制造过程过程审核检查表
制造过程审核检查表

4
1、文件与工装、刀具、模具、检具其中任意 一项未符合最终版本各扣1分。
3
1、包装方案未按照和客户达成一致的包装方 案扣3分。
1、包装上未有客户标识扣1分。
4
2、包装上未有产品名称标识扣1分。 3、包装上未有产品零件号扣1分。
4、包装上未有产品数量标识扣1分。
3
1、无安全库存资料扣2分。 2、安全库存资料不完善扣1分。
1、物料未按要求区域划分待检区、合格区、
不合格区或划分不合理扣1分。
5
2、划分标识不明确扣1分。 3、每批次产品无编码标识扣1分。
4、每批次产品无厂家标识扣1分。
5、每批产品无炉批号扣1分。
第 1 页,共 4 页
文件编号: OK
检具精度能否满足要求,检具 3 得到了有效的验证,检测,
并有有效期标签
4
库存管理程序,来料的安全库 存
三: 生产工位 按照控制计划审核生产过
1 程,设备参数与文件一致
2 产出产品的追溯方案
3 RPN的改进
偶发事件的应急方案,人 4 员,设备,备用工装,检
具,刀具,模具 关键特性是否都在控制方式 5 之内
明确的产品状态及分析报
6
告,红盒子,黄盒子,绿盒 子及调机品,首末件,存储
2
1分。 2、控制计划版本与版本记录不相符不正确扣
1分
1、无工装夹具扣2分。
8
2、工装夹具与清单不相符扣2分。 3、过程责任者不明确扣2分。
4、过程责任者未经培训考核就上岗扣2分
1、未采用SPC统计过程控制扣2分。
5
2、未采用防错过程控制扣2分.
3、未采用全检的控制方式扣1分
5
1、来料未按要求进行检验扣3分。 2、未有检验报告扣2分。
制造过程工序审核检查表

要求等是否清楚,查岗
位能力确认表
操作人员是否进行产品首检、
2 自检?是否严格按作业指导书
要求规范操作?
3.班长、机修、检验人员的岗
3
位职责是否清楚?检验人员运 用统计技术能力?对计量仪表
器具的使用方法和掌握程度?
人员是否充足,有无定额要
4 求?有无顶岗计划?顶岗人员
是否培训?
2.2设备 工装
1
设备、仪表是否按规定要求进 行日常点检?(操作人员)
有环保意识?
3
产品性能检测环境条件和贮存 条件是否满足规定要求?
工序巡检员是否严格按检验文 1 件进行首检、巡检和工艺纪律
执行情况检查,并认真做好记
2
工艺特性参数监控人员/作业 员是否进行了监测并有记录?
检验人员发现工艺参数偏离或
3
产品要求偏离,是否立即通知 操作者纠正?(抽查相应证
据 发) 现不合格品是否按规定进行
4
标识、隔离、评审、处置,重 大质量问题是否立即报告?
(提供8D报告证据)
抽查流传单、作业记录、首检
1
、巡检和工艺纪律检查记录是 否清晰,填写内容完整,数据
准 检确 查, 现可 场实 统现 计追 数溯 据?和统计图表
2
、不良分析和纠正预防措施及 验证资料使用和管理是否适
当?
3
记录是否定期整理、标识,归 入资料库保存,便于查询?
4
是否按规定的保存期限和规定 的程序办理销毁手续?
备 注 : OK 符 合 规 定 要 求 , 合 格 , 记 1 分 ; NC 不 符 合 规 定 要 求 ,
具 体 可 另 附 过 程 审 核 记 录 纸 进 行 说 明 。 NC 项 需 开 列 “ 内 审 不 符 合
过程审核检查表(SMT-MI)(经典)

�握掌否是员业作�照对何如 楚清识标型机应对、号型 �录记无有上表录记收验�量测何如 �告报、书格规商应供无有 �踪跟何如�准标楚清否是员业作 06~54 O 钢锈不 次0001<
19 09 98 88 具 78 治/具工 刀刮 68 58 48 38 网钢 28 18 08 97 87 77 67 57 47 刷印 膏锡 80
94 84 箱烤
)外除板废的叉打(纸胶缠再 式 纸白净洁垫先面两下上叠每 方绑捆的BCP叠层 距间叠层 度厚叠层 间时烤烘 度温烤烘 度湿境环区该 型类料辅
74
44
出 64 领/备 54 准料 物线 产生
60
34 24 14 04 93
�盾矛的足不间空箱烤理处何如�时大量 mc01≥ 产生�标超否是际实�准标应相楚清否是员业作 �类CI�mc5�3�BCP 层01≤�类CI�)下 �标 以mm1()片大(片05≤�)上 超否是度厚放叠际实�准标应相楚清否是员业作 以mm1()片大(片52≤�BCP �踪跟无有�准标应相楚清否是员业作 求要件器元体具照按 �录记无有 求要件器元体具照按 �标超否是度温际实�准标应相楚清否是员业作 �踪跟及析分因原 HR%07�%04 无有时标超�标超否是度湿际实�录记无有度湿 � 致一》 用利效有和楚清否是员业作�表照对有否是场现 表照对用使、号型料辅《与
。态状识标/类分的料物场现查抽 晰 度显明 �则原或法方识标/类分的料物楚清否是员业作 清识标类分料装包原、料散 识标、类分的料物 �向反否是件器向有的内带装包查抽 向反无向方料物的内带装包 向 方料物的内带装包 装包料物
号型格规料物
83
量数料物 度感敏DSM
73 63
痕折个5过超不时scp005≥ �品格合不理处、制控何如 �痕折个2 �准标该楚清否是员业作场现 过超不时scp005≤�数痕折 名签上盘料在并,片 。名签否是盘料应对查抽�误无格规料物用所 1对核、量测盘每阻电/容电 证保以�对核/配匹何如间之件文与格规料物、2 片贴的印丝无面表有所、2 �性确正其证保以�对核/配匹何如间之们它 �致一NCE/MOB/单 �件文些这有否是员理管问询、1 料套与、对核、1 �性确正其证保以�对核/配匹何如间 致 之件文与量数料物�件文些这有否是员理管问询 一NCE/MOB/单料套与、对核 。效有DSM证保以 �控监行进间时和度湿的露暴其对否是�过超若 %02≤值示指签标敏潮 �%02过超否是值示指的CI的装包坏损 �性确正件文证保以�对核/配匹何如间之们它 �件文些这有否是员理管问询 全齐 全齐 法办制控DSE合符
制造过程审核检查表
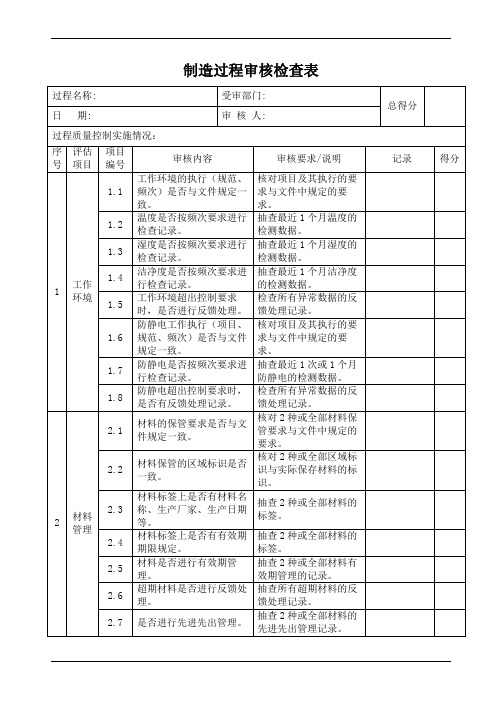
设备状态标识是否正确。
核对3台设备的状态标识。
4.4
是否制定年度PM工作计划。
检查年度PM工作计划。
4.5
是否按照年度PM工作计划实施。
抽查3个项目确认实施情况。
4.6
关键设备的备件是否进行可得性分析。
抽查最近2个月设备可得性分析记录表。
4.7
是否对关键设备的停机原因进行分析并改善。
抽查最近2个月关键设备故障停机原因分析及改善记录表。
4.8
设备故障维修后是否进行记录。
抽查最近2个月设备维修的记录。
4.9
设备维修后是否进行QC验证。
抽查最近2个月设备维修后的QC记录。
5
工装管理
5.1
是否有工装保管台账。
检查工装保管台账。
5.2
是否按工装文件的规定进行管理。
抽查2个工装核对其实施情况与文件规定的要求。
6
量测管理
6.1
是否有量测设备的管理台账。
检查没有达成质量目标的分析改进措施。
7.13
Cpk、Ppk是否满足要求。
检查工序的过程能力分析指数Cpk、Ppk值。
7.14
过程能力(Cpk、Ppk)不满足要求时,是否进行分析改进。
检查过程能力分析改进的相关措施。
7.15
关键参数是否按要求进行SPC管控。
检查要求SPC管控的管控图。
7.16
超出规范限或控制限后是否进行处置。
核对5项CP文件与作业指导书的内容。
7.3
设备中的工艺参数是否与文件中的规定一致。
抽查3台设备核对当前程序的工艺参数与文件规定的要求。
7.4
记录表中监控要求是否与作业指导书要求一致。
制造过程检查表

制造过程检查表制造过程审核检查表被审核的制造过程:审核员/日期:审核项目涉及的标准条款审核内容审核中的观察和证据记录判**果备注P-FEMEA及控制计划7.3.2.37.3.3.27.5.1.11.是否有识别产品和过程的特殊特性?这些特殊特性的制定,形成文件和控制方面是否符合顾客的要求?2.是否建立产品的过程流程图?流程图与实际的作业过程是否一致?3.P-FMEA中是否包含了过程流程图中的全部作业步骤?4.P-FMEA所确定采取的措施是否被列入到控制计划或作业指导书中?5.是否有试生产和生产的控制计划?控制计划是否包含了对所有特殊特性的控制方法?6.控制计划是否包含了顾客要求信息?7.当任何影响产品、制造过程、测量、供货来源或FMEA的更改发生时,是否更新了控制计划?8.是否为所有负责过程操作的人员提供了文件化的作业指导书?9.这些作业指导书是否在操作这得工作岗位并易于得到?人员素质/能力6.2.1?6.2.2.26.2.2.36.2.2.41.对于新上岗和调整岗位的人员是否进行了岗位培训,并具备了从事岗位工作所需的能力?2.所有操作人员是否具备了相应的资格和能力?特殊岗位人员是否进行了资格鉴定?3.员工是否了解所从事工作的相关性和重要性?是否知道不符合质量要求会给顾客带来怎养的后果?4.员工是否了解本部门的质量目标,以及如何为实现质量目标做出贡献?5.员工是否明确工作职责,是否知道如何清楚的与上下工序沟通各种情况?6.当发生质量异常时,员工是否知道如何反馈给现场管理者?7.是否有效地使用了提高员工工作积极性的方法?生产设备/工装管理7.5.1.47.5.1.51.是否有建立机器/设备的预防性与预见性维护计划?并按计划执行日常保养和定期保养活动,是否有维护记录?2.设备出现异常时现场如何处理?3.是否建立关键生产设备的零配件清单?并在需要时可以得到?4.生产设备/工装模具是否能满足产品特定的质量要求?5.在批量生产中使用的检测、试验设备是否能有效的监控质量要求?6.设备、工装、量具的储存和防护是否有规定的要求、并按其执行?7.是否建立易损工装的更换?8.工装的使用、存放、标识和维护是否有规定要求,并按其执行?9.是否有工装的设计图纸或文件?设计图纸/文件与实际工装是否相符合?7.5.1????????7.5.1.38.2.3.18.2.41.生产前应作哪些生产准备?这些准备是否能充分满足生产的要求?2.生产的安排和布置是否符合工艺流程或流程图的规定?3.是否有执行首件确认并有相应记录?4.有关过程参数的设定是否符合作业指导书或控制计划的规定?关键参数的设定是否有做记录?5.生产中的各作业步骤是否按控制计划的要求执行相应的控制?6.控制计划中要求用控制图控制的特殊特性是否有收集数据并绘制相应的控制图?7.当控制图显示过程不稳定时,是否进行了分析和采取了什么措施来改进?8.是否有做生产能力分析?当生产能力不满足≥1.33或顾客的要求时,是如何处置的?9.是否有按控制计划安排执行生产检验并有记录?10.当生产异常时是否启动控制计划中的反映计划?11.生产中的物料、半成品、成品、合格品、不合格品等是否按规定的要求标识清楚?12.当生产中的工作环境条件有规定要求时,是否按规定要求实施控制?不合格品控制8.3????8.3.2????????8.3.41.当生产中发生不合格时是如何处理的?如何将不合格及时通知给负有纠正措施的管理者?是否有处理结果的记录?2.是否有返工作业指导书?这些作业指导书是否易于被适当的人员得到并使用?3.当产品或制造过程与当前批准的不同,在继续生产之前,是否获得顾客的让步或偏离许可?4.返工半成品、成品是否经过重新检验合格**转入下工序或出货?包装与搬运7.5.51.产品包装是否按照包装规范的要求进行包装?2.产品的包装是否符合顾客的要求,并能确保对产品的防护?3.产品的搬运和转移是否能确保不混批、不混料并保证可追溯性?4.是否有规定搬运的工具和方法?这些方法是否确保物料/产品不被跌落或损坏?纠正与预防措施8.5.2?8.5.2.28.5.2.3?8.5.31.当外部发生异常或顾客投诉,是否将相关信息通知到生产部门?生产部门是否针对异常原因进行了分析,采取了什么措施?是否验证措施的有效性?2.纠正措施是否应用了防错方法?3.是否将纠正措施和实施的控制应用与其他类似的过程和产品?4.当内部和外部发生异常时,是否有评审P-FMEA和控制计划?是否有作适当的更新?5.当数据分析或控制图显示有潜在异常的趋势时,是否有采取预防措施以防不合格的发生?数据分析和目标业绩8.41.是否有根据生产的目标和衡量指标定期统计和分析?2.当数据显示目标或指标未达成时,采取了哪些改进措施?持续改进8.5.1.21.当制造过程有能力且稳定或当产品特性可预测且满足顾客要求时,是否有考虑持续改进的措施?2.当数据显示目标或指标未达成时,是否有作进一步的提升?备注:要求程度的打分依据分数对符合要求程度的评定10完全符合8绝大部分符合,只有微小的偏差6部分符合,有较大的偏差4小部分符合,有严重的偏差0完全不符合。
VDA6.3 最新2016版过程审核检查表
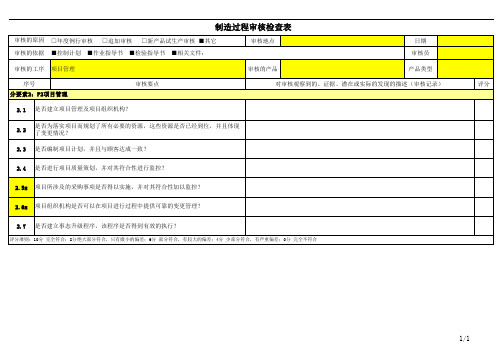
审核的原因 □年度例行审核 □追加审核 □新产品试生产审核 ■其它
审核地点
审核的依据 ■控制计划 ■作业指导书 ■检验指导书 ■相关文件:
日期 审核员
审核的工序 项目管理
序号 分要素2:P2项目管理
审核要点
审核的产品
产品类型
对审核观察到的、证据、潜在或实际的发现的描述(审核记录)
2.1 是否建立项目管理及项目组织机构?
Hale Waihona Puke 2.2是否为落实项目而规划了所有必要的资源,这些资源是否已经到位,并且体现 了变更情况?
2.3 是否编制项目计划,并且与顾客达成一致?
2.4 是否进行项目质量策划,并对其符合性进行监控?
2.5x 项目所涉及的采购事项是否得以实施,并对其符合性加以监控?
2.6x 项目组织机构是否可以在项目进行过程中提供可靠的变更管理?
2.7 是否建立事态升级程序,该程序是否得到有效的执行?
评分准则:10分 完全符合;8分绝大部分符合,只有微小的偏差;6分 部分符合,有较大的偏差;4分 少部分符合,有严重偏差;0分 完全不符合
评分
1/1
过程审核检查表
7、该工序有否其他管理性文件?其控制是否为现行有效?
8、调查该工序操作人员(和检验人员)对控制计划相关控制内容是否了解、清楚?对相关作业指导书(或检验指导书)及其他管理性文件的内容是否理解并掌握?
9、观察工序操作人员(和检验人员)对该工序操作及检验的执行情况,并听取其意见和要求。
3、控制计划中对该工序质量要素的控制是否明确、是否正确?
4、在该工序能否发现有效的控制计划版本?
5、与控制计划相对应的相关作业指导书是否可在该工序获得?作业指导书是否为现行有效版本?
6.对于该工序的质量控制要求,相关作业指导书与控制计划的
规定是否一致,有否存在矛盾的情况?
规定是否一致,有否存在矛盾的情况?
10、根据上述活动,评价质量控制计划是否可行与正确,评价工序操作人员对质量控制要求的理解与执行程度,并得出是否能够满足生产要求的结论。
序号
审核项目
审核内容
实施记录
判定
2
工序因素的受控情况
1.在该工序质量控制计划中规定了哪些方面的控制要求?(有
无特殊特性的要求?)
无特殊特性的要求?)
2.在实际作业中,各工序要素的控制是否达到了工序质量控制
文件的要求?(通过现场核对、调查,作出分析和评价)
文件的要求?(通过现场核对、调查,作出分析和评价)
文件的要求?(通过现场核对、调查,作出分析和评价)
3.现场调查和评价该工序所涉及的人、机、料、法、环、测等诸因素,特别是该工序的主导因素是否达到了工序质量控制文件的要求(如关于人员的培训及岗位要求、设备的点检及维护保养、物料的控制、环境的维持、记录的获取、检验和试验的进行、产品的追溯等方面)
审核时,尤其应注意对工序中的特殊特性的控制
IATF16949过程审核检查表
2.1生产设备/工装模具是否能保证满足产品特定的质量要求? 2.2在批量生产中使用的检测、试验设备是否能有效地监控质量要求? 2.3生产工位、检验工位是否符合要求? 2.4生产文件和检验文件中是否标出所有的重要技术要求并坚持执行? 2.5对产品调整/更换是否有必备的辅助器具? 2.6是否进行批量生产起始认可,并记录调整参数及偏差情况? 2.7要求的纠正措施是否按时落实并检查其有效性? 3 运输/搬运/贮存/包装
4.1是否完整地记录质量数据/过程数据,并具有可评定性? 4.2是否用统计技术分析质量数据/过程数据,并由此制订改进措施? 4.3在与产品要求/过程要求有偏差时,是否分析原因并检查纠正措施的 有效性? 4.4对过程和产品是否定期进行审核? 4.5对产品和过程是否进行持续改进? 4.6对产品和过程是否有确定的目标值,并监控是否达到目标? 补充说明:
3.1产品数量/生产批次的大小是否按需求而定?是否有目的地运往下道 工序? 3.2产品/零件是否按要求贮存?运输器具/包装方法是否按产品/零件的 特性而定? 3.3废品、返修件和调整件以及车间内的剩余料是否坚持分别贮存并标 识? 3.4整个物流是否能确保不混批、不混料并保证可追溯性? 3.5模具/工具,工装,检验、测量和试验设备是否按要求存放? 4 缺陷分析/纠正措施/持续改进(KVP)
过程审核检查表
(供审核制造过程用)
审核工序:
审核员: 审核项目
审核日期: 得分 审核发现的问题
1
人员/素质
ቤተ መጻሕፍቲ ባይዱ
1.1是否对员工委以监控产品质量/过程质量的职责和权限? 1.2是否对员工委以负责生产设备/生产环境的职责和权限? 1.3员工是否适合于完成所交付的任务并保持其素质? 1.4是否有包括顶岗规定的人员配置计划? 1.5是否有效地使用了提高员工工作积极性的方法? 2 生产设备/工装
IATF16949制造过程内部审核检查表
内 部 审 核 检 查 表
工程变更管理
程序
生产管制程序生产计划控制
程序
118.6.2
128.6.3 139.1.1.1 组织生产的零部件是否被顾客指定为“外观项目”如果是组织是否提供了1.适当的资源,2.适当的颜色,文理,金属亮度,组织结构,映像清晰度的触感技术的标准样件,3.外观标准样品及评价设备的维护和控制,4.对从事外观评价人员的能力和资格的验证
是否对制造过程进行了监视和测量?是否采用统计过程控制方法对特殊特性工序进行了监控,并保持过程能力负荷生产件批准时的要求?是否出现过程能力不足或不受控的情况?如出现是否启动反应计划?是否制定了纠正措施计划并实施验证?
组织是否按照控制计划中的规定,根据顾客的工程材料和性能标准,对每一种产品进行全尺寸检验和功能性验证,其结果可供顾客评审。
制造过程审核检查表
得分
审核情况描述
不符合项目编号
1/4
20160304 ZTQR01092 AO
制造过程审核检查表
审核员: 日期: 审核过程: 陪同人员:
1、评分标准:10分---完全符合要偏差严重; 2、实际审核过程中对每一项要进行审核证据的描述;
得分
审核情况描述
不符合项目编号
2/4
20160304 ZTQR01092 AO
制造过程审核检查表
审核员: 日期: 审核过程: 陪同人员:
1、评分标准:10分---完全符合要求,不存在偏差; 4分----少部分符合要求,偏差严重; 2、实际审核过程中对每一项要进行审核证据的描述;
序号 35 36 37 38 39 40 41 42 43 44 45 46 47 48 49 50 51 不合格分析、 纠正措施、持 续改进 生产设备、 工装 测量 审核项目
8分---绝大部分符合要求,有少量偏差; 6分---部分符合要求,有较大偏差; 0分---完全不符合要求; NA---不涉及
审核项目 审核内容 不合格分析、 纠正措施、持 返工产品是否经过重新检验合格后才转入下工序或出货? 续改进 当发生顾客投诉时是否将相关信息传达到制造部门? 是否针对异常原因进行了分析?采取了什么措施?是否有效? 过程中所产生相关记录是否齐全?字迹是否清楚,真实? 是否有存在随意涂改现象? 相关记录是否按文件要求进行保管标识?
得分
审核情况描述
不符合项目编号
物料:运输/搬 产品/零件,运输器具/包装方法合理,不会造成产品的倒塌、损坏、锈蚀等; 运/贮存/包装 产品的包装是否符合顾客的要求? 不良品是否有明确的存放地点,标识清楚; 当制程发生不合格时是如何处置的?是否有处理结果的记录? 是否有返工作业指导书,这些指导书是否易于被适当的人员得到并使用?
- 1、下载文档前请自行甄别文档内容的完整性,平台不提供额外的编辑、内容补充、找答案等附加服务。
- 2、"仅部分预览"的文档,不可在线预览部分如存在完整性等问题,可反馈申请退款(可完整预览的文档不适用该条件!)。
- 3、如文档侵犯您的权益,请联系客服反馈,我们会尽快为您处理(人工客服工作时间:9:00-18:30)。
检查工艺卡或监控计划中的检测设备齐全。
6
检测设备准确度符合质量特性的检测要求。
7
检测设备在校准有效期内。
8
检测设备失效时,对检测结果进行了有效性评价。
9
按规定的项目和频次检验。
10
检查记录和控制图按规定项目和频次得到记录。
11
特殊工序的参数得到连续的监控。
12
对不合格品进行了追溯。
13
记录的不合格品得到了处理。
四.环境因素
1
通道、地面、工位设施的布置符合要求。
2
工装设备、零件及材料进行了定置管理。
3
不同型号和状态的零部件进行了标识和隔离。
4
环境温度、湿度、清洁度、光照度符合要求。
5
防止磕碰、划伤及锈蚀的措施有效。
五.材料因素
1
上线的材料及辅料经检验和试验合格。
2
避免了材料及辅料混漏的可能。
制造过程确认检查表(续)
10
能鉴别产品的缺陷或发现异常。
11
按要求进行标识和记录。
二.方法因素
1
生产工艺文件为最新版本。
2
操作说明能保证工人在操作中不会造成质量问题。
3
确定了追溯性原则并遵照执行。
4
质量信息传递方式已确定并渠道畅通。
5
不合格品的程序已制定并遵照执行。
6
周转卡符合要求。
三.设备因素
1
工艺卡规定的工装设备齐全。
序号
符 号
说 明
扣分值
1
NC
本工序不适用,可以不查。
2
S
满意,达到要求,合格。
0
3
A
可接受,质量风险不大,待改进。
1
4
NS
不满意,不可以接受存在较大的质量风险。
2
5
R
不存在,没有措施,风险大。
3
2
设备的编码和标记齐全。
3
工装设备进行了规范的调试和检定。
4
工具更换的频次已说明并得到遵守。
5
设备工具及切削液在使用中不会造成质量问题。
6
工装设备损坏产品的危险得到了控制。
7
工装设备的预防性维护已制定措施并遵照执行。
8
工装设备的故障修复已制定措施并遵照执行。
9
防错系统已运行。
10
工装、模具维修后经过验证。
序号
检 查 内 容
检查结果
NC
S
A
NS
R
3
对上线的材料、辅料或产品进行标识。
4
材料及辅料应在有效期内。
5
紧急放行的产品和材料有明பைடு நூலகம்的标识和记录。
六.检测因素
1
检查工艺卡或监控计划为有效版本。
2
检查记录卡或控制图为有效版本。
3
检查工艺卡或监控计划已明确特性参数的中间值、公差和控制限。
4
首件检查并确认。
制造过程审核检查表
受检查单位:受检查过程名称:
序号
检查内容
检查结果
NC
S
A
NS
R
一.人为因素
1
数量满足要求。
2
了解生产和质量的目标和指标。
3
经过单位培训合格。
4
通过资格评定并持有上岗证。
5
熟悉工艺要求及操作要领。
6
严格执行操作规程。
7
熟悉设备保养内容。
8
熟悉检测内容及频次。
9
熟悉使用检测设备或工具。
14
工序能力达到了要求。
小计
总计
总平均得分值:Tq=〔(2×审核项目数-扣分值)/(2×审核项目数)〕×100%
=
结论:
审核员:年月日
审核组长:年月日
批准:年月日
说明:
1.总平均得分值Tq:大于或等于90%为过程控制目标。当低于该目标、审核结果远小于以前的结果或出现趋势下降时。应采取必要的有效措施。