1700铝箔轧机弯辊液压系统工作原理分析
一种铝箔轧机辅助液压系统改造方案
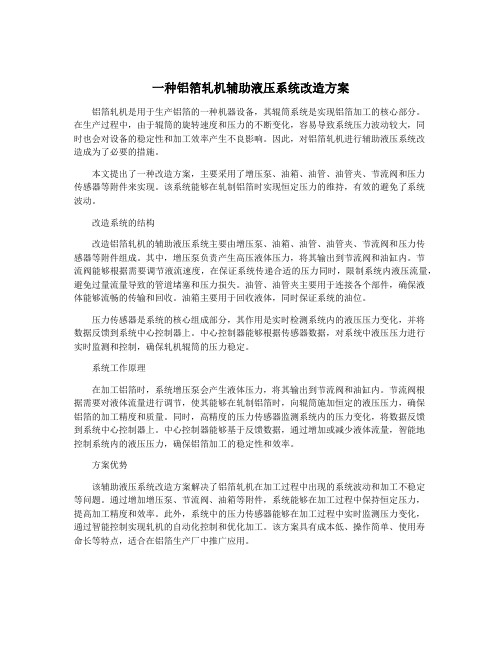
一种铝箔轧机辅助液压系统改造方案铝箔轧机是用于生产铝箔的一种机器设备,其辊筒系统是实现铝箔加工的核心部分。
在生产过程中,由于辊筒的旋转速度和压力的不断变化,容易导致系统压力波动较大,同时也会对设备的稳定性和加工效率产生不良影响。
因此,对铝箔轧机进行辅助液压系统改造成为了必要的措施。
本文提出了一种改造方案,主要采用了增压泵、油箱、油管、油管夹、节流阀和压力传感器等附件来实现。
该系统能够在轧制铝箔时实现恒定压力的维持,有效的避免了系统波动。
改造系统的结构改造铝箔轧机的辅助液压系统主要由增压泵、油箱、油管、油管夹、节流阀和压力传感器等附件组成。
其中,增压泵负责产生高压液体压力,将其输出到节流阀和油缸内。
节流阀能够根据需要调节液流速度,在保证系统传递合适的压力同时,限制系统内液压流量,避免过量流量导致的管道堵塞和压力损失。
油管、油管夹主要用于连接各个部件,确保液体能够流畅的传输和回收。
油箱主要用于回收液体,同时保证系统的油位。
压力传感器是系统的核心组成部分,其作用是实时检测系统内的液压压力变化,并将数据反馈到系统中心控制器上。
中心控制器能够根据传感器数据,对系统中液压压力进行实时监测和控制,确保轧机辊筒的压力稳定。
系统工作原理在加工铝箔时,系统增压泵会产生液体压力,将其输出到节流阀和油缸内。
节流阀根据需要对液体流量进行调节,使其能够在轧制铝箔时,向辊筒施加恒定的液压压力,确保铝箔的加工精度和质量。
同时,高精度的压力传感器监测系统内的压力变化,将数据反馈到系统中心控制器上。
中心控制器能够基于反馈数据,通过增加或减少液体流量,智能地控制系统内的液压压力,确保铝箔加工的稳定性和效率。
方案优势该辅助液压系统改造方案解决了铝箔轧机在加工过程中出现的系统波动和加工不稳定等问题。
通过增加增压泵、节流阀、油箱等附件,系统能够在加工过程中保持恒定压力,提高加工精度和效率。
此外,系统中的压力传感器能够在加工过程中实时监测压力变化,通过智能控制实现轧机的自动化控制和优化加工。
铝箔生产过程中的厚度控制原理及弯辊异常分析
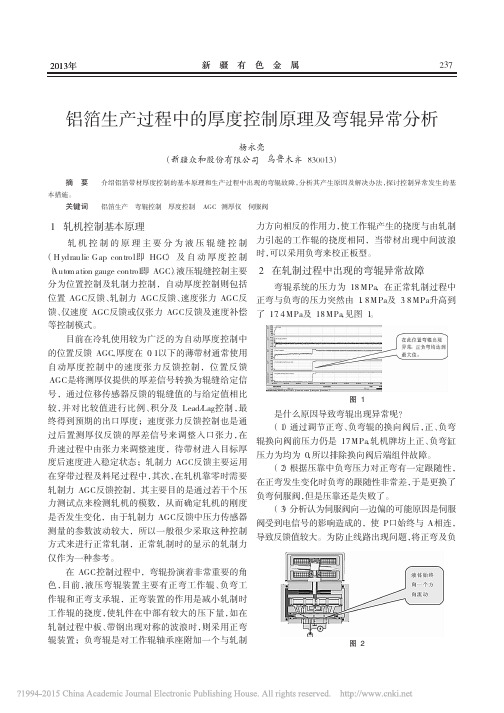
争中立于不败之地。
参考文献
[1] 黄志彬.建筑机电设备安装管理问题的几点思考[J].价
值工程,2010(12).
[2] 张莹,关于机电安装工程的质量控制和需注Байду номын сангаас的问题,
城市建设理论研究,2011(14).
[3] 马海燕,建筑机电设备安装施工中常见问题及对策探
讨[J],机电信息,2010(. 36)。
2013 年
新疆有色金属
237
铝箔生产过程中的厚度控制原理及弯辊异常分析
杨永亮 (新疆众和股份有限公司 乌鲁木齐 830013)
摘要 本措施。
关键词
介绍铝箔带材厚度控制的基本原理和生产过程中出现的弯辊故障,分析其产生原因及解决办法,探讨控制异常发生的基 铝箔生产 弯辊控制 厚度控制 AGC 测厚仪 伺服阀
时,反馈值依然为 98%,从这个现象就可以说明伺服 (AGC)、测厚仪外,加强日程管理,保证设备的完好及 阀空载流量特性出现异常,零位偏移量过大,即当输 来料的质量,对于保证厚度控制的一致性和稳定性, 入电流为零时,流量却不为零,于是更换了正弯伺服 有着至关重要的意义。
阀,随后伺服阀的反馈变为了零,压靠过程中弯辊给
参考文献
定值的逻辑也可以正常通过,轧制试机料正常。这是
[1] 郑申白,史冬日,马劲红.轧钢自动化.北京:化学工业出
我们目前遇到的较为罕见的弯辊系统两个伺服阀同 版社,2009.
时发生故障的现象,所以希望通过此次处理过程与大
[2]黄华清.轧钢机械.北京:冶金工业出版社,1979.
!家!共!享!,电!液!伺!服!阀!的!控!制!原!理!见!图!4!。!!!!!!!!!!!!!!!!!!!!收!稿!:2!01!3-!02!-2!7 !
铝箔轧机熨平辊的分析与探讨
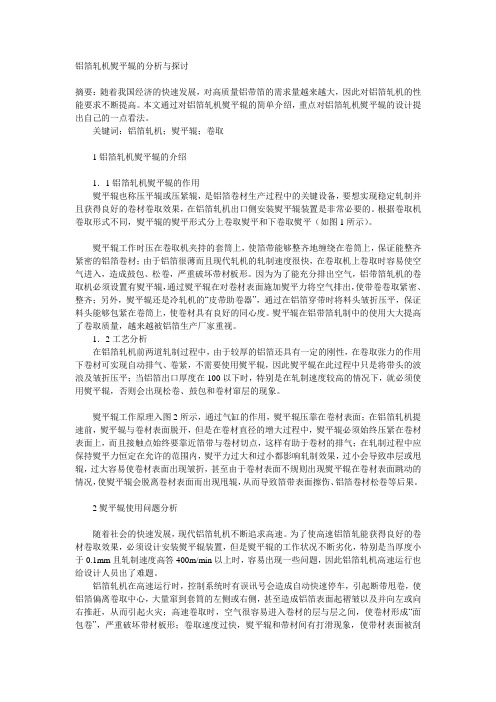
铝箔轧机熨平辊的分析与探讨摘要:随着我国经济的快速发展,对高质量铝带箔的需求量越来越大,因此对铝箔轧机的性能要求不断提高。
本文通过对铝箔轧机熨平辊的简单介绍,重点对铝箔轧机熨平辊的设计提出自己的一点看法。
关键词:铝箔轧机;熨平辊;卷取1铝箔轧机熨平辊的介绍1.1铝箔轧机熨平辊的作用熨平辊也称压平辊或压紧辊,是铝箔卷材生产过程中的关键设备,要想实现稳定轧制并且获得良好的卷材卷取效果,在铝箔轧机出口侧安装熨平辊装置是非常必要的。
根据卷取机卷取形式不同,熨平辊的熨平形式分上卷取熨平和下卷取熨平(如图1所示)。
熨平辊工作时压在卷取机夹持的套筒上,使箔带能够整齐地缠绕在卷筒上,保证能整齐紧密的铝箔卷材;由于铝箔很薄而且现代轧机的轧制速度很快,在卷取机上卷取时容易使空气进入,造成鼓包、松卷,严重破坏带材板形。
因为为了能充分排出空气,铝带箔轧机的卷取机必须设置有熨平辊,通过熨平辊在对卷材表面施加熨平力将空气排出,使带卷卷取紧密、整齐;另外,熨平辊还是冷轧机的“皮带助卷器”,通过在铝箔穿带时将料头皱折压平,保证料头能够包紧在卷筒上,使卷材具有良好的同心度。
熨平辊在铝带箔轧制中的使用大大提高了卷取质量,越来越被铝箔生产厂家重视。
1.2工艺分析在铝箔轧机前两道轧制过程中,由于较厚的铝箔还具有一定的刚性,在卷取张力的作用下卷材可实现自动排气、卷紧,不需要使用熨平辊,因此熨平辊在此过程中只是将带头的波浪及皱折压平;当铝箔出口厚度在100以下时,特别是在轧制速度较高的情况下,就必须使用熨平辊,否则会出现松卷、鼓包和卷材窜层的现象。
熨平辊工作原理入图2所示,通过气缸的作用,熨平辊压靠在卷材表面;在铝箔轧机提速前,熨平辊与卷材表面脱开,但是在卷材直径的增大过程中,熨平辊必须始终压紧在卷材表面上,而且接触点始终要靠近箔带与卷材切点,这样有助于卷材的排气;在轧制过程中应保持熨平力恒定在允许的范围内,熨平力过大和过小都影响轧制效果,过小会导致串层或甩辊,过大容易使卷材表面出现皱折,甚至由于卷材表面不规则出现熨平辊在卷材表面跳动的情况,使熨平辊会脱离卷材表面而出现甩辊,从而导致箔带表面擦伤、铝箔卷材松卷等后果。
轧机液压辊缝控制系统的原理及应用
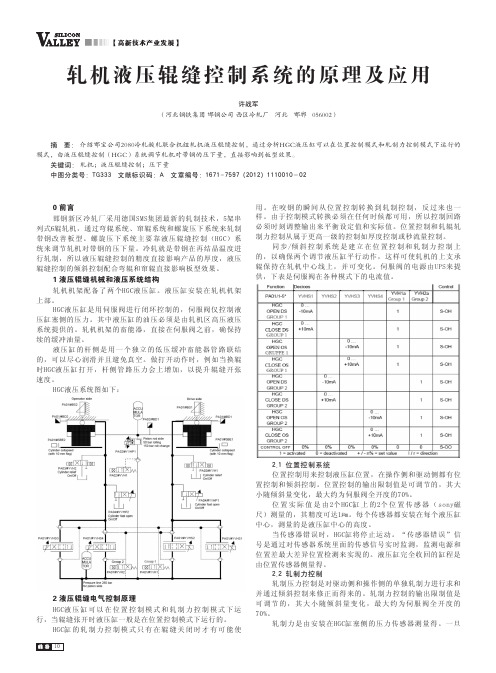
轧机液压辊缝控制系统的原理及应用许战军(河北钢铁集团 邯钢公司 西区冷轧厂 河北 邯郸 056002)摘 要: 介绍邯宝公司2080冷轧酸轧联合机组轧机液压辊缝控制,通过分析HGC液压缸可以在位置控制模式和轧制力控制模式下运行的模式,由液压辊缝控制(HGC)系统调节轧机对带钢的压下量,直接影响到板型效果。
关键词: 轧机;液压辊缝控制;压下量中图分类号:TG333 文献标识码:A 文章编号:1671-7597(2012)1110010-02用。
在咬钢的瞬间从位置控制转换到轧制控制,反过来也一0 前言样。
由于控制模式转换必须在任何时候都可用,所以控制回路邯钢新区冷轧厂采用德国SMS集团最新的轧制技术,5架串必须时刻调整输出来平衡设定值和实际值。
位置控制和轧辊轧列式6辊轧机,通过弯辊系统、窜辊系统和螺旋压下系统来轧制制力控制从属于更高一级的控制如厚度控制或秒流量控制。
带钢改善板型。
螺旋压下系统主要靠液压辊缝控制(HGC)系同步/倾斜控制系统是建立在位置控制和轧制力控制上统来调节轧机对带钢的压下量。
冷轧就是带钢在再结晶温度进的,以确保两个调节液压缸平行动作,这样可使轧机的上支承行轧制,所以液压辊缝控制的精度直接影响产品的厚度,液压辊保持在轧机中心线上,并可变化。
伺服阀的电源由UPS来提辊缝控制的倾斜控制配合弯辊和窜辊直接影响板型效果。
供,下表是伺服阀在各种模式下的电流值。
1 液压辊缝机械和液压系统结构轧机机架配备了两个HGC液压缸。
液压缸安装在轧机机架上部。
HGC液压缸是用伺服阀进行闭环控制的,伺服阀仅控制液压缸塞侧的压力。
其中液压缸的油压必须是由轧机区高压液压系统提供的。
轧机机架的畜能器,直接在伺服阀之前,确保持续的缓冲油量。
液压缸的杆侧是用一个独立的低压缓冲畜能器管路联结的,可以尽心润滑并且避免真空。
做打开动作时,例如当换辊时HGC液压缸打开,杆侧管路压力会上增加,以提升辊缝开张速度。
HGC液压系统图如下:2.1 位置控制系统位置控制用来控制液压缸位置,在操作侧和驱动侧都有位置控制和倾斜控制。
一种铝箔轧机辅助液压系统改造方案
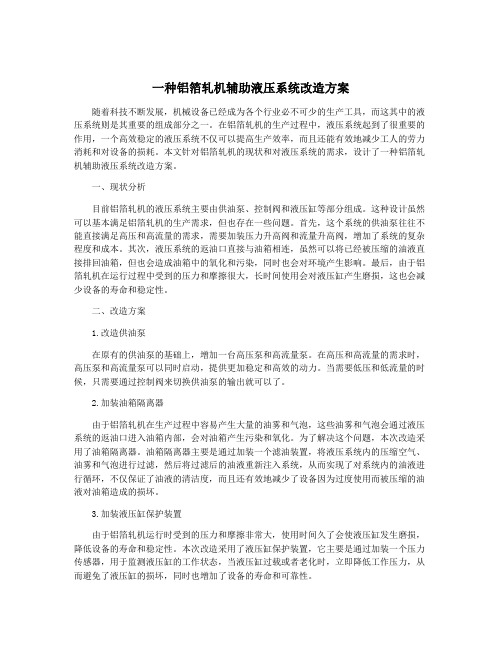
一种铝箔轧机辅助液压系统改造方案随着科技不断发展,机械设备已经成为各个行业必不可少的生产工具,而这其中的液压系统则是其重要的组成部分之一。
在铝箔轧机的生产过程中,液压系统起到了很重要的作用,一个高效稳定的液压系统不仅可以提高生产效率,而且还能有效地减少工人的劳力消耗和对设备的损耗。
本文针对铝箔轧机的现状和对液压系统的需求,设计了一种铝箔轧机辅助液压系统改造方案。
一、现状分析目前铝箔轧机的液压系统主要由供油泵、控制阀和液压缸等部分组成。
这种设计虽然可以基本满足铝箔轧机的生产需求,但也存在一些问题。
首先,这个系统的供油泵往往不能直接满足高压和高流量的需求,需要加装压力升高阀和流量升高阀,增加了系统的复杂程度和成本。
其次,液压系统的返油口直接与油箱相连,虽然可以将已经被压缩的油液直接排回油箱,但也会造成油箱中的氧化和污染,同时也会对环境产生影响。
最后,由于铝箔轧机在运行过程中受到的压力和摩擦很大,长时间使用会对液压缸产生磨损,这也会减少设备的寿命和稳定性。
二、改造方案1.改造供油泵在原有的供油泵的基础上,增加一台高压泵和高流量泵。
在高压和高流量的需求时,高压泵和高流量泵可以同时启动,提供更加稳定和高效的动力。
当需要低压和低流量的时候,只需要通过控制阀来切换供油泵的输出就可以了。
2.加装油箱隔离器由于铝箔轧机在生产过程中容易产生大量的油雾和气泡,这些油雾和气泡会通过液压系统的返油口进入油箱内部,会对油箱产生污染和氧化。
为了解决这个问题,本次改造采用了油箱隔离器。
油箱隔离器主要是通过加装一个滤油装置,将液压系统内的压缩空气、油雾和气泡进行过滤,然后将过滤后的油液重新注入系统,从而实现了对系统内的油液进行循环,不仅保证了油液的清洁度,而且还有效地减少了设备因为过度使用而被压缩的油液对油箱造成的损坏。
3.加装液压缸保护装置由于铝箔轧机运行时受到的压力和摩擦非常大,使用时间久了会使液压缸发生磨损,降低设备的寿命和稳定性。
一种铝箔轧机辅助液压系统改造方案

一种铝箔轧机辅助液压系统改造方案铝箔轧机在生产中起到了至关重要的作用,而辅助液压系统作为铝箔轧机的重要组成部分,直接影响了轧机的运行效率和产品质量。
随着技术的不断进步和市场需求的不断变化,原有的辅助液压系统可能已经无法满足现代化生产的需求,因此需要进行改造和升级。
本文将针对铝箔轧机辅助液压系统的现状进行分析,提出一种改造方案,并对改造后的系统进行详细介绍。
一、现状分析1.原辅助液压系统存在的问题(1)性能跟不上需求:随着铝箔轧机的不断升级,对辅助液压系统的性能要求也越来越高,原系统的压力、流量等性能已经无法满足现代化生产的需求。
(2)能效比低:原辅助液压系统存在能耗较大的问题,能效比低下,不符合节能环保的要求。
(3)维护困难:原辅助液压系统存在维护难度大、易损件多等问题,增加了设备的故障率和维护成本。
2.改造必要性针对以上问题,对铝箔轧机辅助液压系统进行改造具有重要的意义。
改造后的系统将能够提升设备性能,降低能耗,减少维护成本,提高生产效率和产品质量,符合企业的可持续发展战略和市场需求。
二、改造方案1.选用高性能液压元件为了满足现代化生产的需要,我们将选用高性能的液压元件进行替换。
包括高压柱塞泵、液压缸和阀组等。
这些元件具有更高的压力、流量和稳定性,能够满足辅助液压系统的工作需求。
2.增加节能控制系统在系统中增加节能控制系统,可以根据实际需要自动调节液压系统的工作状态,使系统在不同工况下能够达到最佳的工作效果,并有效降低能耗。
3.改进润滑系统通过改进润滑系统,可以提高液压元件的工作寿命,减少摩擦损耗,降低设备的维护成本,同时也有利于减少液压系统的能耗。
4.优化管路设计通过优化管路设计,减少管路阻力,提高系统的响应速度和精度,提升设备的生产效率和产品质量。
5.安全保护系统在改造后的辅助液压系统中增加安全保护系统,包括液压系统过载保护、泄漏报警等功能,确保设备在安全可靠的工作状态。
三、改造后的效果1.性能提升:通过改造后的辅助液压系统,设备的性能得到了大幅提升,包括压力、流量、响应速度等方面都有了明显的改善。
辊压机液压系统工作原理

两路流量调节阀18.2
三位四通阀Y2得电液压油断路
三位四通阀Y4得电 三位四通阀Y6得电
单向过滤器5
油箱
5、开辊 泵
压力过流器
两位三通阀
止回阀组27
退回缸46.1 退回缸46.2 退回缸46.3 退回缸46.4
回油: 充压缸45.1 充压缸45.2 充压缸45.3 充压缸45.4
两路流量调节阀18.1 液压开启单向阀50.1 两路流量调节阀18.2 液压开启单向阀50.2
超过180bar限压阀工作
单向节流阀15.1 单向节流阀15.2
三位四通阀 限压阀13 三位四通阀
两路流量调 三位四通阀Y2得电液压油断路 两路流量调
左边氮气储能器 右边氮气储能器
4、泄压
泵
压力过滤器 12
(所以在卸压
三位四通阀 限压阀13 三位四通阀
回油: 左边氮气储能器
两路流量调节阀18.1
右边氮气储能器
三位四通阀Y11得电 三位四通阀Y13得电
开启式单向阀61.1 开启式单向阀61.2
球阀63.2 球阀63.4
液压油缸64.1 液压油缸64.2
单向过滤器5 油箱
附:辊压机润
润滑油桶 测油位装置(低报器)
压缩空气 闸阀8.2 空气过滤器 减压阀 油污器 节流阀8.5 电磁阀8.6
气泵
油脂过滤器8.7
三位四通阀Y4得电 限压阀36(0.5-2bar)
三位四通阀Y6得电
单向过滤器5 油箱
二、开关滑
1、关滑阀 泵
压力过滤器 12
单向节流阀60.1 单向节流阀60.2
三位四通阀Y1பைடு நூலகம்得电 三位四通阀Y12得电
回油: 液压油缸64.1 球阀63.2 开启式单向阀61.1 液压油缸64.2 球阀63.4 开启式单向阀61.2
铝箔轧机的工作原理与日常维护
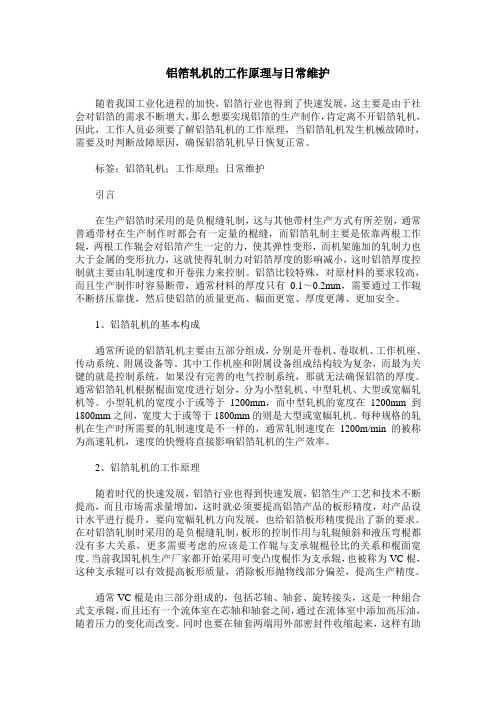
铝箔轧机的工作原理与日常维护随着我国工业化进程的加快,铝箔行业也得到了快速发展,这主要是由于社会对铝箔的需求不断增大,那么想要实现铝箔的生产制作,肯定离不开铝箔轧机,因此,工作人员必须要了解铝箔轧机的工作原理,当铝箔轧机发生机械故障时,需要及时判断故障原因,确保铝箔轧机早日恢复正常。
标签:铝箔轧机;工作原理;日常维护引言在生产铝箔时采用的是负棍缝轧制,这与其他带材生产方式有所差别,通常普通带材在生产制作时都会有一定量的棍缝,而铝箔轧制主要是依靠两根工作辊,两根工作辊会对铝箔产生一定的力,使其弹性变形,而机架施加的轧制力也大于金属的变形抗力,这就使得轧制力对铝箔厚度的影响减小,这时铝箔厚度控制就主要由轧制速度和开卷张力来控制。
铝箔比较特殊,对原材料的要求较高,而且生产制作时容易断带,通常材料的厚度只有0.1~0.2mm,需要通过工作辊不断挤压靠拢,然后使铝箔的质量更高、幅面更宽、厚度更薄、更加安全。
1、铝箔轧机的基本构成通常所说的铝箔轧机主要由五部分组成,分别是开卷机、卷取机、工作机座、传动系统、附属设备等。
其中工作机座和附属设备组成结构较为复杂,而最为关键的就是控制系统,如果没有完善的电气控制系统,那就无法确保铝箔的厚度。
通常铝箔轧机根据棍面宽度进行划分,分为小型轧机、中型轧机、大型或宽幅轧机等。
小型轧机的宽度小于或等于1200mm,而中型轧机的宽度在1200mm到1800mm之间,宽度大于或等于1800mm的则是大型或宽幅轧机。
每种规格的轧机在生产时所需要的轧制速度是不一样的,通常轧制速度在1200m/min的被称为高速轧机,速度的快慢将直接影响铝箔轧机的生产效率。
2、铝箔轧机的工作原理随着时代的快速发展,铝箔行业也得到快速发展,铝箔生产工艺和技术不断提高,而且市场需求量增加,这时就必须要提高铝箔产品的板形精度,对产品设计水平进行提升,要向宽幅轧机方向发展,也给铝箔板形精度提出了新的要求。
在对铝箔轧制时采用的是负棍缝轧制,板形的控制作用与轧辊倾斜和液压弯棍都没有多大关系,更多需要考虑的应该是工作辊与支承辊棍径比的关系和棍面宽度。
- 1、下载文档前请自行甄别文档内容的完整性,平台不提供额外的编辑、内容补充、找答案等附加服务。
- 2、"仅部分预览"的文档,不可在线预览部分如存在完整性等问题,可反馈申请退款(可完整预览的文档不适用该条件!)。
- 3、如文档侵犯您的权益,请联系客服反馈,我们会尽快为您处理(人工客服工作时间:9:00-18:30)。
1700铝箔轧机弯辊液压系统工作原理分析黄晓华(中铝公司西北铝加工厂,甘肃定西748111)【摘要】本文单就弯辊系统的工作及控制原理进行分析,以便于更好的使用及维护好该设备,充分发挥设备的技术性能优势。
【关键词】弯辊力弯辊缸交界力1700铝箔轧粗中轧机和精轧机是我厂从奥钢联-克莱西姆公司引进的具有当代世界先进水平的轧机。
该轧机采用了很多先进的控制技术.本文单就弯辊系统的工作及控制原理进行分析,以便于更好的使用及维护好该设备,充分发挥设备的技术性能优势。
1弯辊力的作用安装在轧机机架牌坊上的弯辊缸用于通过轧机轴承箱给轧辊施加径向的外力。
正弯辊所施加的力使上下工作分离;负弯缸所施加的力使上工作辊和上支承分离、下工作辊和下支承辊分离,负弯力使上下工作辊轴承箱靠拢。
加到工作两端的弯辊力起到使工作辊弯曲的作用,从而控制带材的平整度。
在该轧机上正弯缸和负弯缸同时加力,实际的轧辊弯曲取决于正弯力和负弯力的净力即净弯辊力,净弯辊力作用在带材板形上弯辊力的改变是均匀的和近似平行的,因而,轧辊液压缸常被用于控制材料误差的均匀性。
弯辊缸的弯辊力取决缸中油压与无杆腔面积的乘积再乘以缸的数量。
在该系统中,为了实现净弯力,正负弯缸采用两套独立的液压回路,由一套油泵供油,各自采用单独的电液伺服阀、液压缸及传感器。
单独的伺服阀及压力传感器用于各自弯辊缸中压力的闭环、开环的控制及显示。
为了实现净弯力,控制系统必须能单独控制正弯和负弯压力。
通过单独的伺服控制,正负弯缸由单独的伺服阀在任何给定的时间供给压力油,通过各自压力传感器控制缸中的油压。
该设计的优点是进出正负弯缸的油互不影响,从提高了弯辊控制的高稳定性(特别是零位附近)、高响应、无冲击等高性能。
2弯辊控制原理及目的在该轧机上,弯辊伺服阀能用开环和闭环两种方式控制:(1)开环。
用于直接设置轧辊弯辊伺服阀给弯辊缸一个固定输入输出流量的情况,使正常情况下正弯油缸达到设置点的最大压力,以确保轧机急停时,正负力达到设置的最大值,使急停时上下工作辊快速分离。
(2)闭环。
系统内部所有弯辊性能将以要求的净弯辊力的形式表达出来。
带材上力的分配和对平直度的影响主要是净弯辊力影响的,正负弯力的控制被单独的闭环控制器支持,每一个控制器的设置必须从净弯辊力的效果来计算,从而达到设置的净弯力,每一个控制器将测量弯辊压力,从测量到的弯辊压力计算相关缸的弯辊力。
为了得到油缸压力的精确测量值,系统含有在传感器传入信号中加入偏移的程序,以确保油缸排空时压力测量值是零。
弯辊力对轧机上工作轧辊之间的力及对作用在带材上力和工作辊与支承辊之间的力也有影响,控制程序从测量的弯辊力预测这些影响之间的数量,并结合测量到的载荷缸的力确定作用在带材上的力及工作辊和支撑辊之间的临界力,该计算由载荷控制程序负责。
在较低的轧制力下,弯辊力是跟轧制力成比例关系,作用在带材上的轧制力主要由负弯缸供给,因而在轧辊上的载荷缸的力和潜在的轧辊交界力的危险性降低。
当轧机趋于停止时,交界力可使两辊之间的摩擦力保持一定的值,特别是载荷缸在位置或辊逢控制方式下,从而保证轧辊不擦划伤。
实际交界力取决于轧辊载荷缸的力和轧辊弯辊力。
通过增加压上油缸力可以增加交界力,增加净弯辊力也将使轧辊交界力增加。
减少净弯辊力,将导致交界力减小。
该作用能将交界力维持在确保辊系的安全水平上。
下述2种情况可使弯辊控制器处于开环状态。
(1)如果交界力降到一个可接受的水平上,防止轧辊弯辊进一步减小。
(2)弯辊力的值保证交界力是安全值的上限,弯辊力可达到足够产生轧辊开辊缝时的交界力。
很显然,状态1将影响AFC控制带材平直度的能力,状态2参考弯辊预置能潜在引起弯辊力过大变化而导致带材断裂,必须采取措施防止交界力降到一个必须的水平上。
状态1将用于防止弯辊推动交界力降低,但在轧制期间将限制平直度控制系统修正平直度误差的能力而导致带材平直度恶化,增加带材断裂的概率,因而,弯辊提供将限制保护交界力,而用轧辊载荷力以厚度控制为代价积极控制保持交界力。
交界力的测量在轧辊控制应用程序上计算和监视,当交界力较低或开辊缝时,将应用预置弯辊查询。
预置弯辊限制。
预置弯辊的使用是为偶然的开辊缝或交界力太低和实际需要而设计。
预置弯辊在下面几种情况下选择:(1)标准模式。
标准模式在轧辊辊缝检测的基础上选择,独立的预置弯辊可以在开辊缝和不开辊缝的情况下使用。
(2)交界力低。
如果测得的交界力在最小设定值下,将选择预置弯辊,这个条件通过轧机载荷控制程序确定。
(3)开尾。
在轧机上带材能以一个速度开尾,这时必须立即选择预置弯辊。
开尾保证带材尾部通过轧辊而不会立即制动。
(4)急停。
由于急停时减速率过大,设置一个预知弯辊确保辊和工作辊不发生滑动。
(5)换辊。
在换辊模式下,不用调整弯辊值而设置为最大弯辊即伺服阀开环。
预置值仅仅为了确保最小交界力达到。
如交界力比使用名义值大,名义值将被取代。
弯辊预置参考值的产生。
在程序处理上,弯辊参考设置达到适应正在轧制的产品的辊逢形状。
在该轧机上弯辊了结合载荷产生的力,在辊逢横截面上一个及时调整从而保证带材平整度的力。
在该设备中,系统支持三个基本的弯辊目标设置:(1)平直度控制初始弯辊值。
平直度控制程序包括了基本的数值选择模型,初始弯辊值是基于从相联系的处理模型预测。
(2)MSU弯辊值。
在这个情况下,初始弯辊值将与产品的轧制表相一致。
因轧制表是固定的,未考虑轧制条件,所以MSU弯辊值是不够精确的。
(3)缺省的初始弯辊值。
基于初始值的模型或MSU缺席。
弯辊程序支持它自己的初始值,意味着它留下轧制最后道次的弯辊值。
故弯辊参考必须支持设备参考值在轧制期间动态的改变。
操作者能修订该参数值,AFC程序将在轧制期间调整基于预测的平整度值误差。
由于弯辊参考值跟正在轧制的产品相适应,它作为轧制模式或弯辊的参考值,在卷材尾部将编制弯辊的缺省值。
轧制模式不必使用所有轧制条件,程序必须支持以下几个参考值:(1)弯辊集成块的补偿。
(2)轧机弹性测量。
(3)预置弯辊值。
轧制模式净弯辊值是结合初始弯辊值跟操作者对望的修正和AFC弯辊修正计算得来的。
弯辊力对带材上的力的影响:由于弯辊对作用在带材上的力有影响,要保证加到带材上的力的恒定。
由于对弯辊参考值可以进行补偿,载荷测量的力仅在弯辊参考改变时变化。
因此附加的测量带材力的影响程序提前计算弯辊参考值对带材力的影响。
AFC程序自动补偿通过AFC直接修正、调整弯辊缸的值。
在这种情况下,弯辊对带材力影响不包括AFC修正对带材力的影响。
由于这个原因,在确定弯辊参考对带材力的影响之前,累计的AFC 弯辊修正必须从实际弯辊参考中被减去。
对该设备正负弯辊独立的液压回路,其控制策略安排如下:净弯参考从最小增加到最大时,正弯值增加;净弯参考从最大减到最小时,负弯增加。
净弯参考的任何改变将导致正弯和负弯的改变。
参考通过“O”的净弯参考,可导出设置点的方法作为分析参考,该算法中包括了在存储器设置维持最小力的规定。
正常情况下,实际弯辊输出将被限制到系统供给压力和各自尺寸有关的最大弯辊力。
最大参考是最大正弯力、最小参考是最大负弯力取反。
也可以通过程序设计而在正弯和负弯缸中保持最小弯辊力,以保证轴承箱跟弯辊柱塞持续接触,最小力由工程师进行确定,以有效克服所有弯辊缸的摩擦。
在该设备上,每个弯辊伺服阀能在开环或闭环方式下工作。
为保证伺服阀输出跟随输入的线性关系,要通过控制程序对伺服阀在不同的工况下对伺服阀进行补偿。
另外控制系统还有对伺服阀进行偏移补偿、输出限制及辊对带材力影响的补偿,弯辊对带材和载荷缸力变化的补偿。
偏移补偿能保证伺服阀输入为零时,阀的输出为零;输出限制能防止工作辊快速升起时上支承辊被磕伤。
3结论通过对该设备弯辊控制系统工作原理及的分析,较好的掌握了设计理念,对于正确操作及维护设备起到了积极作用,可有效提高产品轧制性能及保证设备该系统工作在最佳状态,防止轧制过程中意外情况的发生。
(上接第26页)化,混凝土中的碱度降低(pH ≤10)或其他原因导致水、氧等进入混凝土时钢筋将发生如下反应:4Fe (OH )2+2H 2O +O → 24Fe (OH )3生成铁锈的体积比参与反应的铁的体积要大得多,因此产生膨胀,出现裂缝,最终导致混凝土结构破坏。
产生的裂缝常常沿着骨料或钢筋下方,并使保护层剥落。
图3混凝土缩水收缩3桥梁施工中保证混凝土质量及控制裂缝的措施3.1荷载裂缝控制措施首先要分析桥梁随着混凝土施工其结构内力的变化规律,进而在合理的配置纵横向钢筋,以确保结构有足够的抗剪和抗扭钢筋,进而避免桥梁结构的受荷载作用产生的弯曲裂缝、受扭裂缝等。
对于桥梁因横向弯矩引起的纵向裂缝可通过改善结构的横向受力或配置横向预应力钢筋来解决;对于预应力束锚固下的受拉裂缝可通过配置钢筋网来加强。
此外为了确保桥梁结构有足够预压应力,可优先选择预应力损失小的预应力筋[3]。
3.2变形裂缝控制措施对于变形裂缝的控制,首先可选用干缩较小、早期强度较高的硅酸盐或普通硅酸盐水泥,严格控制水泥和掺合料的用量,选用级配良好的砂子和石子。
气温较低时,在混凝土中掺加促凝剂,以加速混凝土的凝结和强度发展。
掺加一定量的纤维,如聚丙烯纤维等。
其次应从材料的选择和施工方案的确定入手,采用“抗”与“放”相结合的方法进行裂缝控制。
其中“抗”是约束,理论上增强对混凝土的约束作用并不能防治裂缝的产生,但能分散裂缝以减小裂缝宽度。
“放”即是减小混凝土收缩应力的累计,释放收缩应力,或者人为引导收缩裂缝在规定位置产生。
特别是要提高混凝土的抗拉强度,降低混凝土的弹性模量和水化热,减少混凝土的收缩。
最后要确保桥梁混凝土某方向裂缝宽度的总和应等于混凝土在该方向的收缩值与约束收缩值之差,混凝土收缩大,约束作用不足或不均匀,裂缝将难以避免[4]。
3.3加强施工质量控制为了避免材料裂化引起的裂缝,可从以下几个方面入手:(1)在桥梁混凝土设计时,应按照相关规范控制裂缝宽度,并使保护层的厚度满足工程需求,不宜过厚,否则会降低构件的有效高度,从而桥梁在受力时,容易加大裂缝宽度。
(2)严格控制混凝土的水灰比、对石子和砂也要进行一定选择,经过试配调整,特别是对砂率、和易性、可泵性绝热温升和坍落度损失等性能指标进行了多次试验,来最终确定混凝土配合比。
(3)加强施工管理和现场的温度监测,及时对出现超过规定指标的部位实行多层保温等技术手段,确保严格按规定的指标进行控制。
4结语总的来说,要做好桥梁砼施工首先要充分审核施工设计图纸,并严格检测原材料及配合比设计;其次要综合考虑温度、材料等多方面的因素,对桥梁砼裂缝成因进行正确分析,并选择科学的处理对策;最后还要做好施工过程的监督和管理,如:施工工序、工作流程是否科学合理,施工工艺是否可以进一步优化等。