JB-T10051—1999金属切削机床液压系统通用技术条件解读
立车装配质量检验记录

立车装配质量检验记录编号:J8.2-02 普通型双立柱立式车床数控总装装配质量检验记录产品型号:产品名称:用户名称:出厂编号:______________ 公司总则一、此卡片为检验普通、数控型双柱立式车床;二、机床的几何精度、数控精度、工作精度按所检验产品型号的合格证及补充验收报告验收技术要求执行;三、参照标准及文件:GB/T9061-20__6 金属切削机床通用技术条件;JB/T9874-1999 金属切削机床装配通用技术条件;JB/T4116-96 单、双柱立式车床精度检验;JB/T10051-1999 金属切削机床液压系统通用技术条件;JB/T9877-1999 金属切削机床清洁度的测定;GB/T6576-20__2 润滑系统技术条件;GB15760-20__4 安全防护通用技术条件;Q/Q2J06.06-2021 铸铁件和铸钢件清理检验及涂底漆工艺规程;GB5226.1-20__2 机械安全、机械电气设备;Q/Q2JO1.271-20__5 机床电气检验要求;JB/T 8356.1-1996 机床包装技术条件;JB/T 8356.2-1996 机床包装箱;GB/T 4879-1999 防锈包装。
四、机床验收检验报告顺序:1、总装;2、空运转试验(试车)与电气检验交叉进行;3、负荷试验;4、几何精度检验;5、数控精度检验;6、工作精度检验;7、油漆检验;8、包装检验。
五、机床验收检验要求:验收检验前,应将机床安装和调整好,一般应自然调平,使机床处于水平位置。
主要零件登记表零件名称图号编号备注一、试车工序序号检验内容及要求检验结论备注 1 各部零件装配齐全,加工表面无磕碰、划伤、锈蚀等现象。
2 沉头螺钉不应凸出零件表面,螺栓尾端应略凸出螺母倒角值,固定销钉应略凸出零件表面。
3 夹紧机构可靠稳定,各油缸无渗油现象,操纵机构灵活可靠。
4 工作台液压浮起(),当低于 0.04 时电位传感器报警,浮起一致性0.01。
加工中心安全防护技术条件.
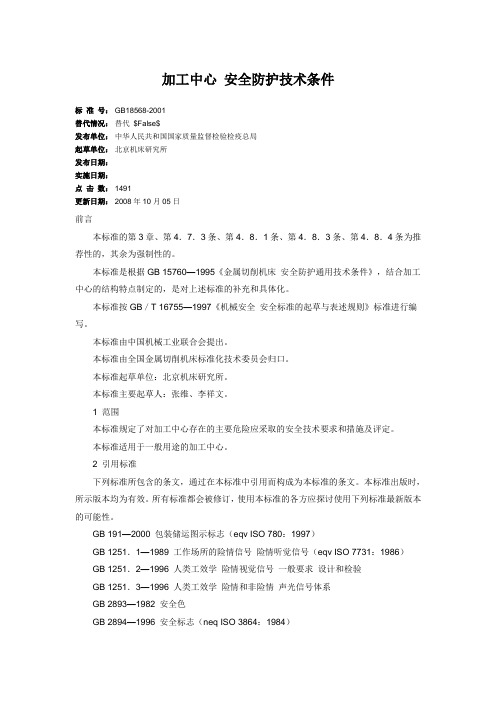
加工中心安全防护技术条件标准号:GB18568-2001替代情况:替代$False$发布单位:中华人民共和国国家质量监督检验检疫总局起草单位:北京机床研究所发布日期:实施日期:点击数:1491更新日期:2008年10月05日前言本标准的第3章、第4.7.3条、第4.8.1条、第4.8.3条、第4.8.4条为推荐性的,其余为强制性的。
本标准是根据GB 15760—1995《金属切削机床安全防护通用技术条件》,结合加工中心的结构特点制定的,是对上述标准的补充和具体化。
本标准按GB/T 16755—1997《机械安全安全标准的起草与表述规则》标准进行编写。
本标准由中国机械工业联合会提出。
本标准由全国金属切削机床标准化技术委员会归口。
本标准起草单位:北京机床研究所。
本标准主要起草人:张维、李祥文。
1 范围本标准规定了对加工中心存在的主要危险应采取的安全技术要求和措施及评定。
本标准适用于一般用途的加工中心。
2 引用标准下列标准所包含的条文,通过在本标准中引用而构成为本标准的条文。
本标准出版时,所示版本均为有效。
所有标准都会被修订,使用本标准的各方应探讨使用下列标准最新版本的可能性。
GB 191—2000 包装储运图示标志(eqv ISO 780:1997)GB 1251.1—1989 工作场所的险情信号险情听觉信号(eqv ISO 7731:1986)GB 1251.2—1996 人类工效学险情视觉信号一般要求设计和检验GB 1251.3—1996 人类工效学险情和非险情声光信号体系GB 2893—1982 安全色GB 2894—1996 安全标志(neq ISO 3864:1984)GB/T 3168—1993 数字控制机床操作指示形象化符号(neq ISO 2972:1979)GB 4053.1—1993 固定式钢直梯安全技术条件GB 4053.2—1993 固定式钢斜梯安全技术条件GB 4053.3—1993 固定式工业防护栏杆安全技术条件GB 4053.4—1983 固定式工业钢平台GB/T 5226.1—1996 工业机械电气设备第一部分:通用技术条件(eqv IEC 204—l:1992)GB/T 6527.2—1986 安全色使用导则(eqv ISO 3864:1984)GB/T 6576—1986 机床润滑系统(neq ISO 5170:1977)GB 7247—1995 激光产品辐射安全、设备分类、要求和用户指南(idt IEC 825:1984)GB/T 7632—1987 机床用润滑剂的选用GB/T 7932—1987 气动系统通用技术条件(neq ISO 4414:1982)GB 8196一t987 机械设备防护罩安全要求GB 8197—1987 防护屏安全要求GB 9969.1—1998 工业产品使用说明书总则GB 12265.1—1997 机械安全防止上肢触及危险区的安全距离GB 12265.2—2000 机械安全防止下肢触及危险区的安全距离GB 12265.3—1997 机械安全避免人体各部位挤压的最小间距GB/T 13379-一1992 视觉工效学原则室内工作系统照明(neq ISO 8995:1989)GB/T 14775—1993 操纵器一般人类工效学要求GB/T 14776—1993 人类工效学工作岗位尺寸设计原则及其数值GB/T 15241.2—1999 与心理负荷相关的工效学原则第2部分:设计原则(idt ISO 10075-2:1996)GB/T 15706.1—1995 机械安全基本概念与设计通则第1部分:基本术语、方法学GB/T 15706.2—1995 机械安全基本概念与设计通则第2部分:技术原则与规范GB 15760—1995 金属切削机床安全防护通用技术条件GB/T 1625l—1996 工作系统设计的人类工效学原则(eqv ISO 6385:1981)GB 16754—1997 机械安全急停设计原则(eqv ISO/IEC 13850:1995)GB/T 16769一1997 金属切削机床噪声声压级测量方法GB/T 16855.1—1997 机械安全控制系统有关安全部件第一部分:设计通则GB/T 16856一1997 机械安全风险评价的原则GB/T 17161—1997 机床控制装置的操作方向(eqv ISO 447:1984)GB/T 17454.1—1998 机械安全压敏防护装置第1部分:压敏垫和压敏地板设计和试验通则GB 17888.1—1999 机械安全进入机器和工业设备的固定设施第1部分:进入两级平面之间的固定设施的选择GB 17888.2—1999 机械安全进入机器和工业设备的固定设施第2部分:工作平台和通道GB 17888.3—1999 机械安全进入机器和工业设备的固定设施第3部分:楼梯、阶梯和护栏GB 17888.4—1999 机械安全进入机器和工业设备的固定设施第4部分:固定式直梯GB/T 18153—2000 机械安全可接触表面温度确定热表面温度限值的工效学数据GB 18209.1—2000 机械安全指示、标志和操作第l部分:关于视觉、听觉和触觉信号的要求(idt IEC 61310-1:1995)GB 18209.2—2000 机械安全指示、标志和操作第2部分:标志要求(idt IEC 61310-2:1995)JB/T 8356.1—1996 机床包装技术条件JB/T 8356.2—1996 机床包装箱JB/T 8356.3—1996 机床包装用中、小木箱JB/T 9878—1999 金属切削机床粉尘浓度的测定JB/T 9879—1999 金属切削机床油雾浓度测量方法JB/T 10051—1999 金属切削机床液压系统通用技术条件3 机床的危险3.1 机械危险3.1.1 挤压危险a)主轴箱与工作台之间的挤压危险;b)工作台与墙或其他物体之间的挤压危险;c)滑鞍(或滑板)与墙或其他物体之间的挤压危险;d)刀具与刀库之间的挤压危险;e)刀具与刀具夹紧机构或机械手之间的挤压危险;f)工件与工件动力夹紧机构之间或工件运动(例如:工件分度)的挤压危险;g)机械排屑装置运动部分与固定部分之间的挤压危险;h)由于操作者意料不到运动或观察加工时产生的挤压危险。
JB-T9885-1999_组合机床液压滑台技术条件

,2 调整滑鞍的进给速度为最小工作进给速度, . 检验其在 最大进给力和空载时的进给速度变化, 其变 化率[ ( )不得超过t 在 1 循环中连续测量 3 见式 1 1 1 5 %, 0个 0次, 这时滑鞍进给应 平稳 , 用百分表 触 在滑鞍前端面上检查滑鞍的移动, 表针应平稳转动. 跳动不应相过 0 1 , .m 0 m
表 1
缸孔直径
M E n
2 5
3 2
4 0
5 0
பைடு நூலகம்
6 3
8 0
10 0
1 5 2
10 6
20 0
压
力
M P a
04 .0
03 .5
03 .0
02 .5
0.0 2
0.8 1
注
1 表内 数值只适合于活塞所采用的密封圈为0, X, U , Y形式。
5. 5活 杆 动 稳 检验 .2 4. 塞 移 平 性
了
在活塞杆不承受载荷的条件下,向油缸前进腔通人压力油, 使活塞杆以 该部件所规定的最小进给 速度移动, 这时活塞杆的移动应平稳, 用百分表触在活塞杆端部,检查活塞杆的移动, 表针应平稳转 动,跳动不应超过 0 1 . .m 0 m
55 装配 .
注:测量 压力振摆时 ,压 力计不应带阻尼器。
542 油缸的试验项 目 ..
5421 试运转及行程测量 ... 将被试验的油缸安装在相应的试验台上, 在空载情况下全 行程往复动作 7次, 这时不得有外渗漏 和冲击等不正常现象。同时, 将油缸的 活塞分别停留 在行程的两端, 测量全行程的长度,其长度应符 合设计要求。 5422 活塞及活塞杆移动的阻力检验 ... 在活塞杆没有承受载荷的 条件下向 油缸前进腔通人压力油, 使活塞杆以一定的 进给速度移动, 测 量所需的压力不得超过表 1 所列数值。
JBT3818-99 《液压机技术条件》标准
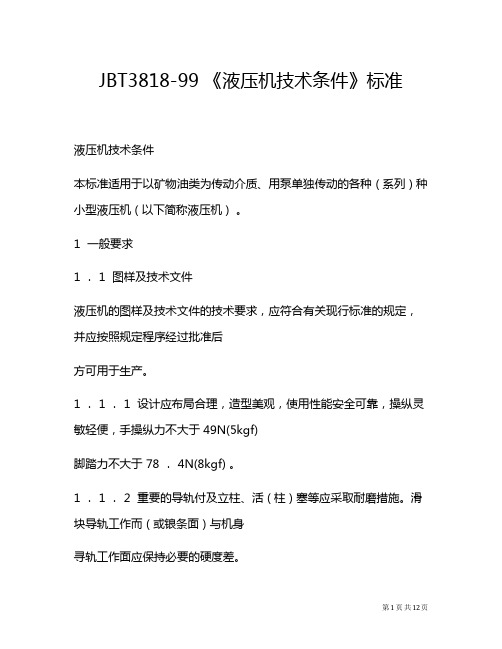
JBT3818-99 《液压机技术条件》标准液压机技术条件本标准适用于以矿物油类为传动介质、用泵单独传动的各种 ( 系列 ) 种小型液压机 ( 以下简称液压机 ) 。
1 一般要求1 . 1 图样及技术文件液压机的图样及技术文件的技术要求,应符合有关现行标准的规定,并应按照规定程序经过批准后方可用于生产。
1 . 1 . 1 设计应布局合理,造型美观,使用性能安全可靠,操纵灵敏轻便,手操纵力不大于 49N(5kgf)脚踏力不大于 78 . 4N(8kgf) 。
1 . 1 .2 重要的导轨付及立柱、活 ( 柱 ) 塞等应采取耐磨措施。
滑块导轨工作而 ( 或锒条面 ) 与机身寻轨工作面应保持必要的硬度差。
1 . 1.3 重量超过 15kg 的零部件、元件或装备等均须便于吊运和安装,必要时应设有起吊孔或起吊钩 ( 环 ) 。
1 . 1 . 4 整体或部分包装的液压机及其零部件,应符合运输和装载的现行标准和有关规定。
1 . 1 . 5 分装的零部件,应有相关的安装识别标记,其中板式或管式阀等安装时须有正确的定向措施;其中管路和液压元件的通道口应有防尘措施。
1 .2 型式及参数液压机的型式、基本参数与尺寸,应按照现行标准的规定或按指导性技术文件的推荐优先选用。
如无标准则应按照规定程序批准的图样及技术文件制造。
1 . 3 精度及刚度液压机应具有足够的精度和刚度,并应符合现行标准和有关规定。
1 . 4 配套要求1 . 4 . 1 出厂的液压机,应备有必须的附件及备用易损件。
特殊附件由用户与制造厂商定,随机供应或单独订货。
1 . 4 .2 液压机的外购配套件 ( 包括液压、电气、气动元件和密封件等 ) 及外协件应符合有关现行标准并取得其合格证,且须安装在液压机上进行运转试验。
1 . 5 其他1 . 5 . 1 液压机的液压、气动、润滑、冷却等系统和有关零部件,均不应漏油、漏水、漏气,并不得互相混入。
1 . 5 .2 液压机上的标牌和操纵、指示、润滑、安全等标牌及标志,均应符合有关现行标准和规定,并能保持长久清晰。
JBT3818-99 《液压机技术条件》标准
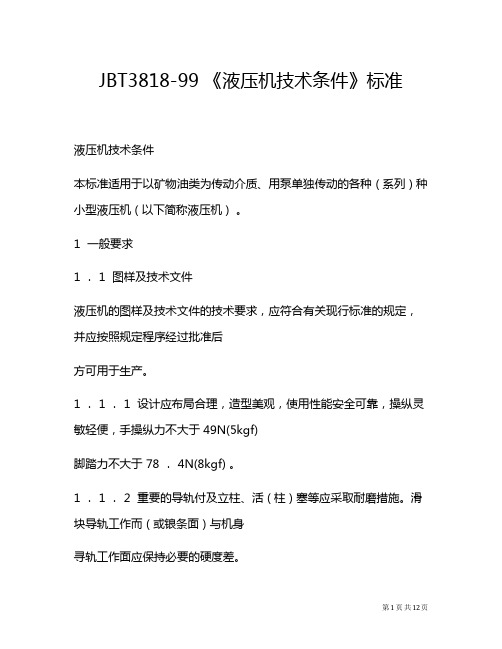
JBT3818-99 《液压机技术条件》标准液压机技术条件本标准适用于以矿物油类为传动介质、用泵单独传动的各种 ( 系列 ) 种小型液压机 ( 以下简称液压机 ) 。
1 一般要求1 . 1 图样及技术文件液压机的图样及技术文件的技术要求,应符合有关现行标准的规定,并应按照规定程序经过批准后方可用于生产。
1 . 1 . 1 设计应布局合理,造型美观,使用性能安全可靠,操纵灵敏轻便,手操纵力不大于 49N(5kgf)脚踏力不大于 78 . 4N(8kgf) 。
1 . 1 .2 重要的导轨付及立柱、活 ( 柱 ) 塞等应采取耐磨措施。
滑块导轨工作而 ( 或锒条面 ) 与机身寻轨工作面应保持必要的硬度差。
1 . 1.3 重量超过 15kg 的零部件、元件或装备等均须便于吊运和安装,必要时应设有起吊孔或起吊钩 ( 环 ) 。
1 . 1 . 4 整体或部分包装的液压机及其零部件,应符合运输和装载的现行标准和有关规定。
1 . 1 . 5 分装的零部件,应有相关的安装识别标记,其中板式或管式阀等安装时须有正确的定向措施;其中管路和液压元件的通道口应有防尘措施。
1 .2 型式及参数液压机的型式、基本参数与尺寸,应按照现行标准的规定或按指导性技术文件的推荐优先选用。
如无标准则应按照规定程序批准的图样及技术文件制造。
1 . 3 精度及刚度液压机应具有足够的精度和刚度,并应符合现行标准和有关规定。
1 . 4 配套要求1 . 4 . 1 出厂的液压机,应备有必须的附件及备用易损件。
特殊附件由用户与制造厂商定,随机供应或单独订货。
1 . 4 .2 液压机的外购配套件 ( 包括液压、电气、气动元件和密封件等 ) 及外协件应符合有关现行标准并取得其合格证,且须安装在液压机上进行运转试验。
1 . 5 其他1 . 5 . 1 液压机的液压、气动、润滑、冷却等系统和有关零部件,均不应漏油、漏水、漏气,并不得互相混入。
1 . 5 .2 液压机上的标牌和操纵、指示、润滑、安全等标牌及标志,均应符合有关现行标准和规定,并能保持长久清晰。
中国机械工业标准汇编
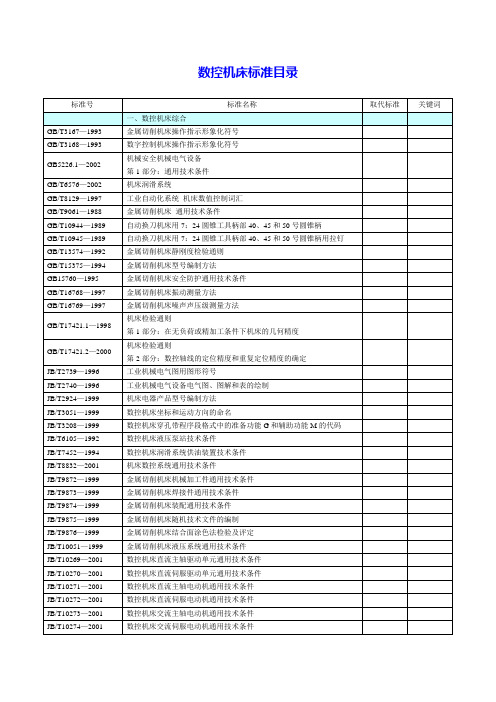
GB/T9061—1988
金属切削机床通用技术条件
GB/T10944—1989
自动换刀机床用7:24圆锥工具柄部40、45和50号圆锥柄
GB/T10945—1989
自动换刀机床用7:24圆锥工具柄部40、45和50号圆锥柄用拉钉
GB/T13574—1992
金属切削机床静刚度检验通则
数控机01
数控机床直流伺服电动机通用技术条件
JB/T10273—2001
数控机床交流主轴电动机通用技术条件
JB/T10274—2001
数控机床交流伺服电动机通用技术条件
JB/T10275—2001
数控机床交流主轴驱动单元通用技术条件
JB/T10276—2001
GB/T15375—1994
金属切削机床型号编制方法
GB15760—1995
金属切削机床安全防护通用技术条件
GB/T16768—1997
金属切削机床振动测量方法
GB/T16769—1997
金属切削机床噪声声压级测量方法
GB/T17421.1—1998
机床检验通则
第1部分:在无负荷或精加工条件下机床的几何精度
JB/T3208—1999
数控机床穿孔带程序段格式中的准备功能G和辅助功能M的代码
JB/T6105—1992
数控机床液压泵站技术条件
JB/T7452—1994
数控机床润滑系统供油装置技术条件
JB/T8832—2001
机床数控系统通用技术条件
JB/T9872—1999
金属切削机床机械加工件通用技术条件
JB/T9934.2—1999
滚珠丝杠副
第2部分:公称直径和公称导程公制系列
3.5米数控立车技术规格书
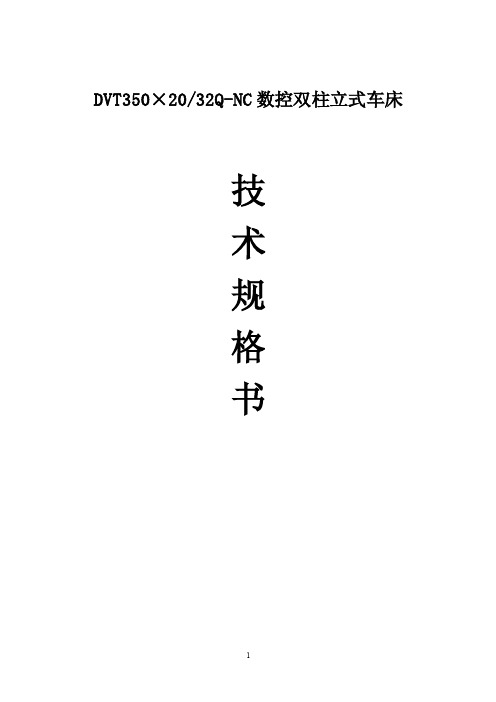
DVT350×20/32Q-NC数控双柱立式车床技术规格书1.机床主要用途及组成1.1机床主要用途本机床适用于高速钢和硬质合金刀具,加工各种黑色金属、有色金属和部分非金属材料的工件。
在本机床上可完成粗、精车内外圆柱面、内外圆锥面、平面、曲面以及切槽、车螺纹等工序。
1.2 机床组成机床主要由龙门架、主传动变速箱、工作台、横梁、横梁升降机构、数控刀架、刀架进给箱、液压系统、电控系统等组成2.主要规格与参数2.1 最大车削直径φ3500 mm2.2 最大工件高度 2000 mm2.3 最大工件重量 32t2.4 工作台2.4.1 工作台直径φ3150 mm2.4.2 工作台转速级数无级机械二挡2.4.3 工作台转速范围 0.63~63r/min2.4.4 工作台最大扭矩 100kN.m2.5 垂直刀架2.5.1 垂直刀架进给量级数无级2.5.2 垂直刀架进给量范围 0.1-1000mm/min2.5.3 垂直刀架快速移动速度 8000mm/min2.5.4 垂直刀架最大水平行程-20~2015mm2.5.5 垂直刀架滑枕垂直行程 1250 mm2.5.6 垂直刀架滑枕截面尺寸 220×220mm2.5.7 垂直刀架最大切削力 35kN2.6 横梁行程 1500 mm2.7 横梁升降速度 350 mm/min2.8 横梁升降电机功率 11 kW2.9 主电机功率 55kW2.10 机床重量(约) 60t2.11 机床外形尺寸(长×宽×高) 约7412×5460×7195mm3.主要结构及性能3.1 机床总体布局本机床的总体布局为龙门式热对称结构。
由左右立柱、联接梁和工作台底座构成框架式结构,经有限元法计算,使机床大件及整机具有高强度、高刚度、高吸振性的特点。
横梁在左、右立柱导轨上移动,由双轴伸交流电机驱动,经左右横梁升降箱、螺母丝杠传动,实现横梁上下移动,在横梁上设置一个垂直刀架,刀架为数控刀架,由交流伺服电机驱动。
JB-T10045.1-1999.pdf

电 弧一 压 缩空气气刨是利用电弧及压缩空气在表面进行切割的热切割方法 。由电弧和材料燃烧时产
生热量使材料能够连续的熔化及嫩烧 。反应过程沿移动方 向发展 ,由压缩 空气流驱除熔融物及熔渣而形
成切 口。
5.2.3 等离子弧切割
采用 等 离 子弧的热能实现切割的方法
5.2.3门 转移电弧的等离子弧切割(图 12)
/liuyx866
切 割方 向
工件
图 5 矿 石 粉 末 一火 焰 切 割
图 6 火焰气刨
5.1.4 火焰表面清理(图 7)
采 用 气 割火焰铲除钢锭表面缺陷的方法 。 5.1.5 火焰穿孔(图 s)
火焰 穿孔 是用氧矛在矿石或金属材料上穿孔 ,它是一种热穿孔方法。氧矛的外露端被加热到熔点, 并在加入氧的条件下燃烧
转移 电弧 进行等离子弧切割时 ,工件处于 切割 电流回路内,故被切割的材料必须是导电的 。
5.2-3.2 非转移电弧的等离子弧切割(图 13)
非转 移 电弧进行等离子弧切割时 ,工件不须处于切割电流回路内,故可以切割导 电的及不导 电的材
料。
5.3 采用束流的热切割
5.3.1 激光切割
采用 激 光 束的热能实现切割的方法 。
JB/T 10045.1 一 1999
前言
本标准等同采用德国标准 DIN 2310T 6-1980(热切割 方法和分类》。 本标 准 是 对ZBJ 590 02.1-88《热切割 方法和分类》的修订。修订时仅做了编辑性修改,技术 内容
无变化。
本标准自实施之日起代替 ZB7 590 02.1-88. 本标准由全国焊接标准化技术委员会提出并归 口。
金属 粉 末 一熔化切割是在送人金属粉末的情况下,利用气体火焰及切割氧进行的热切割方法。用气 体火焰及燃烧的金属粉末热量将材料熔化 ,并将金属(或矿石)熔融物转变成稀薄的熔渣(或熔岩),被切
- 1、下载文档前请自行甄别文档内容的完整性,平台不提供额外的编辑、内容补充、找答案等附加服务。
- 2、"仅部分预览"的文档,不可在线预览部分如存在完整性等问题,可反馈申请退款(可完整预览的文档不适用该条件!)。
- 3、如文档侵犯您的权益,请联系客服反馈,我们会尽快为您处理(人工客服工作时间:9:00-18:30)。
金属切削机床液压系统通用技术条件
JB/T 10051—1999
国家机械工业局1999—10—08批准 2000—03—01实施
前言
本标准是对ZB J50 016—89《金属切削机床液压系统通用技术条件》的修订。
修订时,对原标准作了编辑性修改,技术内容有以下变化:——原3.3.7删去“对于复杂的液压系统,其外露”的字样,改为“管路应作标记,用涂不同颜色的涂料加以区别”;
——原3.4.3前面加“在条件允许的情况下,液压站的底部可……”;
——增加“3.4.9油箱内壁可镀锌,但不得涂油漆”。
本标准自实施之日起代替ZB J50 016—89。
本标准由广州机床研究所提出并归口。
本标准起草单位:广州机床研究所。
本标准主要起草人:刘镇藩、朱俊峰、罗慧、老国鎏。
1 范围
本标准规定了金属切削机床液压系统的要求、装配与调试、安全及其它。
本标准适用于以液压油为工作介质的金属切削机床液压传动及控制系统。
2 引用标准
下列标准所包含的条文,通过在本标准中引用而构成为本标准的条文。
本标准出版时,所示版本均为有效。
所有标准都会被修订,使用本标准的各方应探讨使用下列标准最新版本的可能性。
GB/T 786.1—1993 液压气动图形符号
GB/T 7632—1987 机床用润滑剂的选用
JB/T 7938—1995 液压泵站油箱容量系列
JB/T 9871一1999 金属切削机床精度等级
JB/T 9875—1999 金属切削机床随机技术文件的编制
3 要求
3.1 基本要求
3.1.1 金属切削机床液压系统的设计、制造与使用应满足以下要求:
a)人身安全;
b)运转正常;
c)设备使用寿命长;
d)维修方便。
3.1.2 机床液压系统所用的液压元件和部件,其性能必须符合有关质量标准或设计的各项技术要求。
3.1.3 为保证机床液压系统的正常工作,应选用符合GB/T 7632规定的油液作为工作介质。
必须在便于更换维修的位置设置油液过滤装置,油液在注入液压
系统油箱(池)前应仔细过滤。
液压系统用油液的清洁度应符合相应标准的规定。
3.1.4 液压系统用油与导轨或其他机械部件用油应互相分隔。
如难以分隔,则应符合下述要求:
a)必须严格过滤,以排除油液中的杂质;
b)所有油液能同时满足各种使用要求。
3.2 管路、接头及通道
3.2.1 液压系统管接头材料为金属,管道材料一般为金属、耐油橡胶编织软管、合成树脂高压软管及其它工作介质相容的材质,其管壁在承受系统最大工作压力的1.5倍时应能正常工作。
3.2.2 液压系统所有接头处和外露结合处不应渗漏。
在接头及其它结合处允许使用密封填料或密封胶,但禁用麻、丝等杂物代替。
3.2.3 油管弯曲处应圆滑,不应有明显的凹痕及压偏现象,短长轴比不小于0.75。
3.2.4 液压系统在装配前,接头、管道、通道(包括铸造型芯孔、机加工等)及油箱(池),均应清洗干净。
3.3 管道
3.3.1 液压系统所用通道应有足够的通流面积。
3.3.2 管道设置应安全合理,排列应整齐,便于元件调整、修理、更换。
为避免管道的振动、撞击,管道间应有一定的间隙。
在长管道间或产生振动、撞击发出音响时应采用管夹加以固定,各管夹间距离可参与表1的数值。
3.3.3 管夹不得焊于管子上,也不应损坏管路。
3.3.4 管路一般不允许用来支承元件或油路板。
3.3.5 软管一般用于可动件之间且便于替换件的更换处、抑制机械振动或噪声的传递处,并使其长度尽可能短,避免设备在运行中软管发生严重弯曲与变形,必要时应设软管保护装置。
3.3.6 管道需架空跨越时,其高度应便于维修及保证人员的安全,支承要牢靠。
3.3.7 管路应做标记,用涂不同颜色的涂料加以区别:
压力管路红色;
回油及泄漏管路黄色;
控制管道蓝色。
3.4 液压泵站与油箱
3.4.1 液压泵站与油箱的公称容量应符合JB/T 7938的规定。
3.4.2 在整个工作周期内,液位必须保持安全工作高度,并有足够的空间以便热膨胀和分离空气,在正常工况下,必须能容纳全部从系统中流回的油液,必须防止溢出或漏出的被污染油液直接回到油箱中去。
3.4.3 在条件允许的情况下,液压站的底部可提高到离安装面150mm以上,
以便于搬运、放油和散热。
3.4.4 可拆卸的盖板,在其结构上应能防止杂质进入油箱。
3.4.5 用挡流板或其它措施将回油与液压泵的进口分开,如用挡流板应不妨碍油箱清洗。
3.4.6 油箱底部的形状必须能将液压油排空,油箱应配备一个或一个以上的手孔盖,以便清洗油箱整个内部。
3.4.7 穿过油箱顶盖的管子均应有效密封,回油管路终端应在油箱最低液位之下。
3.4.8 充液点近旁应设有液位计,在通气油箱的上部应有空气滤清器。
3.4.9 油箱内壁可镀锌,但不得涂油漆。
3.5 压力表
3.5.1 系统设置的压力表应安装在便于观察的明显部位。
3.5.2 压力表量程应为被检测压力的1.5~2.0倍,精度不得低于2.5级。
3.5.3 压力表一般应带有卸压装置,或采用耐震压力表,外加阻尼器等。
3.5.4 测量多个压力时,可采用具有一个压力表和一个选择阀组成的多点测量装置。
3.6 超重措施
所有重量超过15kg的元件、部件或设备,必须能方便地起吊或设起吊装置。
3.7 包装
3.7.1 液压系统的外露口应用密封帽封闭,外螺纹必须加以保护。
3.7.2 包装的其它要求应符合有关标准的规定。
4 装配与调试
4.1 为便于装配、调试和维修,液压系统的管道与主机分离部件的接口处均应进行编号和标志,并使管道编号、标志与有关技术文件一致。
4.2 安装油泵时,应注意保证与驱动电动机传动轴的同轴度。
刚性联结时,其同轴度允差为0.05mm;柔性联接时,其同轴度允差为0.1mm。
4.3 油液温度与温升
4.3.1 在额定工作压力下使系统连续运行至油液达到热平衡后,检验油液的温度和温升,其温度和温升不得大于表2的规定值。
4.3.2 测温时,温度计应尽量靠近吸油口。
所用温度计等级不低于1.5级,量程不大于100℃。
5 安全
5.1 运动部件间的动作顺序应有联锁安全装置。
采用静压装置时,为确保在建立静压后才能驱动液压系统或其他机械运动,一般也应有联锁安全装置。
5.2 设计机床液压系统时,对全自动液压机床或当机床的液压系统失去正常压力可能产生不安全因素时,应在系统中设置必要的报警装置或指示信号。
5.3 油泵与驱动电动机联结处外露时应设有安全防护装置。
5.4 当机床停车时,装有蓄能器的液压回路必须能自动释放蓄能器中的压力,或能使回路与蓄能器可靠隔离。
5.5 当机床停车时,液压回路仍要利用蓄能器中有压油液来工作的情况下,必须在蓄能器上或靠蓄能器的显眼处示出安全使用说明,其中包括“注意,压力容器”的字样。
6 其他
6.1 液压系统说明应按JB/T 9875的规定编人机床使用说明书,其内容一般应包括:
a)液压系统原理与使用说明,包括液压系统原理图,管道示意图,液压元件型号与规格的明细表,以及表中对专用液压元件代号及制造厂的说明,每个液压控制阀的压力的调定值,要求注入系统至最高液位的油量,规定的油液品种与黏度范围,有关的电气及机械控制元件操作时间程序表,管路两端的识别标志等;
b)液压系统使用注意事项;
c)液压系统维修、故障及其分析和排除的说明;
d)要求定期测试与维护保养的测试点、加油口、排油口、取样口、滤油器等的设置位置。
6.2 液压系统所用图形符号应符合GB/T 786.1的规定。