轧机压下装置液压系统的优化设计
液压系统的优化设计

液压系统的优化设计随着科技的进步和社会的快速发展,液压系统在各个领域应用越来越广泛,如工业、农业、建筑、航空等。
在这些领域中,液压系统扮演着重要的角色,如汽车制造、飞机制造、船舶制造、建筑机械等需要大量使用液压系统。
因此,液压系统的优化设计显得尤为重要。
一、液压系统的基本原理及构成液压系统是一种利用液体传递能量,并将互不相干的行动组合起来的系统。
液压系统的基本原理是利用液体的压缩性小和容积稳定,通过不同的工作机构来完成某一特定工作的机械装置。
液压系统的构成包括工作部分、执行部分、控制部分和电气部分。
其中,工作部分是指液压泵或发生器、液压马达和液压缸;执行部分是指在液压系统中完成具体工作的机械设备或装置,如液压升降机、液压抓取器等;控制部分是指液压系统中的各种控制装置,如液压阀等;电气部分是指支持液压系统的电气设施,如液压泵电机等。
二、1. 功率密度与效率液压系统的设计中需要考虑功率密度和效率两个方面。
功率密度指的是液压系统单位体积或单位重量所能输出的功率大小。
增加液压系统的功率密度可以提高其工作效率。
效率指的是液压系统的机械工作输出功率与输入功率之比。
在液压系统的设计中应该尽量提高系统的效率,以减少能量损失。
2. 选择合适的组件液压系统的设计中,应该根据不同的工作要求选择合适的组件,如液压泵、液压马达、液压缸和液压阀等。
同时,应注意选择正确的组件配合以确保系统的稳定和可靠性。
例如,液压泵需要与液压马达和液压阀相匹配,才能形成合理的液压系统。
3. 液体选用液压系统液体的选用也是液压系统优化设计的重要因素之一。
液压系统液体应具有压缩性小、稳定粘度、抗氧化性能强、抗腐蚀性好、防爆性能高、热稳定性好等特点,以确保液压系统的可靠性和长寿命。
4. 控制方式确定液压系统的控制方式是液压系统设计中的一个关键问题。
液压系统的控制方式应根据工作条件和要求确定。
例如,对于一些要求精度高、速度快、工作负荷重的工作环境,需要采用闭环控制液压系统,以保证工作的稳定性和可靠性。
液压系统优化设计技术研究

液压系统优化设计技术研究液压系统已经成为现代机械制造业发展的重要组成部分,其广泛应用于工业生产和民生领域。
随着现代科技的不断进步和全球市场竞争的日益激烈,如何提高液压系统的效率和性能已经成为生产制造企业所面临的重要问题。
因此,液压系统优化设计技术的研究和应用已经成为目前液压技术研究方向的重要领域之一。
一、液压系统的基本结构和工作原理液压系统主要由液压泵、液压马达、液压缸、液压阀等组成,其基本工作原理是利用工业油液将电力转换为机械动力,提供机械装置所需的能量。
液压系统在工业生产中应用广泛,如汽车工业、模具加工、航空航天、石油化工、机床制造等行业均离不开液压技术的应用。
二、液压系统优化设计技术的研究意义液压系统在各种不同的应用领域中,需要满足不同的工作条件。
因此,如何优化液压系统的设计,提高其效率和性能已经成为重要的研究课题。
针对这个问题,液压系统优化设计技术应运而生。
液压系统优化设计技术的研究意义在于:1. 提高液压系统的效率,减少能量损失,实现节能环保。
2. 降低生产成本,提高生产效率和生产线的稳定性。
3. 提高产品的质量和可靠性,使产品更加适合市场需求。
三、液压系统的优化设计技术研究内容液压系统优化设计技术研究应包括以下主要内容:1. 变量泵及电液伺服阀控制技术。
电液伺服阀是一种高性能的节流控制元件,其结构也越来越复杂。
通过对电液伺服阀和变量泵的研究,能够实现更加精确的流量和压力控制。
2. 液压系统中的流场分析。
液压系统中的液体流动具有非线性、非稳定性和非静态性,流场分析是液压系统优化设计过程中的一个重要环节。
流场分析可以通过仿真技术来进行,以验证设计方案的可用性和稳定性。
3. 液压系统中的噪声和振动控制。
液压系统中的噪声和振动都会影响到系统的稳定性和工作效率。
因此,如何减少系统中的噪声和振动,提高系统的稳定性和可靠性也是液压系统优化设计的一个重要研究内容。
四、结语液压系统优化设计技术的研究和应用已经成为现代化生产制造企业不可或缺的组成部分。
轧机的液压压下装置

轧机的液压压下装置压下装置是轧机的核心装置,其性能的优良与否决定了带材的质量。
文章阐述了液压压下装置在冷轧机中所起到的重要作用,介绍了该装置在轧机上的安装方式、结构及安装结构的主要优缺点、并讲述了压下装置的控制原理及其在实际项目中的推广应用。
标签:压下油缸;位置传感器;检测装置;位置闭环1 前言近年来,随着经济的发展,我国黑色及有金属薄带材产品、产量迅速增长,而轧机也向高速、大型、连轧、自动化方向发展。
目前,所有的冷轧机的压下装置都采用液压压下这种方式。
液压压下是轧机现代化的突出重要标志之一,它较易适应轧制及操作条件的变化,根据轧制类型和轧制道次程序,如压下轧制或平整轧制,并能给予最佳补偿,并利用轧机刚性可调的特点,对冷轧机采用递降式刚度分配方式,以得到高质量的产品,从而保证带材厚度及平整度,使带材质量最佳,不论是在最硬和最软的条件下都是如此。
同时液压压下具备自动及快速卸荷功能,以防止轧辊及轧辊轴承的过载和损坏,延长轧辊寿命等特点。
液压压下方式虽然有各种各样的方案,但就其压下油缸安放位置来说,分为压下和压上两种结构形式。
2 液压压下油缸安放在轧机机架上部将液压压下油缸安放在轧机机架上部(上支承辊轴承座上面),这种安装方式在一定程度上可以使其免受来自轧机工艺润滑系统的乳化液、轧制油等造成对液压压下油缸污染,但是由于液压压下油缸处在轧机机架上部,轧制时,当需要压下油缸活塞往上运动时,因无外力使其活塞动作,所以在液压压下系统中还需设置压下油缸活塞平衡回路及必要的电气联锁控制,因此增加了液压压下系统设备制造成本。
油缸安装于轧机机架上部时安装、维修不便,由于液压压下油缸处在轧机机架上部,还需增加固定液压压下油缸的悬挂机构。
液压压下油缸维修时,必须先卸掉液压压下油缸的悬挂机构后,才能将液压压下油缸落下,并放在上支承辊轴承座上面拉出,全部工作需要在轧机机架上进行,从而导致更换困难。
因液压压下油缸安装在轧机机架上部,考虑安装、维修等因素,压下油缸阀装置与液压压下油缸多数分开设置,两者之间是靠管道连接,这样就导致管道油液质量转化到压下油缸活塞上当量质量增加,直接影响到系统的动态指标是否满足要求,容易导致轧机刚度降低,系统响应频率降低等不良后果,为了减小这些不良影响,压下油缸阀装置的安放位置及其连接管道受到严格制约。
轧机的液压压下装置
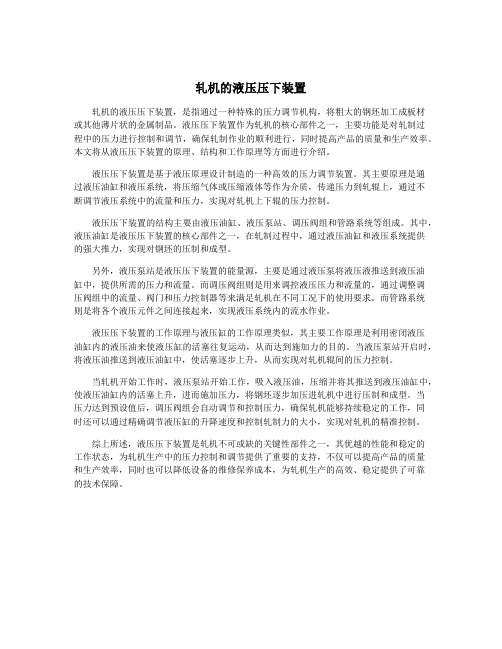
轧机的液压压下装置轧机的液压压下装置,是指通过一种特殊的压力调节机构,将粗大的钢坯加工成板材或其他薄片状的金属制品。
液压压下装置作为轧机的核心部件之一,主要功能是对轧制过程中的压力进行控制和调节,确保轧制作业的顺利进行,同时提高产品的质量和生产效率。
本文将从液压压下装置的原理、结构和工作原理等方面进行介绍。
液压压下装置是基于液压原理设计制造的一种高效的压力调节装置。
其主要原理是通过液压油缸和液压系统,将压缩气体或压缩液体等作为介质,传递压力到轧辊上,通过不断调节液压系统中的流量和压力,实现对轧机上下辊的压力控制。
液压压下装置的结构主要由液压油缸、液压泵站、调压阀组和管路系统等组成。
其中,液压油缸是液压压下装置的核心部件之一,在轧制过程中,通过液压油缸和液压系统提供的强大推力,实现对钢坯的压制和成型。
另外,液压泵站是液压压下装置的能量源,主要是通过液压泵将液压液推送到液压油缸中,提供所需的压力和流量。
而调压阀组则是用来调控液压压力和流量的,通过调整调压阀组中的流量、阀门和压力控制器等来满足轧机在不同工况下的使用要求。
而管路系统则是将各个液压元件之间连接起来,实现液压系统内的流水作业。
液压压下装置的工作原理与液压缸的工作原理类似,其主要工作原理是利用密闭液压油缸内的液压油来使液压缸的活塞往复运动,从而达到施加力的目的。
当液压泵站开启时,将液压油推送到液压油缸中,使活塞逐步上升,从而实现对轧机辊间的压力控制。
当轧机开始工作时,液压泵站开始工作,吸入液压油,压缩并将其推送到液压油缸中,使液压油缸内的活塞上升,进而施加压力,将钢坯逐步加压进轧机中进行压制和成型。
当压力达到预设值后,调压阀组会自动调节和控制压力,确保轧机能够持续稳定的工作,同时还可以通过精确调节液压缸的升降速度和控制轧制力的大小,实现对轧机的精准控制。
综上所述,液压压下装置是轧机不可或缺的关键性部件之一,其优越的性能和稳定的工作状态,为轧机生产中的压力控制和调节提供了重要的支持,不仅可以提高产品的质量和生产效率,同时也可以降低设备的维修保养成本,为轧机生产的高效、稳定提供了可靠的技术保障。
新型液压系统的设计与优化

新型液压系统的设计与优化液压系统在现代工业中扮演着重要的角色,广泛应用于机械、汽车、冶金、航空等领域。
随着科技的不断进步,新型液压系统的设计和优化成为了研究的热点。
本文将从设计需求、原理、优化方法及应用等方面来探讨新型液压系统的发展。
设计需求是液压系统设计的第一步,设计者需要充分了解用户的需求和使用环境,从而确定系统的工作压力、流量和输出功率等参数。
对于大型机械设备,稳定性和可靠性是设计的重点;而对于高速运动的汽车或航空器,系统的灵敏度和响应速度则是主要考虑因素。
因此,设计者需要根据具体应用场景进行针对性的设计。
在原理方面,新型液压系统的设计通常借鉴了现有的液压系统结构和工作原理,但也加入了创新的元素。
例如,引入了可变负载技术来提高系统的能效;采用分布式电控系统实现自动化控制,提高系统的灵活性和精确性。
此外,随着电动技术的发展,电液混合系统和纯电动系统也成为了新的研究方向,既满足了环保要求,又提高了系统的效率。
优化方法是新型液压系统设计的关键环节。
传统液压系统存在能量损失大、噪音高和维护成本高等问题,因此系统的优化设计迫在眉睫。
在流体传动方面,可以采用高效液压元件和流路设计来降低能量损失;在控制方面,采用先进的传感器和自适应控制算法来提高系统的响应速度和稳定性。
同时,模拟仿真技术可以帮助设计者在设计阶段就发现潜在问题,避免在实际生产中出现差错。
在应用方面,新型液压系统已经被广泛应用于各个领域。
在机械制造业中,新型液压系统在大型挖掘机、装载机等重型设备中得到了广泛应用,其高效的能量传输和稳定的工作性能为机械设备的生产力提升做出了重要贡献。
在汽车行业,电液混合系统和纯电动系统已经成为了汽车的发展趋势,提高了汽车的燃油经济性和环保性能。
在航空领域,新型液压系统在飞机的起落架、刹车系统等部位发挥着重要作用,保障了航空器的安全性和可靠性。
总之,新型液压系统的设计和优化是工业发展不可或缺的一部分。
设计者需要充分了解用户需求,灵活运用现有技术和创新技术,同时采用合适的优化方法来提高系统性能。
连轧管生产线毛管移送装置液压系统的优化设计

o PTI I M ZATI oN DESI GN ON HYDRAULI S C YS TEM F o H o LLo W BLo 压 TRANS o FER DEVI CE N PE I PI RoLLI NG PR oDUCTI oN NE LI
W e n n Z a gJ aja nXimi h n u nu n
( E I n ier ga dR sa hC roa o , atu0 4 1 ,N i n g ) R SE g ei n eer op rt n B o 1 0 0 e B n n c i o me gu
Ab tac Thi a r i r d c d t e o i ie e in o d a lc cr u tf rh lo b o m o e i sr t s p pe nto u e h pt z d d sg ft hy r u i ic i o o lw l o c nv yng m he
mi fs l p p im ee . Th scc n e to c s t n e r t h die to a y r u i o ia l o ma l i e d a t r l eba i o c p fwhih wa oi t g ae t ebi r c in lh d a lc lg c l v l e,t ote v le a y r u i o to h c ae i t n o to a v lc av hr t av nd h d a lc c n r lc e k v l n o o e c n r lv le b o k whih c n b o n ce l c a ec n e td t h ic i o u p  ̄ c l e O a o r p a e t x si g c n e i n lcr u t T e de i n wa i l o t e cr u t fs p o yi nd rS st e l c he e itn o v nt a ic i. h sg s smp e o a d ce r a to y r a ie he s e d c n r lo he s p  ̄ c l e o a o d t e r v ri g i a t n l a , nd no nl e lz d t p e o to ft up o y i rt v i h e e sn mp c , nd b tas i p i e h o fg r to u lo sm l i d t e c n u a in,a d g e ty s v d t e c sso he c n r lee e t. f i n r al a e h o t ft o to lm n s K e o ds p nc i g ma hi y w r u h n c ne;c n r lv l e b o k;o tm ie e i n o to av l c p i z d d sg
液压传动系统的优化设计及控制
液压传动系统的优化设计及控制液压传动系统是机械传动领域中重要的一部分,广泛应用于航空、航天、军事、船舶、工程机械等众多领域。
其优点在于能够实现大功率、精密控制、高可靠性和高效率等特点。
但同时,液压传动系统也面临着无法避免的问题,如流量变化、压降损失、泄漏、振动和噪音等。
因此如何进行优化设计及控制是解决液压传动系统问题的关键。
1. 控制策略传统的液压传动系统控制基于“开环控制”方法,即通过调节活塞直径、行程和泵的转速来控制液压传动系统的输出功率。
这种方法存在着许多问题,如对系统瞬态响应的振荡、功率损失等影响。
因此,目前研究液压传动系统控制的主要方法是“闭环控制”,即通过流量、压力和位置等传感器反馈的实时信息,调节阀门和泵的控制信号来精确控制系统的输出功率。
这种方法可以提高控制精度和响应速度,降低系统波动和噪音,具有非常广阔的应用前景。
2. 优化设计为了进一步提高液压传动系统的性能和可靠性,需要进行系统的优化设计。
液压传动系统的优化设计主要包括以下几个方面:(1)活塞和缸体设计在活塞和缸体设计上,一般需考虑液压传动系统的工作压力和额定负载。
活塞和缸体的直径和壁厚是影响系统输出功率和承载能力的重要因素。
为了最大限度地提高系统的工作效率,还需考虑缸径的优化设计,即确定合适的缸长和缸径比。
(2)泵和阀门设计泵和阀门是液压传动系统中最重要的组件,对系统的工作性能和品质起着决定作用。
设计泵和阀门时,需考虑它们的设计压力和流量,确保它们能够适应系统的工作条件。
同时,在设计泵和阀门时,还需关注它们的可靠性和维修性。
(3)油液设计油液是液压传动系统中必不可少的组成部分,决定着系统的工作性能和寿命。
油液的设计需要考虑到其粘度、密度、燃点和氧化标准等因素,以适应系统的工作条件。
同时还要关注油液的污染、水分和酸值等因素,保证油液不会对系统造成损害。
3. 优化控制液压传动系统的优化控制主要包括以下几个方面:(1)PID控制PID控制是液压传动系统中最重要的一种优化控制方法,它通过不断调节传感器反馈的信号和控制器输出的控制信号,实现系统的动态控制和稳态控制,提高系统的控制精度和响应速度。
液压系统的优化设计
液压系统的优化设计液压系统在现代工程中扮演着重要角色,广泛应用于机械设备、航空、汽车、工程机械等行业。
优化液压系统设计可以提高系统的效率、可靠性和经济性。
本文将探讨液压系统优化设计的一些关键要素和方法。
1. 设备选型在液压系统的设计中,合理的设备选型是关键的一步。
选择合适的液压泵、液压马达、液压缸等设备,能够提高系统的工作效率。
关注设备的额定工作压力、流量、容量以及质量和可靠性。
同时,对于长时间工作的设备,寿命和维护成本也是需要考虑的因素。
2. 系统布局液压系统的布局对系统的效率和性能有重要影响。
合理的布局可以提高系统的能量利用率、减少能量损失和压力损失。
布局时应考虑系统的整体结构和关键组件的相对位置,减少管道长度和管道弯曲,确保流体的快速流动和正常运行。
3. 控制阀选型液压系统中的控制阀起着关键作用,决定了液压系统的动作和性能。
选用合适的控制阀能够实现系统的自动化、高效率和精确控制。
在选型时应注意控制阀的类型,如单向阀、节流阀、溢流阀等,以及阀的额定工作压力、流量和响应速度等参数。
4. 液压油选择液压油是液压系统中传递能量和润滑的介质,对系统的正常运行起着关键作用。
优化液压油的选择可以提高系统的效率和寿命。
选用合适的液压油,考虑其黏度、粘度指数、抗氧化性、抗磨性和防腐性等性能。
此外,定期检查和更换液压油是保障系统稳定性的重要操作。
5. 噪音与振动控制液压系统在工作过程中常常伴随着噪音和振动。
优化设计可以减少系统的噪音和振动,提高设备的工作环境和可靠性。
通过合理的管道布局、隔振措施和吸声材料的使用,可以降低噪音和振动对周围环境和操作人员的影响。
6. 故障诊断与维护液压系统的故障诊断与维护是优化设计的重要环节。
采用先进的故障诊断技术和设备,及时发现和排除系统中的故障,可以减少停机时间和损失。
定期维护和保养液压系统,对系统的各个组件进行检查、清洁和润滑,延长系统的使用寿命。
7. 系统集成与自动化随着科技的发展,液压系统的集成与自动化正在成为趋势。
轧机升降台液压系统设计与计算
轧机升降台液压系统设计与计算摘要:本文论述了轧机升降台液压系统的设计,并对其上升和下降工况时的流量和压力等参数进行了分析和计算。
关键词:升降台平衡缸升降缸1 前言大型轧机升降台,目前多采用传统的“垂锤平衡,曲柄连杆机构驱动”的结构型式。
此类升降台因其重锤惯性大,相应的机械传动、紧固装置容易受损,故设备故障多、维修费用高、管理工作量大、年停机时间长。
研究新型的液压升降台取代传统的结构型式已成为一种发展趋势。
2 升降台液压系统及其工作原理图1为液压升降台工作示意图,图中F G为升降台及钢坯重力,F s为升降缸柱塞推力,F p 为平衡缸柱塞推力。
图1 轧机液压升降台工作示意图图2为升降台液压系统原理图,该系统由油源、平衡回路、升降回路和卸荷回路组成。
当升降台处于水平位置时,有固定支承承载升降台和钢坯的自重,系统进入预备工作状态时,起动油泵电机,油泵15输出的压力油经单向阀5进入平衡蓄能器8,当其压力达到p p1=x c F G/x p 时,电接点压力表12发讯,IDT得电,锥阀1开启,液压油经锥阀1进入升降缸7,升降缸的压力不断上升,升降缸与平衡缸一起推动升降台上升,在升降台上升过程中,平衡回路的压力p p由大到小变化,而升降回路的压力p s则由小到大变化(见图3),当升降台上升到设定位置时,由旋转编码器检测并发讯使3DT得电,锥阀3开启,泵对蓄能器9充液,当压力达到p s2+0.3MPa后,由电接点压力表13发讯,使IDT失电,锥阀1关闭,接着使4DT得电,锥阀4开启,泵卸荷,蓄能器9实施对升降回路的补油功能,防止升降台因升降回路的泄漏而下降,保持在上止点位置。
平衡蓄能器8也提供必需的先导阀控制油源,以保证系统工作的可靠性和连续性。
当升降台下降时,3DT失电,锥阀3关闭,接着2DT得电,锥阀2开启,升降缸的油液经锥阀2和液控节流阀J回油箱,升降台在自重力矩x c F G和平衡缸、升降缸的上托力矩x p A p p p和x s A s p s的共同作用下下降,在下降过程中,平衡回路的压力p p由小变大(平衡缸的油液此时被压入平衡蓄能器8中),升降回路的压力p s则由大变小,最后变为零。
液压系统的优化设计与工程应用
液压系统的优化设计与工程应用随着现代机械制造业的持续发展和技术的不断进步,液压系统在机械制造、工程建设等领域得到了广泛应用。
液压系统的作用在于将液体能量转换成机械能,实现某一特定运动或作用。
液压系统的优化设计和工程应用,可以提高机械性能、减少机械故障、降低生产成本等,具有重要的意义和价值。
一、液压系统的基本原理和构成液压系统是由液压源、液压执行器、液压控制元件、液压传动装置和液压工作介质五部分组成。
液压源是关键的能源,它通常由泵、发动机或电动机、气压机等提供动力。
液压执行器是实现工作的元件,可分为液压缸和液压马达两类。
液压控制元件是对液压系统进行液压功率控制或流量/压力控制的元件,例如:伺服阀、节流阀、溢流阀、比例阀、多路换向阀等。
液压传动装置则负责将能量传递给执行器。
液压工作介质则是液压系统中传递动力的介质,如机油、水等。
在液压系统的运行过程中,液体在各个元件之间流动,通过一定的流道和元件来实现机械能的转化和传递。
液压系统的优化设计和工程应用,则在于提高系统的效率、稳定性和可靠性,实现最优化的液压功率控制和流量/压力控制。
二、液压系统的优化设计液压系统的优化设计,主要包括液压功率控制和流量/压力控制。
对于液压功率控制,产品应通过最小化泵源流量、最小化回油压力、降低油管管路损失等方面来提高系统效率。
对于流量/压力控制,优化设计应通过使用中点消耗控制、最小间隙节流和最小回程节流等控制方法,来消除液压波动和闪烁,并提高系统的稳定性和可靠性。
液压波动和闪烁是液压系统常见的问题,它们的存在会导致机械设备的噪音和振动加剧,降低机械性能和工作效率。
中点消耗控制是一种常见的消除液压波动和闪烁的方法,它通过增加油路的缓冲容量,使得压力波动和流量波动能够被吸收和缓冲。
最小间隙节流和最小回程节流这两种节流方法,也可以有效地减少液压波动和闪烁,同时还能提高系统的传动效率和工作性能。
三、液压系统的工程应用液压系统的工程应用广泛,涉及船舶、航空、机械制造、建筑工程等多个领域。