热轧窄带钢压下规程设计
压下规程
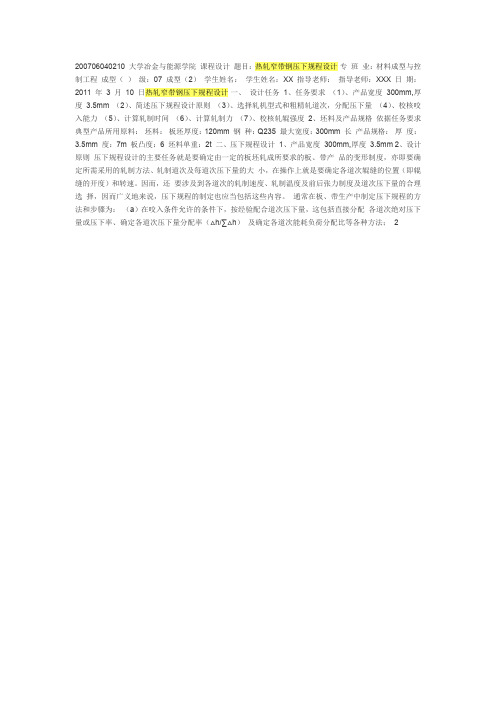
200706040210 大学冶金与能源学院课程设计题目:热轧窄带钢压下规程设计专班业:材料成型与控制工程成型()级:07 成型(2)学生姓名:学生姓名:XX 指导老师:指导老师:XXX 日期:2011 年3 月10 日热轧窄带钢压下规程设计一、设计任务1、任务要求(1)、产品宽度300mm,厚度3.5mm (2)、简述压下规程设计原则(3)、选择轧机型式和粗精轧道次,分配压下量(4)、校核咬入能力(5)、计算轧制时间(6)、计算轧制力(7)、校核轧辊强度2、坯料及产品规格依据任务要求典型产品所用原料:坯料:板坯厚度:120mm 钢种:Q235 最大宽度:300mm 长产品规格:厚度:3.5mm 度:7m 板凸度:6 坯料单重:2t 二、压下规程设计1、产品宽度300mm,厚度 3.5mm 2、设计原则压下规程设计的主要任务就是要确定由一定的板坯轧成所要求的板、带产品的变形制度,亦即要确定所需采用的轧制方法、轧制道次及每道次压下量的大小,在操作上就是要确定各道次辊缝的位置(即辊缝的开度)和转速。
因而,还要涉及到各道次的轧制速度、轧制温度及前后张力制度及道次压下量的合理选择,因而广义地来说,压下规程的制定也应当包括这些内容。
通常在板、带生产中制定压下规程的方法和步骤为:(a)在咬入条件允许的条件下,按经验配合道次压下量,这包括直接分配各道次绝对压下量或压下率、确定各道次压下量分配率(△h/∑△h)及确定各道次能耗负荷分配比等各种方法; 2热轧窄带钢压下规程设计(b)制定速度制度,计算轧制时间并确定逐道次轧制温度;(c)计算轧制压力、轧制力矩;(d)校验轧辊等部件的强度和电机功率;(e)按前述制定轧制规程的原则和要求进行必要的修正和改进。
板带轧制规程设计的原则要求是:充分发挥设备能力,提高产量和质量,并使操作方便,设备安全。
3、粗精轧道次,分配压下量粗精轧道次,3.1、轧制道次的确定有设计要求可知板坯厚度为120mm;成品厚度为 3.5mm,则轧制的总延伸率为:?∑ = 式中H 120 = = 34.28 h 3.5 ? ∑ 总延伸率H 坯料原始厚度h 产品厚度平均延伸系数取 1.36 则轧制道次的确定如下N= log ? ∑ log 34.28 = = 12(取整) log ? p log1.36 ? ps由此得实际的平均延伸系数为:= 12 ? ∑ =1 .3 4 ? ∑ 7 34.28 = =1.3 1.45 ?cp 5 由上面计算分配轧制道次,和粗精轧平均延伸洗漱如下:I :取粗轧 5 道次,平均道次延伸系数为 1.40。
热轧板带钢轧制规程设计

热轧板带钢轧制规程设计一、引言热轧板带钢是一种广泛应用于工业领域的金属材料,其性能的稳定性和质量的优越性对产品的质量和使用寿命至关重要。
因此,热轧板带钢的制造过程需要遵循一定的规程和标准,以确保产品质量的稳定性。
本文将介绍一个热轧板带钢的轧制规程设计。
二、设计目标本轧制规程的设计目标是制定一套科学合理的生产工艺和操作规程,以确保热轧板带钢的质量和性能达到预期要求。
具体的设计目标包括:1.确定合适的轧制温度和轧制速度,以确保给定的产品尺寸和机械性能的要求。
2.设计适当的冷却方式,以确保产品在冷却过程中达到理想的组织结构。
3.确定合适的轧制压力和辊缝尺寸,以确保产品的形状和尺寸的精度。
4.设计适当的轧制工艺和操作规程,以确保生产过程的稳定性和可控性。
5.设计合适的质量检验方法和标准,以确保产品的质量符合要求。
三、设计思路本轧制规程的设计思路是在充分了解产品需求和原材料性能基础上,通过迭代优化的方式确定最佳的轧制工艺和操作规程。
具体的设计思路包括:1.通过分析产品的尺寸要求、力学性能要求和成分要求等,确定轧制温度和轧制速度的范围。
根据产品的板厚和钢种,选择适当的温度和速度条件,以满足产品的性能要求。
2.设计合适的冷却方式,以确保产品在冷却过程中达到理想的组织结构。
根据产品的厚度和形状,选择适当的冷却方式,并确定冷却速度、冷却介质等参数。
3.确定合适的轧制压力和辊缝尺寸,以确保产品的形状和尺寸的精度。
通过分析产品的厚度、宽度和长度要求,选取合适的辊缝尺寸,并确定合适的轧制压力。
4.设计合适的轧制工艺流程和操作规程,以确保生产过程的稳定性和可控性。
根据产品的尺寸和性能要求,确定轧制的工艺流程,并设计详细的操作规程。
5.设计合适的质量检验方法和标准,以确保产品的质量符合要求。
制定合适的质量检验方法和标准,进行产品的质量检验和评价。
四、设计步骤1.分析产品需求和原材料性能,确定轧制温度和轧制速度的范围。
2.设计合适的冷却方式,确定冷却速度和冷却介质。
金属压力加工车间设计之热轧板带钢轧制规程设计(56页)
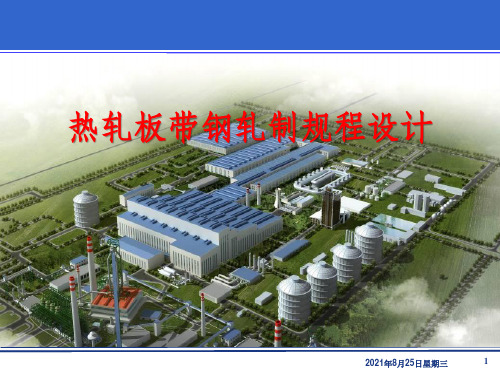
在校核粗轧机咬 入能力时,取机 架最大压下量的 那道次进行,精 轧F1~F3可取 F1较核,F4~ F7可取F4校核.
热轧带钢时,最大咬入角一般为15°~20°,低速轧制时为20°, 所以上述咬入角符合条件,咬入能力满足。
2021年8月25日星期三
19
3 速度制度设计-粗轧速度制度
粗轧为可逆式轧制,一般采用梯形速度图
38.1
34.8
16.76 9.69 6.00
7.07 9.69
3.69 6.00
2.09 3.91
F5 30.2 3.91 1.18 2.73
F6 24.6 2.73 0.67 2.06
F7 12.5 2.06 0.26 1.8
2021年8月25日星期三
18
2 咬入能力校核
压下量与咬入角的关系
h D (1 cos ) cos 1 h
No 轧制力能参数校核
Yes 压下规程、速度规程等
最终确定
结束
2021年8月25日星期三
2
压力加工车间设计课程
➢ 初始压下规程设计 ➢ 咬入能力校核 ➢ 速度制度设计 ➢ 轧制温度计算 ➢ 道次变形程度计算 ➢ 道次轧制力和轧制力矩计算
2021年8月25日星期三
3
压力加工车间产线概况
生产工艺流程
SF 2 4 9.69 1 2 0.25
7.07 400
0.13
SF3
3.69 4 6.00
1
1 2 0.25
3.69 400
0.12
SF 4
4
2.09 3.91
1
1 2 0.25
2.09 375
0.11
SF5
4
热轧带钢轧制规程设计

热轧带钢轧制规程设计摘要钢铁行业是国民经济的支柱产业,而热轧带钢生产是钢铁生产中的主要环节。
热轧带钢工艺的成熟,为冷轧生产提供了优质的原料,大大地满足了国民生产和生活的需要。
本车间参考鞍钢1700ASP生产线,本设计中主要包括六部分,第一部分从热轧带钢机的发展、国外带钢生产先进技术以及我国带钢发展等几个方面阐述了热轧带钢发展情况;第二部分参考了鞍钢ASP1700生产线以及实际设计情况确定了车间的轧钢机械设备及参数;第三部分以典型产品Q235,3.8×1200mm为例从压下规程、轧制速度、轧制温度等方面确定了生产工艺制度;第四部分以典型产品为例进行了轧制力和力矩计算;第五部分根据设备参数和实际制定的生产工艺进行了咬入、轧辊强度的校核;第六部分本次设计总结。
关键词:热轧带钢,轧制工艺制度,轧辊强度目录1综述 (1)1.1引言 (1)1.2 热轧带钢机的发展现状 (1)1.3热轧板带钢生产的工艺流程 (2)1.4 热轧板带钢生产的生产设备 (3)1.5ASP1700热轧板带钢生产的新技术 (3)2 主要设备参数 (4)3 典型产品轧制工艺确定 (6)3.1 生产工艺流程图 (6)3.2 坏料规格尺寸的选定 (7)3.3 轧制工艺制定 (7)3.3.1 加热制度 (7)3.3.2 初轧和精轧各自压下制度 (7)3.3.3 精轧轧制速度 (9)3.3.4 精轧温度制度 (10)4力能参数计算 (10)4.1 精轧各机架轧制力计算 (10)4.2 精轧各机架轧制力矩的计算 (13)5设备强度及能力校核 (13)5.1 精轧机咬入角校核 (13)5.2 轧辊强度校核 (14)5.2.1 辊身弯曲强度校核 (17)5.2.2 辊颈弯曲和扭转强度校核 (19)5.2.3 辊头扭转强度校核 (20)5.2.4接触应力的校核 (20)6结语 (22)参考文献 (23)1 综述1.1引言按照厚度可将板带分为厚板、薄板和极薄带钢三大类,我国将厚度60mm以上的钢板称为特厚板,20mm~60mm的钢板称为厚板,4.0mm~20mm的钢板称为中板,0.2mm~4mm的钢板称为薄板,其中0.2mm~1.2mm又称为超薄板带,小于0.2mm的极薄板带称为箔材。
压下标准规范tWord文档
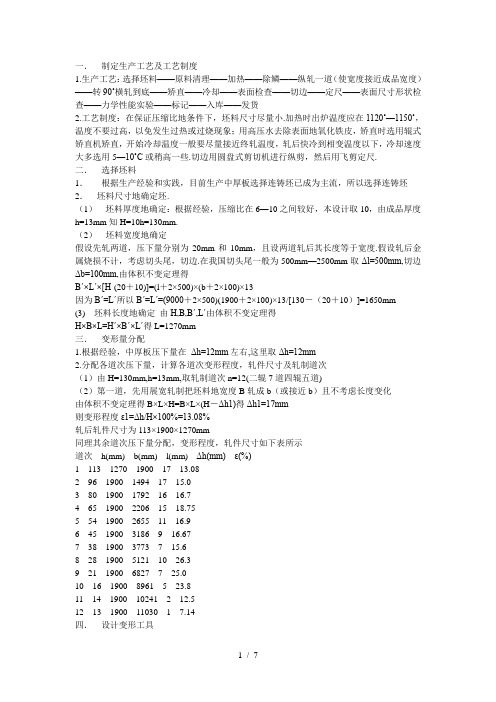
一.制定生产工艺及工艺制度1.生产工艺:选择坯料——原料清理——加热——除鳞——纵轧一道(使宽度接近成品宽度)——转90˚横轧到底——矫直——冷却——表面检查——切边——定尺——表面尺寸形状检查——力学性能实验——标记——入库——发货2.工艺制度:在保证压缩比地条件下,坯料尺寸尽量小.加热时出炉温度应在1120˚—1150˚,温度不要过高,以免发生过热或过烧现象;用高压水去除表面地氧化铁皮,矫直时选用辊式矫直机矫直,开始冷却温度一般要尽量接近终轧温度,轧后快冷到相变温度以下,冷却速度大多选用5—10˚C或稍高一些.切边用圆盘式剪切机进行纵剪,然后用飞剪定尺.二.选择坯料1.根据生产经验和实践,目前生产中厚板选择连铸坯已成为主流,所以选择连铸坯2.坯料尺寸地确定坯.(1)坯料厚度地确定:根据经验,压缩比在6—10之间较好,本设计取10,由成品厚度h=13mm知H=10h=130mm.(2)坯料宽度地确定假设先轧两道,压下量分别为20mm和10mm,且设两道轧后其长度等于宽度.假设轧后金属烧损不计,考虑切头尾,切边.在我国切头尾一般为500mm—2500mm取Δl=500mm,切边Δb=100mm,由体积不变定理得Bˊ×Lˊ×[H-(20+10)]=(l+2×500)×(b+2×100)×13因为Bˊ=Lˊ所以Bˊ=Lˊ=(9000+2×500)(1900+2×100)×13/[130-(20+10)]=1650mm(3) 坯料长度地确定由H,B,Bˊ,Lˊ由体积不变定理得H×B×L=Hˊ×Bˊ×Lˊ得L=1270mm三.变形量分配1.根据经验,中厚板压下量在Δh=12mm左右,这里取Δh=12mm2.分配各道次压下量,计算各道次变形程度,轧件尺寸及轧制道次(1)由H=130mm,h=13mm,取轧制道次n=12(二辊7道四辊五道)(2)第一道,先用展宽轧制把坯料地宽度B轧成b(或接近b)且不考虑长度变化由体积不变定理得B×L×H=B×L×(H-Δh1)得Δh1=17mm则变形程度ε1=Δh/H×100%=13.08%轧后轧件尺寸为113×1900×1270mm同理其余道次压下量分配,变形程度,轧件尺寸如下表所示道次 h(mm) b(mm) l(mm) Δh(mm)ε(%)1 113 1270 1900 17 13.082 96 1900 1494 17 15.03 80 1900 1792 16 16.74 65 1900 2206 15 18.755 54 1900 2655 11 16.96 45 1900 3186 9 16.677 38 1900 3773 7 15.68 28 1900 5121 10 26.39 21 1900 6827 7 25.010 16 1900 8961 5 23.811 14 1900 10241 2 12.512 13 1900 11030 1 7.14四.设计变形工具1. 设计二辊(1)辊身长度L:由L=bmax+a bmax=1900mm 当b=1000-2500mm a=150-200mm 取a=200mm所以L=1900+200=2100mm(2) 辊径尺寸中厚板轧机L/D=2.2-2.8 取L/D=2.6 得D=808mm 取810mm(3) 辊颈尺寸查表3-5 取d/D=0.75(轧钢机械邹家祥主编) 得d=608mm取d=600mm辊颈长度l 取d/l=1 得l=600mm(3)辊头设计因为对于中厚板轧机来说轧辊调整行程比较大,倾角在8˚-12˚间所以应选择万向辊头.(4)各部分地尺寸关系如下(5) Dmin=Dmax-Dmax×重车率中厚板轧机最大重车率5%-8% 取5% Dmin=810-810×5%=767mmD1=Dmin-(5-15mm) 取D1= Dmin-5=762 mmS=(0.25-0.28)D1 取S=0.25D1=197.5 mma=(0.5-0.6) D1 取a=0.5 D1=381 mmb=(0.15-0.2) D1取b=0.2 D1=152mmc=b=152mm(6)辊颈与辊身地过度圆角r由r/D=0.1—0.12 取0.1 得r=0.1×810=81mm2. 设计四辊(1)支撑辊设计1)辊身长度设计和二辊一样L=2100 mm2) 辊径D2 查表3-3 (轧钢机械邹家祥主编)取L/D2=2.0 得D2=1050mm3) 辊颈尺寸取d2/D0.75 d2=1050×0.75=788mm 取d2=800mm4)辊颈长度l2 l2 /d2=1.0 得l2=800mm5) 辊头设计选择万向辊头选择原因同二辊各部分地尺寸关系如下所示Dmin=Dmax-Dmax×重车率中厚板轧机最大重车率5%-8% 取5% Dmin=1050-1050×5%=998D1=Dmin-(5-15mm) 取D1= Dmin-5=993mmS=(0.25-0.28)D1 取S=0.25D1=248 mma=(0.5-0.6) D1 取a=0.5 D1=497 mmb=(0.15-0.2) D1取b=0.2 D1=100mmc=b=100mm6) 辊颈与辊身地过度圆角r2 取r2=0.1D2=105mm(2)工作辊设计1)辊身设计同前L=2100 mm2) 辊径尺寸据经验当轧件较厚时由于要求较大工作辊直径,取D2/D1较小值由表3-3得(轧钢机械邹家祥主编) 取D2/D1=1.5 得D1=700mm3) 辊颈尺寸取d1/D1=0.6 d1=420mm 取l1/d1=1 得l1=420mm4) 辊颈与辊身地过度圆角r1取r1=0.1D1=70mm辊头设计(略)五.计算力能参数1.选择速度图:由于整个轧制过程中,轧件较长,所以选择梯形速度图较理想.2.设计轧制速度(n1 n2 n3 a b)目前,可逆式中厚板轧机粗轧机地轧辊咬入和抛出转速一般在10-20r/min和15-25r/min 范围内选择,精轧机地轧辊咬入和抛出转速一般在20-60r/min和20-30r/min范围内选择. 而且轧制时是低速咬入和抛出.所以在二辊轧机上轧制时,取咬入转速n1=10r/min n2<nH(nH-电机地最大转速)取n2=30 r/min 取n3=20r/min.在四辊轧机上轧制时,取咬入转速n1=20r/min n2<nH(nH-电机地最大转速)取n2=40 r/min 取n3=25r/min.现代化轧机起动加速度a=30-80r/mi ṇ.s,速度b=60-120r/min.s 取a=40r/min.s b=80r/min.s3. 速度图和轧制图表见附图4. 计算每道次各组成时间第1道设等速轧制时间为t3加速轧制时间为t2减速轧制时间为t4,空载加速时间为t1空载减速时间为t5对于二辊轧机等速轧制时间t3=1/n2[60l/ΠD+n²。
热轧板带钢轧制规程设计

表1.3粗轧机组各道相对压下率分配表
机座号或道 1
2
3
4
5
6
次
相对压下率, 15~23 22~30 26~35 27~40 30~50 33~35 %
某热轧生产线,产品规格1.8*1200mm带卷,材质 STE255,轧制规程设计如下
设计目录 安排轧制规程 校核咬入能力 确定速度制度和轧制延续时间
确定轧制温度温度 计算各道次的变形程度
计算各道次轧制力和轧制力矩
1 安排轧制轧制规程
1.1 轧制方法 本次采用综合轧制法,由2架粗轧机组和7架四
辊不可逆式轧机组成的连轧机组共同完成轧制过 程。
C2 :热膨胀系数,C2 =1.105;
B0 :常温下坯宽 ,B0 =1250mm,
ij :立辊压下量分配系数。
表1.6 立辊压下量分配系数表
立辊道次
侧压量分配系
数
0.21 0
0.25 0.24 0.24 0
1.1.6计算立辊各道次侧压量
BE11 =108×0.21=22.7≈23mm BE12 =108×0=0mm BE13 =108×0.24=25.9≈26mm BE21 =108×0.24=25.9≈26mm BE22 =108×0=0mm BE23 =108×0.25=27mm;
轧制规程设计就是根据钢板的技术要求、原 料条件、温度条件和生产设备的实际情况,运用 数学公式或图表进行人工计算或计算机计算,来 确定各道次的实际压下量,空载辊缝,轧制速度 等参数,并在轧制过程中加以修正和应变处理, 达到充分发挥设备潜力,提高产量,保证质量, 操作方便,设备安全的目的。
压下规程制定
压下规程制定实例一
t1=(n2-n1)/a; t3=(n2-n3)/b;
2 2 L / π d + n12 / 2a + n3 / 2b − (a + b)n2 / 2ab / n 2 t2= 60
式中
L——为轧件长度; d——为工作轧辊直径。
压下规程制定实例一
6)轧制温度的确定。为了确定各道的轧制 温度,必须求出逐道的温度降。高温时的 轧件温度降可按辐射散热计算,而且认为 对流和传导所散失的热量大致可以与变形 功所转换的热量相抵消。由于辐射散热所 引起的温降可由下列近似式计算:
压下规程制定实例一
附加摩擦力矩由两部分组成: Mm=Mml+Mm2 Mml 为轧辊轴承中的摩擦力矩,Mm2 为传动机构 中的摩擦力矩。在四辊轧机中 Mml 可近似由下式计算: Mml=Pfdz(Dg/Dz) 式中 f——支承辊轴承的摩擦系,取 f=0.005; dz——支承辊辊颈直径,本例中 dz=1370mm; Dg、Dz——工作辊及支承辊直径。
河北工业职业技术学院 金属材料工程系
压下规程制定应考虑的因素
电机力矩 轧制力 影响因素 板形 产品性能
压下规程制定应考虑的因素
可逆轧机的基本限制条件是轧制电机力矩 限制、轧制力限制、板形和产品性能限制。 在这些限制条件下决定压下规程并计算出 轧机辊缝及轧辊转速的设定值,保证总轧 制时间最少及精轧板形、精轧尺寸合乎目 标值。一般的计算顺序如图所示,分别确 定展宽轧制和长度方向轧制中的压下规程, 根据此压下规程预测轧制力并算出轧机设 定值。
压下规程
驱动电机力矩—速度特性
压下规程
改变各道次轧制力矩和加速力矩的比例求出轧 制力矩的极限值M与道次数N、总轧制时间T的 关系如下图。图中A点是给出最少轧制时间的道 次数和轧制力矩。此轧制力矩若取作全部道次 的平均力矩,则各道的轧制力矩位于固定道次 数N时的曲线上,即A点附近的值(加速力矩所占 份额不同)。这个平均力矩分配给各道次求出压 下量。在实际的轧制规程计算中给出轧制力矩 向各道次分配的模式,乘以他的分配系数ηi。第 i道次的压下量∆hi以下式给出:
设计压下规程
5 典型产品工艺设计5.1 典型产品原料尺寸及成品尺寸Q235船板用钢坯料尺寸(mm ):200×2300×3300 成品尺寸(mm ):30 ×3800×实长 板坯重量(t ): 开轧温度1120℃.。
5.2 轧制道次确定及压下量分配先用立辊轧机轧边一次,再纵向轧制一次,然后转钢90°,横轧到底。
轧制道次n :μlg lg lg 0tF F n -=(5-1)u 取1.3。
计算得n=7.23,取n=8。
最大压下量:)cos 1(α-=∆k D h (5-2) 咬入角α取20°,Δh=67.54mm 。
采用经验分配压下量,在进行校核及修正的设计方法。
压下量分配如下:表5.1压下规程表5 横轧 四辊精轧 42 3800 9511 15 26.36 横轧 四辊精轧 34 3800 11749 8 19.07 横轧 四辊精轧 31 3800 12886 3 8.8 8 横轧四辊精轧3038001331613.25.3 轧制各工艺参数的计算5.3.1 轧制速度制度的确定根据宽厚板的生产经验,为操作方便,粗轧阶段与精轧阶段均采用梯形速度图。
根据经验资料可得,取平均角加速度a=40r/(min ·s),平均角减速度b=60r/(min ·s),由于咬入能力很大,且咬入时速度高更利于轧机轴承油膜的形成,所以采用稳定速度咬入。
第1,2,3道次,n=20r/min 第4,5道次,n=40r/min 第6,7,8道次,n=60r/min 。
抛出速度:n p =20r/min 。
图5.1 梯形速度图5.3.2 确定轧制延续时间在梯形速度图下,每道次轧制延续时间0t t t z +=,其中t 0为间隙时间,t Z 为纯轧时间,21t t t z +=。
设v 1是t 1内的轧制速度,v 2是t 2时间内的平均速度,l 1及l 2为在t 1及t 2时间内轧过的轧件长度,l 为该道次轧后轧件长度,有:mm/s 2.11726020112014.3601=⨯⨯==yDn v π (5-3)mm/s 2.117260112014.3220206022=⨯⨯+=⎪⎪⎭⎫ ⎝⎛+=D n n v py π (5-4) mm/s 06020202=-=-=bn n t py (5-5) 所以减速阶段轧件轧后长度:mm/s 0222=⋅=v t l(5-6)∴121v l l t -= (5-7) 所以:第一道次: s 24.32.11723800111z ===v l t 第二道次:s 69.22.11723154222z ===v l t 第三道次:s v l t 92.32.11724592333z === 对于第4,5道次,y n =40r/min p n =20r/min,有:mm/s 5.23446040112014.3601=⨯⨯==yDn v πmm/s 4.175860112014.3220406022=⨯⨯+=⎪⎪⎭⎫ ⎝⎛+=D n n v py π mm/s 33.06020402=-=-=bn n t py mm/s 2.5804.175833.0222=⨯=⋅=v t l 所以:s v l l 74.25.23442.5807008t 1244-1=-=-=s v l l 81.35.23442.5809511t 1255-1=-=-=第四道次:s t t t z 07.333.074.22414=+=+=-第五道次:s t t t z 14.433.081.32515=+=+=-对于第6,7,8道次,y n =6r/min p n =20r/min,有:mm/s 8.35166060112014.3601=⨯⨯==yDn v πmm/s 5.234460112014.3220606022=⨯⨯+=⎪⎪⎭⎫ ⎝⎛+=D n n v py π mm/s 67.06020602=-=-=bn n t py mm/s 8.15705.234467.0222=⨯=⋅=v t l 所以:s v l l 89.28.35168.157011749t 1266-1=-=-=s v l l 22.38.35168.157012886t 1277-1=-=-=s v l l 34.38.35168.157013316t 1288-1=-=-=第六道次:s t t t z 56.367.089.22616=+=+=- 第七道次:s t t t z 89.367.022.32717=+=+=- 第八道次:s t t t z 01.467.034.32818=+=+=- 间歇时间确定:根据经验资料,在四辊轧机上可逆轧制时。
热轧带钢压下规程设计
4
(1187 .06 273)4
1185 .290C
132.2
1000
故第六道尾部温度为 :
1185.29 12.912.38 4
15.86(1185 .29 273)4
1167.050C
103.1
1000
2)精轧时各道次的温降
带坯在中间辊道上的冷 却时间,等于间隙时间 加精轧第1架的纯轧时间。
3道次。为控制宽展R1前设有立辊E1。第二架为四辊可逆式轧机,板坯在此机架上轧制1~3道次。各轧机采用单独传动。粗轧机组设备主要有粗轧机辊道,侧导板,高压水除鳞装置,定宽压力机,立辊轧机,中间辊道,热卷箱和废品
推出机等组成。
2精轧机组
由7架四辊不可逆式轧机组成连轧机组。各机架采用PC轧机。前三架主要完成压下,后四架主要控制板形。各机架负荷分配亦不同,因此前三台采
精轧第1架的纯轧时间,等于精 轧周期减去尾部通过精轧各架的时间。
轧件尾部通过精轧各架 的时间为:
t0
S0
(1
1
1)6(1
1
1) 8.8s
v1
v2
vn 12.69
3.59
8
故精轧第 架的纯轧时间为:
1
t0
tj
t0
30.1 8.8 21.3s
带坯在中间辊道上的冷 却时间为:
Z
16
23.2
37.3s
轧件经粗轧完后经冷却装置温度降500C,则T0=1167.05-50=1117.050C
1208.4 12.94
(1208.4 273)4
1207.40C
255
1000
故第三道尾部温度为:
毕业设计(论文)-6×1700mm热轧带钢粗轧压下规程制定
攀枝花学院学生课程设计(论文)题目:6×1700mm热轧带钢粗轧压下规程制定学生姓名:学号: 201111102034 所在院(系):材料工程学院专业:材料成型及控制工程班级: 2011级压力加工班指导教师:肖玄职称:助教2014年10 月13 日攀枝花学院教务处制攀枝花学院本科学生课程设计任务书课程设计(论文)指导教师成绩评定表摘要板带钢是钢铁产品的主要产品之一,广泛应用于工业、农业、建筑业以及交通运输业。
热轧板带钢在国名经济发展中起到巨大的推动作用。
热轧板带生产一直是轧制行业中高新技术应用最为集中、人为最为关注的领域。
本次设计的是中板坯连铸连轧生产线的粗轧压下规程。
本次设计介绍了热轧板带钢的粗轧压下规程,主要设备参数,以中板坯连铸连轧生产线来设计选择坏料,制定粗轧压下规程,制定速度制度、温度制度,最后对轧机的咬入角和轧辊的强度进行校核。
关键词:热轧带钢,中板坯连铸连轧,温度制度,速度制度,轧辊强度ABSTRACTPlate band steel is one of the main products of steel products, which is widely used in industry, agriculture, construction and transportation industry. Hot-rolled strip steel plays a huge role in national economic development. Hot-rolled strip production has been being the field of the application of high technology which is the most concentrated and of most concern in the rolling industry. The design of the rolling schedule of rough rolling of slab continuous casting and rolling production line has been made. This design introduces the roughing press rules of hot-rolled strip steel, main equipment parameters, the choices of bad material of slab continuous casting and rolling production line, develops speed system and temperature system, and checks the bite angle of rolling mill and the strength of the roller.Key words hot-rolled strip steel, slab continuous casting and rolling production line, speed system, temperature system, the strength of the roller目录摘要 (I)ABSTRACT (II)1热轧板带钢概述 (1)1.1热轧板带钢概述 (1)1.2热轧板带钢生产的工艺流程 (1)1.3热轧板带钢生产的生产设备 (1)2典型产品轧制工艺制定 (3)2.1压下规程设计 (3)2.1.1坏料尺寸 (3)2.1.2粗轧机组压下量的分配 (3)2.1.3校核咬入能力 (3)2.1.4确定速度制度 (4)2.1.5确定轧制温度 (6)2.1.6轧制压力的计算 (7)2.1.7传动力距的计算 (8)3 轧辊强度校核与电机能力验算 (10)3.1轧辊的强度校核 (10)3.1.1支承辊弯曲强度校核 (10)3.1.2工作辊的扭转强度校核 (12)3.1.3工作辊与支承辊之间的接触应力 (13)3.2电机的校核 (14)3.2.1 静负荷图 (14)3.2.2主电动机的功率计算 (15)4结束语 (17)参考文献 (18)1 热轧板带钢概述1.1热轧板带钢概述国名经济建设与发展中的大量使用的金属材料中钢铁材料占很大比例,例如2005年世界钢产量约为11亿吨。
- 1、下载文档前请自行甄别文档内容的完整性,平台不提供额外的编辑、内容补充、找答案等附加服务。
- 2、"仅部分预览"的文档,不可在线预览部分如存在完整性等问题,可反馈申请退款(可完整预览的文档不适用该条件!)。
- 3、如文档侵犯您的权益,请联系客服反馈,我们会尽快为您处理(人工客服工作时间:9:00-18:30)。
201224050120河北联合大学轻工学院课程设计题目:12mm热轧窄带钢压下规程设计专业:金属材料工程班级:12轧钢学生姓名:赵凯指导老师:李硕日期:2015年12月3日目录1 任务要求 (3)1.1 任务要求 (3)1.2 原料及产品规格 (3)2 压下规程设计 (3)2.1 产品规格 (3)2.2 设计原则 (3)2.3 粗精轧道次,分配压下量 (4)2.3.1轧制道次的确定 (4)2.3.2 粗轧机组压下量分配 (4)2.3.3 精轧机组的压下量分配 (5)2.4 咬入能力的校核 (6)2.5 计算轧制时间 (6)2.5.1 粗轧速度制度 (6)2.5.2 精轧速度制度 (7)2.5.3 各道轧件速度的计算 (8)2.6 轧制压力的计算 (9)2.6.1 粗轧温度的确定 (9)2.6.2 精轧机组温度确定 (10)2.6.3 粗轧段轧制力计算 (10)2.6.4 精轧段轧制力计算 (13)2.7 轧辊强度校核 (14)2.7.1 支撑辊弯曲强度校核 (15)2.7.2 工作辊的扭转强度校核 (16)3 设计总结 (19)一、设计任务1、任务要求(1)、产品宽度1650mm,厚度12mm(2)、简述压下规程设计原则(3)、选择轧机型式和粗精轧道次,分配压下量(4)、校核咬入能力(5)、计算轧制时间(6)、计算轧制力(7)、校核轧辊强度2、坯料及产品规格依据任务要求典型产品所用原料:坯料:板坯厚度:120mm钢种:Q235最大宽度:300mm长度:7m产品规格:厚度:12mm板凸度:6错误!未找到引用源。
坯料单重:2t二、压下规程设计1、产品宽度300mm,厚度12mm2、设计原则压下规程设计的主要任务就是要确定由一定的板坯轧成所要求的板、带产品的变形制度,亦即要确定所需采用的轧制方法、轧制道次及每道次压下量的大小,在操作上就是要确定各道次辊缝的位置(即辊缝的开度)和转速。
因而,还要涉及到各道次的轧制速度、轧制温度及前后张力制度及道次压下量的合理选择,因而广义地来说,压下规程的制定也应当包括这些内容。
通常在板、带生产中制定压下规程的方法和步骤为:(a )在咬入条件允许的条件下,按经验配合道次压下量,这包括直接分配各道次绝对压下量或压下率、确定各道次压下量分配率(△h/∑△h )及确定各道次能耗负荷分配比等各种方法;(b )制定速度制度,计算轧制时间并确定逐道次轧制温度; (c )计算轧制压力、轧制力矩;(d )校验轧辊等部件的强度和电机功率;(e )按前述制定轧制规程的原则和要求进行必要的修正和改进。
板带轧制规程设计的原则要求是:充分发挥设备能力,提高产量和质量,并使操作方便,设备安全。
3、粗精轧道次,分配压下量 3.1、轧制道次的确定有设计要求可知板坯厚度为120mm ;成品厚度为12mm ,则轧制的总延伸率为:式中 ∑μ 总延伸率 H 坯料原始厚度 h 产品厚度平均延伸系数取1.36则轧制道次的确定如下由此得实际的平均延伸系数为:由上面计算分配轧制道次,和粗精轧平均延伸洗漱如下: I : 取粗轧5道次,平均道次延伸系数为1.40。
II :精轧为7道次连轧,各道次平均延伸系数为按μ分配原则我们将粗、精轧的延伸系数如下:3.2、粗轧机组压下量分配根据板坯尺寸、轧机架数、轧制速度以及产品厚度等合理确定粗轧机组总变形量及各道次压下量。
其基本原则是:12034.283.5H h μ∑===log log34.2812()log log1.36p N μμ∑===取整s = 1.34p μj p μ(1)、由于在粗轧机组上轧制时,轧件温度高、塑性好,厚度大,故应尽量应用此有利条件采用大压下量轧制。
考虑到粗轧机组与精扎机组之间的轧制节奏和负荷上的平衡,粗轧机组变形量一般要占总变形量的60%--80%(2)、提高粗轧机组轧出的带坯温度。
一方面可以提高开轧温度,另一方面增大压下可能减少粗轧道次,同时提高粗轧速度,以缩短延续时间,减少轧件的温降。
(3)、考虑板型尽量按照比例分配凸度,在粗轧阶段,轧制力逐渐较小使凸度绝对值渐少。
但是,第一道考虑厚度波动,压下量略小,第二道绝对值压下最大,但压下率不会太高。
本设计粗轧采用四分之三式,轧机配置为四架,粗轧制度为:第一架轧机为二辊不可逆,轧制一道次;第二架轧机为四辊可逆,轧制三道次;第三架轧机为四辊不可逆,轧制一道次(预留一架)。
由此计算粗轧压下量分配数据如下表:3.3、精轧机组的压下量分配精轧连轧机组分配各架压下量的原则;一般也是利用高温的有利条件,把压下量尽量集中在前几架,在后几架轧机上为了保证板型、厚度精度及表面质量,压下量逐渐减小。
为保证带钢机械性能防止晶粒过度长大,终轧即最后一架压下率不低于10%,此外,压下量分配应尽可能简化精轧机组的调整和使轧制力及轧制功率不超过允许值。
依据以上原则精轧逐架压下量的分配规律是:第一架可以留有余量,即考虑到带坯厚度的可能波动和可能产生咬入困难等,使压下量略小于设备允许的最大压下量,中间几架为了充分利用设备能力,尽可能给以大的压下量轧制;以后各架,随着轧件温度降低、变形抗力增大,应逐渐减小压下量;为控制带钢的板形,厚度精度及性能质量,最后一架的压下量一般在10-15%左右。
精轧机组的总压下量一般占板坯全部压下量的10-25%。
本次设计采用7架连轧,结合设备、操作条件直接分配各架压下量如下:精轧机组压下量分配及各项参数如表(2)所示:4、咬入能力的校核热轧钢板时咬入角一般为15~22°,低速咬入可取20°,由公式其中D 为对应道次轧机工作辊直径。
轧辊的工作辊直径选用400mm ,粗精轧机工作辊相同。
将各道次压下量及轧辊直径代入可得各轧制道次咬入角为:粗、精轧各道次咬入角的校核5、计算轧制时间(1)粗轧速度制度粗轧为保证咬入,采用升速轧制。
根据经验资料,取平均加速度a=40rpm/s ,平均减速度b=60rpm/s 。
由于咬入能力很富裕故可采用稳定高速咬入,考虑到粗轧生产能力与精轧生产能力得匹配问题,确定粗轧速度如下:咬入速度为n 1=50rpm ,抛出速度为n 2=20rpm 。
粗轧各道次的轧制转速均可设置为n 1=50rpm ,则粗轧的稳定轧制速度为:道 次 F1 F2 F3 F4 F5 F6 F7 延伸系数分配1.321.35 1.32 1.30 1.28 1.27 1.26 出口厚度(mm ) 16.58 12.29 9.31 7.16 5.60 4.41 120 压 下 量(mm ) 5.82 4.29 2.98 2.15 1.56 1.19 0.91 压 下 率(%) 26.0 25.924.223.121.821.320.6轧件长度(m)50.66 68.35 90.23 117.32 150.00 190.48 240.00道 次:R1R2 R3R4R5F1F2F3F4F5F6F7轧辊直径(mm ) 400 400400 400 400 400 400 400 400 400 400 400压下量(mm ) 34.3 25.3 18.7 11.5 7.8 5.82 4.29 2.98 2.15 1.56 1.19 0.91咬入角(°)21222.5 19.3 15.2 12.4 10.5 9.2 7.5 6.4 5.4 4.6 4.2arccos(1)hDα∆=-因此,对于各架粗轧机减速用时:s b n n t 5.0605020122=--=-= 稳定轧制时间:间隙时间:s Dn lt j 5.3601==π t=0.5*5+9.33+13.34+19.18+26.50+35.71+12=110.06s(2)精轧速度制度确定确定精轧速度制度包括:确定末架的穿带速度和最大轧制速度;计算各架速度及调速范围;选择加减速度等。
精轧末架的轧制速度决定着轧机的产量和技术水平。
确定末架轧制速度时,应考虑轧件头尾温差及钢种等,一般薄带钢为保证终轧温度而用高的轧制速度;轧制宽度大及钢质硬的带钢时,应采用低的轧制速度。
本设计典型产品12mm ,终轧速度设定为12m/s 。
末架穿带速度在8m/s 左右,带钢厚度小,其穿带速度可高些。
穿带速度的设定可有以下三种方式:I 、当选用表格时,按标准表格进行设定;II 、采用数字开关方式时,操作者用设定穿带速度的数字开关进行设定,此时按键值即为穿带速度;III 、其它各架轧制速度的确定:当精轧机末架轧制速度确定后,根据秒流量相等的原则,各架由出口速度确定轧件入口速度。
根据各架轧机出口速度和前滑值求出各架轧辊线速度和转速。
(3)各道轧件速度的计算:12345 3.14500.41.05/6060nD v v v v v m sπ⨯⨯=======()Ri i wRi il l t v -=已预设末架出口速度为12 m/s 由经验向前依次减小以保持微张力轧制依据秒流量相等原则即其中i v 为各机架出口速度;i h 为各机架出口厚度。
根据以上公式可依次计算得:各道次精轧速度的确定道次F1 F2 F3 F4 F5 F6 F7 入口速度(m/s ) 1.9 2.5 3.4 4.5 5.9 7.5 9.5 出口速度(m/s) 2.53.44.55.97.59.512.0精轧阶段加速前纯轧时间:s v DN s t j s 3.137=+=π式中 j s ——精轧机组末架至卷曲机间距,取100m D ——卷取机卷筒直径 N ——参数,取57v ——第七架穿带速度,取8s m /精轧机组间机架间距为6米,各道次纯轧时间为t X =300×12/12/12=85.7s间隙时间分别为t j1=6/2.5=2.4s ;t j2=6/3.4=1.76s ;t j3=6/4.5=1.5s ;tj4=6/5.9=102s ;t j5=6/7.5=0.8s ; t j6=6/9.5=0.63s; t j7=6/12=0.5s 则精轧总延续时间s t t t t j x s 61.07161.87.8513.3=++=++=∑。
r i i c v H vh v h==6、轧制压力的计算(1)粗轧温度确定为了确定各道次轧制温度,必须求出逐道次的温度降。
高温轧制时轧件温度降可以按辐射散热计算,计算原则为:对流和传导所散失的热量可大致与变形功所转化的热量相抵消。
由于辐射散热所引起的温度降在热轧板带时可按下式计算:41)1000(9.12T h Z t =∆ 有时为简化计算,也可采用以下经验公式1116400h Z t t ⨯-=∆其中 1t 、1h ——分别为前一道轧制温度(℃)与轧轧出厚度,mm ;Z ——辐射时间即该道次轧制延续时间t j Z=t j ;T 1——前一道的绝对温度 ,K ; h ——前一道的轧出厚度。