细晶钢技术
超细晶化理论及技术与炉外精炼技术

超细晶化理论及技术是21世纪新一代钢铁材料的重要发展方向。
目前,工业生产和广泛应用的低合金钢的屈服强度约为400MPa,抗拉强度约为500MPa,晶粒尺寸约为lOpm。
长期研究和生产实践表明,具有高强度且有高韧度的钢铁材料是最理想的材料,晶粒细化处理是同时提高材料强度和韧度的最有效途径,因此世界各国研究者力争通过对低合金钢进行细晶化的研究,将低合金钢的屈服强度由目前的400MPa级提高到800MPa级,其核心理论和技术是实现钢材的超细晶(或超细组织)。
1997年4月,日本开始了“新世纪结构材料(或超级钢材料)”为期10年的研究计划,提出生产将现有钢材强度翻番和使用寿命翻番为目标的新一代钢材。
之后韩国在1998年启动了“21世纪高性能结构钢”,我国予1998年末确立启动了“新一代钢铁材料重大基础研究”项目(国家973项目),其目标是将现有的普碳钢和低合金钢的强度和寿命提高1倍,同时不降低钢的综合性能。
东亚相差不到1年,设立相同目标的研究项目带动了欧美各国钢铁界竞相参与和重视。
控制超细晶粒钢的组织而使钢强韧化的观点出发,对现有高强度低合金(HSLA)钢晶粒细化的理论和技术进行了探讨。
探讨高强度低合金钢的晶粒细化理论。
1.高强度低合金钢的晶粒细化理论:2.低合金高强钢最重要的力学性能指标是屈服强度GB和韧脆转变温度T。
对于新一代钢铁材料来说,提高其屈服强度民,降低其韧性转变温度T是研究和开发的重点。
提高钢铁材料强度的方法有:固溶强化、析出相强化、弥散强化、形变强化,细晶强化等。
钢铁材料提高强度的途径主要有4条Ⅲ:通过合金元素和间隙元素原子溶解于基体组织产生周溶强化通过加工变形增加位错密度造成钢材承载时位错运动困难(位错强化)通过晶粒细化使位错穿过晶界受阻产生细晶强化通过第二相(一般为M(C,N),析出相或弥散相)使位错发生弓弯和受阻产生析出强化。
各种强化机制的效果。
其中,细晶强化是唯一能同时提高强度和韧性的方法,其它强化方法得到的显微组织都存在强度提高而韧性下降的缺点。
简述细晶强化的原理

简述细晶强化的原理嘿,咱来聊聊细晶强化呗!你知道不,这细晶强化就像是一个神奇的魔法,能让材料变得超级强大。
先说说啥是细晶强化。
简单来讲呢,就是通过把材料的晶粒变得细小,从而让材料的性能大幅提升。
这就好比一支军队,士兵们个个都精明强干,那这支军队的战斗力肯定杠杠的。
材料也是一样,晶粒细小了,材料的强度、硬度、韧性啥的都能蹭蹭往上涨。
那细晶强化到底是咋做到让材料变强的呢?这可就有讲究了。
你想啊,晶粒细小了,晶界就多了。
这晶界就像是一道道坚固的城墙,能阻碍位错的运动。
位错是啥?位错就像是材料内部的小捣蛋鬼,它们的运动可会让材料变形甚至断裂。
有了晶界这道墙,位错就没那么容易乱窜了,材料自然就更结实了。
这就好比在一条马路上,如果没有红绿灯和交警,车辆就会乱开,容易出事故。
但要是有了很多红绿灯和交警,车辆就得规规矩矩地行驶,马路就会更安全。
晶界对于位错来说,就像是红绿灯和交警对于车辆一样。
而且啊,晶粒细小了,材料的变形也会更加均匀。
这就像一群人一起拉一个重物,如果大家力气都差不多,一起使劲,那重物就会很平稳地被拉动。
但如果有的人力气特别大,有的人力气特别小,那重物就会拉得歪歪扭扭的。
材料也是这样,晶粒细小了,各个部分的变形就会比较协调,不容易出现局部变形过大而导致断裂的情况。
细晶强化还有一个好处,就是能提高材料的韧性。
韧性这玩意儿可重要了,就像人的柔韧性一样,柔韧性好的人不容易受伤。
材料的韧性好了,就能承受更大的冲击和振动,不容易断裂。
晶粒细小了,材料在受力的时候,会有更多的晶粒参与变形,就像一群人一起分担压力,这样就不容易一下子就被压垮了。
你说这细晶强化神奇不神奇?它就像是一个默默无闻的英雄,悄悄地让材料变得更强大。
在很多领域,细晶强化都发挥着重要的作用。
比如在航空航天领域,那些高强度的材料很多都是通过细晶强化来实现的。
在汽车制造领域,细晶强化能让汽车更加安全可靠。
在机械制造领域,细晶强化能让机器的寿命更长。
细晶强化的原理

细晶强化的原理
细晶强化是一种材料强化技术,通过在材料结构中形成细小晶粒,提高材料的强度和硬度。
该技术的原理是通过控制材料的热处理过程和添加合适的合金元素,使晶粒尺寸显著减小。
在材料加热过程中,晶粒会开始生长,并逐渐增大。
晶粒的尺寸直接影响材料的力学性能,通常情况下,晶粒尺寸越小,材料的强度和硬度越高。
因此,通过控制加热温度和保温时间,可以限制晶粒生长的速率,使晶粒尺寸保持在一个较小的范围内。
此外,通过添加合适的合金元素,可以进一步限制晶粒的生长。
合金元素可以在晶界处形成所谓的强化相,阻碍晶粒的生长,从而细化晶粒尺寸。
强化相的形成可以通过固溶、析出和相变等方式实现。
细晶强化技术有助于提高材料的强度和硬度,同时还可以改善材料的塑性和耐磨性等性能。
然而,过度细化晶粒可能导致材料的韧性下降,因此在实际应用中需要综合考虑材料的各种性能要求。
总结而言,细晶强化通过控制材料的热处理过程和添加合适的合金元素,使晶粒尺寸减小,从而提高材料的强度和硬度。
这一技术在材料科学和工程领域具有广泛的应用前景。
一文读懂金属材料的晶粒细化方法

蚀性和加⼯性。
轻⾦属的晶粒尺⼨对耐蚀性能的影响亚微⽶的晶粒组织还可以在⾼温下表现出低温超塑性和⾼应变速率超塑性。
晶粒尺⼨对材料流动应⼒的影响2钢铁材料的晶粒细化⼯艺⽬前实现钢铁材料晶粒细化的⽅法主要有:冶⾦处理细化、热处理与加⼯⼯艺、磁场或电场处理细化、机械球磨法、⾮晶晶化法。
凝固组织细化技术由⾦属凝固理论可知,等轴晶的形成条件是:凝固界⾯前沿的液相中有晶核来源,在液相中存在晶核形成和⽣长所需的过冷度。
因⽽对⾦属和合⾦材料凝固组织的细化,⽆外乎是基于以下的基本原理:增加液相中的形核质点,提⾼形核率;降低晶核的长⼤速度或抑制晶核的长⼤;控制结晶前沿的温度分布等。
⽬前,⾦属凝固组织细化⽅法主要有四类:(1)浇注过程和传热条件控制⽅法;(2)化学处理⽅法;(3)机械处理⽅法;(4)外加物理场⽅法。
浇注过程和传热条件控制⽅法浇注过程和传热条件控制⽅法包括浇注⼯艺控制技术、低温浇注、提⾼冷却速度和增加过冷度等。
在铸件浇注过程中,通过控制浇注⼯艺,如进⾏缓慢浇注或合理设置浇⼝等措施,能细化⾦属凝固组织。
除了控制浇注⽅式外,降低浇注过热度,在接近于液相线温度下浇注也是细化凝固组织、扩⼤等轴晶区的有效⽅法。
提⾼冷却速度快速凝固可明显细化⾦属的凝固组织,获得⾮常好的细化效果。
薄板坯连铸⼯艺使铸坯的凝固冷却速率提⾼1~2个数量级,快速凝固使⼆次枝晶臂间距减⼩,最⼩臂间距可达到亚微⽶级。
铸坯⼆次枝晶间距与冷却速率的关系在提⾼冷却速度基础上,通过去除液相中的异质晶核(熔体净化),抑制低过冷度下的形核,使合⾦液获得很⼤过冷度,在⼤过冷度下产⽣爆发式形核,也能细化⾦属凝固组织,该⽅法即为深过冷凝固技术。
熔体的凝固速率与其过冷度有关,过冷度越⼤,凝固速率越快。
化学处理⽅法化学处理的⽅法是指向⾦属熔体中添加少量的化学物质或化学元素。
这种物质⼀般称为孕育剂或变质剂。
该⽅法操作简便,细化效果显著。
但要求孕育剂细⼩且弥散才能有效细化晶粒,否者将影响钢铁材料的性能。
钢的晶粒细化工艺

钢的晶粒细化工艺钢的晶粒细化工艺是通过控制钢的冷却速度和加热温度来实现的。
晶粒细化可以提高钢材的力学性能、耐蚀性和耐磨性等方面的性能。
下面将详细介绍一种常用的钢的晶粒细化工艺。
一、冷却速度控制1. 快速冷却:通过快速冷却可以有效地减小钢材中的晶粒尺寸。
快速冷却可以采用水淬或油淬等方法,将加热至适宜温度的钢材迅速浸入冷却介质中,使其迅速降温。
这种方法适用于碳含量较低的低合金钢。
2. 慢速冷却:对于高碳合金钢或需要保持一定韧性的材料,可采用慢速冷却的方法。
慢速冷却可以通过将加热至适宜温度的钢材放置在空气中自然冷却或用炉内保温等方式实现。
二、加热温度控制1. 高温处理:在高温范围内进行处理可以促进晶粒的长大,适用于需要较大晶粒尺寸的钢材。
通常在1100℃以上进行高温处理,使晶粒迅速长大。
2. 低温处理:在低温范围内进行处理可以抑制晶粒的长大,适用于需要较小晶粒尺寸的钢材。
通常在800℃以下进行低温处理,使晶粒细化。
三、表面处理1. 酸洗:将钢材浸入酸性溶液中进行酸洗可以去除表面氧化层和锈蚀物,提高表面光洁度。
酸洗还能够改善钢材的耐蚀性能。
2. 抛光:通过机械或化学方法将钢材表面进行抛光可以提高表面平整度和光洁度。
四、热处理1. 固溶处理:将加热至固溶温度的钢材保温一段时间后迅速冷却可以实现固溶处理。
固溶处理可以改善钢材的强度和塑性。
2. 淬火处理:将加热至淬火温度的钢材迅速冷却可以实现淬火处理。
淬火处理可以增加钢材的硬度和耐磨性。
3. 回火处理:将淬火后的钢材加热至回火温度并保温一段时间后冷却,可以实现回火处理。
回火处理可以调节钢材的硬度和韧性。
五、细化剂添加1. 稀土元素:稀土元素在钢中具有良好的晶粒细化效果,可以通过添加稀土元素来实现晶粒细化。
稀土元素主要包括镧、铈、钕等。
2. 微合金化:通过添加微量的合金元素如铌、钛、锰等来实现晶粒细化。
这些合金元素能够形成碳化物或氮化物,抑制晶粒长大。
六、机械加工通过机械加工如冷轧、拉拔等可以进一步细化钢材中的晶粒尺寸。
细晶强化原理

细晶强化原理随着科技的不断发展,我们人类的生活也越来越依赖于各种设备和器材。
因此,对于这些设备和器材的性能提升,一直是科技领域的重要发展方向。
在材料科技领域,细晶强化技术就是一种极其有效的方法。
本文将从细晶强化原理入手,为大家讲解这种技术的相关知识。
第一、细晶强化原理:细晶强化技术是一种通过抑制材料的晶粒生长,使晶粒尺寸变得更小而提高材料强度的方法。
细晶强化技术主要包含以下几个方面:1. 通过加工过程套用增强效益。
细晶强化材料的最终性能取决于材料的颗粒尺寸,物理和力学属性,以及晶粒的结晶程度。
加工过程对于抑制晶粒生长,修正和调节晶粒结构也非常重要。
低具有高塑性的金属通常采用冷变形或焊托工艺以保持或延长几何系统的结构,从而产生更多的变形和增强韧性的塑性留存。
这种变形有助于产生更细小的晶粒尺寸,并增加材料的强度。
2. 通过添加合适的合金元素增强材料抵御内部压应力的能力。
合金元素添加可以降低材料内部空隙,从而限制传热损失,减轻机械应力损失,同时增加强度和硬度。
合金材料增加严格的原子构成,增加晶界的能量和位错运动,实现无序晶界的环境侵蚀和防腐功能。
3. 通过不同的表面处理方法提高材料强度。
表面处理方法包括沉积层,化学夹层和氧化层等多种形式。
这些表面涂层技术具有防止表面化学反应和腐蚀的作用,既可以用来加强材料的结构稳定性,还有助于增强材料的强度和硬度。
第二、细晶强化技术的应用:细晶强化技术主要应用于以下几个领域:1. 材料加工领域。
在材料加工的过程中,可以使用细晶强化技术来提高材料的硬度和强度,从而增加其使用寿命和耐久性。
2. 电子领域。
在电子领域,细晶强化技术可以帮助电子设备更加轻薄化,同时提高设备的耐用性和可靠性。
3. 航空航天领域。
在航空航天领域,细晶强化技术可以用于制造高性能的材料。
这些材料具有极高的强度和硬度,可以为航空航天领域提供支持。
第三、总结:细晶强化技术是一种非常有效的材料工程技术。
通过抑制材料的晶粒生长,在材料加工中添加合适的合金元素、采用不同的表面处理方法等多种手段,可以提高材料的硬度和强度,增加其使用寿命和耐久性。
细晶强化的概念

细晶强化的概念
细晶强化是一种新型的铸态加工技术,它能够改善金属材料的力学性能。
它的原理是,在材料中改变细微的晶粒,使得晶粒结构更紧密,形成细小的晶粒内强化结构,从而提高材
料的强度。
细晶强化的技术已经被广泛应用于航空航天、汽车、机械制造等行业中。
在航空航天领域,已经成功制备出一种超级强力钢,用于制造飞机发动机叶片等大型结构零件。
在汽车行业,细晶强化技术可以制备出耐用的材料,可以比传统铸造技术制备出更强韧的零件,而且可以降低整车重量,用于整车空气动力学等改进。
另外,细晶强化技术在机械制造领域也有着重要的应用,可以制备出更加精密的零件,且
能够抵抗强大的磨擦、弯曲及冲击载荷,使产品更加精致耐用。
此外,这种技术还可以更
有效地利用资源,减少产品制造所需物料及人工成本。
总而言之,细晶强化技术是一项重要的工业技术,能够改善金属材料的力学性能,并在航空航天、汽车等行业中得到了广泛的应用,降低了部件的成本,提高了产品的性能。
它的
用途非常广泛,不仅能够改善材料的强度,更能够更有效地利用资源。
细晶强化的原理及应用
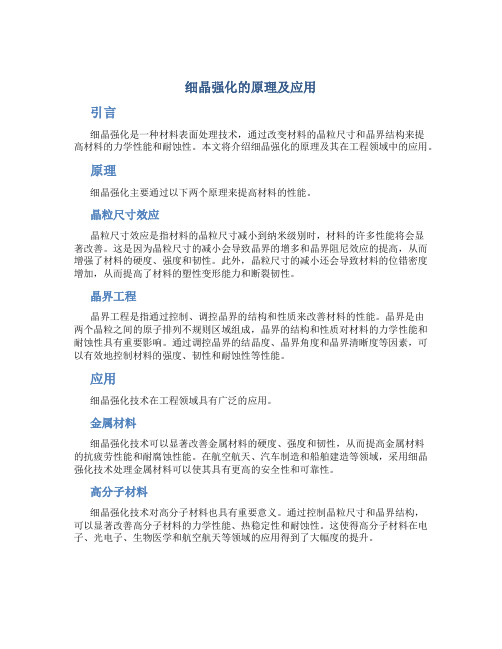
细晶强化的原理及应用引言细晶强化是一种材料表面处理技术,通过改变材料的晶粒尺寸和晶界结构来提高材料的力学性能和耐蚀性。
本文将介绍细晶强化的原理及其在工程领域中的应用。
原理细晶强化主要通过以下两个原理来提高材料的性能。
晶粒尺寸效应晶粒尺寸效应是指材料的晶粒尺寸减小到纳米级别时,材料的许多性能将会显著改善。
这是因为晶粒尺寸的减小会导致晶界的增多和晶界阻尼效应的提高,从而增强了材料的硬度、强度和韧性。
此外,晶粒尺寸的减小还会导致材料的位错密度增加,从而提高了材料的塑性变形能力和断裂韧性。
晶界工程晶界工程是指通过控制、调控晶界的结构和性质来改善材料的性能。
晶界是由两个晶粒之间的原子排列不规则区域组成,晶界的结构和性质对材料的力学性能和耐蚀性具有重要影响。
通过调控晶界的结晶度、晶界角度和晶界清晰度等因素,可以有效地控制材料的强度、韧性和耐蚀性等性能。
应用细晶强化技术在工程领域具有广泛的应用。
金属材料细晶强化技术可以显著改善金属材料的硬度、强度和韧性,从而提高金属材料的抗疲劳性能和耐腐蚀性能。
在航空航天、汽车制造和船舶建造等领域,采用细晶强化技术处理金属材料可以使其具有更高的安全性和可靠性。
高分子材料细晶强化技术对高分子材料也具有重要意义。
通过控制晶粒尺寸和晶界结构,可以显著改善高分子材料的力学性能、热稳定性和耐蚀性。
这使得高分子材料在电子、光电子、生物医学和航空航天等领域的应用得到了大幅度的提升。
硅材料细晶强化技术也被广泛应用于硅材料中。
硅材料在电子器件中起着重要作用,而细晶强化技术可以显著提高硅材料的机械强度和热稳定性,从而提高电子器件的性能和可靠性。
陶瓷材料细晶强化技术对陶瓷材料也起到了重要作用。
陶瓷材料在航空航天、化工和电子等领域中广泛应用,而通过细晶强化技术可以改善陶瓷材料的耐热性、耐蚀性和耐磨性。
这使得陶瓷材料可以在极端的环境条件下发挥更好的性能。
结论细晶强化技术是一种有效提高材料性能的表面处理技术。
- 1、下载文档前请自行甄别文档内容的完整性,平台不提供额外的编辑、内容补充、找答案等附加服务。
- 2、"仅部分预览"的文档,不可在线预览部分如存在完整性等问题,可反馈申请退款(可完整预览的文档不适用该条件!)。
- 3、如文档侵犯您的权益,请联系客服反馈,我们会尽快为您处理(人工客服工作时间:9:00-18:30)。
第四章细晶钢及超细晶钢及其生产技术钢铁材料作为人类使用的最传统和最主要的结构材料,其经济性和性能多样性的结合是目前任何一类工程材料难以媲美的,并在今后相当长的时间内仍将发挥主导作用。
但也应该看到,钢铁材料的生产正面临着能源、资源和环境问题的巨大压力,同时也面临着其它材料的激烈竞争。
因此,从上世纪末开始,世界上许多国家(如日本、韩国、中国、欧盟等)陆续启动了旨在大幅度提高钢材的强韧性和使用寿命的大型科研项目,掀起了新一轮钢铁材料研究的热潮[1-3]。
我国于1999年正式启动了“新一代钢铁材料的重大基础研究”项目,其主要目标是保证生产经济性的前提下,使钢材的强度和韧性提高一倍,或强度、韧性没有明显增加,但其使用寿命提高一倍[1]。
提高材料强度的方法有多种,但晶粒细化是唯一既能提高强度又能改善韧性的方法,其它方法均会损害韧性。
因此,超细晶组织应是新一代钢最主要的特征。
根据Hall-Petch关系,低碳碳素钢的屈服强度从目前的200MPa级提高到400MPa级,其铁素体晶粒尺寸应细化至3-5μm;而对于低合金钢和微合金钢,其屈服强度从目前的400MPa级提高到800MPa级,铁素体晶粒应细化至1μm或更小。
这是新一代钢所追求的目标[1]。
自上世纪六十年代以来,人们一直致力于钢材晶粒细化的研究和开发工作,先后开发出未再结晶控轧(传统控轧)、再结晶控轧以及控制冷却等晶粒细化工艺,并在实际中得以广泛应用[4]。
但是,运用上述工艺获得的铁素体最小晶粒尺寸,对于碳素钢为10μm,而对于微合金钢为4~5μm,其屈服强度分别在200~300MPa级和400~500MPa级[4]。
自上世纪九十年代开始,一些新的晶粒细化方法又相继问世,如超大塑性变形、极限热机械加工等[34, 39-48],铁素体晶粒可细化至亚微米甚至纳米级,材料的强度大幅度提高。
但是,这些方法目前仅能在实验室中实现,而且制备出的材料尺寸小,成本高,不符合我国新一代钢低成本、大规模生产的要求。
上世纪八十年代初(1981),R. Priestner首次报道了低碳钢轧制时轧缝中(roll gap)发生的γ→α相变,并称之为应变诱导铁素体相变(Strain-induced Transformation to Ferrite)[52];Yada等的工作表明,通过1073K多道次变形,可将普通C-Mn钢的铁素体晶粒尺寸细化到1-3μm,晶粒细化的原因被认为是变形诱导相变(Deformation Induced Transformation)和铁素体动态再结晶综合作用的结果[54](1987)。
此后,澳大利亚的Hodgoson等[59](1992),韩国的Lee等[75](1995)、W.Y. Choo等[3](1998)相继报道了类似的现象,并分别称其为应变诱导相变(Strain Induced Transformation)和应变诱导动态相变(Strain Induced Dynamic Transformation)。
尽管上述名称各异,研究方法也不尽相同,但其实质相同:(1)强调了相变发生于变形过程中,而不是变形之后的冷却过程中;(2)强调了可以形成超细铁素体晶粒。
我国新一代钢铁材料的重大基础研究借鉴了上述学术思想,但深度和广度有了进一步提高。
采用变形诱导铁素体相变(Deformation Induced Ferrite Transformation)或变形强化相变(Deformation Enhanced Transformation),我国已分别将碳素钢和低碳微合金钢的铁素体晶粒尺寸细化到3μm和<1μm,屈服强度分别提高到400MPa和800MPa以上[89, 94]。
与其它晶粒超细化的方法相比,变形诱导铁素体相变工艺的最大优势在于它与现行钢铁生产工艺流程接近,在现有轧制设备上或经过一定改造的设备上就可以实现,因而具有广阔的发展前景。
但这一技术真正走向成熟,有赖于基础研究的深入进行。
目前的基础研究大多集中于碳素钢和C-Mn钢,而对于低碳钢微合金钢变形诱导铁素体相变问题的研究还不够充分。
本报告将主要围绕低碳微合金钢的变形诱导铁素体相变开展工作,以期阐明其组织演变特点、变形参数和化学成分的影响规律以及热力学和动力学基础,为DIFT技术在这类钢中的应用提供理论依据。
1.2 低碳钢(微合金钢)晶粒细化技术和理论的研究进展纵观低碳钢晶粒细化问题的研究,大致可分为两个阶段。
第一阶段是上世纪六十年代初开始的以控轧控冷工艺为核心的热机械加工技术和相关理论问题的研究。
这一研究在七十年代达到高潮,进入八十年代有所减少,但一直延续至今。
这一阶段系统地研究了奥氏体的再结晶问题、微合金碳氮化物的溶解与析出以及奥氏体再结晶的耦合关系、铁素体的形核和长大问题等,确立了未再结晶区控轧和再结晶控轧以及控制冷却工艺并在实际中大量使用[4-21]。
进入八十年代中后期特别是九十年代以后,超细晶的制备技术和理论研究受到很大重视,先后出现了变形诱导铁素体相变加工[54]、极限热机械加工[34, 35]、超大塑性变形[39-48]、多向变形[28, 33]等超细晶制备新技术,铁素体晶粒细化到微米亚微米级,甚至纳米级。
这是低碳钢晶粒细化问题研究的第二阶段。
上世纪九十年代后期世界上一些国家启动的“超细晶粒钢”研究,将这一阶段推向高潮。
下面首先简要地回顾传统热机械加工技术(控轧控冷)的研究概况(第一阶段),然后重点介绍近些年发展起来晶粒超细化的新技术和新理论(第二阶段)。
变形诱导铁素体相变的研究进展将在1.3节中单独介绍。
1.2.1 传统热机械加工技术(控轧控冷)的研究概述文献[4]图示了控制轧制包括的三个阶段,以及每个阶段奥氏体发生的组织变化(图1.1)。
Ⅰ阶段:奥氏体再结晶区变形。
早期轧机由于轧制压下量较小,奥氏体通过图1.1控制轧制的三个阶段及奥氏体组织变化[4]反复的静态再结晶促使其晶粒细化。
现代轧机由于轧制压下量较大,轧制中可能发生动态再结晶,而在轧后则可能发生亚动态再结晶。
亚动态再结晶与静态再结晶的差别在于:前者速率较快,且再结晶晶粒尺寸仅取决于Zener-Hollomon 参数,与原始奥氏体晶粒尺寸和变形量无关;而后者速率较慢,再结晶晶粒尺寸与原始奥氏体晶粒尺寸和变形量有关[4, 23, 24]。
文献[4, 9]指出,在晶界形核情况下,铁素体晶粒尺寸D α与再结晶奥氏体晶粒尺寸D γ的关系为:3131612γααπD I D s --⎪⎪⎭⎫ ⎝⎛⎪⎭⎫ ⎝⎛= (1.1) 式中I s 为铁素体在奥氏体晶界上的形核率,α为抛物线速率常数。
由上式可见,奥氏体的再结晶细化,会导致铁素体晶粒的细化,但同时应该看到,其细化效果并不十分显著。
例如,若奥氏体晶粒尺寸细化1/8,铁素体晶粒仅细化1/2。
Ⅱ阶段:奥氏体未再结晶区变形。
奥氏体晶粒被压扁,晶界面积增加,同时晶内引入位错、变形带(孪晶界)等缺陷,使铁素体形核位置进一步增加。
这是铁素体晶粒细化的重要原因之一。
铁素体晶粒细化的另一原因是变形改变了奥氏体晶界的状态,使铁素体在奥氏体晶界上的形核率大大增加。
对造成上述情况的原因存在着不同的解释。
Khlestov 等认为变形使奥氏体晶界附近原子的排列更加无序,提高了晶界能,从而显著提高了铁素体的形核率[15];Tamura 等认为变形在奥氏体晶界上引入微台阶,铁素体在微台阶上的临界形核功下降为晶界上临界形核功的θ/π倍,从而提高了形核率[4];Sandberg 和Robert 认为变形造成奥氏体晶界局部迁移,形成晶界凸起,在这些位置铁素体的临界形核功降低,导致形核率的增加[16];而Amin 等人认为变形奥氏体晶界附近存在很大的应变梯度(或位错密度梯度),位错回复形成亚晶,从晶界到晶内亚晶尺寸逐渐减小;铁素体在亚晶界上形核、长大之至接触,在晶界附近形成了细小的铁素体晶粒带[18]。
未再结晶奥氏体相变的晶粒细化效果要好于再结晶奥氏体[4,5]。
图1.2示出了由不同状态的奥氏体(未再结晶奥氏体和再结晶奥氏体),所获得的铁素体晶粒尺寸与奥氏体有效晶界面积的关系[16]。
可以看到,在相同的S V 下,由未再结晶奥氏体得到的铁素体晶粒更细。
其原因在于变形奥氏体晶界形核率的提高。
为提高奥氏体未再结晶温度,扩大未再结晶区的温度范围,需要加入微合金元素。
研究表明,Nb 、V 、Ti 、Al 等元素都会程度不同的提高奥氏体未再结晶温度,但Nb 的作用效果最明显[4,5,19]。
关于微合金元素推迟奥氏体再结晶的作用机理,普遍认为有两种:一是固溶微合金元素的溶质拖曳作用,二是微合金碳氮化物的质点钉扎作用。
它们均会阻碍位错的运动和晶界(亚晶界)的迁移,从而推迟再结晶的发生[4, 5]。
Ⅲ阶段:奥氏体和铁素体双相区变形。
一方面奥氏体晶粒被压扁,晶内引入大量缺陷;另一方面,铁素体在较小变形量下发生回复,形成亚晶结构,而在大变形条件下发生连续动态再结晶,形成被大角晶界所分隔的晶粒[99]。
在冷却过程中,变形奥氏体转变为铁素体,但由于第二相铁素体的存在,相变铁素体的长大受到阻碍,获得的晶粒尺寸较小[4]。
控轧之后的控制冷却对于铁素体的晶粒细化也非常重要。
铁素体晶粒尺寸随冷速的增加先是减小,然后逐渐达到一稳定值。
铁素体晶粒细化的原因有二:一是冷速增加,相变过冷度和驱动力增大,形核率提高[4,5];二是铁素体晶粒的粗化过程因冷速快而受到抑制[26]。
尽管控轧控冷工艺与普通热轧相比,细化晶粒效果有显著改善,但仍很难获得超细晶。
这一点可用Bengochea 等提出的经验关系式[13]来说明:)))015.0exp(1(4.1335.4)(5.01(2/147.0γαεd T d --++-=- (1.2) 式中,d α为铁素体晶粒尺寸,d γ为奥氏体晶粒尺寸,ε为奥氏体未再结晶区的累积变形量,T为冷速。
根据该式,作出了铁素体晶粒尺寸与累积变形量和冷速的关系图(图1.3)。
在实际的控制轧制中,奥氏体未再结晶区的累积变形量一般不大于1,而再结晶奥氏体的晶粒尺寸一般不小于30μm ,由此得到传统控轧获得的最小铁素体晶粒尺寸为4~5μm ,这与实际生产的结果相符合。
另外由图还可看到,传统控轧要获得1μm 的超细晶,累积变形量应不小于3.5,说明了大变形对于获得超细晶的重要性。
实际上近年来关于超细晶粒钢生产技术的研究中,许多都强调了大变形的作用。
图1.2由不同状态奥氏体得到的铁素体晶粒尺寸与有效晶界面积的关系[16]1.2.2 低碳钢晶粒超细化研究的新进展1.2.2.1 极限热机械加工(Ultimate Use of TMCP) 技术及理论极限热机械加工的概念是由日本“超级金属”研究项目首先提出的,目标是获得1μm 左右的超细晶[34,35]。