齿轮的表面粗糙度误差检测
滚齿机的加工工艺规程及其质量检测
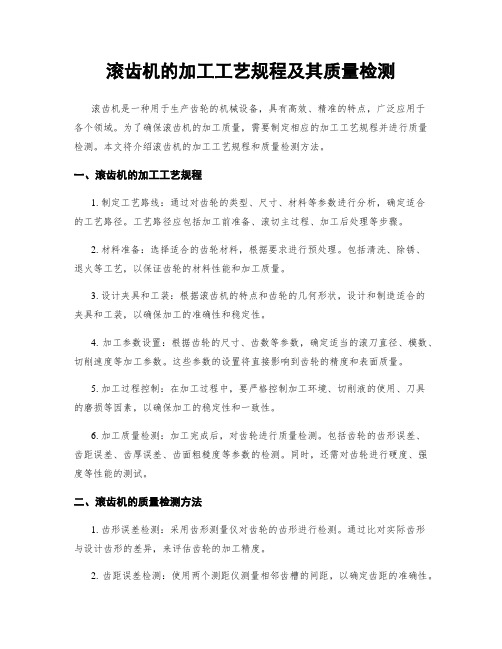
滚齿机的加工工艺规程及其质量检测滚齿机是一种用于生产齿轮的机械设备,具有高效、精准的特点,广泛应用于各个领域。
为了确保滚齿机的加工质量,需要制定相应的加工工艺规程并进行质量检测。
本文将介绍滚齿机的加工工艺规程和质量检测方法。
一、滚齿机的加工工艺规程1. 制定工艺路线:通过对齿轮的类型、尺寸、材料等参数进行分析,确定适合的工艺路径。
工艺路径应包括加工前准备、滚切主过程、加工后处理等步骤。
2. 材料准备:选择适合的齿轮材料,根据要求进行预处理。
包括清洗、除锈、退火等工艺,以保证齿轮的材料性能和加工质量。
3. 设计夹具和工装:根据滚齿机的特点和齿轮的几何形状,设计和制造适合的夹具和工装,以确保加工的准确性和稳定性。
4. 加工参数设置:根据齿轮的尺寸、齿数等参数,确定适当的滚刀直径、模数、切削速度等加工参数。
这些参数的设置将直接影响到齿轮的精度和表面质量。
5. 加工过程控制:在加工过程中,要严格控制加工环境、切削液的使用、刀具的磨损等因素,以确保加工的稳定性和一致性。
6. 加工质量检测:加工完成后,对齿轮进行质量检测。
包括齿轮的齿形误差、齿距误差、齿厚误差、齿面粗糙度等参数的检测。
同时,还需对齿轮进行硬度、强度等性能的测试。
二、滚齿机的质量检测方法1. 齿形误差检测:采用齿形测量仪对齿轮的齿形进行检测。
通过比对实际齿形与设计齿形的差异,来评估齿轮的加工精度。
2. 齿距误差检测:使用两个测距仪测量相邻齿槽的间距,以确定齿距的准确性。
3. 齿厚误差检测:使用专用测量仪器对齿轮齿面的厚度进行测量,确认其与设计要求的一致性。
4. 齿面粗糙度检测:使用表面粗糙度仪测量齿轮齿面的粗糙度,以评估齿轮表面质量。
5. 硬度测试:采用硬度测量仪对齿轮的硬度进行检测,以确保其达到要求的强度标准。
6. 强度测试:通过进行强度试验或者材料化学成分分析,来评估齿轮的强度性能。
通过以上的质量检测方法,可以全面评估滚齿机加工出的齿轮的质量。
第三章第齿轮副中心距极限偏差和轴线平行度公差节齿轮精度指标的公差及其精度等级

公称中心距 a=( d1+ d2)/2=(60.606+239.394)/2=150mm
齿轮圆周速度
v= d1n1=3.14×327×60.606/1000=62.23m/min=1.04m/s
参考表10-5所列通用减速器的齿轮和表10-6所列某些机器中的普通齿
轮所采用的精度等级,按本例齿轮圆周速度,综合考虑三项精度要求
式中
j b n m i n ( E s n s 1 E s n s 2 ) c o s n f 2 s i n n J b n
E s n s jb 2 n m c i o ns J n b nfta nn
团结 信赖 创造 挑战
§7 齿轮侧隙指标的公差和齿轮坯公差
3. 齿厚下偏差的确定
Esns2
jbnmin Jbn
2cos
fa
tan
429cos4230.7 31.5tan2061m
团结 信赖 创造 挑战
§7 齿轮侧隙指标的公差和齿轮坯公差
基准孔和齿顶圆柱面的尺寸公差按齿轮精度等级从附表 10-6选用。
基准端面对基准孔轴线的端面圆跳动公差tt由端面的直 径Dd、齿宽b和齿轮螺旋线总公差Fβ按下式确定:
tt 0.2(D d/b)F
切齿时,如果齿顶圆柱面用来在切齿机上将齿轮基准孔轴 线相对于工作台回转轴线找正;或以齿顶圆作为测量齿 厚的基准时,则需要规定齿顶圆柱面对齿轮基准孔轴线
团结 信赖 创造 挑战
§7 齿轮侧隙指标的公差和齿轮坯公差 四. 齿轮齿面和基准面的表面粗糙度轮廓要求
齿轮齿面、盘形齿轮基准面孔、齿轮轴轴颈、基准端面、 径向找正用的圆柱面、作为测量基准的齿顶圆柱面的表 面粗糙度轮廓幅度参数Ra上限值参见表10-7
第三章--表面粗糙度及检测
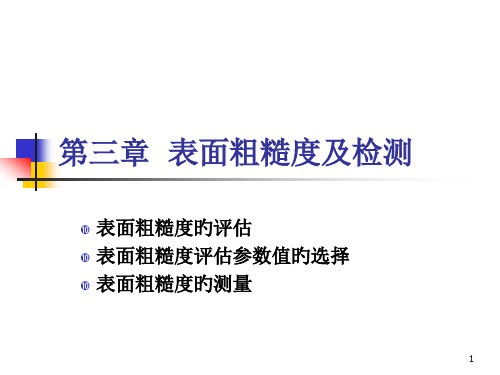
第二节 表面粗糙度评估参数值旳 选择
评估参数值旳选择
总原则:在满足功能要求旳前提下,尽量选择较大旳表 粗糙度参数值,以减小加工难度,降低成本。
选择措施:类比法。 一般原则: (1)同一零件上工作表面比非工作表面粗糙度参数值小。 (2)摩擦表面比非摩擦表面旳粗糙度参数值小,滚动摩擦 表面比滑动摩擦表面旳粗糙度参数值小。 (3)承受交变载荷旳表面及易引起应力集中旳部分(如圆 角,沟槽)粗糙度参数值应小些。
t
p
p
l
100%
1 l
n i 1
bi
100%
S、Sm和tp称为间距参数,值越小,轮廓表面越细密,密 封性愈好。
13
第一节 表面粗糙度旳评估
❖评估参数旳数值
原则要求:当Ra为0.025~6.3μm或Rz为0.100 ~25μm范围时,应优先 选用Ra参数。 Ra <0.025μm, Ra >6.3μm时,用光学仪器测量比较适 合,因而应选用Rz 。
个最大旳轮廓谷深平均值之和:
5
5
y pi yvi
Rz i1
i 1
5
Rz
(h2
h4
h10 ) (h1 5
h3
h9 )
Rz值越大,表面越粗糙。
10
第一节 表面粗糙度旳评估
(3)轮廓最大高度Ry 在取样长度内,轮廓峰顶线和轮廓谷底线之间旳距离。
Ra、Rz和Ry称为表面粗糙度旳高度参数。
11
要求:国标推荐, ln=5l;对均匀性好旳表面,可选ln<5l;对均匀 性较差旳表面,可选ln> 5l。
5
第一节 表面粗糙度旳评估
取样长度、评估长度和轮廓中线
6
Hale Waihona Puke 第一节 表面粗糙度旳评估(3)中线 中线是指用以评估表面粗糙度参数旳一条基准线。
齿轮表面粗糙度的确定
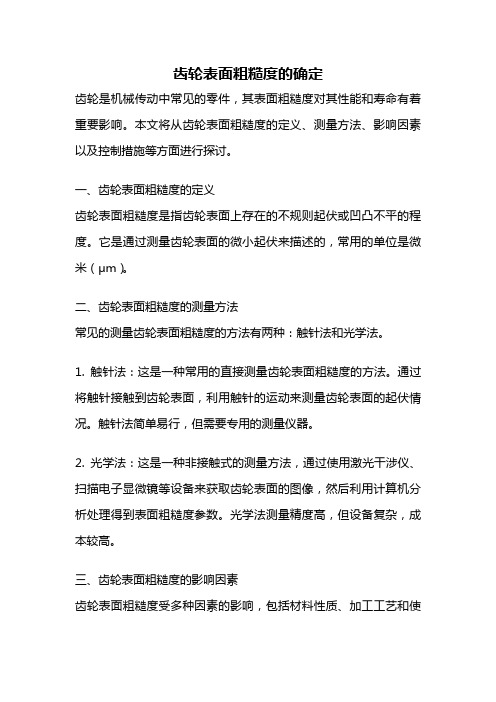
齿轮表面粗糙度的确定齿轮是机械传动中常见的零件,其表面粗糙度对其性能和寿命有着重要影响。
本文将从齿轮表面粗糙度的定义、测量方法、影响因素以及控制措施等方面进行探讨。
一、齿轮表面粗糙度的定义齿轮表面粗糙度是指齿轮表面上存在的不规则起伏或凹凸不平的程度。
它是通过测量齿轮表面的微小起伏来描述的,常用的单位是微米(μm)。
二、齿轮表面粗糙度的测量方法常见的测量齿轮表面粗糙度的方法有两种:触针法和光学法。
1. 触针法:这是一种常用的直接测量齿轮表面粗糙度的方法。
通过将触针接触到齿轮表面,利用触针的运动来测量齿轮表面的起伏情况。
触针法简单易行,但需要专用的测量仪器。
2. 光学法:这是一种非接触式的测量方法,通过使用激光干涉仪、扫描电子显微镜等设备来获取齿轮表面的图像,然后利用计算机分析处理得到表面粗糙度参数。
光学法测量精度高,但设备复杂,成本较高。
三、齿轮表面粗糙度的影响因素齿轮表面粗糙度受多种因素的影响,包括材料性质、加工工艺和使用条件等。
1. 材料性质:不同材料具有不同的表面硬度和塑性变形能力,这会直接影响齿轮表面的粗糙度。
一般来说,硬度较高的材料表面粗糙度较小。
2. 加工工艺:齿轮的加工工艺会对表面粗糙度产生重要影响。
加工精度、切削液的选择和刀具磨损等因素都会对表面粗糙度产生影响。
3. 使用条件:齿轮在使用过程中会受到载荷、转速和润滑等因素的影响,这些因素会对表面粗糙度产生一定的影响。
例如,高载荷和高转速会增加齿轮表面的磨损,导致表面粗糙度增加。
四、齿轮表面粗糙度的控制措施为了保证齿轮的性能和寿命,需要采取一些措施来控制齿轮表面粗糙度。
1. 合理的材料选择:选择硬度适中、塑性变形能力好的材料,可以减小表面粗糙度。
2. 优化的加工工艺:采用合适的切削参数、切削液和刀具,以及有效的冷却和润滑措施,可以降低表面粗糙度。
3. 表面处理技术:通过磨削、抛光、电化学抛光等表面处理技术,可以提高齿轮表面的光洁度,减小表面粗糙度。
齿轮、表面粗糙度测量实验报告心得

齿轮、表面粗糙度测量实验报告心得
本次实验是通过测量齿轮和表面粗糙度来学习测量方法和原理。
在实验中,我学到了许多关于测量仪器和工具的知识,如卡尺、游标卡尺、外径测量仪等。
同时,我还了解了齿轮和表面粗糙度的定义、测量方法和影响因素。
在进行实验的过程中,我对各种测量仪器的使用方法有了更深入的了解,尤其是在使用卡尺时需要注意测量时的垂直度和读取时的精度。
在测量齿轮和表面粗糙度时,我学到了如何选择合适的测量仪器,以及如何通过多次测量并取平均值来提高测量准确度。
此外,我还发现在实验中需注意实验环境的温度、湿度等因素对测量结果的影响,并要求自己在进行实验时保持冷静和耐心,以保证实验顺利进行。
总的来说,本次实验让我获得了实际操作的经验,并让我对测量方法和原理有了更深刻的认识,同时也提高了我的实验能力和创新能力。
齿轮的误差及其分析

齿轮误差及其分析第一节:渐开线圆柱齿轮精度和检测对于齿轮精度,主要建立了下列几个方面的评定指标:一.运动精度:评定齿轮的运动精度,可采用下列指标:1.切向综合总偏差F i′:定义:被测齿轮与理想精确的测量齿轮单面啮合时在被测齿轮一转,(实际转角与公称转角之差的总幅度值)被测齿轮的实际转角与理论转角的最大差值。
切向综合总偏差F i′。
(它反映了齿轮的几何偏心、运动偏心和基节偏差、齿形误差等综合结果。
)ΔF i2.齿距累积总偏差F p,齿距累积偏差F pk。
定义:齿轮同侧齿面任意弧段(k=1或k=z)的最大齿距累积偏差。
它表现为齿距累积偏差曲线的总幅值。
——齿距累积总偏差。
在分度圆上,k个齿距的实际弧长与公称弧长之差的最大绝对值,称k个齿距累积误差ΔF pk。
k为2到小于Z/2的正数。
这两个误差定义虽然都是在分度圆上,但实际测量可在齿高中部进行。
这项指标主要反映齿轮的几何偏心、运动偏心。
用ΔF p 评定不如ΔF i′全面。
因为ΔF i是在连续切向综合误差曲线上取得的,而ΔF p不是连续的,它是折线。
ΔF i′= ΔF p+ Δf f测量方法:一般用相对法,在齿轮测量机上测量。
3.齿圈径向跳动ΔF r与公法线长度变动ΔF w:ΔF r定义:在齿轮一转围,测头在齿槽,于齿高中部双面接触,测头相对于齿轮轴线的最大变动量。
它只反映齿轮的几何偏心,不能反映其运动偏心。
(用径跳仪测量检测。
)由于齿圈径跳ΔF r 只反映齿轮的几何偏心,不能反映其运动偏心。
因此要增加另一项指标。
公法线长度变动ΔF w。
ΔF w定义:在齿轮一周围,实际公法线长度最大值与最小值之差。
ΔF w=W max-W min测量公法线长度实际是测量基圆弧长,它反映齿轮的运动偏心。
测量方法:用公法线千分尺测量。
4.径向综合误差ΔF i″和公法线长度变动ΔF w:齿轮的几何偏心还可以用径向综合误差这一指标来评定。
ΔF i″定义:被测齿轮与理想精确的测量齿轮双面啮合时,在被测齿轮一转,双啮中心距的最大变动量。
齿轮滚刀使用及检验标准

齿轮滚刀(直槽)使用及检验标准一、齿轮滚刀使用标准 1、滚刀的轴向窜刀滚刀使用过程中,除进行正确的安装、调整外,还应进行轴向窜动,以延长滚刀的使用寿命。
1.1滚刀的起始安装位置如图1-1 滚刀切削区域向齿轮端面的投影图,滚刀实际切削区域长度=切出长度(l 0)+切入部分(l )。
图1-1滚刀切削区域向齿轮端面的投影图切出长度l 0=0*cos tan 0*cos ha βαδ式中0ha ——滚刀的齿顶高; β——被切齿轮的螺旋角; 0α——滚刀刀齿的齿形角; δ——滚刀的安装角。
切入长度l =(2*11)*1cos ra h h δ式中1ra ——被切齿轮齿顶圆半径; 1h ——滚齿时的切入深度; δ——滚刀的安装角。
安装滚刀的初始位置时,应使展成中心位于距切入端端面为l 的位置上,检验计算展成中心与切出端端面距离不小于l 0。
1.2 轴向窜刀的方向滚刀的轴向窜刀,通常应在与被加工齿轮旋转方向相反的方向上进行,如图1-2轴向窜刀的方向。
图1-2 轴向窜刀的方向1.3 轴向窜刀的窜刀量直槽滚刀的窜刀量S 可用下式确定: S=*d*cos dnm c Z πγ式中n ——滚刀头数; m ——滚刀模数;Zd——滚刀圆周齿数;γ——滚刀螺旋升角;dc——(确定窜刀量大小的系数,为4、5、6、7、8、9等整数值)。
推荐轴向窜刀的窜刀量S等于滚刀的轴向齿距Px。
1.4轴向窜刀的时机滚刀轴向窜刀的时机推荐为后刀面磨损约为磨钝标准的25%~30%时,即进行窜刀(单工步未加工完除外)。
在不同的切削条件下,滚刀窜刀量和窜刀时间间隔的最佳数值还要根据实际磨损情况,试验分析后确定。
1.5轴向窜刀的方法我车间滚齿机的轴向窜刀需靠手动完成,基本方法有两种,推荐方法为方法一。
方法一:按照确定窜刀量的各种倍数值,制作垫刀垫圈,通过变换滚刀心轴上垫圈的厚度,使滚刀沿其轴线移动,以改变滚刀对被加工齿轮轴线的位置。
方法二:切削一定数量的齿轮后,将分齿挂轮脱开,并转动滚刀,以达到轴向窜刀的目的。
齿轮测量的方法
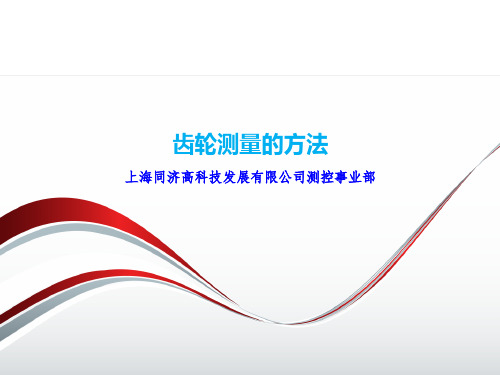
上海同济的基础是齿轮精度理论。齿轮测量技术的发展历程是以齿轮精度理 论的发展为前提的。齿轮精度理论的发展实质上反映了人们对齿轮误差认识的深 化。迄今,齿轮精度理论经历了齿轮误差几何学理论、齿轮误差运动学理论和齿 轮误差动力学理论的发展过程。
谢谢观赏
专业生产销售 有需求请联系 本人账号头像上有联系方式
1、几何长度测量法; 2、轮廓测量法; 3、粗糙度测量法; 4、传动噪音测量法; 5、齿轮整体误差测量法;
齿轮测量方法
齿轮几何长度的测量主要有以下几个项目: 公法线、齿厚、跨棒距(M值)、顶圆直径、齿轮中心距、齿圈径向 跳动等等。
测量齿轮几何量可以用通用测量工具如公法线千分尺、万能齿轮 测量仪等进行测量,也可以用带表装置进行测量。对于高精度、大批 量精密齿轮的测量可以定做专用检具进行测量,例如气动综合测量仪、 电感综合测微仪等。
齿轮测量方法
齿轮是回转零件,其结构特点是直径一般大 于长度,通常由外圆柱面(圆锥面)、内孔、键 槽(花键槽)、轮齿、齿槽及阶梯端面等组成。 测量齿轮要达到传递运动准确性、传动平稳 性、载荷分布均匀等要求。 齿轮制造的误差可能来自于机床制造误差、 刀具误差、齿坯制造误差、安装误差等。
齿轮测量方法
根据齿轮误差来源的几个方面,齿轮测量方法 归结为以下几点:
- 1、下载文档前请自行甄别文档内容的完整性,平台不提供额外的编辑、内容补充、找答案等附加服务。
- 2、"仅部分预览"的文档,不可在线预览部分如存在完整性等问题,可反馈申请退款(可完整预览的文档不适用该条件!)。
- 3、如文档侵犯您的权益,请联系客服反馈,我们会尽快为您处理(人工客服工作时间:9:00-18:30)。
河南工学院2016―2017学年第一学期《机械产品检测与质量控制(2)》大作业
题目:齿轮的表面粗糙度误差检测
班级:
姓名:
学号:
日期:
摘要
在加工制造过程中,由于机床本身误差、刀具安装误差等因素的存在,使齿轮各部分几何尺寸不能完全达到设计标准的要求,影响到其制造精度。
为确保传动齿轮在额定功率下能减小齿轮传动的噪声、冲击、振动等不利因素影响,保证齿轮传动有较高的工作平稳性,使齿轮传动的瞬时速比变化尽可能小,就必须对齿轮的齿面粗糙度制造质量加以严格控制。
齿面粗糙度的大小对齿轮副的磨损、强度、能耗、寿命、锈蚀、稳定性都有直接的影响。
关键词:齿轮、表面粗糙度、检测、齿面
国家对齿轮表面质量的评定规定
齿轮轮齿表面的加工方法很多,不同的加工方法能形成多种加工纹理。
齿面的形状较复杂,加工纹理的多样性和表面形状的复杂性给齿面粗糙度的测量带来了很多困难。
根据我国现行的表面粗糙度评定的国家标准GB/T3505—2000《表面粗糙度
术语及其参数》规定:测量和评定表面粗糙度轮廓中的实际轮廓是指理想平面与实际表面相交所得的轮廓线为实际轮廓。
按相截方向可分为横向和纵向实际轮廓。
取样长度是指测量或评定表面粗糙度时所规定的一段基准线长度;评定长度是指在评定轮廓表面粗糙度所必须的一段长度,即评定表面粗糙度参数值的一段长度,包括一个或几个取样长度;轮廓中线是评定表面粗糙度参数值大小的一条参考线,包括轮廓的最小二乘中线和轮廓的算术平均中线。
齿面粗糙度评定存在的问题
齿轮的加工方法很多,不同加工方法形成了轮齿表面不同种类的加工纹理。
加工纹理的多样性和表面形状的复杂性,给齿面质量的控制带来了很多困难。
齿轮表面质量按表现形式和影响产品质量的不同,可分为微观形状误差(粗糙度)、中间形状误差(波纹度)和宏观形状误差。
不同的齿轮工艺方法,形成了齿面微观复杂的形貌特征,给齿面粗糙度的评
判带来了困难。
究其原因:一方面是齿面精加工技术应用还不普遍;另一方面是人们对齿轮齿面粗糙度评定不统一、分析见仁见智,对国家标准的理解也很不一致,从而造成对齿轮齿面粗糙度等级判别与实际有偏差。
齿轮加工业乃至与齿轮行业有关的其他行业普遍反映齿轮轮齿表面粗糙度
的评定方法不合理,主要表现在没有从齿轮零件的功能出发选择合适的评定参数,而且评定方法也不规范,各单位各行其事,致使齿面粗糙度评定结果能相差1~2
级甚至更多,给齿轮轮齿表面粗糙度质量评定和齿轮行业间的仲裁带来困难。
主要有以下几方面的问题:①评定参数和参数定义不统一;②选取测量部位数量和
方法不统一,影响测量结果的最后评定;③轮齿表面缺陷与齿面粗糙度的区分界
定不统一;④测量方向的问题。
由于以上种种原因,表面粗糙度的评定一直存在着严重问题,这些问题也成为了许多厂家关于表面粗糙度方面沟通的绊脚石。
齿轮表面粗糙度误差检测方法
齿轮表面粗糙度的测量方法有:比较法、光切法、针描法、印模法等等。
在一些检测中,测量部位随机选取几个均匀分布的部位比较合适;至于表面加工纹理分布的不均匀可以用增加测量部位的办法来解决。
1.目视检查法:指操作者或检验人员根据加工纹理和加工表面特征,通过视觉经验,结合手感(用指甲轻划或手摸)或其他方法进行比较,对被测表面的粗糙度进行评定的方法。
具体特征见下表:
此方法使用器具简单,操作方便,是目前生产现场最常用的方法。
但此方法并不科学,检测准确度完全依赖操作者的经验和水平。
2.比较法:指操作者将表面粗糙度比较样块与被测工件表面靠在一起,用目测或借助放大镜、比较显微镜等直接进行比较,或用手感(摸,指甲划动的感觉)来判断表面粗糙度。
还可以用油滴在被测表面和表面粗糙度标准样块上,用油的流动速度(此时要求样块与工作倾斜角度与温度相同)来判断表面粗糙度,流动速度快的表面粗糙度数值小,此方法测量不够精确。
3.光切法:指利用“光切原理”来测量表面粗糙度的一种法。
光切法检测使用的仪器叫光切显微镜,一般适用于测量用车、铣、刨等加工方法完成的金属平面或外圆表面。
光切法主要用于测量表面粗糙度的Rz参数,Rz测量范围为0.5-60um。
4.针描法:这是一种接触式测量,又称感触法即利用金刚石触针在被测表面滑行而测出表面粗糙度Ra值的一种方法。
目前针描法较常用的仪器是电动轮廓仪,可直接显示Ra值,其测量范围Ra 为0.025-6.3um。
电动轮廓仪的原理是利用触针在被测表面划动,使触针上下移动,引起传感器内电量变化,将电量变化值经微机处理后可直接读出Ra参数值。
该仪器还可以通过记录器获得轮廓放大图,从而可测Ry值。
5.印模法:是一种非接触式间接测量表面粗糙度的方法,适用于大型笨重零件和难以用仪器直接测量或样板比较的表面的粗糙度测量。
印模法的原理是利用某些塑性材料做成块状印膜贴在零件表面上,从而将零件表面轮廓印制在印模上,然后对印模进行测量,得出粗糙度参数值。
印模法由于印模材料不能完全充满被测表面微小不平度的谷底,所以测得印模表面粗糙度参数值比实际参数值小。
因此,对印模所得出的表面粗糙度测量结果需要进行修正(修正时也只能凭经验)。
除了上述的几种方法外,还有干涉法和激光测微仪检测法,这些方法都能对齿轮表面粗糙度进行测量,不过各种方法所测精度不同,所测范围也不同,故而需要根据实际情况,选用合适的方法进行测量。
心得感受
总之,齿面粗糙度对齿轮副的磨损、强度、使用寿命、抗锈蚀性、稳定性都有极大的影响。
而影响齿轮齿面粗糙度的评定因素有:①评定参数和参数定义不统一;②选取测量部位数量和方法不统一;③轮齿表面缺陷与表面粗糙度的区分界定不统一;④加工纹理方向和测量方向的问题。
在实际齿轮齿面粗糙度的测量中,可以结合以上的分析与判定,找出齿面粗糙度测量产生偏差的原因,并换用不同方法进行检测改善,以提高齿轮齿面的质量。
不过齿轮表面质量包含齿轮齿面形状误差、轮齿表面波纹度和齿面的粗糙度,严格意义上来说,评定齿面粗糙度很难从以上两种误差中区分开,评定齿面质量时要综合考虑,找出其中影响大的误差,加以改进。
参考文献
{1}王茂元--机械制造技术--北京:机械工业出版社
{2}梁子午--检验工实用技术手册--南京:江苏科学技术出版社{3}徐鸿本--实用五金大全--武汉:湖北科学技术出版社
{4}机械加工质量检验技能培训手册(内部资料)。