烧结钕铁硼的生产工艺流程
烧结钕铁硼的生产工艺流程要点

烧结钕铁硼的生产工艺流程要点
第一步,原料搅拌。
烧结钕铁硼的原料包括钕、铁、硼和其他添加剂等。
这些原料首先要经过严格的筛选和粉碎,然后按照一定的比例混合,
并添加一些流动剂,以便于原料的均匀混合。
最后,通过球磨机或其他搅
拌设备进行搅拌,使得原料的成分均匀。
第二步,成型。
搅拌均匀的原料会被送到成型机中进行成型。
成型的
目的是将原料压制成所需的形状,常见的形状有圆柱形、方形、棒形等。
成型机可以采用冷压成型或热压成型的方式。
在成型过程中,需要控制成
型压力和温度,以确保成型件的密实度和尺寸精度。
第三步,烧结。
成型后的绿体会被送入烧结炉中进行烧结。
烧结是将
原料在高温下进行热处理,使其结晶相互结合,形成致密的永磁材料。
烧
结过程中的主要控制参数有温度、时间和气氛。
通常情况下,烧结温度为1100-1300摄氏度,烧结时间为1-3小时,烧结气氛可使用氮气、氢气等。
烧结后的产品会形成一定的孔隙率,需要进一步处理。
第四步,磨削。
烧结后的产品会有一定的尺寸误差和表面粗糙度,需
要进行磨削处理。
磨削可以采用平面磨床、内外圆磨床等设备进行。
通过
磨削,可以使产品的尺寸精确,表面光滑,以提高产品的质量和加工精度。
第五步,磁化。
磨削后的产品需要经过磁化处理,以获得所需的磁性能。
磁化可以采用交流或直流磁化方法。
在磁化过程中,需要通过磁场的
作用,使产品的磁矩方向趋于一致,以形成良好的磁性能。
钕铁硼烧结工艺
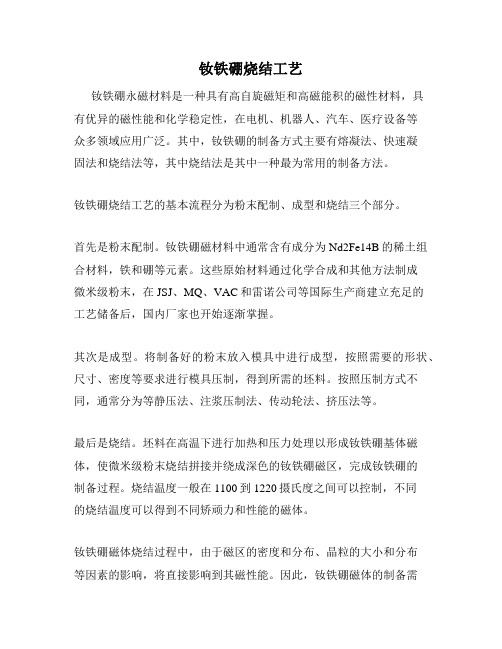
钕铁硼烧结工艺钕铁硼永磁材料是一种具有高自旋磁矩和高磁能积的磁性材料,具有优异的磁性能和化学稳定性,在电机、机器人、汽车、医疗设备等众多领域应用广泛。
其中,钕铁硼的制备方式主要有熔凝法、快速凝固法和烧结法等,其中烧结法是其中一种最为常用的制备方法。
钕铁硼烧结工艺的基本流程分为粉末配制、成型和烧结三个部分。
首先是粉末配制。
钕铁硼磁材料中通常含有成分为Nd2Fe14B的稀土组合材料,铁和硼等元素。
这些原始材料通过化学合成和其他方法制成微米级粉末,在JSJ、MQ、VAC和雷诺公司等国际生产商建立充足的工艺储备后,国内厂家也开始逐渐掌握。
其次是成型。
将制备好的粉末放入模具中进行成型,按照需要的形状、尺寸、密度等要求进行模具压制,得到所需的坯料。
按照压制方式不同,通常分为等静压法、注浆压制法、传动轮法、挤压法等。
最后是烧结。
坯料在高温下进行加热和压力处理以形成钕铁硼基体磁体,使微米级粉末烧结拼接并绕成深色的钕铁硼磁区,完成钕铁硼的制备过程。
烧结温度一般在1100到1220摄氏度之间可以控制,不同的烧结温度可以得到不同矫顽力和性能的磁体。
钕铁硼磁体烧结过程中,由于磁区的密度和分布、晶粒的大小和分布等因素的影响,将直接影响到其磁性能。
因此,钕铁硼磁体的制备需要不断地优化工艺和技术,使其性能更加优异。
总之,钕铁硼是一种优异的磁材料,其中烧结法是制备钕铁硼磁体的常见工艺之一,其制备过程包括粉末配制、成型和烧结,其中每一个环节都关键影响制备的磁体的性能和质量。
随着工艺和技术的不断更新和优化,钕铁硼磁体的应用范围将会进一步拓展。
烧结钕铁硼永磁材料

烧结钕铁硼永磁材料烧结钕铁硼(NdFeB)永磁材料是一种重要的稀土永磁材料,具有高磁能积、高矫顽力、良好的抗腐蚀性和优异的机械性能,被广泛应用于电机、传感器、声学器件等领域。
本文将对烧结钕铁硼永磁材料的制备工艺、性能特点及应用领域进行介绍。
烧结钕铁硼永磁材料的制备工艺主要包括原料配比、混合研磨、成型压制、烧结等步骤。
首先,将氧化铁、钕铁合金粉末和硼酸盐按一定的化学计量比混合均匀,然后进行球磨或气流粉碎,以提高粉末的活性和均匀度。
接下来,将混合粉末通过模具成型,并在一定的温度和压力下进行烧结,使其晶粒长大并形成致密的结构。
最后,通过热处理和表面处理等工艺,得到具有一定形状和性能要求的烧结钕铁硼永磁材料。
烧结钕铁硼永磁材料具有高磁能积、高矫顽力、良好的抗腐蚀性和优异的机械性能。
其中,高磁能积是指在单位体积内所储存的磁能量,是衡量永磁材料性能优劣的重要指标,烧结钕铁硼永磁材料的高磁能积使其在小型化和轻量化设备中得到广泛应用。
高矫顽力则表明材料在外加磁场作用下不易磁化和去磁化,具有良好的稳定性。
此外,烧结钕铁硼永磁材料还具有良好的抗腐蚀性和优异的机械性能,能够满足不同应用场合的要求。
烧结钕铁硼永磁材料被广泛应用于电机、传感器、声学器件等领域。
在电机领域,烧结钕铁硼永磁材料可以制成各种形状和规格的永磁体,用于直流电机、步进电机、无刷直流电机等,广泛应用于家用电器、汽车、航空航天等领域。
在传感器领域,烧结钕铁硼永磁材料可以制成微型传感器,用于测量和控制系统中,具有灵敏度高、稳定性好的特点。
在声学器件领域,烧结钕铁硼永磁材料可以制成扬声器、耳机等产品,具有高音质和高灵敏度。
总之,烧结钕铁硼永磁材料具有制备工艺简单、性能优异、应用广泛的特点,是一种重要的永磁材料。
随着科学技术的不断发展,烧结钕铁硼永磁材料在新能源、新材料等领域的应用前景将更加广阔。
烧结钕铁硼成型工艺
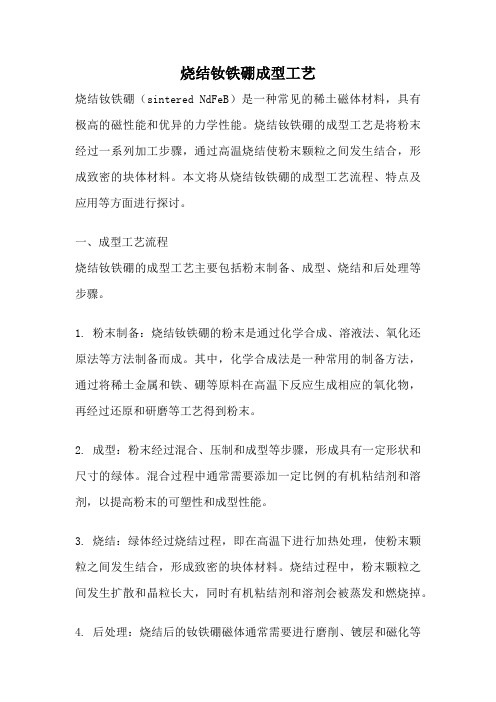
烧结钕铁硼成型工艺烧结钕铁硼(sintered NdFeB)是一种常见的稀土磁体材料,具有极高的磁性能和优异的力学性能。
烧结钕铁硼的成型工艺是将粉末经过一系列加工步骤,通过高温烧结使粉末颗粒之间发生结合,形成致密的块体材料。
本文将从烧结钕铁硼的成型工艺流程、特点及应用等方面进行探讨。
一、成型工艺流程烧结钕铁硼的成型工艺主要包括粉末制备、成型、烧结和后处理等步骤。
1. 粉末制备:烧结钕铁硼的粉末是通过化学合成、溶液法、氧化还原法等方法制备而成。
其中,化学合成法是一种常用的制备方法,通过将稀土金属和铁、硼等原料在高温下反应生成相应的氧化物,再经过还原和研磨等工艺得到粉末。
2. 成型:粉末经过混合、压制和成型等步骤,形成具有一定形状和尺寸的绿体。
混合过程中通常需要添加一定比例的有机粘结剂和溶剂,以提高粉末的可塑性和成型性能。
3. 烧结:绿体经过烧结过程,即在高温下进行加热处理,使粉末颗粒之间发生结合,形成致密的块体材料。
烧结过程中,粉末颗粒之间发生扩散和晶粒长大,同时有机粘结剂和溶剂会被蒸发和燃烧掉。
4. 后处理:烧结后的钕铁硼磁体通常需要进行磨削、镀层和磁化等后处理工艺,以提高磁体的表面光洁度、耐腐蚀性和磁性能。
二、成型工艺特点烧结钕铁硼的成型工艺具有以下特点:1. 粉末冶金工艺:烧结钕铁硼是一种粉末冶金工艺,可以制备出复杂形状的磁体,满足不同工艺要求。
2. 高温烧结:烧结钕铁硼的烧结温度通常在1000℃以上,高温下粉末颗粒之间能够发生扩散和结合,形成致密的磁体材料。
3. 熔点低:钕铁硼的主要成分为稀土元素钕和铁、硼等金属,这些金属具有较低的熔点,便于烧结过程的实施。
4. 磁性能优异:烧结钕铁硼具有极高的磁性能,磁能积和剩磁等指标远高于其他磁体材料。
三、应用领域烧结钕铁硼广泛应用于电子、电机、汽车、航空航天等领域。
主要的应用包括:1. 电机和发电机:烧结钕铁硼可以制成各种形状和规格的磁体,用于电机和发电机中,提高电机的输出功率和效率。
烧结钕铁硼的生产工艺流程要点
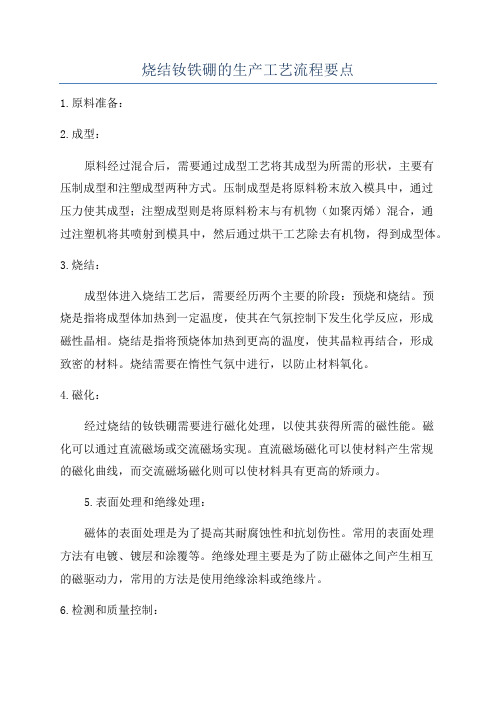
烧结钕铁硼的生产工艺流程要点1.原料准备:2.成型:原料经过混合后,需要通过成型工艺将其成型为所需的形状,主要有压制成型和注塑成型两种方式。
压制成型是将原料粉末放入模具中,通过压力使其成型;注塑成型则是将原料粉末与有机物(如聚丙烯)混合,通过注塑机将其喷射到模具中,然后通过烘干工艺除去有机物,得到成型体。
3.烧结:成型体进入烧结工艺后,需要经历两个主要的阶段:预烧和烧结。
预烧是指将成型体加热到一定温度,使其在气氛控制下发生化学反应,形成磁性晶相。
烧结是指将预烧体加热到更高的温度,使其晶粒再结合,形成致密的材料。
烧结需要在惰性气氛中进行,以防止材料氧化。
4.磁化:经过烧结的钕铁硼需要进行磁化处理,以使其获得所需的磁性能。
磁化可以通过直流磁场或交流磁场实现。
直流磁场磁化可以使材料产生常规的磁化曲线,而交流磁场磁化则可以使材料具有更高的矫顽力。
5.表面处理和绝缘处理:磁体的表面处理是为了提高其耐腐蚀性和抗划伤性。
常用的表面处理方法有电镀、镀层和涂覆等。
绝缘处理主要是为了防止磁体之间产生相互的磁驱动力,常用的方法是使用绝缘涂料或绝缘片。
6.检测和质量控制:在整个生产过程中,需要进行各种检测和质量控制措施,以确保产品的质量稳定。
常用的检测方法有磁性测试、物理性能测试、化学成分分析、尺寸测量等。
总结起来,烧结钕铁硼的生产工艺流程主要包括原料准备、成型、烧结、磁化、表面处理和绝缘处理等环节。
通过精心控制每个环节的工艺参数和质量控制措施,可以生产出高质量的烧结钕铁硼产品,满足不同行业的需求。
烧结钕铁硼生产工艺
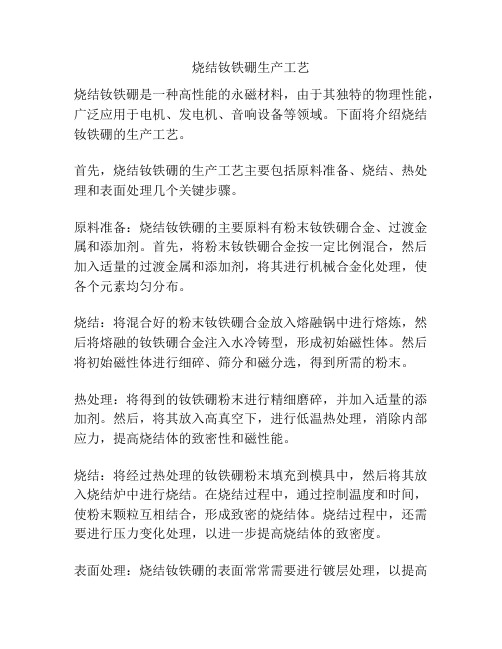
烧结钕铁硼生产工艺
烧结钕铁硼是一种高性能的永磁材料,由于其独特的物理性能,广泛应用于电机、发电机、音响设备等领域。
下面将介绍烧结钕铁硼的生产工艺。
首先,烧结钕铁硼的生产工艺主要包括原料准备、烧结、热处理和表面处理几个关键步骤。
原料准备:烧结钕铁硼的主要原料有粉末钕铁硼合金、过渡金属和添加剂。
首先,将粉末钕铁硼合金按一定比例混合,然后加入适量的过渡金属和添加剂,将其进行机械合金化处理,使各个元素均匀分布。
烧结:将混合好的粉末钕铁硼合金放入熔融锅中进行熔炼,然后将熔融的钕铁硼合金注入水冷铸型,形成初始磁性体。
然后将初始磁性体进行细碎、筛分和磁分选,得到所需的粉末。
热处理:将得到的钕铁硼粉末进行精细磨碎,并加入适量的添加剂。
然后,将其放入高真空下,进行低温热处理,消除内部应力,提高烧结体的致密性和磁性能。
烧结:将经过热处理的钕铁硼粉末填充到模具中,然后将其放入烧结炉中进行烧结。
在烧结过程中,通过控制温度和时间,使粉末颗粒互相结合,形成致密的烧结体。
烧结过程中,还需要进行压力变化处理,以进一步提高烧结体的致密度。
表面处理:烧结钕铁硼的表面常常需要进行镀层处理,以提高
其耐腐蚀性和机械强度。
常见的表面处理方法有镀镍、镀锌、镀锡等。
此外,还可根据实际需要对材料进行研磨、切割等工艺处理。
综上所述,烧结钕铁硼生产工艺包括原料准备、烧结、热处理和表面处理几个关键步骤。
通过这些工艺步骤,可以制备出具有优异物理性能的烧结钕铁硼材料。
随着技术的不断改进和创新,烧结钕铁硼的生产工艺也将不断提高,以满足不同领域对高性能永磁材料的需求。
烧结钕铁硼的生产工艺流程
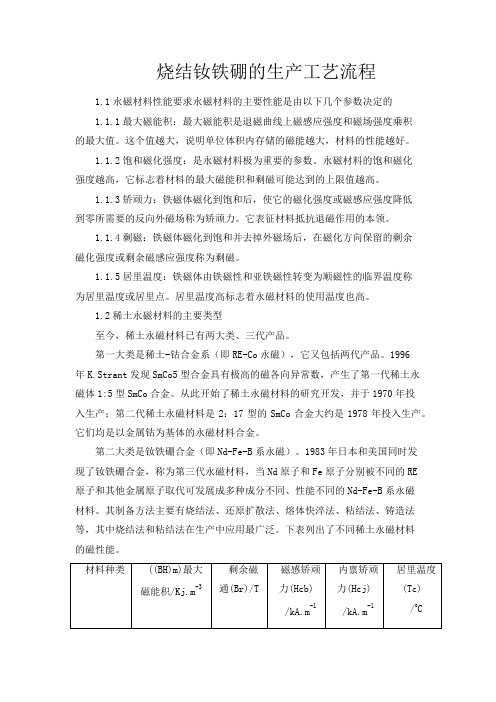
烧结钕铁硼的生产工艺流程1.1永磁材料性能要求永磁材料的主要性能是由以下几个参数决定的1.1.1最大磁能积:最大磁能积是退磁曲线上磁感应强度和磁场强度乘积的最大值。
这个值越大,说明单位体积内存储的磁能越大,材料的性能越好。
1.1.2饱和磁化强度:是永磁材料极为重要的参数。
永磁材料的饱和磁化强度越高,它标志着材料的最大磁能积和剩磁可能达到的上限值越高。
1.1.3矫顽力:铁磁体磁化到饱和后,使它的磁化强度或磁感应强度降低到零所需要的反向外磁场称为矫顽力。
它表征材料抵抗退磁作用的本领。
1.1.4剩磁:铁磁体磁化到饱和并去掉外磁场后,在磁化方向保留的剩余磁化强度或剩余磁感应强度称为剩磁。
1.1.5居里温度:铁磁体由铁磁性和亚铁磁性转变为顺磁性的临界温度称为居里温度或居里点。
居里温度高标志着永磁材料的使用温度也高。
1.2稀土永磁材料的主要类型至今,稀土永磁材料已有两大类、三代产品。
第一大类是稀土-钴合金系(即RE-Co永磁),它又包括两代产品。
1996年K.Strant发现SmCo5型合金具有极高的磁各向异常数,产生了第一代稀土永磁体1:5型SmCo合金。
从此开始了稀土永磁材料的研究开发,并于1970年投入生产;第二代稀土永磁材料是2:17型的SmCo合金大约是1978年投入生产。
它们均是以金属钴为基体的永磁材料合金。
第二大类是钕铁硼合金(即Nd-Fe-B系永磁)。
1983年日本和美国同时发现了钕铁硼合金,称为第三代永磁材料,当Nd原子和Fe原子分别被不同的RE原子和其他金属原子取代可发展成多种成分不同、性能不同的Nd-Fe-B系永磁材料。
其制备方法主要有烧结法、还原扩散法、熔体快淬法、粘结法、铸造法等,其中烧结法和粘结法在生产中应用最广泛。
下表列出了不同稀土永磁材料的磁性能。
法。
所以下面主要介绍烧结钕铁硼永磁材料的生产流程。
2烧结钕铁硼的生产流程总流程如下:2.1熔炼工段熔炼工段主要负责将按比例称量好的原材料进行熔炼,分为配料和熔炼两个部分。
烧结钕铁硼的生产工艺流程
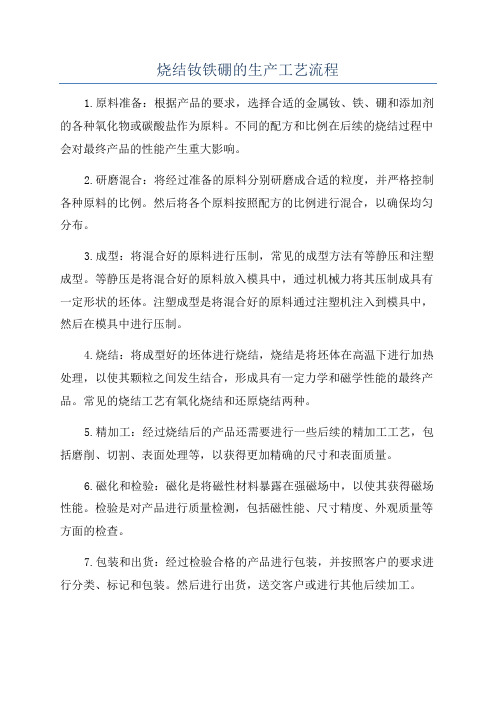
烧结钕铁硼的生产工艺流程
1.原料准备:根据产品的要求,选择合适的金属钕、铁、硼和添加剂的各种氧化物或碳酸盐作为原料。
不同的配方和比例在后续的烧结过程中会对最终产品的性能产生重大影响。
2.研磨混合:将经过准备的原料分别研磨成合适的粒度,并严格控制各种原料的比例。
然后将各个原料按照配方的比例进行混合,以确保均匀分布。
3.成型:将混合好的原料进行压制,常见的成型方法有等静压和注塑成型。
等静压是将混合好的原料放入模具中,通过机械力将其压制成具有一定形状的坯体。
注塑成型是将混合好的原料通过注塑机注入到模具中,然后在模具中进行压制。
4.烧结:将成型好的坯体进行烧结,烧结是将坯体在高温下进行加热处理,以使其颗粒之间发生结合,形成具有一定力学和磁学性能的最终产品。
常见的烧结工艺有氧化烧结和还原烧结两种。
5.精加工:经过烧结后的产品还需要进行一些后续的精加工工艺,包括磨削、切割、表面处理等,以获得更加精确的尺寸和表面质量。
6.磁化和检验:磁化是将磁性材料暴露在强磁场中,以使其获得磁场性能。
检验是对产品进行质量检测,包括磁性能、尺寸精度、外观质量等方面的检查。
7.包装和出货:经过检验合格的产品进行包装,并按照客户的要求进行分类、标记和包装。
然后进行出货,送交客户或进行其他后续加工。
以上是烧结钕铁硼的生产工艺流程的主要步骤。
整个流程需要严格控
制各个环节的工艺参数和质量要求,以确保最终产品的性能和质量。
同时,不同厂家和产品会有不同的工艺细节和特殊要求,需要根据实际情况进行
具体操作和调整。
- 1、下载文档前请自行甄别文档内容的完整性,平台不提供额外的编辑、内容补充、找答案等附加服务。
- 2、"仅部分预览"的文档,不可在线预览部分如存在完整性等问题,可反馈申请退款(可完整预览的文档不适用该条件!)。
- 3、如文档侵犯您的权益,请联系客服反馈,我们会尽快为您处理(人工客服工作时间:9:00-18:30)。
烧结钕铁硼的生产工艺流程1.1永磁材料性能要求永磁材料的主要性能是由以下几个参数决定的1.1.1最大磁能积:最大磁能积是退磁曲线上磁感应强度和磁场强度乘积的最大值。
这个值越大,说明单位体积内存储的磁能越大,材料的性能越好。
1.1.2饱和磁化强度:是永磁材料极为重要的参数。
永磁材料的饱和磁化强度越高,它标志着材料的最大磁能积和剩磁可能达到的上限值越高。
1.1.3矫顽力:铁磁体磁化到饱和后,使它的磁化强度或磁感应强度降低到零所需要的反向外磁场称为矫顽力。
它表征材料抵抗退磁作用的本领。
1.1.4剩磁:铁磁体磁化到饱和并去掉外磁场后,在磁化方向保留的剩余磁化强度或剩余磁感应强度称为剩磁。
1.1.5居里温度:铁磁体由铁磁性和亚铁磁性转变为顺磁性的临界温度称为居里温度或居里点。
居里温度高标志着永磁材料的使用温度也高。
1.2稀土永磁材料的主要类型至今,稀土永磁材料已有两大类、三代产品。
第一大类是稀土-钴合金系(即RE-Co永磁),它又包括两代产品。
1996年K.Strant发现SmCo5型合金具有极高的磁各向异常数,产生了第一代稀土永磁体1:5型SmCo合金。
从此开始了稀土永磁材料的研究开发,并于1970年投入生产;第二代稀土永磁材料是2:17型的SmCo合金大约是1978年投入生产。
它们均是以金属钴为基体的永磁材料合金。
第二大类是钕铁硼合金(即Nd-Fe-B系永磁)。
1983年日本和美国同时发现了钕铁硼合金,称为第三代永磁材料,当Nd原子和Fe原子分别被不同的RE原子和其他金属原子取代可发展成多种成分不同、性能不同的Nd-Fe-B系永磁材料。
其制备方法主要有烧结法、还原扩散法、熔体快淬法、粘结法、铸造法等,其中烧结法和粘结法在生产中应用最广泛。
下表列出了不同稀土永磁材料的磁性能。
法。
所以下面主要介绍烧结钕铁硼永磁材料的生产流程。
2烧结钕铁硼的生产流程总流程如下:2.1熔炼工段熔炼工段主要负责将按比例称量好的原材料进行熔炼,分为配料和熔炼两个部分。
2.1.1配料1、常用的金属有如下几种:金属钕,镨钕,特硼,精硼,铜,铝,镓,铽,钴,铁(太原铁、武钢铁、上海铁),镝铁,铌铁。
2、所用仪器、工具、辅助材料等:不同规格的电子秤、钢筋切断机、除锈抛光机、橡胶手套、口罩。
3、工作流程:根据当天的生产要求,统计各种原材料的用量,经核对后去原材料库领料;回来后根据单配料。
配料时以及配料完成后要完成相关的记录。
4、注意事项:(1)因称量金属时在空气中有金属粉末,所以在操作过程中需要戴口罩。
而且为防止金属伤手需要佩戴专用手套(2)由于原材料库中的铁棒较长并且容易生锈,所以在配料时需要切断并抛光,以便于称量并减少杂质。
(3)在操作钢筋切断机时需要特别注意安全,小心伤到手指。
(4)正确熟练掌握电子称的用法,将公差严格控制在要求范围内。
复称时更需严格把关,保证后续的有效正常生产。
作业过程的正确与否直接影响到产品的优劣高低。
2.1.2熔炼熔炼主要负责将配好的料进行铸片。
1、铸片熔炼(1)所用仪器、工具、辅助材料等:FMI-I-600R真空熔炼铸片炉、行车、原料车、吊具、铁锤、铁夹、吸尘器、辅助照明工具、炉渣桶、秒表、热电偶、氮气、氩气、手套、防尘口罩、海绵。
(2)流程图如下:流程:准备→装料→抽真空→熔炼→铸片→冷却→出料(3)操作步骤:①抽真空:自动→同时按下“确认”“准备”→泵准备→等待检漏完成②烘炉:加热运行→调至200kw左右(20min)③熔炼:调至0kw→自动→氩气导入(0.04~0.06Mpa)→手动→盘内控制→关机械泵1 2→调大功率(480kw)→计时并记录观察→表面完全融化→重新计时(8~12min)→测温(目标温度1450°±10℃)④保温:达到1450°±10℃后→保温5min(功率70~100kw)→测温1420°±10℃→浇铸⑤浇铸:辅助机构→自动→准备→手动倾斜到合金液快要流出→开始浇铸(注意观察流速,通过控制功率与角度控制流速)⑥浇铸完成:调0kw→停止加热→盘内控制→氩气导入(73kpa自动停止)→开风机1 2→关闭急冷辊→回坩埚⑦炉前:料叉下降到极限位⑧出炉开盖:冷却2h,铸片温度<35℃→盘内控制→关风机1 2→开液压→开机械泵1 2→开主阀(20kpa以下)→关主阀→关机械泵1 2 (4)注意事项①装料时,一般坩埚口周围温度较高,操作时应穿大头鞋、防护手套、垫好隔热垫,以免烫伤。
②吊装过程中必须在吊装区内作业;吊装前应仔细检查钢丝绳、吊钩、吊架,确保正常;吊装时,应确保安全隔离区内无人,设备平台吊装车行进路线上无人、以防人员伤害。
③浇注时,上操作员应留在浇注控制位,观察浇注口液体流动情况,并时刻留意下操作员的信息反馈;下观察员应持续观察中间包侧部溢流口及铜辊轮与中间包结合部位情况,当发现溢流口合金液溢出或中间包底板漏液等异常现象时应及时通知上操作员,此时应暂停浇注,待异常消除后继续浇注。
④更换中间包作业需佩戴口罩,减小粉尘对人体的危害。
⑤卸料及装料时操作人员应佩戴手套、口罩、不能裸手作业。
防止人体对铸片的污染;防止铸片划伤人体。
2.2制粉工段制粉工段负责将熔炼后的产品制成细粉,主要过程有氢碎(中碎)、粗粉搅拌、气流磨、细粉搅拌。
产品生产流程:配料→铸片→氢碎→粗粉搅拌→气流磨→细粉搅拌。
流程图如下:2.2.1氢碎1、氢碎:利用稀土金属间的吸氢特性,将钕铁硼合金置于氢气环境下,氢气沿富钕相薄层进入合金,使之膨胀爆裂而破碎,沿富钕相层处开裂,从而使薄片变为粗粉。
2、粗粉搅拌粗粉搅拌是通过搅拌罐的旋转使氢碎(中碎)后的粗粉混合均匀。
工艺流程:(1)搅拌罐定压:打开搅拌罐截止阀,打开搅拌罐排气罐,观察压力表,直至符合工艺卡要求。
间断打开关闭排气罐,观察压力表,达到指定压力后关闭排气阀,压力不足时补气,达到压力后关闭截止阀。
(2)加剂:按工艺卡要求用量筒量取加剂,然后倒入加剂装置,连接喷嘴管与搅拌罐充气阀,打开充气阀,打开截止阀,设置搅拌时间,启动搅拌机,使搅拌罐前后摆动,打开喷剂装置进行喷剂。
(3)搅拌:加剂后,关闭截止阀,关闭充气阀,关闭加剂设备,取开加剂连接设备,再开启搅拌罐旋转,搅拌结束后自动停止。
2.2.2气流磨1、气流磨原理:用高压气流将搅拌后的粗粉吹起,通过相互之间的碰撞使粒度变小,成为细粉。
2、所用仪器、工具、辅助材料等:400AFM-R型气流磨、电子称、粒度仪、钢瓶、小推车、行车、胶圈、卡箍、橡胶榔头、防护面罩。
3、工艺流程(1)准备工作:安排磨粉作业,检查设备,设定参数,按生产计划排料(2)开机:在开机前打到自动模式状态,如已符合开机状态,按“S11”键返回压缩机图,按“S3”键气流磨自动启动,记录开机时间,开启空压机。
(3)接细粉钢瓶:将已排氧的细粉钢瓶与筛粉机出料口连接。
(4)加料:用吊车将钢瓶吊至加料口进行加料,加料完毕要盖住加料斗口。
(5)排氧:开启振动筛、打开出料阀,进行排氧。
(6)磨料:分离轮转速达到要求后按下加料按钮,气流磨加料口粗粉自动进入磨室,进行磨料;磨料落入首瓶钢瓶中,记录磨料开始时间及相关参数。
(7)加氧钝化:当自动加料至设定值时,调整加氧流量进行加氧。
(8)第一瓶接料与钢瓶更换:当第一瓶钢瓶内粉料达到工艺卡要求时进行更换钢瓶,并为首瓶粒度取样做好准备。
(9)首瓶粒度取样:取塑料袋预先充满氮气,用手包扎口并包紧取样气阀,氮气管开启并一同插入塑料袋内;瞬间打开取样球阀后关闭,粉料样品充入塑料袋内,取样完毕。
经过钝化准备测量,用于粒度检验(10)更换钢瓶与继续接料。
(11)粒度样品取样与报验:依据气流磨工艺卡要求对钢瓶顺序号进行取样,粒度样品顺序号为取样时上一钢瓶顺序号。
(12)首检与处置:操作人员对第一瓶粉料进行平均粒度自检,合格则继续,若连续三瓶不合格则停止加料。
(13)称重与转移:将装料钢瓶称重并移至细粉库,将氮气管接入钢瓶。
(14)铸片尾料处理:将尾料放置在细粉尾料区。
(15)关机:当上料斗无料时,应将其转换为空运转,然后按“S4”设备自动关机,关闭空气压缩机电源。
(16)清场:当发生由铸锭转铸片作业时,应进行底料清理。
4、细粉搅拌细粉搅拌是将经气流磨后不同牌号的细粉按照配比进行混合。
操作过程与粗粉搅拌相同。
5、注意事项(1)运行过程中,若发现管道漏气,及时用胶带纸粘住。
若漏气严重,则停止加料,将磨室内粉料充氮气保护。
(2)运行过程中,若发生研磨室或过滤器内超细粉着火,应关机充氮气保护,如情况严重,则按“急停”。
(3)接料时发生粉料泄漏,应尽快用黄沙或石棉布将粉料覆盖住,待冷却后清理干净。
(4)钢瓶吊装过程中应特别注意人员安全,吊架下严禁人员进入(5)钢瓶翻转时,应特别注意,防止夹手。
出料、取样作业过程必须佩带防护面罩,防止粉料喷出,伤害人体。
2.3成型工段成型工段负责将粉末压制成型,包括成型和等静压两部分。
2.3.1成型1、成型原理:根据要求选择相应的模具,将细粉压制成所需的形状。
2、所用仪器、工具、辅助材料等:自动磁场成型压机、圆柱成型压机、方块成型压机、真空包装机、自动称粉机、流转车、电子秤、卡尺、小铜铲、毛刷、磁粉洁具、磁柱、压柄、保护垫、真空包装袋、内包装薄膜、流转筐、流转盒。
3、流程图:4、具体操作规程(1)成型模具安装与拆卸:准备→装模→压机准备→安装下压头→安装模框→安装上压头→垂直度检查→脱模(2)成型压机磁场测量与调整:校准→磁场测量与调整→清场(3)称粉:称粉的准备→取料→上料→下料→称粉→更换料筒→清理和清场(4)压机操作圆柱类:上缸下→停顿→取向→压制→保压→退磁→上缸上→下缸上。
方块类:上缸下→压住模具→侧缸进→取向→压制→保压→退磁→侧缸退→上缸上。
(5)包装:准备→检查与记录→包内膜→装袋→真空→装箱→标识与转序(6)清理:压型机清理→自动称粉机清理→包装箱清理→真空包装机清理 →工作区地面清理(7)成型压机清场:拆卸空料筒→自动称粉机清扫→压机清扫→包装箱清扫→工作区地面清扫5、注意事项(1)在充磁过程中,特斯拉计探头应放在磁极中间,不与任何物体接触,手动充磁时间不宜过长,以免烧坏设备。
(2)在称粉中主操作应随时观察测氧仪,当发现氧含量大于0.04%时,应暂停作业,调整氮气含量,确保氧含量合格后方可继续作业。
(3)拆卸料筒时一定要先将进料口处的手动蝶阀关闭,更换前要将料筒内的氮气放掉,以免下料时磁粉喷到人体。
2.3.2等静压1、等静压原理:等静压工作原理为帕斯卡定律:“在密闭容器内的介质(液体或气体)压强,可以向各个方向均等地传递。
”具体地说,待压制产品装进设备后,产品受到各向均等的超高压介质作用,使产品密度增加,压块的收缩量取决于材料的可压缩性及压制时压力的大小。