制造过程审核检查表
合集下载
制造过程审核检查表

4
1、文件与工装、刀具、模具、检具其中任意 一项未符合最终版本各扣1分。
3
1、包装方案未按照和客户达成一致的包装方 案扣3分。
1、包装上未有客户标识扣1分。
4
2、包装上未有产品名称标识扣1分。 3、包装上未有产品零件号扣1分。
4、包装上未有产品数量标识扣1分。
3
1、无安全库存资料扣2分。 2、安全库存资料不完善扣1分。
1、物料未按要求区域划分待检区、合格区、
不合格区或划分不合理扣1分。
5
2、划分标识不明确扣1分。 3、每批次产品无编码标识扣1分。
4、每批次产品无厂家标识扣1分。
5、每批产品无炉批号扣1分。
第 1 页,共 4 页
文件编号: OK
检具精度能否满足要求,检具 3 得到了有效的验证,检测,
并有有效期标签
4
库存管理程序,来料的安全库 存
三: 生产工位 按照控制计划审核生产过
1 程,设备参数与文件一致
2 产出产品的追溯方案
3 RPN的改进
偶发事件的应急方案,人 4 员,设备,备用工装,检
具,刀具,模具 关键特性是否都在控制方式 5 之内
明确的产品状态及分析报
6
告,红盒子,黄盒子,绿盒 子及调机品,首末件,存储
2
1分。 2、控制计划版本与版本记录不相符不正确扣
1分
1、无工装夹具扣2分。
8
2、工装夹具与清单不相符扣2分。 3、过程责任者不明确扣2分。
4、过程责任者未经培训考核就上岗扣2分
1、未采用SPC统计过程控制扣2分。
5
2、未采用防错过程控制扣2分.
3、未采用全检的控制方式扣1分
5
1、来料未按要求进行检验扣3分。 2、未有检验报告扣2分。
制造过程审核检查表
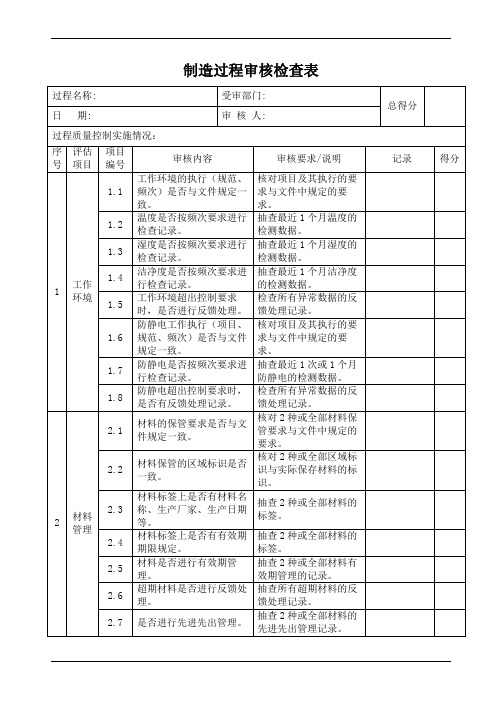
4.2
设备状态标识是否正确。
核对3台设备的状态标识。
4.4
是否制定年度PM工作计划。
检查年度PM工作计划。
4.5
是否按照年度PM工作计划实施。
抽查3个项目确认实施情况。
4.6
关键设备的备件是否进行可得性分析。
抽查最近2个月设备可得性分析记录表。
4.7
是否对关键设备的停机原因进行分析并改善。
抽查最近2个月关键设备故障停机原因分析及改善记录表。
4.8
设备故障维修后是否进行记录。
抽查最近2个月设备维修的记录。
4.9
设备维修后是否进行QC验证。
抽查最近2个月设备维修后的QC记录。
5
工装管理
5.1
是否有工装保管台账。
检查工装保管台账。
5.2
是否按工装文件的规定进行管理。
抽查2个工装核对其实施情况与文件规定的要求。
6
量测管理
6.1
是否有量测设备的管理台账。
检查没有达成质量目标的分析改进措施。
7.13
Cpk、Ppk是否满足要求。
检查工序的过程能力分析指数Cpk、Ppk值。
7.14
过程能力(Cpk、Ppk)不满足要求时,是否进行分析改进。
检查过程能力分析改进的相关措施。
7.15
关键参数是否按要求进行SPC管控。
检查要求SPC管控的管控图。
7.16
超出规范限或控制限后是否进行处置。
核对5项CP文件与作业指导书的内容。
7.3
设备中的工艺参数是否与文件中的规定一致。
抽查3台设备核对当前程序的工艺参数与文件规定的要求。
7.4
记录表中监控要求是否与作业指导书要求一致。
设备状态标识是否正确。
核对3台设备的状态标识。
4.4
是否制定年度PM工作计划。
检查年度PM工作计划。
4.5
是否按照年度PM工作计划实施。
抽查3个项目确认实施情况。
4.6
关键设备的备件是否进行可得性分析。
抽查最近2个月设备可得性分析记录表。
4.7
是否对关键设备的停机原因进行分析并改善。
抽查最近2个月关键设备故障停机原因分析及改善记录表。
4.8
设备故障维修后是否进行记录。
抽查最近2个月设备维修的记录。
4.9
设备维修后是否进行QC验证。
抽查最近2个月设备维修后的QC记录。
5
工装管理
5.1
是否有工装保管台账。
检查工装保管台账。
5.2
是否按工装文件的规定进行管理。
抽查2个工装核对其实施情况与文件规定的要求。
6
量测管理
6.1
是否有量测设备的管理台账。
检查没有达成质量目标的分析改进措施。
7.13
Cpk、Ppk是否满足要求。
检查工序的过程能力分析指数Cpk、Ppk值。
7.14
过程能力(Cpk、Ppk)不满足要求时,是否进行分析改进。
检查过程能力分析改进的相关措施。
7.15
关键参数是否按要求进行SPC管控。
检查要求SPC管控的管控图。
7.16
超出规范限或控制限后是否进行处置。
核对5项CP文件与作业指导书的内容。
7.3
设备中的工艺参数是否与文件中的规定一致。
抽查3台设备核对当前程序的工艺参数与文件规定的要求。
7.4
记录表中监控要求是否与作业指导书要求一致。
制造过程审核检查表

评分
6.2.5
对产品调整/更换是否有必备的辅助器具?如调整计划、调整辅助装置/比较辅助方法、灵活的模具更换装置、极限标样
评分
6。2。6
是否进行批量生产起始认可,并记录调整参数及偏差情况?如:产品更改、停机/过程中断、生产参数更改、首件检验记录并存档、工作岗位的整齐和清洁、包装、检具与检验、测量和试验设备的认可/更改状态
评分
6。4.5
对产品和过程是否进行持续改进?如:成本优化、减少浪费(如:废品和返修)、优化更换装备时间,提高设备利用率、降低流转时间、降低库存量等
评分
6。4。6
对产品和过程是否有确定的目标值,并监控是否达到目标?目标必须明确并可实现,且必须保证其现时性,必需时必续确定特别的措施加以落实。如:人员的出勤率、缺勤率、已生产数量(例如:缺勤率、审核结果)、流转时间、缺陷成本(不符合性)、过程特性值(过程能力指数)
序号
审核项目/内容
审核结果记录及评分
6。3.1
产品数量/生产批次大小是否按需求而定?是否有目的地运往下道工序?如:足够、合适的运输器具、定置库位、最小库存/无中间库存、看板管理、向下道工序直供合格件数量记录等
工序1
工序2
工序3
工序4
工序5
工序6
工序7
工序8
工序9
工序10
评分
6.3。2
产品/零件是否按要求贮存?运输方式/包装方法是否按产品/零件特性而定?如:防损伤、零件定置、整齐、清洁、不超装(周转箱)、控制贮存时间、环境影响
评分
6。2.7
要求的纠正措施是否按时落实并检查其有效性?纠正措施涉及整个生产过程链、从原材料到客户的使用,如:风险分析(过程P-FEMA)/缺陷分析、审核后提出改进计划、内部/外部接口会谈、内部抱怨、顾客抱怨、顾客调查
6.2.5
对产品调整/更换是否有必备的辅助器具?如调整计划、调整辅助装置/比较辅助方法、灵活的模具更换装置、极限标样
评分
6。2。6
是否进行批量生产起始认可,并记录调整参数及偏差情况?如:产品更改、停机/过程中断、生产参数更改、首件检验记录并存档、工作岗位的整齐和清洁、包装、检具与检验、测量和试验设备的认可/更改状态
评分
6。4.5
对产品和过程是否进行持续改进?如:成本优化、减少浪费(如:废品和返修)、优化更换装备时间,提高设备利用率、降低流转时间、降低库存量等
评分
6。4。6
对产品和过程是否有确定的目标值,并监控是否达到目标?目标必须明确并可实现,且必须保证其现时性,必需时必续确定特别的措施加以落实。如:人员的出勤率、缺勤率、已生产数量(例如:缺勤率、审核结果)、流转时间、缺陷成本(不符合性)、过程特性值(过程能力指数)
序号
审核项目/内容
审核结果记录及评分
6。3.1
产品数量/生产批次大小是否按需求而定?是否有目的地运往下道工序?如:足够、合适的运输器具、定置库位、最小库存/无中间库存、看板管理、向下道工序直供合格件数量记录等
工序1
工序2
工序3
工序4
工序5
工序6
工序7
工序8
工序9
工序10
评分
6.3。2
产品/零件是否按要求贮存?运输方式/包装方法是否按产品/零件特性而定?如:防损伤、零件定置、整齐、清洁、不超装(周转箱)、控制贮存时间、环境影响
评分
6。2.7
要求的纠正措施是否按时落实并检查其有效性?纠正措施涉及整个生产过程链、从原材料到客户的使用,如:风险分析(过程P-FEMA)/缺陷分析、审核后提出改进计划、内部/外部接口会谈、内部抱怨、顾客抱怨、顾客调查
过程审核检查表-ok

4
过程能力/目标
与过程有关的质量目标是否达到?
抽××件产品进行检测,查其合格率是否符合规定要求(如目标要求)?
查看现场的SPC控制图,判断过程是否受控?
与特殊特性有关的过程是否进行了过程能力研究?
收集数据,计算过程能力指数?结果是否符合要求?
FR820203 B/0
控制计划中有无产品和过程特殊特性的控制要求?是否执行?
控制计划中的反应计划是否得到实施?
综合评价控制计划的可行性与正确性?
2/1
过程/人的因素
是否持证上岗?有无经验?技能如何?
上岗前是否接受过上个岗培训?有无过程质量控制的知识?
是否熟悉本岗位的作业文件并能掌握其要求?
是否能认真执行作业文件的规定?
作业效率高低如何?
员工是否熟悉并执行包装规范,是否明确包装要求?
产品包装质量是否符合要求,是否进行了检查?
2
交付
是否确定了与顾客保持联络的顾客代表?
交付时产品是否满足了所有顾客要求?
产品出库是否符合程序或文件规定,手续是否齐全?
交付是否按合同要求进行,是否满足100%准时?
在交付至目的地期间,是否对产品进行了防护?
3
材料在仓库和车间现场是否进行了适当防护?
是否对顾客财产按要求进行了接收、贮存、使用、异常报告?
FR820203 B/0
过程审核检查表
No
品名规格
审核过程
交付/服务
审核员
审核日期
序号
审核
项目
审核内容
审核情况记录(分)
备注
10
7
4
0
nb
1
终检
包装
对最终产品是否进行了验证(检验和试验),是否符合顾客或订单要求?
过程能力/目标
与过程有关的质量目标是否达到?
抽××件产品进行检测,查其合格率是否符合规定要求(如目标要求)?
查看现场的SPC控制图,判断过程是否受控?
与特殊特性有关的过程是否进行了过程能力研究?
收集数据,计算过程能力指数?结果是否符合要求?
FR820203 B/0
控制计划中有无产品和过程特殊特性的控制要求?是否执行?
控制计划中的反应计划是否得到实施?
综合评价控制计划的可行性与正确性?
2/1
过程/人的因素
是否持证上岗?有无经验?技能如何?
上岗前是否接受过上个岗培训?有无过程质量控制的知识?
是否熟悉本岗位的作业文件并能掌握其要求?
是否能认真执行作业文件的规定?
作业效率高低如何?
员工是否熟悉并执行包装规范,是否明确包装要求?
产品包装质量是否符合要求,是否进行了检查?
2
交付
是否确定了与顾客保持联络的顾客代表?
交付时产品是否满足了所有顾客要求?
产品出库是否符合程序或文件规定,手续是否齐全?
交付是否按合同要求进行,是否满足100%准时?
在交付至目的地期间,是否对产品进行了防护?
3
材料在仓库和车间现场是否进行了适当防护?
是否对顾客财产按要求进行了接收、贮存、使用、异常报告?
FR820203 B/0
过程审核检查表
No
品名规格
审核过程
交付/服务
审核员
审核日期
序号
审核
项目
审核内容
审核情况记录(分)
备注
10
7
4
0
nb
1
终检
包装
对最终产品是否进行了验证(检验和试验),是否符合顾客或订单要求?
过程审核检查表

规定是否一致,有否存在矛盾的情况?
7、该工序有否其他管理性文件?其控制是否为现行有效?
8、调查该工序操作人员(和检验人员)对控制计划相关控制内容是否了解、清楚?对相关作业指导书(或检验指导书)及其他管理性文件的内容是否理解并掌握?
9、观察工序操作人员(和检验人员)对该工序操作及检验的执行情况,并听取其意见和要求。
3、控制计划中对该工序质量要素的控制是否明确、是否正确?
4、在该工序能否发现有效的控制计划版本?
5、与控制计划相对应的相关作业指导书是否可在该工序获得?作业指导书是否为现行有效版本?
6.对于该工序的质量控制要求,相关作业指导书与控制计划的
规定是否一致,有否存在矛盾的情况?
规定是否一致,有否存在矛盾的情况?
10、根据上述活动,评价质量控制计划是否可行与正确,评价工序操作人员对质量控制要求的理解与执行程度,并得出是否能够满足生产要求的结论。
序号
审核项目
审核内容
实施记录
判定
2
工序因素的受控情况
1.在该工序质量控制计划中规定了哪些方面的控制要求?(有
无特殊特性的要求?)
无特殊特性的要求?)
2.在实际作业中,各工序要素的控制是否达到了工序质量控制
文件的要求?(通过现场核对、调查,作出分析和评价)
文件的要求?(通过现场核对、调查,作出分析和评价)
文件的要求?(通过现场核对、调查,作出分析和评价)
3.现场调查和评价该工序所涉及的人、机、料、法、环、测等诸因素,特别是该工序的主导因素是否达到了工序质量控制文件的要求(如关于人员的培训及岗位要求、设备的点检及维护保养、物料的控制、环境的维持、记录的获取、检验和试验的进行、产品的追溯等方面)
审核时,尤其应注意对工序中的特殊特性的控制
7、该工序有否其他管理性文件?其控制是否为现行有效?
8、调查该工序操作人员(和检验人员)对控制计划相关控制内容是否了解、清楚?对相关作业指导书(或检验指导书)及其他管理性文件的内容是否理解并掌握?
9、观察工序操作人员(和检验人员)对该工序操作及检验的执行情况,并听取其意见和要求。
3、控制计划中对该工序质量要素的控制是否明确、是否正确?
4、在该工序能否发现有效的控制计划版本?
5、与控制计划相对应的相关作业指导书是否可在该工序获得?作业指导书是否为现行有效版本?
6.对于该工序的质量控制要求,相关作业指导书与控制计划的
规定是否一致,有否存在矛盾的情况?
规定是否一致,有否存在矛盾的情况?
10、根据上述活动,评价质量控制计划是否可行与正确,评价工序操作人员对质量控制要求的理解与执行程度,并得出是否能够满足生产要求的结论。
序号
审核项目
审核内容
实施记录
判定
2
工序因素的受控情况
1.在该工序质量控制计划中规定了哪些方面的控制要求?(有
无特殊特性的要求?)
无特殊特性的要求?)
2.在实际作业中,各工序要素的控制是否达到了工序质量控制
文件的要求?(通过现场核对、调查,作出分析和评价)
文件的要求?(通过现场核对、调查,作出分析和评价)
文件的要求?(通过现场核对、调查,作出分析和评价)
3.现场调查和评价该工序所涉及的人、机、料、法、环、测等诸因素,特别是该工序的主导因素是否达到了工序质量控制文件的要求(如关于人员的培训及岗位要求、设备的点检及维护保养、物料的控制、环境的维持、记录的获取、检验和试验的进行、产品的追溯等方面)
审核时,尤其应注意对工序中的特殊特性的控制
IATF16949过程审核检查表
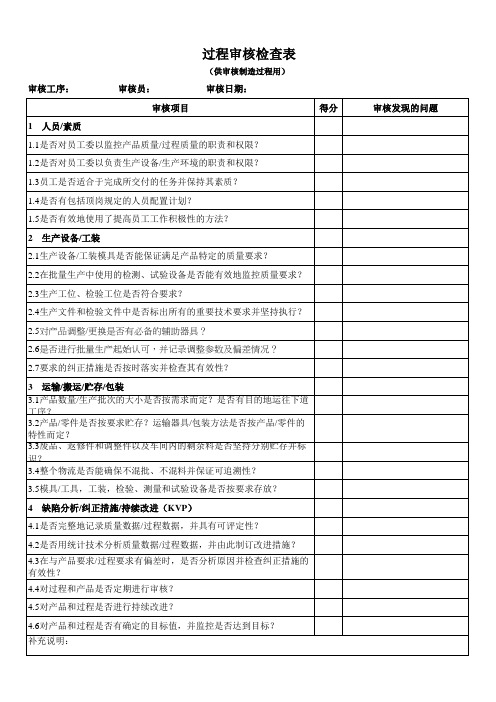
2.1生产设备/工装模具是否能保证满足产品特定的质量要求? 2.2在批量生产中使用的检测、试验设备是否能有效地监控质量要求? 2.3生产工位、检验工位是否符合要求? 2.4生产文件和检验文件中是否标出所有的重要技术要求并坚持执行? 2.5对产品调整/更换是否有必备的辅助器具? 2.6是否进行批量生产起始认可,并记录调整参数及偏差情况? 2.7要求的纠正措施是否按时落实并检查其有效性? 3 运输/搬运/贮存/包装
4.1是否完整地记录质量数据/过程数据,并具有可评定性? 4.2是否用统计技术分析质量数据/过程数据,并由此制订改进措施? 4.3在与产品要求/过程要求有偏差时,是否分析原因并检查纠正措施的 有效性? 4.4对过程和产品是否定期进行审核? 4.5对产品和过程是否进行持续改进? 4.6对产品和过程是否有确定的目标值,并监控是否达到目标? 补充说明:
3.1产品数量/生产批次的大小是否按需求而定?是否有目的地运往下道 工序? 3.2产品/零件是否按要求贮存?运输器具/包装方法是否按产品/零件的 特性而定? 3.3废品、返修件和调整件以及车间内的剩余料是否坚持分别贮存并标 识? 3.4整个物流是否能确保不混批、不混料并保证可追溯性? 3.5模具/工具,工装,检验、测量和试验设备是否按要求存放? 4 缺陷分析/纠正措施/持续改进(KVP)
过程审核检查表
(供审核制造过程用)
审核工序:
审核员: 审核项目
审核日期: 得分 审核发现的问题
1
人员/素质
ቤተ መጻሕፍቲ ባይዱ
1.1是否对员工委以监控产品质量/过程质量的职责和权限? 1.2是否对员工委以负责生产设备/生产环境的职责和权限? 1.3员工是否适合于完成所交付的任务并保持其素质? 1.4是否有包括顶岗规定的人员配置计划? 1.5是否有效地使用了提高员工工作积极性的方法? 2 生产设备/工装
IATF16949制造过程内部审核检查表

内 部 审 核 检 查 表
工程变更管理
程序
生产管制程序生产计划控制
程序
118.6.2
128.6.3 139.1.1.1 组织生产的零部件是否被顾客指定为“外观项目”如果是组织是否提供了1.适当的资源,2.适当的颜色,文理,金属亮度,组织结构,映像清晰度的触感技术的标准样件,3.外观标准样品及评价设备的维护和控制,4.对从事外观评价人员的能力和资格的验证
是否对制造过程进行了监视和测量?是否采用统计过程控制方法对特殊特性工序进行了监控,并保持过程能力负荷生产件批准时的要求?是否出现过程能力不足或不受控的情况?如出现是否启动反应计划?是否制定了纠正措施计划并实施验证?
组织是否按照控制计划中的规定,根据顾客的工程材料和性能标准,对每一种产品进行全尺寸检验和功能性验证,其结果可供顾客评审。
制造过程审核检查表
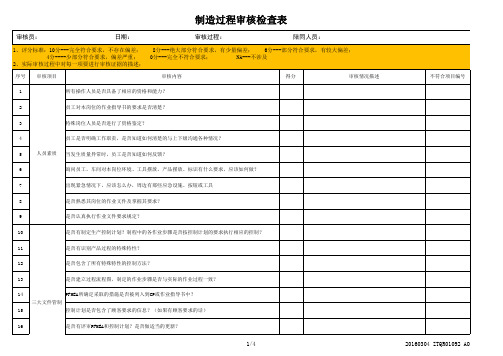
得分
审核情况描述
不符合项目编号
1/4
20160304 ZTQR01092 AO
制造过程审核检查表
审核员: 日期: 审核过程: 陪同人员:
1、评分标准:10分---完全符合要偏差严重; 2、实际审核过程中对每一项要进行审核证据的描述;
得分
审核情况描述
不符合项目编号
2/4
20160304 ZTQR01092 AO
制造过程审核检查表
审核员: 日期: 审核过程: 陪同人员:
1、评分标准:10分---完全符合要求,不存在偏差; 4分----少部分符合要求,偏差严重; 2、实际审核过程中对每一项要进行审核证据的描述;
序号 35 36 37 38 39 40 41 42 43 44 45 46 47 48 49 50 51 不合格分析、 纠正措施、持 续改进 生产设备、 工装 测量 审核项目
8分---绝大部分符合要求,有少量偏差; 6分---部分符合要求,有较大偏差; 0分---完全不符合要求; NA---不涉及
审核项目 审核内容 不合格分析、 纠正措施、持 返工产品是否经过重新检验合格后才转入下工序或出货? 续改进 当发生顾客投诉时是否将相关信息传达到制造部门? 是否针对异常原因进行了分析?采取了什么措施?是否有效? 过程中所产生相关记录是否齐全?字迹是否清楚,真实? 是否有存在随意涂改现象? 相关记录是否按文件要求进行保管标识?
得分
审核情况描述
不符合项目编号
物料:运输/搬 产品/零件,运输器具/包装方法合理,不会造成产品的倒塌、损坏、锈蚀等; 运/贮存/包装 产品的包装是否符合顾客的要求? 不良品是否有明确的存放地点,标识清楚; 当制程发生不合格时是如何处置的?是否有处理结果的记录? 是否有返工作业指导书,这些指导书是否易于被适当的人员得到并使用?
- 1、下载文档前请自行甄别文档内容的完整性,平台不提供额外的编辑、内容补充、找答案等附加服务。
- 2、"仅部分预览"的文档,不可在线预览部分如存在完整性等问题,可反馈申请退款(可完整预览的文档不适用该条件!)。
- 3、如文档侵犯您的权益,请联系客服反馈,我们会尽快为您处理(人工客服工作时间:9:00-18:30)。
制造过程审核检查表
部门
产品类别
制造过程
序号
审核容
1 1.1 1.2 1.3 1.4 1.5
2 2.1 2.2 2.3 2..4 2.5
3 3.1 3.2 3.3
4 4.1 4.2 4.3 4.4 4.5
5 5.1 5.2 5.3 5.4
6 6.1
6.2
6.3 6.4
过程输入是什么?(过程输入) 是否在开发和批量生产之间进行了项目交接,以确保生产顺利启动? 来料是否在约定的时间按所需数量/生产批次大小被送至正确的存放位置/工位? 是否对来料进行了适当的仓储,所使用的运输工具/包装设备是否适合来料的特殊特性? 来料是否具备必要的标识/记录/放行,并且得以适当地体现? 是否对在量产过程中的产品或过程变更开展了跟踪和记录? 所有生产过程是否受控?(过程管理) 控制计划的要求是否完整并得到有效落实? 是否进行了生产启动的重复性放行? 是否对生产中的特殊特性进行了管理? 是否对未放行和/或缺陷零件进行了管理? 是否能确保材料/零部件在流转过程中不发生混合/弄错? 哪些岗位为过程提供支持?(人力资源) 员工是否能从事安排的工作? 员工是否了解监视产品和过程质量的职责与权限? 是否有必要的人力资源? 使用哪些手段执行过程?(物质资源) 是否能够利用生产设备满足顾客对产品的具体要求? 生产设备和工具的维护保养是否受控? 是否能利用监视和测量设备对质量要求进行有效的监控? 生产和检验工位是否满足需求? 是否正确地存放工具、装置和检验设备? 过程落实的效果如何?(效果、效率、避免浪费) 针对制造过程是否设定了目标? 是否对质量和过程数据开展了收集和分析? 一旦与产品和过程要求不符,是否分析了原因,并且验证了纠正措施的有效性? 是否对过程和产品定期开展审核? 过程应产生什么?过程结果(输出) 是否根据需要确定产量/生产批量,并且有目的地运往下道工序?
是否根据要求对产品/零部件进行适当仓储,所使用的运输设备/包装设备是否与产品/零部件 的特殊特性相适应?
是否保持了必要的记录和放行? 最终产品交付时是否满足顾客的要求?
审核日期
审核结果
判定 符合 不符合 观察
部门
产品类别
制造过程
序号
审核容
1 1.1 1.2 1.3 1.4 1.5
2 2.1 2.2 2.3 2..4 2.5
3 3.1 3.2 3.3
4 4.1 4.2 4.3 4.4 4.5
5 5.1 5.2 5.3 5.4
6 6.1
6.2
6.3 6.4
过程输入是什么?(过程输入) 是否在开发和批量生产之间进行了项目交接,以确保生产顺利启动? 来料是否在约定的时间按所需数量/生产批次大小被送至正确的存放位置/工位? 是否对来料进行了适当的仓储,所使用的运输工具/包装设备是否适合来料的特殊特性? 来料是否具备必要的标识/记录/放行,并且得以适当地体现? 是否对在量产过程中的产品或过程变更开展了跟踪和记录? 所有生产过程是否受控?(过程管理) 控制计划的要求是否完整并得到有效落实? 是否进行了生产启动的重复性放行? 是否对生产中的特殊特性进行了管理? 是否对未放行和/或缺陷零件进行了管理? 是否能确保材料/零部件在流转过程中不发生混合/弄错? 哪些岗位为过程提供支持?(人力资源) 员工是否能从事安排的工作? 员工是否了解监视产品和过程质量的职责与权限? 是否有必要的人力资源? 使用哪些手段执行过程?(物质资源) 是否能够利用生产设备满足顾客对产品的具体要求? 生产设备和工具的维护保养是否受控? 是否能利用监视和测量设备对质量要求进行有效的监控? 生产和检验工位是否满足需求? 是否正确地存放工具、装置和检验设备? 过程落实的效果如何?(效果、效率、避免浪费) 针对制造过程是否设定了目标? 是否对质量和过程数据开展了收集和分析? 一旦与产品和过程要求不符,是否分析了原因,并且验证了纠正措施的有效性? 是否对过程和产品定期开展审核? 过程应产生什么?过程结果(输出) 是否根据需要确定产量/生产批量,并且有目的地运往下道工序?
是否根据要求对产品/零部件进行适当仓储,所使用的运输设备/包装设备是否与产品/零部件 的特殊特性相适应?
是否保持了必要的记录和放行? 最终产品交付时是否满足顾客的要求?
审核日期
审核结果
判定 符合 不符合 观察