板材轧制过程中快速有限元在线算法
SSP定宽机轧制过程的有限元分析5001

SSP定宽机轧制过程的有限元分析李晓娜 1(1.一重集团大连设计研究有限公司工程师,辽宁 大连 116600)摘要:近年来,连铸连轧技术发展迅速,必须采用适当的板坯宽度调整技术来实现连铸和热轧之间宽度上的连接。
定宽机对减少连铸生产的板坯宽度规格、扩大热轧生产规模起到了良好作用。
本文用有限元分析软件ANSYS对SSP定宽机轧制过程进行模拟,分析锤头模块角度,板坯材质,初始宽度对轧制力的影响,以及板材截面的狗骨高度。
关键词:定宽机;有限元分析;轧制力;模块角度;狗骨高度随着连铸和热连轧技术的不断发展和市场竞争,连铸板坯宽度调整技术得到了广泛的应用,调宽技术作为连铸和连轧的中间环节,在整个轧制生产线上起着重要的作用,从某种意义上可以说:调宽技术是钢板轧制生产线的咽喉。
常用的两种调宽技术是立辊轧制调宽和调宽压力机大侧压调宽技术。
其中调宽压力机的开发和应用大大提高了调宽效率,降低了板坯头尾的切损。
调宽压力机调宽变形改变了以往板坯立辊轧制调宽的连续变形的状态,使板坯变形间断进行,因而定宽机以其调宽范围大,侧压速度快,侧压后板坯形状好,切损量少等优点,广泛应用在很多热连轧生产线上,布置在加热炉和可逆粗轧机之间。
本文以某2250mm热轧线SSP定宽机的锤头模块模拟轧制板坯过程,用有限元软件对轧件进行受力分析,分析模块角度,板坯材质和初始宽度对轧制力的影响,以及板材截面的狗骨高度。
1 SSP定宽机的主要原理1.1 SSP定宽机的主要参数SSP定宽机的结构包含侧压机构、同步机构和调宽机构三个主要部分。
整个侧压部分可以分为侧压框架和同步框架,同步框架挂在机架上,它只有平行于轧线方向的同步动作;侧压框架完成主偏心轴的侧压动作,还随同步框架随轧制线方向运动。
侧压模块的动作是两个框架运动的复合,侧压机构和同步机构的结构简图(见图1)。
SSP主要技术参数如下:来料温度:1150~1250 ℃最大压下量: 350 mm最大减宽压力: 22000 kN最大减宽扭矩:2×1530 kN·m压头工作频率:42次/min板坯递进最大长度: 428 mm板坯递进最大速度: 0.5 m/s板坯平均运行速度: 0.3 m/s模块开口度: 1000-2050mm主传动电机:AC 4400 kW 0~607 rpm 1台开口度调整形式: 电动预摆最大开口度: 2050 mm最小开口度: 1000 mm检修开口度: 2800 mm开口度调整速度: 43 mm/s (单侧)开口度调整电机:440 kW 0~950 rpm 2台图1. SSP机构组成1.2 SSP定宽机的侧压原理模块对板坯的侧压是斜面过渡性轧制,第一次拍击是斜面拍击,从第二次拍击开始,平面参与拍击,起修复板坯变形的作用。
板材冲压成形过程有限元网格优化算法

Science and Technology &Innovation ┃科技与创新2020年第06期·41·文章编号:2095-6835(2020)06-0041-02板材冲压成形过程有限元网格优化算法*高孝书1,王旭东2(1.宁夏职业技术学院(宁夏广播电视大学),宁夏银川750021;2.宁夏镁业有限公司,宁夏银川750021)摘要:板材冲压成形是一个复杂的大变形过程,包含几何非线性、材料非线性、接触非线性等强非线性问题。
因板材局部大变形导致有限元网格形状的畸变,会严重降低有限元网格质量,甚至造成模拟计算失败。
针对此问题,提出了一种有限元网格优化算法,通过消除碎小单元网格和优化网格形态的方法,赋予网格节点结构关联权重,量化网格节点加叠值,在保留板材变形模型特征及精度的同时,优化了板材冲压成形的有限元网格,以实例模型验证了算法的有效性。
关键词:板材冲压;结构关联权重;加叠值;有限元网格中图分类号:TG386文献标识码:ADOI :10.15913/ki.kjycx.2020.06.013在板材冲压成形有限元模拟过程中,由于冲压模具几何结构的复杂性,板材随冲压进程产生局部非线性大变形,使得有限元网格划分[1]时生成大量碎小或狭长的劣质单元。
这些劣质单元将造成后期有限元分析结果的不稳定或迭代计算不收敛[2],因此有限元网格的形态优化是决定模拟计算成败的关键。
有限元网格优化算法是在保持板材变形模型特征及精度的前提下,赋予有限元网格节点结构关联权重,建立网格节点结构关联权重计算规则和网格节点加叠规则,量化网格节点加叠值,通过定向移动和合并网格节点实现网格节点的加叠,消除碎小或狭长的劣质单元,达到优化网格形态、提高网格质量的目的。
1加叠算法目前国内外主要的网格简化算法有加叠简化算法[3]、顶点聚类简化算法[4]、区域合并简化算法等。
加叠算法是选取三角网格中小于临界点距的2个点(u 和v ),将其中一个点v 加叠映射至点u ,然后修改拓扑关系,删除多余的边和面,完成简化操作。
有限元法在板材热轧中的应用

有限元法在板材热轧中的应用
张德丰;陆建生;宋鹏;周洁
【期刊名称】《南方金属》
【年(卷),期】2006(000)001
【摘要】采用弹塑性大变形热力耦合有限元法研究板材热轧过程.利用有限元理论建立了板材热轧模型;应用MSC/MARC软件进行计算,重点分析了轧制过程和变形区中轧件的温度场分布和变化、金属的流动、应力应变的变化趋势,以及轧制力的变化情况.计算结果与实际生产情况相吻合,同时表明有限元理论可以实现对板材热轧过程的数值模拟.
【总页数】4页(P18-20,43)
【作者】张德丰;陆建生;宋鹏;周洁
【作者单位】昆明理工大学,云南,昆明,650093;昆明理工大学,云南,昆明,650093;昆明理工大学,云南,昆明,650093;昆明理工大学,云南,昆明,650093
【正文语种】中文
【中图分类】TG335.5
【相关文献】
1.有限元法在热轧辊三维温度场研究中的应用 [J], 陈国樑
2.有限元法在热轧机工作辊轴承座热特性分析中的应用 [J], 张思成;王建梅;徐春园
3.有限元法在板材热轧中的应用 [J], 徐颖彬;于慧林;程军风
4.有限元法在热轧辊三维温度场分析中的应用 [J], 陈国樑
5.有限元法在板材成形分析中的应用进展 [J], 张士宏;王仲仁
因版权原因,仅展示原文概要,查看原文内容请购买。
有限元法在板材热轧中的应用
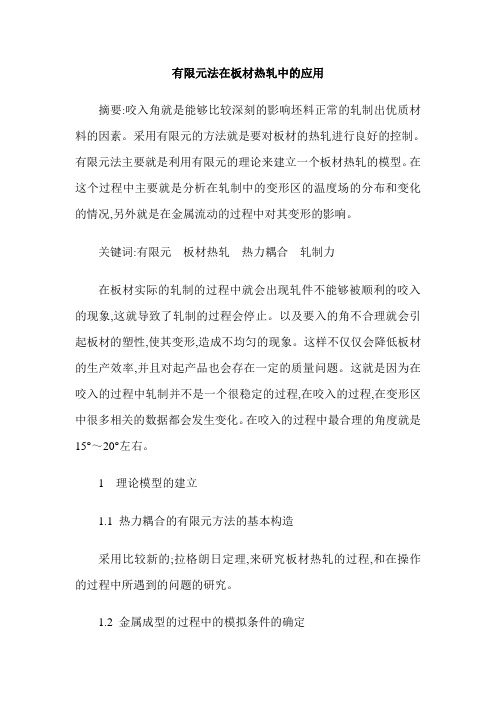
有限元法在板材热轧中的应用摘要:咬入角就是能够比较深刻的影响坯料正常的轧制出优质材料的因素。
采用有限元的方法就是要对板材的热轧进行良好的控制。
有限元法主要就是利用有限元的理论来建立一个板材热轧的模型。
在这个过程中主要就是分析在轧制中的变形区的温度场的分布和变化的情况,另外就是在金属流动的过程中对其变形的影响。
关键词:有限元板材热轧热力耦合轧制力在板材实际的轧制的过程中就会出现轧件不能够被顺利的咬入的现象,这就导致了轧制的过程会停止。
以及要入的角不合理就会引起板材的塑性,使其变形,造成不均匀的现象。
这样不仅仅会降低板材的生产效率,并且对起产品也会存在一定的质量问题。
这就是因为在咬入的过程中轧制并不是一个很稳定的过程,在咬入的过程,在变形区中很多相关的数据都会发生变化。
在咬入的过程中最合理的角度就是15°~20°左右。
1 理论模型的建立1.1 热力耦合的有限元方法的基本构造采用比较新的;拉格朗日定理,来研究板材热轧的过程,和在操作的过程中所遇到的问题的研究。
1.2 金属成型的过程中的模拟条件的确定1.2.1 轧制的参数在设计中需要按照设计所需要的数据来进行轧制参数的设计。
然后来选取研究的对象。
1.2.2 边界条件和材料的相关的参数轧件在变形的时候温度主要就是需要收到接触的热来传导的,与环境之间的热对流和辐射还有外界冷却水的降温,还有轧件塑性变形等等影响,接触热传导的一般都是会影响到轧件的表面层的温度分布的。
在一般的操作施工中,稳定的轧制时的温度大约是150左右,在轧件之间的接触热传递的系数的影响关系是比较小的,其等效热交换系数取0.015kW/m2k,20℃冷却水与轧件间的热传导系数取0.6W/mk,塑性变形热、摩擦生热结合考虑其有效转化系数取0.9。
1.2.3 初始的条件板材在开轧之后的温度大约是1000℃左右,平时的环境温度大约是20℃左右。
1.3 材料设备的计算模拟的坯料的钢种主要就是需要采用双线性的材料模型来进行操作。
板带轧制过程刚塑性有限元求解的初速度场设定

200812JOURNAL OF JIANGSU TEACHERS UNIVERSITY OF TECHNOLOGY(Natura l S cience Edition)Dec.,2008板带轧制过程刚塑性有限元求解的初速度场设定陈伟1,梅瑞斌2, 李长生2, 刘相华2(1.江苏技术师范学院学生工作处,江苏常州213001;2.东北大学轧制技术及连轧自动化国家重点实验室,辽宁沈阳110004)摘要:在保证计算精度的情况下,以减少迭代步数和提高计算效率为目标,提出基于工程法和细分单元法设定初始速度场。
依据某钢厂轧制过程数据,通过自行开发的刚塑性有限元程序模拟板带轧制过程。
结果表明:轧制力计算值和实测值吻合良好,计算误差控制在5%之内;和工程法相比该方法设定的初始速度场更加接近真实速度场,明显减少了迭代求解步数,提高了求解稳定性,迭代步数基本控制在30 次以内,单道次计算时间少于150 m s。
研究结果可为板带轧制过程刚塑性有限元法快速求解提供一定的理论指导。
关键词:刚塑性有限元;板带轧制;工程法;初始速度场;迭代步数中图分类号:TG335.5;TP391.9文献标识码:A文章编号:1674- 2222(2008)04- 0006- 07引言刚塑性有限元法能够有效求解各种金属大变形问题,如:轧制、挤压、锻造、拉拔和板料成型等[1]。
随着轧制技术和计算机技术的发展,刚塑性有限元法越来越广泛应用于轧制过程速度场、温度场和应力场求解,宽展、前滑和裂纹分析以及提高板形控制精度等方面。
刘相华等[2- 7]研究了刚塑性有限元变分原理和泛函极值唯一性并求解了平板轧制、型钢轧制、板坯立轧和纵筋板轧制等轧制过程。
熊尚武等[8]通过划分薄层单元法有效解决了第一类奇异点问题,提高了收敛速度和计算精度。
姜正义等[9- 10]利用三维刚塑性有限元研究了摩擦模型对平板轧制过程的影响规律。
对板材轧制来说,轧制参数在线设定模型直接影响轧制效率、板形控制精度和板带质量。
板材多道次热轧的有限元连续模拟

板材多道次热轧的有限元连续模拟张金玲;崔振山【摘要】为充分考虑各因素对板形的影响,建立了三维弹性等效空心辊模型,开发了有限元数据的参数化生成模块;自主编制了网格重划分及参数传递模块,并与有限元软件MARC相结合,显著节约了建模及计算时间,使多道次连续模拟成为可能;成功解决了计算过程中网格畸变带来的计算困难并实现了前后道次之间参数的连续性,最终实现了中厚板多道次热轧过程的连续模拟;模拟成功施加了弯辊力、轧辊初始凸度及热膨胀系数,充分考虑到对板形产生影响的各因素,以实际轧制规程为参考,进行了七道次热轧过程的连续模拟;轧制力、温度以及轧件的变形特征与实际吻合较好%To fully consider the infect of all the factors on plate shape,a 3-D elastic 'hollow-roll' model and the parametric generation module of FEM model is establelished,which makes it possible to simulate a multi-pass rolling process continuously.An input data generating system is also set up which involves a mesh refinement module and parameter transfer module.Through this system,the calculation results from the former pass can be directly transferred to the next pass input file as initial conditions and the refined mesh can be directly added into the input file too.This enables the simulation for multi-pass rolling going continuously.The model considers the factors influencing plate profile,such as roll-bending force,initial crown,thermal crown and heat transfer during rolling and inter-pass cooling.A seven-pass industrial hot rolling process was continuously simulated and the results show that the rollingforce,temperature and plate profile agree well with the measured ones respectively.【期刊名称】《材料科学与工艺》【年(卷),期】2011(019)003【总页数】6页(P76-81)【关键词】多道次;连续模拟;等效空心辊;网格重划分;参数传递【作者】张金玲;崔振山【作者单位】上海交通大学模具CAD国家工程研究中心,上海200030;上海交通大学模具CAD国家工程研究中心,上海200030【正文语种】中文【中图分类】TG335.5良好的板形是衡量中厚板产品质量的一个重要标准,决定了产品的市场竞争力[1-2].而板形问题的影响因素复杂,导致其现有离线模拟水平有限,不能满足实际生产的需要[3-5].采用有限元方法对轧制力[6-7]、轧制温度[8-9]及微观组织[10-11]进行分析的工作常见于文献.而板形同时受到轧辊弹性压扁、弹性弯曲、轧辊初始凸度以及热变形等因素的共同作用,应用有限元法模拟轧制过程的板形问题时,必须要考虑以上变形,因此轧辊模型必须是可变形体.这将导致模拟过程的计算量急剧增加,给应用带来相当大的困难.另外,多道次热轧过程中,温度变化是连续的,所以要求数值模拟过程应该是连续的.在多道次轧制中经过多次重划分网格,将带来新旧网格间单元信息和节点信息的多次交换问题,若这些交换是人工完成的,则无法实现多道次过程的连续计算.由于上述困难的存在,目前对中厚板轧制主要仍停留在单道次变形研究的水平,只有极少数涉及了多道次轧制过程[12-13].而且现有的研究工作中轧辊多采用刚性体,未考虑其弹性变形[14-15].这种方法不能反映轧辊变形对轧件变形的影响,因而不适用于板形研究.基于以上考虑,文中以等效空心弹性轧辊替代实际的实心轧辊,充分反映轧辊弹性变形及初始辊形等对轧件变形的影响,并且在保证计算精度的前提下,显著节省计算时间;模型参数化生成模块的建立,实现了脱离有限元软件前处理界面的建模方式,避免了具有相同几何特征模型的重复建模过程,明显节约建模时间;另外,开发了网格重划分模块和参数传递模块,构建了基于样板的有限元输入数据生成系统,使多道次热轧过程的连续模拟可在无人工干预的条件下完成.在保证轧辊可变形特性的同时,为了尽可能减少单元数目,建立了等效空心轧辊模型来替代实际实心辊.为保证轧辊简化不会影响轧件变形,要满足2个条件:施加弯辊力时弯曲挠度等效;与轧件接触时轧辊的压扁变形等效,因此,等效空心辊模型由2层构成,如图1所示.其外层单元与实际轧辊弹性模量保持一致,以保证轧辊弹性压扁变形的等效性;内层单元取一相对较大的弹性模量,以保证轧辊弹性弯曲变形的等效.根据材料力学梁的弯曲挠度理论有式中:w为挠度;M(x)为对应坐标x处的弯矩;E为弹性模量;I为截面惯性矩.可见,当辊身长度和受力条件(包括约束条件)一定时,轧辊的挠度与抗弯截面模量EI成反比,因此,若轧辊简化前后抗弯截面模量相等,则弯曲变形必等效.对于实心轧辊:其中Is为实心辊截面惯性矩,D为轧辊直径.对于空心轧辊外层:其中I1为空心辊外层截面惯性矩,D1空心辊外层直径.对于空心轧辊内层:其中I2为空心辊内层截面惯性矩,d为空心辊内层直径.为使抗弯截面模量相等,应使得其中E为真实轧辊材料的弹性模量,Ek是空心内层单元的等效弹性模量.由此得到在相同轧制条件下,分别采用实心轧辊和等效空心轧辊进行模拟,得到实心辊与等效空心辊的挠度结果如图2所示.两者的挠度值非常接近,说明空心辊模型满足挠度等效要求.图3为等效空心辊与实心辊进行模拟时轧辊与轧件接触区域应力状态比较.从图3可以看出两者引起的接触区应力状态几乎没有差别,说明2种情况空心辊都满足压扁变形等效要求.由图2和3给出的结果比较可以看出,等效空心辊完全满足等效要求,可以替代实心辊模拟进行板形研究.采用2种模型分别对同一单道次轧制规程进行模拟,其单元数目及计算效率对比见表1,可以看出等效空心辊模型单元数目明显减少,计算效率显著提高.等效空心辊 4320 16628 90029.16 s(25 h)由于实际模型具有对称性,模拟取其1/4建模.而且中厚板多道次热轧过程中各道次模型几何特征相同,只有几何尺寸不同.针对这一特点,开发了模型参数化生成模块来代替借助有限元软件前处理模块建模的方式,显著节约建模时间.用户只需在输入文件中输入轧辊直径、初始凸度值、辊身长度等几何参数,运行系统会自动生成有限元模型.以等效空心辊模型为例,轧辊具有轴对称性,所以首先建立其子午面上的二维有限元模型,如图4所示.轧辊轮廓建立为抛物线型以描绘其初始凸度特征.然后将二维模型绕其对称轴旋转,进而得到三维有限元模型.模型沿轴线方向被分为5份,每份具有不同的网格密度.为了便于模拟轧件边部减薄现象,轧辊与轧件边部的接触区域网格划分较密.图4中NW1、NELR等标注为每部分的网格划分数目.轧辊凸度方程为式中:x和Y为二维轧辊表面轮廓上任意点的坐标;A、B、C为抛物线方程的待定系数.鉴于轧辊模型沿轴向的对称性特点,可知B=0.由边界条件:可知式中:R为辊身段轧辊半径最小值;δ为设定的轧辊原始凸度;l为模型中辊身长度,即实际辊身长度的一半.所以轧辊凸度曲线为轧件的生成遵循相同原则.另外,由于轧件与轧辊的形状规整,整个模型采取八节点六面体单元进行离散.热轧中厚板过程为复杂的热力耦合过程.MARC采用弱耦合形式,同时处理热传导和力平衡2类不同场方程.在辐射和对流边界上,表面换热系数h为温度的函数[8],即式中:hc为对流换热系数,取52 W/(m2·K);hr为辐射换热系数;δ为波耳兹曼常数;η为黑体辐射系数,取0.9;Ti为轧件表面温度;Tamb为环境温度.根据各道次轧制情况不同,轧辊与轧件之间的摩擦系数依次取0.30、0.29、0.28、0.25、0.25、0.25和0.23;在轧制变形区内,接触换热系数受接触体表面粗糙度和接触压力等影响,在模拟中依次取20、20、20、20、25、25和25kW/(m2·K).变形功及摩擦功的功热转换系数分别取0.90和0.85[9-10].模拟中轧辊为可变形体,其转动必须通过刚体带动实现.如图5所示,在轧辊有限元模型的端面处生成一个相同大小的刚性圆盘,并将刚性圆盘与弹性辊端面“粘接”在一起.为刚性面设置了2个控制节点,使其与刚性面具有相同自由度.转动载荷与弯辊力分别施加在控制节点2与节点1上,所以轧辊的转动与弯曲得以同时实现.材料的高温流动应力实际上是应变、应变速率、温度的函数:根据实际轧制过程应变速率及温度的变化范围,采用Gleeble1500热模拟试验机对轧件材料进行了单向压缩试验,获得其真应力-应变关系.实验温度点分别取为800、900、1000及1100℃;根据轧制过程瞬时变形速度,应变速率实验点取为5、10、20及30 s-1.根据实验获得的应力-应变数据,在MARC材料库中新建相应实际材料的材料属性文件,以供求解时调用.多道次轧制后,材料的流动将导致轧件网格发生严重畸变从而造成精度下降,甚至不能收敛.此时需要进行网格重划分,由于现有有限元软件本身不具备成熟的六面体网格重划分功能,本文在MARC运行环境外部开发了1套适合于中厚板轧制模拟的六面体网格重划分方法.在中厚板轧制过程中,轧件主要发生压下及延伸变形,所以可以依据单元内角和边长比来判断网格是否需要重划分.当单元内角在可用范围内但边长比不满足要求时,需要在轧制方向对网格进行加密,此时新增节点的坐标通过插值得到式中:NZ为沿轧制方向相邻两排对应节点的编号差;X为旧节点坐标;x为新节点坐标.当单元内角不满足要求时,则需要在轧件所在的空间内重新计算各节点的坐标:式中:N0为轧制方向上各排节点的初始编号;j =1,…,NZ-1.图6为网格重划分前后单元质量对比,可见其单元边长比及内角获得了明显改善.为了保证求解的连续性,下一道次模型还要继承上一道次的其他特征参数,如温度.首先要通过调用MARC的后处理子程序将节点温度输出到过度文件中,在下一道次模型生成时将其作为初始条件施加在相应节点上;如果需要进行网格重划分,则通过插值程序获得新节点的温度值,以初始条件的形式带入新生成模型.以上所有过程都通过批处理文件在后台运行无需借助软件的前处理模块.为验证模拟方法的可靠性,以某厂七道次中厚板热轧规程为例进行模拟.轧制规程见表2.轧件原始宽度和厚度分别为 1509、48.69 mm,第1道次接触弧长最长为89.93 mm,为了既保证计算的准确性又节约计算时间,取轧件的模型长度为900mm.模型中轧件沿z轴负方向前进.轧辊辊身长1 880 mm,具有0.1 mm的正凸度特征.模拟中各道次摩擦系数分别为:0.3、0.29、0.28、0.25、0.25、0.25、0.23.图7给出道次1、3、5的轧制力及摩擦力沿接触弧长的线分布密度.从轧制方向摩擦力变化可以看到在后滑区摩擦力与轧件前进方向一致,为轧件前进的动力;在前滑区,由于金属流动,轧件的前进速度大于轧辊线速度,导致摩擦力方向突变,开始阻碍轧件前进,符合实际变化规律.随着压下量的增大轧制压力逐渐增大,由于模拟中流动应力取值并非常数,所以轧制力的最大值不是出现在中性面处,而是在中性面两侧出现2个峰值点,与传统轧制理论中的单峰值规律有所不同.表3给出轧制力模拟值与实测值的对比.可以看出,轧制力模拟结果与实测值吻合较好,最大偏差-7.18%出现在第7道次.图8给出模拟获得的轧件心部及表面温度变化及与实测表面温度的对比.在辊缝内,轧辊的急冷作用导致轧件表面温度迅速下降,而塑性功转化的热量导致心部温度稍有上升;轧件出辊缝后,由于厚度方向的温度差,心部热量被迅速传至表面,导致表面温度回升而心部温度下降.从表面温度模拟值与实测值比较可以看到两者吻合较好.下面主要从板凸度、板形、及边部断面特征几个方面对轧件横向形状进行分析.3.3.1 头部变形特征图9为经过3道次轧制后轧件头部单元形状与原始形状的对比.可见,因轧制过程的表面摩擦而导致头部侧面节点发生了上翻现象,在实际生产中可以通过减小摩擦来缓解头部上翻的畸变.在模型中,角部单元已不再是六面体单元,因此,为了保证其后道次的模拟精度,单元的重划分很必要.3.3.2 凸度曲线轧件凸度主要以厚度沿宽度方向的分布来体现.图10给出道次1、6、7轧后轧件厚度沿宽度方向分布曲线.轧辊模型的正凸度导致轧件中心局部负凸度的产生,这与实际的板形特点相符.随着道次压下量的减小,轧件负凸度逐渐获得缓解.第7道次轧后轧件的整体凸度约为35 μm.1)开发了中厚板多道次热轧的有限元连续模拟方法,其中等效空心辊模型的建立在保证计算精度的前提下显著节约计算时间,模型生成模块的建立实现了有限元模型的参数化生成、单元网格的重划分及前后道次间的参数传递,最终实现了多道次的连续模拟.2)以实际7道次热轧规程为例进行了模拟计算.模拟结果与实测值吻合良好,证明了模拟方法的正确性3)模拟结果为以获得良好板形为目标的轧制规程的改进提供了指导.【相关文献】[1]HWANG S M,SUN C G,RYOO S R.An integrated FE process model for precision analysis of thermo-mechanical behaviors of rolls and strip in hot strip rolling [J].Computer Methods in Applied Mechanics and Engineering,2002,191(37/38):4015-4033.[2]刘宏民,丁开荣,李兴东,等.板形标准曲线的理论计算方法[J].中国机械工程,2008,44(8):137-142.[3]邵健,何安瑞,杨荃,等.热连轧机板形设定控制系统仿真及应用[J].钢铁研究学报,2008,20(6):53-56.[4]YU Hai-liang,LIU Xiang-hua,Lee G T,et al.Numerical analysis of strip edge drop for Sendzimir mill[J].Journal of Materials Processing Technology,2008,208(1/2/3):42-52.[5]ISHIKAWA T,YUKAWA N,TOZAWA Y.Optimization of pass schedule from the view point of shape and profile of cold rolled strip[J].CIRP Annals-Manufacturing Technology,1989,38(1):257-260.[6]俞海良,赵宪明,刘相华.板带精轧过程轧制力的三维弹塑性有限元分析[J].钢铁研究,2005,33(1):14-16.[7]DONG Hong-bo,KANG Yong-lin.Prediction model for rolling force parameters during rolling of medium and heavy plate[J].Special Steel,2004,25(2):6-8.[8]LIU Cai,CUI Zhen-shan.Thermo mechanical coupled finite-element modelling of slab hot rolling[J].Chinese Journal of Mechanical Engineering,1998,34(4):35-39.[9]REZA R,SIAMAK S.Three-dimensional model for hot rolling of aluminum alloys [J].Materials and Design,2007,28:2366-2372.[10]XIAO Hong,XU Hong-biao,BI En-fu.Prediction of rolling loads,temperature and microstructure variation during hot strip rolling[J].Iron&Steel,2003,38 (9):35-38.[11]JANG Y S,KO D C,KIM B M.Application of the finite element method to predict microstructure evolution in the hot forging of steel[J].Journal of Materials Processing Technology,2000,101(1/2/3):85-94.[12]KOMORI K.Simulation of deformation and temperature in multi-pass three-roll rolling[J].Journal of Materials Processing Technology,1999,92-93:450-457.[13]WANG Min-ting,ZANG Xin-liang,LI Xue-tong.Finite element simulation of hot strip continuous rolling process coupling microstructural evolution[J].Journal of Iron and Steel Research,International,2007,14 (3):30-36.[14]CHANDRA S,DIXIT U S.A rigid-plastic finite element analysis of temper rolling process[J].Journal of Materials Processing Technology,2004,152(1):9-16.[15]JIANG Z Y,TIEU A K.A simulation of three-dimensional metal rolling processes by rigid-plastic finite element method[J].Journal of Materials Processing Technology,2001,112(1):144-151.[16]PAWELSKI O,PIBER V.Possibilities and limits of deformation in width direction in hot flat rolling[J].Stahl und Eisen,1980,100(17):937-949.。
轧制过程中粗轧宽度变形的三维有限元模拟
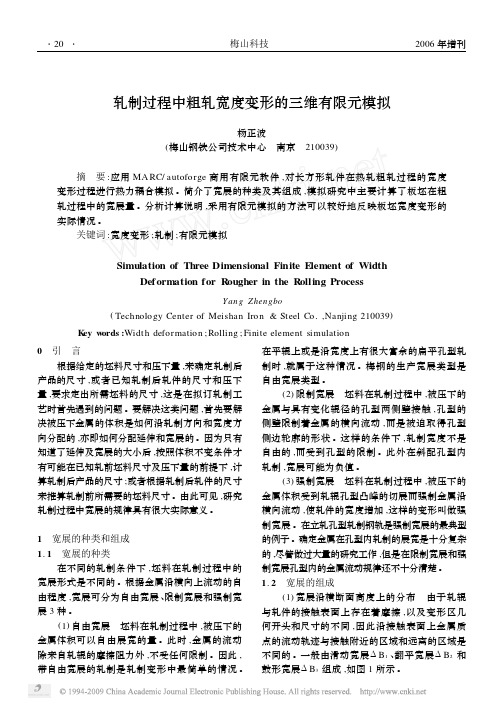
轧制过程中粗轧宽度变形的三维有限元模拟杨正波(梅山钢铁公司技术中心 南京 210039) 摘 要:应用MARC/autoforge商用有限元软件,对长方形轧件在热轧粗轧过程的宽度变形过程进行热力耦合模拟。
简介了宽展的种类及其组成,模拟研究中主要计算了板坯在粗轧过程中的宽展量。
分析计算说明,采用有限元模拟的方法可以较好地反映板坯宽度变形的实际情况。
关键词:宽度变形;轧制;有限元模拟Simulation of Three Dimensional Finite Element of WidthDeformation for Rougher in the Rolling ProcessYang Zhengbo(Technology Center of Meishan Iron&Steel Co.,Nanjing210039) K ey w ords:Widt h deformation;Rolling;Finite element simulation0 引 言 根据给定的坯料尺寸和压下量,来确定轧制后产品的尺寸,或者已知轧制后轧件的尺寸和压下量,要求定出所需坯料的尺寸,这是在拟订轧制工艺时首先遇到的问题。
要解决这类问题,首先要解决被压下金属的体积是如何沿轧制方向和宽度方向分配的,亦即如何分配延伸和宽展的。
因为只有知道了延伸及宽展的大小后,按照体积不变条件才有可能在已知轧前坯料尺寸及压下量的前提下,计算轧制后产品的尺寸;或者根据轧制后轧件的尺寸来推算轧制前所需要的坯料尺寸。
由此可见,研究轧制过程中宽展的规律具有很大实际意义。
1 宽展的种类和组成1.1 宽展的种类 在不同的轧制条件下,坯料在轧制过程中的宽展形式是不同的。
根据金属沿横向上流动的自由程度,宽展可分为自由宽展、限制宽展和强制宽展3种。
(1)自由宽展 坯料在轧制过程中,被压下的金属体积可以自由展宽的量。
此时,金属的流动除来自轧辊的摩擦阻力外,不受任何限制。
有限元模拟在板材轧制中的应用
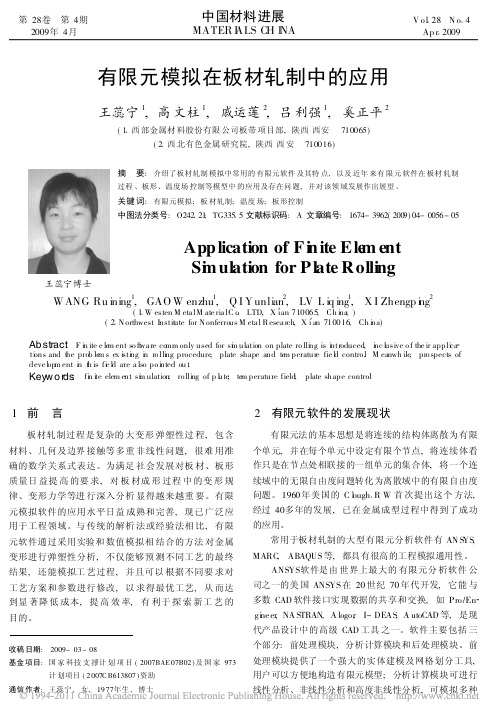
1前 言
板材轧制过程是复杂的 大变形 弹塑性过 程, 包含 材料、几何及边界 接触等多重 非线性问题, 很难 用准 确的数学关系式表达。为满足 社会发展对板 材、板形 质量日 益提 高 的要 求, 对 板 材成 形 过程 中 的变 形 规 律、变形力学等进 行深入分析 显得越来越重 要。有限 元模拟软件的应用水平日益 成熟和完善, 现已 广泛应 用于工程领域。与 传统的解析 法或经验法相 比, 有限 元软件通过采用实验和 数值模拟相 结合的方法 对金属 变形进行弹塑性分析, 不仅能够预 测不同工艺 的最终 结果, 还能模拟工 艺过程, 并且可以 根据不同要 求对 工艺方案和参数进行修改, 以 求得最优工艺, 从 而达 到显 著降 低 成本, 提 高 效 率, 有 利于 探 索 新工 艺 的 目的。
58
中国材料进展
第 28卷
性有限元法就已成功地用于求解锻压、挤压、拉拔和轧 制等各种金属压力加工过程。在金属塑性加工成形过程 中, 材料不仅表现出塑性, 同时也表现出粘性。对此, 人们提出了粘塑性材料模型。在高应变速率下的金属材 料一般作为弹粘塑性处理。如果弹性变形较小, 可以忽 略, 则作为刚粘塑性处理。 Z ienk iew cz在有限元法中引 入了刚粘塑性模型, 提出了刚粘塑性有限元法。
分析板带轧制过程, 必须研究轧件塑性变形和轧辊 弹性变形的耦合问题。以 4辊板带轧机为例, 辊系弹性 变形应包括: 工作辊和支承辊的弹性弯曲变形; 工 作辊与支承辊之间的弹性接触变形; 轧件与工作辊的 弹性压扁变形。轧机辊缝形状对轧件的塑性变形有直接 影响。较 理 想的 计 算方 法 是采 用 有 限元 法 或 边界 元 法 [ 1- 2] 将工作辊和轧件的弹塑性接触变形以及工作辊与 支承辊的弹性接触变形耦合进行求解, 建立轧制过程整 体模型。其中将轧件视为弹塑性或刚塑性材料, 轧辊被 视为弹性体, 并通过和轧件接触直接耦合在一起 [ 3] 。但 该方法对计算机计算速度和存贮容量要求较高, 特别是 当板带的宽厚比较大时, 对实际的板带轧制过程进行模 拟尚有难度。另一思路是将轧件与轧辊分开计算, 通过 接触力和变形协调关系, 采用一种迭代的方案将二者间 接耦合起来 [ 4- 5]。文献 [ 6] 采用间接耦合有限元法计算 模型, 轧件的变形采用刚塑性有限元法计算, 辊系变形 计算采用弹性有限元法。利用迭代方法得到所求的运动 许可速度场, 进而求出应力应变场、轧件变形和轧制压 力。其中刚塑性有限元法收敛准则常采用总泛函变化率 修正量的欧氏范数收敛以及节点应力不平衡量收敛。该 方法在计算量和复杂程度上优于弹塑性有限元法, 但在 弹性变形占总变形量比例较小可以忽略的情况下采用, 有一定局限性。图 2是将工作辊的弹性变形和轧件的塑 性变形耦合的计算系统流程图 [ 7] 。
- 1、下载文档前请自行甄别文档内容的完整性,平台不提供额外的编辑、内容补充、找答案等附加服务。
- 2、"仅部分预览"的文档,不可在线预览部分如存在完整性等问题,可反馈申请退款(可完整预览的文档不适用该条件!)。
- 3、如文档侵犯您的权益,请联系客服反馈,我们会尽快为您处理(人工客服工作时间:9:00-18:30)。
的功率泛函
≯=熹fc磊m£珞△vf眦I Tvdl节∥卅
(1)
式中矿——轧件内部的塑性变形功率 厅——等效应力 言——等效变形速率 m——速度敏感指数 ∥——轧件与轧辊之间的摩擦功率
△K——轧件与轧辊之间的相对滑动速度 诈——摩擦切应力 西‘——外张力功率 r——张应力,”+”为前张力,”一”为后张力 v——相应表面处的位移速度 彳——变形面积(弧长) 厶——摩擦接触区面积(长度) 厶——张力作用的面积(厚度)
第45卷第6期 2009年6月
机械工程学报
JOURNAL OF MECHANICAL ENGINEERnqG
V01.45 Jun.
NO.6 2009
DoI:10.3901/JM:E.2009.06.193
板材轧制过程中快速有限元在线算法水
李长生1 宋叔尼1 梅瑞斌1 张光亮2刘相华1
(1.东北大学轧制技术及连轧自动化国家重点实验室沈阳 110004: 2.中国科学院金属研究所沈阳 1 l0016)
15 206
15 580
2.4
727
1 016
40.68
24.08
1 041
1 008
12 545
12 392
1.2
734
930
40.68
26.14
1 28l
l 037
14 312
14413
0.7
810
900
53.89
36.96
l 550
932
25 803
26050
0.9
817
1 300
37.96
27.54
Roiling
Online calculation
0前言
有限元法(Finite element method,FEM)在轧制
·国家自然科学基金重点资助项Ij(50534020)。20080717收到初稿 20090220收到修改稿
万方数据
过程力能参数、变形参数以及组织演变规律等分析 中得到了广泛的应用p击】。FEM虽然计算精度高, 但是由于计算效率低而使其在线应用受到了限制。 如何提高FEM计算和收敛速度,在保证计算精度 的前提下,实现FEM在线应用已经成为科技人员 追求的目标。
雳D|to径ni。/v (ra速m毒· S,、 a)轧H0前瑚/m=紫/厚H 度m、 lTl 8| W槭/” mm ℃ 筹轧制F埘c/kN算值轧F舄瞄 划kN恼舅2|羲确
629
2430
18.37
11.7l
l 035
960
13 013
13 320
2.3
641
1 550
30.00
18.37
1 035
969
机械工程学报
第45卷第6期
快速有限元(Fast finite element,FFE)是在FEM 基础上提出的通过改善单元、改进算法和改善收敛 稳定性等以加快计算速度的方法。HETMANIUK
掣‘7】采用虚构区域分解法,解决了对称声学刚性求 解发散问题,缩短了计算时间。SASCHA等[81基于 形素算法开发了颈椎骨运动快速有限元模型,对颈 椎治疗进行跟踪减少医疗风险。陈璞等【9】提出了刚
采用Newton.Raphson方法求解泛函式(1)的最 小值,通过迭代与搜索得到近似真实的速度场,由 速度场计算应变速率和应力场,从而得到轧制力。 1.2边界条件
图1所示为¥LN过程的FEM网格。其中Do为 板材轧前厚度,D1为板材轧后厚度,a为咬入角。 速度边界条件是,AB/CD:vx=vxl,vy=0;BD:
本文在刚塑性有限元(Rigid plastic finite element method,RPFEM)求解轧制过程研究工作基 础上开发了板材轧制过程FFE模型,分析了计算方 法和计算机配置等对计算时间的影响。制定了某热 轧带钢厂轧制过程轧制力设定技术的FFE在线应用 方案,应用效果良好。
1轧制过程FEM求解
度矩阵超方程的细胞稀疏索引存储方法,减少了磁 盘存储空间,一定程度上加快了计算速度。鲍益东 等[10】基于有限元网格等距原则提出了等距算法,从 而提高了汽车覆盖件等距计算效率。周国发等【llJ基 于聚合物多组分成形技术,建立了三维非稳态等温 多相分层充模流动模型,通过分离各场变量分析过 程从而提高CPU存储能力和求解效率。
l 550
921
25 457
25 ห้องสมุดไป่ตู้10
1.3
837
1 700
32.63
22.35
I 628
918
25426
25 110
1.2
810
1 000
53.70
37.82
1 550
938
24647
24 140
2.1
万方数据
2009年6月
李长生等:板材轧制过程中快速有限元在线算法
BXl和BX2分别代表本钢l 700 mln轧机的两组数 据,BSI~BS4分别代表宝钢2 050 mm轧机的四组 数据。可以看出,最大轧制力计算误差值为2.4%。
In addition,the influence of operating system,hardware and sottware of computer on the calculating time is also discussed.The FFE
online calculation module developed is well used in a hot strip plant. Key words:Finite element method Fast finite element Arithmetic
deformation,temperature and microstructure evolution during rolling process.But online calculation is impossible because of the
long time consumed in the FEM calculation of rolling parameters.Fast finite element(FFE)method has advantage of calculation
with high precision and fast speed.On the basis of rigid plastic finite element method(RPFEM),the FFE method in strip rolling is
developed,Effects of element numbers on calculation time and precision are analyzed.Onlme arithmetic methods of accelerating convergence and reducing search time are researched,including the combined damped Newton and Brunt method to reduce the one dimensional searchtime;the better initial value Can be obtained by adopting improved mid—point integral Newton method;improved Newton method with trust region method and forced positive definite Hessian matrix method are used to reduce the convergence time
Northeastern University,Shenyang 1 1 0004; (2.Institute ofMetal Research,China Academy of Science,Shenyang 1 10016)
Abstract:Finite element method(FEM)plays a very important role in the simulation and prediction of the parameters of pressure,
图2所示为单元数目与计算时间和迭代次数的 关系,图3表示了单元数目从0~100时的计算时间 变化。可以看出,计算时间和迭代次数有随着单元 数目增加而增加的趋势;单元数目较少,迭代次数 对计算时间影响较小,而单元数目较多时对计算时 间影响较大。由图3可以看出,单元数目在0~100 变化时,计算时间小于0.6 S。
40 50 60 70 80
单元数目,阶
图3单元数目对计算时间的影响
90 100
O
8 6
4
2
。咎糊磷琳基
O
2
0
100 2【m
300 400
摘要:有限元法(Finite element method,FEM)在轧制过程力能参数、变形参数、温度参数以及组织演变等模拟与预测中发挥 了重要作用,但由于有限元求解问题时所需的计算时间较长而无法实现轧制过程参数的在线计算。快速有限元(Fast fmite element,FFE)方法具有计算精度高和计算速度快等优点。基于刚塑性有限元(Rigid plasticity finite element method,RPFEM)方 法开发了板材轧制过程FFE程序。讨论了单元数目对计算时间和计算精度的影响规律,研究加快计算收敛速度和减少搜索 时间的在线算法,包括采用阻尼Newton-Brunt法相结合减少一维搜索时间;采用改进循环中点求积Newton法为 Newton.Raphson迭代法寻求比较好的初始值;采用信赖域Newton混合迭代法以及改进的Cholesky分解使Hessian矩阵强迫 正定以加快收敛速度;研究计算机操作系统、软硬件条件对计算时间的影响。开发的FFE在线设定模块在某热轧带钢厂取 得良好的应用效果。 关键词:有限元法快速有限元算法轧制在线计算 中图分类号:TG301