PCD刀具的特点及其使用方法介绍
PCD双刃刀加工参数表

PCD双刃刀加工参数表
1、PCD刀具介绍
金刚石作为一种超硬刀具材料已广泛应用于切削加工,天然金刚石价格昂贵限制了金刚石刀具的发展,20世纪70年代,人们利用高压合成技术合成了聚晶金刚石(PCD),解决了天然金刚石数量稀少、价格昂贵的问题,使金刚石刀具的应用范围扩展到航空、航天、汽车、电子、石材等多个领域。
聚晶金刚石(PCD)刀具主要用于加工有色金属等非黑色金属,
能够刃磨出很锋利的刃口,得到较好的加工表面,而且还是加工非金属新型材料的首选材料,可以切削硬质合金及工业陶瓷等高硬度产品。
2、PCD刀具的性能优势
(1)PCD的硬度可达8000HV,为硬质合金的80~120倍,而且PCD的耐磨性更好。
(2)PCD的导热系数为700W/MK,为硬质合金的1.5~9倍,甚
至高于PCBN和铜。
因此PCD刀具热量传递迅速,良好的传热性在很
大程度上能够延长刀具寿命。
(3)PCD的摩擦系数一般仅为0.1至0.3,而硬质合金的摩擦系数为0.4~1。
因此PCD刀具可显著减小切削力,从而延长了刀具寿命。
(4)PCD的热膨胀系数小,因此PCD刀具热变形小,加工精度高。
刀具热变形越大,加工出的工件表面质量就越差,要想加工出良好加工表面质量的工件就必须严格控制刀具的热变形。
(5)PCD刀具与有色金属和非金属材料的亲和力小,在加工过程中刀尖不易形成积屑瘤。
刀具与被加工材料的亲和力小,那么在加工过程中被加工材料就不容易粘接在刀具表面,也就不容易形成积屑瘤。
(6)PCD刀具的弹性模量大,断裂强度高(比氧化铝高三倍),切削刃钝圆半径值可以磨得很小,不易断裂,能长期保持切削刃的锋利程度。
金刚石(pcd)铰刀的优势特点
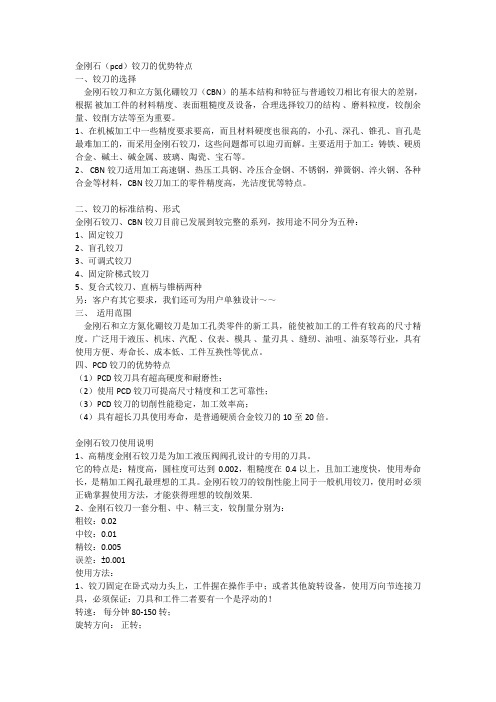
金刚石(pcd)铰刀的优势特点一、铰刀的选择金刚石铰刀和立方氮化硼铰刀(CBN)的基本结构和特征与普通铰刀相比有很大的差别,根据被加工件的材料精度、表面粗糙度及设备,合理选择铰刀的结构、磨料粒度,铰削余量、铰削方法等至为重要。
1、在机械加工中一些精度要求要高,而且材料硬度也很高的,小孔、深孔、锥孔、盲孔是最难加工的,而采用金刚石铰刀,这些问题都可以迎刃而解。
主要适用于加工:铸铁、硬质合金、碱土、碱金属、玻璃、陶瓷、宝石等。
2、CBN铰刀适用加工高速钢、热压工具钢、冷压合金钢、不锈钢,弹簧钢、淬火钢、各种合金等材料,CBN铰刀加工的零件精度高,光洁度优等特点。
二、铰刀的标准结构、形式金刚石铰刀、CBN铰刀目前已发展到较完整的系列,按用途不同分为五种:1、固定铰刀2、盲孔铰刀3、可调式铰刀4、固定阶梯式铰刀5、复合式铰刀、直柄与锥柄两种另:客户有其它要求,我们还可为用户单独设计~~三、适用范围金刚石和立方氮化硼铰刀是加工孔类零件的新工具,能使被加工的工件有较高的尺寸精度。
广泛用于液压、机床、汽配、仪表、模具、量刃具、缝纫、油咀、油泵等行业,具有使用方便、寿命长、成本低、工件互换性等优点。
四、PCD铰刀的优势特点(1)PCD铰刀具有超高硬度和耐磨性;(2)使用PCD铰刀可提高尺寸精度和工艺可靠性;(3)PCD铰刀的切削性能稳定,加工效率高;(4)具有超长刀具使用寿命,是普通硬质合金铰刀的10至20倍。
金刚石铰刀使用说明1、高精度金刚石铰刀是为加工液压阀阀孔设计的专用的刀具。
它的特点是:精度高,圆柱度可达到0.002,粗糙度在0.4以上,且加工速度快,使用寿命长,是精加工阀孔最理想的工具。
金刚石铰刀的铰削性能上同于一般机用铰刀,使用时必须正确掌握使用方法,才能获得理想的铰削效果.2、金刚石铰刀一套分粗、中、精三支,铰削量分别为:粗铰:0.02中铰:0.01精铰:0.005误差:±0.001使用方法:1、铰刀固定在卧式动力头上,工件握在操作手中;或者其他旋转设备,使用万向节连接刀具,必须保证:刀具和工件二者要有一个是浮动的!转速:每分钟80-150转;旋转方向:正转;冷却液:为煤油或柴油(比例一般为80%煤油加20%机油);开关:用脚踏开关控制关停(或者有人配合关机)。
PCD刀具介绍
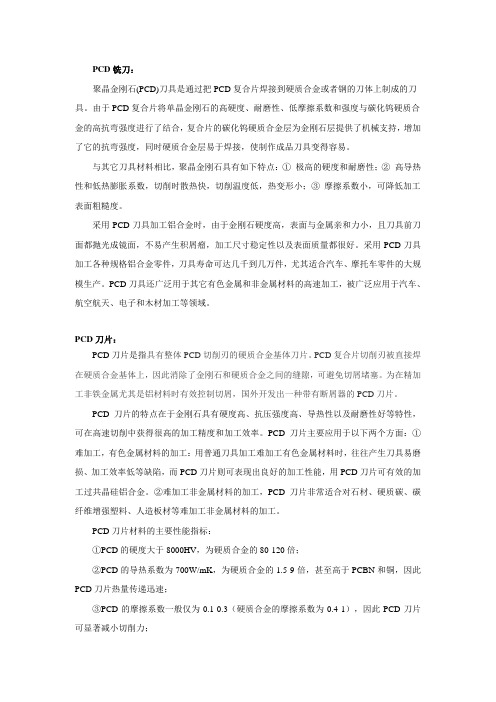
PCD铣刀:聚晶金刚石(PCD)刀具是通过把PCD复合片焊接到硬质合金或者钢的刀体上制成的刀具。
由于PCD复合片将单晶金刚石的高硬度、耐磨性、低摩擦系数和强度与碳化钨硬质合金的高抗弯强度进行了结合,复合片的碳化钨硬质合金层为金刚石层提供了机械支持,增加了它的抗弯强度,同时硬质合金层易于焊接,使制作成品刀具变得容易。
与其它刀具材料相比,聚晶金刚石具有如下特点:① 极高的硬度和耐磨性;② 高导热性和低热膨胀系数,切削时散热快,切削温度低,热变形小;③ 摩擦系数小,可降低加工表面粗糙度。
采用PCD刀具加工铝合金时,由于金刚石硬度高,表面与金属亲和力小,且刀具前刀面都抛光成镜面,不易产生积屑瘤,加工尺寸稳定性以及表面质量都很好。
采用PCD刀具加工各种规格铝合金零件,刀具寿命可达几千到几万件,尤其适合汽车、摩托车零件的大规模生产。
PCD刀具还广泛用于其它有色金属和非金属材料的高速加工,被广泛应用于汽车、航空航天、电子和木材加工等领域。
PCD刀片:PCD刀片是指具有整体PCD切削刃的硬质合金基体刀片。
PCD复合片切削刃被直接焊在硬质合金基体上,因此消除了金刚石和硬质合金之间的缝隙,可避免切屑堵塞。
为在精加工非铁金属尤其是铝材料时有效控制切屑,国外开发出一种带有断屑器的PCD刀片。
PCD刀片的特点在于金刚石具有硬度高、抗压强度高、导热性以及耐磨性好等特性,可在高速切削中获得很高的加工精度和加工效率。
PCD刀片主要应用于以下两个方面:①难加工,有色金属材料的加工:用普通刀具加工难加工有色金属材料时,往往产生刀具易磨损、加工效率低等缺陷,而PCD刀片则可表现出良好的加工性能,用PCD刀片可有效的加工过共晶硅铝合金。
②难加工非金属材料的加工,PCD刀片非常适合对石材、硬质碳、碳纤维增强塑料、人造板材等难加工非金属材料的加工。
PCD刀片材料的主要性能指标:①PCD的硬度大于8000HV,为硬质合金的80-120倍;②PCD的导热系数为700W/mK,为硬质合金的1.5-9倍,甚至高于PCBN和铜,因此PCD刀片热量传递迅速;③PCD的摩擦系数一般仅为0.1-0.3(硬质合金的摩擦系数为0.4-1),因此PCD刀片可显著减小切削力;④PCD的热膨胀系数仅为0.9*10-6-1.18*10-6,仅相当于硬质合金的1/5,因此PCD刀片热变形小,加工精度高;⑤PCD刀片与有色金属和非金属材料的亲和力很小,在加工过程中切屑不易粘结在刀尖上形成积屑瘤。
pcd成型刀是什么意思

pcd成型刀是什么意思
pcd成型刀是指根据产品特殊恳求,需求产品外形的刀具,经过刀具的外形来确保加工出来的零件的外形,可以一次性成型。
比如现代汽车变速箱的设计思索到减轻重量和多功用化的恳求,越来越多地采用压铸铝合金来制造外形复杂的变速箱体,其上设置有许多阶梯状的成型孔,这些成型孔对表面粗糙度、圆度、圆柱度、同心度、无毛刺等质量恳求非常严厉,因此需求pcd成型刀来加工,可以保证质量。
威士PCD成型刀-阶梯铰刀的特性
1、威士PCD成型刀具,基体可采用硬质合金或钢制基体
2、PCD铰刀具有加工精度高,加工,性和导热性强,韧性强的特性。
3、刀具可定制断屑槽,改善缠屑问题
4、PCD铰刀可完成高速切削和硬质材料切削。
5、PCD铰刀加工工件表面粗糙度比普通硬质合金铰刀更好。
6、PCD铰刀运用寿命长。
其运用寿命是普通硬质合金铰刀的10至20倍。
7、可针对不同加工材质和工况设计不同PCD材质
8、可提供返修及换片效劳,降低运用本钱。
金刚石(PCD)铰刀的产品介绍及应用

量,是对金刚石铰刀寿命有很大的影响。 ⑥ 前导向部:前导部是考虑与加工前的孔,其中最小间隙为10--20米欧。
同时还需要注意冷却槽的设计 金刚石铰刀铰孔时,若热量和切屑来不及排出,刀体将发热膨胀,孔的加工质量会明显降低,严重时还会发生“咬死”刀现象。
内镀法
金刚石铰刀内镀的方法: 采用稳定材料制造一个与铰刀外形相反的
高精度内孔胎模,将金刚石磨粒电镀在胎模内表 面,加厚形成电镀层,再将镀层与刀杆粘结在一 起。
金刚石颗粒的顶端整齐,规则地排列在模具 的内表面上,等高性和均匀性较好;
无需修磨,微刃锋利;
所加工孔的尺寸精度和几何精度较高,表面 粗糙度较小,使用寿命较长。
2 PCD铰刀
PCD铰刀的定义及优势
PCD铰刀,一般根据直径大小,采用合金基体或者钢制基体。刃数为2刃或2刃以上。此类刀具主要用于加工公 差要求比较严格,光洁度要求比较高的孔,通孔盲孔均可加工。此类刀具加工的孔,光洁度最高可达Ra0.1以内。
PCD铰刀的优势
具有超高硬度和耐磨性; 具有超长刀具使用寿命; 切削性能稳定,加工效率高; 提高尺寸精度和工艺可靠性。
备注:一般直径15mm左右的可以做成可调式金刚石铰刀,但由于国内市场,可调式金刚石铰刀精度没有固定时金刚 石铰刀好,如果要求精度较高的情况下, 建议选择固定式金刚石铰刀
金刚石铰刀的组成结构及优势
金刚石铰刀的优势
镀层结合力,金刚石粘结牢度,金刚石颗粒分布均匀,外观质量高; 金刚石铰刀前后导向外圆度达到0.005mm,圆柱度为0.005mm/100mm,前导向外圆粗糙度Ra0.63微米, 后导向外圆粗糙度Ra0.16um,刀柄与前后导向部分的同轴度达到0.015mm; 被铰孔工件圆柱度小于0.003,粗糙度可达Ra0.4-0.2,精度高,效率高,使用寿命长; “量体裁衣”式服务,规范化流程,为客服创造的价值超越契约。
PCD刀具刃磨

PCD刀具刃磨PCD复合片的硬度一般在HV4500HV8000之间,仅次于金刚石的硬度(HV9000),同时其硬度因生产厂或牌号的不同而不同。
因此,如何解决PCD刀具的刃磨题目是加工、使用PCD刀具的关键。
目前有两种PCD刀具常用刃磨方法:金刚石砂轮刃磨法采用金刚石砂轮来刃磨PCD刀具,对所用机床要求较高:机床系统刚性好,进给机构精度高,有微进给机构,重复精度高,磨头往复摆动平稳无冲击,同时还需选用合适的金刚石砂轮。
瑞士EWAG公司生产的RS系列机床尤其是RS15机床具有精度高、附件多并带有刃磨PCD刀具(带HSK刀柄)的附件等特点,是PCD刀具刃磨机床的代表。
采用RS15机床刃磨PCD刀具,刀具尺寸精度可达0.001mm,表面粗糙度可达Ra0.08左右。
电蚀刃磨法电蚀刃磨是将工件(PCD刀具)和电蚀轮(或钼丝)形成正负电极,通过正负电极间放电,达到往除PCD的效果。
电蚀刃磨法的PCD往除效果取决于电蚀轮(或钼丝)与PCD刀具刃口间的间隙、走刀进给速度以及电压高低、电流大小等。
电蚀刃磨机床的特点是生产效率高,尺寸精度一般在.0.01mm 左右,表面粗糙度在Ra0.25左右。
德国VOLLMER公司的QM和QW系列机床是采用电蚀法刃磨PCD刀具的代表,其中的新产品Q和QWD760都是五轴联动数控机床。
Q是轮电蚀刃磨机床,用于直线形刃口的PCD 刀具电蚀刃磨。
QWD760是线电蚀刃磨机床,用于各种曲线形刃口的PCD刀具电蚀刃磨。
根据不同机床刃磨PCD刀具的适应范围,一般说来,对尺寸精度和表面粗糙度要求高的PCD铰刀、镗刀等,在RS15等机床上用金刚石砂轮刃磨;对PCD铣刀、锯片和PCD木工刀具等,用Q或QWD760机床进行电蚀刃磨,而用于强化地板开榫的PCD刀具和各种曲线外形的PCD刀具,则采用QWD760机床电蚀刃磨。
pcd刀片切削参数

pcd刀片切削参数PCD刀片切削参数PCD刀片是一种具有超硬度和高热稳定性的切削工具,广泛应用于高效精密切削加工中。
为了获得最佳的切削效果,合理选择和控制PCD刀片的切削参数至关重要。
本文将从切削速度、进给速度、切削深度和切削角度四个方面介绍PCD刀片的切削参数。
一、切削速度切削速度是指PCD刀片在单位时间内切削边缘通过的距离。
切削速度的选择应根据被加工材料的硬度、切削方式和刀具磨损情况等因素进行综合考虑。
一般来说,对于高硬度材料,切削速度应较低;对于低硬度材料,切削速度可以适当提高。
在选择切削速度时,还需考虑刀具的耐用性和切削表面质量。
二、进给速度进给速度是指PCD刀片在单位时间内切削边缘与被加工材料之间的相对运动速度。
进给速度的选择应根据被加工材料的硬度、切削方式和刀具磨损情况等因素进行综合考虑。
一般来说,对于高硬度材料,进给速度应较低;对于低硬度材料,进给速度可以适当提高。
进给速度过高会导致切削力过大,影响刀具寿命;进给速度过低则会降低生产效率。
三、切削深度切削深度是指PCD刀片切削时刀具与被加工材料间的垂直距离。
切削深度的选择应根据被加工材料的硬度、切削方式和刀具磨损情况等因素进行综合考虑。
一般来说,对于高硬度材料,切削深度应较小;对于低硬度材料,切削深度可以适当增大。
切削深度过大会导致刀具受力过大,容易断裂;切削深度过小则会降低切削效率。
四、切削角度切削角度是指PCD刀片切削边缘与被加工材料表面之间的夹角。
切削角度的选择应根据被加工材料的硬度、切削方式和刀具磨损情况等因素进行综合考虑。
一般来说,对于高硬度材料,切削角度应较小;对于低硬度材料,切削角度可以适当增大。
切削角度过小会导致刀具受力集中,容易产生刀具磨损和断裂;切削角度过大则会增加切削力和摩擦,影响切削表面质量。
PCD刀片的切削参数包括切削速度、进给速度、切削深度和切削角度。
合理选择和控制这些切削参数可以提高切削效率、延长刀具寿命和提高加工质量。
石材雕刻机之PCD刀具的使用

石材雕刻机之PCD刀具的使用石材雕刻机之PCD粒度的选择与刀具加工条件有关,如设计用于精加工或超精加工的刀具时,应选用强度高、韧性好、抗冲击性能好、细晶粒的PCD。
粗晶粒PCD刀具则可用于一般的粗加工。
PCD材料的粒度对于刀具的磨损和破损性能影响显著。
研究表明:PCD粒度号越大,刀具的抗磨损性能越强。
采用DeBeers 公司SYNDITE 002和SYNDITE025两种PCD材料的刀具加工SiC基复合材料时的刀具磨损试验结果表明,粒度为2µm的SYNDITE002PCD材料较易磨损。
合理选择PCD刀片厚度通常情况下,PCD复合片的层厚约为0.3∼1.0mm,加上硬质合金层后的总厚度约为2∼8mm。
较薄的PCD层厚有利于刀片的电火花加工。
DeBeers公司推出的0.3mm厚PCD复合片可降低磨削力,提高电火花的切割速度。
PCD复合片与刀体材料焊接时,硬质合金层的厚度不能太小,以避免因两种材料结合面间的应力差而引起分层。
刀具几何参数与结构设计石材雕刻机之PCD刀具的几何参数取决于工件状况、刀具材料与结构等具体加工条件。
由于PCD刀具常用于工件的精加工,切削厚度较小(有时甚至等于刀具的刃口半径),属于微量切削,因此其后角及后刀面对加工质量有明显影响,较小的后角、较高的后刀面质量对于提高PCD刀具的加工质量可起到重要作用。
PCD复合片与刀杆的连接方式包括机械夹固、焊接、可转位等多种方式。
PCD复合片与刀杆连接方式的特点与应用连接方式-特点-应用范围:机械夹固-由标准刀体及可做成各种集合角度的可换刀片组成,具有快换和便于重磨的优点-中小型机床,整体焊接-结构紧凑、制作方便,可制成小尺寸刀具-专用刀具或难于机夹的刀具,用于小型机床,机夹焊接-刀片焊接于刀头上,可使用标准刀杆,便于刃磨及调整刀头位置-自动机床、数控机床,可转位-结构紧凑,夹紧可靠,不需重磨和焊接,可节省辅助时间,提高刀具寿命-普通通用机床,石材雕刻机之PCD刀具的切削参数与失效机理.PCD刀具切削参数对切削性能的影响①切削速度石材雕刻机之PCD刀具可在极高的主轴转速下进行切削加工,但切削速度的变化对加工质量的影响不容忽视。
- 1、下载文档前请自行甄别文档内容的完整性,平台不提供额外的编辑、内容补充、找答案等附加服务。
- 2、"仅部分预览"的文档,不可在线预览部分如存在完整性等问题,可反馈申请退款(可完整预览的文档不适用该条件!)。
- 3、如文档侵犯您的权益,请联系客服反馈,我们会尽快为您处理(人工客服工作时间:9:00-18:30)。
PCD刀具的特点及其使用方法介绍
PCD刀具的特点及其使用方法介绍
价格变化
过去,价格昂贵一直是影响用户广泛接受PCD(聚晶金刚石)刀具的一个主要障碍,但现在情况发生了很大变化。
业界估计,在过去的两三年中,PCD刀具的价格已下降了40~60。
出现PCD刀具价格"跳水"的原因之一是市场供大于求。
在20世纪90年代初,PCD刀具的发展势头开始超过传统的硬质合金刀具,在随后的十年中,对PCD刀具的市场需求不断增加。
但是,随着PCD刀具制造技术的成熟,其销售增长势头开始减缓。
此外,新进入PCD刀具制造业的竞争者也动摇了原有的市场价格体系。
PCD刀具价格下降的另一个原因是刀具制造成本不断降低,刀具制造工艺(如用于金刚石毛坯粗加工的EDM工艺、切削刃精密加工工艺等)不断改进。
此外,与十年前相比,加工PCD刀具用的金刚石砂轮质量显著提高,成本则大大下降。
我国对PCD刀具的需求不断增加。
刀具特点
用PCD刀具加工铝制工件具有刀具寿命长、金属切除率高等优点,其缺点是刀具价格昂贵,加工成本高。
这一点在机械制造业已形成共识。
但近年来PCD刀具的发展与应用情况已发生了许多变化。
如今的铝材料在性能上已今非昔比,在加工各种新开发的铝合金材料(尤其是高硅含量复合材料)时,为了实现生产率及加工质量的最优化,必须认真选择PCD刀具的牌号及几何参数,以适应不同的加工要求。
PCD刀具的另一个变化是加工成本不断降低,在市场竞争压力和刀具制造工艺改进的共同作用下,PCD刀具的价格已大幅下降50以上。
上述变化趋势导致PCD刀具在铝材料加工中的应用日益增多,而刀具的适用性则受到不同被加
工材料的制约。
正确使用
切削加工铝合金材料时,硬质合金刀具的粗加工切削速度约为120m/min,而PCD刀具即使在粗加工高硅铝合金时其切削速度也可达到约360m/min。
刀具制造商推荐采用细颗粒(或中等颗料)PCD牌号加工无硅和低硅铝合金材料。
采用粗颗粒PCD牌号加工高硅铝合金材料。
如铣削加工的工件表面光洁度达不到要求,可采用晶粒尺寸较小的修光刀片对工件表面进行修光加工,以获得满意的表面光洁度。
PCD刀具的正确应用是获得满意加工效果的前提。
虽然刀具失效的具体原因各不相同,但通常是由于使用对象或使用方法不正确所致。
用户在订购PCD刀具时,应正确把握刀具的适应范围。
例如,用PCD刀具加工黑色金属工件(如不锈钢)时,由于金刚石极易与钢中的碳元素发生化学反应,将导致PCD刀具迅速磨损,因此,加工淬硬钢的正确选择应该是PCBN刀具。
一般来说,为了减小切削力,防止产生积屑瘤,PCD刀具应采用正切削角。
但在加工高硅铝合金时(尤其在用PCD刀具替代硬质合金刀具进行加工时),PCD刀具的后角最好比原硬质合金刀具采用的后角(如250)略微减小,以改善PCD刀具切削刃对高硅铝合金的切削性能。
PCD刀具的正前角也不宜过大,因为刀具前角越大,其切削刃强度越低,换句话说,PCD刀具的后角越小,切削刃的强度越高。
为了在保证刀具为正切削角的前提下尽可能提高切削刃强度,美国一家公司将具有负前角的CNMX刀片焊接在PCD刀具刀尖部位并形成正切削角,这样,刀片的负前角既提供了较高的切削刃强度,又不会影响刀具的正常切削。
制备PCD 刀具切削刃时,不需对金刚石刀尖作过多工艺处理,对于PCD铣刀,可对切削刃进行轻微刃磨,此外,使切削刃产生一定的轴向倾角也有助于提高PCD刀具的切削性能。
PCD刀片的成功应用不仅仅取决于合理选用刀具几何参数和切削参数,有时还需要刀具供应商对刀具使用中遇到的问题提供解决方案。
例如,某大型汽车零件加工车间采用J&M金刚石工具公司提供的PCD刀片进行铣槽加工,原来每片PCD金刚石刀片可加工1500个零件,但加工产生的切屑会损伤零件表面,为此,J&M 公司提出用EDM(放电加工)工艺在金刚石刀片顶部加工一条径向断屑槽的解决方案,并专门定制了50片刀片,从而有效解决了这一问题。
现在每片PCD刀片加工的零件数已由1500件提高到4300件。