MIL-DTL-16232G磷酸锰系磷酸锌系厚膜磷化工艺中文翻译
MIL-DTL-16232G磷酸锰系磷酸锌系厚膜磷化工艺中文翻译

有效性说明MIL-DTL-16232G通知12013年3月14日详细说明书磷酸锰基磷酸锌基磷化处理层2000年1月7日提出的MIL-DTL-16232G已经通过审定并按照要求交付使用。
管理人准备活动陆军—AR 军队—AR海军—AS空军--11审核单位陆军—EA注:无测量敏感性MIL-DTL-16232G2000-1-7代替DOD-P-16232F1978-11-7详细说明书磷酸锰基、磷酸锌基重金属(厚膜磷化)磷化膜本规范已通过国防部所有部门和机构的批准1.范围1.1 范围本规范涵盖两种类型的黑色金属磷化工艺,浸入法制备重金属磷化膜。
膜组成为磷酸锰、磷酸锌或在有特殊规定时的补充处理成分(见6.1)1.2 分类按照6.2的规定,膜层类型如下M 类磷酸锰基磷化液第1级按规定进行辅助防护处理或辅助膜层第2级遵照MIL-PRF-16173,3级或MIL-PRF-3150条款采用润滑油的辅助处理第3级无辅助处理第4级化学转换(按照规定可能需要染色)不需要辅助涂层的Z 类磷酸锌基磷化液第1级按规定进行辅助防护处理或辅助膜层第2级遵照MIL-PRF-16173,3级或MIL-PRF-3150条款进行辅助防护处理第3级无辅助处理第4级化学转换(按照规定可能需要染色)不需要辅助涂层的任何有益的建议(更改、添加或删除)或其他可能用于改进本条款的相关数据请联系美国军用武器装备研究、开发工程中心指挥官。
收件人:AMSTA-AR-QAW-E, Picatinny Arsenal,新泽西州07806-5000,在本文件的后面附上标准化文档改进意见并以书信的形式或者在邮件署名的方式寄给我们。
发行说明A:获准公开发行,无限制发行。
2.引用文件2.1 概述本节所列文件是本规范第3、4章的指定使用文件。
本节不包括该规范内其它章节引用文件或推荐的附加信息或作为的范例。
尽管为了完善本表做了很多的努力,文件使用者仍需确保满足本规范第3、4节所有指定的文件要求,无论该条款是否被列出。
磁性材料锌锰系磷化处理工艺

磁性材料锌锰系磷化处理工艺
一、处理工艺:
超声波水洗→除油活化→水洗→中和→水洗→磷化→水洗→吹干
二、工艺参数:
1.除油活化:药液配制:BW-500C 钢材酸性除油剂C3%浓度
磷酸(85%工业级) 6-8%浓度
工作温度:10℃以上
处理时间:超生波清洗 2-3分钟
浸泡: 8-10分钟,有超声波水洗时降低到5-8分钟
2.水洗:处理时间:30秒
3.中和:药液配制:纯碱1%浓度
处理时间:1-2分钟
4.水洗:处理时间:30秒
5.磷化:药液配制:
BW-231 特种材料锌锰系磷化液稀释12-15倍(6.7-8%浓度)
工作温度:35-45℃
处理时间:10-15分钟
6.水洗:处理时间:30秒
7.吹干:边吹边用吸水性较好不脱毛的毛巾擦拭,以免留下水渍。
三、注意事项:
1、清洗所用的清洗水要经常更换,保持水体干净。
2、磷化液工作液的pH值在2.0-2.5范围内,pH超过2.5时要及时补加
药液;也有的单位中间不补加药液,一直使用到药液报废,再重新配
制;磷化反应时间过长会造成膜层粗糙,所以一般不等到反应停止。
3、超声波水洗用于除去表面的加工粉尘,可以降低除油活化时间。
4、磷化液浑浊时及时沉淀清理沉渣。
5、发现磷化膜不均匀时,调整磷化液或补加除油活化液的相关药液。
磷化膜——材料表面与界面

磷化膜汽车的喷涂工艺或者喷漆工艺,集中体现了材料的表面与界面的知识,而磷化膜就是其中一个对喷漆工艺有很大影响的部分。
磷化(Phosphorization)是一种化学与电化学反应形成磷酸盐化学转化膜的过程,所形成的磷酸盐转化膜称之为磷化膜。
1、磷化过程的反应机理磷化过程的反应机理相对比较复杂,目前尚无统一的完整的理论。
磷化过程可归纳为化学反应和电化学反应,不同的磷化体系,不同的基材,磷化反应机理不尽相同,但大都包括以下几个步骤:(1)基体金属溶解:当工件浸入磷化液时,磷化液中游离的磷酸把工件表面的铁溶解并放出氢气,降低了磷化界面的酸度,这是磷化反应的起点,可净化金属表面,破坏磷化槽液中的水解平衡,使水解反应向生磷化膜方向进行,界面处浓度降低。
Me-2e→Me2+2H++ 2e→2 [H]→H2↑(2)促进剂加速:铁溶解过程释放出的氢气吸附在工件表面上,阻止了磷化膜的形成,为加速反应,常加入氧化型促进剂,去除氢气,界面处H+浓度可进一步降低。
[o]+[H]→[R]+H20(3)磷酸根的多级离解:磷化液的基本成分是一种或多种重金属的酸式磷酸盐,其分子式一般用Me(H2P04)2, Me通常指锌、铁、锰等金属离子。
这些酸式th溶于水,在一定条件发生水解反应,产生游离磷酸。
由于界面处H+浓度急剧下降,导致磷酸根离子各级离解平衡向右移动,最终离解出PO43-。
Me(H2PO4)2→MeHPO4+H3PO43 MeHPO4→Me3(PO4)2+ H3PO4H3PO4→H2PO4-+H+→HP042-+2H+→PO43-(4)磷酸盐沉淀结晶成膜当溶液中离解出的PO43-与界面处的金属离子达到溶度积常数Ksp时,就会形成磷酸沉淀结晶成膜。
3Zn2++2 PO43- +4H20→Zn3 (PO4)2·4H202Zn2++Me2++2 P043- +4H20→Zn2Me (P04)2·4H20 例如上述磷酸锌生成的Zn3(PO4)2·4H20和Zn2Fe(PO4)2·4H20的结晶体,其中Me2+代表的是其他金属离子。
锌锰系电解磷化膜工艺的研究
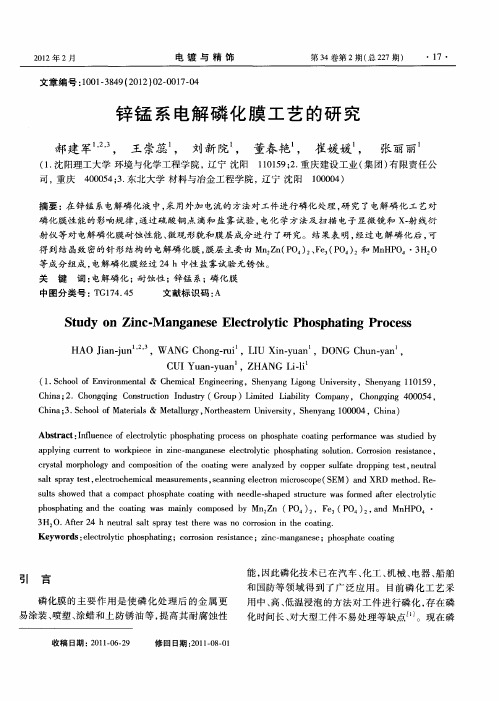
20 1
2 40
0
0
mm×1mm。磷 化 处 理 工 艺 流 程 为 : 样 打磨 一 常 试 温 水洗 一 化学 除 油 ( % 金 属 洗 涤 剂 ,5o 洗 净 为 4 7 C,
止 ) 热水 洗 ( 0— 0 ℃ ) 常 温 水 洗 一 酸 洗 ( % 一 5 6 一 5 H 14 ) 常 温水 洗一 电解 磷 化 ( 0— 0 g L马 C ,0 一 6 7 / 日夫 盐 ;0~6 / 5 0 g L硝 酸 锌 ; 3~5 g L N F; / a 2~1 0 L 硝酸 锰 ; 3 g L添 加 剂 A; 量 添 加 剂 B) 1~ / 适 一 常温 水洗 一 吹干 。
21 年 2 02 月
电 镀 与 精 饰
第 3 卷第 2 总 27 4 期( 2 期)
・ 7・ l
文章 编 号 :0 13 4 ( 0 2 0 -0 7 0 1 0 —8 9 2 1 ) 2 0 1 -4
锌 锰 系 电解 磷 化 膜 工 艺 的研 究
郝建 军 , 王 崇蕊 刘新 院 董春 艳 崔媛媛 张丽丽 , , , , ,
,
sl sry eteet c e cl esrmet,cn ige c o i ocp ( E at pa s,l r h mi aue ns sa nn l t nm c soe S M)a dXR to . e t co am er r n D me d R — h
s ls s o d t a o a tp s hae c a i g wi e d e s a e tu t e wa o e f r ee toy i u t h we h ta c mp c ho p t o tn t n e l —h p d sr cur sf r d a t lc r ltc h m e
锰系磷化说明书

锰系磷化说明书 The manuscript was revised on the evening of 2021高温锰系黑色磷化液说明书一/本品能在钢铁上形成一种晶体状的锰系磷化膜,这层磷化膜能提高工件的耐磨性和耐腐蚀性能,磷化膜具有很强的吸附性,当浸泡了合适的油后具有高效的耐磨损效果,主要由磷酸铁和磷酸锰组成。
这种处理工艺能降低工件如活塞,活塞环,衬垫,凸轮轴,推杠,马达座及类似承载表面的磨损。
其他优点可归纳如下:锰系磷化处理使运动工件迅速跑合,防止承载表面之间金属与金属的直接接触,不会出现划伤或粘结。
由于磷化膜吸油,增加了处理过的表面的润滑作用。
消除了金属在机械加工中留下的刮痕。
延缓了腐蚀作用,因此也可以用作防腐底层。
可适用于汽车,摩托车,船舶,等高速运转零部件的减磨自润滑功能膜层处理。
以及工具,刀刃及较高标准要求标准件的耐摩,耐腐蚀处理。
二.产品特性1.高倍浓缩酸性液体。
2.用于钢铁表面的防腐耐摩处理。
3.也可以用于压铸件的处理。
4.在钢铁表面形成一层黑色的磷酸锰盐层。
5.符合甚至超过国标盐雾实验。
6..环保.安全,操作方便,废水处理简单/三.作业管理标准:管理项目管理标准1.皮膜建浴浓度:1比5(20%)2.全酸度(TA) :祥见本公司内部说明3.游离酸(FA):祥见本公司内部说明4.温度(Temp) 92-98℃.5.时间(Time) 8-20分钟6.限更新周期 12个月四.工艺流程:1.除油(XH-400)--水洗—除锈—水洗—表调(XH-28)--磷化(XH-575)---水洗—干燥或脱水防锈油(XH-300)?五.及添加方法:1.使用仪器及试剂:吸球、吸管、烧杯、 NaOH、酚酞(PP)、溴酚蓝(BPB)2.测量方法:(1)全酸度(TA):取槽处理10mL加酚酞(PP)指示剂3-5滴,再用 NaOH滴定,颜色由无色变至粉红5-10秒不褪色,即为其终点,此时所消耗 NaOH之毫升数,即为其全酸度之度数。
锰系磷化厚度
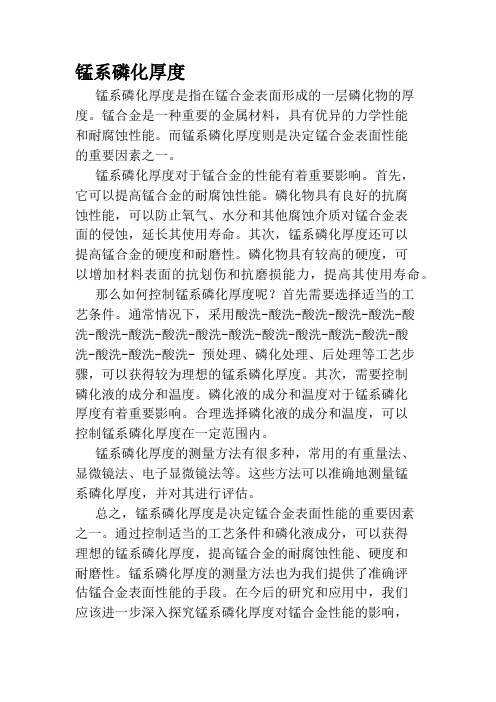
锰系磷化厚度锰系磷化厚度是指在锰合金表面形成的一层磷化物的厚度。
锰合金是一种重要的金属材料,具有优异的力学性能和耐腐蚀性能。
而锰系磷化厚度则是决定锰合金表面性能的重要因素之一。
锰系磷化厚度对于锰合金的性能有着重要影响。
首先,它可以提高锰合金的耐腐蚀性能。
磷化物具有良好的抗腐蚀性能,可以防止氧气、水分和其他腐蚀介质对锰合金表面的侵蚀,延长其使用寿命。
其次,锰系磷化厚度还可以提高锰合金的硬度和耐磨性。
磷化物具有较高的硬度,可以增加材料表面的抗划伤和抗磨损能力,提高其使用寿命。
那么如何控制锰系磷化厚度呢?首先需要选择适当的工艺条件。
通常情况下,采用酸洗-酸洗-酸洗-酸洗-酸洗-酸洗-酸洗-酸洗-酸洗-酸洗-酸洗-酸洗-酸洗-酸洗-酸洗-酸洗-酸洗-酸洗-酸洗- 预处理、磷化处理、后处理等工艺步骤,可以获得较为理想的锰系磷化厚度。
其次,需要控制磷化液的成分和温度。
磷化液的成分和温度对于锰系磷化厚度有着重要影响。
合理选择磷化液的成分和温度,可以控制锰系磷化厚度在一定范围内。
锰系磷化厚度的测量方法有很多种,常用的有重量法、显微镜法、电子显微镜法等。
这些方法可以准确地测量锰系磷化厚度,并对其进行评估。
总之,锰系磷化厚度是决定锰合金表面性能的重要因素之一。
通过控制适当的工艺条件和磷化液成分,可以获得理想的锰系磷化厚度,提高锰合金的耐腐蚀性能、硬度和耐磨性。
锰系磷化厚度的测量方法也为我们提供了准确评估锰合金表面性能的手段。
在今后的研究和应用中,我们应该进一步深入探究锰系磷化厚度对锰合金性能的影响,以提高锰合金的应用价值和推动相关领域的发展。
表面磷化-皂化作业指导书

表面磷化—皂化作业指导书本作业指导书适用于表面处理作业班对紧固件产品进行表面磷化或皂化处理工序的指导。
磷化膜多孔,材料经磷化—皂化后可吸附大量的润滑油而减少磨檫,对原材料改制及半成品勒光、缩杆起到很好的润滑作用,成品表面防腐、耐蚀耐磨性能尤为显著。
一、表面磷化—皂化工艺流程及要点:〈一〉工艺要点:1、磷化:也称磷酸盐处理,是将工件置于中温锌钙系磷化液(本公司所用磷化液)中,在短时间内工件表面形成一层浅灰色至深灰色、难溶于水、细而致密的磷酸盐薄膜—锌磷化膜的过程。
2、皂化:是将已磷化好的工件置于含有16-18碳的饱和脂肪酸皂、减磨极压剂及助剂的拉拔润滑剂皂液中,皂液中的以上成份与工件表面的锌磷化膜反应形成脂肪酸锌膜和皂膜层。
该膜层增加了工件加工变形区的塑性厚度,在模具孔和加工材料间形成润滑膜,可大幅度减小热量,防止金属烧结、熔粘等;由于在拉模和拉件间它能起到减磨介质和塑性作用,从而提高拉拔产品的表面光洁度和加工精度,减少拉拔工具和拉拔模间的磨损并防止损伤。
本品易从工件表面除掉,对产品热处理和退、回火质量无不良影响。
〈二〉工艺流程:1、磷化:工件人工预处理—除油脱脂—水洗—酸洗除锈—水洗—冲洗—磷化—水洗(80℃以上)—干燥—上油(油温150℃以下)2、皂化:工件人工预处理—除油脱脂—水洗—酸洗除锈—水洗—冲洗—磷化—水洗—皂化—干燥二、磷化—皂化作业〈一〉准备工作1、设备检查:作业前对所用作业设备进行全面检查,检查作业设备是否完好,若有问题应及时排除。
2、阅读工艺文件和生产指令:接到任务后,应仔细阅读工艺文件和生产指令,按照工艺流程进行作业按排,并保持工艺文件和生产指令的清洁和完整。
3、原料准备:按照生产指令的要求,根据产品数量的多少,准备相应的化工原料,尽可能做到化工原料不浪费。
4、穿戴和准备必要的安全防护用品和工位器具,准备作业。
〈二〉、磷化作业1、除油:对产品表面有油的产品,必须在除油槽中充分除油。
机柜之酸洗、磷化、热镀锌等工艺详解

机柜之酸洗、磷化、热镀锌等工艺详解本文是对网络服务器机柜生产过程中所采用的酸洗、磷化、热镀锌等流程的详细描述,希望对有兴趣了解网络服务器机柜如何生产的朋友有些许帮助。
~_~酸洗工艺酸洗工艺的酸洗液一般为多种酸的混合物,主要有硫酸、硝酸和氢氟酸等,这些混合酸的腐蚀性很强,同时具有很强的氧化性、较高的腐蚀介质的温度,这对防腐材料的耐蚀性能提出了很高的要求。
不锈钢酸洗生产线工艺从生产到废水废气回收系统,各个环节都存在很强的腐蚀状态,因此防腐材料选择的好坏直接关系到设备、车间地坪、地沟、废水废气的环保回收系统等处的正常使用。
如何对酸洗项目防腐进行选材呢?首先是玻璃钢管道和贮罐的结构及原材料选择,其次是车间地坪、设备基础防腐蚀一般采用树脂砂浆地坪结构。
玻璃钢管道和贮罐的结构及原材料选择。
酸洗项目中所用的贮罐和管路系统及酸雾回收系统现在基本选用玻璃钢材质,结构为防渗层+防腐层+结构强度层。
一般情况下防渗层和防腐层至少厚6~8毫米。
树脂选用合适的耐腐蚀环氧乙烯基树脂,专家介绍说--在介质为非氧化性酸、温度条件不是很高时,宜选用双酚A环氧乙烯基树脂;在氧化性酸、温度条件要求高时,宜选用酚醛环氧乙烯基树脂。
为了降低成本结构层大都选用间苯不饱和聚酯树脂,厚度根据具体的结构设计计算。
混酸和废酸贮罐由于腐蚀介质比较复杂,一般选用PVDF/FRP复合罐,但复合罐间PVDF和玻璃钢的粘结是一个亟待解决的问题,而且价格较高造成成本的增加,宜选用海特酸树脂(791H)做为内衬防腐材料,能满足以上介质条件的防腐蚀要求。
车间地坪、设备基础防腐蚀一般采用树脂砂浆地坪结构,总厚度约为7-10毫米,结构为:底漆1-2道+玻璃钢(2布3油)隔离层+树脂砂浆层(5-7毫米)+面层(约1毫米)。
地坪、设备基础的防腐蚀树脂现在都采用环氧乙烯基树脂,但是在底漆的选择上施工单位还习惯采用环氧树脂做底涂材料,以增加树脂和基层的粘结性能。
环氧树脂一般会采用胺类固化剂,固化后表面有油性物质浮出,再和乙烯基树脂粘结时不能够很好的匹配,需要对固化后的表面进行处理方可进行后续的防腐蚀结构施工,若处理不好容易分层、开裂。
- 1、下载文档前请自行甄别文档内容的完整性,平台不提供额外的编辑、内容补充、找答案等附加服务。
- 2、"仅部分预览"的文档,不可在线预览部分如存在完整性等问题,可反馈申请退款(可完整预览的文档不适用该条件!)。
- 3、如文档侵犯您的权益,请联系客服反馈,我们会尽快为您处理(人工客服工作时间:9:00-18:30)。
有效性说明MIL-DTL-16232G通知12013年3月14日详细说明书磷酸锰基磷酸锌基磷化处理层2000年1月7日提出的MIL-DTL-16232G已经通过审定并按照要求交付使用。
管理人准备活动陆军—AR 军队—AR海军—AS空军--11审核单位陆军—EA注:无测量敏感性MIL-DTL-16232G2000-1-7代替DOD-P-16232F1978-11-7详细说明书磷酸锰基、磷酸锌基重金属(厚膜磷化)磷化膜本规范已通过国防部所有部门和机构的批准1.范围1.1 范围本规范涵盖两种类型的黑色金属磷化工艺,浸入法制备重金属磷化膜。
膜组成为磷酸锰、磷酸锌或在有特殊规定时的补充处理成分(见6.1)1.2 分类按照6.2的规定,膜层类型如下M 类磷酸锰基磷化液第1级按规定进行辅助防护处理或辅助膜层第2级遵照MIL-PRF-16173,3级或MIL-PRF-3150条款采用润滑油的辅助处理第3级无辅助处理第4级化学转换(按照规定可能需要染色)不需要辅助涂层的Z 类磷酸锌基磷化液第1级按规定进行辅助防护处理或辅助膜层第2级遵照MIL-PRF-16173,3级或MIL-PRF-3150条款进行辅助防护处理第3级无辅助处理第4级化学转换(按照规定可能需要染色)不需要辅助涂层的任何有益的建议(更改、添加或删除)或其他可能用于改进本条款的相关数据请联系美国军用武器装备研究、开发工程中心指挥官。
收件人:AMSTA-AR-QAW-E, Picatinny Arsenal,新泽西州07806-5000,在本文件的后面附上标准化文档改进意见并以书信的形式或者在邮件署名的方式寄给我们。
发行说明A:获准公开发行,无限制发行。
2.引用文件2.1 概述本节所列文件是本规范第3、4章的指定使用文件。
本节不包括该规范内其它章节引用文件或推荐的附加信息或作为的范例。
尽管为了完善本表做了很多的努力,文件使用者仍需确保满足本规范第3、4节所有指定的文件要求,无论该条款是否被列出。
2.2 政府文件2.2.1 规范、标准、手册以下标准、规范、手册构成本文件的扩展规范,除非另有规定,文件的条款罗列于国防部标准索引及补充规范中,并应用在招标文件内(见6.2)规范国防部MIL-PRF-3150 润滑油防腐剂媒介MIL-PRF-16173 防腐蚀化合物溶剂稀释冷态喷浆(除非另有说明,联邦和军事规格、标准和手册可从标准化文档桌上获得副本,大厦4层,罗宾斯大道700号,费城,宾夕法尼亚州 19111-5094)2.2 非政府出版文件以下文件形成该文件的扩展规范,除非另行说明,国防部采用的该文件条款均罗列于国防部规范标准索引的招标文件中(见6.2)。
美国试验材料学会(ASTM)ASTM B 117 盐雾试验ASTM F 519 机械法电镀氢脆测试、飞机维修化工方法(申请复印件请联系美国国家测试与标准协会,地址100Barr harbor drive, west conchohocken, PA 19428-2959)(非政府标准及其他出版物可以从制作或发行该文件的组织机构处获得,同样也可以通过图书馆或其它信息服务渠道)2.3 2.4 优先原则。
当该标准文本与引用文件发生冲突时,优先选择文本文件。
但是,除非有特殊说明,该文件不得取代应用法律和规则。
3 要求3.1产前检查除非另有规定(见6.2),零件需进行生产前检查并满足3.2程序要求。
化学品、测试方法和测试频率以及承包商商定的使用设备应当在合同提交管理人员45天内书面提交。
采购活动的书面批准将在45天内完成或在生产之前即可收到。
所有使用材料的确切名称连同制造商的名称应进行统一声明。
该程序包括一个详细的控制方法,包括时间、温度、pH及其它相关参数以确保符合规范的要求。
符合批准过程程序的不得进行未经事先书面批准的采购活动。
审批的过程中,材料和设备并不意味着验收时的结果。
无论新材料或工艺的批准,该磷化膜应符合本规范的所有适用规定。
3.2 过程。
磷化膜将根据控制和如下所述分阶段进行。
一个单一的承包商应当履行包括清洁和涂层加工的所有阶段过程。
除非另有规定(见6.2),须在完成所有机械加工,成型,焊接,和消除应力热处理后进行磷化处理,但磷化工艺又在除氢处理之前。
3.2.1 槽液成分及控制槽液成分及槽液控制应参照如下要求:a 该槽液成分满足生产规范内所有要求类型的磷化膜b 槽液浓度,温度,零件的磷化浸入时间应满足本规范所有要求c 设备材料应具有抵抗磷酸盐溶液的材料组成,与溶液直接接触的材料应不含铜合金接头或钎焊等成分d 在磷化处理与随后的流动冷水洗之间磷化零件禁止干燥。
采用喷雾器喷雾或其它方式以避免零件干燥。
e 磷化零件供应商应永久保存磷化槽液记录单(见3.2.1),内含化学品的添加记录以及槽液分析结果f 磷化槽液成分控制应包括游离酸、总酸、亚铁离子的测定。
除非另有规定(见6.2),槽液游离酸、总酸、亚铁离子含量测试频率应在每次磷化处理之前及磷化4小时之后进行。
高生产率需要更为频繁的分析化验以保证规定限度内的过程控制。
g 槽液控制永久记录单的保存至少在1年以上(7年以上当有特殊规定时,见6.2)并根据要求提供给政府部门。
永久记录应以清晰可拷贝的类型或以采购活动可接受的电子媒介模式进行。
3.2.2 脱脂应当由脱脂溶剂、蒸汽、碱性或乳液清洗。
使用碱性或乳液脱脂时,应在喷砂处理前进行彻底的清洗和干燥。
3.2.2.1 喷砂除非零件图或合同上(见6.2)另有规定,重磷酸盐磷化前应进行喷砂处理.保证零件干燥条件下去除铁锈或剥落,喷砂采用沙砾,钢砂,氧化铝,玻璃珠,塑料珠或其他陶瓷类磨料为介质按照如下要求进行:a 零件喷砂前表面应无油渍,污垢及其它污染缺陷b 震动去毛刺不能代替喷砂处理c 喷砂处理后,零件上的残留磨料应用干燥的压缩空气清除d 当有其它规定,控制和完成喷砂处理时应采用一个网格大小的妥善保存RMS完成品。
e 磷化操作应当在喷砂处理完成后紧接着进行而不再有中间工序3.2.2.2 喷砂替代当零件图或合同另有规定替代磷化前的喷砂工序时,清洁处理后应紧接着进行彻底的冲洗。
如果后续没有以细化涂层表面晶体结构和去除该种溶液对磷化膜表面反应过程所产生影响(见6.5)的调整处理,磷化处理前不应使用强酸强碱性溶液。
当另有规定时,只要不显著降低膜层重量,不影响零件抗盐雾和氢脆性能,可以选择替代清洁的其它处理方式。
3.2.3 磷化磷化膜应按如下浸泡条件下适用:a M类型的磷化膜应为锰基磷酸盐膜,Z型磷化膜应为锌基磷酸盐膜。
用于制备磷化膜的所有材料都应按照采购活动中3.1的规定的进行审批。
b 槽液温度、浓度及零件浸泡处理时间应满足本规范所有要求3.2.4 水洗冷水洗应按照如下要求进行:a 浸洗水槽应得到连续补充,零件浸入应符合本规范的所有要求。
b 漂洗水的流动应可控可调(例如采用电导率控制仪)使其与生产速率相一致,以防止因时间超限而导致的膜层污染及其它不利影响。
c 喷淋漂洗可用于获得相同的最终产品质量d 所有项目零件(第4类除外)均需在流水冲洗后立即进行铬酸冲洗处理3.2.5 铬酸冲洗(第1,2,3类)第1,2,3级零件的铬酸冲洗应按照如下要求进行:a 最后一道冲洗采用铬酸或磷酸铬溶液,将大约300g的铬酸片溶于1000L水中制备所需的冲洗液。
槽液温度应控制在63℃~90 ℃(150°F ~200°F)之间。
b 冲洗液pH应控制在2~4之间,pH值的调节可以通过添加铬酸片或铬酸磷酸混合试剂而实现,每8小时至少完成一次pH值检测。
c 必须按时对槽液游离酸度和总酸度进行标准滴定或采用pH计进行读数测量,任何操作时间内确保槽液成分控制在规定限值内。
d 一旦槽液污染应立即放弃使用。
槽液至少每8小时完成一次酸度检测,当总酸度值大于7倍的游离酸度值时槽液应当废弃并停止使用。
e 零件在槽液浸洗时间至少60Sf 铬酸浸洗后,在辅助处理之前应进行零件的彻底干燥。
3.3 消应力处理除非另有规定,表面或整体洛氏硬度大于39的零件应当进行消应力处理。
包括渗碳、感应淬火、火焰淬火等处理而导致的硬度提升。
此外零件的研磨、冷成型、冷拔等加工都有可能导致残余应力,应采用加热的方式进行消应力处理。
消应力处理的温度为177℃~204 ℃(350°F ~400°F),该条件下每英寸厚度的零件热处理时间不少于1h,但小于1/2英寸的厚度的零件热处理时间不应少于半小时。
渗碳零件可选热处理温度是104℃~155 ℃(225°F ~275°F),时间为8h。
3.4 除氢热处理3.4.1 成膜后除非另有规定(见6.2),具有如表一所示硬度值的零件(含渗碳零件)在磷化后应进行除氢热处理。
3.4.2 烘烤后除非另有规定(见6.2),所有需要烘烤的批次零件或材料均应进行氢脆测试。
3.5 磷化膜重量在任何辅助处理之前的磷化膜重量应满足如下要求:a M类型的磷化膜最小质量要求为16g/m2(当有特殊规定时最小质量为11g/m2)b Z类型磷化膜最小质量要求为11g/m23.6 耐腐蚀试验没有做补充处理的磷化零件应进行盐雾试验测试,按照表2所示的测试时间内试样结果表面应无明显锈点3.7 后处理后处理应在磷化完成后进行,需要做补充处理的零件应做离心甩干或表面充分脱水以去除表面多余物,除非另有规定(见6.2)后处理油膜重量应充分满足3.7.2和3.7.4盐雾试验要求。
3.7.1锰系锌系磷化膜,第1类第1类锌系锰系磷化膜的后处理应按照6.2规定进行。
除非另有规定,单位面积上防锈油的重量要求不适用。
3.7.2 锰系磷化,第2类遵照MIL-PRF-3150或MIL-PRF-16173,第3级要求锰系磷化第2类要求在磷化膜上做浸渍润滑油的后处理。
除非另有规定(见6.2),零件表面单位面积防锈油油膜重量应达到48h盐雾条件下零件表面不出现宏观锈点的要求。
3.7.3 锰系磷化,第4类锰系磷化第4类为在无机盐试剂中发生化学转换后的锰基磷酸盐膜。
当有特殊规定时(见6.2)磷化膜化学转换后的零件需进行染色后处理。
第4类膜层在盐雾试验时应不出现锈点,经后处理后的膜层应至少满足72h盐雾条件下不出现锈点。
3.7.4 锌系磷化,第2类遵照MIL-L-3150或MIL-PRF-16173,第3级要求锌系第2类磷化膜应进行防锈处理。
除非特殊审批(见6.2)单位面积防锈剂重量应满足最小72h盐雾条件下试样表面无锈点。
3.7.5 锌系磷化,第4类锌系磷化第4类为在无机盐试剂中发生化学转换后的锌基磷酸盐膜。
当有特殊规定时(见6.2)磷化膜化学转换后的零件需进行染色后处理。
第4类膜层在盐雾试验时应不出现锈点,经后处理后的膜层应至少满足72h盐雾条件下不出现锈点。