焦化厂炼焦工艺介绍分解
炼焦工艺流程解说
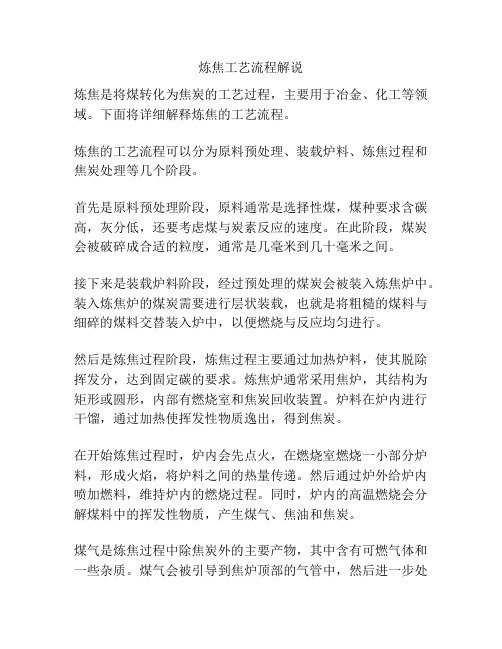
炼焦工艺流程解说炼焦是将煤转化为焦炭的工艺过程,主要用于冶金、化工等领域。
下面将详细解释炼焦的工艺流程。
炼焦的工艺流程可以分为原料预处理、装载炉料、炼焦过程和焦炭处理等几个阶段。
首先是原料预处理阶段,原料通常是选择性煤,煤种要求含碳高,灰分低,还要考虑煤与炭素反应的速度。
在此阶段,煤炭会被破碎成合适的粒度,通常是几毫米到几十毫米之间。
接下来是装载炉料阶段,经过预处理的煤炭会被装入炼焦炉中。
装入炼焦炉的煤炭需要进行层状装载,也就是将粗糙的煤料与细碎的煤料交替装入炉中,以便燃烧与反应均匀进行。
然后是炼焦过程阶段,炼焦过程主要通过加热炉料,使其脱除挥发分,达到固定碳的要求。
炼焦炉通常采用焦炉,其结构为矩形或圆形,内部有燃烧室和焦炭回收装置。
炉料在炉内进行干馏,通过加热使挥发性物质逸出,得到焦炭。
在开始炼焦过程时,炉内会先点火,在燃烧室燃烧一小部分炉料,形成火焰,将炉料之间的热量传递。
然后通过炉外给炉内喷加燃料,维持炉内的燃烧过程。
同时,炉内的高温燃烧会分解煤料中的挥发性物质,产生煤气、焦油和焦炭。
煤气是炼焦过程中除焦炭外的主要产物,其中含有可燃气体和一些杂质。
煤气会被引导到焦炉顶部的气管中,然后进一步处理,用于炼焦炉的燃烧或者作为其他化工生产的原料。
焦油是炼焦过程中除焦炭外的另一个主要产物,其中含有水、苯、酚等有机物质。
焦油会被冷凝成液体,然后通过分离和再加工,可以用于制取煤焦油、柴油等燃料,或作为化工原料。
焦炭是炼焦过程中得到的主要产品,也是电炉炼钢和冶金铸造中的重要原料。
焦炭会被释放出炉体,然后经过冷却、除尘等处理,得到成品焦炭。
最后是焦炭处理阶段,成品焦炭会被进行分类、包装等处理,以便于储存、运输和使用。
总的来说,炼焦工艺流程是将煤炭转化为焦炭的过程,主要包括原料预处理、装载炉料、炼焦过程和焦炭处理等几个阶段。
通过这些工艺步骤,可以有效地将煤炭转化为有用的能源和原材料,满足不同领域的需求。
焦炉炼焦工艺
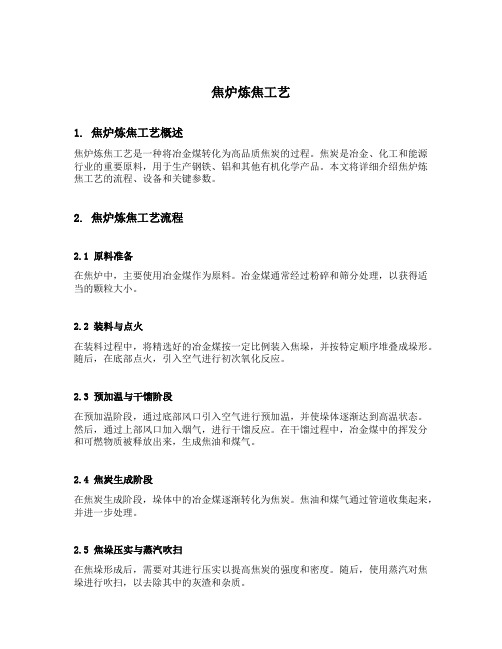
焦炉炼焦工艺1. 焦炉炼焦工艺概述焦炉炼焦工艺是一种将冶金煤转化为高品质焦炭的过程。
焦炭是冶金、化工和能源行业的重要原料,用于生产钢铁、铝和其他有机化学产品。
本文将详细介绍焦炉炼焦工艺的流程、设备和关键参数。
2. 焦炉炼焦工艺流程2.1 原料准备在焦炉中,主要使用冶金煤作为原料。
冶金煤通常经过粉碎和筛分处理,以获得适当的颗粒大小。
2.2 装料与点火在装料过程中,将精选好的冶金煤按一定比例装入焦垛,并按特定顺序堆叠成垛形。
随后,在底部点火,引入空气进行初次氧化反应。
2.3 预加温与干馏阶段在预加温阶段,通过底部风口引入空气进行预加温,并使垛体逐渐达到高温状态。
然后,通过上部风口加入烟气,进行干馏反应。
在干馏过程中,冶金煤中的挥发分和可燃物质被释放出来,生成焦油和煤气。
2.4 焦炭生成阶段在焦炭生成阶段,垛体中的冶金煤逐渐转化为焦炭。
焦油和煤气通过管道收集起来,并进一步处理。
2.5 焦垛压实与蒸汽吹扫在焦垛形成后,需要对其进行压实以提高焦炭的强度和密度。
随后,使用蒸汽对焦垛进行吹扫,以去除其中的灰渣和杂质。
2.6 卸料与冷却最后,在一定时间内完成焦化过程后,将形成的焦炭从焦垛中卸出,并送入冷却塔进行快速冷却。
冷却后的焦炭即可用于下游工艺。
3. 焦炉设备3.1 焦垛焦垛是用于装载冶金煤并进行干馏反应的装置。
它通常由耐火材料构成,具有一定的孔隙结构,以便于煤气和焦油的顺利流出。
3.2 风口风口用于控制空气的进入和排出。
它分为底部风口和上部风口,分别用于预加温和干馏阶段的空气供应。
3.3 管道系统管道系统用于收集焦油和煤气,并将其送往后续处理设备。
它包括主管道、分支管道和收集器等组成部分。
3.4 冷却塔冷却塔用于将炼焦过程中产生的煤气快速冷却,以使其中的焦油凝结并收集起来。
冷却塔通常由多级塞式冷却器组成。
4. 焦炉关键参数4.1 温度在焦炉炼焦过程中,温度是一个重要的参数。
适当的温度可以促进冶金煤中挥发分的释放和焦炭生成反应的进行。
焦化厂详细工艺流程
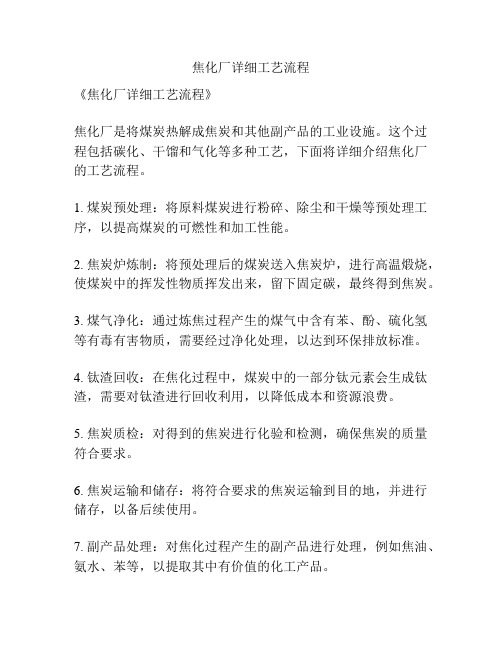
焦化厂详细工艺流程
《焦化厂详细工艺流程》
焦化厂是将煤炭热解成焦炭和其他副产品的工业设施。
这个过程包括碳化、干馏和气化等多种工艺,下面将详细介绍焦化厂的工艺流程。
1. 煤炭预处理:将原料煤炭进行粉碎、除尘和干燥等预处理工序,以提高煤炭的可燃性和加工性能。
2. 焦炭炉炼制:将预处理后的煤炭送入焦炭炉,进行高温煅烧,使煤炭中的挥发性物质挥发出来,留下固定碳,最终得到焦炭。
3. 煤气净化:通过炼焦过程产生的煤气中含有苯、酚、硫化氢等有毒有害物质,需要经过净化处理,以达到环保排放标准。
4. 钛渣回收:在焦化过程中,煤炭中的一部分钛元素会生成钛渣,需要对钛渣进行回收利用,以降低成本和资源浪费。
5. 焦炭质检:对得到的焦炭进行化验和检测,确保焦炭的质量符合要求。
6. 焦炭运输和储存:将符合要求的焦炭运输到目的地,并进行储存,以备后续使用。
7. 副产品处理:对焦化过程产生的副产品进行处理,例如焦油、氨水、苯等,以提取其中有价值的化工产品。
总的来说,焦化厂的工艺流程复杂而严谨,需要精密的设备和严格的操作流程,以确保生产出符合质量标准的焦炭和其他副产品,并将有害物质排放控制在规定范围内,以保护环境和人类健康。
炼焦车间工艺流程
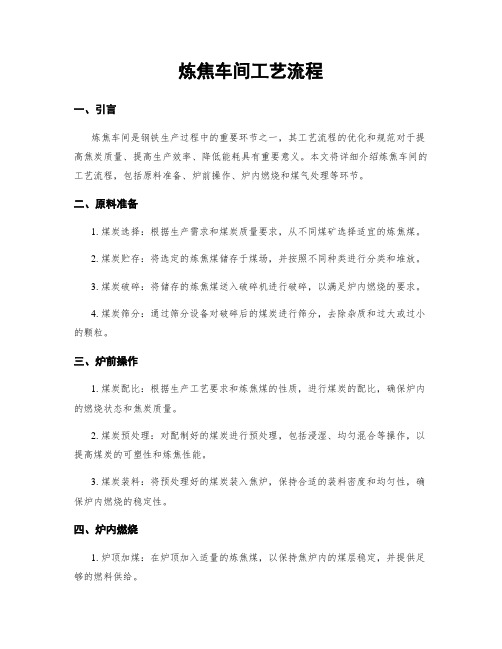
炼焦车间工艺流程一、引言炼焦车间是钢铁生产过程中的重要环节之一,其工艺流程的优化和规范对于提高焦炭质量、提高生产效率、降低能耗具有重要意义。
本文将详细介绍炼焦车间的工艺流程,包括原料准备、炉前操作、炉内燃烧和煤气处理等环节。
二、原料准备1. 煤炭选择:根据生产需求和煤炭质量要求,从不同煤矿选择适宜的炼焦煤。
2. 煤炭贮存:将选定的炼焦煤储存于煤场,并按照不同种类进行分类和堆放。
3. 煤炭破碎:将储存的炼焦煤送入破碎机进行破碎,以满足炉内燃烧的要求。
4. 煤炭筛分:通过筛分设备对破碎后的煤炭进行筛分,去除杂质和过大或过小的颗粒。
三、炉前操作1. 煤炭配比:根据生产工艺要求和炼焦煤的性质,进行煤炭的配比,确保炉内的燃烧状态和焦炭质量。
2. 煤炭预处理:对配制好的煤炭进行预处理,包括浸湿、均匀混合等操作,以提高煤炭的可塑性和炼焦性能。
3. 煤炭装料:将预处理好的煤炭装入焦炉,保持合适的装料密度和均匀性,确保炉内燃烧的稳定性。
四、炉内燃烧1. 炉顶加煤:在炉顶加入适量的炼焦煤,以保持焦炉内的煤层稳定,并提供足够的燃料供给。
2. 炉内燃烧:点火后,通过炉底的风口和煤气出口的排风系统,控制炉内的燃烧过程,使煤炭逐渐转化为焦炭。
3. 炉内温度控制:通过调节燃烧风量、煤气回收和煤层厚度等参数,控制焦炉内的温度,以保证焦炭的质量和产量。
五、煤气处理1. 煤气收集:将炉内产生的煤气通过煤气管道收集到煤气处理系统。
2. 煤气净化:通过除尘器、洗涤塔等设备,去除煤气中的颗粒物、硫化物等有害物质,以净化煤气。
3. 煤气回收:对净化后的煤气进行回收利用,用于供热、发电等用途,以提高能源利用效率。
4. 焦炉排放:对经过处理后的煤气进行排放,确保排放达到环保要求。
六、总结炼焦车间的工艺流程涵盖了原料准备、炉前操作、炉内燃烧和煤气处理等环节。
通过科学的工艺流程和严格的操作控制,可以提高焦炭质量、提高生产效率,并降低能耗。
同时,合理的煤炭选择和煤炭预处理也对炼焦车间的运行和焦炭质量有着重要影响。
焦化厂炼焦工艺介绍分解

焦化厂炼焦工艺介绍分解首先,炼焦过程开始于煤炭的破碎和研磨阶段。
此阶段的目的是将大块煤炭破碎成适合炉料使用的小颗粒。
然后,这些小颗粒被进一步细磨以提高反应速率。
接下来,细磨后的煤炭被送入炼焦炉。
炼焦炉是一个巨大的圆筒形结构,内部设置有多层炼焦炉砖。
炼焦炉通常采用非直接加热方式,即在炉外通过热交换装置将燃烧产生的高温煤气输送到炼焦炉内以加热煤炭。
在炼焦炉的下方放有装料器,用来将细磨后的煤炭均匀地放入炉内。
炉内将煤炭按照时间和温度的不同区域分成干燥预热区、干馏区、焦化区和冷却区。
在干燥预热区,炉内温度逐渐升高,将煤炭中的水分蒸发掉。
同时,在干馏区,高温煤气通过煤炭层,引起煤炭内部的干馏反应。
这个过程将导致煤炭分子内部的结构发生改变,生成焦炭和煤气。
然后,在焦化区,煤炭内部的挥发分子和焦炭分子进一步分解。
这个区域的温度相对较高,可以使煤气中的可燃气体和焦油以及其他挥发分子分离出来。
这些煤气和液态产物被导出到后续处理装置中进行处理和分离。
最后,在冷却区,冷却气体被引入炼焦炉内,将焦炭迅速冷却。
冷却后的焦炭将被输送到焦炭处理装置进行筛分和包装。
总的来说,焦化厂炼焦工艺是一个复杂的过程,需要控制多个参数,如温度、压力和气体流量等。
这些参数的优化会影响煤炭的炼焦效率和焦炭质量。
同时,炼焦过程中产生的煤气也是重要的能源和化学原料,可以用于发电、供热和其他工业生产过程。
因此,焦化厂炼焦工艺的研究和改进对提高能源利用效率和环境保护具有重要意义。
焦化厂炼焦工艺介绍
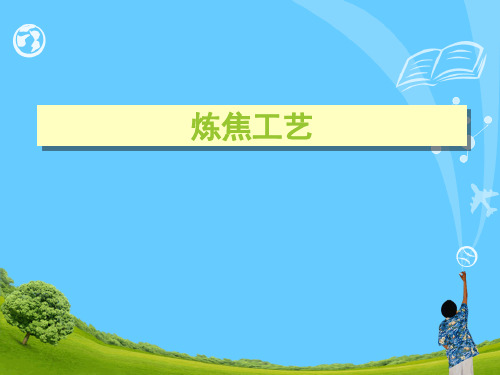
1、焦炭的宏观构造与孔孢结构
焦炭是一种质地坚硬、多孔、呈银灰色,并有不同粗细裂纹 的碳质固体块状材料,其真相对密度约1.80—1.95,视密度 0.88—1.08, 堆积密度约450kg/m3。
焦饼沿纵、横裂纹掰开即得焦块。沿微裂纹分开即得焦体。 焦体由气孔和气孔壁构成,气孔壁又称焦质,其主要成分 是碳和矿物质。焦炭裂纹的多少直接影响焦炭的粒度和抗 碎强度。焦块微裂纹的多少和焦体的孔孢结构则与焦炭的 耐磨强度和高温反应性能有密切关系。孔孢结构通常用气 孔率、气孔平均直径、孔径分布、气孔壁厚度和比表面积 等参数表示。
1、来煤接收 就是将来自矿山的煤卸至煤场。 卸煤机械包括:卸车机械和卸船机械。 卸车机械包括:翻车机、螺旋卸车机、链斗卸车机、
装卸桥、门式抓斗起重机等。 卸船机械就是悬臂抓斗起重机。
2、贮存和倒运 就是将来煤储存于煤场,以便随时取用。
贮存和倒运的目的: (1)保证焦炉连续生产; (2)同类单种混匀以稳定煤质; (3)沥水以稳定水分。 倒运机械包括:堆取料机和门式抓斗机等。
先配合后粉碎工艺 先将各单种煤按一定配比配合后,再进行粉碎的一种备煤工艺。
(1)炭化室和燃烧室
炭化室是煤料隔绝空气进行炭化的地方。燃烧室煤气燃烧 向炭化室供给热量的地方。二者相间排列。
锥度——为了推焦的方便,炭化室的水平截面呈梯形,焦侧 宽机侧窄,焦侧与机侧的宽度差,称为炭化室的锥度。机 、焦侧宽度的平均值,称为炭化室的平均宽度。
第二节 炼焦工艺与设备
备煤、炼焦生产工艺流程
矿山来煤(洗精煤) 接收 贮存 倒运 配合
粉碎 炭化 推焦 (干、湿)熄焦
筛焦 荒煤气 上升管
桥管
集气管
回收车间 气液分离器 >25mm 高炉焦——供高炉炼焦 10~25mm 中块焦——外销 <10mm 粉焦——烧结燃料
炼焦车间工艺流程
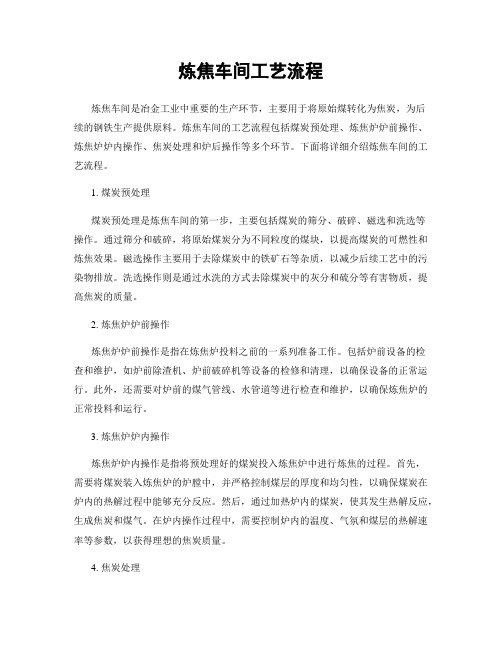
炼焦车间工艺流程炼焦车间是冶金工业中重要的生产环节,主要用于将原始煤转化为焦炭,为后续的钢铁生产提供原料。
炼焦车间的工艺流程包括煤炭预处理、炼焦炉炉前操作、炼焦炉炉内操作、焦炭处理和炉后操作等多个环节。
下面将详细介绍炼焦车间的工艺流程。
1. 煤炭预处理煤炭预处理是炼焦车间的第一步,主要包括煤炭的筛分、破碎、磁选和洗选等操作。
通过筛分和破碎,将原始煤炭分为不同粒度的煤块,以提高煤炭的可燃性和炼焦效果。
磁选操作主要用于去除煤炭中的铁矿石等杂质,以减少后续工艺中的污染物排放。
洗选操作则是通过水洗的方式去除煤炭中的灰分和硫分等有害物质,提高焦炭的质量。
2. 炼焦炉炉前操作炼焦炉炉前操作是指在炼焦炉投料之前的一系列准备工作。
包括炉前设备的检查和维护,如炉前除渣机、炉前破碎机等设备的检修和清理,以确保设备的正常运行。
此外,还需要对炉前的煤气管线、水管道等进行检查和维护,以确保炼焦炉的正常投料和运行。
3. 炼焦炉炉内操作炼焦炉炉内操作是指将预处理好的煤炭投入炼焦炉中进行炼焦的过程。
首先,需要将煤炭装入炼焦炉的炉膛中,并严格控制煤层的厚度和均匀性,以确保煤炭在炉内的热解过程中能够充分反应。
然后,通过加热炉内的煤炭,使其发生热解反应,生成焦炭和煤气。
在炉内操作过程中,需要控制炉内的温度、气氛和煤层的热解速率等参数,以获得理想的焦炭质量。
4. 焦炭处理炼焦炉炉内操作完成后,需要对产生的焦炭进行处理。
首先,将焦炭从炉膛中取出,并进行冷却和除渣操作。
冷却操作主要是通过水冷方式将焦炭迅速降温,以防止焦炭自燃。
除渣操作则是通过机械设备将焦炭表面的渣块和杂质去除,以提高焦炭的质量。
除渣后的焦炭可以进行分级和包装,以满足不同客户的需求。
5. 炉后操作炉后操作是指在炼焦炉炉内操作和焦炭处理完成后的一系列操作。
包括炉后设备的检查和维护,如炉后除渣机、炉后破碎机等设备的检修和清理,以确保设备的正常运行。
此外,还需要对炉后的煤气管线、水管道等进行检查和维护,以确保炼焦炉的正常运行和安全。
炼焦车间工艺流程
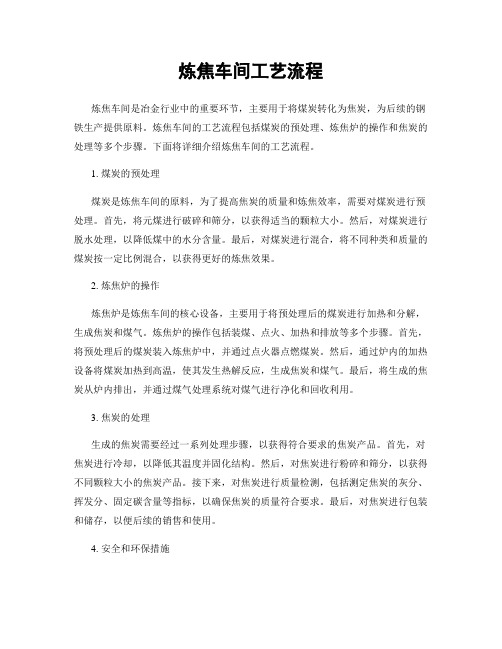
炼焦车间工艺流程炼焦车间是冶金行业中的重要环节,主要用于将煤炭转化为焦炭,为后续的钢铁生产提供原料。
炼焦车间的工艺流程包括煤炭的预处理、炼焦炉的操作和焦炭的处理等多个步骤。
下面将详细介绍炼焦车间的工艺流程。
1. 煤炭的预处理煤炭是炼焦车间的原料,为了提高焦炭的质量和炼焦效率,需要对煤炭进行预处理。
首先,将元煤进行破碎和筛分,以获得适当的颗粒大小。
然后,对煤炭进行脱水处理,以降低煤中的水分含量。
最后,对煤炭进行混合,将不同种类和质量的煤炭按一定比例混合,以获得更好的炼焦效果。
2. 炼焦炉的操作炼焦炉是炼焦车间的核心设备,主要用于将预处理后的煤炭进行加热和分解,生成焦炭和煤气。
炼焦炉的操作包括装煤、点火、加热和排放等多个步骤。
首先,将预处理后的煤炭装入炼焦炉中,并通过点火器点燃煤炭。
然后,通过炉内的加热设备将煤炭加热到高温,使其发生热解反应,生成焦炭和煤气。
最后,将生成的焦炭从炉内排出,并通过煤气处理系统对煤气进行净化和回收利用。
3. 焦炭的处理生成的焦炭需要经过一系列处理步骤,以获得符合要求的焦炭产品。
首先,对焦炭进行冷却,以降低其温度并固化结构。
然后,对焦炭进行粉碎和筛分,以获得不同颗粒大小的焦炭产品。
接下来,对焦炭进行质量检测,包括测定焦炭的灰分、挥发分、固定碳含量等指标,以确保焦炭的质量符合要求。
最后,对焦炭进行包装和储存,以便后续的销售和使用。
4. 安全和环保措施在炼焦车间的工艺流程中,安全和环保是非常重要的考虑因素。
为了确保工人的安全,需要提供必要的个人防护设备,并对操作人员进行培训和指导。
此外,还需要定期检查和维护设备,确保其正常运行。
在环保方面,需要采取措施减少炼焦过程中产生的废气和废水的排放,并对废气和废水进行处理,以符合环保要求。
总结:炼焦车间的工艺流程包括煤炭的预处理、炼焦炉的操作和焦炭的处理等多个步骤。
通过对煤炭的预处理和炼焦炉的操作,将煤炭转化为焦炭和煤气。
焦炭经过冷却、粉碎、筛分和质量检测等步骤后,最终得到符合要求的焦炭产品。
- 1、下载文档前请自行甄别文档内容的完整性,平台不提供额外的编辑、内容补充、找答案等附加服务。
- 2、"仅部分预览"的文档,不可在线预览部分如存在完整性等问题,可反馈申请退款(可完整预览的文档不适用该条件!)。
- 3、如文档侵犯您的权益,请联系客服反馈,我们会尽快为您处理(人工客服工作时间:9:00-18:30)。
CO2+C==2CO-166320Kj FeO+CO==Fe+CO2+13650Kj
FeO+C==Fe+CO-152670Kj 从反应历程来说仍属两步气固反应,但从热力学 观点看,恰如铁氧化物被固态碳还原。因此,在 1100℃以上,铁氧化物的还原属于和固态碳反应、生 成CO并大量吸热的直接还原。
焦炭的作用可以概括为: 高炉冶炼过程的热源; 矿石中铁氧化物的还原剂; 高炉料柱的疏松骨架; 高炉铁的渗碳剂。
(2)斜道区
位于燃烧室和蓄热室之间,是连接燃烧室和蓄热室的通道 。结构复杂。
(3)蓄热室
位于焦炉的下部,是回收废气中的废热并用来预热上升 的空气和高炉煤气的地方。内填格子砖作为热交换的介质 。 下部设小烟道,顶部设蓄热室顶部空间。
1、来煤接收 就是将来自矿山的煤卸至煤场。 卸煤机械包括:卸车机械和卸船机械。 卸车机械包括:翻车机、螺旋卸车机、链斗卸车机、 装卸桥、门式抓斗起重机等。
卸船机械就是悬臂抓斗起重机。
2、贮存和倒运
就是将来煤储存于煤场,以便随时取用。
贮存和倒运的目的: (1)保证焦炉连续生产; (2)同类单种混匀以稳定煤质; (3)沥水以稳定水分。 倒运机械包括:堆取料机和门式抓斗机等。
4、粉碎 就是将配合煤粉碎至一定的细度,以便装炉炼焦。 细度——配合煤料中<3mm粒级的量占总量的百分 数。一般控制在73~82%。 粉碎设备: 粉碎机:锤式粉碎机、反击式粉碎机 5、粉碎工艺 包括: 先配后粉、先粉后配、部分硬质煤预粉碎、分组粉碎、 选择粉碎等流程。
粉碎工艺 炼焦煤的工艺必须适应炼焦煤的粉碎特性,使粒度达到或接近最佳粒度 分布,由于煤的最佳粒度分布因煤种、岩相组成而异,因此不同煤和配 合煤应采用不同的粉碎工艺。
2、高炉内的冶炼过程
炉料:矿石:天然矿、烧结矿、团球矿 熔剂:石灰石、白云石、生石灰 焦炭 从炉顶依次分批、分层装入炉内。
高温空气或富氧空气由风口鼓入,使焦炭在风口前的回旋 区内剧烈燃烧。燃烧产生的热能,是高炉冶炼过程的主要热源, 燃烧反应后产生的CO作为高炉冶炼过程的主要还原剂。 焦炭在回旋区内燃烧生成的高温煤气在上升过程中将热能 传给炉料,与焦炭发生吸热反应生成CO,随后CO将铁矿石中 的铁氧化物还原。
高炉冶炼对焦炭质量的要求
1、具有合适的筛分组成和均匀的块度; 2、较高的机械强度,M40要大,M10要小; 3、水分低且稳定; 4、灰分要低; 5、硫分要低; 6、Vdaf≯1.9%; 7、CRI要适度低,CSR要高; 8、各向异性程度要高; 9、性能稳定。
非高炉用焦炭的特性
1、铸造焦 用于冲天炉熔铁。C + O2 ====CO2 + Q 要求:(1)粒度大且反应性低; (2)硫分低、灰分低 2、气化焦 用于煤气发生炉生产煤气。 C + CO2 ==== 2CO, C + H2O ==== H2 + CO 要求:(1)粒度均匀且反应性高; (2)硫分低、灰分低 3、电石焦 用于电石生产。 CaO + 3C ===== CaC2 + CO (1800—2200℃) 要求:(1)粒度3—20mm; (2)灰分低、碳含量高 (3)水分低,<6%
3、配合
就是将不同的单种煤按一定比例配在一起,以便配
煤炼焦。 配煤方式:煤场配煤和配煤槽配煤。我国常用配煤
槽配煤。
配煤设施和设备:配煤槽、配煤盘(园盘给料机)、 电磁振动给料器等。
1 配煤工艺与设备
两种配煤系统:1)配煤槽
2)煤场配煤
(1)配煤槽的个数与容量,见表。一般比煤种多2~3个,生产能 力较大的焦化厂,配煤槽数量最好为煤种数的一倍。
炼焦工艺
1、焦炭的宏观构造与孔孢结构
焦炭是一种质地坚硬、多孔、呈银灰色,并有不同粗细裂纹 的碳质固体块状材料,其真相对密度约1.80—1.95,视密度 0.88—1.08, 堆积密度约450kg/m3。 焦饼沿纵、横裂纹掰开即得焦块。沿微裂纹分开即得焦体。
焦体由气孔和气孔壁构成,气孔壁又称焦质,其主要成分 是碳和矿物质。焦炭裂纹的多少直接影响焦炭的粒度和抗 碎强度。焦块微裂纹的多少和焦体的孔孢结构则与焦炭的 耐磨强度和高温反应性能有密切关系。孔孢结构通常用气 孔率、气孔平均直径、孔径分布、气孔壁厚度和比表面积 等参数表示。
铁氧化物的还原反应 间接还原: 当温度t<570 ℃时, Fe3O4+4CO==3Fe+4CO2+17220Kj 当温度t=570—800℃时,铁氧化物还原过程按 Fe2O3、Fe3O4、FeO、Fe这一顺序依次进行: 3Fe2O3+CO==2Fe3O4+CO2+37200KJ Fe2O3+CO==3FeO+CO2-20960Kj FeO+CO==Fe+CO2+13650Kj 直接还原: 当温度t>1100 ℃时,碳溶反应的平衡常数和反 应速度常数均很高,一出现CO2亦即刻与焦炭中的碳 相互作用生成CO,即CO2 + C == 2CO,铁氧化物的 还原按以下方式进行:
第二节
炼焦工艺与设备
备煤、炼焦生产工艺流程
矿山来煤(洗精煤) 粉碎 炭化 接收 推焦 贮存 倒运 配合
(干、湿)熄焦
筛焦
荒煤气
上升管
桥管
ቤተ መጻሕፍቲ ባይዱ
集气管
吸气管
回收车间 气液分离器 >25mm 高炉焦——供高炉炼焦 10~25mm 中块焦——外销 <10mm 粉焦——烧结燃料
包括:来煤接收、贮存、倒运、配合、粉碎等工序。其生产目的是: 向焦炉提供数量充够、质量合格的炼焦煤料。
先配合后粉碎工艺 先将各单种煤按一定配比配合后,再进行粉碎的一种备煤工艺。
(1)炭化室和燃烧室
炭化室是煤料隔绝空气进行炭化的地方。燃烧室煤气燃烧 向炭化室供给热量的地方。二者相间排列。 锥度——为了推焦的方便,炭化室的水平截面呈梯形,焦侧 宽机侧窄,焦侧与机侧的宽度差,称为炭化室的锥度。机 、焦侧宽度的平均值,称为炭化室的平均宽度。 加热水平(高度)——为了焦饼上下均匀成熟,炭化室高度 要高于燃烧室,二者的高度差,称为焦炉的加热水平(高 度)。 为了燃烧室长向加热的均匀性和提高炭化室的结构强度,将 燃烧室分成各个立火道。立火道的连接方式有双联式、二 分式、四分式、跨顶式等。 改善高向加热均匀性的措施:废气循环、高低灯头、分段加 热、不同炉墙厚度等