车辆工程毕业设计24110发动机飞轮壳加工工艺及夹具设计
机械工艺夹具毕业设计124110发动机飞轮壳前端面钻模夹具设计说明书

毕业设计(论文)课题名称4110发动机飞轮壳前端面钻模设计学生姓名学号院(系)、专业机械与能源工程系机械设计制造及其自动化指导教师职称内容提要本次进行的是4110发动机飞轮壳前端面钻模的设计。
钻模是钻床类的专用夹具,主要用于保证在加工孔时刀具有一个确切的位置,从而保证孔的位置和精度。
本次夹具设计的步骤是:(1)研究原始资料,明确设计要求;(2)拟定夹具结构方案,绘制夹具结构草图;1)确定定位方案,选择定位元件;2)确定导向装置;3)确定夹紧机构;4)确定其它装置和夹具体;5)绘制夹具总图经过设计和讨论,终于圆满地完成了设计任务。
本次设计整个设计过程条理清晰,能让读者明白整个过程。
力求结构合理,计算准确,经济可靠。
本设计的创新之处在于简化了钻模板的结构设计,使其结构更简便,同时也能满足设计要求。
但是由于本人实践经验的欠缺和知识的局限性,设计过程中难免出现一些错误,该夹具的实际工作情况及可用性还有待于实践的检验,敬请各位领导,老师,同学提出宝贵意见和见解,本人在此表示由衷的感谢!关键词:定位;夹紧;导向目录第1章机床夹具的概述 (7)1.1 机床夹具的概念 (7)1.2 钻床夹具的组成 (8)1.3 钻模及钻模板形式的选择 (9)第2章工件定位方案的确定 (11)2.1 工件定位要则 (11)2.2 工件定位方式的选择 (13)2.3 定位件的计算 (16)2.4 定位误差的分析计算 (18)第3章导向装置的确定 (20)3.1 导向装置的概述 (20)3.2 定位孔导向装置的确定 (21)3.3 其余孔导向装置的确定 (22)第4章夹紧方案的确定 (23)4.1 夹紧机构的确定 (25)4.2 夹紧力三要素的确定 (25)第5章其它装置的确定 (27)5.1 开口垫圈的选择 (27)5.2 垫的设计 (28)第6章夹具体的设计 (28)前言机床夹具是机床上用以装夹工件(和引导刀具)的一种装置。
其作用是将工件定位,以使工件获得相对于机床和刀具的正确位置,并把工件可靠地夹紧。
(完整word版)飞轮零件的加工工艺毕业设计

2.1 确定零件毛坯的类型及其制造方法
毛坯的类型及其制造方法的选择不仅影响毛坯的制造工艺及费用,而且与零件的机械加工工艺和加工质量密切相关。
选择毛坯时应该考虑的因素有:零件的生产纲领、零件材料的工艺性、零件的结构形状和尺寸、现有的生产条件。
2.2 基面的选择
基面的选择是工艺规程设计中的重要工作之一。基面选择得正确、合理,可以保证加工质量,提高生产效率。否则,就会使加工工艺过程问题百出,严重的还会造成零件大批报废,使生产无法进行。
第二章 工艺规程设计………………………………………………2
2.1 确定零件毛坯的类型及其制造方法………………………………2
2.2 基面的选择…………………………………………………………2
2.2.1 粗基准的选择…………………………………………………2
2.2.2 精基准的选择…………………………………………………3
12.5
5
槽
10
10
10
IT9
10±0.018
3.2
6
Φ200端面
Φ200
6
200±2.8
IT12
Φ2020-0.48
3.2
2
IT9
Φ2000-0.115
7
2.2.2 精基准的选择
(1)零件已加工的表面作为定位基准,这种基准称为精基准。合理地选择定位精基准是保证零件加工精度的关键。
(2)选择精基准应先根据零件关键表面的加工精度(尤其是有位置精度要求的表面),同时还要考虑所选基准的装夹是否稳定可靠、操作方便。
(3)精基准的选择原则:
①基准重合原则。尽量选择设计基准作为精基准,避免基准不重合而引起的定位误差。
毕业设计论文-重型汽车发动机飞轮加工工艺的研究

前言目前飞轮加工的方式分为三大类:其一铸造出大飞轮盘,在进行机加工后与大齿圈进行组装;其二用材料成型工艺,用比较厚的钢板进行冲压出飞轮盘,再接着与齿圈拼装;其三用钢板卷成飞轮大圈,将辐板与内圈焊接而成。
其中方案一适合重型汽车发动机,方案二由于飞轮质量的限制,只用于小型轿车上,方案三的飞轮用于转动惯量和回转精度要求不高的地方。
国内对于重型汽车上飞轮加工多采用铸造后再粗加工、精加工,中国重汽斯太尔、江淮重卡格尔发采用的就是本种加工方案。
目前本方案也是各汽车制造厂家采取的制造方法,也是将来趋势。
对于国外重型汽车飞轮加工大多也是通过铸造后机加工等方法。
本文首先对飞轮结构、技术参数的分析,制定工艺路线,工艺方案分析与比较后进而确定更加合适的加工方案。
在方案确定之后,进行加工余量的计算,工序尺寸、尺寸链的计算确定。
本文还选取本零件的典型的工序,计算切削用量。
最后针对典型工序进行夹具的设计,完成夹具的图纸的绘制。
保证飞轮加工质量和效率是生产过程中一项非常重要的工作,也是我们研究的最终目标。
1零件分析1.1飞轮的结构特点图1.1飞轮是安装在发动机曲轴上盘类零件,其功能是调节内燃机曲轴转速变化,起稳定转速作用。
同时有利于内燃机的启动,有利于活塞顺利通过上下止点。
如图1.1在大圆盘阶梯凸台上钻有12×Φ11的孔,其作用是为了和齿圈进行连接;而在大圆盘的上面也有个未钻穿的孔,此孔是为了调节飞轮动平衡的平衡孔;在飞轮最上端的有9×Φ15的用孔,其是固定飞轮在曲轴上面的螺栓孔;在最顶端的凸台有个Φ62的孔,其作用是与曲轴一端进行配合连接,在孔内有个Φ65的内槽,其作用是储存润滑油;连接平衡孔平面和最顶端平面是∠10°过渡斜面。
其表面为铸造表面,不需要机械加工,但是可以在此面刻生产厂家信息。
1.2飞轮主要加工表面及技术参数分析[2](1)飞轮A面的平面度要求不低于0.03mm,表面粗糙度为1.6;(2)在A面上9×Φ15孔相对于A面和飞轮回转中心位置度误差不超过0.3mm,且均布在整个圆周;(3)在A面上1×Φ8的孔的相对于A面和飞轮回转中心位置度误差不超过0.1mm;(4)飞轮内孔φ62H7(+0.03)公差等级不低于IT7表面粗糙度不低于3.2;(5)飞轮内槽φ65H7(+0.30)公差等级不低于IT7,表面粗糙度不低于3.2;(6)尺寸35和46的两平面要求平面度不低于0.03;(7)在φ430h7(00.063-)外圆公差等级不低于IT7,表面粗糙度不低于3.2;且对于A面和轴线的圆跳动不超过0.1mm;(8)在尺寸46面上12×Φ11孔相对于A面和飞轮回转中心位置度误差不超过0.3mm,且均布在整个圆周;(9)在φ475H7(0.063+)公差等级不低于IT7表面粗糙度不低于3.2;而且对于基准A和B的圆跳动不超过0.1,在本尺寸的端面要求平面度不低于0.03/100,端面跳动不超过0.1;1.3飞轮主要加工表面加工方式(1)飞轮A面,止口端面采用车削方式或者铣削方式加工(2)在A面上9×Φ15、1×Φ8、12×Φ11孔采用钻削方式进行加工。
飞轮的加工工艺设计毕业设计
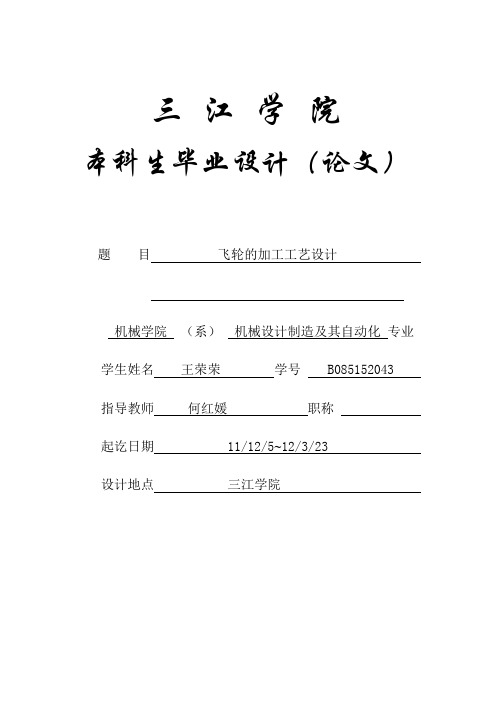
三江学院本科生毕业设计(论文)题目飞轮的加工工艺设计机械学院(系)机械设计制造及其自动化专业学生姓名王荣荣学号 B085152043 指导教师何红媛职称起讫日期 11/12/5~12/3/23 设计地点三江学院摘要本设计课题主要是通过对飞轮进行结构分析,完成实体造型,并根据企业实际情况,重点进行机械加工工艺编制,最后进行数控编程加工。
本课题的意义在于:工学结合,在学校指导老师和企业工程师共同辅导下,在零件实体设计、机械加工工艺编制、数控加工程序编制、收集资料、查阅手册等专业知识与技能方面得到较全面的训练与提高,从生产第一线获得生产实际知识和技能,获得工程技术应用性岗位工作的基本训练,培养利用所学专业知识与技能解决生产实际问题的能力。
同时课题具有一定的综合性,有利于树立正确的生产观念、经济观念和全局观念,实现由学生向工程技术人员的过渡。
关键词:飞轮;实体造型;工艺编制;数控编程;过渡。
ABSTRACTthis design issue is mainly through the flywheel to structural analysis, complete solid model, and according to the actual situation, focused on machining process of preparation, the last NC processing programming. This topics of significance is: workers learn combination, in school guide teacher and Enterprise Engineer common counselling Xia, in parts entity design, and machinery processing technology prepared, and NC processing program prepared, and collection information, and inspection manual, expertise and skills area are more full of training and improve, from production frontline get production actual knowledge and skills, get engineering technology applied posts work of basic training, training using by learn professional knowledge and skills solution production actual problem of ability. Has some general while subject, helps establish a correct concept, and global concept of economic ideas, the transition from student to the technicians.Key words:flywheel;solid modeling; process development;CNC programming; transition.序言学完了大学四年的所有课程,就要开始做毕业设计了,毕业设计课题是要集合我们所学的各门专业知识,理论与实践相结合,完成设计项目,解决工程实际问题,因此我们必须首先对所学课程全面掌握,融会贯通。
发动机活塞加工工艺及夹具设计

发动机活塞加工工艺及夹具设计一、发动机活塞的加工工艺1.原料准备:活塞的原材料一般为铝合金,需要进行铸造或锻造工艺,得到初步成型的活塞毛坯。
2.粗车:将活塞毛坯放入车床中进行粗车,将多余的材料去除,使活塞的外形接近最终形状。
3.精车:将粗车后的活塞放入精车机床中进行精车,使活塞的尺寸和形状达到设计要求。
4.铆装:在活塞上制作并安装活塞销和油垫,确保活塞的运动顺畅。
5.表面处理:对活塞进行喷砂、阳极氧化等表面处理,提高活塞的耐腐蚀性和装配精度。
6.热处理:对活塞进行热处理,提高其硬度和强度,改善活塞的使用寿命。
7.精密加工:对活塞进行高精度的机加工,如磨削、镗孔等,以满足发动机的操作要求。
8.检测和验收:对加工后的活塞进行尺寸、形状、表面质量等各项检测与验收,确保活塞的质量符合要求。
二、发动机活塞的夹具设计夹具是用于固定工件,使其在加工过程中保持正确的位置和姿态的工具。
发动机活塞的夹具设计需要考虑以下因素:1.夹紧力:夹具需要具备足够的夹紧力,以确保活塞在加工过程中不会发生位移或松动。
2.夹持方式:根据活塞的形状和结构特点,选择合适的夹持方式,如机械夹持、气动夹持、液压夹持等。
3.支撑和定位:夹具需要提供适当的支撑和定位,使活塞在加工过程中保持正确的位置和姿态。
4.可调性:夹具需要具备一定的可调性,以适应不同型号、规格的活塞加工。
5.便捷性:夹具的操作简单、快速,能够提高加工效率和工作人员的工作舒适度。
6.辅助工具:夹具需要配备适当的辅助工具,如量具、标尺等,以便进行调试和检测。
7.安全性:夹具需要具备足够的安全性,避免在加工过程中对工作人员和设备造成伤害。
总结:发动机活塞的加工工艺和夹具设计对活塞的质量和性能具有重要影响。
加工工艺需要经历原料准备、粗车、精车、铆装、表面处理、热处理、精密加工等多个环节。
夹具设计需要考虑夹紧力、夹持方式、支撑和定位、可调性、便捷性、辅助工具和安全性等因素。
通过合理的加工工艺和夹具设计,可以提高活塞的质量和性能,确保发动机的正常运行。
飞轮壳加工工艺流程
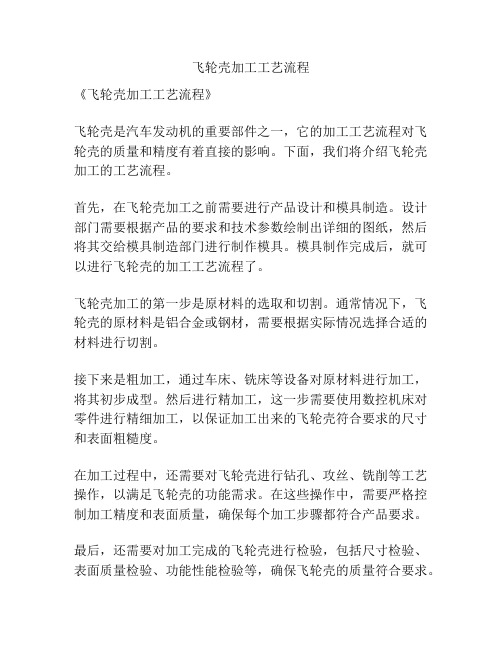
飞轮壳加工工艺流程
《飞轮壳加工工艺流程》
飞轮壳是汽车发动机的重要部件之一,它的加工工艺流程对飞轮壳的质量和精度有着直接的影响。
下面,我们将介绍飞轮壳加工的工艺流程。
首先,在飞轮壳加工之前需要进行产品设计和模具制造。
设计部门需要根据产品的要求和技术参数绘制出详细的图纸,然后将其交给模具制造部门进行制作模具。
模具制作完成后,就可以进行飞轮壳的加工工艺流程了。
飞轮壳加工的第一步是原材料的选取和切割。
通常情况下,飞轮壳的原材料是铝合金或钢材,需要根据实际情况选择合适的材料进行切割。
接下来是粗加工,通过车床、铣床等设备对原材料进行加工,将其初步成型。
然后进行精加工,这一步需要使用数控机床对零件进行精细加工,以保证加工出来的飞轮壳符合要求的尺寸和表面粗糙度。
在加工过程中,还需要对飞轮壳进行钻孔、攻丝、铣削等工艺操作,以满足飞轮壳的功能需求。
在这些操作中,需要严格控制加工精度和表面质量,确保每个加工步骤都符合产品要求。
最后,还需要对加工完成的飞轮壳进行检验,包括尺寸检验、表面质量检验、功能性能检验等,确保飞轮壳的质量符合要求。
总的来说,飞轮壳的加工工艺流程涉及原材料选取、模具制造、粗加工、精加工、工艺操作和检验等多个环节。
只有严格按照这些流程进行操作,才能保证最终加工出符合要求的飞轮壳产品。
东风飞轮壳加工工艺流程
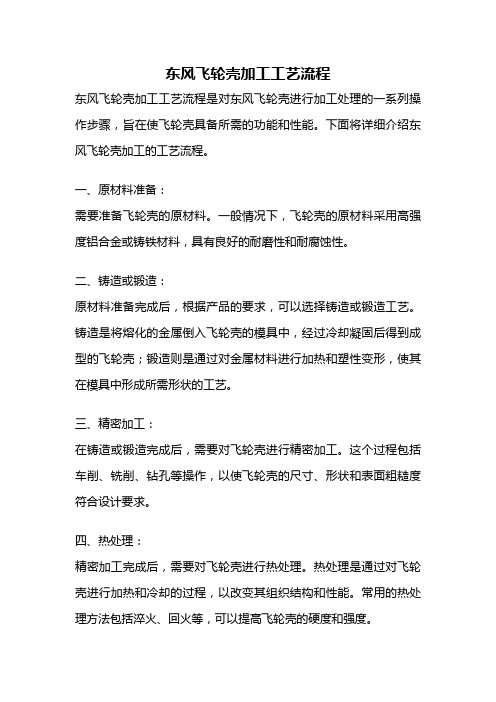
东风飞轮壳加工工艺流程东风飞轮壳加工工艺流程是对东风飞轮壳进行加工处理的一系列操作步骤,旨在使飞轮壳具备所需的功能和性能。
下面将详细介绍东风飞轮壳加工的工艺流程。
一、原材料准备:需要准备飞轮壳的原材料。
一般情况下,飞轮壳的原材料采用高强度铝合金或铸铁材料,具有良好的耐磨性和耐腐蚀性。
二、铸造或锻造:原材料准备完成后,根据产品的要求,可以选择铸造或锻造工艺。
铸造是将熔化的金属倒入飞轮壳的模具中,经过冷却凝固后得到成型的飞轮壳;锻造则是通过对金属材料进行加热和塑性变形,使其在模具中形成所需形状的工艺。
三、精密加工:在铸造或锻造完成后,需要对飞轮壳进行精密加工。
这个过程包括车削、铣削、钻孔等操作,以使飞轮壳的尺寸、形状和表面粗糙度符合设计要求。
四、热处理:精密加工完成后,需要对飞轮壳进行热处理。
热处理是通过对飞轮壳进行加热和冷却的过程,以改变其组织结构和性能。
常用的热处理方法包括淬火、回火等,可以提高飞轮壳的硬度和强度。
五、表面处理:热处理完成后,需要对飞轮壳进行表面处理。
这个过程包括喷砂、电镀、喷涂等操作,以改善飞轮壳的表面光洁度、耐腐蚀性和装饰效果。
六、装配:表面处理完成后,将飞轮壳与其他零部件进行装配。
装配过程包括与曲轴的配合、螺栓的固定等操作,以确保飞轮壳与其他部件的协调工作。
七、检测和调试:装配完成后,需要对飞轮壳进行检测和调试。
这个过程包括外观检查、尺寸测量、功能测试等操作,以确保飞轮壳的质量和性能符合要求。
八、包装和出厂:对经过检测和调试的飞轮壳进行包装,并按照订单要求进行出厂。
包装过程中需要注意保护飞轮壳的表面,防止在运输和存储过程中受到损坏。
以上就是东风飞轮壳加工的工艺流程。
通过原材料准备、铸造或锻造、精密加工、热处理、表面处理、装配、检测和调试、包装和出厂等一系列操作,可以使飞轮壳具备所需的功能和性能,确保其在实际使用中能够发挥应有的作用。
毕业设计飞轮的数控加工工艺及程序设计【大专毕业论文】

毕业设计飞轮的数控加工工艺及程序设计学生姓名:学号:班级:专业:指导教师:年月日摘要数控技术的应用不但给传统制造业带来了革命性的变化,使制造业成为工业化的象征,而且随着数控技术的不断发展和应用领域的扩大,他对国计民生的一些重要行业(IT、汽车、轻工、医疗等)的发展起着越来越重要的作用,因为这些行业所需装备的数字化已是现代发展的大趋势,是提高制造能力和水平,提高对动态多变市场的适应能力和竞争能力,是使国家加速经济发展、提高综合国力和国家地位的重要途径。
飞轮是一个惯性储能零件,拿四冲程发动机来说,进气,压缩,爆燃,排气,这是个冲程之间只有爆燃冲程是对外做正功的,其他三个冲程都是为了这个爆燃冲程所做的准备工作,这三个冲程的能量就是飞轮提供的,飞轮的能量是爆燃冲程积攒下来的,当然这是少部分能量,大部分都变成动力对外输出了。
飞轮是发动机中有重要作用但结构形状相对简单的零件之一,本文主要介绍了某发动机飞轮的数控加工工艺,从零件图纸的分析到工艺的制定,再到程序的编制,最终完成该零件的加工。
关键词:零件图工艺规程数控刀具程序设计目录第一章飞轮的作用 (1)第二章零件图分析 (2)2.1 零件图 (2)2.2零件的工艺分析 (2)第三章工艺规程设计 (3)3.1毛坯的制造形式 (3)3.2基准面的选择 (3)3.2.1粗基准的选择 (3)3.2.2精基准的选择 (4)3.3制定工艺路线 (4)第四章数控加工工艺分析 (5)4.1数控加工内容 (5)4.2数控机床的选择 (5)4.2.1数控车床参数 (5)4.2.2数控插床参数 (6)4.2.3数控铣床参数 (7)4.3夹具的选择 (7)4.3.1数控车床夹具 (7)4.3.2数控插床夹具 (8)4.3.3数控铣床夹具 (8)4.4数控刀具的选择 (8)4.4.1刀具的材料和性能 (8)4.4.2刀具的选择 (9)4.5切削用量的选择 (10)第五章工艺卡片 (12)5.1机械加工工艺过程卡片 (12)5.2数控车削加工工序卡片 (13)第六章数控加工程序清单 (14)6.1数控车床程序 (14)6.2数控铣床程序 (18)总结 (19)参考文献 (20)致谢 (21)第一章飞轮的作用(1)使机械运转均匀飞轮高速旋转,由于惯性作用可贮藏能量,也可放出能量,克服运动阻力,使发动机运转平稳。
- 1、下载文档前请自行甄别文档内容的完整性,平台不提供额外的编辑、内容补充、找答案等附加服务。
- 2、"仅部分预览"的文档,不可在线预览部分如存在完整性等问题,可反馈申请退款(可完整预览的文档不适用该条件!)。
- 3、如文档侵犯您的权益,请联系客服反馈,我们会尽快为您处理(人工客服工作时间:9:00-18:30)。
第1章绪论1.1 选题背景和目的意义飞轮壳是发动机上一个重要的基础件,作用是连接发动机与变速器,承担发动机及变速器的部分重量,保护离合器和飞轮,而且还是发动机的支撑部件。
该零件结构复杂,形似盆状,薄壁,盆底定位面有1/3悬空,工件的刚性差,加工时易变性,属难加工零件。
在选材中,了解其加工工艺,并在工艺设计中,合理安排加工工序,设计合理的夹具,对产品的最终质量具有十分重要的意义[1]。
夹具设计一般是在零件的机械加工工艺过程制订之后按照某一工序的具体要求进行的。
制订工艺过程,应充分考虑夹具实现的可能性,而设计夹具时,如确有必要也可以对工艺过程提出修改意见。
夹具的设计质量的高低,应以能否稳定地保证工件的加工质量,生产效率高,成本低,排屑方便,操作安全、省力和制造、维护容易等为其衡量指标。
飞轮壳是汽车发动机上的重要部件,它是连接发动机和变速器的主要零件。
其结构和加工工艺直接影响零件的性能。
在飞轮壳结构复杂,加工部位除了前后端面及孔之外,在周边,不同的角度上有平面加工和孔的加工。
工艺设计是工艺规划的前提和基础,是连接产品设计和生产制造的重要纽带。
产品的制造可以采用几种工艺方案,零件加工也可以采用不同设备、不同的加工方法。
不同的工艺方案。
同样一个产品,使用不同的工艺方法进行加工,就会产生不同的质量、不同的成本。
飞轮壳的主要功能是实现发动机与变速器的有效联接,通过它的变化,同一型号的发动机可以搭载不同型号的汽车,飞轮壳大多采用灰铸铁铸造毛坯,材料结构特点是壁厚不均匀,加工的部位多,加工难度大,各个加工面和加工孔均要求较高的精度。
其与发动机及离合器连接的两个面面积较大,压铸容易产生变形,并且变形量不容易控制,两个面连接孔必须进行机械加工 [2]。
夹具广泛应用于各种制造过程中,用以将工件定位并牢固的夹持在一定的位置,以便按照产品设计设计规定完成要求的制造过程,一个好的夹具不论在传统制造,还是现在知道系统,都起着十分重要的作用,夹具对加工质量、生产率和产品成本有直接的影响。
保证加工精度,采用夹具安装,可以准确的确定工件与机床、刀具之间的相互位置,工件的位置精度由夹具保证,不受工人技术水平的影响,其加工精度高,提高了生产率。
用夹具装夹工件,可以迅速定位夹紧。
扩大机床的工艺范围,使用专用夹具可以改变原机床的用途和旷达机床的使用范围,实现一机多能。
采用夹具安装,可以准确地确定工件与机床、刀具之间的相互位置,工件的位置精度由夹具保证,不受工人技术水平的影响,其加工精度高而且稳定。
用夹具装夹工件,无需找正便能使工件迅速地定位和夹紧,显著地减少了辅助工时、多工位夹具装夹工件,并采用高效夹紧机构,这些因素均有利于提高劳动生产率。
针对4110发动机飞轮壳零件进行加工工艺和夹具设计,另外,采用夹具后,产品质量稳定,废品率下降,可以安排技术等级较低的工人,明显地降低了生产成本 [3]。
除根据4110发动机飞轮壳确定参数,并完成发动机飞轮壳的工艺设计外,根据飞轮壳的工作条件和结构设计中的确定的材料性能,进行该飞轮壳毛坯和机械加工的工艺路线和加工方法的设计及专用夹具设计。
同时,该设计还培养了我综合运用所学知识,独立完成产品设计的能力,以及分析和解决问题的能力。
1.2 国内外研究现状及发展趋势飞轮壳产品是从2003年开始,比如康明斯、道依茨、卡特彼勒、水星等一些公司已经在中国寻找供应商,他们在中国设立了负责供应商目前国内生产飞轮壳的厂子不是很多,年产量一般不超过40万件。
市场分散造就资源的分散,无法形成规模效益,所以谁先能创新,谁先能投入新的工艺,谁就可能形成新的发展趋势,才能占领新的市场。
目前现代生产要求企业所制造的产品品种经常更新换代,以适应市场的竞争与需求。
然而,一般企业都仍习惯于大量采用传统的专用夹具,每隔三四年就要更新很多专用夹具。
而夹具的实际磨损仅为10~20﹪左右。
特别是近年来,数控机床、加工中心、成组技术、柔性制造系统等新加工技术的应用,对机床夹具提出了许多新的要求例如能迅速方便地装备新产品的投产,以缩短生产准备周期,降低生产成本;能装夹一些特征的工件;提高机床夹具的标准化程度。
夹具是机械加工不可或缺的部件,在机床技术向高速、高效、精密、复合、智能、环保方向发展的带动下,夹具技术正朝着高精、高效、模块、组合、通用、经济方向发展。
1.高精随着机床加工精度的提高。
2.高效为了提高机床的生产效率。
3.模块、组合夹具元件模块化是实现组合化的基础。
4.通用、经济夹具的通用性直接影响其经济性 [4]。
1.3 设计研究的主要内容本设计研究的主要内容包括发动机飞轮壳的工艺规程编制、典型工序夹具设计及夹具的绘制。
具体内容归纳如下:1.4110发动机飞轮壳加工方案设计;2.4110发动机飞轮壳工艺卡片的编制;3.专用夹具工艺设计;4.零件及钻床夹具的流程设计;5.误差计算。
第2章 4110飞轮壳的制造工艺分析2.1 飞轮壳结构特点及主要技术要求2.1.1 飞轮壳的用途及结构特点飞轮壳安装于发动机与变速箱之间,外接曲轴箱、启动机、油底壳,内置飞轮总成,起到连接、防护和载体的作用。
飞轮壳的前端面与发动机的机箱联结,后端面内孔416Φmm 与飞轮盖配合,飞轮飞轮壳内高速转动。
飞轮在高速旋转的过程中,飞轮壳起到连接、防护和载体的作用,因此该零件应具有足够的强度且应具有较强的耐磨性,以适应飞轮壳的工作条件。
该零件的主要工作表面为前端面、后端面、后端面内孔097.00416+Φmm 和马达孔087.0082+Φmm ,其表面粗糙度均为3.2,在设计工艺规程时应重点予以保证。
2.1.2 分析飞轮壳的技术要求4110飞轮壳选用的材料为HT200,珠光体灰铸铁。
该材料强度、硬度相对较高,具有良好的减振性,对机械振动起缓冲作用,从而阻止振动能量的传播;具有优良的耐磨性,缺口敏感性小,外来缺口对灰铸铁的疲劳强度影响甚微,从而增加了零件工作的可靠性。
因此被广泛地用来制作各种承受压力和要求消振性的床身、机架、结构复杂的箱体、壳体。
4110飞轮壳形状简单,结构比较复杂,属壳体类零件。
为实现飞轮壳连接、防护和载体的作用,其后端面内孔与飞轮盖的配合,因此加工精度要求较高。
飞轮壳在工作过程中需要有良好的耐磨性,为增强其切削加工性能,去除内应力,该工件要求经过退火处理,硬度范围175~225HBS [5]。
前端面的平面度0.12mm 直接影响飞轮壳与发动机箱体的接触精度及密封,且前端面中心线与后端面孔中心线的垂直度要求为0.15mm 。
后端面的平面度0.15mm 以及与前端面的平行度0.25mm 保证了其与其他零件和接触精度;与内孔的圆跳动0.25mm 则保证了飞轮在飞轮壳内的正常运转。
后端面孔097.00416+Φ要与其他零件配合,为了保证配合精度,相对与X 轴、Y 轴确定其位置度为0.3mm 。
分析该飞轮壳的技术要求,并将其全部技术要求列于表2.1中。
表2.1 飞轮壳零件技术要求表前端面定位孔2-064.0038.07.12++Φmm 在其后的精加工中将作为精基准,为保证位置的准确,其自身的位置度为0.1mm 。
前端面孔4-17Φmm 将直接影响飞轮壳与发动机箱体的装配,为保证装配精度,相对于X 轴、Y 轴确定其位置度为0.3mm 。
前端面马达螺孔2-M12-7H 影响飞轮壳与马达的装配,为保证装配精度,相对于马达孔中心线的位置度为0.4mm 。
综上所述,该飞轮壳的各项技术要求制订的合理,符合该零件在工作中的功用。
2.1.3 审查飞轮壳的工艺性分析零件图可知,飞轮壳前后两端面均要求切削加工,并在轴向方向上均高于相临表面,这样既减少了加工面积,又提高了工作时飞轮壳端面的接触刚度;前端面定位孔2-064.0038.07.12++Φmm 、孔4-17Φmm 的端面均为平面,可以防止加工过程中钻头钻偏,以保证孔的加工精度;另外,该零件除主要工作表面(飞轮壳前后两端面,后端面孔097.00416+Φmm 、前端面定位孔2-064.0038.07.12++Φmm 、马达孔087.0082+Φmm )外,其余表面加工精度均较低,不需要高精度机床加工,通过铣削、钻床的粗加工就可以达到加工要求;而主要工作表面虽然加工精度相对较高,但也可以在正常的生产条件下,采用较经济的方法保质保量地加工出来。
由此可见,该零件的工艺性较好。
2.2 飞轮壳毛坯及制造工艺2.2.1 选择毛坯由飞轮壳的技术要求分析可知,其材料为HT200,故毛坯选择铸件。
由于要求铸件精度高、具有良好表面质量与机械性能,所以选择砂型铸造中的金属模机器造型,其生产效率较高,适用于大批大量生产[6]。
2.2.2 分析毛坯制造工艺飞轮壳的材料HT200为珠光体灰口铁。
其特性是该材料能承受较大的应力(抗拉强度达200MN/2m ;抗弯强度达400MN/2m )。
其金相组织结构为铁素体和渗碳体组成的机械混合物,由于它是硬的渗碳体和软的铁素体相间组成的混合物,所以其机械性能介于铁素体和渗碳体之间,故强度较高,硬度适中,有一定的塑性,从金相组织显微来看,铸铁中化合碳正好等于0.77%,珠光体中的铁素体与渗碳体一层层交替间隔,呈片状排列,而其余的碳是以片状石墨状态存在,使切削过程中切屑不能连续成形。
由于灰铸铁属于脆性材料,故不能锻造和冲压。
灰铸铁的焊接性能很差,如焊接区容易出现白口组织,裂纹的倾向较大。
但灰铸铁的铸造性能和切削加工性能优良。
由于飞轮壳尺寸较大,形状较为复杂,毛坯宜用铸件。
此外,灰铸铁一般不需要热处理,但消除残余应力,铸造后应安排时效处理。
2.2.3 确定毛坯的尺寸公差和机械加工余量查加工工艺手册大批量生产的毛坯铸件的公差等级知:砂型铸造机器造型和壳型灰铸铁的公差等级CT 为8~12,故取CT 为10。
查加工工艺手册毛坯铸件典型的机械加工余量等级知:砂型铸造机器造型和壳型灰铸铁的要求的机械加工余量等级为E ~G ,故取为G 。
查加工工艺手册铸件尺寸公差和要求的铸件机械加工余量确定该铸件的尺寸公差和机械加工余量,所得结果列于表2.2中。
表2.2 飞轮壳铸造毛坯尺寸公差及机械加工余量2.3 加工的工艺规程2.3.1 定位基准的选择1.精基准的选择根据该飞轮壳零件的技术要求和装配要求,选择飞轮壳的前端面和前端面定位孔2-064.0038.07.12++Φmm 作为精基准,它们既是装配基准,有是设计基准,零件上很多表面都可以采用它们作为基准进行加工,使加工遵循“基准统一”原则,实现壳体零件“一面二孔”的典型定位方式。
前端面定位孔2-064.0038.07.12++Φmm 的轴线是设计基准,选用其作为精基准定位加工马达孔087.0082+Φmm 、前端面孔4-17Φmm 、前端面孔2-13Φmm ,实现了设计基准和工艺基准的重合,保证了被加工孔的位置度要求。