烧结工艺流程
烧结的工艺流程
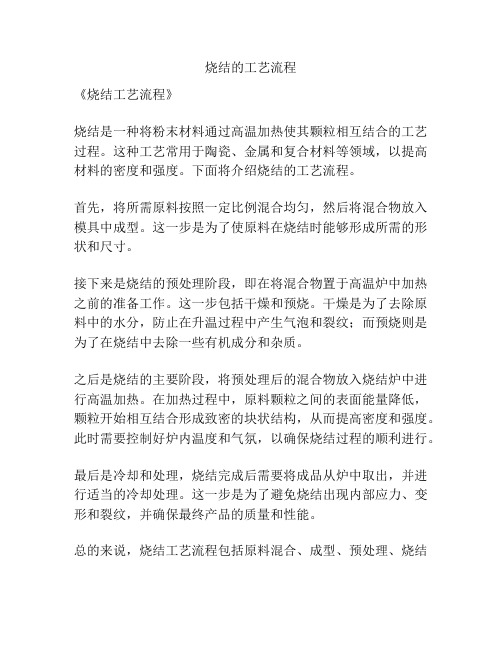
烧结的工艺流程
《烧结工艺流程》
烧结是一种将粉末材料通过高温加热使其颗粒相互结合的工艺过程。
这种工艺常用于陶瓷、金属和复合材料等领域,以提高材料的密度和强度。
下面将介绍烧结的工艺流程。
首先,将所需原料按照一定比例混合均匀,然后将混合物放入模具中成型。
这一步是为了使原料在烧结时能够形成所需的形状和尺寸。
接下来是烧结的预处理阶段,即在将混合物置于高温炉中加热之前的准备工作。
这一步包括干燥和预烧。
干燥是为了去除原料中的水分,防止在升温过程中产生气泡和裂纹;而预烧则是为了在烧结中去除一些有机成分和杂质。
之后是烧结的主要阶段,将预处理后的混合物放入烧结炉中进行高温加热。
在加热过程中,原料颗粒之间的表面能量降低,颗粒开始相互结合形成致密的块状结构,从而提高密度和强度。
此时需要控制好炉内温度和气氛,以确保烧结过程的顺利进行。
最后是冷却和处理,烧结完成后需要将成品从炉中取出,并进行适当的冷却处理。
这一步是为了避免烧结出现内部应力、变形和裂纹,并确保最终产品的质量和性能。
总的来说,烧结工艺流程包括原料混合、成型、预处理、烧结
和冷却处理这几个主要阶段。
通过精确地控制每个环节,可以获得致密、坚固和具有优良性能的烧结制品。
烧结工艺流程

烧结工艺流程烧结工艺是指对金属、陶瓷等粉末材料进行高温加热处理,使其颗粒相互结合形成坚硬的固体材料的工艺。
下面将介绍一种常见的金属烧结工艺流程。
首先,要准备好所需的原料。
通常情况下,金属烧结工艺所需要的原料是金属粉末及部分添加剂。
这些金属粉末可以通过粉末冶金技术或其他方法获得。
而添加剂的选择则根据所需的材料特性来确定。
接下来,将所需的原料进行混合。
原料的混合是为了保证在烧结过程中各个组分均匀分布,从而获得均匀的材料性能。
一般情况下,可以通过机械混合的方式来实现,如球磨机、搅拌器等。
然后,对混合后的原料进行压制。
压制是将原料加入到模具中,并施加适当的压力使其形成所需形状的过程。
压制的目的是使原料形成一定的强度,以保证在烧结过程中不发生变形或破碎。
一般情况下,可采用压力机或挤压机等设备进行压制。
接着,对已压制形状的原料进行烧结。
烧结是将压制后的原料在高温条件下进行加热,使其颗粒间相互结合形成坚硬的固体材料的过程。
烧结时要控制好加热速度和温度,以防止过高温度导致材料熔化或变形。
同时,还需对烧结气氛进行控制,以避免氧化或其它不良反应的产生。
最后,对烧结后的材料进行加工和处理。
烧结后的材料可能存在一定的缺陷,如孔洞、裂纹等,这些缺陷会影响材料的性能。
因此,需要对烧结材料进行磨削、抛光等加工工艺,以提高材料的表面光洁度和尺寸精度。
此外,对于某些特殊要求的材料,还可以进行热处理、表面处理等特殊处理,以获得所需的性能。
以上就是金属烧结工艺的基本流程。
当然,实际的烧结工艺流程还需要根据具体的材料和产品要求进行调整和优化。
烧结工艺是一门复杂的工艺学科,它对材料的制备和性能等方面都提出了很高的要求。
随着技术的不断进步,烧结工艺的应用范围也在不断扩大,为各行各业提供了更多的材料选择,推动了相关产业的发展。
玻璃烧结工艺流程

玻璃烧结工艺流程
玻璃烧结工艺流程
玻璃烧结是一种常见的玻璃加工工艺,主要用于制作玻璃制品。
下面是一种常见的玻璃烧结工艺流程,共分为五个步骤。
第一步:原料准备
首先,需要准备好所需的玻璃原料,通常包括二氧化硅、氧化铝、氧化锌等。
这些玻璃原料需要经过筛网处理,将颗粒大小控制在一定范围内。
第二步:烧结模具制备
接下来,需要制备烧结模具。
烧结模具的形状和尺寸可以根据具体的需求进行设计和定制。
一般情况下,采用模具制造材料如陶瓷材料等。
第三步:原料混合
将准备好的玻璃原料进行混合。
混合的原料需要通过特定的工艺步骤,确保混合均匀,避免出现颗粒过大或过小的情况。
第四步:烧结过程
将混合好的玻璃原料填充到烧结模具中,然后放入高温炉进行烧结处理。
烧结过程中,需要控制好温度和时间,以确保玻璃原料充分烧结并形成所需的形状。
第五步:冷却和修整
烧结完成后,需要将烧结好的玻璃制品进行冷却处理。
在冷却
过程中,需要注意避免快速冷却,以免造成玻璃制品的开裂。
冷却完成后,可以进行修整和加工,根据需要进行切割、打磨等工艺。
以上就是一个常见的玻璃烧结工艺流程。
当然,不同的玻璃制品可能存在差异,具体的工艺流程还需根据实际情况进行调整和改进。
在进行玻璃烧结工艺时,需要注意工艺参数的控制,以确保最终的玻璃制品具备所需的性能和质量。
烧结厂生产工艺流程
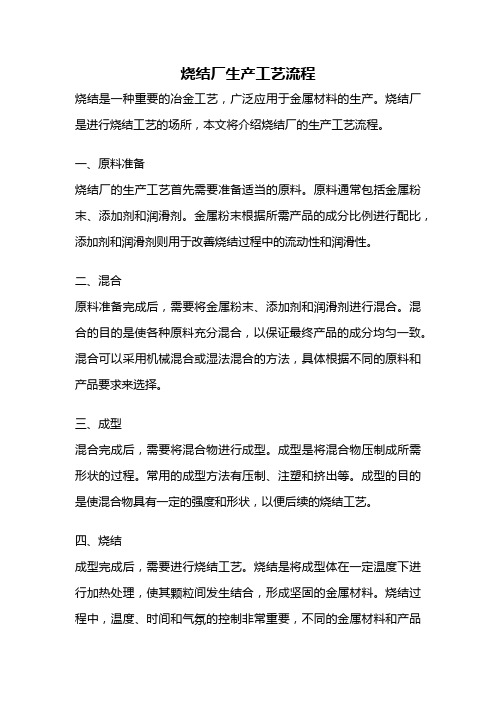
烧结厂生产工艺流程烧结是一种重要的冶金工艺,广泛应用于金属材料的生产。
烧结厂是进行烧结工艺的场所,本文将介绍烧结厂的生产工艺流程。
一、原料准备烧结厂的生产工艺首先需要准备适当的原料。
原料通常包括金属粉末、添加剂和润滑剂。
金属粉末根据所需产品的成分比例进行配比,添加剂和润滑剂则用于改善烧结过程中的流动性和润滑性。
二、混合原料准备完成后,需要将金属粉末、添加剂和润滑剂进行混合。
混合的目的是使各种原料充分混合,以保证最终产品的成分均匀一致。
混合可以采用机械混合或湿法混合的方法,具体根据不同的原料和产品要求来选择。
三、成型混合完成后,需要将混合物进行成型。
成型是将混合物压制成所需形状的过程。
常用的成型方法有压制、注塑和挤出等。
成型的目的是使混合物具有一定的强度和形状,以便后续的烧结工艺。
四、烧结成型完成后,需要进行烧结工艺。
烧结是将成型体在一定温度下进行加热处理,使其颗粒间发生结合,形成坚固的金属材料。
烧结过程中,温度、时间和气氛的控制非常重要,不同的金属材料和产品要求有不同的烧结条件。
五、冷却烧结完成后,需要对烧结体进行冷却。
冷却是将高温的烧结体降温至室温的过程。
冷却的速度对最终产品的性能有影响,过快的冷却可能导致产生内部应力,影响产品的质量。
六、加工冷却完成后,烧结体需要进行加工。
加工包括切割、修磨、钻孔等操作,以得到最终产品的形状和尺寸。
加工的方式可以根据产品的要求选择,常见的有机械加工和电火花加工等。
七、检测加工完成后,需要对产品进行质量检测。
常见的检测项目包括尺寸精度、密度、硬度、强度等。
检测的目的是确保产品符合设计要求和客户需求,以提供优质的产品。
八、包装检测合格的产品需要进行包装。
包装的目的是保护产品不受外界环境的影响,以确保产品的完整性和安全性。
常见的包装方式有纸盒、木箱、塑料袋等,具体根据产品的性质和尺寸来选择。
九、质量控制在整个生产工艺流程中,质量控制是非常重要的环节。
通过严格的质量控制,可以确保产品的质量稳定和一致性。
烧结工艺流程
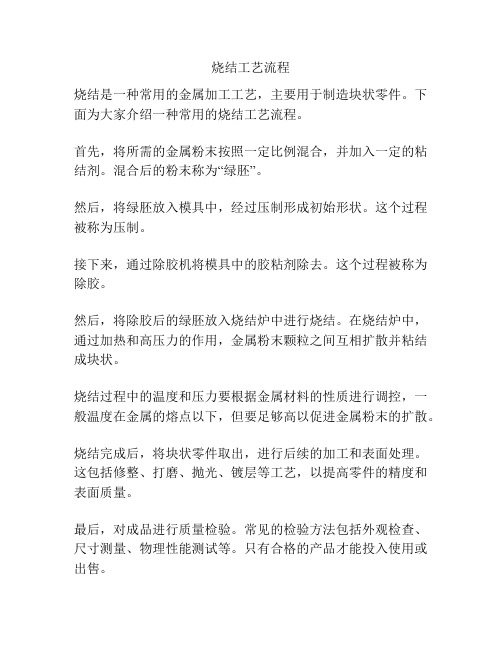
烧结工艺流程
烧结是一种常用的金属加工工艺,主要用于制造块状零件。
下面为大家介绍一种常用的烧结工艺流程。
首先,将所需的金属粉末按照一定比例混合,并加入一定的粘结剂。
混合后的粉末称为“绿胚”。
然后,将绿胚放入模具中,经过压制形成初始形状。
这个过程被称为压制。
接下来,通过除胶机将模具中的胶粘剂除去。
这个过程被称为除胶。
然后,将除胶后的绿胚放入烧结炉中进行烧结。
在烧结炉中,通过加热和高压力的作用,金属粉末颗粒之间互相扩散并粘结成块状。
烧结过程中的温度和压力要根据金属材料的性质进行调控,一般温度在金属的熔点以下,但要足够高以促进金属粉末的扩散。
烧结完成后,将块状零件取出,进行后续的加工和表面处理。
这包括修整、打磨、抛光、镀层等工艺,以提高零件的精度和表面质量。
最后,对成品进行质量检验。
常见的检验方法包括外观检查、尺寸测量、物理性能测试等。
只有合格的产品才能投入使用或出售。
总的来说,烧结工艺流程包括混合、压制、除胶、烧结、后续加工和质量检验。
烧结厂生产工艺流程

烧结厂生产工艺流程烧结是一种常用于金属、陶瓷、石材等材料加工的工艺。
它通过将细粉末状的原料在一定的温度下进行高压热处理,使其颗粒间发生结合,形成一片致密的块体。
以下是一个常用的烧结厂生产工艺流程,可以分为原料处理、烧结制备、烧结成型和后处理等几个步骤。
首先是原料处理。
烧结厂的原料通常是金属、陶瓷或石材等粉末状物料。
这些原料在进入烧结厂之前往往需要经过一系列的处理工序,如研磨、筛选、混合等。
研磨可以使原料颗粒变得更加细小均匀,提高烧结后的品质。
筛选则是通过筛网将原料中的杂质去除。
混合是将不同配方的原料按一定比例混合,以获得需要的材料性能。
第二步是烧结制备。
制备烧结料包括成型料和包裹液料。
成型料是指将粉末状的原料放入成型机中进行压制成型,以便在烧结过程中更好地结合。
常见的成型机包括压力机和挤压机等。
包裹液料则是将成型料表面均匀涂覆上一层液态的材料,以提高成型体的密封性和表面光洁度。
常见的包裹液料有蜡涂料、水浆料等。
第三步是烧结成型。
烧结成型是将成型好的烧结料放入烧结炉中进行热处理。
烧结炉一般是由炉体、加热系统、气体供应系统以及控制系统等组成。
烧结炉可以根据不同的工艺需求进行调整,如控制炉温、气氛、烧结时间等参数。
烧结过程中,原料粉末在高温下发生熔融和结晶反应,形成致密坚固的块体。
最后是后处理。
烧结后的产品一般需要进行后处理,以提高产品质量和外观。
后处理的过程包括修整、研磨、抛光、清洗等。
修整是指对烧结块进行切割或边角修整,使其达到设计要求的尺寸和形状。
研磨和抛光则是对产品的表面进行打磨和抛光,以提高表面光洁度。
清洗是将产品表面的油污和残留物去除,为后续的质检和包装作准备。
总结起来,烧结厂的生产工艺流程主要包括原料处理、烧结制备、烧结成型和后处理等几个步骤。
这些步骤通过一系列的加工技术,将原料转化为具有较高密度和良好性能的成品。
烧结工艺可以广泛应用于金属、陶瓷和石材等材料的加工和制造领域,具有重要的经济和社会意义。
钢厂烧结工艺流程
钢厂烧结工艺流程一、烧结工艺概述烧结是钢铁冶炼过程中的一项重要工艺,通过将细粉状的铁矿石和焦炭等物料加热,使其部分熔化并粘结成为直径一定大小的烧结矿,为后续的铁水冶炼提供原料。
钢厂烧结工艺流程主要包括原料配比、矿石破碎、混合、烧结、冷却、筛分等环节。
二、原料配比钢厂烧结工艺的首要任务是确定合理的原料配比比例。
根据矿石的化学成分和质量要求,钢厂技术人员会制定烧结矿的配比方案。
一般来说,烧结矿的主要成分包括铁矿石、焦炭、石灰石和其他添加剂。
这些原料按一定比例混合后,形成矿料堆积。
三、矿石破碎矿石破碎是将原料中的铁矿石进行粉碎的过程。
首先,将原料送入破碎机中,经过粉碎机的破碎作用,将矿石破碎成一定粒度的颗粒。
矿石破碎的目的是为了增大表面积,提高矿石的反应性,有利于后续的烧结过程。
四、混合矿石破碎后的铁矿石与焦炭、石灰石等原料按照一定比例混合。
混合的目的是确保各种原料在烧结过程中能够充分反应,形成均匀的矿料堆积。
混合通常采用混料机进行,通过机械搅拌使各种原料充分混合。
五、烧结烧结是将混合后的矿料进行加热处理的过程。
在烧结机中,矿料堆积被加热至一定温度,使其部分熔化并形成烧结矿。
烧结过程中,焦炭在高温下发生氧化反应,产生一定量的热量,使矿料熔化并粘结在一起。
同时,石灰石中的CaO也发生反应,形成熔融的CaO-SiO2-Al2O3-Fe2O3等化合物,进一步增强矿料的粘结性。
六、冷却烧结完成后,烧结矿需要进行冷却处理。
冷却的目的是使烧结矿迅速降温,并保持其结构和硬度。
通常采用冷却机进行冷却,通过强风将烧结矿表面的热量带走,使其迅速冷却。
七、筛分经过冷却后的烧结矿需要进行筛分,将不符合规格要求的颗粒进行分离。
筛分的目的是获得符合要求的烧结矿颗粒,以供后续的冶炼使用。
通常采用筛分机进行筛分,根据烧结矿的粒度要求,将不同大小的颗粒进行分离。
八、成品矿料经过上述工艺流程,最终得到的是符合钢厂要求的成品矿料。
这些成品矿料具有一定的强度和耐高温性能,适合用于钢铁冶炼的高炉和转炉炼钢过程。
烧结钕铁硼的生产工艺流程
烧结钕铁硼的生产工艺流程1.原料准备:根据配方要求,将永磁材料的原料(钕、铁、硼等)进行称量和筛分,确保各种原料的粒度和成分符合要求。
2.粉末混合:将称量好的原料放入球磨机中进行混合。
球磨机通过旋转的罐体和球磨体,将原料进行均匀的混合和研磨,以确保粉末颗粒的均一性。
3.筛分和干燥:将混合好的粉末经过筛网进行分级筛分,确保粉末的粒度符合要求。
然后通过干燥设备,将粉末中的水分蒸发掉。
4.粉末成型:将干燥好的粉末放入模具中进行成型。
常见的成型方式包括压制成型、注射成型和挤压成型等。
通过施加高压,使得粉末颗粒之间产生相互作用力,从而形成一定形状的绿体。
5.绿体处理:将成型好的绿体进行除油、除蜡等处理。
除油是指将绿体中的有机物去除,除蜡是将绿体中的蜡去除。
这些处理过程主要是为了提高烧结后的致密度和机械强度。
6.预烧:将绿体放入预烧炉中进行预烧处理。
预烧是将绿体中的有机物在高温下热分解,使得绿体成为一种有一定机械强度的金属氧化物基体。
7.磁场取向:将预烧好的绿体放入磁场取向设备中。
磁场取向是通过在绿体中施加强磁场,使得绿体中的颗粒在磁力的作用下排列起来,达到提高磁化强度和磁晶各向异性的目的。
8.烧结:将经过磁场取向的绿体放入烧结炉中进行真空烧结。
真空烧结是指在高温下,使得绿体中的金属氧化物颗粒在一定的时间内相互扩散,并形成金属间的化合物和结晶。
烧结时间、温度和真空度是影响烧结效果的重要因素。
9.表面处理:经过烧结的NdFeB磁体表面常常存在氧化皮和污染物,需要进行表面处理。
常见的表面处理方法包括电镀、喷涂等,以提高磁体的耐腐蚀性和美观度。
10.检验和包装:将成品进行质量检验,包括外观、磁性能等指标的测试。
合格的产品进行包装,通常采用真空包装,以保护磁体免于氧化和磁场干扰。
以上是烧结钕铁硼的生产工艺流程的详细描述,包括原料准备、粉末混合、筛分和干燥、粉末成型、绿体处理、预烧、磁场取向、烧结、表面处理、检验和包装等步骤。
玻璃烧结工艺流程
玻璃烧结工艺流程玻璃烧结是一种常见的玻璃加工工艺,通过高温加热玻璃原料,使其在一定条件下熔融成型,然后冷却固化而成。
玻璃烧结工艺广泛应用于玻璃制品的生产,包括建筑玻璃、家居用品、工艺品等领域。
下面将介绍玻璃烧结工艺的具体流程。
首先,原料准备。
玻璃烧结的原料主要包括二氧化硅、碳酸钠、石灰石等。
在进行烧结之前,需要对这些原料进行精确的配比,确保每种原料的比例准确无误。
这一步是整个工艺流程中非常关键的一环,原料配比的准确性直接影响到最终产品的质量。
其次,混合和熔融。
将经过配比的原料放入熔窑中,进行混合和熔融的过程。
在高温条件下,原料逐渐熔化并混合在一起,形成玻璃熔体。
这个阶段需要严格控制熔窑的温度和时间,确保玻璃熔体的均匀性和稳定性。
接下来是成型。
经过熔融的玻璃熔体被抽出熔窑,然后通过成型设备进行成型。
成型的方式多种多样,可以采用浇铸、压延、注塑等方法,根据不同产品的要求选择合适的成型方式。
在成型过程中,需要考虑产品的尺寸、形状、表面光洁度等因素。
然后是烧结和冷却。
成型后的玻璃制品被放入烧结窑中进行烧结和冷却。
烧结的目的是使玻璃制品的结构更加致密,提高强度和耐磨性。
在烧结过程中,需要控制烧结的温度和时间,确保产品的质量稳定。
最后是后处理和包装。
经过烧结和冷却的玻璃制品需要进行后处理,包括去除毛刺、打磨、清洗等工序,最终进行包装。
在包装过程中,需要注意保护产品的表面,避免在运输和使用过程中受到损坏。
总的来说,玻璃烧结工艺流程包括原料准备、混合和熔融、成型、烧结和冷却、后处理和包装等多个环节。
每个环节都需要严格控制和精心操作,以确保最终产品的质量和性能。
希望本文对玻璃烧结工艺流程有所帮助,谢谢阅读。
粉末烧结工艺流程
粉末烧结工艺流程下载温馨提示:该文档是我店铺精心编制而成,希望大家下载以后,能够帮助大家解决实际的问题。
文档下载后可定制随意修改,请根据实际需要进行相应的调整和使用,谢谢!并且,本店铺为大家提供各种各样类型的实用资料,如教育随笔、日记赏析、句子摘抄、古诗大全、经典美文、话题作文、工作总结、词语解析、文案摘录、其他资料等等,如想了解不同资料格式和写法,敬请关注!Download tips: This document is carefully compiled by theeditor. I hope that after you download them,they can help yousolve practical problems. The document can be customized andmodified after downloading,please adjust and use it according toactual needs, thank you!In addition, our shop provides you with various types ofpractical materials,such as educational essays, diaryappreciation,sentence excerpts,ancient poems,classic articles,topic composition,work summary,word parsing,copy excerpts,other materials and so on,want to know different data formats andwriting methods,please pay attention!粉末烧结工艺流程粉末烧结工艺是一种将粉末压制成形,然后在高温下进行烧结的制造工艺。
- 1、下载文档前请自行甄别文档内容的完整性,平台不提供额外的编辑、内容补充、找答案等附加服务。
- 2、"仅部分预览"的文档,不可在线预览部分如存在完整性等问题,可反馈申请退款(可完整预览的文档不适用该条件!)。
- 3、如文档侵犯您的权益,请联系客服反馈,我们会尽快为您处理(人工客服工作时间:9:00-18:30)。
-- 1 / 1-- ﻩ烧结工艺流程
烧结是钢铁生产工艺中的一个重要环节,它是将铁矿粉、粉(无烟煤)和石灰按一定配比混匀。经烧结而成的有足够强度和粒度的烧结矿可作为炼铁的熟料。利用烧结熟料炼铁对于提高高炉利用系数、降低焦比、提高高炉透气性保证高炉运行均有一定意义。 由于烧结技术具体的作用和应用太广泛了, 以下介绍一下烧结生产在钢铁工业粉矿造块的意义和作用 我国的铁矿石大部分都是贫矿,贫矿直接入炉炼铁是很不合算b,因此必须将贫矿进行破碎、选出高品位的精矿后,再将精矿粉造块成为人造富矿才能入高炉冶炼。所以,粉矿造块是充分合理利用贫矿的不可缺少的关控环节。 富矿的开采过程中要产生粉矿,为了满足高炉的粒度要兔在整较过程中也会产生粉矿,粉矿直接入炉会51起高炉不顺。恶化高炉技术经济指标,因此粉矿也必须经过造块才能入炉。 粉矿经过迭决后,可以进一步控制相改善合铁原料的性肠获得气孔串高、还原性好、强度合适、软熔温度较高、成份稳定的优质冶金原料,有助于炉况的稳定和技术经济指标的改善。-- 1 / 1-- 粒矿造块过程中,还可以除去部份有害杂质,如硫、氟、砷、锌等,有利于提高生铁的质量。因
为人造富矿比天然富矿更具有优越性,成为了现代商炉原料的主要来源。 粉矿迭块还可综合利用含铁、合被、台钙的粉状工业废料,如高炉炉尘、钢迢、轧钢皮、均热炉渣、硫酸渣、染料铁红、电厂烟尘灰笔适当配入可以成为廉价的高炉好原料,又可以减少环境污染,取得良好的经济效益和社会效益。 粉矿造铁是现代高炉冶炼并获得优质高产的基础,对于高炉冶炼有君十分重要的意义,是钢铁工业生产必不可少的重要工序,对钢铁生产的发展起着重要作用。 1.2 粉矿造块的方法 粉矿造块方法很多,主要是烧结矿和球团矿。此外,还有压制方团矿、辊压团矿、蒸养球团t碳酸化球团,其成球方式和固结方法与球团矿不同,还有小球烧结,国外称为HPs球团化挠结矿,界于球团和烧结之间;还有铁焦生产,是炼焦和粉矿造块相结合。 球团矿的焙烧方法主要乞竖队带式焙烷仇链蓖机—回转窃。目前地方小铁厂还有平地堆烷的。 烧结方法主要有吹风烧结法和抽风烧结法两大类。吹风烧结有平地堆挠、饶结识、挠结盘,抽风烧结有路式侥结、艰面步进式烧绍机、带式烧结机、环形挠结机电即日本矢作式)。 国内外苫遍采用的是常式抽风烧结机,在我国地方小铁广还有相当一部分用平地吹风堆烧和箱式抽风烧结。比外,还有回转窑浇结法、悬浮烧结法。 所谓“烧结”就是指粉状物料加热到熔点以下而粘结成固体的现象. 烧结过程简单来说,就是把品位满足要求,但粒度却不满足的精矿与其他辅助原料混合后在烧结机上点火燃烧,重新造块,以满足高炉的要求。点火器就是使混合料在烧结机上燃烧的关键设备,控制好点火器的温度、负压等,混合料才能成为合格的烧结成品矿。 烧结的主要体系是,配料,混料,看火等。看火的经验:看火主要控制的三点温度是;点火温度,终点温度,和总管废气温度。一般来说把终点温度控制在倒数第2号风箱的温度。 铁矿粉造块 铁矿粉造块目前主要有两种方法:烧结法和球团法。两种方法所获得的块矿分别为烧结矿和球团矿。 铁矿粉造块的目的: ◆综合利用资源,扩大炼铁用的原料种类。 ◆去除有害杂质,回收有益元素,保护环境。 ◆改善矿石的冶金性能,适应高炉冶炼对铁矿石的质量要求。 一、铁矿粉烧结生产 -- 1 / 1-- 1.烧结的概念
将各种粉状含铁原料,配入适量的燃料和熔剂,加入适量的水,经混合和造球后在烧结设备上使物料发生一系列物理化学变化,将矿粉颗粒黏结成块的过程。 2. 烧结生产的工艺流程 目前生产上广泛采用带式抽风烧结机生产烧结矿。烧结生产的工艺流程如图2—4所示。主要包括烧结料的准备,配料与混合,烧结和产品处理等工序。
图2-4 抽风烧结工艺流程 ◆烧结原料的准备 ①含铁原料 含铁量较高、粒度<5mm的矿粉,铁精矿,高炉炉尘,轧钢皮,钢渣等。 一般要求含铁原料品位高,成分稳定,杂质少。 ②熔剂 要求熔剂中有效CaO含量高,杂质少,成分稳定,含水3%左右,粒度小于3mm的占90%以上。 在烧结料中加入一定量的白云石,使烧结矿含有适当的MgO,对烧结过程有良好的作用,可以提高烧结矿的质量。 ③燃料 -- 1 / 1-- 主要为焦粉和无烟煤。
对燃料的要求是固定碳含量高,灰分低,挥发分低,含硫低,成分稳定,含水小于10%,粒度小于3mm的占95%以上。 对入厂烧结原料的一般要求见表2—2。 表2-2 入厂烧结原料一般要求
◆配料与混合 ①配料 配料目的:获得化学成分和物理性质稳定的烧结矿,满足高炉冶炼的要求。 常用的配料方法:容积配料法和质量配料法。 容积配料法是基于物料堆积密度不变,原料的质量与体积成比例这一条件进行的。准确性较差。 质量配料法是按原料的质量配料。比容积法准确,便于实现自动化。 ②混合 混合目的:使烧结料的成分均匀,水分合适,易于造球,从而获得粒度组成良好的烧结混合料,以保证烧结矿的质量和提高产量。 混合作业:加水润湿、混匀和造球。 根据原料性质不同,可采用一次混合或二次混合两种流程。 一次混合的目的:润湿与混匀,当加热返矿时还可使物料预热。 二次混合的目的:继续混匀,造球,以改善烧结料层透气性。 -- 1 / 1-- 用粒度10~Omm的富矿粉烧结时,因其粒度已经达到造球需要,采用一次混合,混合时
间约50s。 使用细磨精矿粉烧结时,因粒度过细,料层透气性差,为改善透气性,必须在混合过程中造球,所以采用二次混合,混合时间一般不少于2.5~3min。 我国烧结厂大多采用二次混合。 ◆烧结生产 烧结作业是烧结生产的中心环节,它包括布料、点火、烧结等主要工序。 ①布料 将铺底料、混合料铺在烧结机台车上的作业。 当采用铺底料工艺时,在布混合料之前,先铺一层粒度为10~25mm,厚度为20~25mm的小块烧结矿作为铺底料,其目的是保护炉箅,降低除尘负荷,延长风机转子寿命,减少或消除炉箅粘料。 铺完底料后,随之进行布料。布料时要求混合料的粒度和化学成分等沿台车纵横方向均匀分布,并且有一定的松散性,表面平整。 目前采用较多的是圆辊布料机布料。 ②点火 点火操作是对台车上的料层表面进行点燃,并使之燃烧。 点火要求有足够的点火温度,适宜的高温保持时间,沿台车宽度点火均匀。 点火温度取决于烧结生成物的熔化温度。常控制在1250±50℃。 点火时间通常40~60s。 点火真空度4~6kPa。 点火深度为10~20mm。 ③烧结 准确控制烧结的风量、真空度、料层厚度、机速和烧结终点。 烧结风量:平均每吨烧结矿需风量为3200m3,按烧结面积计算为(70~90)m3/(cm2.min)。 真空度:决定于风机能力、抽风系统阻力、料层透气性和漏风损失情况。 料层厚度:合适的料层厚度应将高产和优质结合起来考虑。国内一般采用料层厚度为250~500mm。 机速:合适的机速应保证烧结料在预定的烧结终点烧透烧好。实际生产中,机速一般控制在1.5~4m/min为宜。 -- 1 / 1-- 烧结终点的判断与控制:控制烧结终点,即控制烧结过程全部完成时台车所处的位置。
中小型烧结机终点一般控制在倒数第二个风箱处,大型烧结机控制在倒数第三个风箱处。 带式烧结机抽风烧结过程是自上而下进行的,沿其料层高度温度变化的情况一般可分为5层,各层中的反应变化情况如图2—5所示。点火开始以后,依次出现烧结矿层,燃烧层,预热层,干燥层和过湿层。然后后四层又相继消失,最终只剩烧结矿层。
图2-5烧结过程各层反应示意图 ①烧结矿层 经高温点火后,烧结料中燃料燃烧放出大量热量,使料层中矿物产生熔融,随着燃烧层下移和冷空气的通过,生成的熔融液相被冷却而再结晶(1000—1100℃)凝固成网孔结构的烧结矿。 这层的主要变化是熔融物的凝固,伴随着结晶和析出新矿物,还有吸入的冷空气被预热,同时烧结矿被冷却,和空气接触时低价氧化物可能被再氧化。 ②燃烧层 燃料在该层燃烧,温度高达1350~1600℃,使矿物软化熔融黏结成块。 该层除燃烧反应外,还发生固体物料的熔化、还原、氧化以及石灰石和硫化物的分解等反应。 ③预热层 由燃烧层下来的高温废气,把下部混合料很快预热到着火温度,一般为400~800℃。 此层内开始进行固相反应,结晶水及部分碳酸盐、硫酸盐分解,磁铁矿局部被氧化。 ④干燥层 干燥层受预热层下来的废气加热,温度很快上升到100℃以上,混合料中的游离水大量蒸发,此层厚度一般为l0~30mm。 实际上干燥层与预热层难以截然分开,可以统称为干燥预热层。 -- 1 / 1-- 该层中料球被急剧加热,迅速干燥,易被破坏,恶化料层透气性。
⑤过湿层 从干燥层下来的热废气含有大量水分,料温低于水蒸气的露点温度时,废气中的水蒸气会重新凝结,使混合料中水分大量增加而形成过湿层。 此层水分过多,使料层透气性变坏,降低烧结速度。 烧结过程中的基本化学反应 ①固体碳的燃烧反应 固体碳燃烧反应为:
反应后生成C0和C02,还有部分剩余氧气,为其他反应提供了氧化还原气体和热量。 燃烧产生的废气成分取决于烧结的原料条件、燃料用量、还原和氧化反应的发展程度、以及抽过燃烧层的气体成分等因素。 ②碳酸盐的分解和矿化作用 烧结料中的碳酸盐有CaC03、MgC03、FeC03、MnC03等,其中以CaC03为主。在烧结条件下,CaC03在720℃左右开始分解,880℃时开始化学沸腾,其他碳酸盐相应的分解温度较低些。 碳酸钙分解产物Ca0能与烧结料中的其他矿物发生反应,生成新的化合物,这就是矿化作用。反应式为: CaCO3+SiO2=CaSiO3+CO2 CaCO3+Fe2O3=CaO ·Fe2O3+ CO2 如果矿化作用不完全,将有残留的自由Ca0存在,在存放过程中,它将同大气中的水分进行消化作用: CaO+H2O=Ca(OH)2 使烧结矿的体积膨胀而粉化。 ③铁和锰氧化物的分解、还原和氧化 铁的氧化物在烧结条件下,温度高于l300℃时,Fe203可以分解:
Fe304在烧结条件下分解压很小,但在有Si02存在、温度大于1300℃时,也可能分解: 二 、球团矿生产