陶瓷成型技术
陶瓷挤出成型工艺
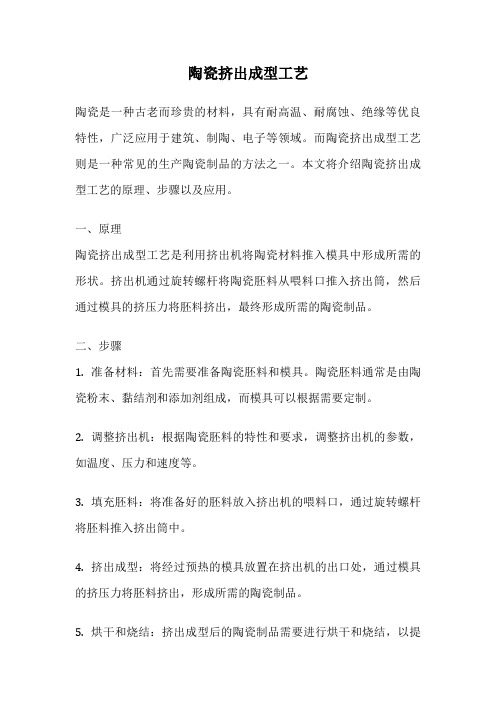
陶瓷挤出成型工艺陶瓷是一种古老而珍贵的材料,具有耐高温、耐腐蚀、绝缘等优良特性,广泛应用于建筑、制陶、电子等领域。
而陶瓷挤出成型工艺则是一种常见的生产陶瓷制品的方法之一。
本文将介绍陶瓷挤出成型工艺的原理、步骤以及应用。
一、原理陶瓷挤出成型工艺是利用挤出机将陶瓷材料推入模具中形成所需的形状。
挤出机通过旋转螺杆将陶瓷胚料从喂料口推入挤出筒,然后通过模具的挤压力将胚料挤出,最终形成所需的陶瓷制品。
二、步骤1. 准备材料:首先需要准备陶瓷胚料和模具。
陶瓷胚料通常是由陶瓷粉末、黏结剂和添加剂组成,而模具可以根据需要定制。
2. 调整挤出机:根据陶瓷胚料的特性和要求,调整挤出机的参数,如温度、压力和速度等。
3. 填充胚料:将准备好的胚料放入挤出机的喂料口,通过旋转螺杆将胚料推入挤出筒中。
4. 挤出成型:将经过预热的模具放置在挤出机的出口处,通过模具的挤压力将胚料挤出,形成所需的陶瓷制品。
5. 烘干和烧结:挤出成型后的陶瓷制品需要进行烘干和烧结,以提高其强度和稳定性。
6. 后处理:经过烧结后的陶瓷制品可能需要进行修整、抛光等后处理工序,以达到更好的外观和质量。
三、应用陶瓷挤出成型工艺在建筑、制陶、电子等领域有着广泛的应用。
1. 建筑领域:陶瓷挤出成型工艺可以用于制作陶瓷砖、陶瓷管道等建筑材料。
由于陶瓷具有耐高温、耐腐蚀等特性,因此在建筑领域中有着重要的应用。
2. 制陶领域:陶瓷挤出成型工艺可以用于制作陶瓷器具、陶瓷艺术品等。
通过挤出成型工艺,可以制作出各种形状独特的陶瓷制品。
3. 电子领域:陶瓷挤出成型工艺可以用于制作陶瓷电子元件、陶瓷基板等。
陶瓷具有绝缘性能,可以在电子领域中起到重要的作用。
总结:陶瓷挤出成型工艺是一种常见的生产陶瓷制品的方法,通过挤出机将陶瓷胚料挤出成所需的形状。
该工艺具有简单、高效、成本低等优点,并在建筑、制陶、电子等领域有着广泛的应用。
随着科技的不断进步,陶瓷挤出成型工艺将会得到进一步的优化和发展,为各个领域提供更多更好的陶瓷制品。
陶瓷材料的成型方法(一)

陶瓷材料的成型方法(一)陶瓷材料已经成为我们生活中一个智能更要的工具了,在现代陶瓷材料的生产中,常用的成型方法有挤制成型、干压成型、热压铸成型、注浆成型、轧膜成型、等静压成型、热压成型和流延成型等。
1.挤制成型挤制成型主要用于制造片形、棒形和管形制品,如电阻的基体蜂窝陶瓷载体的陶瓷棒、陶瓷管等陶瓷制品。
该成型方法生产效率高,产量大、操作简便,使用的挤压机分卧式和立式两种。
配料中新土含量较大时,成型的坯料一般不加黏合剂,配料经过真空练泥、闲料后即可用于挤制成型。
坯料中一般含水量为16%一25%。
配料中含茹土少或不含教土时,将均匀混合了熟合剂的粉料经真空练泥和闲料后,再用于挤制成型。
挤制成型的氧化铝瓷球常用的教合剂有糊精、桐油、甲基纤维素(MC)、羧印基纤维素、泽丙基甲基纤维素(HPMC)和亚硫酸纸浆废液等。
挤制资管时应注意防止坯体变形,管的外径越大,壁越薄,机械强度越差,越容易变形。
2.干压成型干压成型是最常用的成型方法之一,适用于成型简单的瓷件,如圆片形等,对模具质量的要求较高。
该方法少产效率高,易于自动化,制品烧成收缩率小,不易变形。
干压成型方法所用坯料的含水量一般控制在4%一8%左右。
干压常用熟合剂主要有聚乙烯醇(PVA)水溶液、石蜡、亚硫酸纸浆废液等。
通常配料中黏合剂的加入量为:聚乙烯醇水溶液3%一8%、石蜡8%左右、亚硫酸纸浆废液10%左右。
干压成型是利用模具在泊压机上进行的。
干压成型的加压方式有单面加压和双面加压两种。
直接受压一端的压力大,坯体密度大;远离加压一端的压力小,密度小。
金属填料的双面加压时坯体两端直接受压,两端密度大,中间密度小。
造粒料并加润滑剂时,双面加压的尔意图,坯体密度非常均匀。
成型压力的大小直接影响资体的密度和收缩率。
如某BaTiO3系资料,外加5%聚乙烯醇水溶液造粒,在相同烧成条件下,成型压力为0.5MPa时,收缩系数为1.15—1.16;成型乐力为0.6MPa时,收缩系数为1.13—1.14;成型压力为0.7MPa时,收缩系数为1.11-1.12;成型压力为0.8MPa时,收缩系数为1.03。
陶瓷成型方法

陶瓷成型方法
1. 手工成型:传统的陶瓷制作方法,艺术性强,表现力丰富,但制作速度慢,效率低。
2. 模具成型:通过将陶瓷原料压入模具中,辅以压力使其成型,效率高,但制作过程中难以控制细节。
3. 电子成型:利用专门的CAD系统将设计图转换为数字信号,再通过特殊设备将陶瓷原料成型,制作速度快,精度高,但设备价格昂贵。
4. 注射成型:利用氧化铝陶瓷高压注射机将陶瓷原料注入特定模具中成型,制造精度高,成型时间短,但需要较高的生产能力。
5. 吸塑成型:将陶瓷粉末与塑料混合后进行吸塑,成型速度快,成本较低,适合大批量生产,但制作出的产品密度、耐蚀性等性能差距较大。
古代瓷器的6种成型方法

1、手工捏塑法人们用手随心所欲地对泥土进行创作,捏出一些较小的器物,这是最原始最简单的成型方法。
2、泥条盘筑法将泥土搓成泥条,从器底起从下往上将泥条盘筑成器壁直至器口,再用泥浆胶合成全器,最后抹平器壁盘筑时留下的泥缝。
此法出现在新石器时代中期。
3、泥片围接法将原料泥块先加工成泥片,然后将泥片围接组合成需要的形状,如宜兴紫砂茶壶多用此法做成。
4、轮制成型法将泥料放置于轮盘,利用轮盘转动产生的离心力而成型的方法。
它主要用于圆体器型的制作,轮制有慢轮、快轮之分。
5、印模法将泥料嵌入特制的模子中成型的方法。
主要用于制作陶瓷俑、动物和器物部件、纹饰等。
6、注浆法把泥料灌入石膏等模子中,利用石膏模型的毛细管作用力将悬浮的浆料吸附于模具内壁而成型的方法。
注浆法大大提高了胎体的产量和质量,有利于陶瓷生产的发展。
怎样挑选瓷器方法一:一、购买陶瓷餐具一定要选择正规的市场和店面,切不可贪便宜购买没有正式生产厂家的劣质产品。
国家规定,将陶瓷餐具置于4%的醋酸中浸泡,铅的溶出量不得大于7毫克/升,镉的溶出量不得大于0.5毫克/升。
二、购买时要注意看餐具的成色,用手触摸餐具表面,看内壁是否光洁;三、闻闻是否有异味;四、不要购买颜色过于鲜艳的陶瓷餐具。
通常颜色越鲜艳的餐具,重金属就越容易超标;五、应购买原料、工艺控制比较严格的釉中彩、釉下彩餐具;六、餐具使用前用沸水煮5分钟或用食醋浸泡2—3分钟,以溶解方法二:1、看色泽这里说的看色泽主要是看骨瓷的不覆盖花面的胎体部分的色泽,真正骨炭含量高的优质骨瓷,其色泽应该是乳白色或者称为奶白色。
骨瓷不是越白越好,自然的乳白色才是好的骨瓷。
2、听声音听声音有两种方法,第一种就是把瓷器碗托在一只手的手心中(注意:一定不要抓在手心中),另一只手弹下骨瓷的碗口边缘处,好的骨瓷声音清越如钟声一样有清脆的回音,响声越长久说明胎体更圆滑,瓷的品质更好。
第二种就是注入碗中三分之一左右的水,一只手沾些水沿着碗边转会发出“唧唧”的共鸣声,碗越大效果越明显。
陶瓷的三大成型方法

陶瓷的三大成型方法
陶瓷是一种古老的工艺品,制作陶瓷的方法也有很多种。
在这里,我们将介绍陶瓷的三大成型方法:手工制作、轮盘制作和压制制作。
手工制作是最传统的制作陶瓷的方法之一。
这种方法需要使用手工工具,如刀子、刮刀和模具等,将陶泥塑成所需要的形状。
手工制作需要一定的技巧和经验,但可以制作出非常独特和精美的陶瓷作品。
轮盘制作是一种使用陶瓷轮盘的制作方法。
这种方法需要将陶泥放在轮盘上,然后利用手的力量使轮盘旋转。
在旋转的同时,使用手工工具将陶泥塑成所需要的形状。
这种方法可以制作出形状规整、大小一致的陶瓷作品。
压制制作是一种使用陶瓷模具的制作方法。
这种方法需要将陶泥放在模具内部,然后使用手的力量将陶泥压实。
在陶泥变硬之后,将陶瓷从模具中取出。
这种方法可以制作出形状相同、大小一致的陶瓷作品。
除了这三种成型方法外,还有其他的制作方法,如注模制作、挤出成型等。
每种方法都有其独特的优点和缺点,可以根据需要选择适合自己的制作方法。
无论使用哪种制作方法,制作陶瓷都需要注意以下几点:
1. 选择好的陶泥。
陶泥质地、水分含量等因素都会影响成型效果。
2. 考虑好陶瓷的用途。
不同用途的陶瓷需要不同的形状、大小和材质等。
3. 注意细节。
陶瓷的细节处理非常重要,如刻线、打磨等。
4. 控制好温度和湿度。
陶瓷制作需要一定的温度和湿度,需要注意控制好这些因素。
总的来说,陶瓷制作需要一定的技巧和经验,但是也需要耐心和细心。
只有这样,才能制作出精美的陶瓷作品。
陶瓷注射成型技术
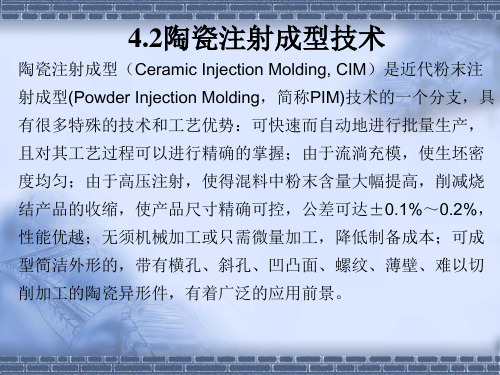
▪ 练泥时间:时间过短则练泥混合效果不好,时间过长则练泥混合效率不高
1) 粉末应专门配制,以求高的极限填充密度和低的成本; 2) 2) 粉末不结块团聚; 3) 3) 粉末外形主要为球形; 4) 4) 粉末间有足够的摩擦力以避开粘结剂脱出后坯件变
形或塌陷,在大多数情况下,自然坡度角应大于55°; 5) 5) 为利于快速烧结,应具有小的平均粒度,一般要
求小于1μm; 6) 6) 粉末本身致密,无内孔隙; 7) 7) 粉末的表面清洁,不会与粘结剂发生化学反应。
立式注射成型机
注射成型机构组成
▪ 可塑化机构(注射机构) ▪ 合模机构(包括模具) ▪ 油压机构 ▪ 电气掌握机构
注射成型模具
注射成型制备氧化锆坯体
注射成型制备氧化锆坯体
注射成型过程中缺陷的掌握
▪ 在注射成型过程中缺陷的掌握基本可从两个方面考 虑:一方面是成型温度、压力和时间三者关系设定; 另一方面是填充时喂料在模腔中的流淌。由于CIM 产品大多数是外形简洁、精度要求高的小尺寸零件, 混料在模腔的流淌就牵涉到模具设计问题,包括进 料口位置、流道的长度、排气孔的位置等,都需对 混料流淌性质、模腔内温度和残余应力分布等参数 有清楚了解。现行计算机充模过程动态模拟,正为 注射成型这一步供应理论指导。
孔洞缺陷
▪ 孔洞,指在生坯的横截面上可以发现的孔隙。 有的是一个近圆形的小孔,有的就进展为几 乎贯穿生坯坯体的中心通孔,这是常见的缺 陷.
陶瓷成型技术
项目1:注浆成型技术
一、注浆成型 传统的定义:在石膏模的毛细管力作用下,含有一 定水分的粘土泥浆脱水硬化、成型的过程。 目前:将所有基于坯料具有一定液态流动性的成型 方法统归为注浆成型。 工艺特点: (1)适于成型各种产品,形状复杂、不规则、薄、 体积较大而且尺寸要求不严的器物,如花瓶、汤碗、 椭圆形盘、茶壶等。 (2)坯体结构均匀,但含水量大且不均匀,干燥 与烧成收缩大。
防止粉化的方法有: ①适当降低模型的干燥速度,使水分能够从模型四 周均匀地蒸发; ②采取提前合模的办法,夜间让模型整体干燥,因 模型湿不宜提前合模的,可在芯子上部盖塑料布, 以防止大量的水分从顶点蒸发; ③待模型的外吃浆面刮去一层,增加透气性,使水 分向外吃浆面蒸发。
5、延长石膏模型的使用寿命 1)石膏模型有一定的使用寿命,一般可塑成型用 模型的使用寿命约100-250次,注浆成型用模型只 有50-150次。其损坏原因主要有以下三方面:其 一是模型本身强度不高,易被碰裂或压裂;其二是 模型工作面被坯料中泥粒磨损而报废;其三是注桨 用模型由于模型与坯料桨中电解质起休化学反应造 成模型的毛细孔中与表面上产生硫酸钠析晶,而降 低吸水能力。
石膏模的寿命不但取决于合理的使用,还与制模的 石膏质量和操作工艺过程有关。如石膏粉炒温度过 高或过低,石膏粉颗粒粗大,浇注时加水过多,混 合不均匀,制备好的石膏粉放在潮湿的地方等情况 均会影响模型使用寿命。 2)为了延长石膏模的使用寿命,应正确掌握制造 模型的工艺操作和合理使用外,还可从提高石膏模 的机械强度入手。
各类产品尽管加工方法不同,但是坯体修整是必要 的,不可忽视的,否则就不能保证瓷器半成品质量。 在修坯中也要防止坯体产生缺陷,并修整那些能修 整的带缺陷的坯体。 修坯分为干修和湿修两种方式。 湿修:坯体的水分16~19%。 干修:坯体的水分 < 2%。
陶瓷的三大成型方法
陶瓷的三大成型方法
陶瓷是一种广泛应用于生活中的材料,它具有高温耐性、耐腐蚀、不易变形等优点,因此被广泛应用于制作餐具、装饰品、建筑材料等领域。
而陶瓷的成型方法也是制作陶瓷制品的重要环节之一,下面将介绍陶瓷的三大成型方法。
一、手工成型法
手工成型法是最古老的陶瓷成型方法之一,它是指通过手工将陶土塑造成所需的形状。
手工成型法的优点是成本低、制作过程简单,可以制作出各种形状的陶瓷制品。
但是,手工成型法的缺点也很明显,制作效率低、成品质量难以保证,因此在现代工业生产中很少采用手工成型法。
二、模压成型法
模压成型法是一种常见的陶瓷成型方法,它是指将陶土放入模具中,通过压力将陶土压制成所需的形状。
模压成型法的优点是制作效率高、成品质量稳定,可以大规模生产各种形状的陶瓷制品。
但是,模压成型法的缺点也很明显,模具制作成本高、制作过程复杂,需要专业的设备和技术支持。
三、注塑成型法
注塑成型法是一种新型的陶瓷成型方法,它是指将陶土放入注塑机
中,通过高压注塑将陶土注入模具中,形成所需的形状。
注塑成型法的优点是制作效率高、成品质量稳定,可以大规模生产各种形状的陶瓷制品。
同时,注塑成型法还可以制作出更加复杂的形状,如空心陶瓷制品。
但是,注塑成型法的缺点也很明显,设备成本高、制作过程复杂,需要专业的技术支持。
手工成型法、模压成型法和注塑成型法是陶瓷的三大成型方法。
每种成型方法都有其优点和缺点,应根据具体情况选择合适的成型方法。
随着科技的不断发展,陶瓷的成型方法也在不断创新,未来陶瓷制品的制作将更加高效、精准和多样化。
陶瓷成型方法
2、热压铸成型工艺
3、热压铸成型工艺 主要工艺参数:
(1) 腊浆温度:60~75℃,温度升 高,则腊浆的粘度下降,坯体致 密,但冷却收缩相应大。温度过 低,则易出现欠注、皱纹等缺陷。 (2) 钢模温度。决定坯体冷却凝固 的速度。一般为20~30℃。 (3) 成型压力:与浆桶深度、料浆 性能有关。压力升高,坯体的致 密度增加,坯体的收缩程度下降。 一般可以采用0.3~0.5 MPa。
3、强化注浆成型方法
(注浆方法的改进)
在注浆过程中人为地施加外力,加速注浆过程的进行,使吸浆 速度和坯体强度得到明显改善的方法。 1) 真空注浆 模具外抽真空,或模具在负压下成型,造成模具内外压力差, 提高成型能力,减小坯体的气孔和针眼。
2)
离心注浆
使模型在旋转情况下进浆,料浆在离心力的作用下紧靠 模壁形成致密的坯体。气泡较轻,易集中在中间最后破 裂排出,故可提高吸浆速度与制品质量。要求:泥浆中 的颗粒分布范围窄,否则大颗粒集中在靠近模型的坯体 表面,而小颗粒集中在坯体内面,造成坯体组织不均匀, 收缩不一致。
2. 滚压成型的主要控制因素 (1) 对泥料的要求:水分低、可塑性好。成型时模具 既有滚动,又有滑动,泥料主要受压延力的作用。要求有 一定的可塑性和较大的延伸量。可塑性低,易开裂;可塑 性高,水分多易粘滚头。阳模滚压和阴模滚压对泥料的要 求有差别。阴模滚压受模型的承托和限制,可塑性可以稍 低,水分可稍多。 (2) 滚压过程控制:分压下(轻)、压延(稳)、抬起 (慢)阶段。 (3) 主轴转速(n1)和滚头转速(n2) :控制生产效率; 对坯料的施力形式,控制坯体的密度均匀和表面光洁。 滚压头的温度热滚压:100~130℃,在泥料表面产生一 层气膜,防止粘滚头,坯体表面光滑。冷滚压:可用塑料 滚压头,如聚四氟乙烯。
陶瓷材料成型方法
陶瓷材料成型方法
陶瓷材料的成型方法有多种,以下是三种主要的方法:
1. 可塑法成型:在外力作用下,使具有可塑性的坯料发生塑性变形而制成坯体的方法。
具体分为手工成形和机械成形两大类。
手工成形如雕塑、印坯、拉坯、手捏等,多用于艺术陶瓷的制造。
而机械成形如旋压和滚压成形,则多用于盘、碗、杯碟等制品的生产。
此外,还有其他陶瓷工业中采用的挤制、车坯、压制、轧膜等可塑成形方法。
2. 注浆法成型:利用多孔模型的吸水性,将泥浆注入其中而成形的方法。
这种成形方法适应性强,凡是形状复杂,不规则的薄壁、厚胎、体积较大且尺寸要求不严的制品都可用注浆法成型。
例如日用陶瓷中的花瓶、汤碗、椭圆形盘、茶壶手柄等都可采用注浆法成型。
3. 压制法成型:利用压力将置于模具内的粉料压紧至结构紧密,成为具有一定形状和尺寸的坯体的成形方法。
此外,还有其他的成型方法,如干压成型、等静压成型等,可以根据不同的需求选择合适的成型方法。
- 1、下载文档前请自行甄别文档内容的完整性,平台不提供额外的编辑、内容补充、找答案等附加服务。
- 2、"仅部分预览"的文档,不可在线预览部分如存在完整性等问题,可反馈申请退款(可完整预览的文档不适用该条件!)。
- 3、如文档侵犯您的权益,请联系客服反馈,我们会尽快为您处理(人工客服工作时间:9:00-18:30)。
• 三、成型需满足的要求: • 由于不同的成形方法对坯料的工艺性能要求不同, 成形应满足烧成所要求的生坯干燥强度、坯体致密 度、生坯入窑水分、器形规整等性能,因此成形工 序应满足下列要求: • 1.坯体应符合产品所要求的生坯形状和尺寸(应考 虑收缩)。 • 2.坯体应具有相当的机械强度,以便于后续工序的 操作。 • 3.坯体结构均匀,具有一定的致密度。 • 4.成型过程适合于多、快、好、省的组织生产
• 模型的材料:石膏模型、多孔树脂模型、无机填料 模型。
• 根据压力的大小可将压力注浆分为: • 微压注浆:压力<0.03 MPa 采用石膏模型 • 中压注浆:压力0.15~0.4 MPa 强度较高的石膏模 型,树脂模型 • 高压注浆:压力> 2 MPa 高强度树脂模型
微压注浆成型原理图
真空脱泡压力注浆示意图
项目1:注浆成型技术
• 一、注浆成型 • 传统的定义:在石膏模的毛细管力作用下,含有一定水分的粘土 泥浆脱水硬化、成型的过程。 • 目前:将所有基于坯料具有一定液态流动性的成型方法统归为注 浆成型。 • 工艺特点: • (1)适于成型各种产品,形状复杂、不规则、薄、体积较大而 且尺寸要求不严的器物,如花瓶、汤碗、椭圆形盘、茶壶等。 • (2)坯体结构均匀,但含水量大且不均匀,干燥与烧成收缩大。
• 干修注意事项:在修坯前,坯体的表面有污物时, 务必清除干净;有棕眼时用浆水糊住;坯体有气泡, 一般在5mm左右,可以用干坯碎块堵,超过5mm, 可用刮刀刮平,使其无明显痕迹,如气泡太大则做 废气处理。表面有明显凹凸一定要刮平。
• (2)湿修 • 含水率较高,为16%左右。适合器形复杂、异形或 大件产品。主要包括修薄、修平和修光操作。 • 2、粘接 • 将分别成形好的陶瓷部件粘成完整坯件的操作。 • 有湿接和干接操作方式。湿接坯件含水率15~19 %,坯体在较软的情况下粘接,粘接头不易开裂, 粘接泥较易配制,同时粘接成功率较高。干接含水3 %以下,操作过程坯体变形小,接头处易开裂,粘 接技术要求高,适合接头面积大且附件较重坯件。
• 四、成形方法的选择依据 • 选择陶瓷成型方法最基本的依据是:产品的器型、 产量和品质要求,坯料的性能及经济效益,通常具 体要求考虑以下几个方面: • 1.产品的形状、大小、厚薄等; • 2.产品的工艺性能; • 3.产品质量及品质要求; • 4.成形设备容易操作,操作强度小,操作条件好,并 便于与前工序联动或自动化; • 5.技术指标高,经济效益好,劳动强度低。
• 2、实心注浆 (双面注浆)
solid casting
• 四、强化注浆方法 • 1、离心注浆法 • 使模型在旋转情况下进浆,料浆在离心力的作用下 紧靠模壁形成致密的坯体。气泡较轻,易集中在中 间最后破裂排出,故可提高吸浆速度与制品质量。 • 要求:泥浆中的颗粒分布范围窄,否则大颗粒集中 在靠近模型的坯体表面,而小颗粒集中在坯体内面, 造成坯体组织不均匀,收缩不一致。
高压注浆成型原理图
• 五、修坯与粘接 • 1、修坯 • 可塑法和注浆法成型的生坯件,表面不太光滑,边 口都呈毛边现象,多合模型的注浆坯件会有接缝痕 迹,某些产品的进一步加工如挖底、打孔等,都需 要进一步加工修平。工厂称此为修坯,这是成型工 艺中的一项必要的工序,决定产品的表面质量、外 观质量等。通过修坯使坯体成为能适应施釉和入窑 焙烧技术要求的精坯
• 各类产品尽管加工方法不同,但是坯体修整是必要 的,不可忽视的,否则就不能保证瓷器半成品质量。 在修坯中也要防止坯体产生缺陷,并修整那些能修 整的带缺陷的坯体。 • 修坯分为干修和湿修两种方式。 • 湿修:坯体的水分16~19%。 • 干修:坯体的水分 < 2%。
• (1)干修
• 适合盘、碟、碗、杯类。在修坯机上操作。含水率 一般小于3%。使用砂布或铜丝网将表面擦干。
• 一、成型的概念
• 成型是将制备好的坯料,用各种不同的方法制成具有一定形状和 尺寸的坯体(生坯)的过程。 • 二、陶瓷成型的分类 • 从工艺上讲,根据坯料的性能和含水量的不同,陶瓷的成型方法 可分为三类:注浆成型、可塑成型、压制成型
热法(热压注法):钢模 注浆成型法
冷法 常压冷法注浆 加压冷法注浆 抽真空冷法注浆 石膏模 坯料含水量 30~35%
• 二、注浆成型的工艺过程 • 将制备好的坯料泥浆注入多孔性模型内,由于多孔 性模型的吸水性,泥浆在贴近模壁的一侧被模子吸 水而形成一均匀的泥层,并随时间的延长而加厚, 当达到所需厚度时,将多余的泥浆倾出,最后该泥 层继续脱水收缩而与模型脱离,从模型取出后即为 毛坯。
三、 普通注浆成型方法 1、空心注浆法(单面注浆) drain casting
• 2、真空注浆 • 在模型外抽真空,或将加固后的石膏模放在真空室 中负压操作,以增大石膏模内外压,提高注浆成型 时的推动力,提高吸浆速度,缩短坯体形成时间, 提高坯体致密度和强度,同时减少坯体的气孔和针 孔。
• 3、压力注浆
• 通过提高泥浆压力来增大注浆过程推动力,加速水 分的扩散,不仅可缩短注浆时间,还可减少坯体的 干燥收缩和脱模后坯体的水分。 • 注浆压力越高,成型速度越大,生坯强 • 粘接泥工艺性能: • 1)黏着性好 • 2)干燥收缩小,干燥强度大,干燥时不开裂 • 3)与坯釉结合良好烧结性能、烧成温度与坯釉相适应 • 4)烧成时应与坯件粘为一体。 • 5)热稳定性好
有模 成型方法 可塑成型法 无模 压制成型法:干压成型,使用钢模 ,坯料含水量4~7%、等静 坯料含水量18~26%
压成型,使用橡皮膜,坯料含水量1.5~3%
成型方法分类
• 1、注浆成型——常见的有普通注浆、高压注浆,适 用范围广,常用于制作空心坯体、异型坯体。 • 2、可塑成型——常见的有滚压、旋压、挤压、辊压、 塑压、拉坯、印模、轧模、雕塑,成型方法多,多 用于制作回旋体、扁平状坯体,也可用于制作大型 或异型产品。 • 3、压制成型——常见的有干压成型、等静压成型, 日用陶瓷常用于制作盘、碟类产品,建筑陶瓷常用 于制作平板状陶瓷砖。 • 4、热压注成型——一般用于特种陶瓷的成型工艺