PCD刀具介绍
什么是PCD刀具

聚晶金刚石刀具聚晶金刚石刀具1.聚晶金刚石(PCD)刀具概述1.1 PCD刀具的发展金刚石作为一种超硬刀具材料应用于切削加工已有数百年历史。
在刀具发展历程中,从十九世纪末到二十世纪中期,刀具材料以高速钢为主要代表;1927年德国首先研制出硬质合金刀具材料并获得广泛应用;二十世纪五十年代,瑞典和美国分别合成出人造金刚石,切削刀具从此步入以超硬材料为代表的时期。
二十世纪七十年代,人们利用高压合成技术合成了聚晶金刚石(PCD),解决了天然金刚石数量稀少、价格昂贵的问题,使金刚石刀具的应用范围扩展到航空、航天、汽车、电子、石材等多个领域。
1.2 PCD刀具的性能特点金刚石刀具具有硬度高、抗压强度高、导热性及耐磨性好等特性,可在高速切削中获得很高的加工精度和加工效率。
金刚石刀具的上述特性是由金刚石晶体状态决定的。
在金刚石晶体中,碳原子的四个价电子按四面体结构成键,每个碳原子与四个相邻原子形成共价键,进而组成金刚石结构,该结构的结合力和方向性很强,从而使金刚石具有极高硬度。
由于聚晶金刚石(PCD)的结构是取向不一的细晶粒金刚石烧结体,虽然加入了结合剂,其硬度及耐磨性仍低于单晶金刚石。
但由于PCD烧结体表现为各向同性,因此不易沿单一解理面裂开。
PCD刀具材料的主要性能指标:①PCD的硬度可达8000HV,为硬质合金的80~120倍;②PCD的导热系数为700W/mK,为硬质合金的1.5~9倍,甚至高于PCBN和铜,因此PCD刀具热量传递迅速;③PCD的摩擦系数一般仅为0.1~0.3(硬质合金的摩擦系数为0.4~1),因此PCD刀具可显著减小切削力;④PCD的热膨胀系数仅为0.9×10-6~1.18×10-6,仅相当于硬质合金的1/5,因此PCD刀具热变形小,加工精度高;⑤PCD刀具与有色金属和非金属材料间的亲和力很小,在加工过程中切屑不易粘结在刀尖上形成积屑瘤。
1.3 PCD刀具的应用工业发达国家对PCD刀具的研究开展较早,其应用已比较成熟。
金刚石(pcd)铰刀的优势特点
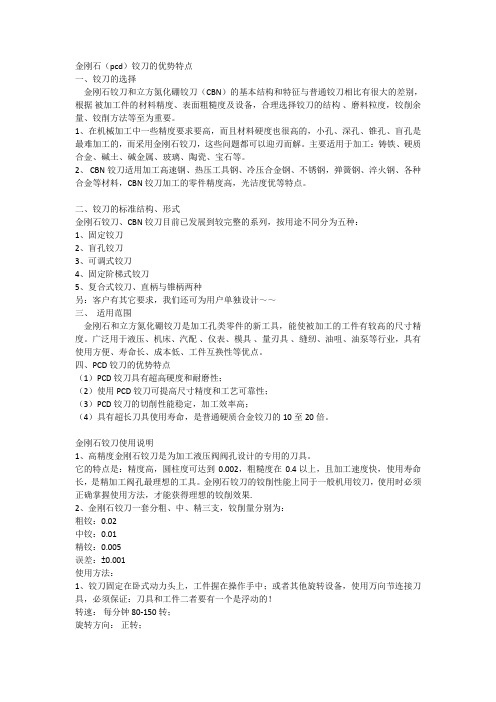
金刚石(pcd)铰刀的优势特点一、铰刀的选择金刚石铰刀和立方氮化硼铰刀(CBN)的基本结构和特征与普通铰刀相比有很大的差别,根据被加工件的材料精度、表面粗糙度及设备,合理选择铰刀的结构、磨料粒度,铰削余量、铰削方法等至为重要。
1、在机械加工中一些精度要求要高,而且材料硬度也很高的,小孔、深孔、锥孔、盲孔是最难加工的,而采用金刚石铰刀,这些问题都可以迎刃而解。
主要适用于加工:铸铁、硬质合金、碱土、碱金属、玻璃、陶瓷、宝石等。
2、CBN铰刀适用加工高速钢、热压工具钢、冷压合金钢、不锈钢,弹簧钢、淬火钢、各种合金等材料,CBN铰刀加工的零件精度高,光洁度优等特点。
二、铰刀的标准结构、形式金刚石铰刀、CBN铰刀目前已发展到较完整的系列,按用途不同分为五种:1、固定铰刀2、盲孔铰刀3、可调式铰刀4、固定阶梯式铰刀5、复合式铰刀、直柄与锥柄两种另:客户有其它要求,我们还可为用户单独设计~~三、适用范围金刚石和立方氮化硼铰刀是加工孔类零件的新工具,能使被加工的工件有较高的尺寸精度。
广泛用于液压、机床、汽配、仪表、模具、量刃具、缝纫、油咀、油泵等行业,具有使用方便、寿命长、成本低、工件互换性等优点。
四、PCD铰刀的优势特点(1)PCD铰刀具有超高硬度和耐磨性;(2)使用PCD铰刀可提高尺寸精度和工艺可靠性;(3)PCD铰刀的切削性能稳定,加工效率高;(4)具有超长刀具使用寿命,是普通硬质合金铰刀的10至20倍。
金刚石铰刀使用说明1、高精度金刚石铰刀是为加工液压阀阀孔设计的专用的刀具。
它的特点是:精度高,圆柱度可达到0.002,粗糙度在0.4以上,且加工速度快,使用寿命长,是精加工阀孔最理想的工具。
金刚石铰刀的铰削性能上同于一般机用铰刀,使用时必须正确掌握使用方法,才能获得理想的铰削效果.2、金刚石铰刀一套分粗、中、精三支,铰削量分别为:粗铰:0.02中铰:0.01精铰:0.005误差:±0.001使用方法:1、铰刀固定在卧式动力头上,工件握在操作手中;或者其他旋转设备,使用万向节连接刀具,必须保证:刀具和工件二者要有一个是浮动的!转速:每分钟80-150转;旋转方向:正转;冷却液:为煤油或柴油(比例一般为80%煤油加20%机油);开关:用脚踏开关控制关停(或者有人配合关机)。
什么是PCD
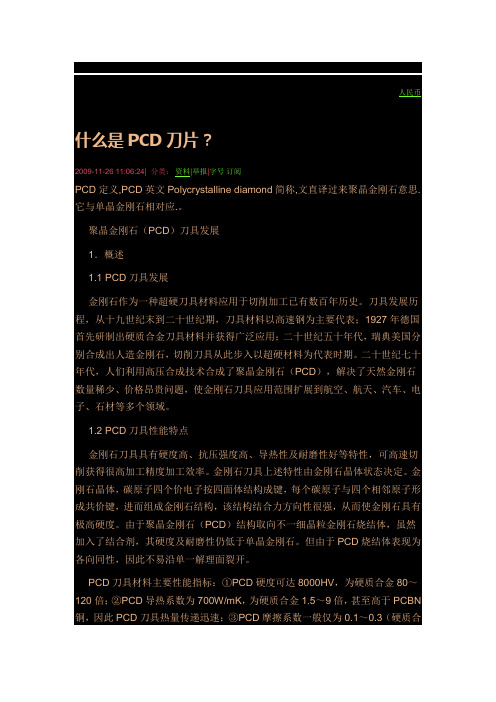
人民币什么是PCD刀片?2009-11-26 11:06:24| 分类:资料|举报|字号订阅PCD定义,PCD英文Polycrystalline diamond简称,文直译过来聚晶金刚石意思.它与单晶金刚石相对应.。
聚晶金刚石(PCD)刀具发展1.概述1.1 PCD刀具发展金刚石作为一种超硬刀具材料应用于切削加工已有数百年历史。
刀具发展历程,从十九世纪末到二十世纪期,刀具材料以高速钢为主要代表;1927年德国首先研制出硬质合金刀具材料并获得广泛应用;二十世纪五十年代,瑞典美国分别合成出人造金刚石,切削刀具从此步入以超硬材料为代表时期。
二十世纪七十年代,人们利用高压合成技术合成了聚晶金刚石(PCD),解决了天然金刚石数量稀少、价格昂贵问题,使金刚石刀具应用范围扩展到航空、航天、汽车、电子、石材等多个领域。
1.2 PCD刀具性能特点金刚石刀具具有硬度高、抗压强度高、导热性及耐磨性好等特性,可高速切削获得很高加工精度加工效率。
金刚石刀具上述特性由金刚石晶体状态决定。
金刚石晶体,碳原子四个价电子按四面体结构成键,每个碳原子与四个相邻原子形成共价键,进而组成金刚石结构,该结构结合力方向性很强,从而使金刚石具有极高硬度。
由于聚晶金刚石(PCD)结构取向不一细晶粒金刚石烧结体,虽然加入了结合剂,其硬度及耐磨性仍低于单晶金刚石。
但由于PCD烧结体表现为各向同性,因此不易沿单一解理面裂开。
PCD刀具材料主要性能指标:①PCD硬度可达8000HV,为硬质合金80~120倍;②PCD导热系数为700W/mK,为硬质合金1.5~9倍,甚至高于PCBN 铜,因此PCD刀具热量传递迅速;③PCD摩擦系数一般仅为0.1~0.3(硬质合金摩擦系数为0.4~1),因此PCD刀具可显著减小切削力;④PCD热膨胀系数仅为0.9×10 -6~1.18×10 -6,仅相当于硬质合金1/5,因此PCD刀具热变形小,加工精度高;⑤PCD刀具与有色金属非金属材料间亲力很小,加工过程切屑不易粘结刀尖上形成积屑瘤。
pcd成型刀是什么意思

pcd成型刀是什么意思
pcd成型刀是指根据产品特殊恳求,需求产品外形的刀具,经过刀具的外形来确保加工出来的零件的外形,可以一次性成型。
比如现代汽车变速箱的设计思索到减轻重量和多功用化的恳求,越来越多地采用压铸铝合金来制造外形复杂的变速箱体,其上设置有许多阶梯状的成型孔,这些成型孔对表面粗糙度、圆度、圆柱度、同心度、无毛刺等质量恳求非常严厉,因此需求pcd成型刀来加工,可以保证质量。
威士PCD成型刀-阶梯铰刀的特性
1、威士PCD成型刀具,基体可采用硬质合金或钢制基体
2、PCD铰刀具有加工精度高,加工,性和导热性强,韧性强的特性。
3、刀具可定制断屑槽,改善缠屑问题
4、PCD铰刀可完成高速切削和硬质材料切削。
5、PCD铰刀加工工件表面粗糙度比普通硬质合金铰刀更好。
6、PCD铰刀运用寿命长。
其运用寿命是普通硬质合金铰刀的10至20倍。
7、可针对不同加工材质和工况设计不同PCD材质
8、可提供返修及换片效劳,降低运用本钱。
pcd铰刀切削参数

pcd铰刀切削参数摘要:1.PCD 铰刀的概述2.PCD 铰刀的切削参数3.PCD 铰刀切削参数的选择4.PCD 铰刀切削参数对切削性能的影响5.结论正文:一、PCD 铰刀的概述PCD 铰刀,即聚晶金刚石铰刀,是一种采用聚晶金刚石作为刀片材料的高速切削刀具。
由于聚晶金刚石具有高硬度、高热导率和高耐磨性等优点,使得PCD 铰刀在高速切削过程中具有优良的切削性能和寿命。
二、PCD 铰刀的切削参数PCD 铰刀的切削参数主要包括切削速度、进给速度和刀具摆动角等。
这些参数对于提高切削效率、保证切削质量以及延长刀具寿命具有重要意义。
1.切削速度:切削速度是PCD 铰刀切削过程中的一个重要参数,其单位为米/分钟。
切削速度的选择应根据被加工材料的硬度、刀具材料以及切削深度等因素来确定。
2.进给速度:进给速度是PCD 铰刀在切削过程中的另一个重要参数,其单位为毫米/转。
进给速度的选择应根据被加工材料的硬度、刀具材料以及切削深度等因素来确定。
3.刀具摆动角:刀具摆动角是PCD 铰刀在切削过程中的一个重要参数,其单位为度。
刀具摆动角的选择应根据被加工材料的形状、刀具材料以及切削深度等因素来确定。
三、PCD 铰刀切削参数的选择PCD 铰刀切削参数的选择应综合考虑被加工材料的硬度、刀具材料、切削深度、切削速度、进给速度和刀具摆动角等因素。
在选择切削参数时,应遵循以下原则:1.确保切削效率:在保证切削质量的前提下,尽可能提高切削速度和进给速度,以提高切削效率。
2.保证切削质量:在保证切削效率的前提下,尽可能选择合适的刀具摆动角,以保证切削质量。
3.延长刀具寿命:在保证切削质量和效率的前提下,尽可能选择合适的切削参数,以延长刀具寿命。
四、PCD 铰刀切削参数对切削性能的影响PCD 铰刀切削参数对切削性能具有重要影响。
合理的切削参数可以提高切削效率、保证切削质量并延长刀具寿命;而不合理的切削参数可能导致切削效率低下、切削质量差甚至刀具损坏。
聚晶金刚石( PCD )和聚晶金刚石复合片( PDC )

聚晶金刚石(PCD)和聚晶金刚石复合片(PDC)与大单晶金刚石相比,作为刀具材料的聚晶金刚石(PCD)以及聚晶金刚石复合刀片(PDC)具有以下优点:①晶粒呈无序排列,各向同性,无解理面,因此它不像大单晶金刚石那样在不同晶面上的强度、硬度以及耐磨性有较大区分,以及因解理面的存在而呈现脆性。
②具有较高的强度,特别是PDC材料由于有硬质合金基体的支撑而有较高的抗冲击强度,在冲击较大时只会产生小晶粒碎裂,而不会像单晶金刚石那样大块崩缺,因而PCD或PDC刀具不仅可以用来进行精紧密削加工和一般半精密加工,还可用作较大切削量的粗加工和断续加工(如铣削等),这大大扩充了金刚石刀具材料的使用范围。
③可以制备大块PDC金刚石复合片刀具坯料,充足大型加工刀具如铣刀的需要。
④可以制成特定形状以适合于不同加工的需要。
由于PDC刀具大型化和加工技术如电火花和激光切割技术的提高,三角形、人字形以及其他异形刀坯均可加工成形。
为适应特别切削刀具的需要还可设计成包裹式、夹心式与花卷式PDC刀具坯料。
⑤可以设计或推测产品的性能,给与产品必要的特点以适应它的特定用途。
比如选择细粒度的PDC刀具材料可使刀具的刃口的质量提高,粗粒度的PDC刀具材料能够提高刀具的耐用度,等等。
总之,随着PCD、PDC金刚石复合片刀具材料的讨论进展,其应用已经快速扩展到很多制造工业领域,广泛应用于有色金属(铝、铝合金、铜、铜合金、镁合金、锌合金等)、硬质合金、陶瓷、非金属材料(塑料、硬质橡胶、碳棒、木材、水泥制品等)、复合材料(纤维加强塑料、金属基复合材料MMCs等)的切削加工,尤其在木材和汽车加工业,已经成为传统硬质合金的高性能替代产品。
切削刀具用PDC、PCD材料要求:①金刚石颗粒间能广泛地形成D—D自身结合,残余粘结金属和石墨尽量少,其中粘结金属不能以聚结态或呈叶脉状分布,以保证刀具具有较高的耐磨性和较长的使用寿命。
②溶媒金属残留量少。
最好是在烧结过程中能起溶媒作用,而在烧结过程完成后将以不起溶媒作用的合金形式充填于烧结金刚石晶粒间隙中,或烧结后残留的溶媒性金属被隔离,避开溶媒金属与金刚石表面直接接触,以提高PCD的抗氧化本领,从而保证刀具具有充足的耐热温度。
关于PCD刀具,最全的都在这了

关于PCD刀具,最全的都在这了PCD刀具介绍:PCD刀具是采用超硬材料PCD(聚晶金刚石)与刀具基体通过特殊工艺制成的刀具。
PCD刀具的特点:硬度高、抗压强度高、导热性好、耐磨性好。
PCD刀具主要指标:1、PCD的硬度可达8000HV,为硬质合金的8~12倍;2、PCD的导热系数为700W/mK,为硬质合金的1.5~9倍,甚至高于PCBN和铜,因此PCD刀具热量传递迅速;3、PCD的摩擦系数一般仅为0.1~0.3(硬质合金的摩擦系数为0.4~1),因此PCD刀具可显著减小切削力;4、PCD的热膨胀系数仅为0.9×10^-6~1.18×10^-6,仅相当于硬质合金的1/5,因此PCD刀具热变形小,加工精度高;5、PCD刀具与有色金属和非金属材料间的亲和力很小,在加工过程中切屑不易粘结在刀尖上形成积屑瘤。
PCD刀具制造技术:制造过程PCD刀具的制造过程主要包括两个阶段:1、PCD复合片的制造:PCD复合片是由天然或人工合成的金刚石粉末与结合剂(其中含钴、镍等金属)按一定比例在高温(1000~2000℃)、高压(5~10万个大气压)下烧结而成。
在烧结过程中,由于结合剂的加入,使金刚石晶体间形成以TiC、SiC、Fe、Co、Ni等为主要成分的结合桥,金刚石晶体以共价键形式镶嵌于结合桥的骨架中。
通常将复合片制成固定直径和厚度的圆盘,还需对烧结成的复合片进行研磨抛光及其它相应的物理、化学处理。
2、PCD刀片的加工:PCD刀片的加工主要包括复合片的切割、刀片的焊接、刀片刃磨等步骤。
切割工艺由于PCD刀具具有很高的硬度及耐磨性,因此必须采用特殊的加工工艺。
目前,加工PCD复合片主要采用电火花线切割、激光加工、超声波加工、高压水射流等几种工艺方法,其工艺特点的比较见表1。
在上述加工方法中,电火花加工效果较佳。
PCD中结合桥的存在使电火花加工复合片成为可能。
在有工作液的条件下,利用脉冲电压使靠近电极金属处的工作液形成放电通道,并在局部产生放电火花,瞬间高温可使聚晶金刚石熔化、脱落,从而形成所要求的三角形、长方形或正方形的刀头毛坯。
PCD(金刚石)刀片

ø85 19
ø70 ø85
■ 切削数据
• 活塞 • Vc = 1000m/min • ap = 2.0mm (Only spree d=5mm) • f = 0.25mm/rev • 湿式 • CNMM120408M
AC8A
Spree 凹面部
60
(加工长度)
75
超微颗粒
KPD001
10,000 个/刃
■ 应用
被加工材料
切削范围 JIS(日本工业规格)分类
精加工 N01
KPD001
PCD
KPD025 KPD010
KPD002
非铁材料 (铝/非铁金属)
N10
N20
粗加工 N30
精加工 S01
KPD001 KPD025
KPD010 KPD002
难于加工材料 (钛合金/镍合金)
S10
S20
粗加工 S30
• 湿式
• 铜焊圆形刀柄
(刀尖半径 = 0.5mm)
超微颗粒
KPD001
1,350 个/刃
传统PCD H
500 ~ 1,060 个/刃
•由于切屑控制情况差而发生崩损。KPD001加工时无崩损
与毛边,工具寿命得到改善。
烧结金属(Cu)
• 连杆 • Vc = 350m/min • ap = 0.08 ~ 0.1mm • f = 0.07mm/rev • 湿式 • TPGN160304SE
90 切削部件
烧结金属(Cu)
超微颗粒
KPD001
300 个/刃
其他公司的PCD G (超微颗粒聚晶PCD)
•间断加工。
(烧结金属存在微小的间隙)
•耐磨损性较其他公司的G更佳。
- 1、下载文档前请自行甄别文档内容的完整性,平台不提供额外的编辑、内容补充、找答案等附加服务。
- 2、"仅部分预览"的文档,不可在线预览部分如存在完整性等问题,可反馈申请退款(可完整预览的文档不适用该条件!)。
- 3、如文档侵犯您的权益,请联系客服反馈,我们会尽快为您处理(人工客服工作时间:9:00-18:30)。
PCD铣刀:
聚晶金刚石(PCD)刀具是通过把PCD复合片焊接到硬质合金或者钢的刀体上制成的刀具。
由于PCD复合片将单晶金刚石的高硬度、耐磨性、低摩擦系数和强度与碳化钨硬质合金的高抗弯强度进行了结合,复合片的碳化钨硬质合金层为金刚石层提供了机械支持,增加了它的抗弯强度,同时硬质合金层易于焊接,使制作成品刀具变得容易。
与其它刀具材料相比,聚晶金刚石具有如下特点:① 极高的硬度和耐磨性;② 高导热性和低热膨胀系数,切削时散热快,切削温度低,热变形小;③ 摩擦系数小,可降低加工表面粗糙度。
采用PCD刀具加工铝合金时,由于金刚石硬度高,表面与金属亲和力小,且刀具前刀面都抛光成镜面,不易产生积屑瘤,加工尺寸稳定性以及表面质量都很好。
采用PCD刀具加工各种规格铝合金零件,刀具寿命可达几千到几万件,尤其适合汽车、摩托车零件的大规模生产。
PCD刀具还广泛用于其它有色金属和非金属材料的高速加工,被广泛应用于汽车、航空航天、电子和木材加工等领域。
PCD刀片:
PCD刀片是指具有整体PCD切削刃的硬质合金基体刀片。
PCD复合片切削刃被直接焊在硬质合金基体上,因此消除了金刚石和硬质合金之间的缝隙,可避免切屑堵塞。
为在精加工非铁金属尤其是铝材料时有效控制切屑,国外开发出一种带有断屑器的PCD刀片。
PCD刀片的特点在于金刚石具有硬度高、抗压强度高、导热性以及耐磨性好等特性,可在高速切削中获得很高的加工精度和加工效率。
PCD刀片主要应用于以下两个方面:①难加工,有色金属材料的加工:用普通刀具加工难加工有色金属材料时,往往产生刀具易磨损、加工效率低等缺陷,而PCD刀片则可表现出良好的加工性能,用PCD刀片可有效的加工过共晶硅铝合金。
②难加工非金属材料的加工,PCD刀片非常适合对石材、硬质碳、碳纤维增强塑料、人造板材等难加工非金属材料的加工。
PCD刀片材料的主要性能指标:
①PCD的硬度大于8000HV,为硬质合金的80-120倍;
②PCD的导热系数为700W/mK,为硬质合金的1.5-9倍,甚至高于PCBN和铜,因此PCD刀片热量传递迅速;
③PCD的摩擦系数一般仅为0.1-0.3(硬质合金的摩擦系数为0.4-1),因此PCD刀片可显著减小切削力;
④PCD的热膨胀系数仅为0.9*10-6-1.18*10-6,仅相当于硬质合金的1/5,因此PCD刀片热变形小,加工精度高;
⑤PCD刀片与有色金属和非金属材料的亲和力很小,在加工过程中切屑不易粘结在刀尖上形成积屑瘤。
PCD刀片上加工三维断屑槽的作用:结合PCD刀片的优良性能,在PCD刀片上加工设计合理的三维断屑槽可以有效防止产生不受欢迎的缎带形和螺旋形切屑。
这种三维PCD 断屑槽除了可增强对切屑的控制外,集成在断屑槽中的较大剪切角还能降低工件的热膨胀厚度减小切削压力,从而可提高工件的加工精度,省略二次加工,同时还能延长刀具寿命,研究表明,与不加工断屑槽的PCD相比较,带有三维断屑槽的PCD刀具使用寿命至少可以增加20-30%。
力博刀具专业生产PCD刀具扣扣玖壹叁玖肆贰贰陆陆。