轧钢机压下装置的分类和设计方法
轧机压下装置工作过程

轧机压下装置工作过程一、引言轧机压下装置是轧机的核心部件之一,其作用是将钢坯或钢板压成所需的形状和尺寸。
本文将详细介绍轧机压下装置的工作过程。
二、轧机压下装置的组成1.上辊组:包括上辊、上辊承受器和上辊调整机构。
2.下辊组:包括下辊、下辊承受器和下辊调整机构。
3.中间滚筒组:包括中间滚筒和中间滚筒承受器。
4.液压系统:包括液压站、油缸和管路等。
5.电气控制系统:包括电气控制柜、PLC控制器等。
三、轧机压下装置的工作原理1.准备阶段:首先需要对轧机进行检查,确保设备正常运行。
然后将钢坯或钢板放在轧机进料口处,待进料系统将其送入到轧机内部。
2.预弯阶段:当钢坯或钢板通过上下两个辊之间时,由于强制挤压作用,使得材料表面出现微小的弯曲,这个过程称为预弯。
3.压下阶段:在预弯后,液压系统开始工作,将上下两个辊向内靠拢,钢坯或钢板被挤压成所需的形状和尺寸。
4.拉伸阶段:在钢坯或钢板通过轧机的过程中,由于受到强制挤压作用,材料内部会产生应力。
为了消除这些应力,需要进行拉伸处理。
5.放松阶段:当钢坯或钢板通过轧机后,需要进行放松处理。
这个过程是将轧制后的材料从轧机中取出,并使其自然冷却至室温。
四、轧机压下装置的工作流程1.启动电气控制系统:首先需要启动电气控制系统,并进行各项参数设置。
2.启动液压系统:接着需要启动液压系统,并对其进行调试和校准。
3.进料阶段:当设备正常运行时,将钢坯或钢板放在轧机进料口处,并启动进料系统将其送入到轧机内部。
4.预弯阶段:当钢坯或钢板通过上下两个辊之间时,由于强制挤压作用,使得材料表面出现微小的弯曲,这个过程称为预弯。
5.压下阶段:在预弯后,液压系统开始工作,将上下两个辊向内靠拢,钢坯或钢板被挤压成所需的形状和尺寸。
6.拉伸阶段:在钢坯或钢板通过轧机的过程中,由于受到强制挤压作用,材料内部会产生应力。
为了消除这些应力,需要进行拉伸处理。
7.放松阶段:当钢坯或钢板通过轧机后,需要进行放松处理。
轧机的液压压下装置

1 前言 近年来,随着经济的发展,我国黑色及有金属薄带材产品、产量迅速增长,而轧机也向高速、大型、连轧、自动化方向发展。
目前,所有的冷轧机的压下装置都采用液压压下这种方式。
液压压下是轧机现代化的突出重要标志之一,它较易适应轧制及操作条件的变化,根据轧制类型和轧制道次程序,如压下轧制或平整轧制,并能给予最佳补偿,并利用轧机刚性可调的特点,对冷轧机采用递降式刚度分配方式,以得到高质量的产品,从而保证带材厚度及平整度,使带材质量最佳,不论是在最硬和最软的条件下都是如此。
同时液压压下具备自动及快速卸荷功能,以防止轧辊及轧辊轴承的过载和损坏,延长轧辊寿命等特点。
液压压下方式虽然有各种各样的方案,但就其压下油缸安放位置来说,分为压下和压上两种结构形式。
2 液压压下油缸安放在轧机机架上部 将液压压下油缸安放在轧机机架上部(上支承辊轴承座上面),这种安装方式在一定程度上可以使其免受来自轧机工艺润滑系统的乳化液、轧制油等造成对液压压下油缸污染,但是由于液压压下油缸处在轧机机架上部,轧制时,当需要压下油缸活塞往上运动时,因无外力使其活塞动作,所以在液压压下系统中还需设置压下油缸活塞平衡回路及必要的电气联锁控制,因此增加了液压压下系统设备制造成本。
油缸安装于轧机机架上部时安装、维修不便,由于液压压下油缸处在轧机机架上部,还需增加固定液压压下油缸的悬挂机构。
液压压下油缸维修时,必须先卸掉液压压下油缸的悬挂机构后,才能将液压压下油缸落下,并放在上支承辊轴承座上面拉出,全部工作需要在轧机机架上进行,从而导致更换困难。
因液压压下油缸安装在轧机机架上部,考虑安装、维修等因素,压下油缸阀装置与液压压下油缸多数分开设置,两者之间是靠管道连接,这样就导致管道油液质量转化到压下油缸活塞上当量质量增加,直接影响到系统的动态指标是否满足要求,容易导致轧机刚度降低,系统响应频率降低等不良后果,为了减小这些不良影响,压下油缸阀装置的安放位置及其连接管道受到严格制约。
轧机的液压压下装置
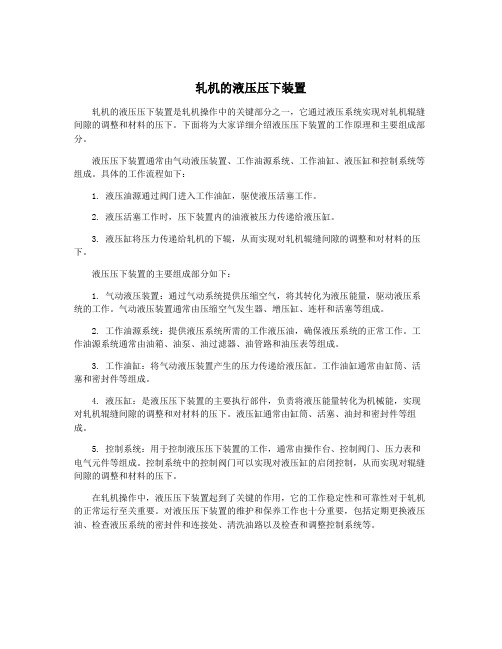
轧机的液压压下装置轧机的液压压下装置是轧机操作中的关键部分之一,它通过液压系统实现对轧机辊缝间隙的调整和材料的压下。
下面将为大家详细介绍液压压下装置的工作原理和主要组成部分。
液压压下装置通常由气动液压装置、工作油源系统、工作油缸、液压缸和控制系统等组成。
具体的工作流程如下:1. 液压油源通过阀门进入工作油缸,驱使液压活塞工作。
2. 液压活塞工作时,压下装置内的油液被压力传递给液压缸。
3. 液压缸将压力传递给轧机的下辊,从而实现对轧机辊缝间隙的调整和对材料的压下。
液压压下装置的主要组成部分如下:1. 气动液压装置:通过气动系统提供压缩空气,将其转化为液压能量,驱动液压系统的工作。
气动液压装置通常由压缩空气发生器、增压缸、连杆和活塞等组成。
2. 工作油源系统:提供液压系统所需的工作液压油,确保液压系统的正常工作。
工作油源系统通常由油箱、油泵、油过滤器、油管路和油压表等组成。
3. 工作油缸:将气动液压装置产生的压力传递给液压缸。
工作油缸通常由缸筒、活塞和密封件等组成。
4. 液压缸:是液压压下装置的主要执行部件,负责将液压能量转化为机械能,实现对轧机辊缝间隙的调整和对材料的压下。
液压缸通常由缸筒、活塞、油封和密封件等组成。
5. 控制系统:用于控制液压压下装置的工作,通常由操作台、控制阀门、压力表和电气元件等组成。
控制系统中的控制阀门可以实现对液压缸的启闭控制,从而实现对辊缝间隙的调整和材料的压下。
在轧机操作中,液压压下装置起到了关键的作用,它的工作稳定性和可靠性对于轧机的正常运行至关重要。
对液压压下装置的维护和保养工作也十分重要,包括定期更换液压油、检查液压系统的密封件和连接处、清洗油路以及检查和调整控制系统等。
轧机的液压压下装置
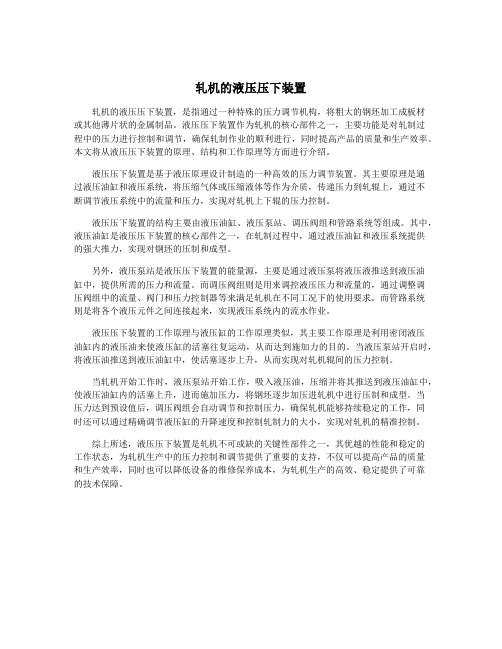
轧机的液压压下装置轧机的液压压下装置,是指通过一种特殊的压力调节机构,将粗大的钢坯加工成板材或其他薄片状的金属制品。
液压压下装置作为轧机的核心部件之一,主要功能是对轧制过程中的压力进行控制和调节,确保轧制作业的顺利进行,同时提高产品的质量和生产效率。
本文将从液压压下装置的原理、结构和工作原理等方面进行介绍。
液压压下装置是基于液压原理设计制造的一种高效的压力调节装置。
其主要原理是通过液压油缸和液压系统,将压缩气体或压缩液体等作为介质,传递压力到轧辊上,通过不断调节液压系统中的流量和压力,实现对轧机上下辊的压力控制。
液压压下装置的结构主要由液压油缸、液压泵站、调压阀组和管路系统等组成。
其中,液压油缸是液压压下装置的核心部件之一,在轧制过程中,通过液压油缸和液压系统提供的强大推力,实现对钢坯的压制和成型。
另外,液压泵站是液压压下装置的能量源,主要是通过液压泵将液压液推送到液压油缸中,提供所需的压力和流量。
而调压阀组则是用来调控液压压力和流量的,通过调整调压阀组中的流量、阀门和压力控制器等来满足轧机在不同工况下的使用要求。
而管路系统则是将各个液压元件之间连接起来,实现液压系统内的流水作业。
液压压下装置的工作原理与液压缸的工作原理类似,其主要工作原理是利用密闭液压油缸内的液压油来使液压缸的活塞往复运动,从而达到施加力的目的。
当液压泵站开启时,将液压油推送到液压油缸中,使活塞逐步上升,从而实现对轧机辊间的压力控制。
当轧机开始工作时,液压泵站开始工作,吸入液压油,压缩并将其推送到液压油缸中,使液压油缸内的活塞上升,进而施加压力,将钢坯逐步加压进轧机中进行压制和成型。
当压力达到预设值后,调压阀组会自动调节和控制压力,确保轧机能够持续稳定的工作,同时还可以通过精确调节液压缸的升降速度和控制轧制力的大小,实现对轧机的精准控制。
综上所述,液压压下装置是轧机不可或缺的关键性部件之一,其优越的性能和稳定的工作状态,为轧机生产中的压力控制和调节提供了重要的支持,不仅可以提高产品的质量和生产效率,同时也可以降低设备的维修保养成本,为轧机生产的高效、稳定提供了可靠的技术保障。
轧机压下装置设计计算
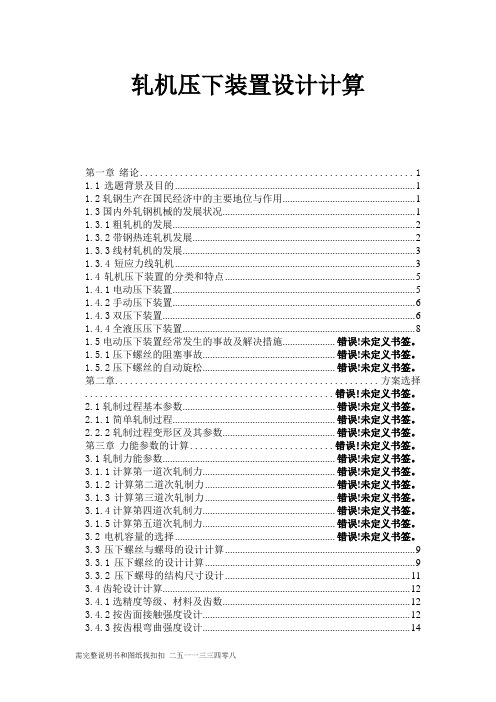
轧机压下装置设计计算第一章绪论 (1)1.1选题背景及目的 (1)1.2轧钢生产在国民经济中的主要地位与作用 (1)1.3国内外轧钢机械的发展状况 (1)1.3.1粗轧机的发展 (2)1.3.2带钢热连轧机发展 (2)1.3.3线材轧机的发展 (3)1.3.4短应力线轧机 (3)1.4轧机压下装置的分类和特点 (5)1.4.1电动压下装置 (5)1.4.2手动压下装置 (6)1.4.3双压下装置 (6)1.4.4全液压压下装置 (8)1.5电动压下装置经常发生的事故及解决措施..................... 错误!未定义书签。
1.5.1压下螺丝的阻塞事故..................................................... 错误!未定义书签。
1.5.2压下螺丝的自动旋松..................................................... 错误!未定义书签。
第二章..................................................... 方案选择.................................................. 错误!未定义书签。
2.1轧制过程基本参数............................................................. 错误!未定义书签。
2.1.1简单轧制过程................................................................. 错误!未定义书签。
2.2.2轧制过程变形区及其参数............................................. 错误!未定义书签。
第三章力能参数的计算............................. 错误!未定义书签。
轧机的液压压下装置
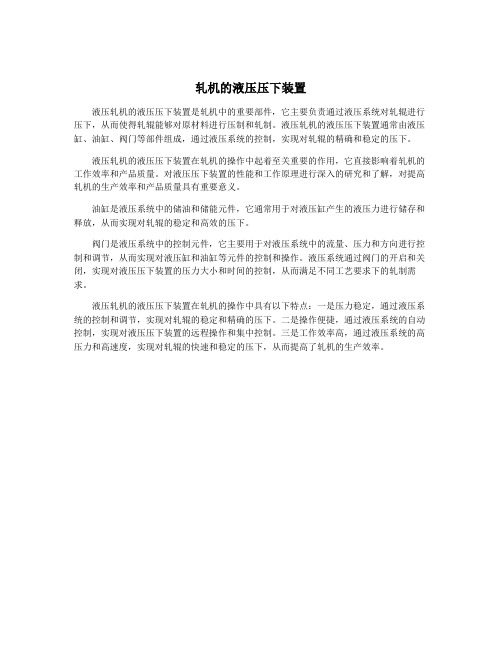
轧机的液压压下装置
液压轧机的液压压下装置是轧机中的重要部件,它主要负责通过液压系统对轧辊进行压下,从而使得轧辊能够对原材料进行压制和轧制。
液压轧机的液压压下装置通常由液压缸、油缸、阀门等部件组成,通过液压系统的控制,实现对轧辊的精确和稳定的压下。
液压轧机的液压压下装置在轧机的操作中起着至关重要的作用,它直接影响着轧机的工作效率和产品质量。
对液压压下装置的性能和工作原理进行深入的研究和了解,对提高轧机的生产效率和产品质量具有重要意义。
油缸是液压系统中的储油和储能元件,它通常用于对液压缸产生的液压力进行储存和释放,从而实现对轧辊的稳定和高效的压下。
阀门是液压系统中的控制元件,它主要用于对液压系统中的流量、压力和方向进行控制和调节,从而实现对液压缸和油缸等元件的控制和操作。
液压系统通过阀门的开启和关闭,实现对液压压下装置的压力大小和时间的控制,从而满足不同工艺要求下的轧制需求。
液压轧机的液压压下装置在轧机的操作中具有以下特点:一是压力稳定,通过液压系统的控制和调节,实现对轧辊的稳定和精确的压下。
二是操作便捷,通过液压系统的自动控制,实现对液压压下装置的远程操作和集中控制。
三是工作效率高,通过液压系统的高压力和高速度,实现对轧辊的快速和稳定的压下,从而提高了轧机的生产效率。
轧钢机轧辊辊缝调整装置-----压下装置
M=M1+P1 tan(ρ±α)=M1+M2
d2—螺丝中径
d2=d-0.5t=376-24×0.5=364mm
ρ—螺纹上的摩擦角,即ρ=arctanμ2,μ2为螺纹接触面的摩擦系数,一般取μ2≈0.1
m= = =10
3、按齿根圆强度设计
m≥
(1)确定公式内的各计算数值
1)由图10-20c查得小齿轮的弯曲疲劳强度极限σFE1=500MPa,大齿轮的弯曲强度极限σFE2=380MPa
2)由图10-18取弯曲疲劳寿命系数 =0.85, =0.88,
3)计算弯曲疲劳施用应力
取弯曲疲劳安全系数s=1.4,由式(10-12)得
7)由图10-19取接触疲劳寿命系数KHN1=0.95,KHN2=0.98
8)计算接触疲劳许用应力
取失效概率为1%,安全系数S=1
〔σH〕1= =0.95×600MPa=570MPa
〔σH〕2= =0.98×550MPa=539MPa
(2)计算
1)计算
≥2.32×
=2.32× mm
=172.415mm
4、轴的结构设计
(1)拟定轴上零件的装配方案
选用图15-22a所示的装配方案。
(2)根据轴向定位的要求确定轴的各段直径和长度
1)取I-II轴段的直径dI-II=110mm,右端用轴端挡圈定位,按轴端直径取挡圈直径D=120mm。
2)初步选择滚动轴承。因轴承同时受有径向力和轴向力的作用,故选用单列圆锥滚子轴承。参照工作要求并根据dII-III=140mm,由轴承产品目录中进行初步选取轴轴承内圈直径为110mm.
轧钢机下压机构设计 正文
1 引言轧机的压下装置是轧机的重要结构之一,用于调整辊缝,也称辊缝调整装置,其结构设计的好坏,直接关系着轧件的产量与质量。
压下装置按传动方式可分为手动压下、电动压下和液压压下,手动压下装置一般多用于不经常进行调节、轧件精度要求不严格、以及轧制速度要求不高的中、小型型钢、线材和小型热轧板带轧机上。
电动压下装置适用于板坯轧机、中厚板轧机等要求辊缝调整范围大、压下速度快的情况,主要由压下螺丝、螺母及其传动机构组成。
在中厚板轧机中,工作时要求轧辊快速、大行程、频繁的调整,这就要求压下装置采用惯性小的传动系统,以便频繁的启动、制动,且有较高的传动效率和工作可靠性。
这种快速电动压下装置轧机不能带钢压下,压下电机的功率一般是按空载压下考虑选用,所以常常由于操作失误、压下量过大等原因产生卡钢、“坐辊”或压下螺丝超限提升而发生压下螺丝无法退回的事故,这时上辊不能动,轧机无法正常工作,压下电动机无法提起压下螺丝,为了克服这种卡钢事故,必须增设一套专用的回松机构。
电动压下装置的主要缺点之一是运动部分的惯性大,因而在辊缝调节过程中反应慢、精度低,对现代化的高速度、高精度轧机已不适应,提高压下装置响应速度的主要途径是减少其惯性,而用液压控制可以收到这样的效果。
液压压下装置,就是取消了传统的电动压下机构,其辊缝的调节均由液压缸来完成。
在这一装置中,除液压缸以及与之配套的伺服阀和液压系统外,还包括检测仪表及运算控制系统。
全液压压下装置有以下优点:1、惯性小、动作快,灵敏度高,因此可以得到高精度的板带材,其厚度偏差可以控制到小于成品厚度的1%,而且缩短了板带材的超差部分长度,提高了轧材的成品率,节约金属,提高了产品质量,并降低了成本;2、结构紧凑,降低了机座的总高度,减少了厂房的投资,同时由于采用液压系统,使传动效率大大提高;3、采用液压系统可以使卡钢迅速脱开,这样有利于处理卡钢事故,避免了轧件对轧辊的刮伤、烧伤,再启动时为空载启动,降低了主电机启动电流,并有利于油膜轴承工作;4、可以实现轧辊迅速提升,便于快速换辊,提高了轧机的有效作业率,增加了轧机的产量。
轧机的液压压下装置
轧机的液压压下装置液压压下装置是轧机中非常重要的组成部分,它主要用于在轧制过程中对轧辊进行压下,以使金属材料在轧制过程中得到良好的形状和尺寸。
液压压下装置一般由液压系统、主缸、液压缸、液压管路等部分组成。
下面将从这几个方面对液压压下装置作详细介绍。
一、液压系统液压系统是液压压下装置中最为核心的部分,它主要由油箱、油泵、阀门和油管等组成。
油箱主要用于储存液压油,并且在油箱中放置油滤器和油温计等,以确保液压系统中的油液清洁和温度适宜。
油泵的作用是将液压油从油箱中抽出并送入液压缸内,从而使液压缸对轧辊进行压下。
油泵一般有液压柱塞泵、液压齿轮泵和液压叶片泵等几种类型。
阀门主要用于控制液压系统中的液压油流动方向、流量和压力等参数,以实现对液压压下装置的控制。
油管主要用于将液压系统中的液压油输送到液压缸中,并且使液压油在液压缸内进行压力传递。
二、主缸主缸是液压压下装置中的一个重要部件,它主要由液压缸筒、活塞、活塞杆、活塞密封等组成。
液压缸筒一般由优质的合金钢材料制造而成,并且经过热处理和精密加工等工艺,以确保其具有足够的强度和刚性。
活塞是主缸内部的运动部件,它的作用是在液压压下装置工作时对轧辊进行压下,从而使金属材料在轧制过程中得到压制和塑性变形。
活塞杆是连接活塞和液压缸筒的部件,它的结构要求具有足够的强度和刚性,以承受液压压下装置工作时产生的巨大作用力。
活塞密封是主缸内部的关键部件,它的作用是防止液压缸内的液压油泄漏,并且保证液压系统的密封性和工作可靠性。
四、液压管路液压管路是液压压下装置中非常重要的部分,它主要由液压管、接头、接头密封等组成。
液压管一般由优质的碳钢管或不锈钢管制造而成,并经过加工和抛光等工艺,以确保其具有足够的强度和耐腐蚀性。
接头主要用于连接液压管和液压缸、液压泵、阀门等部件,使液压油能够顺畅流动。
接头密封一般采用油封圈、O型圈等密封件,它的作用是防止液压管路中的液压油泄漏,并且保持液压系统的密封性和工作可靠性。
轧机的液压压下装置
轧机的液压压下装置轧机的液压压下装置是轧机的重要部件之一,它主要用于轧机在工作过程中对板材进行压下作用。
液压压下装置的设计和性能对轧机的工作效率、产品质量和设备寿命有着重要的影响。
一、液压压下装置的主要功能液压压下装置是轧机的重要部件,主要功能有以下几点:1. 对轧机辊缝中的板材进行压下,保证板材在轧制过程中不会产生变形或者变形较小,从而提高产品的成形精度和表面质量。
2. 通过调整液压压下装置的压下力,可以调节轧机的压下量,满足不同板材的轧制需要。
3. 调整液压压下装置的工作方式和参数,可以适应不同的轧制工艺和板材材质,提高轧机的生产适应性和生产效率。
二、液压压下装置的结构和工作原理液压压下装置通常由液压缸、油缸、阀门、油泵以及压力传感器等部件组成。
其结构如图所示,通过控制阀门的调节,液压系统可以实现对液压缸的压力调节,从而实现对板材的压下作用。
液压压下装置的工作原理如下:当轧机开始工作时,液压系统通过油泵将液压油送入油缸中,使得油缸内的液压缸得以推动,从而对板材进行压下作用。
通过调节液压系统中的阀门,可以控制液压缸的工作压力和压下力的大小,满足不同板材的轧制需要。
通过压力传感器可以实时监测液压系统的工作压力,从而保证轧机的安全运行。
三、液压压下装置的优点液压压下装置相对于机械式压下装置具有以下几个优点:1. 调节性好:液压系统通过调节阀门可以实现对压下力的精确控制,且调节范围大,能够满足不同板材的轧制需求。
2. 压力稳定:液压系统具有压力稳定的特点,能够保证压下力的稳定输出,从而保证产品的成形精度和表面质量。
3. 响应速度快:液压系统的响应速度快,能够满足轧机在工作过程中对压下力的快速调节需求,提高轧机的生产效率。
4. 可靠性好:液压系统的工作过程相对平稳,不易发生振动和冲击,能够保证轧机的稳定运行,延长设备的使用寿命。
四、液压压下装置的应用现状及发展趋势目前,液压压下装置已经在轧机中得到了广泛应用,在改进轧机的生产效率、产品质量和设备可靠性等方面发挥了重要作用。
- 1、下载文档前请自行甄别文档内容的完整性,平台不提供额外的编辑、内容补充、找答案等附加服务。
- 2、"仅部分预览"的文档,不可在线预览部分如存在完整性等问题,可反馈申请退款(可完整预览的文档不适用该条件!)。
- 3、如文档侵犯您的权益,请联系客服反馈,我们会尽快为您处理(人工客服工作时间:9:00-18:30)。
轧钢机压下装置的分类和设计方法
工程论文2009-07-16 15:54:53 阅读418 评论0 字号:大中小订阅
压下装置的设计与计算
一、概述
轧机的压下装置是轧机的重要结构之一,用于调整辊缝,也称辊缝调整装置,其结构设计的好坏,直接关系着轧件的产量与质量。
压下装置按传动方式可分为手动压下、电动压下和液压压下,手动压下装置一般多用于不经常进行调节、轧件精度要求不严格、以及轧制速度要求不高的中、小型型钢、线材和小型热轧板带轧机上。
电动压下装置适用于板坯轧机、中厚板轧机等要求辊缝调整范围大、压下速度快的情况,主要由压下螺丝、螺母及其传动机构组成。
在中厚板轧机中,工作时要求轧辊快速、大行程、频繁的调整,这就要求压下装置采用惯性小的传动系统,以便频繁的启动、制动,且有较高的传动效率和工作可靠性。
这种快速电动压下装置轧机不能带钢压下,压下电机的功率一般是按空载压下考虑选用,所以常常由于操作失误、压下量过大等原因产生卡钢、“坐辊”或压下螺丝超限提升而发生压下螺丝无法退回的事故,这时上辊不能动,轧机无法正常工作,压下电动机无法提起压下螺丝,为了克服这种卡钢事故,必须增设一套专用的回松机构。
电动压下装置的主要缺点之一是运动部分的惯性大,因而在辊缝调节过程中反应慢、精度低,对现代化的高速度、高精度轧机已不适应,提高压下装置响应速度的主要途径是减少其惯性,而用液压控制可以收到这样的效果。
液压压下装置,就是取消了传统的电动压下机构,其辊缝的调节均由液压缸来完成。
在这一装置中,除液压缸以及与之配套的伺服阀和液压系统外,还包括检测仪表及运算控制系统。
全液压压下装置有以下优点:
1. 惯性小、动作快,灵敏度高,因此可以得到高精度的板带材,其厚度偏差可以控制到小于成品厚度的1%,而且缩短了板带材的超差部分长度,提高了轧材的成品率,节约金属,提高了产品质量,并降低了成本;
2. 结构紧凑,降低了机座的总高度,减少了厂房的投资,同时由于采用液压系统,使传动效率大大提高;
3. 采用液压系统可以使卡钢迅速脱开,这样有利于处理卡钢事故,避免了轧件对轧辊的刮伤、烧伤,再启动时为空载启动,降低了主电机启动电流,并有利于油膜轴承工作;
4. 可以实现轧辊迅速提升,便于快速换辊,提高了轧机的有效作业率,增加了轧机的产量。
全液压压下也存在一些缺点:压下系统复杂,工作条件要求高,有些元件(如压力传感器、位移传感器及测厚仪等测量元件)和伺服阀等制造精度要求很高,并要求在高温、高压及有振动条件下,工作不应失灵或下降测量精度和控制灵敏度,因此制造困难、成本高,维护保养要求很严格,以保证控制精度。
虽然液压压下相对于电动压下还存在着一些缺点,但是由于电动压下无法满足目前正在发展的高生
产率、高产品质量的现代化带轧机的工作要求,因而,采用液压压下的板厚自动控制系统来代替电动压下的板厚自动控制系统已是必然趋势,因而随着科学技术的发展,液压压下板厚自动控制系统将会愈来愈完善。
二、南钢2800中板轧机压下装置
南钢2800中板轧机压下装置,由于轧制范围大,压下启动频繁,且要求辊缝调整精度高,采用了电动压下自动控制(APC)和液压压下自动厚度控制(AGC)相结合的联合压下形式。
电动APC用于空载辊缝调整,在压下螺丝顶部的辊缝仪控制下,可进行高速度、高精度的压下辊缝设定;液压压下AGC用于带钢自动厚度调节,可在轧制过程中,随着坯料厚度、轧制压力以及成品厚度的变化,通过设在窗口底部的测压仪及相应的计算机程序控制,随时对轧辊辊缝进行微量校正,从而可以保证板厚偏差控制在公差规定的范围内,同时由于采用液压AGC可使卡钢迅速脱开,既节省了时间,也避免了轧件对轧辊的刮伤、烧伤。
此种压下装置在目前国内中板轧机中属先进水平行列。
1. 四辊可逆轧机技术规范
最大轧制压力:55000 KN
最大轧制力矩:2×1700 KN.m
轧制速度:0~±2.6~±6.3 m/s
轧辊最大开口度:280 mm
工作辊规格:Φ1000/Φ940×3000 mm
支撑辊规格:Φ1800/Φ1650×2800 mm
压下螺丝:S680×40 mm
压下总速比:14.49
压下速度:0~25/37 mm/s
机架立柱断面积:9000 cm2
机架窗口高度:7950 mm
机架窗口宽度:1850/1860 mm
二次除磷压力:19.6 MPa
冷却水压力: 1 MPa
各平衡缸压力:15/21 MPa
上工作辊平衡缸:4×Φ200/Φ140×373
下工作辊平衡缸:4×Φ170/Φ125×190
上支撑辊平衡缸:1×Φ450×475
压下电机:ZZJ820,N=320 KW,n=550/1100r/min
支撑辊轴承:ZYC1350-84KLH ,油膜轴承
2. 基本数据
⑴支撑辊光辊单重:G① = 82012 Kg
⑵油膜轴承重量:G② = 25065 Kg
⑶油膜轴承随动件:G③ = 12800 Kg
⑷上工作辊重量:G④ = 40578 Kg
⑸上支撑辊轴承座单重:G⑤ = 23300 Kg
⑺轧机导卫装置移动件单重:G⑥ = 24500 Kg
⑻平衡系统自重:G⑦ = 19420 Kg
压下装置的设计与计算
⑼AGC缸重量(一对):G⑧ = 12200 Kg
⑽压下螺丝及头部组件:G⑨ = 19292 Kg
3. 轧辊的平衡验算
⑴工作辊平衡力:
K1 = 11QG
Q1 = η1 F1 = η1nP421dπ= 0.85×4×10.2×15×420x2π= 163425.65 Kg G1 = G①+G③+G④ = 82012+12800+40578 = 135390
得K1 = 11QG = 135390163425.65 = 1.21
K1 —作辊的郭平衡系数,取1.1~1.3
Q1 —作辊平衡力,即平衡油缸所产的实际推力
F1 —作辊平衡油缸的理论推力
η1 —虑摩擦损失时,油缸的效率,可取0.85
G1 —被平衡的重量,包括上工作辊部件、上支撑辊光辊及随动件重量
⑵支撑辊平衡力:
K2 = 22QG
Q2 = η2 F2 = η2nP422dπ= 0.85×1×10.2×15×454x2π= 206835.59 Kg G2 = G②- G③+2×G⑤+G⑥+G⑦+G⑧+G⑨
= 25065-12800+2×23300+24500+19420+12200+19292= 134277 Kg 得K2 = 22QG = 134277206835.59 = 1.54
K2 —支撑辊的过平衡系数,取1.1~1.3
Q2 —支撑辊平衡力,即平衡油缸所产的实际推力
F2 —支撑辊平衡油缸的理论推力
η2 —考虑摩擦损失时,油缸的效率,可取0.85
G2 —被平衡的重量和
⑶总平衡力
K0 = 00QG = 2121GQQ++G =
134277135390206835.59163425.65++ = 1.37
K0 ——总的过平衡系数,取1.1~1.3
Q0 ——总平衡力,即所有平衡油缸所产的实际推力
G0 ——被平衡的总重量和
4. 压下装置的设计与计算
⑴压下装置的力能参数
a、确定作用于每个压下螺丝上的力
当轧辊提升时,P′= 21P0′= 21(F-μF-G)
式中
P0′——当轧辊提升时,作用在两个压下螺丝上的力
G ——被平衡件的总重量G = G0 = 269667 Kg
F ——油缸的理论推力,可表示为
F = P(421dπn1+422dπn2)
P ——油缸的工作压力
d1 n1——工作辊的平衡油缸柱塞直径和油缸数量
d2 n2——支撑辊的平衡油缸柱塞直径和油缸数量
μ ——油缸柱塞上的摩擦系数,取0.1~0.2
则F = 15×10.2×(420x2π×4+454x2π×1)= 435601.5 Kg
P = 21(0.9×435601.5-269667)=61187.2 Kg
当轧辊下降时,P″= 21P0″= 21(F+μF-G)= 21(1.2×435601.5-269667)=126527.4 Kg
b、确定作用在每个压下螺丝上的静力矩
当轧辊提升时,Mj′= 4d'Pp0- tg(.-a)+μ2″P0′4'dp
式中
P0′——当轧辊提升时,作用在两个压下螺丝上的力
dp ——螺纹的平均直径,dp = 68-0.75×4 = 65 cm
. ——螺纹中的摩擦角,.=tg-1μ1。