中国烧结钕铁硼磁体工艺技术
钕铁硼烧结工艺
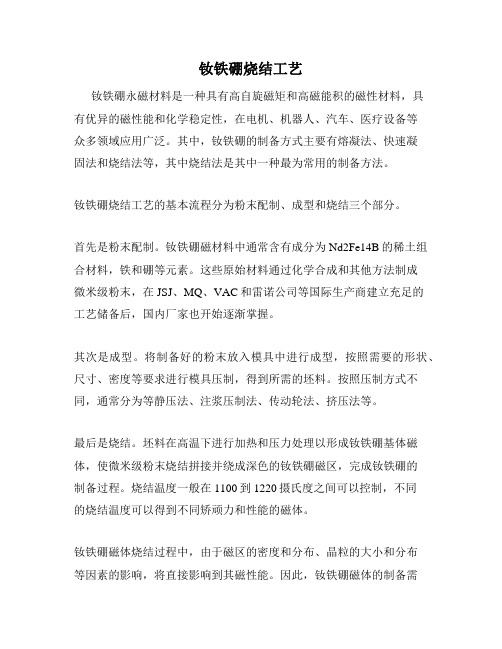
钕铁硼烧结工艺钕铁硼永磁材料是一种具有高自旋磁矩和高磁能积的磁性材料,具有优异的磁性能和化学稳定性,在电机、机器人、汽车、医疗设备等众多领域应用广泛。
其中,钕铁硼的制备方式主要有熔凝法、快速凝固法和烧结法等,其中烧结法是其中一种最为常用的制备方法。
钕铁硼烧结工艺的基本流程分为粉末配制、成型和烧结三个部分。
首先是粉末配制。
钕铁硼磁材料中通常含有成分为Nd2Fe14B的稀土组合材料,铁和硼等元素。
这些原始材料通过化学合成和其他方法制成微米级粉末,在JSJ、MQ、VAC和雷诺公司等国际生产商建立充足的工艺储备后,国内厂家也开始逐渐掌握。
其次是成型。
将制备好的粉末放入模具中进行成型,按照需要的形状、尺寸、密度等要求进行模具压制,得到所需的坯料。
按照压制方式不同,通常分为等静压法、注浆压制法、传动轮法、挤压法等。
最后是烧结。
坯料在高温下进行加热和压力处理以形成钕铁硼基体磁体,使微米级粉末烧结拼接并绕成深色的钕铁硼磁区,完成钕铁硼的制备过程。
烧结温度一般在1100到1220摄氏度之间可以控制,不同的烧结温度可以得到不同矫顽力和性能的磁体。
钕铁硼磁体烧结过程中,由于磁区的密度和分布、晶粒的大小和分布等因素的影响,将直接影响到其磁性能。
因此,钕铁硼磁体的制备需要不断地优化工艺和技术,使其性能更加优异。
总之,钕铁硼是一种优异的磁材料,其中烧结法是制备钕铁硼磁体的常见工艺之一,其制备过程包括粉末配制、成型和烧结,其中每一个环节都关键影响制备的磁体的性能和质量。
随着工艺和技术的不断更新和优化,钕铁硼磁体的应用范围将会进一步拓展。
烧结钕铁硼永磁材料

烧结钕铁硼永磁材料烧结钕铁硼(NdFeB)永磁材料是一种重要的稀土永磁材料,具有高磁能积、高矫顽力、良好的抗腐蚀性和优异的机械性能,被广泛应用于电机、传感器、声学器件等领域。
本文将对烧结钕铁硼永磁材料的制备工艺、性能特点及应用领域进行介绍。
烧结钕铁硼永磁材料的制备工艺主要包括原料配比、混合研磨、成型压制、烧结等步骤。
首先,将氧化铁、钕铁合金粉末和硼酸盐按一定的化学计量比混合均匀,然后进行球磨或气流粉碎,以提高粉末的活性和均匀度。
接下来,将混合粉末通过模具成型,并在一定的温度和压力下进行烧结,使其晶粒长大并形成致密的结构。
最后,通过热处理和表面处理等工艺,得到具有一定形状和性能要求的烧结钕铁硼永磁材料。
烧结钕铁硼永磁材料具有高磁能积、高矫顽力、良好的抗腐蚀性和优异的机械性能。
其中,高磁能积是指在单位体积内所储存的磁能量,是衡量永磁材料性能优劣的重要指标,烧结钕铁硼永磁材料的高磁能积使其在小型化和轻量化设备中得到广泛应用。
高矫顽力则表明材料在外加磁场作用下不易磁化和去磁化,具有良好的稳定性。
此外,烧结钕铁硼永磁材料还具有良好的抗腐蚀性和优异的机械性能,能够满足不同应用场合的要求。
烧结钕铁硼永磁材料被广泛应用于电机、传感器、声学器件等领域。
在电机领域,烧结钕铁硼永磁材料可以制成各种形状和规格的永磁体,用于直流电机、步进电机、无刷直流电机等,广泛应用于家用电器、汽车、航空航天等领域。
在传感器领域,烧结钕铁硼永磁材料可以制成微型传感器,用于测量和控制系统中,具有灵敏度高、稳定性好的特点。
在声学器件领域,烧结钕铁硼永磁材料可以制成扬声器、耳机等产品,具有高音质和高灵敏度。
总之,烧结钕铁硼永磁材料具有制备工艺简单、性能优异、应用广泛的特点,是一种重要的永磁材料。
随着科学技术的不断发展,烧结钕铁硼永磁材料在新能源、新材料等领域的应用前景将更加广阔。
烧结钕铁硼成型工艺
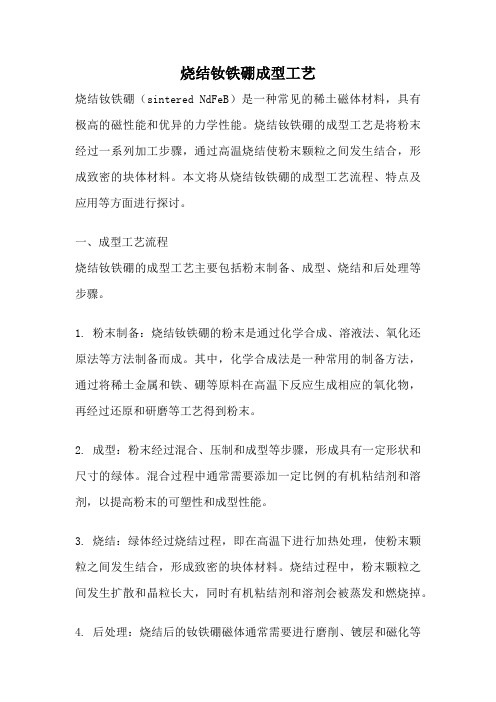
烧结钕铁硼成型工艺烧结钕铁硼(sintered NdFeB)是一种常见的稀土磁体材料,具有极高的磁性能和优异的力学性能。
烧结钕铁硼的成型工艺是将粉末经过一系列加工步骤,通过高温烧结使粉末颗粒之间发生结合,形成致密的块体材料。
本文将从烧结钕铁硼的成型工艺流程、特点及应用等方面进行探讨。
一、成型工艺流程烧结钕铁硼的成型工艺主要包括粉末制备、成型、烧结和后处理等步骤。
1. 粉末制备:烧结钕铁硼的粉末是通过化学合成、溶液法、氧化还原法等方法制备而成。
其中,化学合成法是一种常用的制备方法,通过将稀土金属和铁、硼等原料在高温下反应生成相应的氧化物,再经过还原和研磨等工艺得到粉末。
2. 成型:粉末经过混合、压制和成型等步骤,形成具有一定形状和尺寸的绿体。
混合过程中通常需要添加一定比例的有机粘结剂和溶剂,以提高粉末的可塑性和成型性能。
3. 烧结:绿体经过烧结过程,即在高温下进行加热处理,使粉末颗粒之间发生结合,形成致密的块体材料。
烧结过程中,粉末颗粒之间发生扩散和晶粒长大,同时有机粘结剂和溶剂会被蒸发和燃烧掉。
4. 后处理:烧结后的钕铁硼磁体通常需要进行磨削、镀层和磁化等后处理工艺,以提高磁体的表面光洁度、耐腐蚀性和磁性能。
二、成型工艺特点烧结钕铁硼的成型工艺具有以下特点:1. 粉末冶金工艺:烧结钕铁硼是一种粉末冶金工艺,可以制备出复杂形状的磁体,满足不同工艺要求。
2. 高温烧结:烧结钕铁硼的烧结温度通常在1000℃以上,高温下粉末颗粒之间能够发生扩散和结合,形成致密的磁体材料。
3. 熔点低:钕铁硼的主要成分为稀土元素钕和铁、硼等金属,这些金属具有较低的熔点,便于烧结过程的实施。
4. 磁性能优异:烧结钕铁硼具有极高的磁性能,磁能积和剩磁等指标远高于其他磁体材料。
三、应用领域烧结钕铁硼广泛应用于电子、电机、汽车、航空航天等领域。
主要的应用包括:1. 电机和发电机:烧结钕铁硼可以制成各种形状和规格的磁体,用于电机和发电机中,提高电机的输出功率和效率。
烧结钕铁硼磁体的制备工艺
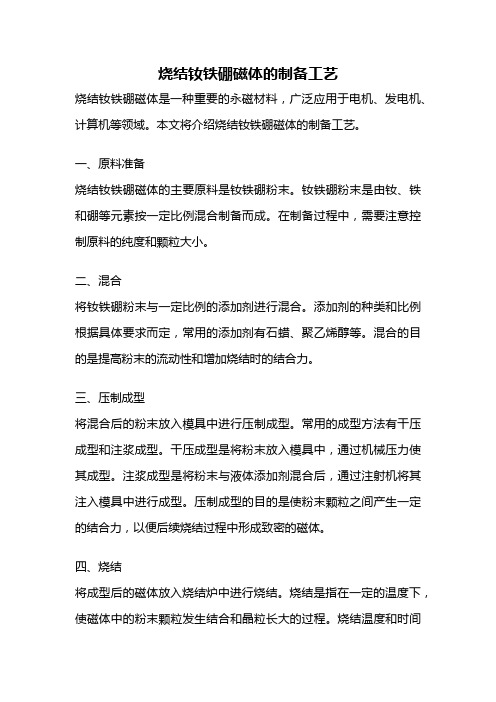
烧结钕铁硼磁体的制备工艺烧结钕铁硼磁体是一种重要的永磁材料,广泛应用于电机、发电机、计算机等领域。
本文将介绍烧结钕铁硼磁体的制备工艺。
一、原料准备烧结钕铁硼磁体的主要原料是钕铁硼粉末。
钕铁硼粉末是由钕、铁和硼等元素按一定比例混合制备而成。
在制备过程中,需要注意控制原料的纯度和颗粒大小。
二、混合将钕铁硼粉末与一定比例的添加剂进行混合。
添加剂的种类和比例根据具体要求而定,常用的添加剂有石蜡、聚乙烯醇等。
混合的目的是提高粉末的流动性和增加烧结时的结合力。
三、压制成型将混合后的粉末放入模具中进行压制成型。
常用的成型方法有干压成型和注浆成型。
干压成型是将粉末放入模具中,通过机械压力使其成型。
注浆成型是将粉末与液体添加剂混合后,通过注射机将其注入模具中进行成型。
压制成型的目的是使粉末颗粒之间产生一定的结合力,以便后续烧结过程中形成致密的磁体。
四、烧结将成型后的磁体放入烧结炉中进行烧结。
烧结是指在一定的温度下,使磁体中的粉末颗粒发生结合和晶粒长大的过程。
烧结温度和时间的选择要根据具体的材料和要求来确定。
烧结过程中,需要控制好温度和气氛,以避免氧化和挥发等问题的发生。
五、磁化处理经过烧结后的磁体通常需要进行磁化处理,以获得所需的磁性能。
磁化处理可以通过电磁线圈或永磁体来实现。
磁化处理的目的是使磁体中的磁畴定向一致,从而提高磁体的磁化强度和剩磁。
六、表面处理经过磁化处理后的磁体还需要进行表面处理。
表面处理的目的是提高磁体的耐腐蚀性和机械强度,常用的方法有电镀、喷涂等。
总结:烧结钕铁硼磁体的制备工艺包括原料准备、混合、压制成型、烧结、磁化处理和表面处理等步骤。
这些步骤的每一环节都需要严格控制,以确保磁体的质量和性能。
随着科学技术的不断进步,烧结钕铁硼磁体的制备工艺也在不断改进,以提高磁体的性能和应用范围。
烧结高性能稀土钕铁硼磁体制备工艺分析

烧结高性能稀土钕铁硼磁体制备工艺分析发布时间:2021-03-17T02:25:00.395Z 来源:《中国科技人才》2021年第4期作者:张楠[导读] 现今,国外制造商具有生产N50,N52和N55品牌产品的能力,而我国的主要产品仍是N45以下的低档产品,产品的一致性和稳定性方面还存在很多问题。
甘肃稀土新材料股份有限公司甘肃白银 730922摘要:以钕铁硼(Nd-Fe-B)而言,其为第三代稀土永磁材料,存在着体积小,重量轻,磁通密度高,温度系数高和动态恢复特性好的特点。
它是迄今为止性价比最高的磁体,被称为“磁体之王”,广泛用于计算机行业和其他工业领域。
针对国产化设备制备高性能钕铁硼磁体产品一致性和稳定性不高这一行业焦点问题,以N52品牌磁体的生产过程为典型的测试示例,研究合金熔炼,氢破制粉,烧结和成型过程。
磁铁材料的关键控制参数会影响磁铁材料的微观结构和磁性能,总结其影响因素的一般规则,并对相关影响因素进行均衡的分析和讨论,然后提出总体思路和计划方案优化。
关键词:烧结高性能;钕铁硼磁;制备工艺1绪论现今,国外制造商具有生产N50,N52和N55品牌产品的能力,而我国的主要产品仍是N45以下的低档产品,产品的一致性和稳定性方面还存在很多问题。
为了解决这些问题,国内外许多学者进行了研究,并在切屑纺丝,氢气粉碎,气流粉碎和等静压等设备改进和技术创新方面取得了重大突破。
在上述研究的基础上,本文以国产设备为基础,通过新技术的应用和开发,制备出高性能的稀土永磁材料,从而提高了稀土资源的利用率,增加产品附加值,增强行业竞争力。
2试验方法2.1试验材料制备稀土永磁材料成分为:Pr Nd 30.7%(wt),B 0.97%(wt),Cu 0.15%(wt),Ga 0.20%(wt),Zr 0.10%(wt),Go 0.50%(wt),其余为高纯铁 Fe。
2.2试验工艺按比例称取原材料投入真空熔炼炉中进行熔炼,浇铸到冷却辊轮进行铸片。
烧结钕铁硼的生产工艺流程要点
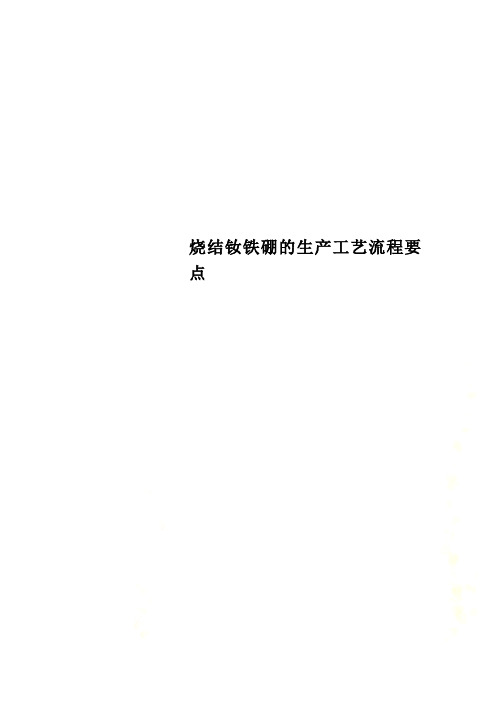
烧结钕铁硼的生产工艺流程要点烧结钕铁硼的生产工艺流程发布日期:2012-03-30 浏览次数:167核心提示:本文对稀土永磁材料的发展过程、性能要求、主要类型等方面做了介绍,着重介绍了烧结钕铁硼磁体的生产工艺流程,最后对目前烧结钕铁硼在生产、科研、生活等各领域中的应用进行了总结,并对其发展方向进行了思考,指出应深入研究烧结钕铁硼磁体生产工艺,提高我国钕铁硼磁体的产品质量,才能增加企业自身的竞争力。
1.1稀土永磁材料概述从广义上讲,所有能被磁场磁化、在实际应用中主要利用材料所具有的磁特性的一类材料成为磁性材料。
它包括硬磁材料、软磁材料、半硬磁材料、磁致伸缩材料、磁光材料、磁泡材料和磁制冷材料等,其中用量最大的是硬磁材料和软磁材料。
硬磁材料和软磁材料的主要区别是硬磁材料的各向异性场高、矫顽力高、磁滞回线面积大、技术磁化到饱和需要的磁场大。
由于软磁材料的矫顽力低,技术磁化到饱和并去掉外磁场后,它很容易退磁,而硬磁材料由于矫顽力较高,经技术磁化到饱和并去掉磁场后,它仍然长期保持很强的磁性,因此硬磁材料又称为永磁材料或恒磁材料。
古代,人们利用矿石中的天然磁铁矿打磨成所需要的形状,用来指南或吸引铁质器件,指南针是中国古代四大发明之一,对人类文明和社会进步做出过重要贡献。
近代,磁性材料的研究和应用始于工业革命之后,并在短时间内得到迅速发展.现今,对磁性材料的研究和应用无论在广度或者深度上都是以前无可比拟的,各类高性能磁性材料,尤其是稀土永磁材料的开发和应用对现代工业和高新技术产业的发展起着巨大的推动作用。
1.2永磁材料性能要求永磁材料的主要性能是由以下几个参数决定的1.2.1最大磁能积:最大磁能积是退磁曲线上磁感应强度和磁场强度乘积的最大值。
这个值越大,说明单位体积内存储的磁能越大,材料的性能越好。
1.2.2饱和磁化强度:是永磁材料极为重要的参数。
永磁材料的饱和磁化强度越高,它标志着材料的最大磁能积和剩磁可能达到的上限值越高。
一种烧结钕铁硼磁体及其制备方法与流程

一种烧结钕铁硼磁体及其制备方法与流程篇一:哎呀,这题目也太难懂啦!什么“烧结钕铁硼磁体”,我一个小学生哪能明白呀!不过,为了写好这篇文章,我还是要努力试试看。
就好像搭积木一样,这个“烧结钕铁硼磁体”的制备是不是也有一步步的流程呢?我猜应该是有的。
你想啊,我们做手工的时候,都得一步一步来,哪能一下子就做好呀!这制备“烧结钕铁硼磁体”肯定也是这个道理。
比如说,第一步是不是得准备好那些材料呀?就像我们做饭得先有菜有米一样。
那这些材料得精挑细选吧,不能随随便便的,不然怎么能做出好的磁体呢?然后呢,是不是得有一些特别的工具和设备来帮忙?这就好像我们画画要有画笔和颜料一样。
在制作的过程中,那些叔叔阿姨们是不是得特别小心?稍微出点差错,那不就前功尽弃啦?还有啊,温度、时间这些是不是都得控制得刚刚好?这就跟我们考试的时候,时间掌握不好就做不完题目一样。
哎呀,我真的是想破脑袋在想这个“烧结钕铁硼磁体及其制备方法与流程”,可还是觉得好复杂呀!不过我觉得,科学就是这样,总是充满了挑战和难题。
虽然我现在不太懂,但我相信,只要努力学习,总有一天我会明白的!我的观点就是:虽然现在这对我来说太难了,但科学的世界那么神奇,我一定要好好学习,将来去探索更多的奥秘!篇二:哎呀呀,这题目也太难懂啦!什么是烧结钕铁硼磁体呀?我一个小学生,根本搞不明白嘛!不过,我还是想努力试试,给您讲讲我想象中的它。
您想想,一块小小的磁体,居然有那么多神秘的制备方法和流程,这就好像我们做一个超级复杂的手工,每一步都得小心翼翼,不能出错。
比如说,就像我们搭积木一样,要先准备好各种各样的小木块,这在制备磁体里,就是要先选好材料。
然后呢,再按照一定的顺序把积木搭起来,这就好比按照特定的流程去处理那些材料。
在制备过程中,那些科学家叔叔阿姨们,就像是超级厉害的魔法师!他们得特别小心地控制温度、压力这些东西。
这温度和压力呀,就像是两个调皮的小精灵,如果控制不好,它们就会捣乱,让整个制备过程都失败。
烧结钕铁硼生产工艺流程
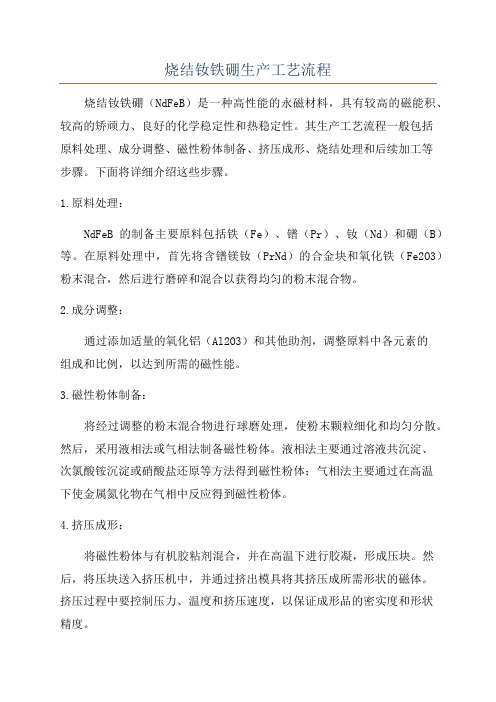
烧结钕铁硼生产工艺流程烧结钕铁硼(NdFeB)是一种高性能的永磁材料,具有较高的磁能积、较高的矫顽力、良好的化学稳定性和热稳定性。
其生产工艺流程一般包括原料处理、成分调整、磁性粉体制备、挤压成形、烧结处理和后续加工等步骤。
下面将详细介绍这些步骤。
1.原料处理:NdFeB的制备主要原料包括铁(Fe)、镨(Pr)、钕(Nd)和硼(B)等。
在原料处理中,首先将含镨镁钕(PrNd)的合金块和氧化铁(Fe2O3)粉末混合,然后进行磨碎和混合以获得均匀的粉末混合物。
2.成分调整:通过添加适量的氧化铝(Al2O3)和其他助剂,调整原料中各元素的组成和比例,以达到所需的磁性能。
3.磁性粉体制备:将经过调整的粉末混合物进行球磨处理,使粉末颗粒细化和均匀分散。
然后,采用液相法或气相法制备磁性粉体。
液相法主要通过溶液共沉淀、次氯酸铵沉淀或硝酸盐还原等方法得到磁性粉体;气相法主要通过在高温下使金属氮化物在气相中反应得到磁性粉体。
4.挤压成形:将磁性粉体与有机胶粘剂混合,并在高温下进行胶凝,形成压块。
然后,将压块送入挤压机中,并通过挤出模具将其挤压成所需形状的磁体。
挤压过程中要控制压力、温度和挤压速度,以保证成形品的密实度和形状精度。
5.烧结处理:将挤压成形的磁体放入高温炉中进行烧结处理。
烧结温度一般在1000℃-1200℃之间,同时施加适量的氮气或氩气作为保护气氛。
烧结过程中,粉末表面的有机物质在高温下分解并挥发,其余的金属氧化物被还原为金属,并且发生晶界扩散和再结晶,形成致密的磁体。
6.后续加工:经过烧结处理的磁体可以进行后续加工,如切割、研磨和涂层等,以得到所需的尺寸和表面质量。
切割一般采用线切割或电火花切割,研磨则通过磨料和研磨机械进行,涂层可以采用镀铜、镀锌等方法进行。
以上就是烧结钕铁硼的生产工艺流程。
这个流程是一个相对简化的描述,实际的工艺流程可能会有所不同,主要取决于具体的生产设备和工艺要求。
不过,总体来说,这个流程可以帮助我们理解烧结钕铁硼的制备过程。
- 1、下载文档前请自行甄别文档内容的完整性,平台不提供额外的编辑、内容补充、找答案等附加服务。
- 2、"仅部分预览"的文档,不可在线预览部分如存在完整性等问题,可反馈申请退款(可完整预览的文档不适用该条件!)。
- 3、如文档侵犯您的权益,请联系客服反馈,我们会尽快为您处理(人工客服工作时间:9:00-18:30)。
近十年内中国钕铁硼磁体产业取得了长速发展,目前烧结钕铁硼的销售量已与日本相当,各占全球41%左右,被称为向阳工业、跨世纪工业。
2000年全球烧结钕铁硼磁体产量约为15090吨,中国的产量为5550吨(37%日本的产量为7700吨(占50%美国和欧洲分别为1020吨(占7%和820吨(占6%此基础上,扩产势头不减,年产千吨的大企业越来越多。
中科三环系统的宁波科宁达工业有限公司及天津三环乐喜新资料有限公司都已达到此规模,而且中科三环所属的北京环磁新技术有限公司、盂县京秀磁材有限公司及肇庆市京粤磁厂(年产500吨扩产项目已完成)等都有扩产计划。
宁波韵升强磁资料有限公司也已经达到千吨规模。
另外有三四家,或设计能力为年千吨,或已有千吨年生产能力,但目前实际生产量都未到而生产能力或生产量已经达到年产100吨的公司估计在15家左右。
面对如此强劲的发展势头,禁不住要问:中国钕铁硼和世界水平相比到底在哪个层次?还有哪些问题?将来向什么方向发展?1管理模式的改变与技术并重以往我钕铁硼企业比较重视技术进步,把性能提高看作企业发展的关键。
过去由于我与国外相比性能相差太远,所以性能如何成为制约企业发展的关键。
没有高的性能我就没有订单,所以过去的做法并没有错。
但是今天,钕铁硼骨干企业基本在性能上都能做到N4545M42H40SH35UH32EH等,有些企业甚至可以做到N5048M45H38UH35EH等,仅从性能上讲基本与世界水准持平或略低,起码已经到中上水平。
而实际上N50之类的高性能订单并不是太多,大多数订单在45M及以下的档次上因此现在关键是"性能做稳定,产品内在品质好,及时交货并且价格低"而要达到上述几点,企业内部的管理将是重要的一环。
认为中国的钕铁硼企业大致可分为三类:1民营企业、2真正合资企业、3国有及类国有企业。
之所以使用"真正合资企业"说法,因为某些企业虽然名义上为合资企业,但实际管理上为激进国有企业的一套管理方法。
这样的企业在钕铁硼行业中并不在少数。
通过访问诸多的同行,发现民营企业的管理效率最高,而且各家都有自己的管理及产品特色。
民营企业管理效率较高本来是情理之中的但如此之高仍然使我大吃一惊。
仅以两个较有代表性的企业为例,年产量在500600吨之间,设备维修部仅有6个人(3个电工,3个机修)而一般国有及类国有同样规模的企业,设备维修部的人数在15~25人之间。
不只是人数少,而且在设备维修效率上民营企业要远远高于国有及类国有企业。
如果我用20个人干6个人同样的工作,那么竞争之中孰赢孰输显而易见。
之所以能够用6个人干20个人的工作,因为以下三点:一般维修由生产班组长自己完成,设备维修部人员仅仅负责大修,设备维修费与生产部挂钩;2部件替换维修法;3空余时间设备维修部人员改造旧设备并制造新设备,同时负责新设备的装置等。
第一点使操作人员更加珍惜设备,大大减少由于误操作而造成的设备损坏,减少了设备维修的次数与成本。
第二点做法是把损坏部件直接换下来,装上好部件,生产继续进行,同时维修损坏部件。
这样维修占用很少的生产时间,大大提高设备的利用率。
完成第三点就意味着可以根据使用情况,使设备设计上得到改善,更适合于本公司的具体情况,从而减少维修。
如果局部设备由自己制造,则维修人员对设备的情况极为熟悉,有利于维修。
以上仅仅为一个实例,从根本上来讲关键是思想的转变和制度的革新。
当然,如果让国有企业或类国有企业完全依照民营企业的一套来办,显然是幼稚的而且是行不通的不过国有企业或类国有企业完全可以参照民营企业的一些方法进行改革,认为这不仅可能,而且一定能够胜利。
记得在太原某公司的一位老总说过这样的一句话"现在以小吃大,以快吃慢"相信这并非虚言。
如果许多大企业仍然是国有企业保守的一套管理办法,这种局面用不了多久就会出现。
依我观点看,也想说一句话:"现在以有特色吃无特色,以高效率吃低效率,以低利息吃高成本"宁波永久磁业的特色在于高效率,较高牌号的产品等;宁波招宝磁业的特色在于产品种类,重点放在高矫顽力产品上;盂县京秀磁材有限公司的管理效率、小圆柱产品特色及低利息值得学习;太原天和高新技术有限公司的特色在于高牌号、高价钱,管理上也有许多值得借鉴之处。
相信这些公司在将来的3~5年内都会有较大的发展。
实际上所有的钕铁硼企业都有许多共同之处,应该在管理上有许多通用的规则,这里我提出几点,供大家参考。
1.1生产各工序实行"联产承包制"联产承包制并非什么新的方法,实际1978年在国的农村就已经开始推广。
20多年过去了事实证明这种方法在农村是胜利的而在钕铁硼行业的许多民营企业中正在胜利地推行这种方法,所以在国有或类国有企业及合资企业中,这种方法对于提高工作效率、保证生产质量、降低利息等都应该是有效的原因很简单,因为工作的业绩与收入捆绑到一起,真正体现了"多劳多得"原则。
可以按熔炼、制粉(包括中碎、气流磨等)成型、烧结、质检、后加工、包装等分组承包。
1.2完善"各工序的自检与他检"如果要采取联产承包制,必需加强自检与他检,否则我会仅仅强调数量而忽视质量。
每一工序必需有自检质量及数量报告同时必需得到下一工序的检认可方可进入下一工序,质检部门作为仲裁单位将在保证质量方面发挥越来越大的作用。
1.3生产设备日常维修与设备部脱钩:基本的日常设备维修应由承包人自己完成。
如果承包人没有能力完成,应该采取与维修工联合承包的方式或日常维修人员一定要隶属于生产车间,并且不是全职维修工。
较大公司的设备部应有2~3名专职人员,配合研发与生产负责设备改造、大修、装置并调试新设备、制造新设备等工作。
强调管理的重要是因为如果管理跟不上,即使再好的技术和产品性能仍然不能保证我激烈的市场竞争中取胜。
可以说今天已经到要强调管理的时候了但这并不意味我技术已经达到完美,技术方面我仍然有许多工作要做。
2技术发展方向对于钕铁硼的认识,单单从知识角度讲,中国人比日本人、美国人、欧洲人等都不差,实际上所谓的技术进步在今天来讲至少有90%设备的进步。
从下面的论述中我会看到有许多工作要做。
2.1 熔炼2.1.1带铸工艺又称速凝薄片工艺。
这种工艺最早由日本的饿三德金属(仅提供速凝薄带,不生产磁体)与住友金属采用并获得专利权。
带铸工艺的特点在于有效地消除了α-Fe富钕相分布均匀并使晶粒得到细化,容易得到高剩磁及高矫顽力的产品。
中国的钕铁硼磁体厂家在1997年前后开始知道此信息并展开研究工作。
经过5年多的努力,中国的设备厂家已经在这方面取得了长足的进步。
现在不只有25kg甩带炉,而且50kg和100kg甩带炉都已经市场化。
但是就带子的一致性上来讲,与三德金属相比还有相当的差异,自由面凹凸不平的现象很严重。
刚开始时的主要问题是带子厚度问题,那时将带子厚度甩到大于0.2mm很困难,存在大量的非晶,很难用于烧结钕铁硼。
现在几个主要厂家的带子厚度都能够做到0.3mm以上,有的甚至可到0.5mm除了带子一致性不好外,粘连问题亦是一个影响质量的重要问题。
图1给出某厂家的产品(有粘连现象)横截面金相)可见大量的α-Fe析出;图2另一厂家的带子的金相,带子厚度在0.3~0.5mm柱状晶晶粒宽大,大部分柱状晶宽度在15~30μm之间,无α-Fe析出;但富钕相分布不太均匀。
图3为日本三德金属的速凝薄带,大部分柱状晶宽度在3μ左右,无α-Fe析出,富钕相分布均匀。
由三张金相照片可以清楚地看到目前的差异。
如果对我国目前的甩带情况下一个结论,则是可用,但不太令人满意。
认为除了要解决均匀性、一致性的问题以外,同时亦要解决产量与效率的问题。
未来3~5年内,设备厂家应该能够提供500~1000kg甩带炉。
现在甩带炉的高度不够,至少要在10~15m高才干够有足够的空间和薄带冷却时间。
如果速凝薄带合格,则带铸工艺应该说是最简单的工艺之一(配方单一,中碎及气流磨效率高,其余与激进工艺无明显区别)因此在中国推广的可能性也最大。
2.1.2.双合金工艺或类双合金工艺除了速凝薄带的工作以外,国大多数厂家的精力放在降低铸锭厚度,提高冷却效率上。
降低铸锭厚度方面已经能够广泛采用双面水冷厚10mm铸锭的工艺,也有采用100kg转盘式单面冷浇注(厚15mm左右)工艺的厂家。
有的厂家采用了盐水冷冻液冷却熔炼炉锭模的方法。
所有这些方法对我提高磁体性能都做出了积极的贡献。
但是也应该看到这种思路几乎已经没有太大的发展空间(浇口不可能更窄,锭模不可能更大;转盘式铸锭厚薄不匀,外表难以打磨)需要换一下思路。
双合金法应该是一条可行之路。
非常遗憾的过去的若干年里中国的钕铁硼厂家大多数没有对双合金法给予足够重视。
双合金法并不是什么玩意,早就有所知,而且其优点也是显而易见的如果采用双合金法我将不需要炼几十种不同配方的锭子,只要有几个主相合金和几个富钕相合金就可以得到所有性能的磁体。
德国的VA C及日本的日立金属等采用这种方法得到性能优异的烧结钕铁硼磁体,而且其产品性能一点都不比住友采用带铸法的产品差。
现在普遍做法是把锭子设法作薄,而双合金法并不太在意锭子的厚度,相反,由于要经过均匀化处理,所以过薄的锭子反而易造成氧化(因为锭子越薄外表积越大)认为在目前中国宜采用200~500kg熔炼炉来炼这种锭子,否则其优点(均匀性、一致性优于25kg炉,效率高等)难以显现进去。
均匀化处理是双合金法的关键一步,实际上经过均匀化处理的锭子亦可以用于单合金法,这里把它叫做"类双合金法"这种方法已经被国内许多厂家用来生产高性能的产品。
但是认为如果仍然用25kg熔炼炉,则这种方法的潜力未能充分发挥。
总之,对于熔炼我应向两极发展:或者更薄,或者更厚。
2.1.3离心甩铸法这种方法是将盛有合金熔液的坩锅置于旋转的金属筒中,当合金熔液倒下时,由于离心作用,熔液贴在金属筒壁上迅速冷凝。
这是一种界于甩带法和激进锭模浇注法之间的一种方法,其产品厚度小于10mm性能优良,效率高,很有发展潜力。
2.2中碎2.2.1氢爆碎工艺(HD这也不是什么新的东西,而且从确切意义上讲,不应该单独被称为一种工艺,只不过是生产中的一步。
即可以用于甩带料,亦可以用于普通铸锭,同时也可以用双合金法。
对于其工艺我都已比较熟悉,主要是由于设备的原因,将HD法用于批量生产推迟了至少3年。
现在氢爆设备的国产化的雏形已经完成,预计在最近三年内至少有一半的中国烧结钕铁硼生产将利用HD工艺。
可喜的据我所知,目前至少已经有三家企业将HD用于批量生产。
通过采用HD可以提高气流磨效率(50~80kg/h改善磁体微结构,大大提高抗蚀能力(例如我某产品在PCT实验箱中120℃,0.2MPa168h后失重仅8mg/cm2图4为HD工艺所得产品的金相照片,晶粒大小在10μm左右。