铜镍硫化精矿熔炼流程
硫化铜镍矿冶炼成低冰镍的工艺
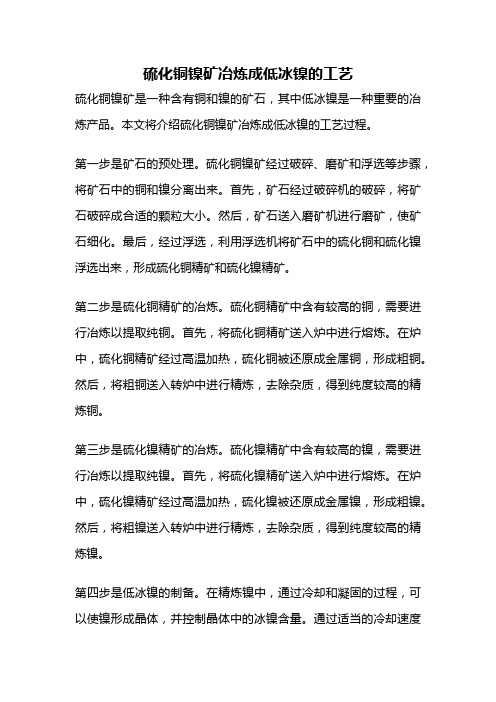
硫化铜镍矿冶炼成低冰镍的工艺硫化铜镍矿是一种含有铜和镍的矿石,其中低冰镍是一种重要的冶炼产品。
本文将介绍硫化铜镍矿冶炼成低冰镍的工艺过程。
第一步是矿石的预处理。
硫化铜镍矿经过破碎、磨矿和浮选等步骤,将矿石中的铜和镍分离出来。
首先,矿石经过破碎机的破碎,将矿石破碎成合适的颗粒大小。
然后,矿石送入磨矿机进行磨矿,使矿石细化。
最后,经过浮选,利用浮选机将矿石中的硫化铜和硫化镍浮选出来,形成硫化铜精矿和硫化镍精矿。
第二步是硫化铜精矿的冶炼。
硫化铜精矿中含有较高的铜,需要进行冶炼以提取纯铜。
首先,将硫化铜精矿送入炉中进行熔炼。
在炉中,硫化铜精矿经过高温加热,硫化铜被还原成金属铜,形成粗铜。
然后,将粗铜送入转炉中进行精炼,去除杂质,得到纯度较高的精炼铜。
第三步是硫化镍精矿的冶炼。
硫化镍精矿中含有较高的镍,需要进行冶炼以提取纯镍。
首先,将硫化镍精矿送入炉中进行熔炼。
在炉中,硫化镍精矿经过高温加热,硫化镍被还原成金属镍,形成粗镍。
然后,将粗镍送入转炉中进行精炼,去除杂质,得到纯度较高的精炼镍。
第四步是低冰镍的制备。
在精炼镍中,通过冷却和凝固的过程,可以使镍形成晶体,并控制晶体中的冰镍含量。
通过适当的冷却速度和温度控制,可以得到冰镍含量较低的镍产品,即低冰镍。
低冰镍具有较高的纯度和稳定的化学性质,适用于多种应用领域。
通过以上工艺步骤,硫化铜镍矿可以被冶炼成低冰镍。
这个工艺过程需要经过多个步骤和设备,严格控制各个环节的温度、时间和条件,以确保冶炼过程的顺利进行和产品质量的稳定性。
同时,也需要对冶炼废气和废水进行处理,以减少对环境的影响。
总的来说,硫化铜镍矿冶炼成低冰镍的工艺是一个复杂的过程,需要经过多个步骤和设备的配合。
通过合理的工艺控制和优化,可以高效地提取铜和镍,并制备出低冰镍产品。
这对于满足工业对低冰镍的需求,促进资源的合理利用和环境保护具有重要意义。
硫化铜镍矿冶炼成低冰镍的工艺

硫化铜镍矿冶炼成低冰镍的工艺硫化铜镍矿是一种含有铜和镍的硫化矿石,其主要矿物为辉黄铜矿和辉镍矿。
低冰镍是指镍含量较低的镍产品,通常用于制造不锈钢、合金等材料。
本文将介绍硫化铜镍矿冶炼成低冰镍的工艺。
硫化铜镍矿的冶炼过程可以分为矿石破碎、矿石磨矿、浮选和精炼四个步骤。
矿石破碎是指将原始的硫化铜镍矿石经过破碎设备碎成合适的颗粒度。
常用的破碎设备有颚式破碎机、圆锥破碎机等。
破碎后的矿石颗粒度应适中,不宜过细或过粗。
矿石磨矿是将破碎后的矿石进行进一步细磨,使其颗粒度更加细小。
常用的磨矿设备有球磨机、矿石磨等。
磨矿过程中需要添加一定比例的水和磨矿剂,以提高磨矿效果。
浮选是将经过磨矿的矿石与浮选剂一起放入浮选槽中进行浮选。
浮选剂通常是一种能与硫化铜镍矿石表面发生物理或化学反应的物质,使其与气泡一起上升到浮选槽表面形成浮选泡沫。
在浮选过程中,通过调整浮选剂的种类和用量,可以选择性地将铜矿和镍矿分离出来。
精炼是指将浮选后得到的铜精矿和镍精矿进行进一步的提纯和炼制。
一般情况下,铜精矿和镍精矿都需要经过烧结预处理、热浸出、电解精炼等步骤。
在这些过程中,通过控制温度、压力、气氛等条件,可以将铜和镍的纯度提高到一定水平。
总结起来,硫化铜镍矿冶炼成低冰镍的工艺主要包括矿石破碎、矿石磨矿、浮选和精炼四个步骤。
在每个步骤中,都需要选择合适的设备和工艺参数,并加入适量的矿石磨剂、浮选剂等辅助物质。
通过精心控制每个步骤的条件,可以实现硫化铜镍矿冶炼成低冰镍的目标。
当然,实际的冶炼工艺还需要根据具体的矿石性质和产品要求进行调整和优化。
此外,冶炼过程中还需要注意环境保护和能源消耗等问题,以实现可持续发展的目标。
硫化铜镍矿熔炼的概述(一)

书山有路勤为径,学海无涯苦作舟硫化铜镍矿熔炼的概述(一)闪速熔炼是火法炼镍的熔炼新技术,它克服了传统熔炼方法未能充分利用粉状精矿的巨大的表面积和矿物燃料的缺点,大大减少了能源消耗,提高发硫的利用率,改善了环境。
闪速熔炼有奥托昆普闪速炉因科纯氧闪速炉两种形式。
目前国内外有5 台奥托昆普型镍闪速炉在运转(见下表),因科型闪速炉炼镍仅作过试生产,但因镍在锍渣两相分配比较低(约65%),故一直未做工业应用。
下继续完成造锍与造渣反应,熔锍与溶渣在沉淀池进行沉降分离,熔渣流入贫化处理后弃,熔锍送转炉炊炼进一步富集成镍高锍。
熔炼产出的SO2 烟气经余热锅炉、电收尘后送制酸系统。
典型的工艺原则流程如图1 所示。
[next] 闪速熔炼系统包括熔炼、转炉吹炼等高温熔炼主系统和物料制备、配料、氧气制取、供水、供风、供电、供油以及炉渣贫化等辅助系统。
有关生产过程简要说明如下:(1)精矿干燥。
选矿精矿一般含水8%~10%,进入闪速炉前不少国家要进行干燥。
金川公司的精矿干燥采用“三段式”干燥方式,即回转窑、鼠笼、气流三段干燥。
在回转窑去除30%的水,鼠笼去掉40%的水,气流干燥去掉30%的水,得到的干精矿含水在0.3%以下,并要求粒度为-0.074mm 的碱于80%以上。
(2)粉煤与熔剂的制备。
粉煤与熔剂的制备大到相同。
煤经粗碎后,进球磨机并通入热风,磨细的煤由热风吹出分级后使用,不合格粗粒返回再磨。
石英熔剂加入球磨机后不通热风,直接用机械转换的热能把水分烘干破碎即可。
(3)返料。
闪速炉系统的自产冷料块经颚式破碎、圆锥破碎后分别送闪速炉贫化区和转炉进行处理,以回收其中的有价金属及控制转炉温度。
(4)氧气制备。
采用富氧鼓风可减少燃料的消耗,甚至实现自热熔炼。
金川公司闪速炉配备。
硫化镍矿的冶炼工艺过程

硫化镍矿的冶炼工艺过程
硫化镍矿的冶炼工艺过程通常包括以下几个步骤:
1. 矿石破碎和磨矿:将硫化镍矿石经过破碎和磨矿处理,使其颗粒细化,便于后续的浸出和冶炼操作。
2. 浸出:将磨碎后的硫化镍矿石与酸性溶液(通常为硫酸)进行浸出反应,将镍和其他有价金属溶解出来形成溶液。
这个过程通常在高温和高压条件下进行,以提高浸出效率。
3. 溶液净化:将浸出得到的含镍溶液进行净化处理,去除其中的杂质和其他有害物质。
这个过程通常包括沉淀、过滤、中和、溶液调节等步骤。
4. 镍的分离和提纯:通过一系列的化学反应和物理分离方法,将溶液中的镍与其他金属离子分离开来。
常用的方法包括溶液萃取、电解、氢气还原等。
5. 镍的精炼:将分离和提纯得到的镍进行进一步的精炼处理,以提高其纯度和质量。
这个过程通常包括电解精炼、熔炼、真空蒸馏等步骤。
6. 镍的制品加工:将精炼得到的镍进行加工和制造,制成各种镍制品,如合金、电池材料、化工原料等。
需要注意的是,不同的硫化镍矿石的冶炼工艺可能会有所不同,具体的工艺流程和操作条件会根据矿石的成分和性质进行调整。
此外,环保和能源消耗也是冶炼工艺设计中需要考虑的重要因素。
铜矿的熔炼工艺与冶炼设备

感谢您的观看
汇报人:
熔炼设备:包括熔炼炉、鼓风机、冷却塔等设备
熔炼过程中的化学反应:包括氧化还原反应、硫化反应等化学反应
铜矿的熔炼过程
矿石准备:将 铜矿石破碎、 研磨、混合,
制成矿粉
熔炼反应:将 矿粉与熔剂、 燃料等混合, 在高温下进行
熔炼反应
熔融提取:将 熔融后的铜液 与熔渣分离,
提取铜液
精炼提纯:将 提取的铜液进 行精炼提纯,
熔炼炉:用于铜矿的熔炼,提高铜的纯 度
电解槽:用于铜的电解,提高铜的纯度
冷却设备:用于铜的冷却,防止铜的氧 化
净化设备:用于铜的净化,去除铜中的 杂质
铸锭设备:用于铜的铸锭,便于运输和 储存
检测设备:用于铜的质量检测,确保产 品质量
铜矿的冶炼设备发展趋势
节能环保:提高能源利用率,减少废气、废水、废渣等污染物排放
自动化与智能化:采用先进的自动化和智能化技术,提高生产效率和产品质量
提高设备使用寿命:通过改进设备材料和工艺,提高设备的耐腐蚀、耐磨损等性能,延长设备使 用寿命
降低生产成本:通过优化设备设计和生产工艺,降低设备投资和运行成本,提高企业经济效益
铜矿的熔炼工艺 与冶炼设备的比 较与选择
铜矿的熔炼工艺与冶炼设备的比较
得到纯铜
铜矿的熔炼方法
火法熔炼:通过高温加热,使铜矿中 的金属元素与氧、硫等元素发生化学 反应,生成熔融状态的金属和熔渣。
电炉熔炼:利用电能产生高温,使铜 矿中的金属元素与氧、硫等元素发生 化学反应,生成熔融状态的金属和熔 渣。
添加标题
添加标题
添加标题
添加标题
湿法熔炼:利用酸、碱等化学试剂, 将铜矿中的金属元素溶解,然后通 过电解、化学沉淀等方法提取金属。
铜的加工冶炼工艺流程

铜的加工冶炼工艺流程3.1.1 原材料(1)铜精矿在自然界中自然铜存量极少,一般多以金属共生矿的形态存在。
铜矿石中常伴生有多种重金属和稀有金属,如金、银、砷、锑、铋、硒、铅、碲、钴、镍、钼等。
根据铜化合物的性质,铜矿物可分为自然铜、硫化矿和氧化矿三种类型,主要以硫化矿和氧化矿,特别是硫化矿分布最广,目前世界钢产量的90%左右来自硫化矿。
铜矿石经选矿富集获得精矿,常见为褐色、灰色、黑褐色、黄绿色,成粉状,粒度一般小于0.074mm。
含铜量13-30%,按行业标准YS/T 318-1997《铜精矿》的规定,其化学成分和产品分类如表1。
(2)未精炼铜按国家标准GB/T 11086-1989《铜及铜合金术语》规定,未精炼铜包括冰铜、黑铜、沉淀铜和粗铜。
冰铜主要由硫化亚铜和硫化亚铁组成的中间产品,黑铜通常用彭风炉熔炼废杂铜或氧化铜矿石而产生的含杂质较多的铜,铜含量一般为60%-85%。
沉淀铜通常用铁从含铜的溶液中置换,沉淀而获得的铜和氧化铜的不纯混合物,干量计算铜含量一般约50%-85%。
粗铜是用转炉吹炼冰铜而产生的纯度不高的铜,粗铜中铜的含量一般约为98%,本标准中规定的未精炼铜,主要指的是粗铜。
粗铜按行业标准YS/T 70-1993《粗铜》的规定,按化学成分分为三个品级,见表2。
表1 铜精矿的化学成分及分类表2 粗铜的化学成分铜精矿的检验方法:铜矿水分含量的测定按GB 14263-1993《散装浮选铜精矿取样、制样方法》中的规定进行,铜精矿化学成分的测定按GB3884-2000《铜精矿化学分析方法》的规定进行。
(3)电解用铜阳极电解用铜阳极的化学成分见表3。
表3(4)铜废碎料铜废碎料涉及的范围较广,包括紫铜、黄铜、青铜、白铜的废杂料,本标准规定的铜废碎料仅指紫杂铜。
紫杂铜为铜制品所产生的各类废料、废件。
如废旧电缆、紫铜管、棒、板、块、带及带薄镀层的上述材料和其它非合金类铜废料等。
有以下5种分类及规格:第1类:(a)紫铜管、棒、板、块、带,表面干净,无油泥和其它沾附、夹杂。
矿山铜镍选矿工艺流程

矿山铜镍选矿工艺流程
1. 开采和破碎
- 采矿作业:采用露天或地下开采方式获取铜镍矿石
- 初步破碎:使用颚式破碎机或锥式破碎机将大块矿石破碎成较小块
2. 研磨
- 球磨或立式磨机:将破碎后的矿石进一步研磨成细粉
3. 浮选
- 粗铜精矿浮选:通过添加浮选药剂和空气搅拌,使铜矿物颗粒附着在气泡上,浮于矿浆液面,从而与矿渣分离
- 精矿脱水:利用滤液或离心脱水设备去除粗铜精矿中的水分
4. 烘干和熔炼
- 烘干:将脱水后的粗铜精矿进行干燥处理,降低水分含量
- 熔炼:在高温熔炉中将干燥的粗铜精矿熔化,生产粗铜
5. 电解精炼
- 阳极铸造:将粗铜浇铸成阳极板
- 电解精炼:通过电解作用,将阳极板中的铜转移到阴极板上,得到高纯度的阴极铜
6. 镍精矿处理
- 镍精矿浮选:将浮选尾矿进一步浮选,获得镍精矿
- 镍冶炼:镍精矿经过烘干、还原和熔炼等工序,生产高纯度的镍金属
7. 尾矿处理
- 尾矿池:浮选后剩余的尾矿通过管线输送到尾矿池中贮存
- 回水系统:从尾矿池回收部分水资源,循环利用于选矿工艺中
该流程包括开采、破碎、研磨、浮选、烘干、熔炼、电解精炼等多个环节,最终获得铜和镍等有价金属产品。
同时,还需要对尾矿进行妥善处理和循环水资源利用,以减小对环境的影响。
硫化铜精矿

铜的生产方法1.火法炼铜火法炼铜是当今生产铜的主要方法,世界上80%以上的铜是用火法从硫化铜精矿中提炼出来的.火法炼铜最突出的优点适应性强,耗能低,生产效率高.硫化铜精矿的火法熔炼,一般包括三个过程.第一个过程是将铜矿熔炼成冰铜,第二个过程是将冰铜吹炼成粗铜,最后把粗铜精炼成纯铜,精炼有分火法精炼和电解精炼.铜精矿熔炼成冰铜的过程,根据所有炉子不同,可分为鼓风炉熔炼,反射炉熔炼,电炉熔炼,闪速熔炼以及其他熔炼等.由于熔炼方法和设备的不同,铜精矿熔炼前必须通过魂捏,干燥,制粒焙烤或烤结,也可以直接熔炼.尽管对精矿处理不同,但熔炼后所得产品都是冰铜.吹炼一般都是在转炉中进行.吹炼的原来是冰铜,产品是粗铜.吹炼产出的粗铜,先经火法精炼,然后电解精炼产出纯铜,并回收金,银等有价金属.2. 湿法炼铜湿法炼铜是在溶液中进行的以中提炼方法.无论贫矿或富矿,氧化矿或硫化矿,都可以用湿法炼铜的方法将同提取出来.湿法炼铜用适当的溶剂浸出铜矿.使铜以例子状态进入溶液,脉石及其他杂质不溶解.浸出后经承情的过滤,得到含铜浸出液和有脉石祖上的不溶残渣既是浸出渣.浸出过程中由于一些金属盒非金属杂质与铜一起进入溶液,浸出液必须净化.净化后的浸出液置换,还原,电积等方法将同提取出来.湿法炼铜的工艺流程如下.铜矿石或铜精矿溶剂浸出渣适当处理废液粗铜精炼1. 粗铜火法精炼粗铜的火法精炼,是在精炼炉正将固体粗铜融化或直接装入粗铜熔体,然后在向其中的鼓入空气,是熔体中的氧亲和力较大的杂质如锌,铁,铅,锡,锑等发生氧化,以氧化钨的形态浮于铜熔体表面形成炉渣,或挥发进入炉气而除去,残留在同熔体中的氧经还原脱去后,铜即可浇铸成电解精炼用的阳极板的过程。
火法精炼的工艺流程.矿粗铜,紫杂铜,残极铜重油(607-810kPa)鼓风炉炉气废阳极板,垃圾铜排气阳极板铜电解精炼痛的电解精炼师以火法精炼铜为阳极,纯铜片为阴极,硫酸和硫酸铜的水溶液为电解液,在直流点的作用下,阳极上的铜和比铜更负电性的金属电化溶液,以离子状态进入电解液; 比铜更正电性的金属和某些难以融化的合物不溶于电解也而已阳极泥形态沉淀;电解也中的铜离子在阴极上电话分析,成为阴极铜,从而实现铜与杂质的分离;电解液中的比铜更负电性的离子积聚在电解也中,在净液时除去;阳极你进一步处理,回收其中的有价金属;残极送火法精炼重熔.铜电解精炼工艺流程。
- 1、下载文档前请自行甄别文档内容的完整性,平台不提供额外的编辑、内容补充、找答案等附加服务。
- 2、"仅部分预览"的文档,不可在线预览部分如存在完整性等问题,可反馈申请退款(可完整预览的文档不适用该条件!)。
- 3、如文档侵犯您的权益,请联系客服反馈,我们会尽快为您处理(人工客服工作时间:9:00-18:30)。
铜镍硫化精矿熔炼流程
我国金川公司和新疆阜康冶炼厂(处理喀拉通克铜镍矿鼓风炉熔炼产出的金属化高镍锍)镍生产的原则工艺流程如图2。
由于高镍锍除含镍和硫以外,还含有相当数量的铜,并富集了原料中的狂族金属和贵金属及钴,困此高镍锍的铜镍分离和精炼是镍冶炼工艺中的突出问题,也是多年处理硫化矿的生产关键。
在镍冶金发展的早期阶段,通常采用四种方法处理高镍锍,即分层熔炼法、选矿磨浮分离法、选择性浸出法、低压基法。
上世纪70年代以来,国内外高镍锍,即镍分离方法较多的优点,应用范围正在逐步扩大。
分层熔炼法的基本理论依据是:将高镍锍和硫化钠混合熔化,在熔融状态下,硫化铜极易溶解在Na2S中,而硫化镍不易溶解于Na2S中。
硫化铜和硫化镍的密度为5300—5800kg/m3,而Na2S 的密度仅为1900kg/m3。
当高镍锍和Na2S混合熔化时,硫化铜大部分进入Na2S相,因其中密度小而浮在顶层,而硫化镍因其密度大面留在底层。
当温度下降到凝固温度时,二者分离得更彻底,凝固后的顶层和底层很容易分开。
为了使硫化铜及硫化镍更好地分离,顶层和底层再分别进行分层熔炼,重新获得分层后的硫化铜和硫化镍,直至满足工艺要求。
由于该法工艺过程复杂、劳动条件差,且生产成本高,除个别工厂经革新后仍在使用外,现已基本淘汰。
利用选矿磨浮分离铜镍—可溶阳极电解传统工艺处理,即:吹炼成高镍锍--转炉渣电炉贫化
--高镍锍磨浮分离--阳极熔炼--电解。
该工艺的缺点是生产疚效率低,排入大气的烟气中含硫量高,耗电量大,有价金属的损失大。
湿法选择性浸出因其铜镍提取方法不同,大致可分为五种。
(1)硫酸选择性浸出电积法。
芬哈贾伐尔塔精炼厂、南非的吕斯腾堡厂均采用这一工艺。
但其流程又不完全相同。
如芬兰哈贾伐尔塔精炼厂处理的高镍锍成分为(%):Ni75、Cu15、S7、Co0.7、Fe0.5、Ni/Cu=5。
原先采用两段常压浸出,由于镍浸出率低。
现已改为三段常压浸出。
吕腾堡厂处理的高镍锍成分为(%):Ni约50、Cu约28、S约22。
采用两段加压浸出,电积提铜和电积提镍。
这种浸出分离与部分净液相结合的工艺流程比较简单:缺点是电能消耗大,当Ni/Cu比低时选择性浸出效果较差。
(2)硫酸选择性浸出氢还原。
本工艺与上一工艺相比不同之外在于以加压氢还原取代镍电积。
代表性的工厂为1974年投产的美国镍港精炼厂。
其流程为高镍锍熔化--水淬--细磨,然后经一段常压浸出和两段加压浸出液经净化后用加压氢还原法制得镍粉。
南非英帕拉厂所采用的流程与镍港精炼厂类似,不同之处是采用三段加压浸出。
本工艺与上一工艺相比,流程比较简单,但能源消耗都比较多;镍粉售价虽然较高,然而在市场销售上的灵活性不如电解镍。
(3)加压氨浸--氢还原法。
代表性的工厂有加拿大舍里特公司克莱夫科精炼厂、澳大利亚克威那拉镍精炼厂。
克威那拉镍精炼厂原设计处理硫化镍精矿,1974年后改为处理卡尔古利镍冶炼厂的高镍锍。
该法的优点是在较低温度和压力下,在碱性介质中浸出,设备的结构和防腐蚀等方面比较容易解决。
缺点是消耗大量氨,大部分硫最终氧化成硫酸根;且对含铜量高的原料亦不太适合。
(4)盐酸浸出法。
代表性工厂有加拿大鹰桥公司在挪威的克里斯蒂安松精煤炼厂的试验工厂。
其方法是经细磨后的高镍锍用浓盐酸溶液在约70℃常压下浸出12h,浸出率为98.7%。
该法选择性浸出效果很好,提镍能耗出比较低;但设备腐蚀比较严重,现已基本不采用。
(5)氯气浸出法。
挪威的克里斯蒂安松厂除了曾试验过上述盐酸浸出法外,1975年后又开始试作氯气选择性浸出新工艺,几次改进后,于1981年建成年产(4—5.5)×104t阴极镍的精炼厂。
该法的实质是,在110℃下通氯气选择性浸出镍,浸出液经置换脱铜,用碳酸镍中和脱铁,溶剂萃取公离镍钴,分别电积得到阴极镍和阴极钴。
在阳极上产生的氯气返回浸出。
高镍锍中的铜、硫几乎全部以CuS形态留于浸出渣中。
该流程的特点是浸出液体中Ni2+高达230g/L,总的溶液量少,阳极析出的氯气返回利用;与其他工艺相比,流程较为简化。
目前世界上用氯气浸出法的还的日本住友新居滨精炼厂。
羰基法生产属于气化冶金方法,以加拿大国际镍公司铜崖精炼厂采用的中压法为代表。
其高镍锍的成分为(%):Ni62、Cu14、S2.0、Fe2、Co1,在旋转转炉内用氧气吹至S为0.2%--4%,在180℃、7.2MPa压力下羰基化,产出高纯镍粉及Ni--Fe粉,铜和贵金属富集于残渣中。
该法比蒙得法效率高,但不像蒙得法要求原料中不能含硫和铜。
高压法虽然比中压法效率要高,但过程要求在200℃、18—20MPa压力下进行,中压法对原料的镍铜比及含硫量量要求比高压法要严格。
俄罗斯诺里尔斯克北镍公司是采用高压羰基法,加拿大国际镍公司英国克莱达奇精炼厂是采用低压羰基法。
从上述高镍锍的分离和精炼工艺发展来看,总的趋势是分离与精炼紧密结合,逐渐简化流程。
但各厂所采用的具体工艺条件都不尽相同,原因是与各厂的原料成分及产品形态要求不同有关,另一方面也说明高镍锍分离和精炼的工艺还有待进一步研究开发.。