数控车床刀塔机械传动研究
数控刀具机械传动数控技术.pptx
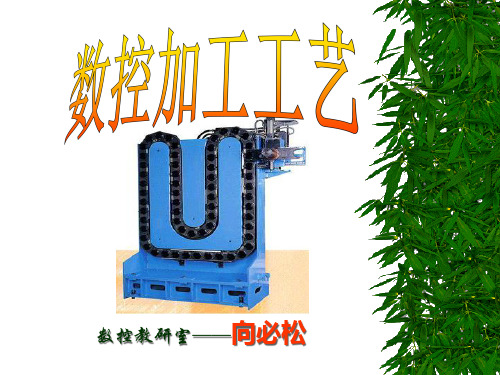
工具系统
由于在数控机床上要加工多种工件,并完 成工件上多道工序的加工,因此需要使用 的刀具品种、规格和数量较多。
为减少刀具的品种规格,有必要发展柔 性制造系统和加工中心使用的工具系统。
车削类工具系统(整体式)
整体式工具系统组成
车削类工具系统(整体式)
目前我国的加工中心采用TSG整体式工具系 统,其柄部有直柄(三种规格)和锥柄(四 种规格)两种,共包括16种不同用途的刀柄。
如金属、非金属,其硬度、刚铣削、镗削或粗加工、半精加工、 精加工和超精加工等。
加工工件信息
工件的几何形状、加工余量、零件的技术经济指 标。
刀具能承受的 切削用量
切削用量三要素,包括主轴转速、切削速度与切 削深度。
辅助因数
如操作间断时间、振动、电力波动或突然中断等。
要有在线监控及尺寸补偿系统
数控刀具的要求与特点
数控车床能兼作粗精车削,因此粗车时,要迁强度高、 耐用度好的刀具,以便满足粗车时大背吃刀量、大进 给量的要求。精车时,要选精度高、耐用度好的刀具, 以保证加工精度的要求。
此外,为减少换刀时间和方便对刀,应尽可能采用机 夹刀和机夹刀片。夹紧刀片的方式要选择得比较合理, 刀片最好选择涂层硬质合金刀片。目前,数控车床用 得最普遍的是硬质合金刀具和高速钢刀具两种。
数控车床刀塔原理及改造
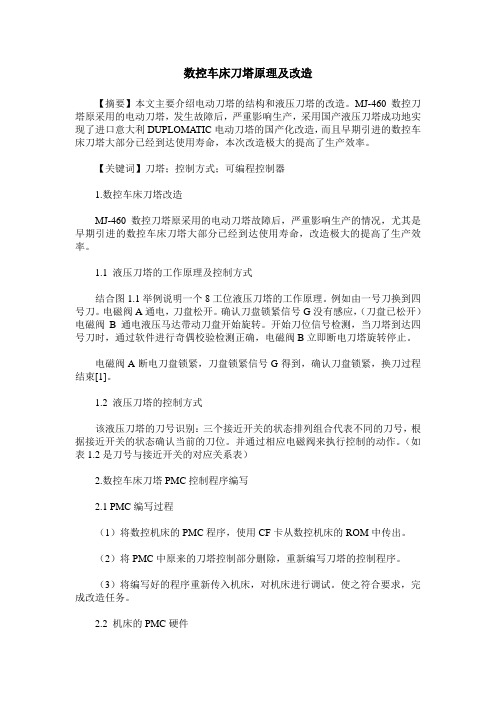
数控车床刀塔原理及改造【摘要】本文主要介绍电动刀塔的结构和液压刀塔的改造。
MJ-460数控刀塔原采用的电动刀塔,发生故障后,严重影响生产,采用国产液压刀塔成功地实现了进口意大利DUPLOMATIC电动刀塔的国产化改造,而且早期引进的数控车床刀塔大部分已经到达使用寿命,本次改造极大的提高了生产效率。
【关键词】刀塔;控制方式;可编程控制器1.数控车床刀塔改造MJ-460数控刀塔原采用的电动刀塔故障后,严重影响生产的情况,尤其是早期引进的数控车床刀塔大部分已经到达使用寿命,改造极大的提高了生产效率。
1.1 液压刀塔的工作原理及控制方式结合图1.1举例说明一个8工位液压刀塔的工作原理。
例如由一号刀换到四号刀。
电磁阀A通电,刀盘松开。
确认刀盘锁紧信号G没有感应,(刀盘已松开)电磁阀B通电液压马达带动刀盘开始旋转。
开始刀位信号检测,当刀塔到达四号刀时,通过软件进行奇偶校验检测正确,电磁阀B立即断电刀塔旋转停止。
电磁阀A断电刀盘锁紧,刀盘锁紧信号G得到,确认刀盘锁紧,换刀过程结束[1]。
1.2 液压刀塔的控制方式该液压刀塔的刀号识别:三个接近开关的状态排列组合代表不同的刀号,根据接近开关的状态确认当前的刀位。
并通过相应电磁阀来执行控制的动作。
(如表1.2是刀号与接近开关的对应关系表)2.数控车床刀塔PMC控制程序编写2.1 PMC编写过程(1)将数控机床的PMC程序,使用CF卡从数控机床的ROM中传出。
(2)将PMC中原来的刀塔控制部分删除,重新编写刀塔的控制程序。
(3)将编写好的程序重新传入机床,对机床进行调试。
使之符合要求,完成改造任务。
2.2 机床的PMC硬件FANUC 0i-MA数控系统的控制单元有内置的I/O卡,用于机床各检测元件信号的采集和控制各种气、液压阀组件,指示灯等的动作。
在控制单元内置的I/O卡,其输入点的点数为96点,输出点点数为64点。
如输入输出数量未能满足要求时,就需要通过控制单元上的I/O LINK扩展I/O 单元来满足使用的要求,并在编写PMC程序时,对各I/O设备的地址进行分配。
第三章 数控车床机械结构与装调第四节 数控车床刀塔

二、液压刀塔介绍
与电动刀塔相比,液压刀塔能实现快 速、低噪声、正反转双向最短路径转动寻 找换刀刀位,松开和锁紧迅速,工作可靠 性好。但需要相应的液压系统提供压力油 和控制装置,所以一般在全功能数控车床 上配置液压刀塔。
二、液压刀塔介绍
数车排式刀塔
排式刀塔的各刀夹固定在横 向滑板上, 刀位切换运动直 接采用X轴快移运动,结构简 单,制造成本低,刀具系统 刚性好。 刀具容量小、整体占用空间 大,适合以纵向进给为主的 小型数控车上应用。
1—活动鼠牙盘 2—导向销 3—上刀架本体 4—下刀架
• 免抬式四刀位电动刀塔
结构特点
1.上刀架与鼠牙盘为独 立的两个零件,用8个 圆周分布的圆柱导向销 2活动连接。 2.活动鼠牙盘1单独作 升降运动,上刀架在导 向销的作用下作单方向 转动,上下刀架始结合 面始终保持接触。
性能特点
在换刀转位过程中,上下刀架始终闭合,有效防止切削液和切屑等杂物 进入刀塔内部,刀塔传动可靠性和精度保持性提高。
拆去棘爪
拆去定 位盘
一、电动刀塔
刀塔拆装调整
③拆卸上刀架等
1
2
拆下 蜗杆
取出定 位盘
拆去上盖 和螺母
34
拆去定 位盘
一、电动刀塔
刀塔拆装调整
④拆卸立轴与轴承
1
2
拆下立轴
用拉马拆除轴承
一、电动刀塔
刀塔拆装调整
⑤装配与调整
一、装配
装配过程与拆卸过程 除了轴承装配采用压 力机以外基本上是逆 向的。
传动原理
2.卧式八刀位电动刀塔
• 联接方式…… • 动作过程: a 从锁紧到抬起
B 从转位到反转夹紧
二、液压刀塔介绍
卧式12刀位液压刀塔
刀塔技术专题,伺服动力,动力伺服刀,转塔刀塔类技术资料
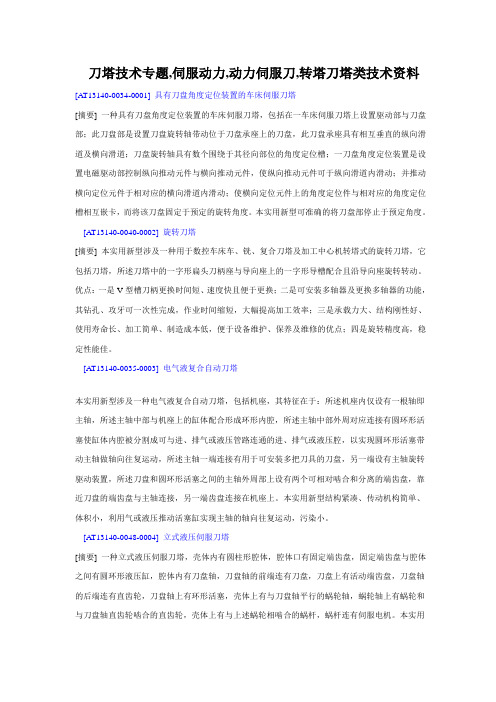
刀塔技术专题,伺服动力,动力伺服刀,转塔刀塔类技术资料[AT13140-0034-0001] 具有刀盘角度定位装置的车床伺服刀塔[摘要] 一种具有刀盘角度定位装置的车床伺服刀塔,包括在一车床伺服刀塔上设置驱动部与刀盘部;此刀盘部是设置刀盘旋转轴带动位于刀盘承座上的刀盘,此刀盘承座具有相互垂直的纵向滑道及横向滑道;刀盘旋转轴具有数个围绕于其径向部位的角度定位槽;一刀盘角度定位装置是设置电磁驱动部控制纵向推动元件与横向推动元件,使纵向推动元件可于纵向滑道内滑动;并推动横向定位元件于相对应的横向滑道内滑动;使横向定位元件上的角度定位件与相对应的角度定位槽相互嵌卡,而将该刀盘固定于预定的旋转角度。
本实用新型可准确的将刀盘部停止于预定角度。
[AT13140-0040-0002] 旋转刀塔[摘要] 本实用新型涉及一种用于数控车床车、铣、复合刀塔及加工中心机转塔式的旋转刀塔,它包括刀塔,所述刀塔中的一字形扁头刀柄座与导向座上的一字形导槽配合且沿导向座旋转转动。
优点:一是V型槽刀柄更换时间短、速度快且便于更换;二是可安装多轴器及更换多轴器的功能,其钻孔、攻牙可一次性完成,作业时间缩短,大幅提高加工效率;三是承载力大、结构刚性好、使用寿命长、加工简单、制造成本低,便于设备维护、保养及维修的优点;四是旋转精度高,稳定性能佳。
[AT13140-0035-0003] 电气液复合自动刀塔本实用新型涉及一种电气液复合自动刀塔,包括机座,其特征在于:所述机座内仅设有一根轴即主轴,所述主轴中部与机座上的缸体配合形成环形内腔,所述主轴中部外周对应连接有圆环形活塞使缸体内腔被分割成可与进、排气或液压管路连通的进、排气或液压腔,以实现圆环形活塞带动主轴做轴向往复运动,所述主轴一端连接有用于可安装多把刀具的刀盘,另一端设有主轴旋转驱动装置,所述刀盘和圆环形活塞之间的主轴外周部上设有两个可相对啮合和分离的端齿盘,靠近刀盘的端齿盘与主轴连接,另一端齿盘连接在机座上。
车铣复合机床核心——动力刀塔结构设计
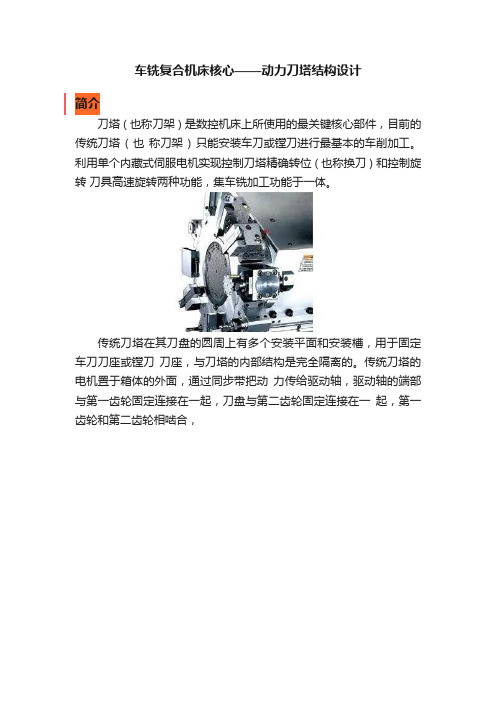
车铣复合机床核心——动力刀塔结构设计简介刀塔 ( 也称刀架 ) 是数控机床上所使用的最关键核心部件,目前的传统刀塔 ( 也称刀架 ) 只能安装车刀或镗刀进行最基本的车削加工。
利用单个内藏式伺服电机实现控制刀塔精确转位 ( 也称换刀 ) 和控制旋转刀具高速旋转两种功能,集车铣加工功能于一体。
传统刀塔在其刀盘的圆周上有多个安装平面和安装槽,用于固定车刀刀座或镗刀刀座,与刀塔的内部结构是完全隔离的。
传统刀塔的电机置于箱体的外面,通过同步带把动力传给驱动轴,驱动轴的端部与第一齿轮固定连接在一起,刀盘与第二齿轮固定连接在一起,第一齿轮和第二齿轮相啮合,从而实现电机转动带动刀盘转动的目的,控制单元通过电机内置的编码器反馈信息进行控制电机的转速、圈数和旋转角度,来实现刀盘的转位控制。
刀座通过定位键和螺钉固定在刀盘的圆周各刀位上,刀座上可安装车刀或镗刀,但此类刀具只能实现直线进给进行车削加工的要求,且外形尺寸较大。
改变了传统刀塔各安装刀具位置的结构,使每个刀具位置既可安装车刀,又可安装旋转刀具。
基本功能——刀塔转位 ( 也称换刀 ) :当离合器活动转齿与离合器固定转齿啮合时,是电机动力传递给旋转刀具的必须条件;当离合器活动转齿与离合器固定转齿脱离时,电机动力就不再驱动旋转刀具旋转,此状态下正是离合器活动转齿通过其圆周齿轮与刀塔转位齿轮 ( 即第一齿轮 ) 进行啮合的状态,达到电机旋转带动刀塔转位的目的。
概括地说,通过控制离合器活动转齿的两个位置 ( 即啮合与脱离状态 ),达到电机动力输出给刀塔转位或输出给旋转刀具旋转的目的。
旋转刀具旋转的实现如下:首先离合器活动转齿与离合器固定转齿的啮合,使刀塔处于刀具旋转状态,控制单元通过外置的编码器5 反馈信息进行控制电机的转速、启停和正反转动,来实现刀具任意速度的正转、反转及停止;另外,该动力刀塔采用的动力刀柄为尾部扁尾结构,因此,在旋转刀具停止时需要停止在固定的角度位置上,才能保证下一把旋转刀具顺利地插入槽中,刀具的固定角度停止功能靠编码器的角度反馈来实现。
基于TRIZ理论的车床转位刀塔改进

1序言在某输入轴柔性制造线的05、10工序上,配有液压转位刀塔的2台数控卧式车床(以下简称车床)承担着8004或0019输入轴的车削加工(见图1)。
车床运行中,断续出现输入轴各台阶长度切短1~4mm的现象(见图2),有时间隔20件出现2根废品,有时间隔35件出现2根废品。
废品发生时,车刀片崩刃损坏。
输入轴的废品数积累至10件时,该条生产线停滞待修理。
图1 输入轴车削示意a)输入轴废品 b)车刀片崩刃图2 输入轴废品及车刀片崩刃示意2问题分析将液压转位刀塔车削零件的工程问题转化为TRIZ标准问题,经功能分析法得到关键问题后,结合功能模型图进行功能裁剪,用因果链分析法得到主/次要问题,经发明原理解决技术矛盾冲突,构建串/并联复合物场模型进行标准求解,并用HOW TO模型进行概念方案探索。
2.1 功能分析法功能分析是识别系统和超系统组件的功能,并分析其特点和成本的一种分析工具。
1)功能组件分析涉及三方面内容:组件分析、相互作用分析和功能模型图绘制。
①组件分析:确定液压转位刀塔车削零件为当前系统组件,I/O信号、继电器、液压油及电能为子系统组件,加工程序和机外在线测量为超系统组件。
②相互作用分析:找出各组件两两之间的相互作用,用“+”表示存在相互作用,用“-”表示不存在相互作用。
③功能模型图绘制:确立各组件之间的具体功能关系,画出功能模型图(见图3),其中实线箭头表示无害、充足作用,波浪线箭头表示有害作用,虚线箭头表示不足作用。
图3 功能模型2)通过功能组件分析得到4个关键问题:转位刀塔对车刀的夹固不足,液压装置对转位刀塔锁紧不足,继电控制线路转换不足,以及PMC及I/O信号触发不足。
3)功能组件裁剪。
依据功能模型图,经裁剪原则B进行组件裁剪,即裁掉可自我执行的有用功能。
拟裁剪组件为继电控制线路,裁剪后的功能模型图如图4所示。
裁剪后的预期成效:可提高液压装置动作信号的稳定性,消除继电控制线路转换I/O信号的不足。
辛辛那提数控车床刀塔控制原理及故障分析
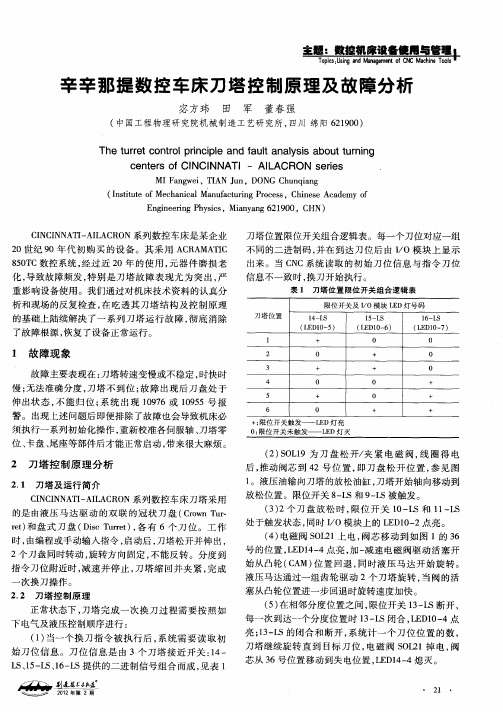
刀塔 位置 限 位开关 组合 逻辑 表 。每一个 刀 位对应 一组 不 同 的二进 制码 , 并在 到 达 刀 位后 由 IO模 块 上 显 示 / 出来 。当 C C系统 读 取 的初 始 刀 位 信 息 与 指 令 刀 位 N 信息 不一 致 时 , 刀开 始执行 。 换
表 1 刀塔 位 置 限位 开关 组合 逻辑 表
MIF n w i I u a g e ,T AN J n,D ONG C u qa g h n in
(ntueo Meh ncl a uatr gPoes hn s cd m f Istt f c a i n fc i rcs,C ieeA a e yo i aM un E g er gP yis Mi yn 2 0 H n i ei h s , a a g 0 ,C N) n n c n 61 9
限位 开 关 及 IO模 块 L D灯 号 码 / E 刀 塔 位 置 1- S 4 L ( E 0 5 L D1— )
1 + O
+
1- S 5 L (E 1— L D 0 6)
0 +
上
1- S 6 L ( E 0 7 L D1 — )
0 0
0
Th u r tc n r l r cpe a d f uta ay i a o t u nn e t re o to i il n a l n lss b u r ig p n t c n e s o NCI ATl — AIACRON e is e t r fCI NN L s r e
2 2 刀塔控 制原 理 .
正 常状 态下 , 塔 完 成一 次 换 刀 过 程 需 要按 照 如 刀 下 电气及 液 压控 制顺 序进 行 :
CN IN T— IA R N系列 数控 车 床是 某 企业 ICN A IA L C O 2 O世 纪 9 O年代 初 购 买 的设 备 。其 采 用 A R MA I C A TC 80 C数 控 系统 , 过 近 2 5T 经 0年 的使 用 , 器 件 磨 损 老 元 化, 导致 故 障频发 , 别 是 刀 塔 故 障表 现尤 为突 出 , 特 严 重影 响设 备使 用 。我 们通 过对 机床 技术 资料 的认 真分 析 和现 场 的反 复 检查 , 吃透 其 刀 塔 结 构及 控 制 原 理 在 的基 础 上陆续 解 决 了一 系 列 刀 塔 运行 故 障 , 彻底 消 除 了故 障根 源 , 恢复 了设 备正 常运 行 。
数控机械传动知识点总结
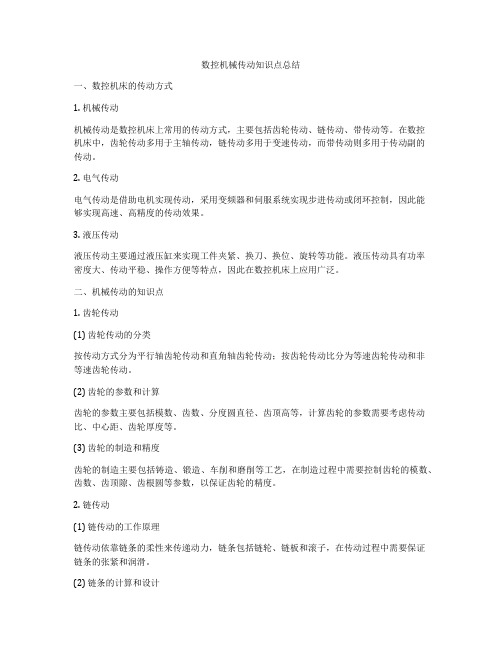
数控机械传动知识点总结一、数控机床的传动方式1. 机械传动机械传动是数控机床上常用的传动方式,主要包括齿轮传动、链传动、带传动等。
在数控机床中,齿轮传动多用于主轴传动,链传动多用于变速传动,而带传动则多用于传动副的传动。
2. 电气传动电气传动是借助电机实现传动,采用变频器和伺服系统实现步进传动或闭环控制,因此能够实现高速、高精度的传动效果。
3. 液压传动液压传动主要通过液压缸来实现工件夹紧、换刀、换位、旋转等功能。
液压传动具有功率密度大、传动平稳、操作方便等特点,因此在数控机床上应用广泛。
二、机械传动的知识点1. 齿轮传动(1) 齿轮传动的分类按传动方式分为平行轴齿轮传动和直角轴齿轮传动;按齿轮传动比分为等速齿轮传动和非等速齿轮传动。
(2) 齿轮的参数和计算齿轮的参数主要包括模数、齿数、分度圆直径、齿顶高等,计算齿轮的参数需要考虑传动比、中心距、齿轮厚度等。
(3) 齿轮的制造和精度齿轮的制造主要包括铸造、锻造、车削和磨削等工艺,在制造过程中需要控制齿轮的模数、齿数、齿顶隙、齿根圆等参数,以保证齿轮的精度。
2. 链传动(1) 链传动的工作原理链传动依靠链条的柔性来传递动力,链条包括链轮、链板和滚子,在传动过程中需要保证链条的张紧和润滑。
(2) 链条的计算和设计链条的计算主要包括链条的尺寸、链轮的选择、链条的轴距、链条的张紧方式等,需要根据实际传动功率和工作条件来确定。
3. 带传动(1) 带传动的分类带传动分为平动带传动和皮带传动,其中平动带传动主要用于长距离传递功率,而皮带传动主要用于变速传动和工作环境要求较严格的场合。
(2) 带传动的设计和计算带传动的设计需要考虑带速比、中心距、带轮尺寸、带条数、张紧装置等参数,同时还需要考虑带传动的强度和工作效率。
三、电气传动的知识点1. 电机的分类与特点电机根据使用场合可以分为交流电机和直流电机,根据工作原理可以分为异步电机和同步电机,根据结构形式可以分为开放式电机和封闭式电机。
- 1、下载文档前请自行甄别文档内容的完整性,平台不提供额外的编辑、内容补充、找答案等附加服务。
- 2、"仅部分预览"的文档,不可在线预览部分如存在完整性等问题,可反馈申请退款(可完整预览的文档不适用该条件!)。
- 3、如文档侵犯您的权益,请联系客服反馈,我们会尽快为您处理(人工客服工作时间:9:00-18:30)。
摘要刀库是自动换刀装置中最主要的部件之一,其容量、布局以及具体结构对加工中心的设计有很大影响。
刀库是在小型加工中心应用最为广泛,根据使用的场合和实际运用的要求,设计了相应的刀的圆盘式刀库,并且对它的控制进行了一定的研究。
论文首先对刀库总体设计方案进行阐述,阐述其各部件的工作原理,然后就刀库的结构设计与控制分章节对各个部分进行计算与设计。
刀库的结构设计是本文研究的重点,传动部分为蜗杆蜗轮的一种减速装置,对于该装置中的蜗杆、蜗轮以及相关的轴都进行了详细的计算;控制部分为刀库送刀部分,由液压控制和PLC控制完成。
关键词:加工中心刀库蜗杆蜗轮液压PLCAbstractTool storage is one of the main components of the automatically-trading-knife installment. Its capacity, position and structure have great influence to the design of the machining centre.tool storage is widely used in the machining centre. Based on the situation and requirement the tool used, the disc-style tool storage of the tool is designed and some research about its control is made in this paper.The paper illustrates the design project of the tool storage firstly, and then explains its operation principle, and at last calculates and designs the structure and control of the tool storage separately by chapters.The design of the structure of the tool storage is the key point of this research. Driving part is a decelerating set of the worm and worm gear. The sizes of the worm, worm gear and axis are calculated. The control parts are tool storage delivering parts, which is completed by the hydraulic pressure and PLC control.Key words: machining centre tool storage worm worm gear hydraulic pressure PLC目录摘要 (I)Abstract ........................................................................................................................................................... I I 1 绪论 (1)1.1 引言 (1)1.2 加工中心简介 (1)1.2.1 加工中心的发展简史 (1)1.2.2 加工中心的结构组成 (2)1.2.3 加工中心的分类 (3)1.2.4 加工中心的主要优点 (4)1.2.5 加工中心的发展趋势 (5)1.3 本文研究的主要内容——刀库 (7)1.3.1 刀库的类型 (7)1.3.2 本文所设计的刀库 (10)2 刀库驱动电动机的选定 (14)2.1 按负载转矩选 (14)2.2 按加速时的最大转矩选 (15)2.3 校验 (15)2.4 分配传动比 (16)3 刀库传动机构的设计 (18)3.1 初定刀套线速度 (18)3.2 刀库传动方式以及 (18)4 传动轴的设计 (23)4.1 轴的材料 (23)4.2 蜗杆轴的初步估算 (23)4.2.1 初步估算轴的最小直径 (23)4.2.2 选择联轴器 (23)4.2.3 确定滚动轴承的类型 (24)4.2.4 初步估计蜗杆轴各段的尺寸 (24)4.3 蜗轮轴的初步估算 (25)4.3.1 初步估算轴的最小直径 (25)4.3.2 确定轴伸处的最小直径 (25)4.3.3 确定滚动轴承的类型 (25)4.3.4 初步估计蜗轮轴的各段尺寸 (26)4.4 轴径的设计与校核 (26)4.4.1 蜗杆轴 (26)4.4.2 蜗轮轴的计算 (31)5 轴承的校核 (36)5.1 蜗杆轴 (36)5.2 蜗轮轴 (37)6 其它零部件尺寸的设计与计算 (37)6.1 回零减速撞块尺寸的计算 (37)6.2 刀盘与刀套的设计 (38)6.2.1 刀套 (38)6.2.2 刀盘 (39)6.3 刀具(刀座)识别装置 (39)7 液压系统的设计 (40)7.1 液压缸的载荷组成和计算 (40)7.2 液压缸内径以及其它尺寸的确定 (41)7.2.1 计算液压缸的主要结构尺寸 (41)7.2.2 油缸壁厚的计算 (42)7.2.3 缸底厚度计算 (42)7.3 油缸长度L的确定 (43)7.4 液压系统初步设计 (44)结论 (45)参考文献 (46)致谢 (47)1 绪论本章首先从数控机床的发展历程引出加工中心的发展趋势,再具体到本次设计针对的刀库的任务要求,明确了本设计任务的主要内容。
1.1 引言1952年世界上出现了第一台数控机床,使多品种、中小批量的机械加工设备在柔性、自动化和效率上产生了巨大变革。
1958年第一台加工中心问世,它将多工序(铣、钻、镗、铰、攻丝等)加工集于一身;适应加工多品种和大批量的工件;增加机床功能(自动换刀、自动换工件、自动检测等),使自动化程度和加工效率上了一个新台阶;使无人化(或长时间无人操作)加工成为现实。
加工中心已成为柔性制造系统、计算机集成制造系统和自动化工厂的基本单元。
加工中心是数控机床的代表,是高新技术集成度高的典型机电一体化机械加工设备,受到世界各工业发达国家的高度重视,技术迅速发展,品种和数量大幅度增加,成为当今世界机械加工设备中最引人注目的一类产品。
1.2 加工中心简介1.2.1 加工中心的发展简史1952年世界上出现第一台数控机床,使多品种、中小批量的机械加工设备在柔性、自动化和效率上产生了巨大变革。
它用易于修改的数控加工程序进行控制,因而比大批量生产重使用组合机床生产线和凸轮、开关控制的专用机床有更大的柔性,容易适应加工件品种的变化,进行多品种加工。
它用数控系统对机床的工艺功能、几何图形运动功能和辅助功能实行全自动的数字控制,因为有更高的自动化程度和加工效率,大大改变了中小批量生产中普通机床占整个机械加工70%~80%的状况。
数控机床能实现两坐标以上联动的功能,其效率和精度比用手工和样板控制加工复杂零件要高得多。
1958年第一台加工中心在美国卡尼、特雷克(Kearney&Trecker)公司问世。
现代加工中心的内容是什么?第一,它是在数控镗床或数控铣床的基础上增加自动换刀装置,可使工件在一次装卡中,能够自动更换刀具,自动完成工件上的铣削、钻孔、镗孔、铰孔、攻丝等工序的数控机床。
第二,加工中心上如果带有自动分度回转工作台或自动转角度的主轴箱,可使工件在一次装卡中,自动完成多个平面和多个角度位置的多工序加工。
第三,加工中心上如果带有交换工作台,工件在工作位置的工作台上进行加工的同时,另外的工件在装卸位置的工作台上进行装卸,不影响加工的进行。
由上述可知,加工重心在加工的柔性、自动化程度和加工效率上,在一般数控机床的基础上又上了一个新的台阶,又是一次新的变革。
加工中心的定义是什么?目前世界上并无标准定义,但目前普遍认为是指:在工件一次装卡中,能够实现自动铣削、钻孔、镗孔、铰孔、攻丝等多工序的数控机床。
更为明确的说法是:加工中心就是自动换刀数控镗铣床。
这就把加工中心与自动换刀数控车床或车削中心区别开来。
1.2.2 加工中心的结构组成加工中心的组成岁机床的类别、功能、参数的不同而有所区别。
机床本身分基本部件和选择部件,数控系统有基本功能和选用功能,机床参数有主参数和其它参数。
机床制造厂可根据用户提出的要求进行生产,但在同类机床的基本功能和部件组成一般差别不大。
从总体上看,加工中心基本上由以下几大部分组成。
1、基础部件主要由床身、立柱和工作台等大件组成。
它们是加工中心的基础结构,要承受加工中心的静载荷以及在加工时的切削负载,因此必须是刚度很高的部件。
这些大件可以是铸铁件也可以是焊接的刚结构件,是加工中心中重量和体积最大的部件。
2、主轴系统主要由主轴箱、主轴电动机、主轴和主轴轴承等零部件组成。
主轴的启动、停止和变转速等动作均由数控系统控制,并通过装在主轴上的刀具参与切削运动,是切削加工的功率输出部件。
主轴系统是加工中心的关键部件,其结构的好坏,对加工中心的性能有很大的影响。
3、数控系统主要由CNC装置、可编程序控制器、伺服驱动装置以及电动机等部分组成,它们是加工中心执行顺序控制动作和完成加工过程的控制中心。
4、自动换刀系统主要由刀库、自动换刀装置等部件组成。
刀库是存放加工过程所要使用的全部刀具的装置。
当需要换刀时,根据数控系统的指令,由机械手(或通过别的方式)将刀具从刀库取出装入主轴孔中。
刀库有盘式、链式和鼓式等多种形式,容量从几把到几百把。
机械手的结构根据刀库与主轴的相对位置几结构的不痛也有多种形式。
如单臂式、双臂式。
回转式和轨道式等等。
有的加工中心利用主轴箱或刀库的移动来实现换刀。
5、辅助系统包括润滑、冷却、排屑防护、液压和随机检测系统等部分。
辅助系统虽不直接参与切削运动。
但对加工中心的加工效率、加工精度和可靠性起到保障作用,因此也是加工中心中不可缺少的部分。
另外,为进一步缩短非切削时间,有的加工中心还配备了自动托盘交换系统。
例如,配有两个自动交换工件托盘的加工中心,一个安装工件在工作台上加工,另一个则位于工作台外进行工件的装卸。
当完成一个托盘上工件的加工后,便自动交换托盘,进行新零件的加工,这样可以减少辅助时间,提高加工效率。
1.2.3 加工中心的分类按照加工中心形态不同进行分类,可分为立式、卧式和五坐标加工中心。