内容。
通常在板、带生产中制定压下规程的方法和步骤为:1.在咬入条件允许的条件下,按经验配合道次压下量,这包括直接分配各道次绝对压下量或压下率、确定各道次压下量分配率(△h/∑△h)及确定各道次能耗负荷分配比等各种方法;2.制定速度制度,计算轧制时间并确定逐道次轧制温度;3.计算轧制压力、轧制力矩;4.校验轧辊等部件的强度和电机功率;5.按前述制定轧制规程的原则和要求进行必要的修正和改进。
板带轧制规程设计的原则要求是:充分发挥设备能力,提高产量和质量,并使操作方便,设备安全。
3 压下规程设计3.1精轧道次,分配压下量3.1.1轧制道次的确定根据板坯尺寸、轧机架数、轧制速度以及产品厚度等合理确定粗轧机组总变形量及各道次压下量。
由于在粗轧机组上轧制时,轧件温度高、塑性好,厚度大,故应尽量应用此有利条件采用大压下量轧制。
考虑到粗轧机组与精扎机组之间的轧制节奏和负荷上的平衡,粗轧机组变形量一般要占总变形量的60%--80%。
在此,取粗轧的压下率为75%,则粗轧后板坯厚度为30mm ,长度为20000mm 。
由设计要求可知中间板坯厚度为30mm ;成品厚度为6mm ,则精轧轧制的总延伸率为:5630===∑h H μ式中 :∑μ 总延伸率 H 坯料原始厚度 h 产品厚度平均延伸系数取1.26则轧制道次的确定如下726.1log 5log log log ===∑p N μμ(取整)由此得实际的平均延伸系数为:258.157==ps μ由上面计算分配轧制道次,和精轧平均延伸系数如下: 2.精轧为7道次连轧,各道次平均延伸系数 1.26 按μ分配原则我们将精轧的延伸系数如下表3.1.1 精轧的延伸系数3.1.2精轧机组的压下量分配精轧连轧机组分配各架压下量的原则;一般也是利用高温的有利条件,把压下量尽量集中在前几架,在后几架轧机上为了保证板型、厚度精度及表面质量,压下量逐渐减小。
为保证带钢机械性能防止晶粒过度长大,终轧即最后一架压下率不低于10%,此外,压下量分配应尽可能简化精轧机组的调整和使轧制力及轧制功率不超过允许值。
依据以上原则精轧逐架压下量的分配规律是:第一架可以留有余量,即考虑到带坯厚度的可能波动和可能产生咬入困难等,使压下量略小于设备允许的最大压下量,中间几架为了充分利用设备能力,尽可能给以大的压下量轧制;以后各架,随着轧件温度降低、变形抗力增大,应逐渐减小压下量;为控制带钢的板形,厚度精度及性能质量,最后一架的压下量一般在10-15%左右。
精轧机组的总压下量一般占板坯全部压下量的10-25%。
本次设计采用7架连轧,结合设备、操作条件直接分配各架压下量如3.1.3:道次 精轧延伸系数1.28 1.30 1.28 1.26 1.24 1.23 1.22表3.1.2 精轧机组压下量分配及各项参数3.2咬入能力的校核热轧钢板时咬入角一般为15~22°,低速咬入可取20°,由公式其中D 为对应道次轧机工作辊直径。
轧辊的工作辊直径选用400mm ,粗精轧机工作辊相同。
将各道次压下量及轧辊直径代入可得各轧制道次咬入角为:表3.2 粗、精轧各道次咬入角的校核3.3计算轧制时间3.3.1精轧速度制度确定确定精轧速度制度包括:确定末架的穿带速度和最大轧制速度;计算各架速度及调速范围;选择加减速度等。
精轧末架的轧制速度决定着轧机的产量和技术水平。
确定末架轧制速度时,应考虑轧件头尾温差及钢种等,一般薄带钢为保证终轧温度而用高道 次 F1 F2 F3 F4 F5 F6 F7 延伸系数分配 1.281.301.281.261.241.23 1.22 出口厚度(mm ) 23.44 18.03 14.09 11.18 9.02 7.33 6.007 压 下 量(mm ) 6.565.413.942.912.161.691.32压 下 率(%) 21.87 23.08 21.85 20.65 19.32 18.74 18.01 轧件长度(m) 25.60 33.28 42.58 53.67 66.52 81.86 99.83道 次: F1 F2 F3 F4 F5 F6 F7 轧辊直径(mm ) 400 400 400 400 400 400 400 压下量(mm ) 6.56 5.41 3.94 2.91 2.16 1.69 1.32咬入角(°)10.49.48.06.96.05.34.7arccos(1)hDα∆=-的轧制速度;轧制宽度大及钢质硬的带钢时,应采用低的轧制速度。
本设计产品6mm ,终轧速度设定为12m/s 。
末架穿带速度在8m/s 左右,带钢厚度小,其穿带速度可高些。
穿带速度的设定可有以下三种方式:1.当选用表格时,按标准表格进行设定;2.采用数字开关方式时,操作者用设定穿带速度的数字开关进行设定, 此时按键值即为穿带速度;3.其它各架轧制速度的确定:当精轧机末架轧制速度确定后,根据秒流量相等的原则,各架由出口速度确定轧件入口速度。
根据各架轧机出口速度和前滑值求出各架轧辊线速度和转速3.3.2各道轧件速度的计算已预设末架出口速度为12 m/s 由经验向前依次减小以保持微张力轧制依据秒流量相等原则即其中:i v 为各机架出口速度; i h 为各机架出口厚度。
根据以上公式可依次计算得: 各道次精轧速度的确定如表3.3:表3.3 各道次精轧速度的确定道次F1 F2 F3 F4 F5 F6 F7 入口速度(m/s ) 2.40 3.07 3.99 5.11 6.44 7.98 9.87 出口速度(m/s)3.073.99 5.116.447.989.8712.00精轧机组间机架间距为5米,各道次纯轧时间为s v h t HLz 3.877==r i i c v H v h v h==间隙时间分别为t j1=5/3.04=1.63s t j2=5/3.99=1.25st j3=5/5.11=0.98s t j4=5/6.44=0.78s t j5=5/7.98=0.63s t j6=5/9.87=0.51s所以,总轧制时间为s t t tj z 1.14=+=3.4轧制压力的计算3.4.1精轧机组温度确定粗轧完得中间板坯经过一段中间辊道进入热卷取箱,再经过飞剪、除鳞机后,再进入精轧第一架时温度降为1050℃。
由于精轧机组温度降可按下式计算:)(100--=i i h h C t t nn n h h ht t C --=00)( 式中 0t 、0h ——精轧前轧件的温度与厚度n t 、n h ——精轧后轧件的温度与厚度[3]代入数据可得精轧机组轧制温度:根据生产现场经验可以预定终轧温度为800℃,即t n=800℃,计算得: C=62.5,表3.4.1 精轧各道次轧制温度(℃)道次 F1 F2 F3 F4 F5 F6 F7 温度℃9709469178828427947383.4.2精轧段轧制力计算目前普遍公认的最适合于热轧带钢轧制力模型的SIMIS 理论公式:T p LcKK BQ P =式中:P ——轧制力N ; B ——轧件宽度mm ;Qp ——考虑接触弧上摩擦力造成应力状态的影响系数; L c ——考虑压扁后的轧辊与轧件接触弧的水平投影长度mm ; K ——决定金属材料化学成分以及变形的物理条件-变形温度、变形速度及变形程度的金属变形阻力K=1.15s σ;K T ——前后张力对轧制力的影响系数; 由以上公式可知平均单位压力:T p KK Q p =① 计算p Q 时用西姆斯公式的简化公式克林特里公式其中② K T 按下式计算Ka a K fb T ττ)1(1-+-=因为前张力对轧制力的影响较后张力小,所以a>0.5,本设计中取a=0.7,前后张力均取3MPa 。
④接触弧投影长度计算:一般以为接触弧长度水平投影长度为R h Lc ⨯∆=表3.4.2 精轧各道的轧制力道 次 F1 F2 F3 F4 F5 F6 F7轧制力(KN) 56671 55285 50966 46263 44758 42006 409353.5轧辊强度校核3.5.1支撑辊弯曲强度校核四辊轧机的支承辊径D 2与工作辊径D 1之比一般在5.2~5.1范围内。