焦化厂炼焦车间工艺流程
炼焦车间工艺流程

炼焦车间工艺流程炼焦车间是冶金生产过程中的重要环节,主要负责将煤炭转化为高热值焦炭。
本文将介绍炼焦车间的工艺流程,包括煤炭处理、焦炉炼焦、焦炭处理和环保措施等。
一、煤炭处理煤炭是炼焦车间的原料,煤种的选择和煤炭质量的分析十分重要。
首先,通过采样车对原料煤进行采样并送至实验室进行化验,确保煤炭的质量符合炼焦要求。
然后,将煤炭送至煤炭仓库,并采用堆煤或者装车的方式储存。
在进入焦炉炼焦前,还需要对煤炭进行破碎、筛分和除尘等处理。
二、焦炉炼焦1.炉前准备焦炉炼焦过程的开始是进行炉前准备工作。
首先,需要点火炉,使焦炉内部温度升高到适宜的炼焦温度。
然后,将预先破碎和筛分好的煤炭装入焦炉的炉膛中,并通过矿泉水进行浇水封固。
2.爆破与变形在焦炉内,煤炭在高温条件下经历爆破与变形的过程。
首先,煤炭在炉膛中被热融露水气化产生一氧化碳,同时放出大量的热量;然后,在高温下,煤炭中的固定碳燃烧形成煤气;最后,煤气通过炼化管排出焦炉。
3.除渣与配风焦炉内部的煤渣会随着冷凝器中凝结水的排放而流出炉外。
炉渣经后处理可再细化为微粒状焦粉。
配风是为了提供足够的氧气支持煤炭燃烧和蒸发,通过压排风机将新风吹入到炉膛和燃烧室中。
三、焦炭处理经过一定时间的炼焦,焦炉内的煤炭会经过焦化过程变成焦炭。
焦炭处理包括降温、除尘、分级和包装等环节。
首先,焦炭从焦炉中排出后需要进行降温,以防止炭块自燃。
然后,通过除尘设备对炼焦过程中产生的粉尘进行收集和处理。
接下来,焦炭会经过粒度分级,筛分出符合要求的炭块。
最后,经过包装,焦炭可以进行储存和运输。
四、环保措施炼焦车间是一个高污染的作业场所,所以环保措施是必不可少的。
首先,焦炉应配备炉渣处理设备,将产生的炉渣经过除渣设施进行处理,防止对环境造成污染。
其次,焦炉煤气通过炼化管进入冷凝器冷却凝结后,再经过除尘设备进行治理。
此外,焦炉应配备高效的除尘设备,对散发的粉尘进行收集和处理。
另外,焦炭处理环节也需要配备相应的除尘设备。
炼焦车间工艺流程
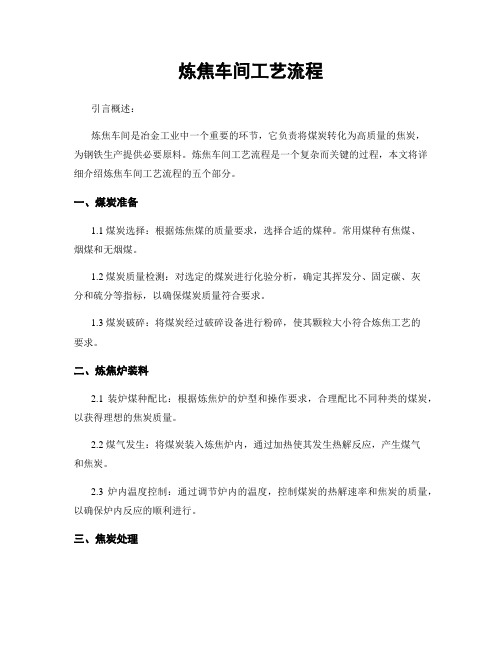
炼焦车间工艺流程引言概述:炼焦车间是冶金工业中一个重要的环节,它负责将煤炭转化为高质量的焦炭,为钢铁生产提供必要原料。
炼焦车间工艺流程是一个复杂而关键的过程,本文将详细介绍炼焦车间工艺流程的五个部分。
一、煤炭准备1.1 煤炭选择:根据炼焦煤的质量要求,选择合适的煤种。
常用煤种有焦煤、烟煤和无烟煤。
1.2 煤炭质量检测:对选定的煤炭进行化验分析,确定其挥发分、固定碳、灰分和硫分等指标,以确保煤炭质量符合要求。
1.3 煤炭破碎:将煤炭经过破碎设备进行粉碎,使其颗粒大小符合炼焦工艺的要求。
二、炼焦炉装料2.1 装炉煤种配比:根据炼焦炉的炉型和操作要求,合理配比不同种类的煤炭,以获得理想的焦炭质量。
2.2 煤气发生:将煤炭装入炼焦炉内,通过加热使其发生热解反应,产生煤气和焦炭。
2.3 炉内温度控制:通过调节炉内的温度,控制煤炭的热解速率和焦炭的质量,以确保炉内反应的顺利进行。
三、焦炭处理3.1 焦炭冷却:将炼焦炉中产生的热焦炭通过冷却设备进行冷却,以降低焦炭的温度,方便后续处理。
3.2 焦炭筛分:将冷却后的焦炭经过筛分设备进行分级,得到不同粒径的焦炭产品。
3.3 焦炭质量检测:对筛分后的焦炭进行化验分析,检测其固定碳、灰分、挥发分和硫分等指标,以确保焦炭质量符合要求。
四、煤气处理4.1 煤气净化:将炉内产生的煤气通过净化设备进行脱硫、脱氨等处理,降低煤气中有害物质的含量。
4.2 煤气回收利用:经过净化处理后的煤气可以作为燃料供给炼焦炉的热解反应,提高能源利用效率。
4.3 煤气排放控制:对煤气进行监测,确保其排放符合环保要求,减少对环境的污染。
五、焦炉操作维护5.1 炉渣处理:定期清理炉渣,保持炉内的清洁,提高炉效。
5.2 炉况监测:对炼焦炉的温度、压力、煤气成分等关键参数进行监测,及时调整操作参数,确保炉内反应的正常进行。
5.3 设备维护保养:定期对炼焦车间的设备进行维护保养,确保设备的正常运行,减少故障发生的可能性。
炼焦车间工艺流程

炼焦车间工艺流程炼焦车间是钢铁生产过程中的重要环节,它主要负责将煤炭转化为高质量的焦炭,为后续的炼钢过程提供原料。
下面将详细介绍炼焦车间的工艺流程。
1. 原料准备炼焦车间的主要原料是冶金焦炭煤和炼焦煤。
这些煤炭经过筛分、粉碎等处理后,按照一定的配比比例送入炼焦炉。
2. 炼焦炉装料炼焦炉是炼焦车间的核心设备,用于将煤炭加热至高温下进行炼焦反应。
在装料过程中,按照一定的层次和厚度将煤炭装入炼焦炉内,并在不同层次上设置隔板,以控制炉内温度和气体流动。
3. 炼焦炉预热在装料完成后,需要对炼焦炉进行预热。
预热的目的是将炉内温度逐渐升高,使煤炭开始发生热解反应。
预热过程通常采用天然气或煤气作为燃料,通过炉内燃烧产生的高温气体对炉内进行加热。
4. 炼焦反应炼焦反应是炼焦车间的关键步骤。
在高温下,煤炭开始发生热解反应,产生大量的气体和焦炭。
在这个过程中,煤炭中的挥发分被释放出来,形成焦炉煤气。
同时,煤炭中的固定碳逐渐转化为焦炭。
5. 焦炭收集在炼焦反应进行的过程中,焦炭逐渐积聚在炼焦炉底部。
当炼焦反应结束后,需要将焦炭从炉内收集出来。
通常采用机械装卸设备将焦炭装入焦斗车,并运输到焦库进行存储。
6. 煤气处理在炼焦过程中产生的焦炉煤气含有大量的有害物质,需要进行处理。
煤气处理包括除尘、脱硫、脱氨等工艺,以减少对环境的污染,并回收其中的有价值成分。
7. 焦炉冷却炼焦炉在炼焦反应结束后需要进行冷却。
冷却过程通常采用水冷方式,将冷却水通过炉体进行循环冷却,以降低炉体温度,同时回收部分热能。
8. 渣铁处理在炼焦车间的炼焦过程中,会产生一定量的渣铁。
渣铁是指炼焦炉内未完全熔化的矿石和煤炭残渣。
渣铁需要进行处理,通常采用磁选、重选等方式进行分离和回收。
9. 能源回收利用炼焦车间的炼焦过程中产生大量的热能和煤气。
这些能源可以通过热交换、发电等方式进行回收和利用,以提高能源利用效率,降低能源消耗。
10. 环境保护炼焦车间是一个高污染的工艺环节,对环境造成的污染较大。
炼焦车间工艺流程
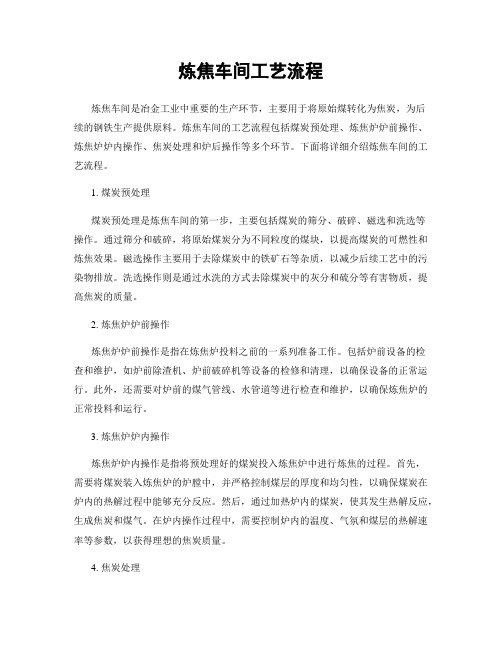
炼焦车间工艺流程炼焦车间是冶金工业中重要的生产环节,主要用于将原始煤转化为焦炭,为后续的钢铁生产提供原料。
炼焦车间的工艺流程包括煤炭预处理、炼焦炉炉前操作、炼焦炉炉内操作、焦炭处理和炉后操作等多个环节。
下面将详细介绍炼焦车间的工艺流程。
1. 煤炭预处理煤炭预处理是炼焦车间的第一步,主要包括煤炭的筛分、破碎、磁选和洗选等操作。
通过筛分和破碎,将原始煤炭分为不同粒度的煤块,以提高煤炭的可燃性和炼焦效果。
磁选操作主要用于去除煤炭中的铁矿石等杂质,以减少后续工艺中的污染物排放。
洗选操作则是通过水洗的方式去除煤炭中的灰分和硫分等有害物质,提高焦炭的质量。
2. 炼焦炉炉前操作炼焦炉炉前操作是指在炼焦炉投料之前的一系列准备工作。
包括炉前设备的检查和维护,如炉前除渣机、炉前破碎机等设备的检修和清理,以确保设备的正常运行。
此外,还需要对炉前的煤气管线、水管道等进行检查和维护,以确保炼焦炉的正常投料和运行。
3. 炼焦炉炉内操作炼焦炉炉内操作是指将预处理好的煤炭投入炼焦炉中进行炼焦的过程。
首先,需要将煤炭装入炼焦炉的炉膛中,并严格控制煤层的厚度和均匀性,以确保煤炭在炉内的热解过程中能够充分反应。
然后,通过加热炉内的煤炭,使其发生热解反应,生成焦炭和煤气。
在炉内操作过程中,需要控制炉内的温度、气氛和煤层的热解速率等参数,以获得理想的焦炭质量。
4. 焦炭处理炼焦炉炉内操作完成后,需要对产生的焦炭进行处理。
首先,将焦炭从炉膛中取出,并进行冷却和除渣操作。
冷却操作主要是通过水冷方式将焦炭迅速降温,以防止焦炭自燃。
除渣操作则是通过机械设备将焦炭表面的渣块和杂质去除,以提高焦炭的质量。
除渣后的焦炭可以进行分级和包装,以满足不同客户的需求。
5. 炉后操作炉后操作是指在炼焦炉炉内操作和焦炭处理完成后的一系列操作。
包括炉后设备的检查和维护,如炉后除渣机、炉后破碎机等设备的检修和清理,以确保设备的正常运行。
此外,还需要对炉后的煤气管线、水管道等进行检查和维护,以确保炼焦炉的正常运行和安全。
炼焦车间工艺流程

炼焦车间工艺流程炼焦车间是钢铁生产过程中的重要环节,主要负责将焦炭原料转化为高质量的焦炭产品。
炼焦车间工艺流程是指在炼焦车间中进行的一系列工艺步骤和操作流程,以确保焦炭的质量和生产效率。
一、原料准备1. 煤炭选择:根据生产需求和煤炭特性,选择适宜的煤种作为原料。
2. 煤炭存储:将选定的煤炭储存在指定的仓库中,确保煤炭的干燥和保存。
二、煤炭处理1. 煤炭破碎:将储存的煤炭通过破碎机进行破碎,使其颗粒大小符合要求。
2. 煤炭筛分:通过筛分设备对破碎后的煤炭进行分级,分离出不同粒度的煤炭。
三、炼焦炉装料1. 炼焦炉装料:将经过处理的煤炭装入炼焦炉中,形成炉料层。
2. 炉顶密封:使用密封材料对炉顶进行密封,防止煤气泄漏。
四、炼焦过程1. 加热阶段:通过点火装置对炉料进行点火,引燃炉料中的挥发分,产生煤气。
2. 高温阶段:在高温条件下,煤料中的挥发分逐渐释放,形成焦炭。
3. 降温阶段:在炼焦过程结束后,对炉内温度进行逐渐降低,避免焦炭过度燃烧。
五、焦炭处理1. 焦炭卸料:待炼焦过程结束后,将炉内的焦炭从炉底卸出。
2. 焦炭降温:将卸出的焦炭进行降温处理,避免其过热。
3. 焦炭筛分:通过筛分设备对焦炭进行分级,得到不同粒度的焦炭产品。
4. 焦炭质量检测:对焦炭产品进行质量检测,包括灰分、挥发分、固定碳等指标的测定。
六、炼焦炉清理1. 炼焦炉倒灰:定期对炼焦炉进行倒灰操作,清除炉内的积灰和杂质。
2. 炼焦炉维修:对炼焦炉进行定期维修和检修,确保其正常运行。
七、炼焦废气处理1. 炉顶除尘:通过除尘设备对炉顶的煤气进行除尘处理,去除其中的灰尘颗粒。
2. 炉底除渣:清除炉底的焦炭渣滓,避免其对环境造成污染。
3. 煤气净化:对炉顶除尘后的煤气进行净化处理,去除其中的有害物质和污染物。
4. 煤气回收利用:通过煤气净化后,将其作为燃料供给其他生产环节使用,实现资源的循环利用。
以上就是炼焦车间工艺流程的详细描述。
通过严格按照这一流程进行操作,可以保证炼焦车间的正常运行和焦炭产品的高质量生产。
炼焦车间工艺流程
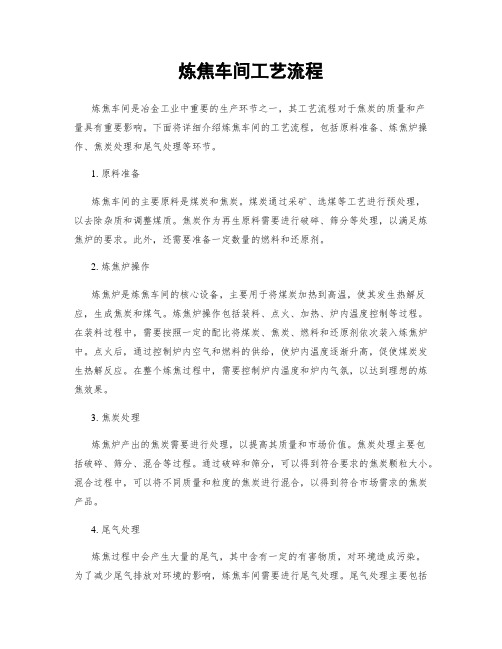
炼焦车间工艺流程炼焦车间是冶金工业中重要的生产环节之一,其工艺流程对于焦炭的质量和产量具有重要影响。
下面将详细介绍炼焦车间的工艺流程,包括原料准备、炼焦炉操作、焦炭处理和尾气处理等环节。
1. 原料准备炼焦车间的主要原料是煤炭和焦炭。
煤炭通过采矿、选煤等工艺进行预处理,以去除杂质和调整煤质。
焦炭作为再生原料需要进行破碎、筛分等处理,以满足炼焦炉的要求。
此外,还需要准备一定数量的燃料和还原剂。
2. 炼焦炉操作炼焦炉是炼焦车间的核心设备,主要用于将煤炭加热到高温,使其发生热解反应,生成焦炭和煤气。
炼焦炉操作包括装料、点火、加热、炉内温度控制等过程。
在装料过程中,需要按照一定的配比将煤炭、焦炭、燃料和还原剂依次装入炼焦炉中。
点火后,通过控制炉内空气和燃料的供给,使炉内温度逐渐升高,促使煤炭发生热解反应。
在整个炼焦过程中,需要控制炉内温度和炉内气氛,以达到理想的炼焦效果。
3. 焦炭处理炼焦炉产出的焦炭需要进行处理,以提高其质量和市场价值。
焦炭处理主要包括破碎、筛分、混合等过程。
通过破碎和筛分,可以得到符合要求的焦炭颗粒大小。
混合过程中,可以将不同质量和粒度的焦炭进行混合,以得到符合市场需求的焦炭产品。
4. 尾气处理炼焦过程中会产生大量的尾气,其中含有一定的有害物质,对环境造成污染。
为了减少尾气排放对环境的影响,炼焦车间需要进行尾气处理。
尾气处理主要包括除尘、脱硫、脱氨等过程。
通过除尘设备,可以去除尾气中的颗粒物;脱硫和脱氨过程则可以去除尾气中的硫化物和氨等有害物质。
总结:炼焦车间的工艺流程包括原料准备、炼焦炉操作、焦炭处理和尾气处理等环节。
在原料准备过程中,需要对煤炭和焦炭进行预处理。
炼焦炉操作是炼焦车间的核心环节,通过控制炉内温度和气氛,使煤炭发生热解反应,生成焦炭和煤气。
焦炭处理过程主要包括破碎、筛分和混合等步骤,以提高焦炭的质量和市场价值。
尾气处理是为了减少炼焦过程中产生的尾气对环境的污染,通过除尘、脱硫和脱氨等过程,去除尾气中的有害物质。
炼焦车间工艺流程
炼焦车间工艺流程炼焦车间是钢铁生产过程中的重要环节,主要负责将煤炭转化为高质量的焦炭,供给高炉使用。
本文将详细介绍炼焦车间的工艺流程,包括原料准备、炼焦炉操作、焦炭处理等环节。
1. 原料准备在炼焦车间工艺流程中,主要原料为煤炭。
首先,需要对煤炭进行筛分和破碎,以确保煤炭的均匀性和适当的粒度。
然后,将煤炭送入混合料仓,与其他辅助原料(如焦炭、石灰石等)进行混合,形成炼焦炉的进料料仓。
2. 炼焦炉操作炼焦炉是炼焦车间的核心设备,主要用于将煤炭加热至高温,使其发生热解和干馏,从而生成焦炭。
炼焦炉的操作主要包括装料、点火、加热、煤气收集等步骤。
2.1 装料装料是指将混合料仓中的原料送入炼焦炉内。
通常采用机械装料方式,将原料通过输送带或斗式提升机送入炼焦炉顶部的装料斗。
2.2 点火装料完成后,需要进行点火操作。
点火主要是通过喷煤枪向炼焦炉内喷射点火煤粉,并通过点火器点燃,使炼焦炉内的煤炭开始燃烧。
2.3 加热点火后,需要对炼焦炉进行加热,使煤炭逐渐升温。
加热过程中,炼焦炉内的煤炭发生热解和干馏反应,生成焦炭和煤气。
加热过程一般分为预热阶段、干馏阶段和冷却阶段。
2.4 煤气收集在加热过程中,煤炭发生热解和干馏反应产生的煤气需要进行收集和处理。
煤气主要通过炼焦炉顶部的煤气管道收集,并经过净化处理后,用于供给其他工序或外部能源利用。
3. 焦炭处理焦炭是炼焦车间的主要产品,需要进行一系列处理操作,以提高其质量和利用价值。
3.1 焦炭出炉在炼焦炉冷却阶段结束后,焦炭会从炼焦炉底部自动排出。
焦炭的出炉温度较高,需要进行冷却处理,以避免自燃。
3.2 焦炭筛分出炉的焦炭通常会经过筛分操作,将不同粒度的焦炭分离。
不同粒度的焦炭可用于不同用途,如高炉煤气化、铁合金生产等。
3.3 焦炭质量检测为确保焦炭质量符合要求,需要进行质量检测。
常见的检测指标包括焦炭灰分、挥发分、固定碳含量等。
检测结果将作为焦炭质量的依据,决定其使用范围和市场价值。
炼焦车间工艺流程
炼焦车间工艺流程炼焦车间是冶金工业中的重要环节,用于将煤炭转化为焦炭,为后续的钢铁生产提供原料。
炼焦车间的工艺流程包括煤炭的选矿、破碎、炼焦和焦炭的处理等多个步骤。
下面将详细介绍炼焦车间的工艺流程。
1. 煤炭选矿:煤炭选矿是将从煤矿中采集的原煤进行筛分和洗选,以去除其中的杂质和硫磷等有害物质。
首先,原煤经过振动筛进行初步的筛分,将大块的煤炭分离出来。
然后,通过浮选机进行浮选,将煤炭和石灰石等杂质分离。
最后,通过重介质分选,根据煤炭的比重差异将煤炭和岩石等进一步分离,得到符合要求的煤炭。
2. 煤炭破碎:经过选矿的煤炭需要进行破碎,以便更好地进行后续的焦化处理。
煤炭破碎一般采用颚式破碎机和辊式破碎机。
首先,将选矿后的煤炭送入颚式破碎机,通过颚板的压力将煤炭破碎成适当的颗粒大小。
然后,将颚碎机破碎后的煤炭送入辊式破碎机,通过辊子的旋转将煤炭进一步破碎成所需的颗粒大小。
3. 炼焦:炼焦是将煤炭在高温下进行加热,使其分解生成焦炭的过程。
炼焦一般分为干炼和湿炼两种方式。
干炼是指将煤炭直接放入焦炉进行加热,湿炼是指将煤炭预先进行水洗后再进行加热。
无论是干炼还是湿炼,炼焦过程中都需要控制温度、时间和煤炭的进料量等参数,以确保焦炭的质量。
炼焦过程中会产生大量的煤气和焦炉煤气,需要进行收集和处理。
4. 焦炭处理:焦炭处理是指对炼焦产生的焦炭进行筛分、冷却和质量检测等工序。
首先,将炼焦产生的焦炭送入筛分机,将焦炭按照不同的颗粒大小进行分级。
然后,将分级后的焦炭送入冷却塔进行冷却,以降低焦炭的温度。
最后,对冷却后的焦炭进行质量检测,包括测定焦炭的灰分、挥发分、固定碳等指标,以确保焦炭的质量符合要求。
总结:炼焦车间的工艺流程包括煤炭选矿、破碎、炼焦和焦炭处理等多个步骤。
通过煤炭选矿,可以去除煤炭中的杂质和有害物质,得到符合要求的煤炭。
煤炭破碎将选矿后的煤炭破碎成所需的颗粒大小。
炼焦过程中,煤炭在高温下分解生成焦炭,需要控制温度、时间和煤炭的进料量等参数。
炼焦车间工艺流程
炼焦车间工艺流程炼焦车间是钢铁生产过程中的重要环节,它是将煤炭转化为焦炭的关键部门。
炼焦车间工艺流程是指在炼焦车间内进行的一系列操作和步骤,以确保高质量的焦炭产出。
下面将详细介绍炼焦车间工艺流程的标准格式文本。
1. 原料准备炼焦车间的原料主要包括煤炭、蒸汽和空气。
首先,煤炭被送入煤仓,并通过输送带或装载机送入煤炭破碎机进行粉碎。
然后,粉碎后的煤炭被输送到煤炭筛分系统,以去除杂质并分级。
最后,符合要求的煤炭被送入配煤系统,按照一定比例混合。
2. 炼焦炉装料配制好的煤炭混合料被送入炼焦炉,装料过程中需要遵循一定的装料规则和技术要求。
装料时,将煤炭混合料均匀地分布在炉膛内,以确保炉内温度和气体分布的均匀性。
3. 炉内加热装料完成后,炼焦炉被密封,进入加热阶段。
炉内加热是通过燃烧炉内的煤气来提供热量的。
煤气通过炉顶的管道进入炉内,与煤炭混合料反应产生高温,使煤炭逐渐升温,发生干馏反应。
4. 炉内干馏在炼焦炉内,煤炭经历干馏过程,即在高温下分解产生气体、液体和固体产物。
干馏过程中,煤炭中的挥发分被释放出来,形成焦炉煤气。
焦炉煤气主要由一氧化碳、氢气和烃类组成,可以用于发电或其他用途。
5. 焦炭产出在炉内干馏的过程中,煤炭逐渐转化为焦炭。
焦炭是一种坚固、多孔的物质,具有高热值和良好的机械强度。
焦炭通过炉底的焦渣口排出,并经过冷却、处理和筛分等工艺步骤后,最终得到高质量的焦炭产品。
6. 炉内除渣在炉内干馏过程中,煤炭中的杂质和灰分会形成焦渣。
为了保证炼焦炉的正常运行,需要定期进行焦渣清除。
焦渣会通过炉底的渣口排出,然后经过冷却和处理,最终得到焦渣产品。
7. 炉内冷却焦炭产出后,需要进行冷却处理。
冷却过程是通过喷水或喷雾装置将冷却介质喷洒到焦炭表面,以降低焦炭温度。
冷却后的焦炭可以更容易地进行处理和筛分。
8. 焦炭处理和筛分冷却后的焦炭需要进行处理和筛分,以去除杂质并得到符合要求的焦炭产品。
焦炭处理包括焦炭破碎、除尘和炭化等工艺。
炼焦车间工艺流程
炼焦车间工艺流程1. 炼焦车间概述炼焦车间是钢铁生产过程中的重要环节,主要负责将煤炭转化为高质量的焦炭。
炼焦车间工艺流程包括原料准备、炉前操作、炉内炼焦、炉后处理等环节。
2. 原料准备炼焦车间的主要原料是冷煤、热煤和焦炭。
冷煤是指从煤矿中开采出来的原始煤炭,经过破碎、筛分等处理后,成为炼焦炉的原料。
热煤是指经过预处理的冷煤,包括热解、干燥等工序。
焦炭则是炼焦炉产生的终产品。
3. 炉前操作炉前操作是指对原料进行预处理,以确保炼焦过程的顺利进行。
主要包括煤炭的破碎、混合和配料等工序。
破碎是将原料煤炭进行粉碎,以增加其表面积,便于燃烧和气化。
混合是将不同种类和质量的煤炭进行混合,以获得更好的炼焦效果。
配料是按照一定比例将混合后的煤炭送入炼焦炉。
4. 炉内炼焦炉内炼焦是指将配料的煤炭送入炼焦炉内进行加热和气化的过程。
炼焦炉一般采用焦炉煤气和煤气发生炉两种方式进行加热。
在加热过程中,煤炭中的挥发分开始释放,产生的气体经过冷却和净化后,变成焦炉煤气。
同时,煤炭中的焦炭开始形成,经过一段时间的炼焦后,炉内的焦炭达到一定质量和数量。
5. 炉后处理炉后处理是指对炼焦炉产生的焦炭进行处理,以获得高质量的焦炭产品。
主要包括焦炭的冷却、粉碎、筛分和质量检测等工序。
焦炭的冷却是将炉内的焦炭经过冷却器冷却至室温,以防止其继续燃烧。
冷却后的焦炭经过粉碎和筛分,得到不同粒度的焦炭产品。
最后,对焦炭进行质量检测,包括灰分、挥发分、固定碳等指标的检测。
6. 炼焦车间的安全措施炼焦车间是一个高温、高压、易燃易爆的工作环境,需要严格遵守安全规程和操作规范。
炼焦车间应配备消防设备,定期进行消防演习和安全培训。
同时,操作人员应佩戴适当的防护装备,如防火服、安全帽、耐高温手套等。
车间内应设置安全警示标识,明确危险区域和禁止行为。
定期检查和维护设备,确保其正常运行和安全使用。
以上是对炼焦车间工艺流程的详细描述。
炼焦车间的工艺流程涉及到多个环节,每个环节都有其特定的操作和要求。
- 1、下载文档前请自行甄别文档内容的完整性,平台不提供额外的编辑、内容补充、找答案等附加服务。
- 2、"仅部分预览"的文档,不可在线预览部分如存在完整性等问题,可反馈申请退款(可完整预览的文档不适用该条件!)。
- 3、如文档侵犯您的权益,请联系客服反馈,我们会尽快为您处理(人工客服工作时间:9:00-18:30)。
焦化厂炼焦车间工艺流程
1、生产流程:
装煤产生的煤尘、水蒸气等进入装煤除尘系统
↑出焦产生的粉尘、烟尘、残余煤气等进入出焦除尘系统
∣荒煤气导出↑水喷淋
∣↑∣↓
配合煤→煤仓→装煤车→炭化室→推焦车→拦焦车→熄焦车→熄焦塔→晾焦台
↑传
∣热
加热∣
回炉煤气------→燃烧室
运焦→筛焦→贮焦仓→外运
↓↓
运焦、筛焦中产生的粉尘进入泡沫除尘器进行处理
2、焦炉燃烧系统气体流向:
(1)加热煤气流向
回炉煤气总管→煤气预热器→煤气主管→煤气节流孔板→加减旋塞→孔板盒
交换旋塞→横管→小孔板→下喷管→直立砖煤气道→立火道灯头砖
(2)空气流向
废气开闭器进风口→小烟道→蓄热室(箅子砖→格子砖)斜道区→立火道底部斜道口(3)废气流向
上升气流立火道底部(空气煤气接触燃烧产生废气)→跨越孔下降气流立火道(一小
部分由废气循环孔倍抽回上升气流)→下降气流斜道区→下降气流蓄热室(格子砖→
箅子砖)→小烟道→分烟道→总烟道→烟囱→排出
3、焦炉荒煤气系统荒煤气流向
氨水喷洒、冷凝清扫
↓
炭化室顶部空间→上升管→桥管→阀体→集气管→吸气管→气液分离器→回收车间
↑
氨水喷洒冷凝
4、出焦除尘系统流程:
压缩空气脉冲反吹清灰
↓
拦焦车→出焦除尘接口翻板机→蓄热式冷却器→ 3700m2脉冲袋式除尘器→出焦除尘烟囱
↓
灰尘进入刮板输送机→粉尘仓→粉尘加湿器→外运
5、装煤除尘系统流程:
出焦除尘的灰尘→预喷涂料仓压缩空气脉冲反吹清灰
↓↓
装煤车→装煤除尘接口翻板阀→1680m2脉冲袋式除尘器→装煤除尘烟囱
↓
灰尘进入刮板输送机→粉尘仓→粉尘加湿器→外运。