MLCC电容物理应力导致击穿问题案例
如何解决电容电应力及热应力造成的微裂纹等问题
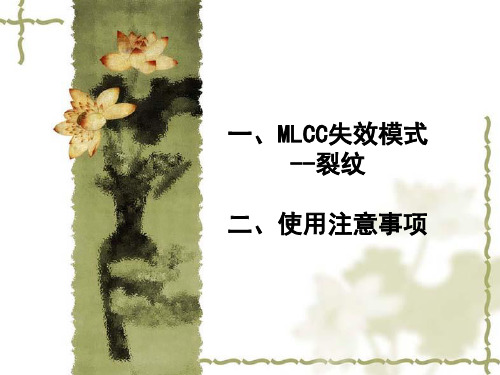
MLCC使用注意事项
焊接工艺
元件突然受热,会降低其机械强度。原因是较大的温度变化会导致 内部变形。为防止造成机械损坏,应对元件和PCB板进行预热。
MLCC使用注意事项
焊接工艺
1206及以上大规格不推荐波峰焊. ΔT≤150℃, 峰值温度≤270℃
MLCC使用注意事项
焊接工艺 :使用烙铁返修
最佳焊料量
MLCC使用注意事项
组装注意
以下动作都可能产生板弯曲从面导致电容 裂纹:
• 应力移动 • 贴装其他元件 • 将带引线的元件插在电路板上 • 安装/拆下插座 • 拧紧螺钉
MLCC使用注意事项
建议认真阅读MLCC供应商提 供的《MLCC使用注意事项》
Q&A Thank You !
一、MLCC失效模式 --裂纹
二、使用注意事项
MLCC失效模式之—裂纹
MLCC产品电性能优良,具有容量体积 比值大,适合SMT自动化工艺等优点,广 泛应用于各种电子产品中。
但因陶瓷材料本身较脆,且其电极和 瓷介质交替的内部结构,在使用时常因使 用时作业不当,容易导致产品漏电、无容 值、短路甚至烧毁等问题。
近些年,客户均已发现产品断裂可以通过PCB的 设计以及制程的管控来避免其发生。但仍存在一些产 品在使用中发现有小比例的断裂问题,而这些产品大 多是X7R材质的小容值产品。而X7R小容值产品易断 裂的根本原因是其机械强度较差。
MLCC失效模式之—裂纹
产品强度对比
MLCC失效模式之—裂纹
产品抗弯曲强度对比
波峰焊设备的制造商和用户现在能更好地掌控产生热冲击 的源头,大部分的波峰焊机器具有足够的预热控制且已经把裂 纹源头最小化(除大规格尺寸外,如1812(4525)以上,或是 厚型产品,厚度大于1.25mm)。
电容器凸底击穿的失效模式分析案例
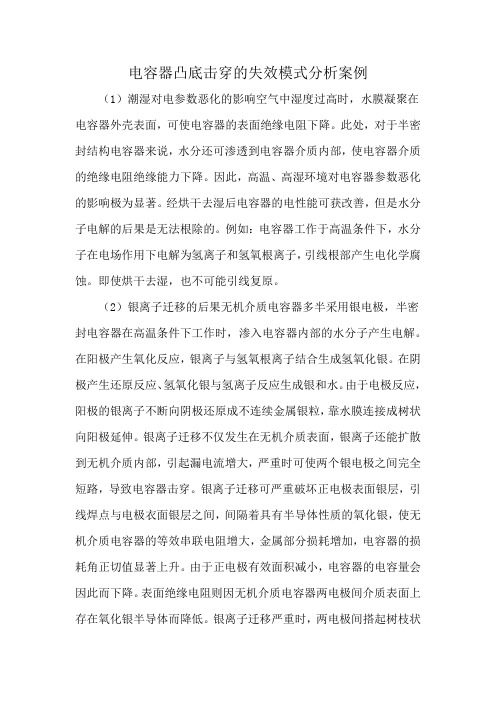
电容器凸底击穿的失效模式分析案例(1)潮湿对电参数恶化的影响空气中湿度过高时,水膜凝聚在电容器外壳表面,可使电容器的表面绝缘电阻下降。
此处,对于半密封结构电容器来说,水分还可渗透到电容器介质内部,使电容器介质的绝缘电阻绝缘能力下降。
因此,高温、高湿环境对电容器参数恶化的影响极为显著。
经烘干去湿后电容器的电性能可获改善,但是水分子电解的后果是无法根除的。
例如:电容器工作于高温条件下,水分子在电场作用下电解为氢离子和氢氧根离子,引线根部产生电化学腐蚀。
即使烘干去湿,也不可能引线复原。
(2)银离子迁移的后果无机介质电容器多半采用银电极,半密封电容器在高温条件下工作时,渗入电容器内部的水分子产生电解。
在阳极产生氧化反应,银离子与氢氧根离子结合生成氢氧化银。
在阴极产生还原反应、氢氧化银与氢离子反应生成银和水。
由于电极反应,阳极的银离子不断向阴极还原成不连续金属银粒,靠水膜连接成树状向阳极延伸。
银离子迁移不仅发生在无机介质表面,银离子还能扩散到无机介质内部,引起漏电流增大,严重时可使两个银电极之间完全短路,导致电容器击穿。
银离子迁移可严重破坏正电极表面银层,引线焊点与电极衣面银层之间,间隔着具有半导体性质的氧化银,使无机介质电容器的等效串联电阻增大,金属部分损耗增加,电容器的损耗角正切值显著上升。
由于正电极有效面积减小,电容器的电容量会因此而下降。
表面绝缘电阻则因无机介质电容器两电极间介质表面上存在氧化银半导体而降低。
银离子迁移严重时,两电极间搭起树枝状的银桥,使电容器的绝缘电阻大幅度下降。
综上所述,银离子迁移不仅会使非密封无机介质电容器电性能恶化,而且可能引起介质击穿场强下降,最后导致电容器击穿。
值得一提的是:银电极低频陶瓷独石电容器由于银离子迁移而引起失效的现象比其他类型的陶瓷介质电容器严重得多,原因在于这种电容器的一次烧成工艺与多层叠片结构。
银电极与陶瓷介质--次烧也过程中,银参与了陶瓷介质表面的固相反应,渗入了瓷银接触处形成界面层。
多层陶瓷电容破裂失效原因
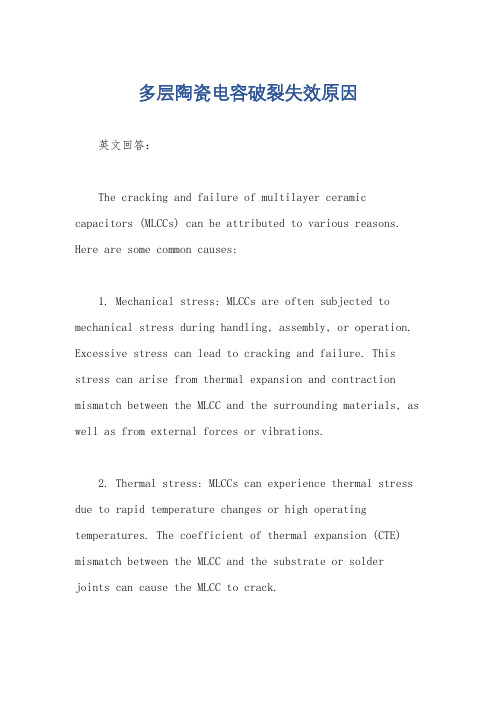
多层陶瓷电容破裂失效原因英文回答:The cracking and failure of multilayer ceramic capacitors (MLCCs) can be attributed to various reasons. Here are some common causes:1. Mechanical stress: MLCCs are often subjected to mechanical stress during handling, assembly, or operation. Excessive stress can lead to cracking and failure. This stress can arise from thermal expansion and contraction mismatch between the MLCC and the surrounding materials, as well as from external forces or vibrations.2. Thermal stress: MLCCs can experience thermal stress due to rapid temperature changes or high operating temperatures. The coefficient of thermal expansion (CTE) mismatch between the MLCC and the substrate or solderjoints can cause the MLCC to crack.3. Moisture and humidity: Ceramic materials are susceptible to moisture absorption. When moisture enters the MLCC, it can cause expansion and contraction during temperature cycling, leading to cracking and failure. Humidity can also cause corrosion of the internal electrodes, resulting in electrical failure.4. Manufacturing defects: MLCCs can have inherent defects introduced during the manufacturing process. These defects can include voids, delamination, or improper electrode connections. These defects can weaken the structural integrity of the MLCC and make it more susceptible to cracking and failure.5. Voltage and current overload: Exceeding the maximum voltage or current ratings of an MLCC can cause it to fail. High voltage or current can generate excessive heat, leading to thermal stress and cracking. It is important to operate MLCCs within their specified limits to avoid failure.中文回答:多层陶瓷电容破裂失效的原因有多种。
mlcc电容击穿短路原因
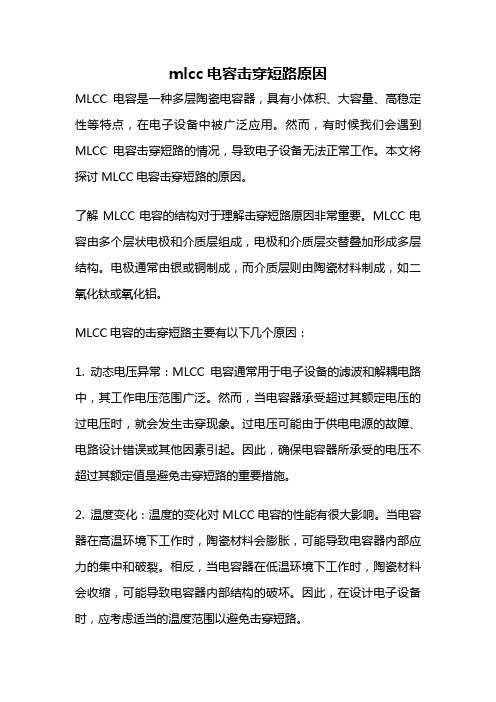
mlcc电容击穿短路原因MLCC电容是一种多层陶瓷电容器,具有小体积、大容量、高稳定性等特点,在电子设备中被广泛应用。
然而,有时候我们会遇到MLCC电容击穿短路的情况,导致电子设备无法正常工作。
本文将探讨MLCC电容击穿短路的原因。
了解MLCC电容的结构对于理解击穿短路原因非常重要。
MLCC电容由多个层状电极和介质层组成,电极和介质层交替叠加形成多层结构。
电极通常由银或铜制成,而介质层则由陶瓷材料制成,如二氧化钛或氧化铝。
MLCC电容的击穿短路主要有以下几个原因:1. 动态电压异常:MLCC电容通常用于电子设备的滤波和解耦电路中,其工作电压范围广泛。
然而,当电容器承受超过其额定电压的过电压时,就会发生击穿现象。
过电压可能由于供电电源的故障、电路设计错误或其他因素引起。
因此,确保电容器所承受的电压不超过其额定值是避免击穿短路的重要措施。
2. 温度变化:温度的变化对MLCC电容的性能有很大影响。
当电容器在高温环境下工作时,陶瓷材料会膨胀,可能导致电容器内部应力的集中和破裂。
相反,当电容器在低温环境下工作时,陶瓷材料会收缩,可能导致电容器内部结构的破坏。
因此,在设计电子设备时,应考虑适当的温度范围以避免击穿短路。
3. 设计和制造缺陷:MLCC电容的设计和制造缺陷也可能导致击穿短路。
例如,电极与陶瓷材料之间的黏结可能不够牢固,导致电容器内部结构的不稳定性。
此外,电容器的表面涂层如果不均匀或存在缺陷,也可能导致击穿短路。
因此,在选择和使用MLCC电容时,应选择质量可靠的产品,并确保其符合相关的标准和规范。
4. 电压梯度:电容器的电压梯度是指电容器两个电极之间的电位差。
当电压梯度超过电容器的承受能力时,就会发生击穿短路。
电压梯度的大小与电容器的尺寸和结构有关。
较大的电容器通常能够承受更高的电压梯度,而较小的电容器则容易发生击穿短路。
因此,在设计电子设备时,应根据实际需求选择合适尺寸的电容器,并确保电压梯度在可接受范围内。
MLCC失效分析全面案例课件
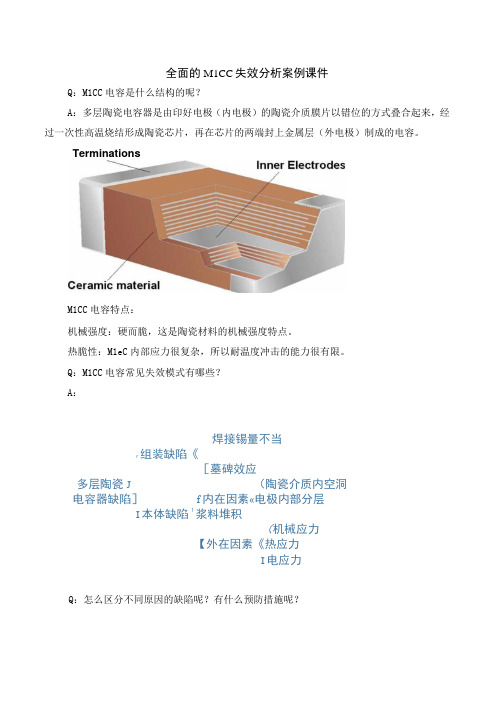
全面的M1CC失效分析案例课件Q:M1CC电容是什么结构的呢?A:多层陶瓷电容器是由印好电极(内电极)的陶瓷介质膜片以错位的方式叠合起来,经过一次性高温烧结形成陶瓷芯片,再在芯片的两端封上金属层(外电极)制成的电容。
TerminationsM1CC电容特点:机械强度:硬而脆,这是陶瓷材料的机械强度特点。
热脆性:M1eC内部应力很复杂,所以耐温度冲击的能力很有限。
Q:M1CC电容常见失效模式有哪些?A:焊接锡量不当r组装缺陷《[墓碑效应多层陶瓷J (陶瓷介质内空洞电容器缺陷]f内在因素«电极内部分层I本体缺陷1浆料堆积(机械应力【外在因素《热应力I电应力Q:怎么区分不同原因的缺陷呢?有什么预防措施呢?当温度发生变化时,过量的焊锡在贴片电容上产生很高的张力,会使电容内部断裂或者电容器脱帽,裂纹一般发生在焊锡少的一侧;焊锡量过少会造成焊接强度不足,电容从PCB板上脱离,造成开路故障。
2、墓碑效应(d)Norma1图3墓碑效应示意图在回流焊过程中,贴片元件两端电极受到焊锡融化后的表面张力不平衡会产生转动力矩,将元件一端拉偏形成虚焊,转动力矩较大时元件一端会被拉起,形成墓碑效应。
原因:本身两端电极尺寸差异较大;锡镀层不均匀;PCB板焊盘大小不等、有污物或水分、氧化以及焊盘有埋孔;锡膏粘度过高,锡粉氧化。
措施:①焊接之前对PCB板进行清洗烘干,去除表面污物及水分;②进行焊前检查,确认左右焊盘尺寸相同;③锡膏放置时间不能过长,焊接前需进行充分的搅拌。
本体缺陷一内在因素1、陶瓷介质内空洞图4陶瓷介质空洞图原因:①介质膜片表面吸附有杂质;②电极印刷过程中混入杂质;③内电极浆料混有杂质或有机物的分散不均匀。
2、电极内部分层图5电极内部分层原因:多层陶瓷电容器的烧结为多层材料堆叠共烧。
瓷膜与内浆在排胶和烧结过程中的收缩率不同,在烧结成瓷过程中,芯片内部产生应力,使M1CC产生再分层。
预防措施:在M1CC的制作中,采用与瓷粉匹配更好的内浆,可以降低分层开裂的风险。
MLCC破裂、短路案例分析
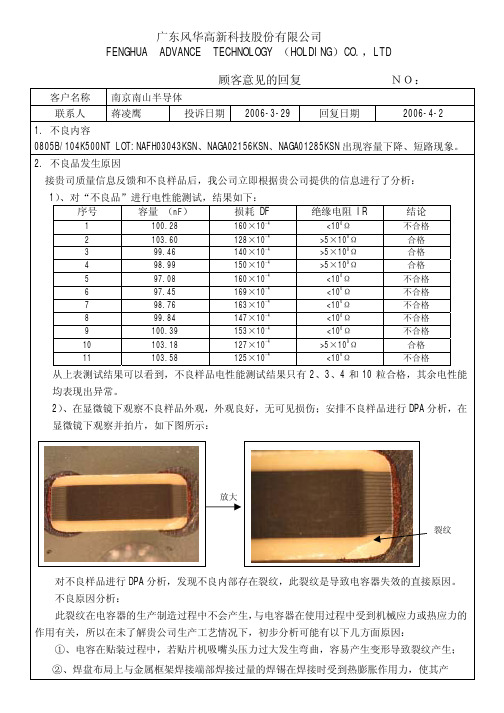
放大
裂纹
对不良样品进行 DPA 分析,发现不良内部存在裂纹,此裂纹是导致电容器失效的直接原因。 不良原因分析: 此裂纹在电容器的生产制造过程中不会产生, 与电容器在使用过程中受到机械应力或热应力的 作用有关,所以在未了解贵公司生产工艺情况下,初步分析可能有以下几方面原因: ①、电容在贴装过程中,若贴片机吸嘴头压力过大发生弯曲,容易产生变形导致裂纹产生; ②、焊盘布局上与金属框架焊接端部焊接过量的焊锡在焊接时受到热膨胀作用力,使其产
1 2 3 4 5 6 7 8 9 10 11 100.28 103.60 99.46 98.99 97.08 97.45 98.76 99.84 100.39 103.18 103.58 160×10 -4 128×10 -4 140×10 -4 150×10 -4 160×10 -4 169×10 -4 163×10 -4 147×10 -4 153×10 127×10 125×10
此裂纹在电容器的生产制造过程中不会产生与电容器在使用过程中受到机械应力或热应力的作用有关所以在未了解贵公司生产工艺情况下初步分析可能有以下几方面原因
广东风华高新科技股份有限公司 FENGHUA ADVANCE TECHNOLOGY (HOLDING)CO.,LTD 顾客意见的回复
客户名称 联系人 1. 不良内容 0805B/104K500NT LOT:NAFH03043KSN、NAGA02156KSN、NAGA01285KSN 出现容量下降、短路现象。 2. 不良品发生原因 接贵司质量信息反馈和不良样品后,我公司立即根据贵公司提供的信息进行了分析: 1) 、对“不良品”进行电性能测试,结果如下: 序号 容量 (nF) 损耗 DF
-4 -4 -4
NO:
回复日期 2006-4-2
MLCC电容物理应力导致击穿问题案例
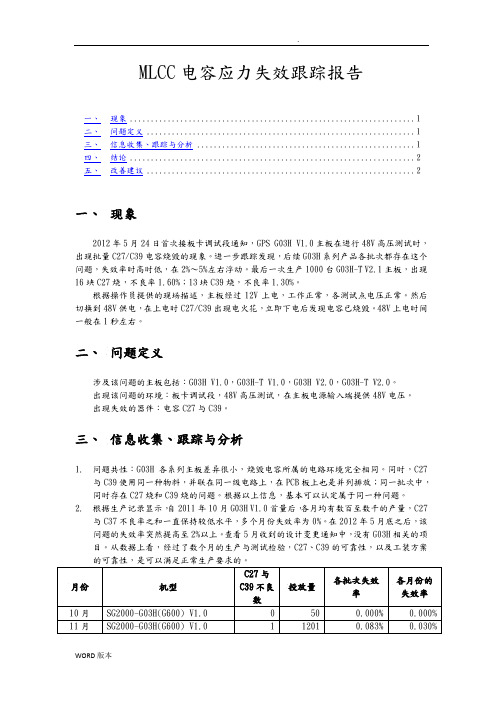
MLCC电容应力失效跟踪报告一、现象 (1)二、问题定义 (1)三、信息收集、跟踪与分析 (1)四、结论 (2)五、改善建议 (2)一、现象2012年5月24日首次接板卡调试段通知,GPS G03H V1.0主板在进行48V高压测试时,出现批量C27/C39电容烧毁的现象。
进一步跟踪发现,后续G03H系列产品各批次都存在这个问题,失效率时高时低,在2%~5%左右浮动。
最后一次生产1000台G03H-T V2.1主板,出现16块C27烧,不良率1.60%;13块C39烧,不良率1.30%。
根据操作员提供的现场描述,主板经过12V上电,工作正常,各测试点电压正常。
然后切换到48V供电,在上电时C27/C39出现电火花,立即下电后发现电容已烧毁。
48V上电时间一般在1秒左右。
二、问题定义涉及该问题的主板包括:G03H V1.0,G03H-T V1.0,G03H V2.0,G03H-T V2.0。
出现该问题的环境:板卡调试段,48V高压测试,在主板电源输入端提供48V电压。
出现失效的器件:电容C27与C39。
三、信息收集、跟踪与分析1.问题共性:G03H各系列主板差异很小,烧毁电容所属的电路环境完全相同。
同时,C27与C39使用同一种物料,并联在同一级电路上,在PCB板上也是并列排放;同一批次中,同时存在C27烧和C39烧的问题。
根据以上信息,基本可以认定属于同一种问题。
2.根据生产记录显示,自2011年10月G03H V1.0首量后,各月均有数百至数千的产量, C27与C37不良率之和一直保持较低水平,多个月份失效率为0%。
在2012年5月底之后,该问题的失效率突然提高至2%以上。
查看5月收到的设计变更通知中,没有G03H相关的项目。
从数据上看,经过了数个月的生产与测试检验,C27、C39的可靠性,以及工装方案的可靠性,是可以满足正常生产要求的。
3.C27与C39是104贴片瓷电容,耐压为50V,作为滤波电容使用。
MLCC电容环境失效案例解析
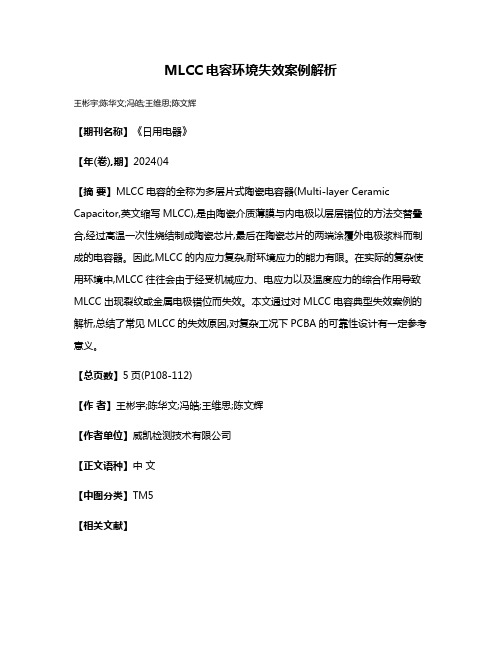
MLCC电容环境失效案例解析
王彬宇;陈华文;冯皓;王维思;陈文辉
【期刊名称】《日用电器》
【年(卷),期】2024()4
【摘要】MLCC电容的全称为多层片式陶瓷电容器(Multi-layer Ceramic Capacitor,英文缩写MLCC),是由陶瓷介质薄膜与内电极以层层错位的方法交替叠合,经过高温一次性烧结制成陶瓷芯片,最后在陶瓷芯片的两端涂覆外电极浆料而制成的电容器。
因此,MLCC的内应力复杂,耐环境应力的能力有限。
在实际的复杂使用环境中,MLCC往往会由于经受机械应力、电应力以及温度应力的综合作用导致MLCC出现裂纹或金属电极错位而失效。
本文通过对MLCC电容典型失效案例的解析,总结了常见MLCC的失效原因,对复杂工况下PCBA的可靠性设计有一定参考意义。
【总页数】5页(P108-112)
【作者】王彬宇;陈华文;冯皓;王维思;陈文辉
【作者单位】威凯检测技术有限公司
【正文语种】中文
【中图分类】TM5
【相关文献】
1.AP14可调电容器瞬间短路的典型失效案例分析
2.铅系多层陶瓷电容器(MLCCs)三层镀失效机理的研究
3.从铝电解电容典型失效案例分析看品质提升
4.MLCC电
容失效分析总结5.薄膜电容器在节能灯上的应用及失效案例分析
因版权原因,仅展示原文概要,查看原文内容请购买。
- 1、下载文档前请自行甄别文档内容的完整性,平台不提供额外的编辑、内容补充、找答案等附加服务。
- 2、"仅部分预览"的文档,不可在线预览部分如存在完整性等问题,可反馈申请退款(可完整预览的文档不适用该条件!)。
- 3、如文档侵犯您的权益,请联系客服反馈,我们会尽快为您处理(人工客服工作时间:9:00-18:30)。
MLCC电容应力失效跟踪报告
一、现象 (1)
二、问题定义 (1)
三、信息收集、跟踪与分析 (1)
四、结论 (2)
五、改善建议 (2)
一、现象
2012年5月24日首次接板卡调试段通知,GPS G03H V1.0主板在进行48V高压测试时,出现批量C27/C39电容烧毁的现象。
进一步跟踪发现,后续G03H系列产品各批次都存在这个问题,失效率时高时低,在2%~5%左右浮动。
最后一次生产1000台G03H-T V2.1主板,出现16块C27烧,不良率1.60%;13块C39烧,不良率1.30%。
根据操作员提供的现场描述,主板经过12V上电,工作正常,各测试点电压正常。
然后切换到48V供电,在上电时C27/C39出现电火花,立即下电后发现电容已烧毁。
48V上电时间一般在1秒左右。
二、问题定义
涉及该问题的主板包括:G03H V1.0,G03H-T V1.0,G03H V2.0,G03H-T V2.0。
出现该问题的环境:板卡调试段,48V高压测试,在主板电源输入端提供48V电压。
出现失效的器件:电容C27与C39。
三、信息收集、跟踪与分析
1.问题共性:G03H各系列主板差异很小,烧毁电容所属的电路环境完全相同。
同时,C27
与C39使用同一种物料,并联在同一级电路上,在PCB板上也是并列排放;同一批次中,同时存在C27烧和C39烧的问题。
根据以上信息,基本可以认定属于同一种问题。
2.根据生产记录显示,自2011年10月G03H V1.0首量后,各月均有数百至数千的产量,C27
与C37不良率之和一直保持较低水平,多个月份失效率为0%。
在2012年5月底之后,该问题的失效率突然提高至2%以上。
查看5月收到的设计变更通知中,没有G03H相关的项目。
从数据上看,经过了数个月的生产与测试检验,C27、C39的可靠性,以及工装
3.C27与C39是104贴片陶瓷电容,耐压为50V,作为滤波电容使用。
48V上电时,实测电
容两端波峰最高不超过46V,稳定在36V,下电时不会造成更高的电压冲击。
因此电压设计是符合要求的。
4.将坏板上的C27、C39电容取下,手工焊上新领的同种物料,进行48V开关机实验,重复
50次,问题不复现。
继续持续48V供电半小时,问题不复现。
基本可以排除由于主板上其他器件不良导致C27/C39烧毁的可能性。
5.对经过12V测试的主板进行筛选,筛选后的主板再进行48V测试。
筛选的方案是使用小
型显微镜观察电容上表面。
筛选后未发现异常,但随后的高压测试中仍有烧毁的情况。
具体分析参见本文结尾附录。
6.对出现问题的主板,拆下烧毁电容(c29或c37)之外的另一个电容,绝大多数都出现外
部金属电极与陶瓷介质剥离的现象,但是在拆下之前外观无异常。
和维修确认,该现象从5月底开始一直存在。
当一个电容烧毁时,导致或者是同时出现另一个电容裂开的可能性很低。
因此应该是在烧毁之前电容就已经开裂。
较为合理的解释是,两个电容事先出现开裂,导致耐压系数降低,在12V时可以工作,但是高压测试时一个电容先被击穿。
7.为了确认在哪一道工序出现异常,申请安排了200台的任务,在生产的各段设置了全检
测试项目,进行线上全程跟踪把关。
在跟踪检测时未发现任何电容异常。
目前这200台主板已经全部通过高压测试,没有出现一例C27/C39烧的情况。
这批任务与最后的1000台的物料清单一致。
四、结论
从线上跟踪的结果来看,200台主板中没有一例电容烧毁,说明该问题不是由于产品设计或是工装方案导致,暂时无法确认电容异常是从哪一道工序开始出现。
五、改善建议
为了避免在后续生产中再次出现C27、C39电容烧毁问题,整理了一些建议,请各部门评估可行性。
1.已经决定后续采用更高耐压值的电容。
请考虑更改PCB布局,尽量减少板边的陶瓷
电容。
如果无法移开,应将电容的方向与板边保持平行。
2.G03H的PCB板两边是邮票口,目前使用斜口钳掰板。
需要制作分板工装,使用分板
机自动分板。
3.在GPS/GSM/CDMA天线头处包上醋酸胶带或橡胶套,进行绝缘保护。
4.确保生产过程中的温升速度在合理范围内,避免快速的升温/降温对器件造成影响。
附录——G03H故障板烧电容C27及C39现象分析(新)
针对SG2000-G03H(G600)V1.0故障板烧电容C27及C39现象初步分析:
1.经询调试板状态上电过程烧毁C27(104/50V 1206)或C39(104/50V 1206)(多层、积层、叠层)片式陶瓷电容器,不存在上电时间长短或12VDC与48VDC切换状态损坏特性。
图一:故障点局部电路
借用12块烧电容故障板及正常板2块做对比试验。
用简易放大镜约30X从物理表面观察故障板(板号F51100026/019/025/068/086/228/229/230/129/130在C27、C39中间处都有裂痕(非烧黑处),其中两块058/232烧的比较严重无法观察。
图二C27电容红圈处断裂
图三C39电容断裂处(红圈处),
图四:C39边缘处烧焦(红圈处)。
而正常F51020780/488两块板电容无裂痕。
经查询对比两种传票号板电容物料有存在两种物料混用的情况,C27/C39旧物料CM0150M073(拆下测量厚实测0.76)和新领物料CM0050M028(厚实测0.74)。
2.以上结论再进一步从电路上做破坏性试验来验证是外力导致还是本身电路或器件引起的烧毁。
电路试验测试:领新物料电容(料号CM0050M028)换上G03板上开关机供电冲击50次,在外电50V供电情况下电容并没有出现异常,实测电源经过前级后到C27和C39端电压就
37.3V-37.5V左右,不存在电流冲击损坏的情况。
在后续观察跟踪中发现同块板烧掉一个电容时,而另一个电容外观完好用烙铁轻轻焊下就已经在端头断裂情况,连续几块板都是如此状况。
附断裂电容图:
图五(电容无烧毁痕迹金属电极与陶瓷介质剥离)图六
图七
并附上G01H电容烧毁现象引用参考:针对现场的测试工装、电源等进行了比测,未发现异常,对库里电容抽100个进行耐压测试正常,但与现场FA技术人员等随机抽20多块板发现有三块板C44电容上有裂纹,各带走一块故障板,带回的故障板电容破裂情况见下图
对破裂的电容进行上电耐压测试,12V起步/1V为单位步进上电,当电压到31V时,上电电容即冒火花烧毁!即,电容是为“过压”烧,但前因是电容因受机械应力导致参数下降(50V的耐压下降到31V)。
后续隐患存在及个人建议:是不是有很多产品是在电容开裂的情况下出货,而这些产品大多数并不是工作在12VDC以上工作环境,表明上看起来工作是“很”正常。
附上烧毁后电容图如下:
3.破坏测试:
领PCB空板8拼1块焊上电容做掰板动作,也没有出现电容裂痕情况,由于今天产线没有排场SG2000-G03H(G600)生产,无法从制程上追溯故障产生原因。
(在6月23号安排200套生产,各段除正常生产调试外,额外设置了针对C27/C39两
端加强36VDC全检测试项目,测试进行线上全程跟踪把关,并没有出现烧电容现象。
)基于以上现象分析从可靠性角度说,是属于机械应力或热冲击失效后导致烧毁,不可能由电路性能上引起烧毁器件。
后续建议:对G03H电容C27 C39改用不同规格封装来避免出现由于CM0050M028厚度较薄导致物理应力损伤,也可考虑更改PCB布局来改变C27 C39放置方向避免生产过程导致电容损伤。
实验分析
2012年。