650五机架冷连轧机液压压上系统设计
四辊轧机液压压下装置液压系统设计
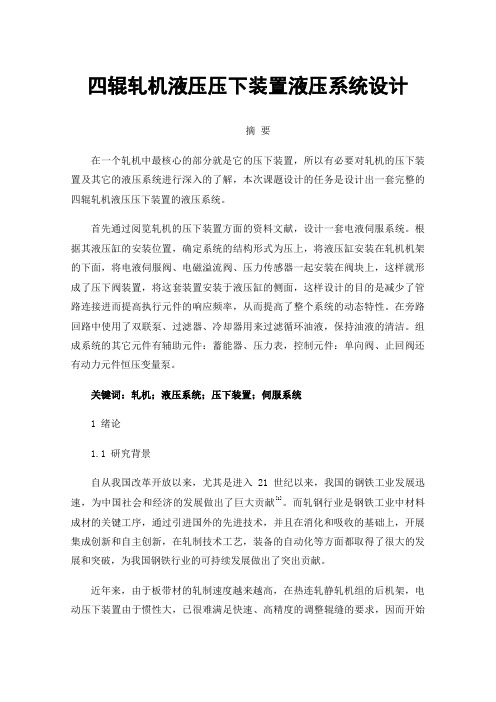
四辊轧机液压压下装置液压系统设计摘要在一个轧机中最核心的部分就是它的压下装置,所以有必要对轧机的压下装置及其它的液压系统进行深入的了解,本次课题设计的任务是设计出一套完整的四辊轧机液压压下装置的液压系统。
首先通过阅览轧机的压下装置方面的资料文献,设计一套电液伺服系统。
根据其液压缸的安装位置,确定系统的结构形式为压上,将液压缸安装在轧机机架的下面,将电液伺服阀、电磁溢流阀、压力传感器一起安装在阀块上,这样就形成了压下阀装置,将这套装置安装于液压缸的侧面,这样设计的目的是减少了管路连接进而提高执行元件的响应频率,从而提高了整个系统的动态特性。
在旁路回路中使用了双联泵、过滤器、冷却器用来过滤循环油液,保持油液的清洁。
组成系统的其它元件有辅助元件:蓄能器、压力表,控制元件:单向阀、止回阀还有动力元件恒压变量泵。
关键词:轧机;液压系统;压下装置;伺服系统1 绪论1.1 研究背景自从我国改革开放以来,尤其是进入21世纪以来,我国的钢铁工业发展迅速,为中国社会和经济的发展做出了巨大贡献[1]。
而轧钢行业是钢铁工业中材料成材的关键工序,通过引进国外的先进技术,并且在消化和吸收的基础上,开展集成创新和自主创新,在轧制技术工艺,装备的自动化等方面都取得了很大的发展和突破,为我国钢铁行业的可持续发展做出了突出贡献。
近年来,由于板带材的轧制速度越来越高,在热连轧静轧机组的后机架,电动压下装置由于惯性大,已很难满足快速、高精度的调整辊缝的要求,因而开始采用电动压下与液压压下相结合的压下方式[2]。
在现代化的冷连轧机组中,几乎已全部采用液压压下装置。
1.3 本课题主要研究内容本课题主要是设计一套四辊轧机压下装置的液压系统,以前冷轧机的压下装置是靠大功率电动机带动牌坊顶部的蜗轮蜗杆和压下螺丝来实现的,自从采用液压技术后,轧制速度提高了10倍以上,精度也大大提高了。
采用液压压下系统的轧机一旦发现误差,能以极短的时间调整辊缝。
所以有必要对轧机液压压下装置进行研究,具体内容如下:(1)首先查阅轧机压下装置液压系统方面的相关资料,了解压下装置的工作原理并对组成压下装置液压系统中的电液伺服阀有一定了解,伺服阀是液压系统中最关键的元件,是液压系统同电气系统的连接元件。
上料机液压系统的设计

上料机液压系统的设计液压系统在上料机上起到了关键作用,它用于实现上料机的升降、倾斜、移动等功能,确保上料机的正常运行。
因此,液压系统的设计对于上料机的性能和稳定性有着重要影响。
本文将从液压系统的组成、工作原理、设计要点等方面展开讨论。
液压系统主要由液压泵、液压马达、液压缸、液压阀、油箱等部件组成。
液压泵负责将机械能转化为液压能,将液压油从油箱中抽出并通过管道输送到液压缸,从而推动上料机的升降、倾斜、移动等动作。
液压马达则是将液压能转化为机械能,将液压油转化为机械运动。
液压阀用于控制液压油的流量和压力,以实现对上料机各项功能的精确控制。
液压系统的工作原理是利用液体的压力传递力量。
当液压泵启动后,液压油被泵入油缸内,形成一定的压力。
通过调整液压阀的开闭情况,控制液压油的流动和压力,从而推动上料机的运动。
当液压油进入液压缸时,液压缸的活塞受到液压力的作用,从而实现对上料机的升降、倾斜等动作。
液压系统的设计要点包括以下几个方面:1.选用合适的液压元件:液压元件的选择对液压系统的性能和稳定性至关重要。
必须选择具有良好性能和可靠性的液压泵、液压马达、液压缸和液压阀等元件,以确保系统的正常运行。
2.合理设计液压管路:液压管路的设计应符合液压系统的工作要求,保证液压油的流动和压力传递的稳定性。
管路的布置应尽量简洁,避免回流、压力损失和漏油等问题。
同时,在设计管路时要考虑到液压油的温度变化和噪声控制等因素。
3.控制方案的设计:液压系统的控制方案应根据上料机的功能需求进行设计。
要考虑到各项功能的协调运行,确保动作的平稳和精确。
同时,在设计控制方案时还需要考虑到用户的使用习惯和安全需求,提供便利和可靠的操作方式。
4.液压系统的过滤和冷却:液压油的过滤和冷却是保持液压系统正常运行的重要环节。
应该在系统中设置合适的过滤器和冷却器,及时清除油液中的杂质和热量,确保系统的稳定性和寿命。
5.液压系统的维护和保养:液压系统的维护和保养工作是系统正常运行的前提。
1450mm冷轧机液压压下(或压上)简介
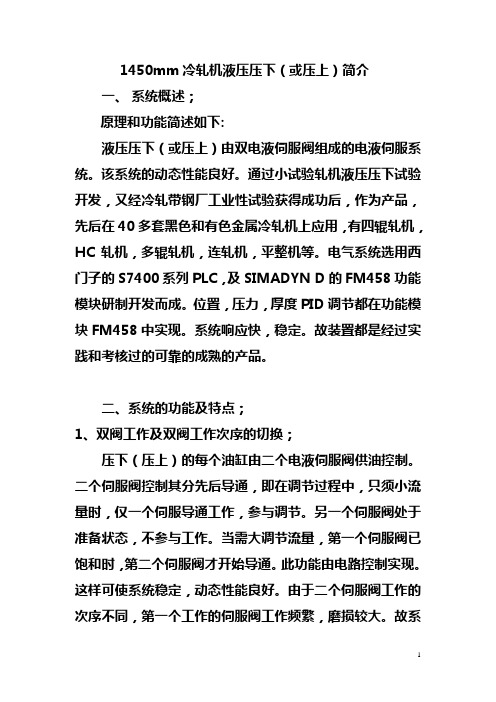
1450mm冷轧机液压压下(或压上)简介一、系统概述;原理和功能简述如下:液压压下(或压上)由双电液伺服阀组成的电液伺服系统。
该系统的动态性能良好。
通过小试验轧机液压压下试验开发,又经冷轧带钢厂工业性试验获得成功后,作为产品,先后在40多套黑色和有色金属冷轧机上应用,有四辊轧机,HC轧机,多辊轧机,连轧机,平整机等。
电气系统选用西门子的S7400系列PLC,及SIMADYN D的FM458功能模块研制开发而成。
位置,压力,厚度PID调节都在功能模块FM458中实现。
系统响应快,稳定。
故装置都是经过实践和考核过的可靠的成熟的产品。
二、系统的功能及特点;1、双阀工作及双阀工作次序的切换;压下(压上)的每个油缸由二个电液伺服阀供油控制。
二个伺服阀控制其分先后导通,即在调节过程中,只须小流量时,仅一个伺服导通工作,参与调节。
另一个伺服阀处于准备状态,不参与工作。
当需大调节流量,第一个伺服阀已饱和时,第二个伺服阀才开始导通。
此功能由电路控制实现。
这样可使系统稳定,动态性能良好。
由于二个伺服阀工作的次序不同,第一个工作的伺服阀工作频繁,磨损较大。
故系统设有工作次序选择切换开关,控制二个阀的磨损程度均衡,提高伺服阀的使用寿命。
如由于伺服阀故障需检修时,系统可选择切换为一个阀工作。
液压压下能继续正常工作。
从而减少停机率。
但必须注意操作侧、传动侧二侧同时选择单阀工作。
此时压下速度减小一半。
2、压下系统的二种闭环调节功能;分别介绍如下:(1)、A.P.C.系统;A.P.C. 系统,由进口的微脉冲位置传感器作为油缸位移的位置实际值,组成位置闭环系统。
系统稳定性好,分辨率高。
可确保分辨0.001mm。
系统设有零辊缝压靠,位置快、慢二挡压下速度给定及快速抬辊。
辊缝倾斜给定、及操作侧、传动侧二侧油缸同步控制环节。
系统能确保压下过程中,轧辊平行移动。
(2)、A.F.C.;(轧制力闭环)A.F.C.由负载腔油压压力传感器作为反馈元件,并经计算机数据处理后作为负载力显示。
基于冷轧热镀锌机组的液压控制系统设计

基于冷轧热镀锌机组的液压控制系统设计目录目录 (I)摘要......................................................................................................................................................... I I ABSTRACT .. (III)第一章绪论 (1)1.1课题研究的背景 (1)1.2课题研究的目的和意义 (1)1.3论文的主要内容 (1)第二章液压控制系统方案设计及系统构成 (2)2.1冷轧厂热镀锌机组的工作原理概述(热镀锌机组) (2)2.2热镀锌机组的液压电气控制系统设计要求 (2)2.2.1 主泵单元 (2)2.2.2 循环单元 (3)2.3热镀锌机组的液压控制系统主要元件参数计算及型号选择 (5)2.3.1 油箱单元 (5)2.3.2 主泵单元 (6)2.3.3 循环单元 (9)2.3.4 冷却单元 (11)2.3.5 加热单元 (14)2.3.6 过滤器 (16)第三章热镀锌机组的液压控制系统设计分析 (17)3.1热镀锌机组的液压控制系统结构 (17)3.2主电路......................................................................................................... 错误!未定义书签。
3.3电磁阀,泵等驱动控制器电路设计 ......................................................... 错误!未定义书签。
3.4信号电路设计............................................................................................. 错误!未定义书签。
液压系统设计篇

液压系统设计篇----4ffaa03a-7161-11ec-876d-7cb59b590d7d液压传动系统设计,除了应符合其主机在动作循环和静、动态性能等方面所提出的要求外,还必须满足结构简单、使用维护方便、工作安全可靠、性能好、成本低、效率高、寿命长等条件。
液压传动系统的设计一般依据流程图见图4-1的步骤进行设计。
图4-1液压传动系统设计流程图第一节明确设计要求要设计一个新的液压系统,首先必须明确机器对液压系统的动作和性能要求,并将这些技术要求作为设计的出发点和基础。
需要掌握的技术要求可能包括:1.机器的特性(1)充分了解主机的结构和总体布置,机构与从动件之间的连接条件和安装限制,以及其用途和工作目的。
(2)负载种类(恒定负载、变化负载及冲击负载)及大小和变化范围;运动方式(直线运动、回转运动、摆动)及运动量(位移、速度、加速度)的大小和要求的调节范围;惯性力、摩擦力、动作特性、动作时间和精度要求(定位精度、跟踪精度、同步精度)。
(3)原动机类型(电机、内燃机等)、容量(功率、速度、扭矩)和稳定性。
(4)操作方式(手动、自动)、信号处理方式(继电器控制、逻辑电路、可编程控制器、微机程序控制)。
(5)系统中每个执行器的动作顺序和动作时间之间的关系。
2.使用条件(1)设置地点。
(2)环境温度、湿度(高温、寒带、热带),粉尘种类和浓度(防护、净化等),腐蚀性气体(所有元件的结构、材质、表面处理、涂覆等),易爆气体(防爆措施),机械振动(机械强度、耐振结构),噪声限制(降低噪声措施)。
(3)维护程度和周期;维修人员的技术水平;保持空间、可操作性和互换性。
3.适用的标准和规则根据用户要求采用相关标准、法则。
4.安全性、可靠性(1)用户在安全方面是否有特殊要求。
(2)指定保修期和条件。
5.经济不能只考虑投资费用,还要考虑能源消耗、维护保养等运行费用。
6.工况分析液压系统的工况分析是为了找出各执行机构在各自工作过程中的速度和负载变化规律。
薄板坯连铸连轧设备生产热轧薄宽钢带的液压系统设计与优化
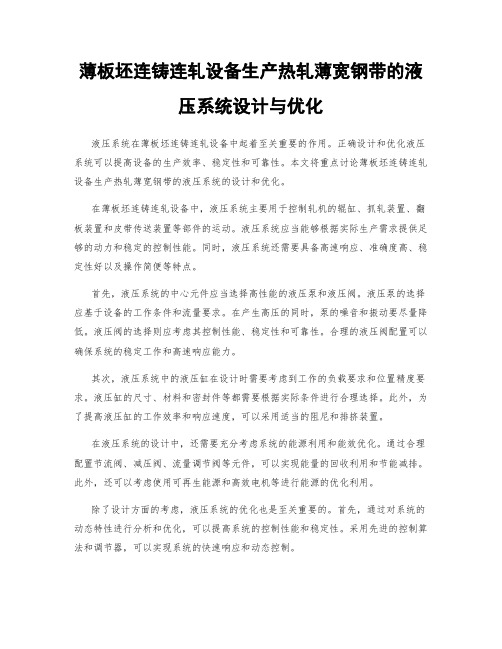
薄板坯连铸连轧设备生产热轧薄宽钢带的液压系统设计与优化液压系统在薄板坯连铸连轧设备中起着至关重要的作用。
正确设计和优化液压系统可以提高设备的生产效率、稳定性和可靠性。
本文将重点讨论薄板坯连铸连轧设备生产热轧薄宽钢带的液压系统的设计和优化。
在薄板坯连铸连轧设备中,液压系统主要用于控制轧机的辊缸、抓轧装置、翻板装置和皮带传送装置等部件的运动。
液压系统应当能够根据实际生产需求提供足够的动力和稳定的控制性能。
同时,液压系统还需要具备高速响应、准确度高、稳定性好以及操作简便等特点。
首先,液压系统的中心元件应当选择高性能的液压泵和液压阀。
液压泵的选择应基于设备的工作条件和流量要求。
在产生高压的同时,泵的噪音和振动要尽量降低。
液压阀的选择则应考虑其控制性能、稳定性和可靠性。
合理的液压阀配置可以确保系统的稳定工作和高速响应能力。
其次,液压系统中的液压缸在设计时需要考虑到工作的负载要求和位置精度要求。
液压缸的尺寸、材料和密封件等都需要根据实际条件进行合理选择。
此外,为了提高液压缸的工作效率和响应速度,可以采用适当的阻尼和排挤装置。
在液压系统的设计中,还需要充分考虑系统的能源利用和能效优化。
通过合理配置节流阀、减压阀、流量调节阀等元件,可以实现能量的回收利用和节能减排。
此外,还可以考虑使用可再生能源和高效电机等进行能源的优化利用。
除了设计方面的考虑,液压系统的优化也是至关重要的。
首先,通过对系统的动态特性进行分析和优化,可以提高系统的控制性能和稳定性。
采用先进的控制算法和调节器,可以实现系统的快速响应和动态控制。
其次,通过系统的模拟、仿真和试验分析,可以对系统进行改进和优化。
通过减小油液泄漏和回油压力的损失,可以降低系统的能量损耗并提高系统的效率。
此外,合理布置和优化系统组件的布局,可以简化系统结构,并提高系统的可靠性。
最后,液压系统的维护和保养也是确保其正常运行和延长寿命的关键。
定期检查和更换油品、过滤器和密封件等,可以减少系统的故障和停机时间。
冷辗环机液压系统设计与控制
1 辗 环机 及环 件轧 制工 艺
2 液压 系统 组成 及设 计
2 1 液压 系统 组成 .
辗 环机 液压 执行 部件 主要 是机 械手 缸 、 圆度辊 缸 、 芯辊缸 、 测量 缸 。液 压 系统 由机 械 手 缸 、 圆度 辊 缸 、 芯 辊缸、 测量缸 4个控 制 回路组 成 。如 图 2所 示 为液 压 系统 原理 图 。
变形 , 直径逐 步扩 大 , 圆度 辊 、 测量 辊 被 动退 回, 件 尺 环
i 进 度 缸 1 辊 圆
芯辊 缸
测 量 辊 缸
垡
; 1
寸达到一定值时, 圆度辊主动退 回至终点 ; 环件 1 尺寸 0 达到要求时 , 停止轧制, 芯辊 9 径向远离辗压轮 7芯辊 、 ; 测量辊退回原位, 进入下一循环。 除轧制进给系统 由交流伺服电机驱动外 , 其他动 作由液压系统实现 , 液压系统必须满足以上工作要求。
HAO n — ig 一,H UA i2 Yo gxn 1 L n
(. 1 华北水利水 电学 院 机 械系 , 河南 郑州
4 0 0 ; .武汉 理工 大学 材料学院 ,湖北 武 汉 50 8 2
40 7 ) 3 0 0
摘
要: 冷辗 环机 的液压 系统 对环件 轧 制过程 具 有重要 影 响 。根 据环 件轧 制 的特 点和 工 艺流程 , 究 了 研
调速方法 : 节流调速系统结构简单 、 造价低廉、 维 护 方便 、 调速 范 围大 、 调 性能 好 , 微 而且 , 环 机液 压 系 辗
统需 要 的功率 小 , 动 速度 低 , 作 负 载 小 。所 以 , 运 工 采 用节 流调 速方 式 。节流 阀调 速分 为进 油节 流调 速和 回 油节 流调 速 。长时 间停 机 , 压 缸 内的 油液 会 流 回油 液 箱 , 回油节 流调 速 方式 下 , 新 向油 箱 供 油 时 , 于 在 重 由 油路 中的节 流 阀不 能 马上 形 成 背 压 , 油 路 没 有节 流 进
上料机液压系统设计
上料机液压系统设计液压系统在上料机中的设计是非常重要的,它是实现上料机正常工作的关键组成部分。
本文将从液压系统的组成、工作原理、设计要求及优化等方面进行详细介绍。
一、液压系统组成液压系统主要由液压源、执行元件、控制元件、辅助元件及液压工作介质等组成。
1.液压源:通常由液压泵提供动力,将机械能转化为液压能。
2.执行元件:主要有液压缸、液压马达等。
在上料机中,液压缸用于实现上料斗的升降和倾斜等动作。
3.控制元件:包括阀门、阀芯、阀座等。
通过对液压油流进行控制和调节,实现液压系统各个部件的协调工作。
4.辅助元件:主要有油箱、滤清器、冷却器等。
油箱提供液压油的贮存和冷却,滤清器用于过滤液压油中的杂质,冷却器用于降低液压油的温度。
5.液压工作介质:通常采用液压油作为液压系统的工作介质。
液压油具有一定的粘度和热稳定性,能够在高温和高压力下正常工作。
二、液压系统工作原理液压系统的工作原理是基于帕斯卡定律。
即压力在静态液体中传递时,作用在液体上的力是与所受面积成正比的。
根据这一原理,液压系统通过控制液压油的流量和压力,实现对液压缸的控制。
当液压系统启动时,液压泵将液压油从油箱中吸入,在压力作用下,向执行元件(液压缸)提供动力。
通过控制元件的控制,可以实现液压油的流向和压力调节,从而实现上料斗的升降和倾斜等动作。
三、液压系统设计要求1.性能要求:液压系统在上料机中的设计应保证系统的工作性能稳定可靠,具有较高的工作效率和运行平稳性。
2.安全要求:液压系统设计应考虑到系统的安全性,包括液压元件的强度和稳定性,系统的漏油及漏压检测与报警等。
3.节能要求:液压系统设计应尽可能降低能源损耗,提高系统的能源利用率。
4.维修保养要求:液压系统的设计应便于维修和保养,包括易于检修和更换液压元件,便捷的油液更换与滤清以及液压系统的保养周期等。
四、液压系统设计优化针对上述设计要求,可以通过以下方式对液压系统进行优化设计:1.选择合适的液压元件:根据上料机的工作条件和需求,选择适合的液压泵、液压缸和控制阀等元件,保证其质量和性能符合要求。
650单机架轧机建立其液压弯辊伺服控制系统建立数学模型研究毕业论文
The650single stand millis discussed in this paper,and we will design the mathematical model aboutthe hydraulic servo control system of bending roll.Furthermore we will research and improve the accuracy, stability and rapidity of the model by using the matlab.At the same time ,we will know the effects of various parameters on the system. Through thispaper we will know how to design hydraulic roll bending system and the mechanism, which providing technical support for the future related research.
摘要
随着现代工业的发展,钢板和带钢作为在经济建设中应用最广泛的钢材,对钢铁企业提供的板带钢的尺寸精度和形状精度提出了更高的要求。
650轧机
2
7.171
5.354
3.399
2.337
0.2
0.1
570
720
645
143
5.354
3.814
2.337
1.436
0.2
0.1
720
750
735
154
164
159
346.0
4
3.814
3.148
1.436
1.047
0.2
0.1
750
780
765
164
173
168
223.8
轧机的平衡装置主要有弹簧式、重锤式和液压式三种主要类型,此处采用液压平衡装置,如图。
液压弯辊
采用液压弯辊快速调整辊型,控制板形的方法是一种板形快速调节 方法,这种方法在冷轧带钢轧机上应用十分广泛。液压弯辊方法有 弯曲工作辊和弯曲支承辊。宽板轧机工作辊相对比较细长,其刚度 远小于支承辊,故弯曲工作辊比弯曲支承辊灵敏,但只能影响边部 的板形。因此,对于宽板轧机,采用弯曲支承辊方法比较好;对于 窄板轧机,采用弯曲工作辊方法比较好[8]。本轧机为窄板轧机,故 采用弯曲工作辊方法。
建立微分方程
图 1-3 厚组元变形微分体受力情况
dp K 2 dy t0 t2 0 dx y dx 2y
(1-1)
解微分方程得后滑区单位轧制力分布方程: PH (K 2H K 2 )( H 2) K 2 hx
(1-2)
前滑区单位轧制力分布方程:
PH (K 2h K 2 N )( hx )m K 2 N
电动压下
电动压下部分,双电机驱动,电机通过两级蜗轮蜗杆驱动压下 螺丝压下,两边通过电磁离合器连接断开,以实现同步、异步 压下功能。