液压系统设计方案书方法
动力滑台液压系统课程设计说明书

动力滑台液压系统课程设计说明书一、引言1.背景介绍随着现代工业的快速发展,动力滑台在各类机械设备中的应用越来越广泛。
液压传动作为动力滑台的核心传动方式,具有传动比稳定、承载能力强、噪音低等优点。
因此,对动力滑台液压系统的研究与设计具有重要的实际意义。
2.设计目的本课程设计旨在了解和掌握动力滑台液压系统的设计方法及原理,培养学生分析和解决实际工程问题的能力。
通过本设计,使学生熟悉液压元件的选型、系统原理图的绘制以及液压系统的仿真与试验等环节。
3.设计内容概述本设计主要内容包括:动力滑台液压系统原理及设计要求、方案设计、仿真与分析、设计优化及试验等。
二、动力滑台液压系统原理及设计要求1.动力滑台液压系统工作原理动力滑台液压系统主要由液压泵、液压缸、阀门及控制元件、辅助元件等组成。
液压泵为系统提供压力油,通过阀门控制油液流向和压力大小,驱动液压缸实现滑台的直线运动。
2.设计技术要求在设计过程中,需满足以下技术要求:(1)系统性能稳定,工作可靠;(2)系统油液清洁,无污染;(3)系统能耗低,运行经济;(4)系统具有一定的安全防护措施。
3.设计性能指标本设计性能指标主要包括:(1)滑台运动速度;(2)最大承载能力;(3)系统压力波动;(4)油液温度升高等。
三、动力滑台液压系统方案设计1.系统组成本设计动力滑台液压系统主要由液压泵、液压缸、阀门及控制元件、辅助元件等组成。
2.主要元件选型(1)液压泵:根据系统流量和压力要求,选择合适的液压泵;(2)液压缸:根据滑台承载能力和行程要求,选择合适的液压缸;(3)阀门及控制元件:根据系统功能需求,选择合适的阀门及控制元件;(4)辅助元件:根据系统油液循环和冷却需求,选择合适的辅助元件。
3.系统原理图设计根据系统组成和元件选型,绘制动力滑台液压系统原理图。
四、动力滑台液压系统仿真与分析1.仿真软件介绍选用某液压仿真软件进行仿真分析,该软件具有丰富的元件库和强大的仿真功能。
小型液压机:液压系统设计方案概述

小型液压机:液压系统设计方案概述
1. 概述
本文档旨在提供小型液压机的液压系统设计方案概述。
液压系统是小型液压机的核心部分,其设计直接影响到机器的性能和工作效率。
2. 设计目标
小型液压机的设计目标是实现以下要求:
- 提供足够的压力和力量以完成所需的工作任务
- 保证系统的安全性和可靠性
- 简化系统结构,降低成本和维护难度
3. 液压系统组成
小型液压机的液压系统主要由以下组件组成:
- 液压泵:负责将液压油从油箱中抽取并提供给液压缸
- 液压缸:通过液压油的压力产生力量,完成机器的工作任务- 液压阀:控制液压油的流量和压力,实现液压系统的各种操作功能
- 油箱:贮存液压油,并保持油温稳定
- 液压管路:连接液压泵、液压缸和液压阀,传递液压油的流动
4. 系统设计方案
为了实现设计目标,我们提出以下液压系统设计方案:
- 选择合适的液压泵:根据工作任务的需求,选择合适的液压泵,确保能够提供足够的压力和流量。
- 选择合适的液压缸:根据工作任务的需求,选择合适的液压缸,确保能够产生足够的力量。
- 选择合适的液压阀:根据工作任务的需求,选择合适的液压阀,确保能够控制液压油的流量和压力。
- 设计合理的油箱:根据系统需求和空间限制,设计合理的油箱,确保能够储存足够的液压油,并保持油温稳定。
- 设计合理的液压管路:根据系统需求和空间限制,设计合理的液压管路,确保液压油能够顺畅地流动。
5. 结论
本文档提供了小型液压机液压系统设计方案的概述。
通过选择合适的液压泵、液压缸和液压阀,并设计合理的油箱和液压管路,可以实现小型液压机的高效、安全和可靠的工作。
组合机床液压系统设计
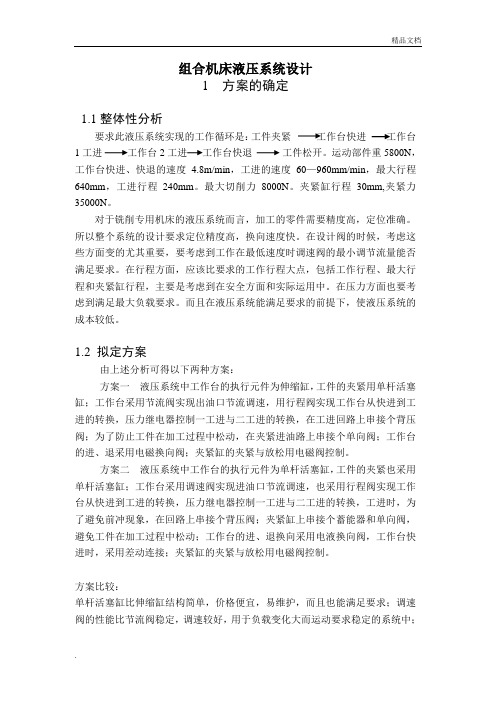
组合机床液压系统设计1 方案的确定1.1整体性分析要求此液压系统实现的工作循环是:工件夹紧工作台快进工作台1工进工作台2工进工作台快退工件松开。
运动部件重5800N,工作台快进、快退的速度 4.8m/min,工进的速度60—960mm/min,最大行程640mm,工进行程240mm。
最大切削力8000N。
夹紧缸行程30mm,夹紧力35000N。
对于铣削专用机床的液压系统而言,加工的零件需要精度高,定位准确。
所以整个系统的设计要求定位精度高,换向速度快。
在设计阀的时候,考虑这些方面变的尤其重要,要考虑到工作在最低速度时调速阀的最小调节流量能否满足要求。
在行程方面,应该比要求的工作行程大点,包括工作行程、最大行程和夹紧缸行程,主要是考虑到在安全方面和实际运用中。
在压力方面也要考虑到满足最大负载要求。
而且在液压系统能满足要求的前提下,使液压系统的成本较低。
1.2 拟定方案由上述分析可得以下两种方案:方案一液压系统中工作台的执行元件为伸缩缸,工件的夹紧用单杆活塞缸;工作台采用节流阀实现出油口节流调速,用行程阀实现工作台从快进到工进的转换,压力继电器控制一工进与二工进的转换,在工进回路上串接个背压阀;为了防止工件在加工过程中松动,在夹紧进油路上串接个单向阀;工作台的进、退采用电磁换向阀;夹紧缸的夹紧与放松用电磁阀控制。
方案二液压系统中工作台的执行元件为单杆活塞缸,工件的夹紧也采用单杆活塞缸;工作台采用调速阀实现进油口节流调速,也采用行程阀实现工作台从快进到工进的转换,压力继电器控制一工进与二工进的转换,工进时,为了避免前冲现象,在回路上串接个背压阀;夹紧缸上串接个蓄能器和单向阀,避免工件在加工过程中松动;工作台的进、退换向采用电液换向阀,工作台快进时,采用差动连接;夹紧缸的夹紧与放松用电磁阀控制。
方案比较:单杆活塞缸比伸缩缸结构简单,价格便宜,易维护,而且也能满足要求;调速阀的性能比节流阀稳定,调速较好,用于负载变化大而运动要求稳定的系统中;采用出油口调速回路中油液通过节流阀产生的热量直接排回油箱散热;夹紧缸进油口处串接蓄能器,更好的保证工件的夹紧力,使工件在加工过程中始终在夹紧状态。
18吨液压绞车液压系统设计

18吨液压绞车液压系统设计简介本文档旨在详细介绍18吨液压绞车液压系统的设计。
液压绞车是一种常用于起重和搬运重物的机械设备,其液压系统是其核心部分,负责提供动力和控制绞车的运动。
系统组成液压绞车液压系统主要由下列组成部分构成:1.液压油箱:用于存储液压油,并保持其温度和质量。
2.液压泵:负责将液压油从油箱中抽出,并产生所需的油压。
3.油压阀:用于控制液压系统的压力和流量。
4.液压缸:将液压能转化为机械能,驱动绞车的运动。
5.液压马达:将液压能转化为机械能,驱动绞车的旋转。
6.液压管路:将液压油从泵传输至液压缸和液压马达,并回流至油箱。
系统工作原理液压绞车液压系统的工作原理如下:1.初始状态下,液压泵未运行,液压油箱中的液压油处于静止状态。
2.当操作人员启动液压泵时,液压泵开始运转,并抽取液压油从油箱中。
3.液压泵产生的液压油被送入油压阀,油压阀根据系统需求调节油压和流量。
4.调节后的液压油通过液压管路传输至液压缸和液压马达。
5.当液压油进入液压缸时,液压能转化为机械能,推动绞车的运动。
6.当液压油进入液压马达时,液压能转化为机械能,推动绞车的旋转。
7.液压油流经液压缸和液压马达后,回流至油箱。
系统设计考虑因素在设计18吨液压绞车液压系统时,需要考虑以下因素:1.载荷能力:液压系统需要能够提供足够的油压和流量,以满足18吨载荷的需求。
2.安全性:液压系统需要具备足够的稳定性和可靠性,以确保绞车的安全运行。
3.效率:液压系统需要具备高效和节能的特性,以减少能源消耗和操作成本。
4.控制性:液压系统需要具备良好的控制性能,以满足操作人员对绞车运动的精确控制需求。
5.维护性:液压系统需要设计合理,易于维护和保养,以延长设备的使用寿命和降低维护成本。
系统设计方案基于上述考虑因素,我们提出以下设计方案:1.选用适当的液压泵和油压阀:根据18吨载荷的需求,选用能够提供足够流量和油压的液压泵和油压阀。
2.设计合理的液压缸和液压马达:根据绞车的结构和运动特点,设计合适的液压缸和液压马达,以满足载荷能力要求。
25吨位起重机伸缩机构液压系统设计说明

25吨位起重机伸缩机构液压系统设计说明设计说明:25吨起重机伸缩机构液压系统一、系统需求分析根据25吨起重机的要求,其伸缩机构需要能够稳定可靠地实现起重机整体的伸缩操作。
因此需要设计一个液压系统,满足以下要求:1.传动功率大:能够承受25吨重物的伸缩操作,需要具备足够的工作压力和流量来传递高功率。
2.稳定可靠:液压系统需要具备稳定可靠的性能,能够在长时间工作中保持压力和流量的稳定。
3.速度控制:需要有控制装置来调节伸缩速度,使其能够根据实际需要实现快速、慢速或中速伸缩。
4.具备安全保护:系统需要具备过载保护、液压缸行程限位以及紧急停机装置等安全保护功能。
5.维护方便:设计需要考虑系统的布局合理性,便于维护和检修。
二、系统设计方案根据以上需求分析,设计的液压系统方案如下:1.液压泵和液压马达:选择适合的液压泵和液压马达,根据起重机的工作要求,确定泵的排量和转速以及马达的扭矩和转速,保证足够的工作压力和流量。
2.液压控制阀:选用符合起重机伸缩机构要求的液压控制阀,能够实现伸缩的快速、慢速和中速调节,同时具备压力和流量稳定的能力。
3.液压缸:选用具备足够承载力和行程的液压缸,能够实现起重机的伸缩操作。
需要具备行程限位和缓冲装置,保证伸缩过程的稳定可靠性。
4.液压储气罐和滤油器:设置液压储气罐用于储存液压系统的过剩液体和气体,保持系统的稳定压力。
同时安装滤油器来过滤液体中的杂质,提高系统的工作效率和寿命。
5.安全保护:设置过载保护阀,当系统受到过载时能够及时减少压力,保护系统的安全。
同时设置液压缸行程限位开关,当液压缸达到极限位置时能够自动停止工作,避免超过承载能力。
还应设置紧急停机按钮,当遇到紧急情况时能够快速停止起重机的伸缩操作。
6.维护方便:设计合理的管路布局,保证液压系统的布局紧凑,方便维护和检修。
并设有液压油温度和压力监测仪器,实时监测和掌握系统的工作状态。
三、液压系统的工作原理液压系统的工作原理是通过液压泵将液体压力传递给液压缸,从而推动起重机的伸缩机构实现伸缩操作。
液压系统设计篇

液压系统设计篇----4ffaa03a-7161-11ec-876d-7cb59b590d7d液压传动系统设计,除了应符合其主机在动作循环和静、动态性能等方面所提出的要求外,还必须满足结构简单、使用维护方便、工作安全可靠、性能好、成本低、效率高、寿命长等条件。
液压传动系统的设计一般依据流程图见图4-1的步骤进行设计。
图4-1液压传动系统设计流程图第一节明确设计要求要设计一个新的液压系统,首先必须明确机器对液压系统的动作和性能要求,并将这些技术要求作为设计的出发点和基础。
需要掌握的技术要求可能包括:1.机器的特性(1)充分了解主机的结构和总体布置,机构与从动件之间的连接条件和安装限制,以及其用途和工作目的。
(2)负载种类(恒定负载、变化负载及冲击负载)及大小和变化范围;运动方式(直线运动、回转运动、摆动)及运动量(位移、速度、加速度)的大小和要求的调节范围;惯性力、摩擦力、动作特性、动作时间和精度要求(定位精度、跟踪精度、同步精度)。
(3)原动机类型(电机、内燃机等)、容量(功率、速度、扭矩)和稳定性。
(4)操作方式(手动、自动)、信号处理方式(继电器控制、逻辑电路、可编程控制器、微机程序控制)。
(5)系统中每个执行器的动作顺序和动作时间之间的关系。
2.使用条件(1)设置地点。
(2)环境温度、湿度(高温、寒带、热带),粉尘种类和浓度(防护、净化等),腐蚀性气体(所有元件的结构、材质、表面处理、涂覆等),易爆气体(防爆措施),机械振动(机械强度、耐振结构),噪声限制(降低噪声措施)。
(3)维护程度和周期;维修人员的技术水平;保持空间、可操作性和互换性。
3.适用的标准和规则根据用户要求采用相关标准、法则。
4.安全性、可靠性(1)用户在安全方面是否有特殊要求。
(2)指定保修期和条件。
5.经济不能只考虑投资费用,还要考虑能源消耗、维护保养等运行费用。
6.工况分析液压系统的工况分析是为了找出各执行机构在各自工作过程中的速度和负载变化规律。
液压系统研制实施方案
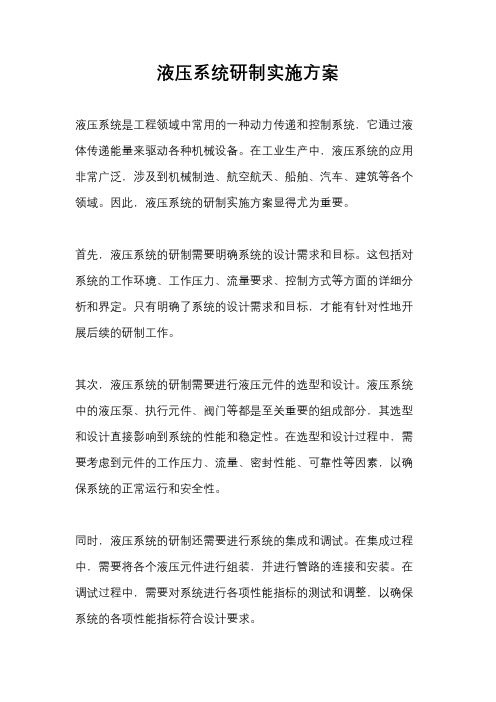
液压系统研制实施方案
液压系统是工程领域中常用的一种动力传递和控制系统,它通过液体传递能量来驱动各种机械设备。
在工业生产中,液压系统的应用非常广泛,涉及到机械制造、航空航天、船舶、汽车、建筑等各个领域。
因此,液压系统的研制实施方案显得尤为重要。
首先,液压系统的研制需要明确系统的设计需求和目标。
这包括对系统的工作环境、工作压力、流量要求、控制方式等方面的详细分析和界定。
只有明确了系统的设计需求和目标,才能有针对性地开展后续的研制工作。
其次,液压系统的研制需要进行液压元件的选型和设计。
液压系统中的液压泵、执行元件、阀门等都是至关重要的组成部分,其选型和设计直接影响到系统的性能和稳定性。
在选型和设计过程中,需要考虑到元件的工作压力、流量、密封性能、可靠性等因素,以确保系统的正常运行和安全性。
同时,液压系统的研制还需要进行系统的集成和调试。
在集成过程中,需要将各个液压元件进行组装,并进行管路的连接和安装。
在调试过程中,需要对系统进行各项性能指标的测试和调整,以确保系统的各项性能指标符合设计要求。
最后,液压系统的研制还需要进行系统的试验和验证。
在试验过程中,需要对系统进行各种负载和工况下的测试,以验证系统的稳定
性和可靠性。
只有通过试验验证,才能确保系统的性能和安全性符
合设计要求。
总的来说,液压系统的研制实施方案需要从系统设计需求和目标的
明确开始,经过液压元件的选型和设计、系统的集成和调试,最终
进行系统的试验和验证,以确保系统的性能和安全性符合设计要求。
只有这样,才能保证液压系统在工程领域中的应用具有更好的效果
和可靠性。
液压系统研制实施方案
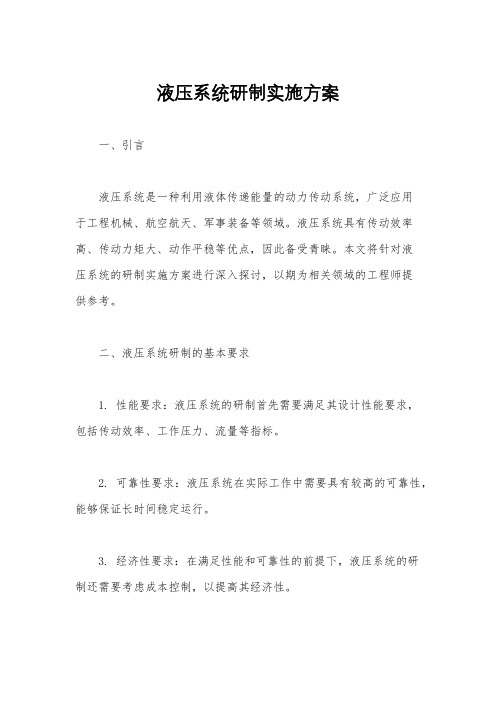
液压系统研制实施方案一、引言液压系统是一种利用液体传递能量的动力传动系统,广泛应用于工程机械、航空航天、军事装备等领域。
液压系统具有传动效率高、传动力矩大、动作平稳等优点,因此备受青睐。
本文将针对液压系统的研制实施方案进行深入探讨,以期为相关领域的工程师提供参考。
二、液压系统研制的基本要求1. 性能要求:液压系统的研制首先需要满足其设计性能要求,包括传动效率、工作压力、流量等指标。
2. 可靠性要求:液压系统在实际工作中需要具有较高的可靠性,能够保证长时间稳定运行。
3. 经济性要求:在满足性能和可靠性的前提下,液压系统的研制还需要考虑成本控制,以提高其经济性。
三、液压系统研制的技术方案1. 液压元件的选型:液压系统的研制首先需要根据设计要求选择合适的液压元件,包括液压泵、液压阀、液压缸等。
在选型时需要考虑元件的性能、品质、价格等因素。
2. 液压系统的布局设计:液压系统的布局设计需要考虑元件之间的连接方式、管路的布置方式、油箱的容积等因素,以保证系统的紧凑性和稳定性。
3. 液压系统的控制策略:液压系统的研制还需要考虑控制策略的制定,包括开环控制、闭环控制、比例控制等方式,以实现对系统的精准控制。
4. 液压系统的试制与调试:在研制过程中需要进行系统的试制与调试工作,以验证设计方案的可行性,并对系统进行性能优化。
四、液压系统研制的实施步骤1. 确定研制目标:明确液压系统的使用环境、工作条件、性能要求等,为研制工作奠定基础。
2. 设计方案制定:根据研制目标,制定液压系统的设计方案,包括选型、布局、控制策略等内容。
3. 元件采购与加工:根据设计方案,采购所需的液压元件,并进行加工制造。
4. 系统组装与调试:将液压元件进行组装,并进行系统的调试工作,验证系统的性能。
5. 系统性能测试:对研制的液压系统进行性能测试,以验证其满足设计要求。
6. 系统优化与改进:根据性能测试结果,对系统进行优化与改进,以提高其性能和可靠性。
- 1、下载文档前请自行甄别文档内容的完整性,平台不提供额外的编辑、内容补充、找答案等附加服务。
- 2、"仅部分预览"的文档,不可在线预览部分如存在完整性等问题,可反馈申请退款(可完整预览的文档不适用该条件!)。
- 3、如文档侵犯您的权益,请联系客服反馈,我们会尽快为您处理(人工客服工作时间:9:00-18:30)。
液压系统设计方法液压系统是液压机械的一个组成部分,液压系统的设计要同主机的总体设计同时进行。
着手设计时,必须从实际情况出发,有机地结合各种传动形式,充分发挥液压传动的优点,力求设计出结构简单、工作可靠、成本低、效率高、操作简单、维修方便的液压传动系统。
液压系统的设计步骤液压系统的设计步骤并无严格的顺序,各步骤间往往要相互穿插进行。
一般来说,在明确设计要求之后,大致按如下步骤进行。
⑴确定液压执行元件的形式;⑵进行工况分析,确定系统的主要参数;⑶制定基本方案,拟定液压系统原理图;⑷选择液压元件;⑸液压系统的性能验算:⑹绘制工作图,编制技术文件。
1.明确设计要求设计要求是进行每项工程设计的依据。
在制定基本方案并进一步着手液压系统各部分设计之前,必须把设计要求以及与该设计内容有关的其他方面了解清楚。
⑴主机的概况:用途、性能、工艺流程、作业环境、总体布局等;⑵液压系统要完成哪些动作,动作顺序及彼此联锁关系如何;⑶液压驱动机构的运动形式,运动速度;⑷各动作机构的载荷大小及其性质;⑸对调速范围、运动平稳性、转换精度等性能方面的要求;⑹自动化程度、操作控制方式的要求;⑺对防尘、防爆、防寒、噪声、安全可靠性的要求;⑻对效率、成本等方面的要求。
2.进行工况分析、确定液压系统的主要参数通过工况分析,可以看出液压执行元件在工作过程中速度和载荷变化情况,为确定系统及各执行元件的参数提供依据。
液压系统的主要参数是压力和流量,它们是设计液压系统,选择液压元件的主要依据。
压力决定于外载荷。
流量取决于液压执行元件的运动速度和结构尺寸。
2.1载荷的组成和计算2.1.1液压缸的载荷组成与计算图1表示一个以液压缸为执行元件的液压系统计算简图。
各有关参数已标注在图上,其中F W是作用在活塞杆上的外部载荷。
F m是活塞与缸壁以及活塞杆与导向套之间的密封阻力。
作用在活塞杆上的外部载荷包括工作载荷F g,导轨的摩擦力F f和由于速度变化而产生的惯性力F a。
⑴工作载荷F g常见的工作载荷有作用于活塞杆轴线上的重力、切削力、挤压力等。
这些作用力的方向如与活塞运动方向相同为负,相反为正。
⑵导轨摩擦载荷F f对于平导轨F f=μ(G+F N)对于V型导轨F f=μ(G+F N)/sin(α/2)式中G——运动部件所受的重力(N);F N——外载荷作用于导轨上的正压力(N);μ——摩擦系数,见表2—1;α——V型导轨的夹角,一般为90°。
表2—1摩擦系数μ⑶惯性载荷F at v g G F a ∆∆= 式中 g ——重力加速度;g =9.81m/s 2Δv ——速度变化量(m/s);Δt ——起动或制动时间(s)。
一般机械Δt =0.1~0.5s ,对轻载低速运动部件取小值,对重载高速部件取大值。
行走机械一般取Δv /Δt =0.5~1.5m/s 2。
以上三种载荷之和称为液压缸的外载荷F W 。
起动加速时F W =F g +F f +F a稳态运动时F W =F g +F f减速制动时F W =F g +F f -F a工作载荷F g 并非每阶段都存在,如该阶段没有工作,则F g =0。
除外载荷F W 外,作用于活塞上的载荷F 还包括液压缸密封处的摩擦阻力F m ,由于各种缸的密封材质和密封形成不同,密封阻力难以精确计算,一般估算为 F m =(1-ηm )F式中 ηm ——液压缸的机械效率,一般取0.90~0.95。
m WF F η=2.1.2液压马达载荷力矩的组成与计算⑴工作载荷力矩T g常见的载荷力矩有被驱动轮的阻力矩、液压卷简的阻力矩等。
⑵轴颈摩擦力矩T fT f =μGr式中 G ——旋转部件施加于轴颈上的径向力(N );μ——摩擦系数,参考表2—1选用;r ——旋转轴的半径(m )。
⑶惯性力矩T atJ J T a ∆∆==ωε 式中 ε——角加速度(rad/s 2);Δω——角速度变化量(rad/s );Δt ——起动或制动时间(s);J ——回转部件的转动惯量(kg ·m 2)。
起动加速时T w =T g +T f +T a稳定运行时T w =T g +T f减速制动时T w =T g +T f -T a计算液压马达载荷转矩T 时还要考虑液压马达的机械效率ηm =0.9~0.98。
m WT T η=根据液压缸或液压马达各阶段的载荷,绘制出执行元件的载荷循环图,以便进一步选择系统工作压力和确定其他有关参数。
2.2初选系统工作压力压力的选择要根据载荷大小和设备类型而定。
还要考虑执行元件的装配空间、经济条件及元件供应情况等的限制。
在载荷一定的情况下,工作压力低,势必要加大执行元件的结构尺寸,对某些设备来说,尺寸要受到限制,从材料消耗角度看也不经济;反之,压力选得太高,对泵、缸、阀等元件的材质、密封、制造精度也要求很高,必然要提高设备成本。
一般来说,对于固定的、尺寸不太受限的设备,压力可以选低一些,行走机械、重载设备压力要选得高一些。
具体选择可参考表2—2和表2—3。
注意,高压化是液压系统发展趋势之一,因此压力应选得高一些,以减小系统的体积是可行的。
此外,低压阀已逐渐淘汰,即使是低压系统也应采用高压阀。
A=2.3计算液压缸的主要结构尺寸和液压马达的排量⑴计算液压缸的主要结构尺寸液压缸主要设计参数见图2。
图a 为液压缸活塞杆工作在受压状态,图b 为活塞杆工作在受拉状态。
活塞杆受压时,2211A p A p F -=活塞杆受拉时,1221A p A p F -=式中 A 1——无杆腔活塞有效作用面积(m 2);A 2——有杆腔活塞有效作用面积(m 2);P 1——液压缸工作腔压力(Pa);P 2——液压缸回油腔压力(Pa),即背压力。
其值根据回路的具体情况而定,初算时可参照表2—4取值。
差动连接时则要另行考虑。
D ——活塞直径(m);d ——活塞杆直径(m)。
一般,液压缸在受压状态下工作,其活塞面积为 1221p A p F A += 运用上式须事先确定A l 与A 2的关系,或是活塞杆径d 与活塞直径D 的关系,令杆径比φ=d /D ,其比值可按表2—5和表2—6选取。
[])1(4221ϕπ--=p p F D 采用差动连接时,v l /v 2=(D 2-d 2)/d 2。
如要求往返速度相同时,应取d =0.71D 。
对行程与活塞杆直径比l /d >10的受压柱塞或活塞杆,还要做压杆稳定性验算。
当工作速度很低时,还须按最低速度要求验算液压缸尺寸m inm in v q A ≥ 式中 A ——液压缸有效工作面积(m 2);q min ——系统最小稳定流量(m 3/s),在节流调速中取决于回路中所设调速阀或节流阀的最小稳定流量。
容积调速中决定于变量泵的最小稳定流量。
v min ——运动机构要求的最小工作速度(m/s)。
如果液压缸的有效工作面积A 不能满足最低稳定速度的要求,则应按最低稳定速度确定液压缸的结构尺寸。
另外,如果执行元件安装尺寸受到限制,液压缸的缸径及活塞杆的直径须事先确定时,可按载荷的要求和液压缸的结构尺寸来确定系统的工作压力。
液压缸直径D 和活塞杆直径d 的计算值要按国标规定的液压缸的有关标准进行圆整。
如与标准液压缸参数相近,最好选用国产标准液压缸,免于自行设计加工。
常用液压缸内径及活塞扦直径见表2-7和表2—8。
⑵计算液压马达的排量 液压马达的排量为pT V M ∆=π2 式中T ——液压马达的载荷转矩(N ·m);Δp ——液压马达的进出口压差(Pa)。
液压马达的排量也应满足最低转速要求m inm in n q V M 式中 q min ——通过液压马达的最小流量;n min ——液压马达工作时的最低转速。
2.4计算液压缸或液压马达所需流量⑴液压缸工作时所需流量q =Av式中 A —液压缸有效作用面积(m 2);v ——活寨与缸体的相对速度(m/s)。
⑵液压马达的流量q =V M n M式中 V M ——液压马达排量(m3/r);n M ——液压马达的转速(r/s)。
2.5绘制液压系统工况图工况图包括压力循环图、流量循环图和功率循环图。
它们是调整系统参数、选择液压泵、阀等元件的依据。
⑴压力循环图——(p —t )图通过最后确定的液压执行元件的结构尺寸,再根据实际载荷的大小,倒求出液压执行元件在其动作循环各阶段的工作压力,然后把它们绘制成(p —t )图。
⑵流量循环图——(q —t )图根据已确定的液压缸有效工作面积或液压马达的排量,结合其运动速度算出它在工作循环中每一阶段的实际流量,把它绘制成(q —t )图。
若系统中有多个液压执行元件同时工作,要把各自的流量图叠加起来绘出总的流量循环图。
⑶功率循环图——(P —t )图绘出压力循环图和总流量循环图后,根据P =pq ,即可绘出系统的功率循环图。
3.制定基本方案和绘制液压系统图3.1制定基本方案⑴制定调速方案液压执行元件确定之后,其运动方向和运动速度的控制是拟定液压回路的核心问题。
方向控制用换向阀或逻辑控制单元来实现。
对于一般中小流量的液压系统,大多通过换向阀的有机组合实现所要求的动作。
对高压大流量的液压系统,现多采用插装阀与先导控制阀的逻辑组合来实现。
速度控制通过改变液压执行元件输入或输出的流量或者利用密封空间的容积变化来实现;相应的调速方式有节流调速、容积调速以及二者的结合——容积节流调速。
节流调速一般采用定量泵供油,配以溢流阀,用流量控制阀改变输入或输出液压执行元件的流量来调节速度。
此种调速方式结构简单。
由于这种系统必须用溢流阀溢流恒压,有节流损失和溢流损失,故效率低,发热量大,用于功率不大的场合。
容积调速是靠改变变量泵或变量马达的排量来达到调速的目的。
其优点是没有溢流损失和节流损失,效率较高。
但为了散热和补充泄漏,需要有辅助泵。
此种调速方式适用于功率大、运动速度高的液压系统。
容积节流调速一般是用变量泵供油,用流量控制阀调节输入或输出液压执行元件的流量,流量控制阀是泵的负载,使泵的供油量与需油量相适应。
此种调速回路效率也较高,速度稳定性较好,但其结构比较复杂。
节流调速又分别有进油节流、回油节流和旁路节流三种形式。
进油节流起动冲击较小,回油节流常用于有负值负载的场合,旁路节流多用于高速。
调速回路一经确定,回路的循环形式也就随之确定了。
节流调速一般采用开式循环形式。
在开式系统中,液压泵从油箱吸油,压力油流经系统释放能量后,再排回油箱。
开式回路结构简单,散热性好,但油箱体积大,容易混入空气。
容积调速大多采用闭式循环形式。
闭式系统中,液压泵的吸油口直接与执行元件的排油口相通,形成一个封闭的循环回路。
其结构紧凑,但散热条件差。
⑵制定压力控制方案液压执行元件工作时,要求系统保持一定的工作压力或在一定压力范围内工作,也有的需要多级或无级连续地调节压力,一般在节流调速系统中,通常由定量泵供油,用溢流阀调节所需压力,并保持恒定。