21个经典生产车间改善案例
车间改善提案案例大全
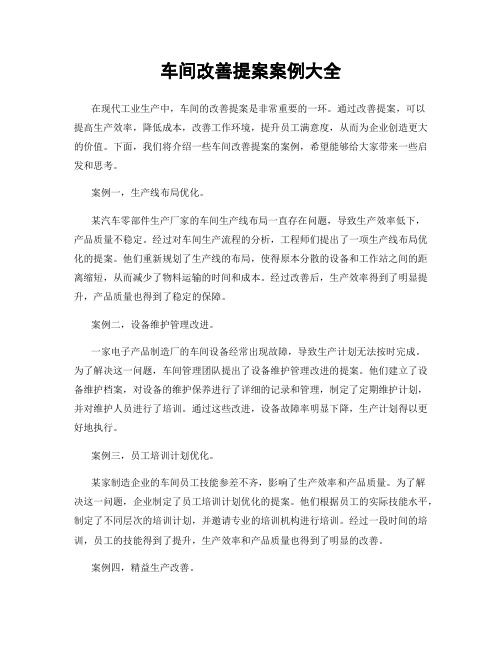
车间改善提案案例大全在现代工业生产中,车间的改善提案是非常重要的一环。
通过改善提案,可以提高生产效率,降低成本,改善工作环境,提升员工满意度,从而为企业创造更大的价值。
下面,我们将介绍一些车间改善提案的案例,希望能够给大家带来一些启发和思考。
案例一,生产线布局优化。
某汽车零部件生产厂家的车间生产线布局一直存在问题,导致生产效率低下,产品质量不稳定。
经过对车间生产流程的分析,工程师们提出了一项生产线布局优化的提案。
他们重新规划了生产线的布局,使得原本分散的设备和工作站之间的距离缩短,从而减少了物料运输的时间和成本。
经过改善后,生产效率得到了明显提升,产品质量也得到了稳定的保障。
案例二,设备维护管理改进。
一家电子产品制造厂的车间设备经常出现故障,导致生产计划无法按时完成。
为了解决这一问题,车间管理团队提出了设备维护管理改进的提案。
他们建立了设备维护档案,对设备的维护保养进行了详细的记录和管理,制定了定期维护计划,并对维护人员进行了培训。
通过这些改进,设备故障率明显下降,生产计划得以更好地执行。
案例三,员工培训计划优化。
某家制造企业的车间员工技能参差不齐,影响了生产效率和产品质量。
为了解决这一问题,企业制定了员工培训计划优化的提案。
他们根据员工的实际技能水平,制定了不同层次的培训计划,并邀请专业的培训机构进行培训。
经过一段时间的培训,员工的技能得到了提升,生产效率和产品质量也得到了明显的改善。
案例四,精益生产改善。
一家机械加工厂的车间存在着材料浪费严重的问题,影响了企业的利润和竞争力。
为了解决这一问题,企业引入了精益生产的理念,提出了精益生产改善的提案。
他们对生产流程进行了精细化的分析,找出了造成材料浪费的根本原因,并采取了相应的改善措施。
经过改善,材料浪费得到了有效控制,企业的利润也得到了提升。
以上案例仅仅是车间改善提案的冰山一角,每个企业的实际情况都有所不同,因此,改善提案也需要因地制宜,因时制宜。
100张工厂车间5S改善案例图

100张工厂车间5S改善案例图,张张经典!
现在很多企业在推进5s相关工作,过程中产生了很多优秀的5s改善的案例,这
些案例对于其他也是很有很有借鉴意义所有整理出很不错 5s图片供给大家学习和
借鉴。
希望对大家的5s工作有很大的帮助。
6s管理
在5s活动的基础上,有的人提出了6s管理活动,记在“整理、整顿、清扫、清洁、素养”的基础上增加了“自检”,即每日下班前作自我反省与检讨,目的是1.总结经
验与不足 2.判定一至两种改进措施 3.培养自觉性、韧性和耐心,加强员工安全教育,每时每刻都有安全第一观念,防范于未然。
8S管理
8S就是整理(SEIRI)、整顿(SEITON)、清扫(SEISO)、清洁(SETKETSU)、素养(SHITSUKE)、安全(SAFETY)、节约(SAVE)、学习(STUDY)八个项目,因其古罗马发音均以“S”开头,简称为8S。
8s管理法的目的,是使企业在现场
管理的基础上,通过创建学习型组织不断提升企业文化的素养,消除安全隐患、节约成本和时间。
使企业在激烈的竞争中,永远立于不败之地。
13S管理
随着管理的不断完善和精细,5S管理的内容也不断地被扩充,已经逐步发展到
13S,即在5S的基础上增加安全、节约、服务、满意、坚持、共享、效率、学习。
其实,无论怎么变化,5S其实是一种管理思想和文化。
1
“定位划线“ good case
2
“定位划线“ good case
3
“生产区域“ good case
4
“办公区域“ good case
“仓库区域“ good case
5
“其他区域“ good case
=。
自行车厂现场改善案例

前言:中兴厂为一百多人生产自行车之小厂,有二栋三层楼之厂房,最近成为本公司外包协力厂,为提高其生产效率,并降低其代工价格,我方派出一改善小组去该厂指导,帮助该厂做现场改善。
改善小组成员包括IE一人,品管一人。
以下是现场改善的过程和改善后成果。
改善无处不存在,改善无人不会做,虽是小小的一个案例,主要说明我们日常解决问题的模式,积沙成塔、涓水成河,实践才是力量。
中兴厂现场改善案例:二、现状分析(改善前)1.总装作业员人数48人,产能22台/小时(平匀每天工作11小时,产出250台成车).2.各工序间的工作时间差太大,最长的时间为89.18秒,最短的时间为17.49秒.造成人员的心里不平衡,产出时间拉长.3.车架要用两人每次2支的从办公楼三楼搬至总装二楼.约移动47M.4.成车要一台一台的搬到一楼仓库.约移动20M5.作业员的积急性不高.三、改善实施(总装)(一)改善方法1.先测出振华厂各工作站的实际所需工时,经过合理的计算后,制订合理的标准工时,编排合理的上线人员,交总装主管审阅是否认可.2.工时及上线人员取得主管的认可后,仍无法执行,经调查从上至下都想依混时间来取得工资.故明明1小时可做完的事故意拖到2小时完成,故当时想采用计件的方式来消除此现象,经萧副总及周科合理计算后以大行但现场的员工都很聪明,先依以往的产能与现行的计件单价进行计算,以原方式每月可领1000元左右的工资,而依计件单价计算每月只有650元左右的工资,故执行不下去.3.按总经理的高额奖金的方试来测试总装的最高产能.先设定一个奖金额各目标产能,再用振华厂之前的最高产能与目标产能的百分比做基数,第一天的产能与目标产能的百分比减去原百分比的数值剩奖金额所得的数值为第一天的奖金, 第二天的产能与目标产能的百分比减去之前的最高百分比的数值剩奖金额所得的数值为第二天的奖金,一次类推.直到达到目标时为止.(当时预计需一个月左右才能达到)4. 员工对高客奖金不感相信,故积极性不高,但毕境是高额奖金,还是有一点吸引力的,所以第天员工先依试探的心态提高一点来试验我们的承诺的真实性.5. 第二天上午九点钟时财务部准时将奖金发到各科长手中,并要求十点钟之前发到员工手中,结果取得了员工的信任.之后仅用七天就达到了目标置.6. 开始公布计件单价,员工们看到单价后与他们最高产能计算,一个月不加一个班也可拿1150元左右.也就有了信心.7. 再进行物流方面的改善..8. 加装空中输送线,减少搬运人员及缩短搬运时间.9. 加装电梯(原振华厂已开始安装),使成品用栈板向成品仓绞库.10. 开始由振华厂自已自发的进行减员.2.成车的移动由原来的20M缩短到现在的9M.3.投资117000元人民币.4.总装线上线人数降到37有人,产能上升到45台/每小时(但因目前订单不足的原因现为336.单从人工费方计算投入回收时间:117000/60/8/26=9.375月≒10月7.制造成本方面的节约因资料不全的情况下只能用百分比来计算:现每天的产能以原来方式需用的小时数:45*8/22=16.36现在的直接费用与原费用比为:8/16.36*100%=49%五、现状分析(涂装)(一).问题分析1.贴花人员13人.2.前处理配员3人,喷手6人,调油由组长兼职,上挂4人,全检一人.3.产能25套/小时.4.烤漆件前处理后下挂专用台车太少.5.作业员的积急性不高.6.返修率偏高.7.以下油漆要喷两次面漆,7776/7775/7871/782/9177/9174/775/8860.8.线长283.5M,315个工位.线速为600时,每25秒可过一工位.要位间距09M.线走一周需7875秒.9.喷一次面漆时可全员生产.10.喷二次面漆时,第一遍由上挂,喷底漆,喷面漆人员(8人)作业,全检及喷金油人员(3人)处于等待状态.第二遍时由喷面漆,喷金油,全检人员(5人)作业,但喷金油及面漆人员(3人)分别有约1H及2H的等待时间.上挂及喷底漆人员完(6人)全处于等待状态.六、改善实施(涂装)(一).改善方法1.依配合总装生产且提高本部门的效率来作奖励的方式来测试最高产能.2.达到目标产能后再公布计件金额.3.结果出现更有效的现象,就时喷一次油漆时只要生产4小时就能完成生产任务啦.前处理只要4小时就能完成生产任务,而所得的新资比之前的还高.最还达到自已内部工作进行自发的调整,前处理上午上班,喷油下午上班.这样合整个车产的设备的运转时间减少了6时左右.直接节约了成本费.4.制定不良品奖惩制度.5.制定油漆使用量标准.(未执行)6.作业员互动.(未执行).七、改善后成果(涂装)1.贴花人员10人.2.喷涂人员13人.3.产能36台/小时(全月平均产能).5.单从人工费方计算每天可节约费用:3.211X11X8=282.48元6.制造成本方面的节约因资料不全的情况下只能用百分比来计算:现每天的产能以原来方式需用的小时数:36*8/25=11.52现在的直接费用与原费用比为:8/11.52*100%=71%.八、现状分析(焊接)(一).问题分析1.焊接组27人.2.冲压组10人.3.产能25套/小时.4.焊接及冲压之间往复搬运.5.作业员的积急性不高.6.一人可以作业的地方却按排两人作业.7.有些设备老化,影响生产进度.8.点焊方面的模治具设计不合理,造成无法完成一人作业.九、改善实施(一).改善方法1.将不合理的模治具及设备进行修改,尽量将一人可以作业的事情尽量避免两人作业.2.将多余的人员调到其它部门去.3.设备的位置进行调整,减少物料的搬运次数.(未完全执行)4.新购设备,改变生产流程.5.依配合总装生产且提高本部门的效率来作奖励的方式来测试最高产能.6.达到目标产能后再公布计件金额.7.但有部分主管却算到自已没有得到好处,故造出你现在这样做虽说工资高了,但拿之前的产能比,你比之前累多啦.故鼓动员工罢工.8.把参加罢工的员工全部开除,先从大行调人支持.确保正常生,让其知道,罢工是无用的.稳定了公司人员的心9.为了减少成本的投入,将焊接一班改为两班.将功能较差的焊机停用.十、改善后的成果(焊接)1.产能34套/小时.1.378X9X8=99.216元4.制造成本方面的节约因资料不全的情况下只能用百分比来计算:现每天的产能以原来方式需用的小时数:34*8/25=10.886.现在的直接费用与原费用比为:8/10.88*100%=73%.。
经典精益生产改善案例

经典精益生产改善案例精益生产说起来容易,做起来难。
精益之行还需要在精益思想、原则和准则的指导下学习和实践一些有用的工具和方法,比如工业工程(IE)、价值流图分析、柔性生产线建立、缩短作业转换时间、拉动式连续“一个流”生产、5S、QC工具、统计质量控制、防呆错技术、TPM等等。
01. 自动化与防呆防错,一个小改善的大效果零缺陷最大的窍门:通过发掘人的智慧,找到“傻瓜”都能做对的办法,减少品质对人的依赖。
1 . 有一家电子生产型企业,他们在组装设备时由于需要装配的螺丝数量多,操作工经常会有遗忘,导致不良。
后来,公司就从精益生产的角度进行考虑,降低人的因素。
他们专门设计了一种机械手,机械手末端有磁铁。
如果这个部位需要装5颗螺丝,机械手就自动抓起5颗螺丝,如果需要装16颗螺丝,机械手就自动抓起16颗螺丝。
操作工只要看下机械手上有没有剩余的螺丝就可以了。
这样就减少了品质不良的发生。
2 . 还有一家生产复印机的工厂,他们的复印机里面有一个小风扇,这个小风扇非常重要,一旦装反了,就会导致机械损坏。
但由于是流水线作业,操作工在装配时,由于疲劳、遗忘等多种原因,可能会出错。
主管就要求操作工装好后要进行检查,用手摸一下,试下风向。
但是每天生产数千台复印机,操作工人可能就会产生错觉,有风?没风?还是会产生装反的现象。
后来,就通过发掘员工潜能,在复印机旁边装一个小风车,如果装配正确就会有风,风车会转,因此只要风车会转,装配就是完好的,否则,就是错误的。
这样这家公司复印机的合格率就大大提高了。
02. 标准化与简单化改善前:出库部分拣集包组班组长日常管理无标准化的管理规范,班组长日常管理的关键管控点存在管控疏漏的情况,不利于班组成长。
改善后:建立规范的班组长时段化管控标准,将日常管理事务标准化,确保管理受控,同时提升班组长的管理能力。
03. 如何强化管理,目视化的改善某企业有一个开放式的大办公室,有200人在一起办公。
由于管理不到位,经常发生办公室的灯、空调没有关的现象。
21个经典生产车间改善案例

09/08/ 12 09/08/ 12
提案部门 确 认人
IE 车间
操作改善
Before(图片)
After(图片)
问 题 点
保护膜卷经常掉下 改 善 后 现 状 已执行
改 善 前
原因分析
保护膜没有被固定
改善对策
将两头固定使得保护膜不会掉下
改 善 结 果
保护膜卷不再掉下
改善成果个案
项目名称 项目类别
三星LED键
改善对策
改 善 结 果
1,螺丝被打花小于1% 2,螺丝有专用地方放,明显整齐.
改善成果个案
项目名称 项目类别
友利通面板
提案人 实施人
邹龙庚 邹龙庚
提案时间 完成时间
09/08/ 17 09/08/ 17
提案部门 确 认人
IE 车间
贴胶纸改善
Before(图片)
After(图片)
问 题 点
改 善 前
问 题 点
改 善 前
气压大小无法监控,导致成型机上下压 力无法控制.
无气压表
改 善 后
现 状
已执行
原因分析
改善对策
安装气压表
改 善 结 果
可以清楚气压大小
改善成果个案
项目名称 项目类别
注塑机房
提案人 实施人
车间 生技
提案时间 完成时间
09/08/ 28 09/09/ 3
提案部门 确 认人
车间 车间
改善成果个案
项目名称 项目类别
G18A壳
提案人 实施人
邹龙庚 欧顺利
提案时间 完成时间
09/07/ 28 09/08/ 1
提案部门 确 认人
IE 邹龙庚
车间改善提案案例大全

车间改善提案案例大全一、背景介绍。
车间作为生产的核心区域,其效率和安全性直接关系到整个企业的运营和发展。
因此,车间改善提案成为了企业持续改进的重要一环。
下面,我们将介绍一些车间改善提案的案例,希望能够给大家带来一些启发和借鉴。
二、提案案例。
1. 生产线优化。
在某生产企业的车间里,生产线的布局一直是一个困扰企业的问题。
为了解决这一问题,车间的管理团队提出了一个生产线优化的提案。
他们对生产线进行了重新布局,将原本分散的设备整合在一起,减少了物料运输的时间和成本,提高了生产效率,降低了生产成本。
2. 设备升级。
另外一个车间改善提案的案例是设备升级。
某企业的车间里使用了一批老旧设备,这些设备在工作效率和能耗上都存在一定的问题。
为了解决这一问题,车间管理团队提出了设备升级的提案,引进了一批新型高效节能设备,不仅提高了生产效率,还降低了能耗,实现了双赢。
3. 安全改善。
在另一家企业的车间里,安全问题一直是一个困扰企业的难题。
为了解决这一问题,车间管理团队提出了一系列的安全改善提案,包括加强员工的安全教育培训、改善车间的安全设施、优化生产流程等。
通过这些改善措施的实施,大大降低了事故发生的概率,提升了车间的安全水平。
4. 生产排程优化。
最后一个案例是关于生产排程优化的提案。
在某企业的车间里,由于生产排程不合理,经常出现生产计划无法按时完成的问题。
为了解决这一问题,车间管理团队提出了生产排程优化的提案,通过对生产流程和生产设备进行优化,合理安排生产计划,最终实现了生产效率的提升和生产计划的准时完成。
三、结语。
以上是一些关于车间改善提案的案例,这些案例都充分体现了车间改善提案在企业持续改进中的重要作用。
希望这些案例能够给大家带来一些启发和借鉴,也希望大家能够在实际工作中,不断探索和创新,为企业的发展贡献自己的力量。
车间安全生产改善案例
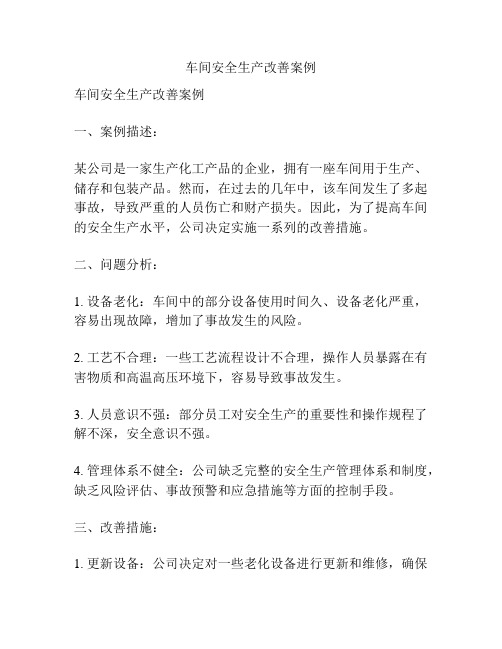
车间安全生产改善案例车间安全生产改善案例一、案例描述:某公司是一家生产化工产品的企业,拥有一座车间用于生产、储存和包装产品。
然而,在过去的几年中,该车间发生了多起事故,导致严重的人员伤亡和财产损失。
因此,为了提高车间的安全生产水平,公司决定实施一系列的改善措施。
二、问题分析:1. 设备老化:车间中的部分设备使用时间久、设备老化严重,容易出现故障,增加了事故发生的风险。
2. 工艺不合理:一些工艺流程设计不合理,操作人员暴露在有害物质和高温高压环境下,容易导致事故发生。
3. 人员意识不强:部分员工对安全生产的重要性和操作规程了解不深,安全意识不强。
4. 管理体系不健全:公司缺乏完整的安全生产管理体系和制度,缺乏风险评估、事故预警和应急措施等方面的控制手段。
三、改善措施:1. 更新设备:公司决定对一些老化设备进行更新和维修,确保设备的稳定运行,降低事故发生的概率。
2. 工艺优化:优化一些工艺流程,减少操作人员接触有害物质和高温高压环境的机会。
同时,引入更安全的工艺和设备,减少潜在风险。
3. 培训提升:定期组织员工进行安全培训,提高员工对安全生产的认识和意识。
同时,加强对操作规程的宣传和培训,确保员工操作规范。
4. 建立安全管理体系:公司成立安全管理部门,负责制定安全生产管理体系,包括风险评估、安全技术规范、事故预警和应急措施等方面的制度和程序。
通过建立健全的管理体系,实现对安全生产的全面管理。
5. 加强监督检查:公司安排专业的监督检查团队,定期对车间进行安全生产检查,发现问题及时纠正,确保车间的安全。
四、实施效果:经过一段时间的努力,公司的改善措施逐步见效。
1. 事故减少:由于设备更新、工艺优化和培训提升等措施的实施,车间事故发生数量明显减少,人员伤亡和财产损失大幅降低。
2. 人员意识提升:员工通过培训和宣传,对安全生产的重要性有了更深刻的认识,安全意识显著提升。
3. 管理规范:安全管理体系的建立使得公司的安全生产工作变得规范化,员工遵守操作规程的意识增强,车间的生产秩序得以保证。
精益思想及生产车间的改善设计案例

一、在精益思想指导下的生产车间的改善设计案例精益生产是以消除不增加价值的等待、排队和其他延迟活动为目标,按照确定的生产节拍进展生产并且每次仅生产单件产品的一种先进的生产方式。
与以往的靠方案系统发出指令的推动式生产方式不同,精益生产系统通过采用拉动的生产方式,来实现快速响应顾客实际需求的目的。
改善,是指以实现更好为标准而进展的持续改良或改变的过程,是精益生产实施中的重要根底组成局部。
通过对生产加工车间的布置和生产节拍进展改善设计,可以平衡生产线,使产品在生产线上的流动更加和谐,使之更有利于满足顾客的需要;通过建立“一个流〞的生产方式,可以消除或简化生产过程中不产生任何价值的工作,使整个企业的潜在价值得以开发。
我们对某变压器厂箱体车间的物流设施布置进展了深入地分析,通过引入精益思想,提出了对目前大批量“成批与排队〞生产线的改善设计步骤及方案。
在充分考虑了原有箱体生产加工的工序、工艺设计根底上,通过对原有设备进展改动,大大减少了产品和在制品的库存量及产品的交货时间,增加了生产线的柔性,提高了生产率。
1、生产车间的现状及存在的问题箱体车间主要生产S9/10KVA-2000KVA的19个种类变压器的箱体,箱体车间的布置现状图见图1。
由于每个箱体的大体构造一样,其加工工艺也十分相似,由此,该车间将箱体的生产分为大件生产区和小件生产区,其中小件工件通常是由人工搬运,而大件工件通常是由车间内部的天吊来完成。
通过对箱体车间的深入分析,得出该车间存在如下几点问题:(1) 物流的路线太长(见图1),造成运输时间的浪费,并且各工序之间的衔接过程存在许多Muda(浪费),造成各工序的生产效率很低;(2) 生产现场存在大量闲置不用的生产设备,占用了大量的空间,同时生产现场显得十分混乱;(3) 生产设备之间的距离较大,操作人员移动距离较大,使得操作人员每人每次只能操作一台机床,不利于操作人员工作效率的提高。
2、在精益思想指导下的生产车间的改善设计针对以上存在的问题,以精益思想为根底,我们提出了如图2所示的设施规划改良程序模型。
- 1、下载文档前请自行甄别文档内容的完整性,平台不提供额外的编辑、内容补充、找答案等附加服务。
- 2、"仅部分预览"的文档,不可在线预览部分如存在完整性等问题,可反馈申请退款(可完整预览的文档不适用该条件!)。
- 3、如文档侵犯您的权益,请联系客服反馈,我们会尽快为您处理(人工客服工作时间:9:00-18:30)。
After(图片)
问题点
改 善 原因分析 前
每班的QC抽检不良品放的到处,导致
漏返工现象
改
善
没有统一规定地方,放置散乱倒置会漏 后 返工
改善对策
规定每班次QC抽检不良品放到办工 室前门口.
现 状 已执行
1,不再会漏掉 改 善 2,不良品会引起班组长,主管的高度 结 果 重视
改善成果个案
项目名称
美的装饰件 提 案 人
提案时间 完成时间
09/08/ 28
提案部门 车间
09/09/ 3
确 认 人 车间
After(图片)
问 题 点 员工从大门搬运产品,搬运距离长
改 善 原因分析 前
窗口开在靠门端,离工作台远
改善对策 将窗口开在工作台旁
改 善 现 状 已执行 后
改 善 检查OK后产品直接从窗口传递出, 结 果 节省搬运距离3M.
产品非规则,容易掉,且桌面粗糙
改 善 现 状 已执行 后
改善对策
产品用胶箱放置,传递到后工序也用胶 箱传递
改 善 产品在此工序不被划伤,掉落. 结果
改善成果个案
项目名称
成型车间电气 提 案 人 公司上层
项目类别
电气改善 实 施 人 生技
Before(图片)
提案时间 完成时间
09/08/ 28
提案部门 公司上
1,降低工作台面 2,台面用泡棉垫 3,机械手用泡棉包好.
改善 后
现 状 已执行 改 善 1,产品不再被机械手刮伤 结 果 2,没有灰尘产生。
改善成果个案
项目名称
VS7665/7666 提 案 人
IE
项目类别
操作改善 实 施 人 邹龙庚
Before(图片)
提案时间 完成时间
09/07/ 提案部门 IE
改善 后
重新制作保护膜架,把保护膜架加高。
现 状 已执行
改善 结果
1,有效把风挡住 2,不再有灰尘掉下 3,5S整齐
改善成果个案
项目名称
不良品标识 提 案 人
车间
项目类别
放置改善 实 施 人 车间
Before(图片)
提案时间 完成时间
09/08/ 17
提案部门 车间
09/08/ 确 认 人 IE
17
改善 后
制作一治具支撑齿轮,在中央挖出圆槽 装螺丝
现 状 已执行
1,螺丝被打花小于1% 改 善 2,螺丝有专用地方放,明显整齐. 结果
改善成果个案
项目名称
友利通面板
提案人
邹龙庚
项目类别
贴胶纸改善 实 施 人 邹龙庚
Before(图片)
提案时间 完成时间
09/08/ 提案部门 IE
17
09/08/ 17
Before(图片)
提案时间 完成时间
09/08/ 提案部门 IE
6
09/08/ 6
确 认 人 邹龙庚
After(图片)
问题点
改 善 原因分析 前
改善对策
员工在M8底壳上印日期时动作浪费, 印完产品后将印张放到桌上,用时再 从桌上拿起然后到印尼盒中沾印尼。
章直接放在印尼盒中,因印尼扁平, 会沾大量的印尼到旁边章上,故放在 桌上
Before(图片)
提案时间 完成时间
09/08/ 19
提案部门 车间
09/08/ 确 认 人 IE
19
After(图片)
问题点
改 善 原因分析 前
改善对策
批锋到处飞
产品为尼龙料,批锋多,用刀批时风 扇将批锋吹得到处。
改善 后
现 状 已执行
将用大胶盒放到桌面,在盒上批后批 锋将掉在盒子中。
改 善 5S明显改善. 结果
Before(图片)
提案时间 完成时间
09/08/ 30
提案部门 车间
09/08/ 31
确 认 人 车间
After(图片)
问题点
改 善 原因分析 前
员工每天中午,下午吃饭时,产品无场 地放导致堆积多
员工换班吃饭时少人,不能加工产品
改 善 现 状 已执行 后
改善对策
制作一个周转架,吃饭时将架搬过来放 货,平时不用时移到外面角落.
改善 后
制做一个高台阶的小盒,直接可将章 直放入。
现 状 已执行
1,减少一个动作,节约2秒 改 善 2,面积缩小,减少印尼油的挥发 结果 量
改善成果个案
项目名称
车间办公室
提案人
邹龙庚
项目类别
5S改善 实 施 人 邹龙庚
Before(图片)
提案时间 完成时间
09/08/ 提案部门 IE
7
09/08/ 7
改 善 保护膜卷不再掉下 结果
改善成果个案
项目名称
三星LED键 提 案 人
车间
项目类别
操作改善 实 施 人 车间
Before(图片)
提案时间 完成时间
09/08/ 12
提案部门 车间
09/08/ 12
确 认 人 邹龙庚
After(图片)
问 题 点 产品小,批锋不好批掉
改 善 原因分析 前
产品太小.不好固定
改 善 现 状 已执行 后
改善对策 制做贴保护膜定位治具
改 善 保护膜贴平整 结果
改善成果个案
项目名称
大金LOGO
提案人
邹龙庚
项目类别
压PC片治具 实 施 人 欧顺利
Before(图片)
提案时间 完成时间
09/07/ 提案部门 IE
28
09/08/ 1
确 认 人 邹龙庚
After(图片)
问题点
1,手动压紧PC贴片效果不太好 2,每次压一个速度较慢
24
09/08/ 27
确 认 人 车间
After(图片)
问 题 点 产品用水口剪花时间长
改 善 原因分析 前
水口剪要剪八次
改善对策 制做一个治具来切。
改 善 现 状 已执行 后
改 善 时间从20秒减少到10秒/PCS。 结果
改善成果个案
项目名称
大金成品
提案人
车间
项目类别
摆放改善 实 施 人 邹龙庚
09/08/ 14
确 认 人 车间
After(图片)
问题点
改 善 原因分析 前
改善对策
胶纸割的长短不一,导致贴胶纸NG
改善 后
员工凭大概随意割胶纸,没有准确长度
现 状 已执行
制作一个治具并在上面按要求割出相 应长度的槽,员工直接用刀片在槽上 划断即可。
改 善 长度保证 结果
改善成果个案
项目名称
捷和必胜
确 认 人 邹龙庚
After(图片)
问 题 点 文件寻找花时间
改 善 原因分析 前
没有定置管理
改善对策 进行定置管理
改 善 现 状 已执行 后
改 善 寻找时间减少2秒/次 结果
改善成果个案
项目名称
捷合齿轮
提案人
车间
项目类别
分模号改善 实 施 人 邹龙庚
Before(图片)
提案时间 完成时间
09/08/ 4
改善成果个案
项目名称
成型机加热板 温度
提案人
公司上层
项目类别
温度测量改 实 施 人 生技
善
Before(图片)
提案时间 完成时间
09/08/ 28
提案部门 公司上
层
09/09/ 3
确 认 人 车间
After(图片)
问题点
改 善 原因分析 前
成型机烘烤板温度无监控,导致烘烤效
果无法保证质量
改善
后
无温控表监控
问 题 点 螺丝散乱
改 善 原因分析 前
没有专用盒子盛放
改善对策 制作专用盒子盛放
改 善 现 状 已执行 后
改 善 螺丝有专用盒子放,明显整齐 结果
改善成果个案
项目名称
友利通面板
提案人
邹龙庚
项目类别
贴胶纸改善 实 施 人 邹龙庚
Before(图片)
提案时间 完成时间
09/08/ 提案部门 IE
14
改 善 产品因堆积被划伤为零 结果
改善成果个案
项目名称
成型片材放置 提 案 人
车间
项目类别
放置改善 实 施 人 邹龙庚
Before(图片)
提案时间 完成时间
09/08/ 29
提案部门 车间
09/08/ 30
确 认
改 善 原因分析 前
成型片材放到工作台上,有被划伤,掉 落到地的风险
提 案 人 邹龙庚
项目类别
操作改善 实 施 人 邹龙庚
Before(图片)
提案时间 完成时间
09/08/ 提案部门 IE
12
09/08/ 12
确 认 人 车间
After(图片)
问 题 点 保护膜卷经常掉下
改 善 原因分析 前
保护膜没有被固定
改善对策 将两头固定使得保护膜不会掉下
改 善 现 状 已执行 后
改 原因分析 善 前
改善对策
1,手动压力不均匀,没有持续时间压 倒一切,每次只压一个.
制做液压形式的治具 做成一出四的治具.
改 善 现 状 已执行 后
压力平整 改 善 速度加快,时间由原来5秒降到3秒 结 果 /PCS
改善成果个案
项目名称
M8底壳
提 案 人 邹龙庚
项目类别
印日期改善 实 施 人 邹龙庚
改善对策 将产品在3000#砂纸把批锋磨掉.
改 善 现 状 已执行 后