3轴向力及其平衡
平衡轴向力的方法
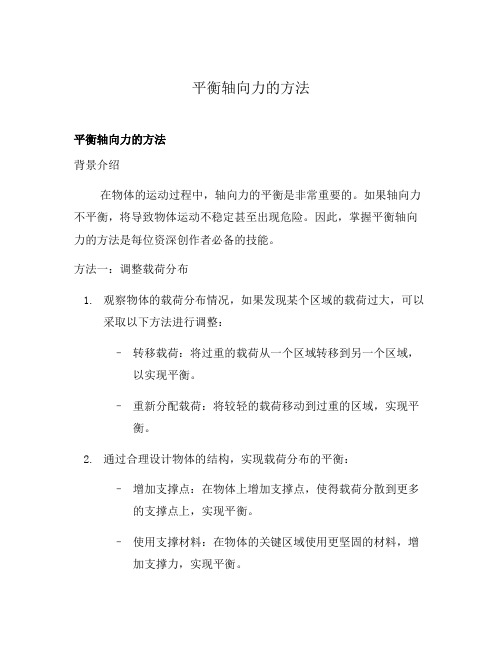
平衡轴向力的方法平衡轴向力的方法背景介绍在物体的运动过程中,轴向力的平衡是非常重要的。
如果轴向力不平衡,将导致物体运动不稳定甚至出现危险。
因此,掌握平衡轴向力的方法是每位资深创作者必备的技能。
方法一:调整载荷分布1.观察物体的载荷分布情况,如果发现某个区域的载荷过大,可以采取以下方法进行调整:–转移载荷:将过重的载荷从一个区域转移到另一个区域,以实现平衡。
–重新分配载荷:将较轻的载荷移动到过重的区域,实现平衡。
2.通过合理设计物体的结构,实现载荷分布的平衡:–增加支撑点:在物体上增加支撑点,使得载荷分散到更多的支撑点上,实现平衡。
–使用支撑材料:在物体的关键区域使用更坚固的材料,增加支撑力,实现平衡。
方法二:调整运动速度1.调整转速:如果物体的轴向力不平衡是由于旋转速度过快或过慢导致的,可以采取以下方法进行调整:–减速:降低旋转速度,减小轴向力。
–加速:增加旋转速度,平衡轴向力。
2.调整运动方向:–改变物体运动的方向,使得轴向力得到平衡。
方法三:使用平衡器1.在物体上添加平衡器,例如平衡块,以实现轴向力的平衡。
2.使用电子平衡器进行实时监测,根据监测结果进行相应的调整,保持轴向力的平衡状态。
方法四:考虑空气动力学效应1.分析物体在运动过程中的空气动力学特性,了解空气对物体产生的阻力和轴向力。
2.根据分析结果,采取相应的措施,减小或者平衡空气对物体产生的轴向力。
方法五:实施质量调整1.增加或减小物体的质量,在合适的位置添加质量块,实现轴向力的平衡。
2.通过质量调整,改变物体的转动惯量,从而影响轴向力的平衡。
以上是一些针对平衡轴向力的方法,创作者可以根据实际需求选择合适的方法来实现轴向力的平衡。
通过合理应用这些方法,将能够提高物体的稳定性和安全性,为创作活动提供有力支持。
多级离心泵常见的轴向力平衡装置

多级离心泵常见的轴向力平衡装置軸向力平衡装置的选取是多级离心泵设计中的关键问题,其目的是平衡轴向力,防止转子的轴向窜动。
文章分析了多级离心泵轴向力产生原因,并介绍了常用的平衡装置。
标签:多级泵;轴向力;平衡装置引言多级离心泵在电力、石油化工等行业被广泛应用。
轴向力平衡装置的选取是泵组设计的关键问题,检查平衡装置是否需要更换或优化也是多级离心泵维修中的一项重要工作。
泵组运转过程中,若平衡装置不能中和泵组产生的轴向力,则会造成泵动静部件摩擦而降低效率,严重时泵转子与各静部件咬死而导致泵损坏。
1 轴向力的产生多级离心泵运行过程中产生的轴向力包括以下几种:因作用在各叶轮吸入端(驱动端)和吐出端(自由端)的压力不相等,从而产生指向泵驱动端的轴向力;液体从吸入口到排出口改变方向时作用在叶片上的力,指向叶轮背面,称为动反力;由于泵内叶轮进口压力与外部大气压不同,在轴端和轴台阶上产生的轴向力;立式泵转子重量引起的向下的轴向力;其他轴向力。
2 轴向力的平衡装置总轴向力会使转子轴向窜动,造成泵动静部件摩擦,而平衡装置的两端有一个压力差,其中的液体形成一个与总轴向力方向相反的平衡力,平衡力大小随平衡盘的移动而变化,直到与轴向力抵消,但由于惯性的作用转子不会立即停止窜动,而是在平衡位置左右窜动且幅度不断减小,最终停留在平衡位置,故随着运行工况的变化,泵转子始终处于动态平衡状态。
平衡装置的设计为多级离心泵设计中的重点,包括叶轮对称布置(适用于偶数级泵)与平衡盘(鼓)法两大类,平衡盘(鼓)法又包括平衡鼓、平衡盘、平衡盘鼓、双平衡鼓形式,随着结构的逐渐复杂,平衡效果也越好。
平衡盘(鼓)法多与推力轴承配合使用,推力轴承一般只承受5%~10%的轴向力,在设计平衡盘(鼓)时,一般不考虑推力轴承平衡的轴向力,保证泵在推力轴承损坏的情况下,平衡盘(鼓)仍能正常工作。
2.1 叶轮对称布置法叶轮级数为偶数时可采用叶轮对称布置法平衡轴向力,设计上要注意反向叶轮入口前的密封节流衬套尺寸要与叶轮轮毂尺寸一致。
离心泵轴向力计算式应用与平衡

离心泵轴向力计算式应用与平衡作者:于锡平来源:《科学与财富》2014年第02期摘要:离心泵在工作过程中,可靠运行的一个重要方面就是平衡部件(平衡盘或平衡鼓)和推力轴承的设计,一般在多级离心泵的叶轮上不考虑平衡轴向力的结构,因此,泵轴向力计算的准确程度影响到平衡部件、推力轴承的设计和使用寿命,本文经多年的设计实践,提出较理想的轴向力计算式,基本在设计卧式多级泵或立式多级泵的平衡盘或平衡鼓的部件时没有失误,可以借鉴。
关键词:离心泵;轴向力;计算式应用;平衡1. 轴向力产生的原因由于叶轮前后盖板因液体压力分布情况不同引起很大的轴向力,叶轮后盖板所受压强大于前盖板所受的压强,形成的压力差,方向自叶轮背面指向叶轮入口,这个力是泵轴向力的主要组成部分。
泵在正常运行时,叶轮吸入口的压力P1,叶轮背面的压力为P2,且P2>P1,因此沿着泵的轴向方向就会产生一个推力。
液体流经叶轮后,由于流动方向变化所产生的动压力F2,在多级离心泵中,流体通常由轴向流入叶轮,由径向流出,流动方向的变化是由于流体受到叶轮的作用力,因此流体也给叶轮一个大小相等、方向相反的反作用力。
扭曲叶片工作面和背面压力不同产生的轴向力。
对于立式泵,转子的重量也是轴向力的组成部分。
其它因素产生的轴向力。
2. 轴向力计算式探讨假定叶轮两侧间隙液体压力分布规律相同,则有轴向力F1=π/4(D21-dh2)ρg[HP-U22/8zg{1-(D21-d2h)/2D22}],实际上,由于存在泄漏,轮盖两侧会有液体从外径处经轮盖密封流向吸入口,轮盘测则由于级间泄漏,有液体自高压级漏失到低压级,从叶轮内径处流向外经处,在轮盖测,液体做向心的径向流动,所以压力要减小,而在轮盘测,液体作离心的径向流动,所以,压力要增大,这样一来,轴向力F1的实际值比上式要大一些,所以,一般使用经验公式F1=(π/4)(D21-d2h)ρgkHi,其中,k为实验系数,与比转数有关,当nS=60-150时,k=0.6;当nS=150-250时,k=0.8;i为叶轮级数。
轴向力径向力及平衡

第10讲:轴向力径向力及平衡10.1 轴向力产生的原因1.泵在运转时,叶轮前后盖板压力不对称产生轴向力,其力的方向指向吸入口方向。
2.动反力:液体从吸入口到排出口改变方向时作用在叶片上的力,该力指向叶轮后面。
3.泵内叶轮进口压力与外部大气压不同在轴端和轴台阶上产生的轴向力。
4.立式泵转子重量引起的轴向力,力的方向指下面。
5.其它因素:泵腔内的径向流动影响压力分布;叶轮二侧密封环不同产生轴向力。
10.2 轴向力的计算10.2.1 叶轮前后盖板不对称产生的盖板力A1假设盖板二侧腔的液体无泄漏流动,并以叶轮旋转角速度之半ω/2旋转,则任意半径R 处的压头h‘为:h‘=(ω2/8g)(R22-R2)R2-叶轮外径半径假定叶轮进口轴面速度与出口轴面速度相等,V m1=V m2,进口圆周分速度V u1=0叶轮出口势扬程H P=H T-((g H T/u2)2/2g)= H T(1-(g H T//2u22)叶轮后盖板任意半径处,作用的压头差为:h=H P-h‘=H P-(ω2/8g)(R22-R2)将上式二侧乘以液体密度ρ和重力加速度g,并从轮毂半径积分到密封环半径,则得盖泵轴向力A1=πρg(R m2-R h2)[H P-(ω2/8g)((R22-(R m2+R h2)/2))]10.2.2 动反力A2A2=ρQ t(V mo-V m3COOα)(N)其中ρ-流体密度(Kg/m3)Q t-泵理论流量V mo V m3 -叶片进口稍前和出口稍后的轴面流速α-叶轮出口轴面速度与轴线方向的夹角10.2.3 总的轴向力:A= A1-A2对多级泵:A=(i -1)(A C)+ A S i-叶轮级数A C-次级叶轮轴向力A S-首级叶轮轴向力按上述方法计算得到的轴向力,通常比实际的要小15~20%。
对泵吸入口对大气有压力的,必须计入轴头和轴肩园截面上产生的轴向力。
对立式泵还应计入转子的重量。
10.3 轴向力的平衡10.3.1 平衡轴向力的主要方法:1.采用推力轴承平衡轴向力2.用平衡孔平衡轴向力3.单级泵采用双吸叶轮平衡轴向力,多级泵采用叶轮背靠背对称布置平衡轴向力。
三轴试验相关理论知识

三轴试验相关理论知识一、基本概念 1.常用术语法向力——垂直于滑动面上的应力,也叫正应力σ。
σ=N/A (N :作用于滑动面的力;A :滑动面的面积)剪应力——与法向力垂直的切向应力τ。
τ=F/A (F :与法向力相垂直的摩擦力) 主平面——没有剪应力的平面。
主应力——主平面上的法向应力(正应力)。
在相互垂直的立方体上(图1)又分成:大主应力(σ1)——轴向应力; 小主应力(σ3)——径向应力;中主应力(σ2)——界于大、小主应力之间的径向应力。
(常规三轴试验的试样呈圆柱形,中、小主应力相等,即σ2=σ3,谓之轴对称条件下的试验。
)偏应力——轴向应力与径向应力(或大、小主应力)之差,即(σ1-σ3)。
摩檫角——剪应力达到极限(土体开始滑动)时的剪破角Φ,此时Φ=α(tan Φ为摩檫系数) 图1 主应力与主应力面抗剪强度——随着剪应力的增加,剪阻力亦相应增加。
而剪阻力达到一定限度就不再增大这个强度称为土的抗剪强度。
2.摩尔圆摩尔圆源自材料力学之应力圆,由于是科学家摩尔首先提出的,故叫摩尔圆。
(图2)通过土体内某微小单元的任一平面,一般都作用着一个合应力,并可分解为法向应力(σ)和剪应力(τ)两个分量。
如图3,沿圆柱体轴线取一个垂直面作应力分析,可得如下的关系式:将两式平方后相加,整理后得出 图2 摩尔应力园上式的几何意义是,在σ-τ坐标系里以(σ1+σ3)/ 2,0为圆心、(σ1-σ3)/ 2为半径的圆。
ασστασσσσσ2sin )(212cos )(21)(21313131-=-++=2312231)2()2(σστσσσ-=++-在三轴试验轴对称时的平面上,当试样给定σ1和σ3,如果已知试样上的大、小主应力面的方向,就可以从摩尔圆上确定试样内任一斜面上的剪应力τ和法向应力σ。
摩尔圆在σ-τ坐标系里的应力关系如图4所示。
图的右边为一三轴试样,左边为相应的摩尔圆。
过圆的D 点(σ1)作平行于试样大主应力面AB 线,交圆上Op 点;过圆E 点(σ3)作平行于小主应 力面AC 线,必通过Op 点(∵AB 与AC 正交,∠DEOp 是半圆的圆周角)。
轴向力及其平衡

6.另一种平衡装置 它是把一对动、静摩擦副装在末级叶轮之后,端 面摩擦副前是末级叶轮出口的高压液体,端面摩擦副 之后与某一低压级连通,由此密封端面把高压液体与 低压区隔开。作用于末级叶轮进口处的高压(等于n 一1级泵的压力)和作用于末级叶轮后面的低压(如等 于大气压力)之差,构成指向叶轮后方的总压力,用来平 衡作用在各级叶轮上指向叶轮前方的总平衡力。
4.平衡鼓
平衡鼓是个圆柱体,装在末级叶轮之后,转子一 起旋转。平衡鼓外圆表面与泵体间形成径向间隙 。平衡鼓前面是末级叶轮的后泵腔,后面是与吸 入口相连通的平衡室。这样作 用 在平衡鼓上的压差,形成指 向背向吸入口的平衡力,该力 用于平衡作用在转子上的轴 向力。
5.双吸叶轮或叶轮对称布置
单级离心泵可以将叶轮做成双吸叶轮,对于多级泵, 可以将其叶轮半数对半数,面对面或背靠背按一定次 序排列起来,可以使轴向力相互平衡,这种方法主要 用于蜗壳式多级泵。 节段式泵对称布置可以平衡轴向力,但级间泄漏增加。
离心泵轴向力平衡
班级: 体(卓越)1102
目录
1.产生轴向力的原因 2.轴向力的平衡
泵在运转中,转子上作用着轴向力,该力将拉动转 子轴向移动。轴向力产生原因可分为以下几类: 1.叶轮前后盖板不对称压力产生的轴向力,这是所 有轴向力中最重要的一个因素。又由于叶轮盖板的形 状是不规则的,所以其轴向力大小比较复杂,此力指 向压力小的盖板方向,用F1表示; 2.液体流过叶轮由于方向改变产生的冲力(动反力) ,此力指向叶轮后面,用F2表示; 3.轴台、轴端等结构因素引起的轴向力,用F3表示; 4 .转子重量产生的轴向力,其方向与转子的布置方 式有关,用F4表示; 5.其他;
缺点:1.不能完全平衡轴向力; 2. 容积损失增加; 3.经平衡孔的泄漏流与进入叶轮的主液流相冲 击,破坏了正常的流动状态,会使泵的抗汽蚀性 能下 降。
离心泵轴向力的产生及平衡措施

离心泵轴向力的产生及平衡措施许华峰【摘要】分析离心泵轴向力产生的原因,根据具体实际情况采用平衡措施,有效减少泵的故障,为装置平稳运行创造有利条件,同时也降低了维修成本.【期刊名称】《中国设备工程》【年(卷),期】2015(000)012【总页数】3页(P61-63)【关键词】轴向力;平衡措施;轴向力计算【作者】许华峰【作者单位】山东天弘化学有限公司,山东东营 257000【正文语种】中文【中图分类】TH311离心泵在运转时产生轴向力,流体作用在转子上的轴向力主要是由于其作用在叶轮两侧的压力分布不对称而引起的,此轴向力在工况稳定的情况下是一定值,即静态轴向力,设计时一般采用平衡装置将其平衡掉,剩余部分由止推轴承承担;而实际上,作用在止推轴承上的轴向力并不是固定不变的,运行工况、密封间隙、制造及装配误差等因素均会引起轴向力的变化,轴向力的变化部分称之为动态轴向力,而它是平衡装置无法平衡的。
加上各种轴向力计算公式理论上都存在着误差,静态轴向力的平衡也是不准确的。
这两方面是引起泵本身及电动机损坏的主要原因,极易造成作用在止推轴承上的轴向力过大或过小,轴向力过大则造成烧瓦、断轴、密封隔板的损坏或增大止推轴承的摩擦,主轴、叶轮向进口方向移动致使叶轮与泵壳发生摩擦,电动机负载加大;如果轴向力过小,则会引起转子的前后窜动。
1.轴向力的产生在离心泵中液体是在低压力P1下进入叶轮,而在高压力P2下流出叶轮。
由于出口压力大于进口压力及叶轮前后盖板的不对称,使得叶轮两侧所受的液体压力不相等,因而产生了轴向推力,如图1所示。
从图1可以看出,作用在叶轮右边的压力为:P右=πr22P2;作用在叶轮左边的压力为:P左=πr12P1+π(r22-r12)P2。
式中r1、r2为叶轮的内、外圆半径,ΔP=P右+P左=πr12(P1-P2)。
因P2>P1,故ΔP是正值。
因此当离心泵运转时总有一个沿轴并指向吸入口的力作用在转子上。
叶轮入口部位是低压,而出口及叶轮背部是高压,在叶轮的前轮盖和后轮盖之间形成压差,这个压差就形成了轴向力。
汽轮机原理-3-3多级汽轮机的轴向推力及平衡方法

d 2 ( pd
p2 )
其中, pd为叶轮前的压力。
d1
d2
4
第三节 级汽轮机的轴向推力及平衡方法
一. 多级汽轮机的轴向推力
3、作用在轴封凸肩上的轴向力 Fz3
Fz3
4
(d12
d22 )p
汽轮机某一级的轴向推力为:
F' z
Fz1 Fz 2
Fz 3
多级汽轮机总的轴向推力为各级轴向推力之和。即 :
2. 转子设计成转鼓形式:适用于反动式汽轮机
反动式汽轮机,各级的反动度较大
动叶片两侧的压差很大
转子设计成转鼓形式, 减少每级叶轮上产生的轴向推力
px p0
Fz
7
第三节 级汽轮机的轴向推力及平衡方法
二. 轴向推力的平衡方法
3. 叶轮上开平衡孔 适用于冲动式汽轮机
平衡孔
在叶轮上开设平衡孔可以减少叶轮两侧的压力差,
一. 多级汽轮机的轴向推力
蒸汽通过汽轮机通流部分膨胀作功时,对叶片的作 用力由圆周分力和轴向分力所组成。其中,圆周分力推动 叶轮作功,而轴向分力则对转子产生一个轴向推力。
在一般情况下,作用在一个冲动级上的轴向推力 由 3 部分所组成:
1、作用在动叶片上的轴向力 Fz1 2、作用在叶轮面上的轴向力 Fz2
Fz Fz'
d1
d2
5
第三节 级汽轮机的轴向推力及平衡方法
二. 轴向推力的平衡方法
在多级汽轮机中,总的轴向推力很大。特别是反动式汽轮机,其总的轴向推力可达 200~300T,冲动式汽轮机,其总的轴向推力可达40~80T。这样大的轴向推力是推力轴 承所不能承受的。因此,必须设法减少总的轴向推力,使之符合推力轴承的能承载能力。 也就是说,对汽轮机总的轴向推力应加以平衡。
- 1、下载文档前请自行甄别文档内容的完整性,平台不提供额外的编辑、内容补充、找答案等附加服务。
- 2、"仅部分预览"的文档,不可在线预览部分如存在完整性等问题,可反馈申请退款(可完整预览的文档不适用该条件!)。
- 3、如文档侵犯您的权益,请联系客服反馈,我们会尽快为您处理(人工客服工作时间:9:00-18:30)。
第三节离心泵的轴向力一、轴向力的产生双吸叶轮由于叶轮对称布置,轴向力相互平衡,所以不存在轴向力。
但是单吸叶轮不具备像双吸叶轮那样的对称性,由于作用在叶轮两侧的压力不等,故有轴向力存在。
下图为一般单吸多级泵叶轮两侧的压力分布情况。
叶轮吐出压力为P2,一般认为在叶轮和泵体间的液体,受叶轮旋转效应的影响以N/2(N为泵转速)速度旋转,所以在叶轮和泵体间的压力是按抛物线形状分布的。
图的右侧是在叶轮后盖板上压力分布情况,左侧为在前盖板上压力分布情况。
由图中可见,在密封环半径r w以上,叶轮两侧的压力是对称的,没有轴向力。
在密封环半径r w以下,作用在左侧的是叶轮入口压力P1,作用在右侧的仍是按抛物线分布的压力。
因此,两侧压差ABCD乘相应的面积就是作用在叶轮上的轴向力。
轴向力的大小可按下列经验公式计算:F1=KHiγπ(rw2-rh2)式中F1—作用在一个叶轮上的轴向力(公斤);Hi—单级杨程(米);γ—液体重度(公斤/米r w—叶轮密封环半径(米);r h—叶轮毂半径(米);K—实验系数。
与比转数有关。
当n s =40–200时,K=0.6–0.8。
半开式(没有前盖板)叶轮的形状与比转数有关。
作用在半开式叶轮上的轴向力也与比转数有关,可以近似地用下列经验公式计算:F1=2πr1d1kHiγ式中k—轴向力系数;d1—圆心在叶片进口边上,并与叶轮轮廓相切的圆的直径(米);它的圆心处的半径就是r1(米)。
除了由于压力不对称所引起轴向力以外,液体的反冲力也能产生轴向力。
液体进入叶轮后运动方向由轴向变为径向,就给予叶轮一个反冲力,其方向与轴压力不对称所引起的轴向力相反。
在起动时,由于泵内正常压力还没有建立,所以反冲力的作用比较明显。
如:起动时深井泵转子上串,多级泵转子后串,都是这个原因,但是正常运转中,这个力是比较小的,可以忽略不计的。
除了由于叶轮外部压力分布不对称相起轴向力外,叶轮内部压力不对称也级引起轴向力。
我们知道,叶片工作面压力大于叶片背面的压力。
扭曲叶片的工作面在平面图上的投影面积为,叶片背面在平面图上的投影面积为,叶片工作面和背面的压力乘以相应面积后的差值就是轴向力。
由叶轮内部压力分布不对称所产生的轴向力方向是指向前盖板的。
现在还没有适当的方法计算这个力,由于这个力不大,一般也不考虑。
对一般入口压力较低的泵来说,只要计算由叶轮两侧压力分布不对称所引起的轴向力就可以了,但是对入口压力较高的悬臂式单吸泵来说,还必须考虑由作用在端上的入口压力所引起的轴向力。
二、轴向力的平衡如果不设法消除和平衡叶轮上的轴向力,泵的转动部分(转子)必然在轴向力推动下发生串动,转子与泵体发生研磨,使泵不能工作。
因此克服轴向力并限制转子的轴向串动,是必须的。
经过长期的生产实践,人们从分析轴向力产生的原因中找出了以下平衡轴向力的方法1.利用对称性,平衡轴向力从分析对称形状的双吸叶轮可知,它是由两个相互对称的单吸叶轮靠在一起构成的,相当于两个单吸叶轮并联工作,这种叶轮的轴向力是自动平衡的。
根据这个道理,把两个叶轮背靠背地或面对面地装在一根轴上,并使它们串联工作,这就成了多级泵。
尽管在单个叶轮上仍有轴向力的作用,但是,对由两个对称叶轮组成的泵转子整体说不,却没有轴向力了。
这个办法,广泛的应用在单吸两级悬臂泵、涡壳式多级泵以及筒袋泵、立式多级泵等产品上。
2.改造叶轮,以减小或平衡轴向力用改造叶轮形状的办法,降低叶轮背面压力,达到平衡或减小轴向力的目的。
2.1在叶轮后盖上装密封环,其直径与前盖板密封环直径相等。
后盖板上的密封环与叶轮后盖板上的平衡孔相配合,或与泵体上的平衡管相配合,就能平衡大部分轴向力。
这样的叶轮两侧的压力基本是是平衡的。
这种泵结构简单,只是有一部分液体流回叶轮吸入口,降低了泵的容积效率.通常取平衡管截面面积或平衡孔截面总面积为密封环间隙环形截面面积的3-6倍。
在用平衡孔平衡轴向力时,平衡孔的位置对平衡轴向力的程度和泵效率有一定影响。
一般的说,平衡孔越靠近密封环,平衡轴向力的效果越好,但由于叶轮流道中的液流受到平衡孔液流的冲击,所以泵效率略有降低,如图所示。
平衡孔或平衡管在单级泵上广泛采用。
在一部分小型多级泵上也有采用平衡孔和止推轴承相配合以平衡轴向力的。
2.2利用叶轮后盖板上的径向筋板平衡或减小轴向力。
筋板强迫叶轮后面的液体加快旋转,使叶轮背面压力显著下降,达到了减小或平衡轴向力的目的。
但这种方法在实际中还很少采用。
3.采用专门平衡装置在平衡轴向力的专门装置中最容易想到的就是使用止推轴承,止推轴承在小型泵中可以承受全部轴向力。
而且采取上述两种平衡轴向力办法的同时,也必须试验止推轴承来承担剩余的轴向力,并限制转子的轴向窜动。
但在分段式多级泵中,由于轴向力很大,一般止推轴承是无力胜任的。
3.1平衡鼓装置平衡鼓是个装在轴上的圆柱体,它在多级泵末级叶轮之后。
平衡鼓外圆表面与泵体上的平衡套之间,有很小的间隙。
这和活塞装在气缸里的情形完全一样。
用联通管把平衡鼓后面和泵吸入口连通起来。
这样,平衡鼓前面是高压区,压力为P(与末级叶轮背面一样),而平衡鼓后面却是低压区,压力为P O(由于和泵吸入口相通),平衡鼓受液体向后(即由叶轮入口向后盖板方向)的推力,这个力叫平衡力。
显然,平衡力与平衡鼓承压面积和平衡鼓两侧压差有关。
平衡鼓两侧压差用下列经验公式计算:P-P0=10-4[H -(1-k) ]H iγ式中(P-P0)---平衡鼓两侧压差(公斤/厘米2)H—泵的总扬程(米);H i---末级叶轮扬程(米);K---公式中经验系数,一般取K=0.6γ――液体重度(公斤/米3)单独使用平衡鼓时,必须有止推轴承配合,因为由于计算不完全切合实际,或在泵的工作点改变时,就会破坏轴向力和平衡力的平衡,整个转子上仍然会有剩余的轴向力。
此外,平衡鼓不能限制转子轴向窜动,也是需要加止推轴承的原因。
现在单独使用平衡鼓装置时较少的,有时平衡鼓与平衡盘联合使用。
在这种装置中,平衡鼓承受了50—80%左右的轴向力,这样就减少了平衡盘的负荷。
经验表明这种结构效果还是比较好的。
对于起停频繁的小型多级泵,可以采用平衡鼓与止推轴承联合使用,以平衡轴向力。
3.2平衡盘装置平衡盘装置如图P203所示。
在平衡盘装置中,除了轮毂(或轴套)与泵体之间有一个径向间隙之外,在平衡盘与泵体之间还有一个轴向间隙b0,平衡盘的后面和吸入口相通。
这样,径向间隙前的压力就是末级叶轮背面的压力P,而平衡盘后的压力P0则接近泵的入口压力。
在多级泵中,平衡盘装置两边的压差P/-P0是很大的。
液体受这个压差的作用,流过径向间隙,压力下降到P/,再流过轴向间隙,压力下降到P0,最后流到泵的入口。
在平衡盘上,由于两侧存在着压力差P/-P0,就有一个向后的力作用在平衡盘上,这个力就叫平衡力,方向与叶轮上的轴向力正好相反。
平衡盘是怎样工作的呢?平衡盘的两个间隙又有什么特点呢?当叶轮上的轴向力大于平衡盘上的平衡力时,泵转子就会向前移动,使轴向间隙b0减小,增加液体的阻力损失,因而就减小了泄漏量Q,泄漏量减小后,液体流过径向间隙的压力下降就较少了,从而提高了平衡盘前面的压力P,压力的上升,就增加了平衡盘上的平衡力。
转子不断向前移动,平衡力就不断增加,到某一个位置,平衡力和轴向力相等,达到平衡。
同样,当轴向力小于平衡力时,转子将向后移动,移动一定距离后,轴向力和平衡力达到了平衡。
但是,由于惯性,运动着的转子不会立刻停止在新的平衡位置上,还要继续移动,轴向间隙继续变化,例如间隙变小,平衡力就会超过轴向力而阻止转子继续移动,直到停止。
可是,转子停止移动的位置并非平衡位置,此时平衡力超过轴向力,使转子又向后移动,又开始了从不平衡到平衡的矛盾运动,使转子回到平衡位置。
当然,转子还是要离开平衡位置的。
离心泵在工作中,工作点是经常变化的,轴向力也就经常变化,转子就会经常发生轴向移动,以达到新的平衡。
综上所述,平衡盘的平衡状态是动态的,也就是说,泵的转子是在某一平衡位置左右做轴向脉动。
当工作点改变时,转子会自动地移到到另一平衡位置上去做轴向脉动。
由于平衡盘有自动平衡轴向力的特点,因而得到广泛应用。
离心泵在运转中,过大的轴向移动和过大的轴向脉动都是不许可的。
过大的轴向移动和轴向脉动,会使平衡盘,平衡板,叶轮,泵体发生研磨而损坏,会使泵发生振动而失去平稳性。
为了限制过大的轴向移动和轴向脉动,必须在轴向间隙改变不大的情况下,能够使作用在平衡盘上的平衡力发生较大的变化。
为此,还是要从对两个间隙的分析中找出办法来已经指出,平衡盘的自动平衡是靠轴向间隙的变化而产生的,同时也必须靠固定的径向间隙相配合,才能实现。
如果径向间隙很大,即径向间隙所造成的压力会很小,则平衡盘前面的压力将等于叶轮背面的压力P,任凭轴向间隙怎样变化,也不会改变平衡力的大小,平衡盘就失去了自动平衡的特点。
如果径向间隙很小,即径向间隙所造成的压力将很大时,在正常工作时,平衡盘前面的压力P较小,只要轴向间隙b0稍有变动,平衡盘前面的压力P 就变化很大(在b0=0时,即平衡盘与平毁板靠死时,P/接近于P;但是当平衡盘推开后P下降幅度较大)。
比较了径向间隙造成的压力下降越大,也就是平衡盘前面压力P/越低,平衡盘自动平衡能力越强,平衡盘轴向移动越小,泵工作的可靠性越高。
但是,平衡盘前面压力过低,会加大平衡盘的尺寸。
平衡盘加大,除了难以保证加工精度外,还增加摩擦损失和增加泄漏量。
因此,在确定平衡盘两侧压差比P/-P0/P-P0时,必须综合考虑平衡盘的大小,工作时稳定性,灵敏性,泄漏量以及泵的结构等多种因素。
有时,平衡盘的工作,也不像预想的那样正常。
这是因为,平衡盘的工作受到许多因素的影响,如:泵的制造质量、平衡机构的材质、液体粘性、轴向力变化以及间隙因磨损而加大等因素。
而设计计算又不可能全部反映这些因素。
广大工人在生产实践中,积累了保证平衡盘工作的宝贵经验:当平衡盘推不开发生研磨时,恰当加大径向间隙,以便增加平衡力而使平衡盘推开;当平衡盘轴向间隙过大,泄漏太大,并使泵失去平衡性时,恰当减小径向间隙,减小平衡盘前的压力,以保证平稳工作并减小泄漏量。
另外,平衡盘和平衡板的材质,表面光洁度,表面硬度,摩擦面对轴心线的垂直度都对平衡盘的工作有重要影响。