汽车前后防撞梁设计规范
前后防撞梁和
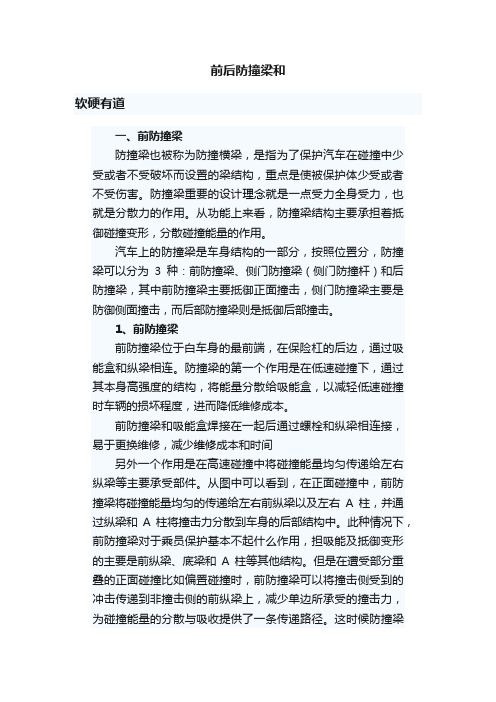
前后防撞梁和软硬有道一、前防撞梁防撞梁也被称为防撞横梁,是指为了保护汽车在碰撞中少受或者不受破坏而设置的梁结构,重点是使被保护体少受或者不受伤害。
防撞梁重要的设计理念就是一点受力全身受力,也就是分散力的作用。
从功能上来看,防撞梁结构主要承担着抵御碰撞变形,分散碰撞能量的作用。
汽车上的防撞梁是车身结构的一部分,按照位置分,防撞梁可以分为3种:前防撞梁、侧门防撞梁(侧门防撞杆)和后防撞梁,其中前防撞梁主要抵御正面撞击,侧门防撞梁主要是防御侧面撞击,而后部防撞梁则是抵御后部撞击。
1、前防撞梁前防撞梁位于白车身的最前端,在保险杠的后边,通过吸能盒和纵梁相连。
防撞梁的第一个作用是在低速碰撞下,通过其本身高强度的结构,将能量分散给吸能盒,以减轻低速碰撞时车辆的损坏程度,进而降低维修成本。
前防撞梁和吸能盒焊接在一起后通过螺栓和纵梁相连接,易于更换维修,减少维修成本和时间另外一个作用是在高速碰撞中将碰撞能量均匀传递给左右纵梁等主要承受部件。
从图中可以看到,在正面碰撞中,前防撞梁将碰撞能量均匀的传递给左右前纵梁以及左右A柱,并通过纵梁和A柱将撞击力分散到车身的后部结构中。
此种情况下,前防撞梁对于乘员保护基本不起什么作用,担吸能及抵御变形的主要是前纵梁、底梁和A柱等其他结构。
但是在遭受部分重叠的正面碰撞比如偏置碰撞时,前防撞梁可以将撞击侧受到的冲击传递到非撞击侧的前纵梁上,减少单边所承受的撞击力,为碰撞能量的分散与吸收提供了一条传递路径。
这时候防撞梁才能起到真正的作用。
碰撞时撞击力经过防撞梁的分解作用后的传递路线前防撞梁强度太弱,导致防撞梁内凹,发动机严重受损,而和防撞梁想连接的吸能盒则却安然无恙,防撞梁失去应有作用从以上可以知道,在碰撞过程中前防撞梁不能发生断裂失效,否则就不能在关键时刻起到传递和分解力的作用,所以防撞梁本身应该具有极高的强度。
而影响其强度的有材料、结构和尺寸三个方面。
对于汽车防撞梁而言,现在主要有三种材料:高强度钢材、玻璃纤维和铝合金等轻金属合金。
汽车前后防撞梁设计地的要求的要求规范
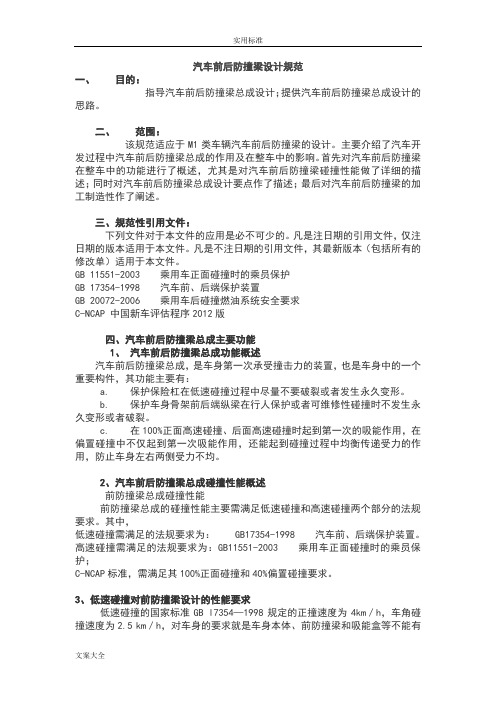
汽车前后防撞梁设计规范一、目的:指导汽车前后防撞梁总成设计;提供汽车前后防撞梁总成设计的思路。
二、范围:该规范适应于M1类车辆汽车前后防撞梁的设计。
主要介绍了汽车开发过程中汽车前后防撞梁总成的作用及在整车中的影响。
首先对汽车前后防撞梁在整车中的功能进行了概述,尤其是对汽车前后防撞梁碰撞性能做了详细的描述;同时对汽车前后防撞梁总成设计要点作了描述;最后对汽车前后防撞梁的加工制造性作了阐述。
三、规范性引用文件:下列文件对于本文件的应用是必不可少的。
凡是注日期的引用文件,仅注日期的版本适用于本文件。
凡是不注日期的引用文件,其最新版本(包括所有的修改单)适用于本文件。
GB 11551-2003 乘用车正面碰撞时的乘员保护GB 17354-1998 汽车前、后端保护装置GB 20072-2006 乘用车后碰撞燃油系统安全要求C-NCAP 中国新车评估程序2012版四、汽车前后防撞梁总成主要功能1、汽车前后防撞梁总成功能概述汽车前后防撞梁总成,是车身第一次承受撞击力的装置,也是车身中的一个重要构件,其功能主要有:a. 保护保险杠在低速碰撞过程中尽量不要破裂或者发生永久变形。
b. 保护车身骨架前后端纵梁在行人保护或者可维修性碰撞时不发生永久变形或者破裂。
c. 在100%正面高速碰撞、后面高速碰撞时起到第一次的吸能作用,在偏置碰撞中不仅起到第一次吸能作用,还能起到碰撞过程中均衡传递受力的作用,防止车身左右两侧受力不均。
2、汽车前后防撞梁总成碰撞性能概述前防撞梁总成碰撞性能前防撞梁总成的碰撞性能主要需满足低速碰撞和高速碰撞两个部分的法规要求。
其中,低速碰撞需满足的法规要求为:GB17354-1998 汽车前、后端保护装置。
高速碰撞需满足的法规要求为:GB11551-2003 乘用车正面碰撞时的乘员保护;C-NCAP标准,需满足其100%正面碰撞和40%偏置碰撞要求。
3、低速碰撞对前防撞梁设计的性能要求低速碰撞的国家标准GB l7354—1998规定的正撞速度为4km/h,车角碰撞速度为2.5 km/h,对车身的要求就是车身本体、前防撞梁和吸能盒等不能有任何损坏,最好前保险杠也不能破裂或者发生永久变形。
汽车车门防撞防撞梁设计规范
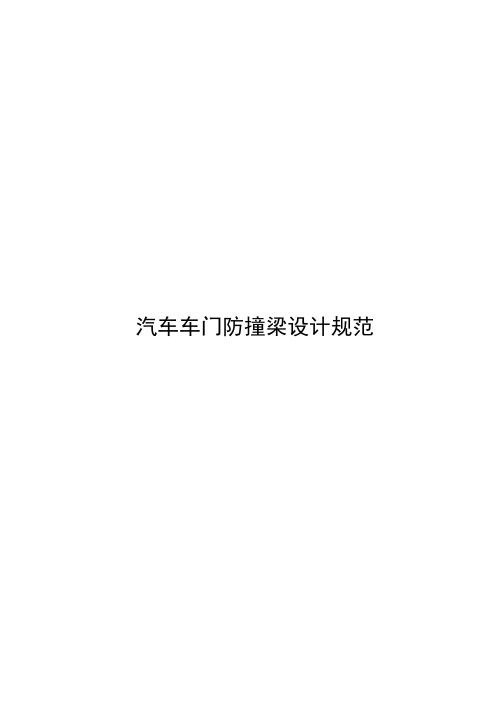
汽车车门防撞梁设计规范汽车车门防撞梁设计规范1 范围本标准规定了汽车车门防撞杆相关设计标准本标准适用于本公司汽车车门防撞杆产品2 规范性引用文件下列文件对于本文件的应用是必不可少的。
凡是注日期的引用文件,仅注日期的版本适用于本文件。
凡是不注日期的引用文件,其最新版本(包括所有的修改单)适用于本文件。
GB/T 10125-1997 人造气氛腐蚀试验盐雾试验GB 20071-2006 汽车侧面碰撞的乘员保护Q/B 05 021-2010 汽车门防撞杆技术规范3 术语和定义3.1防撞梁总成防撞梁总成位于侧门内外板之间,在汽车发生碰撞的时候能够保证车内的生存空间,很好的保证乘员的身体及生命安全。
3.2 MBD可移动可变性障壁3.3 R点车辆制造商规定的基准点,一般式正常行驶时最低、最后位置时,躯干和大腿旋转点的理论位置,或由车辆制造商对于每个乘坐位置给定的位置4 技术要求4.1安全性能要求碰撞过程中起到力的传递及抗冲击作用,减小碰撞过程中变形量,保护乘员生命安全,安全性能方面的要求符合《GB 20071-2006 汽车侧面碰撞的乘员保护》规定的相关要求;4.3 适应于外部环境要求标准数值/ 参考资料耐水性能车辆经过淋雨和涉水行驶后,产品仍然应该保持符合技术任务书要求。
耐腐蚀性能车门侧面防撞加强板应该经受以下试验:程序:按照GB/T 10125-1997的盐雾试验方法进行测试要求的结果:在试验之后, 在公差范围限度内,所有侧面防撞板的安全性功能应该得到保证。
为了确保在6年内外观无"红色锈迹", 在经过480h盐雾试验后,车的可见部分不允许出现红色锈迹和严重的白色锈迹,不管锈迹是来自那里(例如: 从不可见部分流下来的) 。
与加强板相关的螺纹连接在经过240h循环后不应该出现红色锈迹。
防腐涂镀层前车门侧防撞加强杆被固定在对角位置。
位于一个极易腐蚀的区域。
根据防腐标准,如果有水流过钢材的内部,为了保证没有锈液滴出,应该在钢材的每个表面涂镀10 µm的锌(不妨害外观6年的保质期).根据关于带镀层钢板车门侧防撞加强杆的防腐推荐措施,在进行电泳处理时,应该允许在加强杆的每一个表面去除掉8µm的电泳镀层。
关于汽车防撞梁结构设计的相关研究
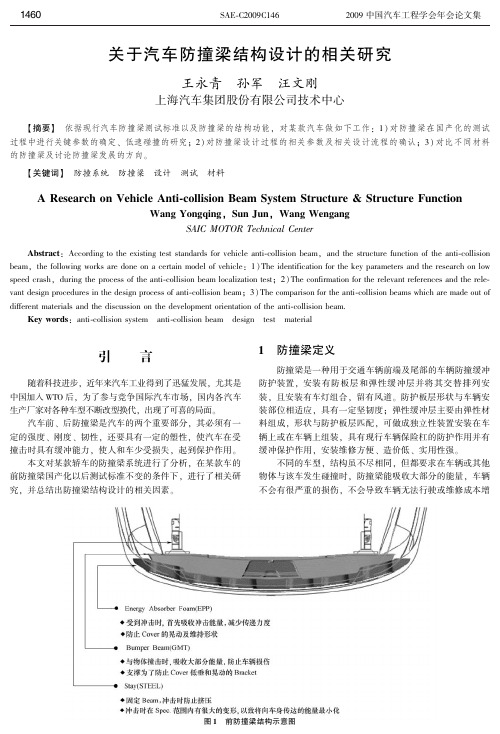
RH CNR 445mm PEND。 试验后 速度: 2郾 54km / h, Force 828 kgf 右角闯入 30mm I 防撞杆无破裂 & 吸能盒摇 轻微破裂
离第一次碰撞 300mm, 高度为 445mm 摆锤位置: 试验前[满载] 摆锤重量: 1120kg(85% )952kg 摆锤重量: 1120kg(400kg UP) 1520kg(85% )1292kg
摇 摇 摇 现以某款车型国产化过程中的产品测试为例, 进行结 果分析。 摇 摇 设计尺寸图见图 4。 摇 摇 检测数据见表 3。 摇 摇 图 5 为检测时照片及结果: 摇 摇 从检测结果可知: 中心闯入量为 114mm, 角碰后零部
表摇 2
FMVSS Part 581 ( 美国标准)
公司要求
速度
中心碰撞 / 障碍物 角碰( 30 毅 )
图摇4表摇2fmvsspart581美国标准公司要求cmvss215加拿大标准europeanr42欧洲标准速度中心碰撞障碍物2郾5mileh5郾0mileh5郾0mileh2郾5mileh角碰30毅1郾5mileh3郾0mileh3郾0mileh2郾5mileh摆锤高度1620in16in装车验证20in装车验证1620in445mm碰撞条件中心碰撞2次1620in2次1620in2次1620in空载1次满载1次大于空载位置300mm角碰2次20in1620in2次20in1620in2次20in1620in空载1次满载1次对面障碍物1次1次1次车身重量摆锤车身重量车身重量包括汽油车身重量摆锤重量为空载重量车身重量
摇 2009 中国汽车工程学会年会论文集
SAE鄄C2009C146
1463
Model ( Type)
重量 / kg
前碰撞横梁总成参考-设计参考

前碰撞横梁总成参考-设计参考目录1.适用范围-----------------------------------------------------------------------------------042.引用标准------------------------------------------------------043.前碰撞横梁的制造工艺-------------------------------------------044.车型结构实例及实车结构尺寸参考---------------------------------055.前碰撞横梁的设计------------------------------------------------226.吸能盒设计------------------------------------------------------247.材料及料厚推荐--------------------------------------------------258.结束语----------------------------------------------------------25前碰撞横梁总成参考-设计参考1 适用范围本规范规定了前碰撞横梁设计的设计流程、材料选取、结构参数以及前碰撞横梁的设计质量检查等内容。
本规范适用于前碰撞横梁的设计开发工作。
2 引用标准标准化工作导则第1部分标准的结构和编写规则。
汽车设计规范、工艺规范、试验规范编制工作指南3前碰撞横梁的制造工艺1.冲焊工艺:冲压焊接工艺适应性强,开发周期短,成本较高,形状多变,不要求断面一致,可以在以后的使用中根据实际状态设变,但性能提高主要靠材料牌号的升级和料厚的增加,其与吸能结构可以点焊连接,后期改动的设变成本低。
如下图:2.辊压成型:辊压成型若是单一车型使用则成本很高,但现在基本上是多个车型共用,多车型共用时,这种结构成本最低,但一般要求断面一致,变断面辊压技术目前尚未投入量产,辊压对大量生产的零件成本极低,但辊压断面一旦确定,调整范围有限,一旦形状改变,只能新开。
汽车前防撞横梁总成设计指南
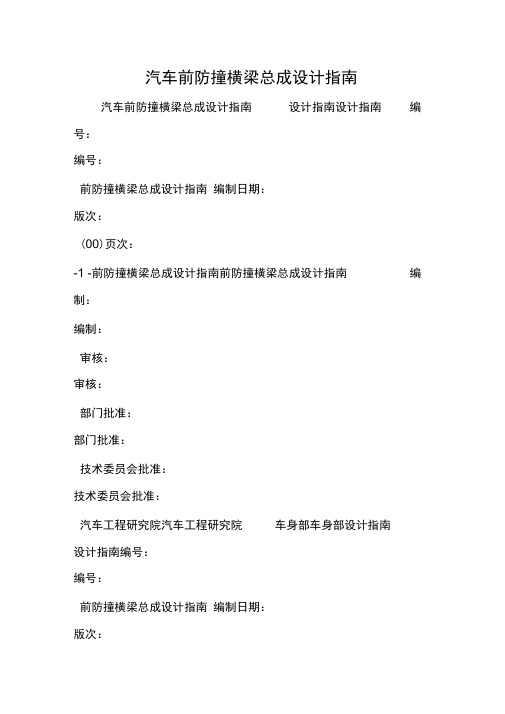
汽车前防撞横梁总成设计指南汽车前防撞横梁总成设计指南设计指南设计指南编号:编号:前防撞横梁总成设计指南编制日期:版次:(00)页次:-1 -前防撞横梁总成设计指南前防撞横梁总成设计指南编制:编制:审核:审核:部门批准:部门批准:技术委员会批准:技术委员会批准:汽车工程研究院汽车工程研究院车身部车身部设计指南设计指南编号:编号:前防撞横梁总成设计指南编制日期:版次:(00)页次:--目目录录第一章概述1 1.1该指南的主要目的1 1.2该指南的主要内容1第二章法规对比分析1 2.1低速碰撞法规要求1 2.1.1政府法规试验规范简介 1 2.1.2保险协会试验规范简介.4 2.2高速碰撞法规要求5第三章前防撞横梁的布置设计6 3.1前防撞横梁离地高度布置要求.6 3.2前防撞横梁距前保蒙皮、发动机盖前缘等部件的距离.9 3.3前防撞横梁长度要求.12第四章前防撞横梁结构设计13 4.1前防撞横梁的安装方式.13 4.2前防撞横梁的工艺分类.14 4.3前防撞横梁的截面型式.16 4.4前防撞横梁的轨迹曲线.19 4.5吸能盒结构设计.20 4.5.1常见吸能盒结构.20 4.5.2特殊吸能盒结构.22 4.6拖车钩结构设计.23第五章前防撞横梁的材料定义及减重24 5.1前防撞横梁材料选用.245.2前防撞横梁减重设计.25第六章前防撞横梁的CAE模拟分析266.1典型截面的CAE对比分析26 6.2前防撞横梁总成碰撞CAE 模拟分析27第七章前防撞横梁的设计趋势30 7.1高强度材料运用.30 7.2保护系统装配集成、前端模块轻量化.30设计指南设计指南编号:编号:前防撞横梁总成设计指南编制日期:版次:(00)页次:-0 -第一章第一章概述概述保险杠系统由保险杠蒙皮、吸能块、防撞横梁及小腿保护梁所组成防撞横梁总成是保险杠系统的重要组成部分,也是车身结构的重要组成部分,它在汽车低速碰撞中起着决定性作用,同时在高速碰撞中也起着吸能和力量传导的重要作用。
汽车前后防撞梁设计要求规范
汽车前后防撞梁设计规一、目的:指导汽车前后防撞梁总成设计;提供汽车前后防撞梁总成设计的思路。
二、围:该规适应于M1类车辆汽车前后防撞梁的设计。
主要介绍了汽车开发过程中汽车前后防撞梁总成的作用及在整车中的影响。
首先对汽车前后防撞梁在整车中的功能进行了概述,尤其是对汽车前后防撞梁碰撞性能做了详细的描述;同时对汽车前后防撞梁总成设计要点作了描述;最后对汽车前后防撞梁的加工制造性作了阐述。
三、规性引用文件:下列文件对于本文件的应用是必不可少的。
凡是注日期的引用文件,仅注日期的版本适用于本文件。
凡是不注日期的引用文件,其最新版本(包括所有的修改单)适用于本文件。
GB 11551-2003 乘用车正面碰撞时的乘员保护GB 17354-1998 汽车前、后端保护装置GB 20072-2006 乘用车后碰撞燃油系统安全要求C-NCAP 中国新车评估程序2012版四、汽车前后防撞梁总成主要功能1、汽车前后防撞梁总成功能概述汽车前后防撞梁总成,是车身第一次承受撞击力的装置,也是车身中的一个重要构件,其功能主要有:a. 保护保险杠在低速碰撞过程中尽量不要破裂或者发生永久变形。
b. 保护车身骨架前后端纵梁在行人保护或者可维修性碰撞时不发生永久变形或者破裂。
c. 在100%正面高速碰撞、后面高速碰撞时起到第一次的吸能作用,在偏置碰撞中不仅起到第一次吸能作用,还能起到碰撞过程中均衡传递受力的作用,防止车身左右两侧受力不均。
2、汽车前后防撞梁总成碰撞性能概述前防撞梁总成碰撞性能前防撞梁总成的碰撞性能主要需满足低速碰撞和高速碰撞两个部分的法规要求。
其中,低速碰撞需满足的法规要求为: GB17354-1998 汽车前、后端保护装置。
高速碰撞需满足的法规要求为:GB11551-2003 乘用车正面碰撞时的乘员保护;C-NCAP标准,需满足其100%正面碰撞和40%偏置碰撞要求。
3、低速碰撞对前防撞梁设计的性能要求低速碰撞的国家标准GB l7354—1998规定的正撞速度为4km/h,车角碰撞速度为2.5 km/h,对车身的要求就是车身本体、前防撞梁和吸能盒等不能有任何损坏,最好前保险杠也不能破裂或者发生永久变形。
后防撞梁设计要求
后防撞梁设计要求#### 引言嘿,朋友!你有没有想过汽车后面那个防撞梁呀?每次开车在路上,虽然我们都希望平平安安的,但意外这个小怪兽说不定啥时候就冒出来了。
防撞梁就像是汽车尾部的小卫士,默默地保护着我们呢。
今天呀,咱们就来唠唠后防撞梁的设计要求,这可不是什么干巴巴的理论,而是实实在在能让汽车更安全、更靠谱的干货。
不管你是汽车爱好者,还是汽车相关行业的小伙伴,相信这些要求都会让你大有收获的。
#### 主要要求**1. 足够的强度和刚度**- 核心点:后防撞梁要能承受一定程度的撞击力,在碰撞时不易变形。
- 为什么重要?咱们开车在路上,要是发生追尾事故,后防撞梁强度不够的话,那可就惨了。
比如说,有数据表明,很多车辆在低速追尾时,如果防撞梁强度差,就可能导致后备箱严重变形,甚至影响到后排乘客的安全空间。
我有个朋友就遇到过这样的事,被轻轻追尾了一下,结果后备箱关不上了,维修还花了不少钱呢。
- 具体怎么做?在材料选择上,要优先考虑高强度钢材或者一些新型的复合材料。
设计结构的时候呢,可以采用加固的梁体结构,像增加横梁的厚度或者采用双层结构。
在连接部位,使用高强度的螺栓或者焊接工艺,确保在撞击时不会轻易断开连接。
- 常见误区或注意事项:有些设计师为了追求轻量化,过度减少防撞梁的材料用量,这是很危险的。
要知道,强度和轻量化得找到一个平衡点。
不能光为了减重就牺牲了防撞梁的主要功能。
如果发现防撞梁在模拟撞击测试中变形过大,那就得重新审视设计方案了。
**2. 合理的吸能设计**- 核心点:让后防撞梁在碰撞时能够有效地吸收能量。
- 为什么重要?你想啊,如果防撞梁不能很好地吸收能量,那撞击的能量就会直接传递到车身其他部位,就像一个硬邦邦的东西直接撞到墙上,墙肯定容易坏。
在实际事故中,不合理的吸能设计可能导致车辆内部结构受损严重。
据调查,那些吸能效果不好的车辆,在碰撞后的维修成本往往更高,因为受损范围更广。
- 具体怎么做?可以采用一些专门的吸能盒结构,吸能盒就像是一个小的能量缓冲区。
汽车铝合金防撞梁总成技术规范标准
铝合金防撞梁总成技术规、本标准适用于本标准适用于XX公司〔以下简称XX公司〕乘用车防撞梁总成〔铝合金〕。
2 参考标准与规性引用文件以下文件对于本文件的引用是必不可少的。
但凡注日期的引用文件,仅所注日期的版本适用于本文件。
但凡不注日期的引用文件,其最新版本〔包括所有的修改单〕适用于本文件。
GB/T 191-2008 包装储运图示标志GB/T 2651-2008 焊接接头拉伸试验方法GB/T 2828.1~GB/T 2828.4计数抽样检验程序GB/T 3323-2005 金属熔化焊焊接接头射线照相GB/T 6892-2006 一般工业用铝与铝合金挤压型材GB/T 6987 铝与铝合金化学分析方法GB/T 16865-2013 变形铝、镁与其合金加工制品拉伸试验用试样与方法GB 17354-1998 汽车前、后端保护装置GB/T 17432-2012 变形铝与铝合金化学成分分析取样方法GB/T 18305-2003质量管理体系汽车生产件与相关维修零件组织应用GB 20072-2006 乘用车后碰撞燃油系统平安要求GB/T 26988-2011汽车部件可回收利用性标识GB/T 30512-2014汽车禁用物质要求77/389/EEC 拖车钩安装点强度试验BAMS-096 汽车产品零部件标识规定3 术语和定义以下术语和定义适用于本文件3.1防撞梁 Rear Bumper Impact Bar发生碰撞时用来保护车辆后部的一种装置,主要作用是将碰撞力有效传递至吸能盒上。
3.2吸能盒 Crash Box用于有效吸收碰撞能量,并将剩余碰撞能量传递至后纵梁,尽可能减小撞击力对车身与乘员的伤害。
3.3安装板 Support Panel将后防撞梁与车身进展连接,起到安装固定后防撞梁总成的作用。
3.4拖车钩 rear tow hock汽车的一种牵引装置,主要作用是在汽车被牵引时提供安装点。
4 技术要求4.1 外观要求总成〔钢板〕的所有零件无裂纹、开焊、腐蚀斑点缺陷;阻碍装配、功能或平安操作的毛刺;4.2 性能要求防撞梁总成〔铝合金〕采用熔焊时,焊缝数量、位置、尺寸应符合产品图样规定,外露焊缝应打磨平整,毛刺应清理干净,并应满足以下要求:拖车钩安装点的强度要求,按5.5条规定的试验方案,试验结果应符合产品图纸的相应规定。
整车碰撞安全设计建议
330mm 200mm
空载地面线
L
建议: 前纵梁上端到空载地面线 的高度小于570mm。
后端腔体 较前端相 比太粗壮。
2)前纵梁截面及形状要求
Z方向凸起太高 ,腔体截面相对 前后急剧变小
期望的纵梁结构形式 红线围城的区域
腔体截面大小保持一致
前防撞横梁
1、断面问题: 参考车防撞横梁抗弯能力弱,建议换成辊压 结构。 2、防撞横梁长度不够,前碰撞纵梁易弯。
整车碰撞安全设计建议
说明: 如下要求主要针对在分析计算遇到的问题以及结合自身经验所 提出的建议,希望在前期设计阶段能够规避掉,其中达到碰撞安全 要求的一些技术参数不再体现(例如前碰空间等等)。
目录 一、前碰撞 二、侧面碰撞 三、行人保护-小腿撞击区域空间要求 四、总布置要求及其他设计要求
一、前碰撞 1)前纵梁离地高度
三、行人保护-小腿撞击区域空间要求
小腿撞击区域
小腿碰撞区域最小距离L=24.8mm,小于理论计算的37.0mm,更达不到工程 经验要求的60mm。
1、调整总布置、使得小腿碰撞区域空间达到60mm以上; 2、细化造型、缩小小腿碰撞区域,从而规避小腿碰撞未达到60mm的区域。
3)总布置要求及其他设计要求
发动机托架
存在问题:前碰撞中,发动机挤压发动机托板,造成加速度偏大。 建议:局部优化发动机托板结构。
二、侧面碰撞
后座椅前横梁
存在问题:侧碰时该区域薄弱,易变形。 建议:按虚线趋势优化横梁结构。
B柱结构
存在问题:B柱加强件结构零散,材料牌号低,碰撞易变 形。 建议:完整设计铰链加强件,强化B柱结构。
B柱内饰缺口未 能覆盖假人肋骨
B柱内饰要求: B柱的缺口要覆盖整个假人肋骨,并且上下Z 方向的距离大于40mm,缺口的宽度(X方向)大于 80mm。
- 1、下载文档前请自行甄别文档内容的完整性,平台不提供额外的编辑、内容补充、找答案等附加服务。
- 2、"仅部分预览"的文档,不可在线预览部分如存在完整性等问题,可反馈申请退款(可完整预览的文档不适用该条件!)。
- 3、如文档侵犯您的权益,请联系客服反馈,我们会尽快为您处理(人工客服工作时间:9:00-18:30)。
汽车前后防撞梁设计规范一、目的:指导汽车前后防撞梁总成设计;提供汽车前后防撞梁总成设计的思路。
二、范围:该规范适应于M1类车辆汽车前后防撞梁的设计。
主要介绍了汽车开发过程中汽车前后防撞梁总成的作用及在整车中的影响。
首先对汽车前后防撞梁在整车中的功能进行了概述,尤其是对汽车前后防撞梁碰撞性能做了详细的描述;同时对汽车前后防撞梁总成设计要点作了描述;最后对汽车前后防撞梁的加工制造性作了阐述。
三、规范性引用文件:下列文件对于本文件的应用是必不可少的。
凡是注日期的引用文件,仅注日期的版本适用于本文件。
凡是不注日期的引用文件,其最新版本(包括所有的修改单)适用于本文件。
GB 11551-2003 乘用车正面碰撞时的乘员保护GB 17354-1998 汽车前、后端保护装置GB 20072-2006 乘用车后碰撞燃油系统安全要求C-NCAP 中国新车评估程序2012版四、汽车前后防撞梁总成主要功能1、汽车前后防撞梁总成功能概述汽车前后防撞梁总成,是车身第一次承受撞击力的装置,也是车身中的一个重要构件,其功能主要有:a. 保护保险杠在低速碰撞过程中尽量不要破裂或者发生永久变形。
b. 保护车身骨架前后端纵梁在行人保护或者可维修性碰撞时不发生永久变形或者破裂。
c. 在100%正面高速碰撞、后面高速碰撞时起到第一次的吸能作用,在偏置碰撞中不仅起到第一次吸能作用,还能起到碰撞过程中均衡传递受力的作用,防止车身左右两侧受力不均。
2、汽车前后防撞梁总成碰撞性能概述前防撞梁总成碰撞性能前防撞梁总成的碰撞性能主要需满足低速碰撞和高速碰撞两个部分的法规要求。
其中,低速碰撞需满足的法规要求为: GB17354-1998 汽车前、后端保护装置。
高速碰撞需满足的法规要求为:GB11551-2003 乘用车正面碰撞时的乘员保护;C-NCAP标准,需满足其100%正面碰撞和40%偏置碰撞要求。
3、低速碰撞对前防撞梁设计的性能要求低速碰撞的国家标准GB l7354—1998规定的正撞速度为4km/h,车角碰撞速度为2.5 km/h,对车身的要求就是车身本体、前防撞梁和吸能盒等不能有任何损坏,最好前保险杠也不能破裂或者发生永久变形。
在国外,从事汽车保险业务的保险机构,一般采用15km/h的碰撞试验来模拟最常见的可维修碰撞,试验的目的是要求尽量减少零部件的损坏以减少维修和保险费用。
具体来说,一般要通过合理设计将损坏零件控制在翼子板、发动机罩盖、前保险杠系统、前格栅、前大灯等外表面零件和部分骨架件,比如前防撞梁以及吸能盒等零件范围内。
车身零体,特别是纵梁不能产生任何变形。
当然最好大灯支架、水箱上横梁等零件不要损坏,即使损坏,也要便于修复。
在可维修碰撞中,合理设计传力路径是非常重要的,重点来说说汽车防撞梁吸能盒的设计a、将吸能盒设计成和纵梁在同一轴线上,避免产生弯曲变形。
b、在吸能盒上预设一些压溃筋,以便让吸能盒在轴向上发生压溃进而吸收所有能量,从而不对包括前纵梁在内的车身本体产生损害。
c、将这些容易损坏的部分骨架件,如前防撞梁和吸能盒设计成用螺栓和车身本体联结的可拆卸结构,为减少维修和保险成本。
4、高速碰撞对前防撞梁设计的性能要求目前设计上普遍接受和采用的是将车身分为前中后3个吸能区,其中前吸能区主要由前防撞梁和吸能盒组成,利用强韧的吸能材料尽可能多地通过变形吸收因撞击产生的巨大能量,同时利用结构上的受力连续进行左右分流并将能量向后面传递。
中吸能区主要由前纵梁和副车架组成,通过合理变形来吸收大部分能量。
后吸能区主要为高强度和刚度的驾驶舱,设计上通过避开可能发生对乘员不利的危险变形,减少正面碰撞导致的对驾驶舱的侵入和保持相对较低的碰撞减速度,以此保证乘员的安全。
前中后3个吸能区是设置正面碰撞多层传力路径的基础,设置正面碰撞多层传力路径的目的也就是为体现3个吸能区的优势,使能量能合理有效地吸收和传递。
正面碰撞多层传力路径一般是3层。
正面碰撞3层传力路径一般分为上中下3层,正面碰撞传力路径上层是由发动机舱上纵梁和前悬塔状形罩板等零件组成,吸收了部分从前部传来的碰撞能量并把其余能量向A柱和前围及其加强梁进行分散传递。
中层主要是由前纵梁组成,也包括了前防撞梁和吸能盒等,是主要的传力路径。
前防撞梁和吸能盒将接受到的碰撞能量进行左右分流和初步吸收,并通过它们将能量往前纵梁延伸板、门槛、中央通道等分散传递。
下层主要是由前副车架组成,吸收了部分从前部传来的碰撞能量并把其余能量向前纵梁延伸板和门槛等分散传递。
五、汽车后防撞梁总成碰撞性能后防撞梁总成的碰撞性能主要需满足低速碰撞和高速碰撞两个部分的法规要求。
其中,低速碰撞需满足的法规要求为:GB 17354-1998 汽车前、后端保护装置。
高速碰撞需满足的法规要求为:GB 20072-2006 乘用车后碰撞燃油系统安全要求。
低速碰撞对后防撞梁设计的性能要求:后防撞梁总成需满足的低速碰撞性能要求同前防撞梁总成。
高速碰撞对后防撞梁设计的性能要求:国标GB 20072-2006规定:碰撞器撞击表面应平坦,高度不小于800mm,撞击器表面下边缘至地面的间隙应为175±25mm,后防撞梁对后碰的主要贡献为利用吸能盒的压溃变形吸收能量,缓解碰撞刚性变形,保证燃油箱周围安全的变形空间。
因此在设计后防撞梁及吸能盒时,需综合考虑下面三方面:a、保证基本的许可变形量。
许可变形量,决定了碰撞过程中的平均减速度。
汽车的纵向变形量与平均减速度是成反比的。
平均减速度作为汽车结构耐碰撞性的主要设计指标,在设计开始阶段就必须综合考虑确定。
b、保证基本的许可变形空间。
保证许可变形空间是指汽车在发生碰撞后,变形区域不会对乘员和危险部件(如油箱、燃汽罐)形成威胁和伤害,而且包括后部许可变形区域内的塑性变形不会导致在碰撞过程中车门打开、碰撞后车门锁死等状况发生。
c、调整截面形状(通过吸能筋与加强筋的布置)、厚度、尺寸和结构形式等使结构的变形阻力保持在适当水平,并重视局部弱化使整车刚度分配符合设计原则及能量吸收曲线图,增大撞击吸收能量的腔型结构。
六、汽车前后防撞梁总成设计要点概述1.汽车前后防撞梁总成设计,主要是根据市场法规和标准来定义前防撞梁总成的性能。
如:法规前碰ODB的定义、汽车前后防撞梁低速碰撞吸能、压溃空间、C NCAP试验ODB碰撞标准、整车性能等。
为满足这些要求,我们需要对汽车前后防撞梁的碰撞性能的敏感性,如:汽车前后防撞梁的布置高度、结构、压溃空间、截面面积、材料等进行研究。
2、整车碰撞对汽车前后防撞梁的布置要求汽车前后防撞梁的布置高度由前纵梁的高度来决定,如果此高度匹配不合理会导致前纵梁在碰撞过程中压溃失稳,导致前纵梁后端大弯曲变形很可能对乘员舱侵入量过大。
汽车前后防撞梁的安装位置,除需满足上述碰撞要求的相容性原理,即两车发生正面相撞时,不合适的防撞梁高度既保护不到自身,还会对对方车辆造成巨大伤害;还需要根据车身高度,轮毂直径的大小来综合评定,并没有一个明确的标准。
一般车型的安装高度在400-500mm左右,但如果超过520mm,则会对C NCAP等相关碰撞试验的成绩造成影响。
保证与周边件间隙≧10mm。
前防撞梁总成一般是螺接到机舱纵梁上,误差积累大,同时车身前端安装有很多子件,故要求前防撞梁总成与周边件的间隙在10mm 以上。
在X 向预留出70mm 的行人保护缓冲空间。
3 、汽车前后防撞梁总成结构形式标准的汽车前后防撞梁总成一般由防撞梁本体和吸能盒组成,部分车型还包含拖车钩螺纹管,为降低维修成本,防撞梁一般采用螺栓连接固定在车身上。
4、前后防撞横梁结构形式前防撞横梁的结构主要有四种方式:冷冲压不同技术对应的优化断面,有不同程度的差别。
冷冲压拼焊的前防撞横梁保持了与车身其它钣金相同的制造技术,不需要单独生产线,故制造成本低廉,不足在于重量大,不便于车身轻量化。
通常材料选用HC420/780DP或HC550/980DP,具体结构、材料根据车型差异及CAE分析相应选择。
辊压成形的前防撞横梁,需要一条专用辊压线,其断面为箱体结构,类似双层板,重量方面优势不大。
通常材料选用HC420/780DP或HC550/980DP,料厚1.8mm,具体根据车型差异及CAE分析相应选择。
根据目前供应商制造工艺限制,目前合理的防撞梁半径R≥2700mm。
热冲压的前防撞横梁,需要一条专用热成形加工线及专用模具,综合成本较高,优势在于重量轻。
铝制的前防撞横梁,需要专用设备及工装,综合成本较高,优势在于重量轻。
5、后防撞横梁结构形式后防撞横梁的制造主要为冷冲压和铝制,冷冲压横梁一般为U形截面结构,通常材料选用HC250/450DP、HC340/590DP,具体形状、材料根据车型差异及CAE分析相应选择。
6、吸能盒设计要求吸能盒上一般需布置2至3条吸能筋,主要目的是便于低速碰撞时吸收足够的能量,保证车身本体不被破坏。
同时设计吸能筋时需遵循以下4条原则:a. 加强筋的轴线必须垂直于受力方向,否则在振动时会引起扭转;b. 必须沿支撑之间最短距离布置;c. 采用交叉筋时,应考虑在交叉点容易产生应力集中,相对减小了交叉点的刚性,所以在交叉点要注意圆角过渡,圆角半径应大于筋的宽度的两倍;d. 加强筋的形状在平的或稍凸起的零件上,加强筋应沿零件对角线布置,在深弯曲的零件上应垂直于零件的弯曲轴线。
定义防撞梁本体和吸能盒截面尺寸:Z 向高度、Y 向宽度、X 向长度:A 级车型吸能盒在X 向长度一般在120mm 左右,A0 级车型长度约在100 mm。
横梁本体X 向截面尺寸受吸能盒和保险杠位置所限制,故不能取值太大,一般在55mm。
可以根据钣金材料级别、整车受力大小和整车安全星级等综合因素而调整。
吸能盒Z向高度、Y向宽度与纵梁截面基本一致,偏差不大于5mm。
吸能盒和纵梁中心轴线一致。
7、前拖车钩结构设计要求前拖车装置工作方式(如:螺接、挂钩)和布置位置;一般前拖车装置采用螺接方式。
布置位置,理论上希望拖车装置对称中心线与机舱纵梁中心重合,或偏离距离越小越好。
挂钩或螺母套主要配合尺寸;根据整车装备质量,确定拖车装置所需要承受载荷,选择合适的螺母套及拖钩,公司现有M20 螺纹规格,不同车型可以通用。
8、防撞梁和车身连接标准件采用8.8级M8螺栓。
七、防撞梁总成设计经验1、吸能盒螺栓固定点分布要求尽量靠近吸能盒,均匀分布。
四个螺栓连接点分布距吸能盒偏远,碰撞中受到扭转力或拉力作用导致前纵梁前安装板和前防撞梁安装板连接处开口。
优化方案:将螺栓安装点靠近吸能盒安装。
2、吸能盒与防撞梁及安装板连接必须可靠,保证连接强度。
中心柱碰撞及偏置碰撞时由于吸能盒与安装板点焊强度不足,导致吸能盒脱落,优化方案:加强连接强度,将点焊改为二保焊,并增加焊接点。