1万吨单极式离子膜烧碱新技术开发项目环境影响报告书
氯碱工业离子膜和电槽的进展

氯碱工业离子膜和电槽的进展氯碱工业离子膜和电槽的进展氯碱工业离子膜法已被公认为是一种带有方向性的氯碱生产新工艺,其特点是节能、优质、基本无污染,生产成本及投资均较低廉。
离子膜法技术的进展是离子膜从磺酸膜到羧酸膜及羧酸-磺酸复合膜,电槽从单极式到复极式,极间距进展到小极距或“零”极距。
1.离子交换膜的进展离子交换膜是氯碱工业膜法制碱的核心,目前应用于食盐水溶液电解的阳离子交换膜,根据其离子交换基团的不同,可分为全氟磺酸膜和全氟羧酸膜和全氟羧酸-磺酸复合膜。
美国杜邦(Dupont)公司于1938年起开始研制氟化学品,首先三制成功聚四氟乙烯,1960年研制成功耐氯碱的全氟磺酰氟(XR)树脂,并首次应于于燃料电池,之后又研制了Nafion系列膜,1975年Nafion-315膜被日本旭化成公司成功地用于延冈工厂生产烧碱,第一次实现了工业化离子膜法的氯碱生产。
Nafion-100、300、400系列适合生产低浓度烧碱,Nafion -300系列是一种增强复合离子膜,为了获得高电压率率,其阴极侧采用低吸水层,为了获得低电压,其阳极侧采用高吸水层,这种膜在生产稀碱时电耗较低;Nafion-400系列是一种物理耐久性较好的增强离子膜;Nafion-900系列在保持性能稳定而长期生产高浓度烧碱方面,兼有高电流效率和低电压的特点,Nafion-901膜可用来直接生产浓度为32%的碱液,电流效率接近96%;国际上认为Nafion-90209及Nafion-961运转效益尚好,新问世的NX-966膜,其机械性能比N-90209提高近一半,寿命较长且更安全,碱浓度为30%~35%时,NX-966的槽电压下降了150mV。
1976年日本旭化成公司用全氟羧酸膜取代了杜邦公司的全氟磺酸膜,接着又开发了羧酸-磺酸复合膜。
全氟羧酸膜具有很强的阻止OH透过的性能,在较广泛的烧碱浓度范围内(20%~40%)都可以超过90%的电流效率,并且碱浓度为20%~30%内有较低的槽电压,因而可以显著地节省电耗,然而全氟羧酸膜在酸性条件下会成为非异体。
(完整版)离子膜法烧碱工艺毕业论文
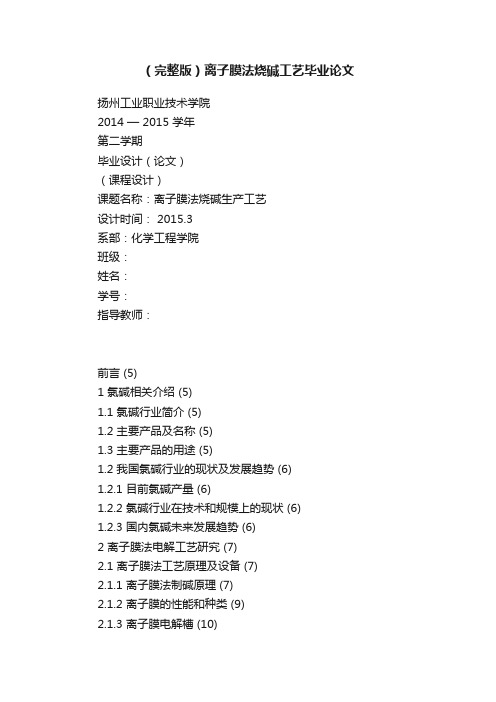
(完整版)离子膜法烧碱工艺毕业论文扬州工业职业技术学院2014 — 2015 学年第二学期毕业设计(论文)(课程设计)课题名称:离子膜法烧碱生产工艺设计时间: 2015.3系部:化学工程学院班级:姓名:学号:指导教师:前言 (5)1 氯碱相关介绍 (5)1.1 氯碱行业简介 (5)1.2 主要产品及名称 (5)1.3 主要产品的用途 (5)1.2 我国氯碱行业的现状及发展趋势 (6)1.2.1 目前氯碱产量 (6)1.2.2 氯碱行业在技术和规模上的现状 (6)1.2.3 国内氯碱未来发展趋势 (6)2 离子膜法电解工艺研究 (7)2.1 离子膜法工艺原理及设备 (7)2.1.1 离子膜法制碱原理 (7)2.1.2 离子膜的性能和种类 (9)2.1.3 离子膜电解槽 (10)2.2 离子膜法制碱工艺流程 (12)2.2.1 一次盐水 (12)2.2.2 二次盐水 (14)2.2.3 电解工艺 (15)2.2.4 淡盐水脱氯 (17)2.2.5 氯氢处理 (18)2.2.6 废氯气处理 (22)2.2.7 氯气液化 (22)3. 结论 (23)参考文献 (24)致谢 (25)离子膜法烧碱生产工艺摘要:随着科技的迅猛发展,我国的氯碱工业行业也得到了迅速的发展和扩大,很多氯碱化工企业也都扩大了生产,加大了生产力度。
然而随着社会高速的发展,提高氯碱的生产规模和更有效、更经济的发展氯碱行业的发展也催生了很多新的企业加入到行业中来,氯碱行业已经开始向规模化、技术化、经济化这种良好的态势发展,特别是离子膜法工艺的出现,将会更加有利于此行业的发展和提高壮大。
本论文主要论述了离子膜法烧碱生产工艺规程。
关键词:氯碱生产工艺离子膜法abstract:Along with the rapid development of science and technology,China's chlor-alkali industry rapid development and expansion, a lot ofchlor-alkali chemical enterprises are also enlarged the production, weintensified the efforts on the production. However, with the development ofthe society of and the development of more effective and more economical development of chlor-alkali industry also rise to a lot of new companies to join the industry, Chlor-alkali industry to scale, technology, economize the good state of development, especially the emergence of ion membrane process, will be more conducive to the development of the industry and improve.This thesis mainly discusses the method of ionic membrane caustic soda production process procedures.Keywords:chlor-alkali production process Ionic membrane law前言随着世界氯碱工业生产和进出口格局的转变,我国已成为世界上氯碱化工的重要生产基地。
万吨年单极式离子膜烧碱新技术开发项目环境影响报告书

1万吨/年单极式离子膜烧碱新技术开发项目环境影响报告书一、现有工程工程概况及污染源调查(一)产品及规模现有工程主要产品及生产规模为:烧碱30000t/a,液氯18000t/a,盐酸21000t/a。
(二)生产工艺该厂现有3万吨/年烧碱装置为金属阳极隔膜电解法,其工艺过程主要包括化盐、电解、氢处理、氯处理、液氯、碱蒸发、盐酸等工段。
1、盐水工段盐水生产是将原料盐溶解成饱和的氯化钠溶液,并经精制反应、澄清、过滤、中和等过程使之成为电解所需的合格的精盐水。
在盐水生产过程中,排放物主要是盐泥。
2、电解工段将化盐工段送来的精制盐水连续均匀地分别输入各个电解槽,在直流电的作用下,盐水被电解生成H2、Cl2、NaOH溶液。
在阳极上产生的氯气经氯气管送至氯气处理工序;在阴极上产生的氢气导入氢气管送至氢气站,电解液自阴极箱导出管导出,流入电解液总管,送蒸发工段。
反应原理为:阳极反应:2Cl-2e → Cl2阴极反应:2H2O+2e →H2↑+2OH-Na++OH-→ NaOH总反应式:2NaCl+2H2O=2NaOH+Cl2↑+H2↑由上述食盐水溶液电解反应式可知,电解过程中每生成一吨100%NaOH电解液,可同时产生0.886吨氯气及0.025吨氢气,需要折合100%NaCl1.461吨。
3、氢气处理工段自电解工段来的80~90℃的高温氢气通过冷凝,除去所含水份,再用罗茨鼓风机加压送入氯化氢合成工段。
4、氯气处理及液氯工段由电解来的80~90℃的高温氯气首先经过冷却,然后经三组并联的泡沫干燥塔,在塔板上与溢流下来的浓硫酸呈泡沫状充分接触,氯气中的水份被浓硫酸除去。
冷却时产生的含氯废水,现有装置直接排全厂循环水池。
由氯气处工序来的压缩氯气,经液化机组以氨制冷,将氯气在低温下液化,冷凝下来的液氯进入计量槽和液氯贮槽,并灌瓶包装出售,液化尾气送盐酸工段。
5、电解液蒸发工段来自电解工段的电解液含碱浓度只有10%左右,把电解液用泵送入三效蒸发器,经过蒸发,碱液被浓缩至32-35%,然后进行冷却、配碱,分配合格的碱用泵送入碱栈台。
离子膜烧碱
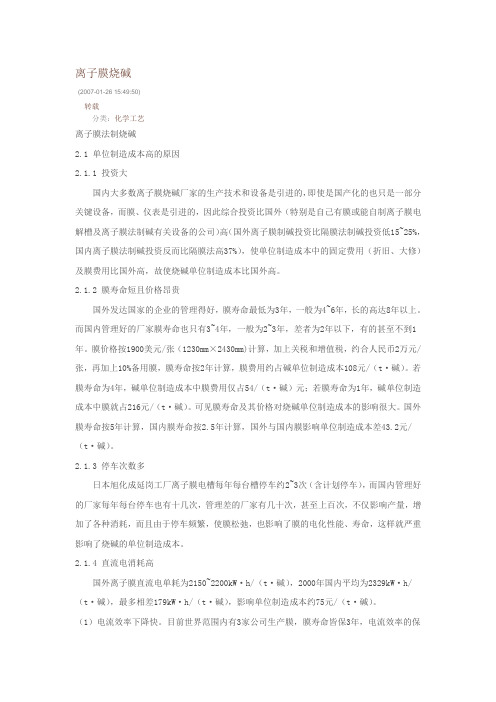
离子膜烧碱(2007-01-26 15:49:50)转载分类:化学工艺离子膜法制烧碱2.1 单位制造成本高的原因2.1.1 投资大国内大多数离子膜烧碱厂家的生产技术和设备是引进的,即使是国产化的也只是一部分关键设备,而膜、仪表是引进的,因此综合投资比国外(特别是自己有膜或能自制离子膜电解槽及离子膜法制碱有关设备的公司)高(国外离子膜制碱投资比隔膜法制碱投资低15~25%,国内离子膜法制碱投资反而比隔膜法高37%),使单位制造成本中的固定费用(折旧、大修)及膜费用比国外高,故使烧碱单位制造成本比国外高。
2.1.2 膜寿命短且价格昂贵国外发达国家的企业的管理得好,膜寿命最低为3年,一般为4~6年,长的高达8年以上。
而国内管理好的厂家膜寿命也只有3~4年,一般为2~3年,差者为2年以下,有的甚至不到1年。
膜价格按1900美元/张(1230mm×2430mm)计算,加上关税和增值税,约合人民币2万元/张,再加上10%备用膜,膜寿命按2年计算,膜费用约占碱单位制造成本108元/(t·碱)。
若膜寿命为4年,碱单位制造成本中膜费用仅占54/(t·碱)元;若膜寿命为1年,碱单位制造成本中膜就占216元/(t·碱)。
可见膜寿命及其价格对烧碱单位制造成本的影响很大。
国外膜寿命按5年计算,国内膜寿命按2.5年计算,国外与国内膜影响单位制造成本差43.2元/(t·碱)。
2.1.3 停车次数多日本旭化成延岗工厂离子膜电槽每年每台槽停车约2~3次(含计划停车),而国内管理好的厂家每年每台停车也有十几次,管理差的厂家有几十次,甚至上百次,不仅影响产量,增加了各种消耗,而且由于停车频繁,使膜松弛,也影响了膜的电化性能、寿命,这样就严重影响了烧碱的单位制造成本。
2.1.4 直流电消耗高国外离子膜直流电单耗为2150~2200kW·h/(t·碱),2000年国内平均为2329kW·h/(t·碱),最多相差179kW·h/(t·碱),影响单位制造成本约75元/(t·碱)。
离子膜烧碱工艺设计说明

4 化工工艺及系统
4.1 概述
装置设计规模,装置组成与各工序名称 (1)2 万吨/年离子膜烧碱装置: 20000t/a ;60t/d;2.5t/h (2)1.7 万吨/年氯气液化及汽化装置。 (3)一次盐水工序、二次盐水工序、电解工序、淡盐水真空脱氯工序、氯气处理 工序、氢气处理工序、尾气处理工序、液氯贮存及汽化 、液碱罐区及卸车。
化学品较多,所以选用 BaCl2 法。 一次盐水加入 NaOH、Na2CO3 等精制剂进行精制反应,再用凯膜过滤技术和氯化钡
离子膜烧碱生产项目可行性研究报告(专业完整版)

离子膜烧碱生产项目可行性研究报告(此文档为word格式,下载后您可任意修改编辑!)1总论1.1概述1.1.1项目名称、主办单位、企业性质及负责人项目名称:某某(某某)化工有限公司200kt/a离子膜烧碱项目承办单位:某某(某某)化工有限公司(以下简称:某某公司)企业性质:国有法人代表:罗某某(董事长)负责人:林某某项目性质:新建项目类型:化工企业经营机制:有限责任公司企业管理体制:经理负责制企业法定地址:某某市某某区某某临港工业区项目建设地点:某某市某某区某某临港工业区1. 1. 2主办单位的基本情况某某(某某)化工有限公司是中国某某(集团)总公司控股的子公司,并于2004 年10月10日在某某市工商局注册成立。
某某(某某)化工有限公司己选址在某某市某某区某某临港工业区内,规划投资建设一批具有国际竞争力的项目,最终形成化工生产产业园。
某某临港工业区位于某某市某某区,海河入海的南岸地区,大沽沙河道南侧,距某某市中心46公里,某某滨海国际机场38公里,某某地区中心10公里,某某港2公里,其北部为某某港南疆港区,西北部为某某东大沽生活区,西部为某某港南疆散货物流中心,南部为规划海滨风景旅游区。
某某(某某)化工有限公司以化工新材料为主导产业。
依托中国某某集团的有机硅、聚碳酸酯、双酚A、聚氨酯、聚甲醛、PBT等多种化工新材料、工程塑料在国内外的领先优势,依靠自有技术和引进国际先进工艺相结合,计划在3〜5年内,初步建成国内领先、世界知名的化工产业园。
某某市和某某区政府为公司的成立和今后的发展提供了强有力的支持。
某某临港工业区将配套建设化工产业园界区外的公用工程设施。
1. 1.3项目提出的背景,投资的目的、意义和必要性1. 1.3. 1项目提出的背景中国某某(集团)总公司是一家大型化工企业,隶属于中国化工集团公司。
中国化工集团公司是经国务院批准,于2004年5月9日正式成立的,是在原化工部所属企业的基础上重新组建的国有大型企业。
年产1万吨烧碱 (NaOH)生产线建设项目可行性研究报告

年产1万吨烧碱(NaOH)生产线建设项目可行性研究报告总论近年来,正蓝旗旗委、政府抓住国家实施西部大开发和建设京津生态屏障的有利时机,全面推进农牧业产业化、工业化、城镇化进程,坚持‚牧业富旗‛不动摇,按照‚因地制宜、突出重点、农牧结合、协调发展‛的方针,调整优化农牧业产业结构,发展特色、绿色生态农牧业,使我旗农牧业初步走上集约化发展的道路。
该项目的实施,培育了正蓝旗的化工产业及周边地区硝、碱淖的开发利用。
极大提高地区工业的竞争能力和地方经济效益,对促进正蓝旗的经济发展、农牧民增收、社会和谐具有重要意义。
1.1设计项目背景简述查干淖位于锡盟正蓝旗宝绍代苏木境内。
2007年锡盟怡翔商贸有限责任公司组织科技人员对该淖进行了初步勘探结果表明,该淖内储有纯碱(Na2CO3)、硝(Na2SO4)等多种无机化合物,是天然的无机化工原料。
由于受技术力量和储量等条件所限,该淖一直未能投资开发利用。
为此,2007年底经旗发改局引见并请示旗委、旗政府同意,决定对该淖进行开发治理。
同时在2007年底由锡盟怡翔公司组织科技力量对蓝旗境内的达格淖、桑根达来淖等进行了排查,发现这些淖相对集中在桑根达来镇、宝绍代苏木境内,排勘察结果表明,因单个淖储量有限,无法进行规模化开发。
只能将这些分散的淖统一规划治理并传授技术于当地牧民,由牧民负责管理和采收原料,金山蓝化公司统一收购,集中提纯、加工生产。
可形成一个年产纯碱10000吨、烧碱10000吨的化工企业。
其具体实施计划如下:一期工程为原料基地建设投资500万元,项目形成后年生产基础原料日晒碱(Na2CO3)2万吨。
建设工期为(2008年3-6月)三个月。
二期工程为1万吨纯碱生产线建设纯碱(Na2CO3)生产线为二期工程,投资800万元,项目形成后年生产纯碱1万吨。
建设工期为(2009年5月- 10月)六个月。
三期工程为1万吨烧碱(NaOH)生产线建设投资1300万元,项目形成后年产量1万吨烧碱,建设工期为(2009年10月-20010年10月)十二个月。
离子膜法烧碱生产中曾发生的问题及解决办法

20 09年 4月 , 某企业使 用旭化成 M 3 N H L一 2 C 和 M 3 N Z电解 槽 , L一 2 C 因凯膜 过 滤 器 垫 片漏 , 次 二 盐水 中 C“、 ¨ 质量 分数 之 和高达 ( a Ng 1—2 )X
l ~, O 电解 槽 电 流 效 率 由 9 . % 下 降 至 9 % ~ 45 2
外, 在设 计离 子膜 法 电解 生产工 艺时 , 不但离 子膜 法 电解 的氯 气 总管上要 有氯 气正 、 负压水 封 , 隔膜法 电 解 的氯气 总管 上也要 有正 、 负压水 封 。 4 1 二 次盐水 品质 欠佳 导 致 电 流效 率 下 降 、 电 .1 槽 压 升高 二次 盐 水不 纯 物严 重 超标 , 使 电 流效 率 急剧 会
第4 8卷nd sr lrAl a iI u ty
21 0 2年 3月
Vo . 1 48,No 3 . Ma .,2 2 r 01
【 解】 电
离 子膜 法烧 碱 生产 中 曾发 生 的 问题 及 解 决 办法
程 殿 彬
( 天津大沽化 工股份有限公 司, 天津 305 ) 04 5
佳 、 a1 度分 布不 均 以外 , 要 原 因 是 二 次 盐 水 NC 浓 主 品质 欠佳 。企 业 日常分 析 未 发 现 盐水 品质 有 问题 。
上述 l 6家二次盐水中 cL 、 g 等离子严重 a M2 2 超标 , 电解槽电流效率急剧下降, 使 槽电压升高。由 此 得到 如下教 训 。 () 1 盐水品质是保证离子膜运行性能稳定的关 键, 出现盐水品质问题 , 要及 时采取相关措施 , 问题
- 1、下载文档前请自行甄别文档内容的完整性,平台不提供额外的编辑、内容补充、找答案等附加服务。
- 2、"仅部分预览"的文档,不可在线预览部分如存在完整性等问题,可反馈申请退款(可完整预览的文档不适用该条件!)。
- 3、如文档侵犯您的权益,请联系客服反馈,我们会尽快为您处理(人工客服工作时间:9:00-18:30)。
1万吨/年单极式离子膜烧碱新技术开发项目环境影响报告书(关键内容部分)第三章工程分析一、现有工程工程概况及污染源调查(一)产品及规模现有工程主要产品及生产规模为:烧碱30000t/a,液氯18000t/a,盐酸21000t/a。
(二)生产工艺该厂现有3万吨/年烧碱装置为金属阳极隔膜电解法,其工艺过程主要包括化盐、电解、氢处理、氯处理、液氯、碱蒸发、盐酸等工段。
1、盐水工段盐水生产是将原料盐溶解成饱和的氯化钠溶液,并经精制反应、澄清、过滤、中和等过程使之成为电解所需的合格的精盐水。
在盐水生产过程中,排放物主要是盐泥。
2、电解工段将化盐工段送来的精制盐水连续均匀地分别输入各个电解槽,在直流电的作用下,盐水被电解生成H2、Cl2、NaOH溶液。
在阳极上产生的氯气经氯气管送至氯气处理工序;在阴极上产生的氢气导入氢气管送至氢气站,电解液自阴极箱导出管导出,流入电解液总管,送蒸发工段。
反应原理为:阳极反应:2Cl-2e → Cl2阴极反应:2H2O+2e →H2↑+2OH-Na++OH-→ NaOH总反应式:2NaCl+2H2O=2NaOH+Cl2↑+H2↑由上述食盐水溶液电解反应式可知,电解过程中每生成一吨100%NaOH电解液,可同时产生0.886吨氯气及0.025吨氢气,需要折合100%NaCl1.461吨。
3、氢气处理工段自电解工段来的80~90℃的高温氢气通过冷凝,除去所含水份,再用罗茨鼓风机加压送入氯化氢合成工段。
4、氯气处理及液氯工段由电解来的80~90℃的高温氯气首先经过冷却,然后经三组并联的泡沫干燥塔,在塔板上与溢流下来的浓硫酸呈泡沫状充分接触,氯气中的水份被浓硫酸除去。
冷却时产生的含氯废水,现有装置直接排全厂循环水池。
由氯气处工序来的压缩氯气,经液化机组以氨制冷,将氯气在低温下液化,冷凝下来的液氯进入计量槽和液氯贮槽,并灌瓶包装出售,液化尾气送盐酸工段。
5、电解液蒸发工段来自电解工段的电解液含碱浓度只有10%左右,把电解液用泵送入三效蒸发器,经过蒸发,碱液被浓缩至32-35%,然后进行冷却、配碱,分配合格的碱用泵送入碱栈台。
6、盐酸合成工段反应式:H2+Cl2=2HCl自氯氢处理来的氯气和氢气分别进入各自的缓冲器,再经各自的阻火器后,进入合成炉反应,生成的氯化氢气体由顶部加入的来自尾气吸收塔的稀盐酸吸收,再冷却制成盐酸,未被吸收的氯化氢气体经尾气吸收塔用水吸收,生成稀盐酸流入合成炉,剩余尾气由水喷射泵抽走。
制成的盐酸送入成品酸罐出售。
工艺流程见图3-1。
电解氯处理液化化盐原盐水精盐水氯气氯气氢处理氢气氢气盐酸工段氯气盐酸成品液氯包装电解液回收盐水蒸发工段固碱工段30%、42%成品液成品固碱♣洗槽水♣氯水♣蒸发水图例♣废水♠废渣♠盐泥图3-1 工艺流程图(三)主要原辅材料及能源消耗主要原辅材料及能源消耗消耗情况见表表3-1。
表3-1 主要原辅材料及能源消耗一览表 序号 材料名称 单位 消耗量来源 吨NaOH 耗 年耗 1 原盐 t 1.67 5×104 外购2 碳酸钠 t 0.023 700 外购 3 浓硫酸 kg 9 27×104 外购 4 煤 t 0.85 2.55×104 外购 5 水 m 3 28.8 86.4×104 自采 6电Kwh31009300×104外购(四)主要生产设备表3-2 主要生产设备一览表 序号 设 备数 量1化盐桶22道尔澄清桶23隔膜法金属阳极电解槽664氢气冷却塔25Ⅰ段钛冷却器26Ⅱ段钛冷却器17泡沫干燥塔38筛板干燥塔19氯压机610三效蒸发器111浸没蒸发器312闪蒸蒸发器113双级氨压缩机314合成炉415一、二级吸收器416锅炉4(五)给排水1、给水该厂现有深井4眼,包括两眼400米深井,600米和800米深井各一眼,供水能力为180m3/h,实际供水110m3/h。
2、排水该厂各工段废水全部进入废水处理池处理后,大部分循环使用,20m3/h废水排入厂外排干渠,干旱季节基本上被渗漏、蒸发,雨季可与雨水混合经由老黄南排干入海。
(六)供电、供热公司电源引自距离1.5公里处的黄骅110KV变电站,厂内现有35KV变电站一座,动力变压器二台,总计4000KV A,整流变压器二台,总计15902KVA。
厂内现有20t/h蒸汽锅炉和10t/h蒸汽锅炉各两台,各开一备一,均燃用大同烟煤(低位发热值24000kJ/kg,灰分4-16%,全硫分1.5%),每天耗煤80吨。
(七)污染源调查与监测1、废水(废液)现有装置外排废水主要是氯处理工段产生的氯水、电解工段修槽工序产生的洗槽水、电解液蒸发工段产生的蒸发废水等,各工段废水全部汇入废水处理池(循环水池)絮凝沉淀后,回用工艺,废水处理池污水排放量为20m3/h。
氯处理工段产生废硫酸,浓度78%,产生量360t/a,出售给有关单位利用。
现有工程主要废水排放及治理措施见表3-3。
表3-3 现有工程主要废水排放及治理措施名称来源污染物mg/L排水量排放方式处理措施氯水氯处理活性氯8234 0.5 m3/h连续排循环水池洗槽水修槽工序SS 227 2 m3/d 间断排循环水池循环水池中的水溢流外排,排水口废水流量为20 m3/h。
根据监测,厂排水口废水中pH:11.4,SS:212mg/L,活性氯:36.4mg/L,皆超过《烧碱、聚氯乙烯工业水污染物排放标准》(GB15581-95)中的二级标准;CODcr:138mg/L,符合《污水综合排放标准》(GB8978-1996)中表4的二级标准。
全厂废水排放量为160000 m3/a,按照年产30000吨烧碱计,吨产品排水量为5.3m3/t,符合《烧碱、聚氯乙烯工业水污染物排放标准》。
2、废气正常生产时,电解工段电解槽排放的含氢废气部分回收,部分直排大气;盐酸工段氯化氢尾气经尾气吸收塔吸收后,经15米排气筒排放。
液氯生产过程中由于泄漏等原因造成氯气的损失一般为0.1-0.2kg/t液氯;0.5m3/h高浓度氯水中50%的氯挥发进入大气,气态氯排放量为1.7kg/h。
这两类氯气属面源无组织排放。
非正常生产时,电解槽开停车过程中及氯气系统事故状态下产生的废氯气,目前经由氯气管道上的水封外排。
辅助工程废气主要是锅炉烟气,该厂现有20t/h和10t/h蒸汽锅炉各两台,20t两台锅炉采用水膜除尘器,公用烟囱高30米;两台10吨锅炉各采用文丘里水膜除尘器,两烟囱各高25米。
废气污染物排放情况见表3-4。
表3-4 现有装置废气排放情况污染源处理前处理措施处理后效率高排气量m3/h浓度mg/m3排气量m3/h浓度mg/m3%度m20t 锅炉35140SO2 2049麻石水膜除尘器38654SO2 13323530烟尘2134烟尘249.388.310t 锅炉17880SO2 2013文丘里水膜除尘器20563SO2 11684225烟尘2097烟尘239.488.6HCl尾气--尾气吸收塔10502199.815电解氢气1632H2:62500部分回收多余排放500H2:62500利用7020事故氯气<1100m3/次Cl2 950893(60%)水封吸收无组织排放基本不变基本不变微1氯气无组织排放量 2.04kg/h由表3-4可以看出,电解氢气只利用了70%,其余皆放空;氯化氢合成尾气排放速率为0.022kg/h,符合《大气污染物综合排放标准》》(GB16297-1996)。
在调查监测期间,氯气无组织厂外监控点浓度低于《大气污染物综合排放标准》。
由于事故氯气没有得到有效的处理,一旦事故发生,由于氯气的溶解度较小,管道水封几乎起不到任何作用,将造成大量氯气的外泄,引起环境污染,对厂区及附近居民或农田造成危害。
10t/h锅炉烟气经文丘里水膜除尘器除尘和脱硫后,烟尘及SO2符合《锅炉大气污染物排放标准》(GB13271-91),但排放高度不达标,其高度应大于40米。
20t/h锅炉烟气经麻石水膜除尘器除尘和脱硫后,烟尘符合排放标准,SO2不达标,排放高度也不达标,其高度应大于45米。
3、废渣盐水工段产生的盐泥,排放量为1680t/a,其中含NaCl9%、泥沙61%,目前排入废水处理池沉淀后,定期捞出沉淀物送盐泥池堆存;漂白液废渣,产生量300t/a,主要成分为Ca(OH)2,漂白液废渣经压滤后用来铺路;锅炉燃煤产生大量炉渣及除尘后的粉煤灰,产生量为5938t/a,粉煤灰、炉渣一起卖给用户烧砖。
废渣排放见表3-5。
表3-5 废渣排放一览表序号产生源主要成分产生量(t/a)处置措施1盐水工段盐泥泥沙、NaCl1680堆存2漂白液废渣Ca(OH)2300铺路3锅炉粉煤灰5938出售4、噪声厂内噪声源主要来自各种泵、罗茨鼓风机、氨压缩机等。
主要噪声源见表3-6。
表3-6 主要噪声源序号噪声源排放方式声压级dB(A)降噪措施1氯压机连续100室内布设2氢压机连续95室内布设3纳氏泵间断95室内布设4锅炉引风机间断95隔声厂区内高噪声设备较多,大部分设备位于车间内部,且厂区较大,厂界噪声经监测大部分点位符合《工业企业厂界噪声标准》,只有厂区西南角处厂界噪声夜间为56.1dB(A),超过标准值1.1dB,主要是锅炉房噪声所致。
(八)现有环保措施根据1989年黄骅氯碱厂委托天津大沽化工厂设计所编制的《华北制药厂黄骅氯碱分厂1万吨/年烧碱改造扩建工程初步设计(环境保护篇)》,以及1991年7月1日编制的《华北制药厂黄骅氯碱分厂年产3万吨烧碱扩建项目工程可行性研究报告》,氯碱厂目前应有以下环保措施:1、废水处理措施(1)废氯处理设施,包括脱氯塔和漂液设施,氯水先经脱氯塔脱氯后,氯气回工艺,废氯水生产漂白液。
目前本装置未设脱氯塔,氯处理产生的氯水直排下水道,汇入循环水池;现有漂液装置的氯源为液氯工段的废氯。
由于氯水中活性氯浓度极大,仅仅由于稀释的原因使得排水口浓度降低,但仍超标。
(2)修槽废石棉绒过滤池,修槽时含石棉绒的冲洗水经沉淀过滤,加以回收,外售作石棉瓦。
目前电解车间未设石棉绒过滤池,造成电解车间排水中石棉悬浮物浓度较高。
(3)废水处理(中和)池,各车间排出的废水通过下水道汇集在废水处理池中,通过检测pH值,适量加入酸碱,调整pH值,达到国家排放标准。
该厂现有循环水池一套,总面积13000m2,全厂所有废水都汇集于此,经沉淀,澄清后回用全厂循环水系统。
水位高出一定水平时,池水溢流外排。
循环水池的利用提高了全厂水循环利用率,同时外排水经过较长时间的沉淀也在感官上较澄清。
循环水pH值每天由环保科监测,但只考虑到工艺的满足条件,外排水碱性较大,超标严重。
2、废气处理措施(1)开、停车氯气处理措施,开停车时由于设备内有空气存在,氯气的纯度较低,全部送漂液工段处理。