提高早期预分解窑产量的措施
分解窑质量和台时能力的提高与稳定
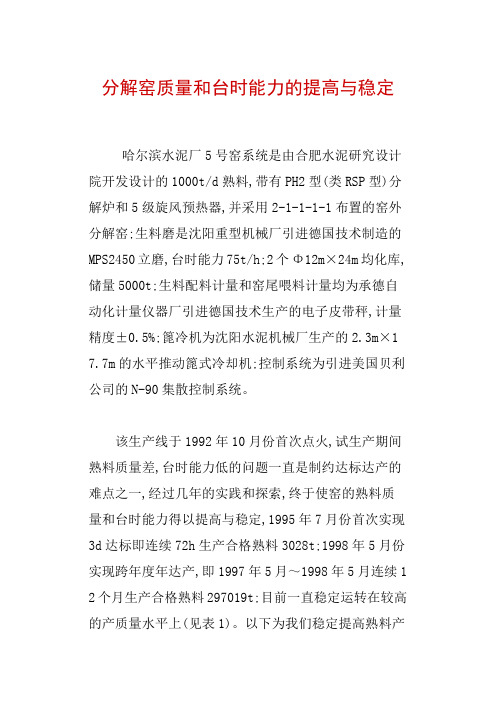
分解窑质量和台时能力的提高与稳定哈尔滨水泥厂5号窑系统是由合肥水泥研究设计院开发设计的1000t/d熟料,带有PH2型(类RSP型)分解炉和5级旋风预热器,并采用2-1-1-1-1布置的窑外分解窑;生料磨是沈阳重型机械厂引进德国技术制造的MPS2450立磨,台时能力75t/h;2个Φ12m×24m均化库,储量5000t;生料配料计量和窑尾喂料计量均为承德自动化计量仪器厂引进德国技术生产的电子皮带秤,计量精度±0.5%;篦冷机为沈阳水泥机械厂生产的2.3m×1 7.7m的水平推动篦式冷却机;控制系统为引进美国贝利公司的N-90集散控制系统。
该生产线于1992年10月份首次点火,试生产期间熟料质量差,台时能力低的问题一直是制约达标达产的难点之一,经过几年的实践和探索,终于使窑的熟料质量和台时能力得以提高与稳定,1995年7月份首次实现3d达标即连续72h生产合格熟料3028t;1998年5月份实现跨年度年达产,即1997年5月~1998年5月连续1 2个月生产合格熟料297019t;目前一直稳定运转在较高的产质量水平上(见表1)。
以下为我们稳定提高熟料产质量的具体做法。
表1 1995~1998年6月窑运转状况1 改进三通道喷煤嘴结构及安放位置,建立维护制度1.1 三通道喷煤嘴结构的改进我厂窑头喂煤用三通道喷煤嘴,原设计内风角度为45°,使用中出现刷窑皮、烧蚀耐火砖的现象,开始烧成带用200mm厚的磷酸盐砖,使用一周时间火点处就只剩下2mm厚,造成红窑,后来使用不烧结镁铬砖和半直接结合镁铬砖也只能使用2~3个月。
而短粗的火焰使高温区过于集中也不利于熟料的烧成,此后,将内风角度改为15°,这样虽然火焰细长,但角度太小不能将风煤很好地搅拌混合,燃烧效率低,降低了对熟料的烧成能力甚至造成不完全燃烧使窑尾斜坡和缩口结皮加重,进而造成窑炉两路风的不匹配,引发塌料和堵塞,严重影响熟料质量和台时能力的提高,最后将内风角度改为3 0°,解决了问题。
窑外分解窑熟料产量和质量的提高与稳定

2500/d窑外分解窑熟料产量和质量的提高与稳定某水泥有限公司2500t/h熟料生产线是由天津水泥工业设计研究院设计的。
分解炉为DD炉,预热器为双系列的;回转窑规格为Ф4×60m;生料磨为Ф4.6×10+3.5m中卸烘干磨;煤磨为Ф2.8×5+3m风扫磨;煤粉计量采用德国PFISTER公司生产的DRW4.10转子秤;篦冷机为天津院开发的带有充气篦板的冷却机;控制系统为天津院开发的集散型控制系统。
该生产线于2006年1月份点火,试生产期间熟料质量不稳定,日产熟料2500t左右。
经过1年多来的实践和探索,使窑的熟料质量和日产能力得以提高与稳定, 2006年连续12个月生产合格熟料729045t;2007年1月至4月共生产熟料259802t;从2006年10月份开始到目前一直稳定运转在较高的产质量水平上(见表1)。
以下为我们稳定提高熟料产质量的具体做法。
表1 2006年-2007年4月窑运转情况1 积极采取措施稳定生料质量1)严把原材料关。
我公司有自己的石灰石矿山,地质勘探结果表明,CaO含量平均为52.4%,含有夹石层,我们做法是,对矿山进行分片取样检验,根据检验结果,再进行高品位石灰石与低品位石灰石进行搭配开采(即使每片石灰石CaO含量都在控制范围内,也要多点搭配开采),要求矿山车间遵照执行,下山石灰石每两小时检验一次CaO含量,发现有低于49%时,及时通知矿山车间更改搭配比例,确保下山石灰石CaO含量在50%-53%之间,另外严格控制石灰石破碎粒度要<25mm。
我公司砂岩附近采购,化验室人员定期到砂岩矿取样检验,进行指导开采,要求进厂砂岩SiO2含量在72-73%之间,一旦检验结果超出此范围,及时通知砂岩矿调整搭配比例,确保砂岩成分被动严格控制在较小的范围内,砂岩粒度控制在<25mm。
我公司主要从两家采购,严格控制进厂水分和品位。
2)充分发挥均化设施作用。
我公司有Ф80m石灰石预均化库,公司要求堆料层数达到500层以上,并进行往复式布料,整个预均化库储存量不低于15000t;对砂岩的做法是,在矿点附近设不低于6000t储存量露天堆场,再输送到我公司砂岩堆棚,进行二次倒堆,在公司堆棚内储存量也低于6000t,再通过皮带输送砂岩预均化库再次均化;对铁粉的做法是,每批铁粉到公司露天堆场后,进行拢堆,再通过皮带输送铁粉预均化库。
第8章 预分解窑调节与控制

机冷却风机鼓风量,窑头负压减小,甚至出现正压。
一般采用调节篦冷机剩余空气排风机(窑头主排风机)风量 的方法控制窑头负压在规定的范围内。
② C1、C5筒出口负压
预热器各部位负压的测量,是为了监视各部分阻力,以判断
生料喂料量是否正常、风机闸门是否开启、防爆风门是否关闭以 及各部分有无漏风或者堵塞情况。 当最上一级旋风筒负压升高时,首先要检查旋风筒是否堵塞 ,如正常,则结合气体分析结果确定排风是否过大;当负压降低
炉下部
炉中部
气温
约850℃
约880℃
料温
820℃,上升趋势
850℃,稳定
煤粉燃烧与生料分解情况
燃烧放热速度>分解吸热速度
燃烧放热速度=分解吸热速度
炉上部
炉出口
850~900℃
850~900℃
880℃,开始下降
870℃,下降趋势
燃烧放热速度<分解吸热速度
燃烧放热速度<分解吸热速度
④ C1筒出口气体温度
① 电流轨迹平稳
窑传动电流很平稳、所描绘出的轨迹很平,这表明窑系统很 平稳、热工制度很稳定。
② 电流轨迹很细
窑传动电流所描绘出的轨迹很细,说明窑内窑皮平整或虽不 平整但在窑转动过程中所施加给窑的扭矩是平衡的。
③ 电流轨迹很粗
窑传动电流描绘出的轨迹很粗,说明窑皮不平整,在转动过 程中,窑皮所产生的扭矩呈周期性变化。
分解炉)系统的热力分布状况。
窑尾温度高:有利于过渡带内物料的迅速分解,缩短过渡带
的长度,但窑尾烟室、上升烟道及C4、C5筒易结皮堵塞。
窑尾温度一般控制在950~1100℃,目前控制温度普遍偏
高,尤其对于窑气入炉流程。
③ 分解炉或C5筒出口气体温度
提高2500td新型干法窑熟料产量的措施
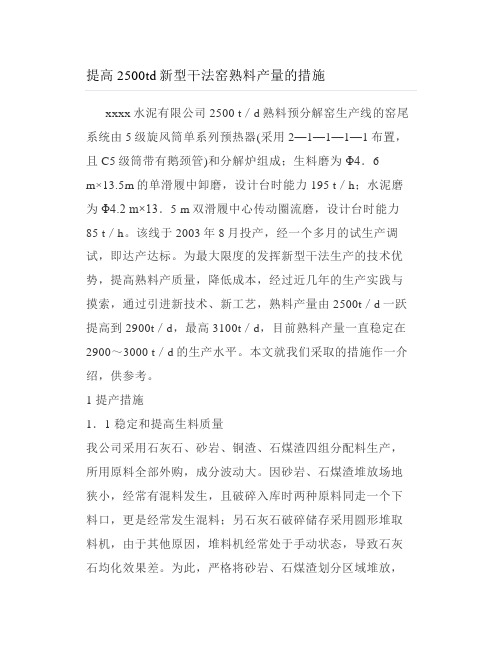
提高2500td新型干法窑熟料产量的措施xxxx水泥有限公司2500 t/d熟料预分解窑生产线的窑尾系统由5级旋风筒单系列预热器(采用2—1—1—1—1布置,且C5级筒带有鹅颈管)和分解炉组成;生料磨为Φ4.6m×13.5m的单滑履中卸磨,设计台时能力195 t/h;水泥磨为Φ4.2 m×13.5 m双滑履中心传动圈流磨,设计台时能力85 t/h。
该线于2003年8月投产,经一个多月的试生产调试,即达产达标。
为最大限度的发挥新型干法生产的技术优势,提高熟料产质量,降低成本,经过近几年的生产实践与摸索,通过引进新技术、新工艺,熟料产量由2500t/d一跃提高到2900t/d,最高3100t/d,目前熟料产量一直稳定在2900~3000 t/d的生产水平。
本文就我们采取的措施作一介绍,供参考。
1 提产措施1.1 稳定和提高生料质量我公司采用石灰石、砂岩、铜渣、石煤渣四组分配料生产,所用原料全部外购,成分波动大。
因砂岩、石煤渣堆放场地狭小,经常有混料发生,且破碎入库时两种原料同走一个下料口,更是经常发生混料;另石灰石破碎储存采用圆形堆取料机,由于其他原因,堆料机经常处于手动状态,导致石灰石均化效果差。
为此,严格将砂岩、石煤渣划分区域堆放,且控制堆放量并及时破碎后入各自的储存库,以最大程度避免了混料现象发生;同时,行车抓料堆放时采用抛撒堆料,堆取料机以自动状态堆料。
使石灰石均化效果更佳。
这样使原料质量得到控制,从而能稳定和提高入窑生料成分的波动。
1.2 控制原燃料中有害成分的含量原料、原煤中的有害成分,对预热器的结皮影响较大,尤其这些有害成分在回转窑—预热器的循环大量富集,形成硫钾钙石、灰硅钙石和硫硅钙石等低熔点易结皮的矿物质,加速窑尾上升烟道、分解炉及C4,C5级筒结皮过厚,影响系统通风,产量降低。
我公司曾经出现几次原煤中SO3含量过高[w(SO3)最高达到1.8%],造成预热分解系统结皮严重而堵塞。
预分解窑操作体会(精简版)

预分解窑操作体会预分解窑操作体会预分解窑操作体会]在水泥厂中,烧成车间相对而言要比其他车间复杂得多,预分解窑操作体会。
这主要是孰料烧成有严格的热工制度,要求风、煤、料、窑速进行合理匹配,出现异常情况要及时调整。
否则,短时间内影响一点产量事小,如果处理不当还会出现红窑或预分解系统堵塞等问题。
通过生产实践体会到,当一个好的操作员,既要解决在中控窑操作自如,判断正确、果断,又要解决好现场出现的实际问题,实属不易。
下面就预分解窑的操作谈一些体会,供大家参考。
1、看火操作的具体要求1)作为一名回转窑操作员,首先要学会看火。
要看火焰形状、黑火头长短、火焰温度及是否顺畅有力,要看熟料结粒、带料高度和翻滚情况以及后面来料的多少,要看烧成带窑皮的平整度和厚度等。
2)操作预分解窑窑坚持前后兼顾,要把预分解系统情况与窑头烧成带情况结合起来考虑,要提高窑的快转率。
在操作上,要严防大起大落、顶火逼烧,要严禁跑生料或停窑烧。
3)监视窑和预分解系统的温度和压力变化、废气中2和含量变化和全系统热工制度的变化。
要确保燃料的完全燃烧,减少黄心料。
尽量使熟料结粒细小均齐。
4)严格控制熟料F-a含量小于1.5℅,立升重波动±g/L 以内。
5)在确保孰料产量的前提下,保持适当的废气温度,缩小波动范围,降低燃料消耗。
6)确保烧成带窑皮平整,厚薄均匀,坚固。
操作中要努力保护好窑衬,延长安全运转周期。
2、预热器系统的调整2.1撒料板的调节撒料板一般都置于旋风筒下料的底部。
经验告诉我们,通过排灰阀的物料都是成团的,一股一股的。
这种团状或股状物料,气流不能带起而直接入旋风筒中造成短路。
撒料板的作用就是将团状或股状物料撒开,是物料均匀分散地进入下一级旋风筒进口管道的气流中。
在预热器系统中,气流与均匀分散物料间的传热主要在管道内进行的。
尽管预热器系统的结构形式有较大的差别,但下面一组数据基本相同。
一般情况下,旋风筒进出口气体温度之差在℃左右,出旋风筒的物料温度比出口气体温度低10℃左右。
2500td预分解窑熟料产质量的提高与稳定
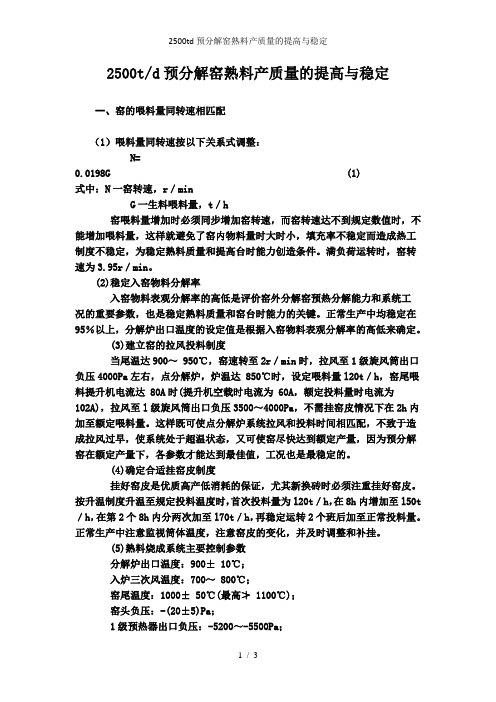
2500t/d预分解窑熟料产质量的提高与稳定一、窑的喂料量同转速相匹配(1)喂料量同转速按以下关系式调整:N=0.0198G (1)式中:N一窑转速,r/minG一生料喂料量,t/h窑喂料量增加时必须同步增加窑转速,而窑转速达不到规定数值时,不能增加喂料量,这样就避免了窑内物料量时大时小,填充率不稳定而造成热工制度不稳定,为稳定熟料质量和提高台时能力创造条件。
满负荷运转时,窑转速为3.95r/min。
(2)稳定入窑物料分解率入窑物料表观分解率的高低是评价窑外分解窑预热分解能力和系统工况的重要参数,也是稳定熟料质量和窑台时能力的关键。
正常生产中均稳定在95%以上,分解炉出口温度的设定值是根据入窑物料表观分解率的高低来确定。
(3)建立窑的拉风投料制度当尾温达900~ 950℃,窑速转至2r/min时,拉风至1级旋风筒出口负压4000Pa左右,点分解炉,炉温达 850℃时,设定喂料量l20t/h,窑尾喂料提升机电流达 80A时(提升机空载时电流为 60A,额定投料量时电流为102A),拉风至l级旋风筒出口负压3500~4000Pa,不需挂窑皮情况下在2h内加至额定喂料量。
这样既可使点分解炉系统拉风和投料时间相匹配,不致于造成拉风过早,使系统处于超温状态,又可使窑尽快达到额定产量,因为预分解窑在额定产量下,各参数才能达到最佳值,工况也是最稳定的。
(4)确定合适挂窑皮制度挂好窑皮是优质高产低消耗的保证,尤其新换砖时必须注重挂好窑皮。
按升温制度升温至规定投料温度时,首次投料量为l20t/h,在8h内增加至l50t /h,在第2个8h内分两次加至l70t/h,再稳定运转2个班后加至正常投料量。
正常生产中注意监视筒体温度,注意窑皮的变化,并及时调整和补挂。
(5)熟料烧成系统主要控制参数分解炉出口温度:900± 10℃;入炉三次风温度:700~ 800℃;窑尾温度:1000± 50℃(最高≯ 1100℃);窑头负压:-(20±5)Pa;1级预热器出口负压:-5200~-5500Pa;入窑物料分解率:>95%。
窑预分解系统的问题分析及改进措施

窑预分解系统的问题分析及改进措施摘要:我厂1号RSP窑经过6年多的运转,系统耐火材料呈现出不同程度的磨损、烧坏现象。
SB室下部掉砖,进而壳体烧损;SC室用风不良,导致边壁物料保护层不均衡,局部衬砖磨损严重;斜烟道及鹅颈管侧墙衬砖垮落,由于鹅颈管结构缺陷,经常结皮和堆料;MC室断面物料分布不均,物料稀相区炉壁烧损,直至筒体严重变形;因窑尾缩口处风速低,喷腾能力减弱而塌料;高温级旋风筒分离效率低,导致物料大量返回,内循环增加等。
本文依据热工标定结果,对该预分解系统出现的问题进行分析,并提出改进措施。
1 RSP窑系统工况分析热工标定主要参数对比见表1、表2,窑尾高温区工艺流程见图1。
表1 预热预分解系统温度变化℃表2 RSP炉的分解进程变化注:1997年数据为南京化工大学硅酸地方国营工程研究所的热工标定结果,SC 室出口指斜烟道出进口等同于鹅颈管出口。
图1 窑尾高温区工艺流程1.1 三次风温度及其对SC室工况的影响由表1可见,三次风温度和入炉生料温度分别只有600℃和671℃。
入炉生料温度低主要是由于C4锥体及下料管增开人孔门较多,外漏风量和散热损失增加引起的,通过加强管理,隔热堵漏后完全可以解决;三次风温度目前基本稳定在560~580℃,提高的余地很小。
其原因是:我厂采用单筒冷却机,经过多年的运转,内部装置所遭受的磨损和腐蚀不断加剧,而且增加了砌筑耐火砖的长度,熟料停留时间短(约为30min),出机熟料温度高(~290℃),使热效率本身就不高的单筒冷却机热回收率进一步降低(1997年热工标定结果为56.6%)。
三次风温度是影响分解率和燃尽率的重要因素。
较低的三次风温度导致炉内煤粉着火速度减慢,形成滞后燃烧,特别是SC室内煤粉是在纯助燃空气中燃烧,助燃空气的温度在很大程度上决定了煤粉燃尽率,三次风温度低,即使分解炉多加煤,SC室内温度也不会高,反而会加剧煤粉滞后燃烧。
从表1和表2可以看出,SC室生料出口温度和分解率分别是948℃和43.4%,结合入炉生料表观分解率已达22.6%的实际情况,说明SC室内的分解反应极低,煤粉燃烧状况不理想。
9 预分解窑系统的调节与控制

• ⑤窑尾烟室废气温度控制:投料前应以窑尾废气温度为准, 按升温制度调整加煤量,投料初期可控制在950~1000℃ 范围内,当尾温超过1050℃时,窑头加煤必须及时采取措 施,并应检查窑喂料室和炉下烟道内结皮情况,如发现结 皮要及时清理。
• ⑥窑速控制:点火后当窑尾废气温度达到200℃以上时开 始间断转窑,窑尾温度达到700~800℃时按电气设备允 许最低转速连续转窑,到加料前窑速加快到1.8r/min,并 加大喂料、喂煤量,当窑产量达到接近设计指标时,窑速 应达到3.2~3.5r/min左右。
3.预分解窑自动控制系统
• 预分解窑的自动控制:通过自动化仪表和装置对 整个生产过程进行全面地监视、控制和管理, 特别是计算机控制技术的推广应用,对增加产 量、提高质量、减少劳动强度、提高工作效率、 降低消耗、增加经济效益、提高生产过程的控 制水平和企业现代管理水平发挥了重要的作用。
• 20世纪90年代初,集散控制系统在水泥厂 得以广泛的应用。
• g.在设定喂料量下进行投料。调整点火烟囱开度,使高 温风机口温度不超过400℃。
• 分解炉的控制:
• 由于三次风温和C4物料温度较高,煤粉在预燃炉 内可以稳燃,如煤粉仍不能稳燃,则需继续加油 助燃。通常预燃炉出口温度应控制900℃左右, 混合室出口温度应控制在870~890℃。随着预燃 炉燃烧稳定,即可断油。但要注意及时调整炉用 喷煤管的位置、SB室风量和喷煤管内外风比例, 防止预燃炉内无烟煤的燃烧温度过高,造成炉内 火砖损坏。
• ⑦窑筒体表面温度控制:间断转窑时应投窑筒体红外扫描 测温仪,控制在350℃以下,最高不得超过400℃。
• ⑧加煤量的控制:窑尾烟室温度350℃以上时可开始窑头 加煤,实现油煤混烧,煤量约1t/h左右,不可太小,注意 调整窑头一次风机转速和多通喷煤管内外风比例来保持火 焰形状。
- 1、下载文档前请自行甄别文档内容的完整性,平台不提供额外的编辑、内容补充、找答案等附加服务。
- 2、"仅部分预览"的文档,不可在线预览部分如存在完整性等问题,可反馈申请退款(可完整预览的文档不适用该条件!)。
- 3、如文档侵犯您的权益,请联系客服反馈,我们会尽快为您处理(人工客服工作时间:9:00-18:30)。
提高早期预分解窑产量的措施
摘要:提高早期预分解窑产量的措施
我国在上世纪80年代引进和自行设计开发的一些预分解窑生产线,限于当时的技术水平,存在一些缺点与不足。
其中有的已在生产实践中解决,如原来的预分解窑设计为烧油或优质煤,因此分解炉偏小,许多厂已将分解炉加高加大,以改善煤粉特别是劣质煤的燃烧条件;对分解炉内气流的流速、流场分布、燃料的悬浮和燃烧,生料的悬浮和分解的研究和认识也已深化,生料入窑的分解率也逐渐提高。
但有些生产线至今仍沿用老的喷煤管,回转窑仍维持着原来较低的转速。
据报道[1],广东地区上世纪80年代及90年代初建设的4家预分解窑的转速分别为2.87r/min、2.5r/min、3.0r/min 及2.5r/min,明显低于当今预分解窑3.0~3.5r/min的水平。
当时的喷煤管虽也是三风道的,但其一次风大多数在15%左右,而目前的三风道喷煤管的一次风量多在10%以下,一般为5%~6%。
由于一次风量减少可提高火焰温度,即提高熟料煅烧温度,而窑的转速提高可提高回转窑的产量。
因此,笔者认为通过改用一次风量小的大推力高风速喷煤管和提高回转窑转速可提高早期建设的预分解窑的产量。
1 提高预分解窑转速的技术可行性
早期建设的预分解窑窑速可以提高,其关键是目前的许多技术使预分解窑的火焰温度提高,另一个因素是分解炉技术成熟,生料入窑分解率提高。
1.1 更换新的喷煤管,火焰温度可以提高
早期建设的预分解窑所用的喷煤管一次风量占总风量的15%左右。
当今的喷煤管多为大推力、小风量、高风速的三风道或四风道喷煤管,其一次风用量最少的只占总风量的5%~6%,煤风的风速约为20m/s,而内、外风的风速达170m/s,国外有些喷煤管的外风风速更高,甚至高达350m/s,加上结构合理,黑火头短、火焰短粗、火焰温度高。
由于一次风温只有50℃左右,而二次风温一般都在1000℃以上甚至更高,一次风的减少将提高火焰温度。
加上火焰短粗,热力集中,物料煅烧温度提高,熟料形成反应速度加快。
据文献[2],熟料烧成阶段,C3S的形成主要是CaO在高温液相中溶解以Ca2+
形式在液相中向C2S扩散来完成。
C3S形成过程中,Ca2+的扩散系数为(2.62~5.31)×10-5cm2/s,C3S 的结晶速度为5×10-5cm/s,CaO的溶解速度只有(6.95~22.5)×10-6cm/s,因此C3S的形成被CaO的溶解过程所控制。
CaO的溶解和Ca2+的扩散均与温度有关。
温度提高CaO的溶解速度加快,Ca2+的扩散速度也加快。
当煅烧温度从1400℃分别提高到1450℃和1500℃时,0.1mm粒径的CaO的溶解完毕的时间从15min分别降至5min和1.8min;0.05mm粒径的则从5.5min分别下降至2.3min和1.7min;而
0.025mm粒径的则从1400℃的3min下降至1450℃的1min。
从上述数据估计,温度每提高50℃,CaO溶解时间约减少66%,即溶解时间减少至原来的1/3。
由于CaO溶解时间缩短,C3S形成速度将大为加速。
煅烧温度提高,也使Ca2+的扩散速度加快。
如当煅烧温度从1400℃提高至1450℃时,Ca2+在饱和溶液中扩散系数从3.77×10-5cm2/s增大至5.31×10-5cm2/s,增大了40%,这意味着Ca2+在液相中扩散时间缩短了40%,也就意味着C3S形成速度加快。
C3S形成时间缩短。
因此,物料在窑内停留的时间可以缩短,回转窑的转速可以加快。
目前,新设计的预分解窑正常运行转速多在3.2r/min,甚至高达3.5r/min。
1.2 篦冷机用厚料层,提高一室风压使二次风温提高,从而提高火焰温度
篦冷机用厚料层操作,并将一室或二室的风压提高,可提高二次风温。
例如,广西鱼峰水泥有限公司[3]将篦冷机二室的风压从原来的5.6~5.9kPa提高至7.8kPa,二次风温达1000℃,三次风温达850℃。
江西万年青水泥有限公司[4]4号窑曾出现黄心料,采用厚料层并将一室风压从4.2kPa提高至4.6kPa,提高了二次风温,解决了产生黄心料的问题。
二次风温提高,使火焰温度提高,从而为加快窑速提供条件。
1.3 生料入窑分解率提高
早期建设的预分解窑,由于对分解炉内燃料的悬浮、燃烧以及生料的悬浮分解技术认识不够,致使当时的生料入窑分解率要求只大于85%即可。
随着对分解炉技术认识的深入,分解炉的操作技术日趋成熟,现在生料入窑分解率都在90%以上,不少已达95%以上。
生料入窑分解率的提高,将有利于窑的转速提高。
2 提高预分解窑转速的措施
2.1 更换喷煤管
如前所述,要想提高回转窑转速,必须用新的三风道或四风道喷煤管代替老的喷煤管。
所选用的喷煤管,其一次风量应尽可能小,最好达5%~6%。
另外,其结构应有利于火焰的调节,应该推力大,火焰短粗,这样才能提高火焰温度。
目前,耐火砖的耐火度已有较大的提高,只要维护好窑皮,短粗的火焰对耐火砖的寿命不会造成危害。
2.2 更换回转窑主传动的减速机
为提高窑速,应更换减速机的小齿轮,最好使回转窑的最高转速达3.5r/min甚至更高些。
回转窑的转速除了与火焰温度有关外,还与生料的易烧性以及配料方案有关。
各厂的情况不尽相同,应根据具体情况具体分析。
对生料易烧性好的、直径大的回转窑,转速可快些,其转速可高达3.5r/min;对生料易烧性差的、直径小的回转窑,转速宜慢些。
据介绍[3],广西鱼峰2000t/d用无烟煤煅烧熟料生产线在调试过程中窑速保持3.5r/min,坚持薄料快转,很快达标达产。
据介绍[3],窑速每增加0.1r/min,喂料量增加5t/h,相当于每小时产量增加3t左右,按83.3t/h熟料计,产量增加3.6%。
若按早期建设的预分解窑转速为2.8r/min计,当窑速分别提高到3.0r/min和3.2r/min时,在保持窑内物料填充率不变的前提下,台时产量可分别增加7%和14%。
按增加产量14%计,2000t/d生产线的熟料产量可达2280t/d,而日产4000t的生产线熟料产量可达4560t/d。
回转窑转速的提高还可使物料受热均匀,从而使熟料的质量均匀。
由于窑的转速加快,窑用电动机所消耗的功率也相应增大。
若原有电动机功率有一定的储备能力,可不更换,否则,应更换电动机。
2.3 其它设备的改造或更换
2.3.1 冷却机
回转窑熟料产量增加要求冷却机冷却能力相应增大。
在产量增加15%以内,若冷却机的料层
<500mm,则可将料层增加至600mm左右,而不需对冷却机进行改造。
2.3.2 煤磨系统
回转窑产量增加,若熟料热耗不变(产量增加,热耗可能会稍微降低),要求煤粉用量增加。
煤磨的设计一般都有一定的储备能力,若产量增加幅度在15%以内,可通过降低入磨煤的粒度,改善磨机研磨体级配,降低入磨煤的水分(或提高入磨热风温度)等措施,提高煤磨产量,满足煤粉用量增加的要求。
2.3.3 窑尾排风机
更换喷煤管提高回转窑转速,熟料产量提高,要求窑尾排风能力大为增加。
更换喷煤管使一次风量减少,要求二次风相应增加。
例如,一次风从15%减少到6%,则二次风要求相应增加9%;若窑的产量增加15%,则窑尾排风机风量大约要增加24%。
通过减少系统漏风,特别是改善窑头和窑尾的密封,可望减少废气量。
是否要更换窑尾排风机取决于一次风量减少的程度和回转窑产量增加的幅度。
2.3.4 旋风筒及其连接管道
窑的产量增加使废气量增大,旋风筒截面风速和管道风速相应增大,系统阻力增加,要求窑尾风机抽力增大。
若原来设计的旋风筒截面风速和管道风速均不高,那么可通过选用保温材料(如硅酸钙板)和减薄耐火砖厚度等措施增大旋风筒有效内径,使旋风筒截面风速不致过大。
2.3.5 窑尾电除尘器
窑尾废气量增大,要求窑尾电收尘处理能力增大。
若粗略地按产量增加与废气量增加的比例相同考虑,在产量增幅<15%的情况下,可望增大废气通过电除尘器的风速而不需增大电除尘器的收尘面积。
3 结束语
我国早期建设的预分解窑生产线,窑内煅烧温度偏低,窑速偏慢,建议更换一次风量小、推力大的新型喷煤管,提高窑内煅烧温度,加快回转窑转速,以便提高其产量。
新闻来源:中国水泥网。