剧烈塑性变形获得的超细晶材料
超细晶材料塑性变形制备方法分析

累积 轧 制 一 复合 法 ( A c c u mu l a t i v e Ro l l Bo n d i n g , ARB ) 。
为了实现 块体 超细 晶材料 的工业化 生产, S a i t o 提 出 了ARB方
高 压 扭 曲变 形 法 ( Hi g h P r e s s u r e a n d T o r s i o n , HP T ) 。 它 可以用来制备超 细晶金属 、 合金 , 复合材料和半导体 器件, 通 常
B r o a d Di s c u s s Commu n 计 y 博 论 社 区
超 细 晶材 料塑 性 变 形 制 备方法 分析
张 雅 妮 西 安石 油 大学 材 料 科学 与 工程 学 院
超 细 晶 材 料 是 指 在 三 维 空 间 尺寸 至 少 有一 维 是 处于 亚 微 米
E C AP 变 形 己 经 成 功 地 制 备 了Al 和 Al 合 金, Mg 合 金, C u 和C u 合金, Ti 和 Ti 合 金 以 及 超 细 晶 钢 。目前 EC AP 制 备 试 样 尺 寸
方 法有高压 扭曲变形 法、 多次锻 压法、 循 环 挤 压 一墩 粗 法 、 等径
较高 。 固 相 法 中 的 非 晶 晶化 技 术 由于 受 到 合 金 非 晶 形 成 能 力 大
等径弯曲通道 变形法 ( Equ a l Cha n ne l An gUl a r
P r e s s i n g, E C AP ) 。 该 方 法 通 过 利 用 由两 个 相 交 的 等 径 通 道 组 成 的模 具 使金 属 获得大 的塑 性剪性 变 形 , 试 样 变 形 前 后 的 形 状 和 尺 寸 不 发 生 改 变 ,因 而 可 以 进 行 多 次 变 形 。 所 制 备 出 的 超 细 晶 材 料 的 性 能 主 要 由 变 形 途 径 、变 形 道 次 , 模 具 内角 , 变 形 过 程 中的 润 滑 、 变 形 速 率 和 变 形 温 度 等 决 定 。目前 , 采 用
剧烈塑性变形:不仅是晶粒细化
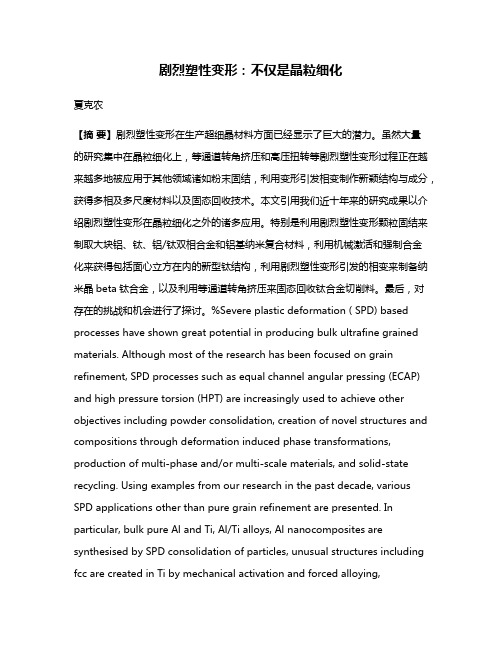
剧烈塑性变形:不仅是晶粒细化夏克农【摘要】剧烈塑性变形在生产超细晶材料方面已经显示了巨大的潜力。
虽然大量的研究集中在晶粒细化上,等通道转角挤压和高压扭转等剧烈塑性变形过程正在越来越多地被应用于其他领域诸如粉末固结,利用变形引发相变制作新颖结构与成分,获得多相及多尺度材料以及固态回收技术。
本文引用我们近十年来的研究成果以介绍剧烈塑性变形在晶粒细化之外的诸多应用。
特别是利用剧烈塑性变形颗粒固结来制取大块铝、钛、铝/钛双相合金和铝基纳米复合材料,利用机械激活和强制合金化来获得包括面心立方在内的新型钛结构,利用剧烈塑性变形引发的相变来制备纳米晶beta钛合金,以及利用等通道转角挤压来固态回收钛合金切削料。
最后,对存在的挑战和机会进行了探讨。
%Severe plastic deformation ( SPD) based processes have shown great potential in producing bulk ultrafine grained materials. Although most of the research has been focused on grain refinement, SPD processes such as equal channel angular pressing (ECAP) and high pressure torsion (HPT) are increasingly used to achieve other objectives including powder consolidation, creation of novel structures and compositions through deformation induced phase transformations, production of multi-phase and/or multi-scale materials, and solid-state recycling. Using examples from our research in the past decade, various SPD applications other than pure grain refinement are presented. In particular, bulk pure Al and Ti, Al/Ti alloys, Al nanocomposites are synthesised by SPD consolidation of particles, unusual structures including fcc are created in Ti by mechanical activation and forced alloying,nanocrystalline beta Ti alloys are produced with the assistance of SPD induced phase transformation, and Ti machining chips are recycled in the solid state. Challenges and opportunities are discussed.【期刊名称】《材料与冶金学报》【年(卷),期】2015(000)004【总页数】6页(P239-244)【关键词】剧烈塑性变形;等通道转角挤压;高压扭转;粉末固结;相变【作者】夏克农【作者单位】墨尔本大学机械工程学院,澳大利亚维多利亚3010【正文语种】中文【中图分类】TG146.2The last two decades haveseena dramatic rise in interest in the use of severe deformation techniques to produce ultra-fine grained materials. The potential benefits of submicron-grained aluminium alloys, such as enhanced strength and superplasticity, are well-documented[1-2], but are offset bysome negative properties, such asa tendency for low stable elongation and shear localization[3]. Several processing methods have been shown to be effective for the production of ultra-fine grained metals, which include Equal Channel Angular Extrusion (ECAE) and Accumulative Roll Bonding (ARB)[4].More recently, continuous variants of the ECAE process have been developed, which in the future will allow morecommercially viable production[5]. All of these techniques involve deformation to ultra-high plastic strains (typically a true strain of 6-10) without a net billet shape change, which would otherwise result in a foil or filament. The deformation history in such processes is frequently complex, sensitive to the tooling and friction conditions and does not generally involve a constant strain path. This is especially true for the ECAE process (e.g[6-8]).Submicron grained material, produced by a severe plastic deformation process,is defined as requiring the average spacing of high angle boundaries (HABs), misorientated by >15(°), to be less than 1 μm in all directions andthe fraction of HAB area to be greater than 70%[9]. This definition was originally proposed as in many cases materials deformed by severe deformation techniques are simply called submicron grained, based on measurement of their cell size in the TEM, without discriminating between high and low angle boundaries[10]. Understanding how deformation structures evolve to ultra-high strains and the grain refinement mechanisms involved is thus of considerable interest not least because,as will be seenwith certain material and deformation route combinations, ultra-fine grained materials, according to the above definition, are not obtainedand the materials produced still predominantly contain subgrains[11].The general behaviour of the deformation structure evolution using the ECAE process has been previously reported, particularly using route A (no billet rotation)[9-12]. The increase in HAB area with strain originates fromgrain subdivision processes, such as deformation banding via orientation splitting and micro- shearbanding (which predominantly occurs at low stains <3), and the extension of grain boundary area with strain.The importance of orientation splitting and shear banding has been noted by other researchers[7,13-14]. With deformation processes involving continuous material element distortion, (e.g. ECAE -Route A) theHABs rotate and compress in spacing with strain to form a lamellar structure.The spacing of the lamellar boundaries reduces until it converges with the subgrain size forming thin ribbon grains, by a strain of 5~7. At higher strains the microstructure refines by the break-up of the ribbon grains into lower aspect ratio submicron grains.This occurs inhomogeneously and starts to develop locally in bands at strains as low asεvm~4[9,12]. The high-strain breakup and spheroidisation of lamellar HAB structures has been attributed to heterogeneity in plastic flow, diffuse shear banding, and dynamic recovery/recrystallisation[9,12]. Where severe plastic deformation involves no net element shape change, due to a redundant strain, the development of the deformed state is less well understood, but grain refinement predominately occurs by deformation banding and shear banding[9, 12, 14-16].Here results are presented that use a selection of model Al-alloys, processing routes, and die angles, to clarify in more detail some important aspects of the deformation structure development during ECAE processing. In par ticular, the role of the die’s shear plane orientation in the formation of cell bands (or cell blocks) and shear bands, along with orientationsplitting, at low strainsis investigated, as well asif a steady state is ultimately achieved at ultra high strains. It is worth noting that in terms of developing a more complete understanding of the general development of deformation structures in metals ECAE offers certain advantages compared to plane strain deformation, astheoretically under ideal conditions there is one principal shear plane with an orientation defined by the die geometry, and this makes it easier to determine the crystallographic, or non-crystallographic, alignment of features such as cell bands and microshear bands.All the results presented were obtained by ECAE using a split die held in a hydraulic clamp, so that extrusion could be stopped partway through a cycle and samples extracted. Deformation was carried out at room temperature, on well lubricated 15 mm diameter by 100 mm billets, using a ram speed of 50 mm/min and either a 90 or 120(°) die (=2φ), with only a small blend radius between the die channels. This restricted the deformation zone to a narrow fan of less than 2 mm in width about the theoretical shear plane[5]. Data from three materials is shown; a single phase Al-0.1%Mg, a fine 20 nm Al3Sc dispersiod containing (Vf=0.004)Al-Sc alloy and AA8079, which contained coarse 2 μm Al13Fe4, particles(Vf=0.025), deformed by route A and BC. Most data shown below is for the Al-0.1%Mg alloy, except where comparisons are made to example data from the other materials. Full details of the materials and their pre-processing can be found in[12,17-18]. EBSD orientation maps were acquired from samples at different strain levels, using a high resolutionFEGSEM.Data analysis was carried out using VMAP, an in-house software package.HABs were defined as having misorientations ≥ 15(°) and low-angle boundaries (LABs) misorientations<15(°). A minimum misorientation cut-off of 1.5(°) was normally used to elimina te excessive misorientation noise.2.1 Cell bandsAfter the first pass of ECAE deformation the most characteristic feature of the fine scale deformation microstructure in dilute Al-alloys with a reasonable initial grain size (>10 μm) are aligned dense disl ocation walls (DDWs) 0.7~1.5 μm in spacing (Fig.1). Similar features have been widely reported in rolling and ECAE[9-12,19-20]. These structures have been termed ‘cell blocks’, where they have been suggested to represent volume elements operating on a similar set of slip systems, or are differentiated from their neighbouring blocks in terms of different local strains,and have been claimed to show preferential alignment with the active {111} slip plane[20]. However, it has been shown recently that they are probably not crystallographically related and tend to align with the principle shear direction (e.g.36(°) to the rolling plane)[19]. In idealized ECAP deformation with a narrow deformation zone, the principal shear plane is theoretically the plane of intersection of the two die channels, and this allows a simple test of these two ideas,although pure shear does not generally occur in ECAE due to die friction and spreading of the deformation zone through an arc, which introduces other minor strain components[6-7]. Nevertheless, after 1 ECAE pass in all materials examinedthe DDWsin every grain were always found to be strongly aligned with the die shear plane across the centre of the billet, for both 90(°) and 120(°) dies, at 45(°) and 60(°) to ED respectively (Fig.1).Another set of cell bands was also seen within some grains aligned with the extrusion direction, which may reflect the presence of other strain components in imperfect ECAE shear. Slip plane trace analysis clearly showed that there was no preferential {111} alignment, as can be seen from the example pole figure in Fig.1c. The DDWs are typically only one cell wide, and contain very low angle transverse boundaries. Such structures are thus more accurately described as cell bands, as proposed by Humphreys and Hurley[19], and are formed by the coalescence of dislocation networks into sheets by climbontoplanes where there is no out of plane shear. The average misorientation across the cell bands was 3~4(°) for the 120(°) die and 4~5(°) for the 90(°) die, w hich reflects the higher strain intensity of the lower die angle.No new HABs were formed at cell band boundaries, except where there was observed to be an underlying orientation gradient, either due to grain interactions, or deformation banding (see Fig.4b).The cell band structure thus initially develops independently of orientations splitting, which is driven by crystal instability.At high strains, when the minimum grain fragment HAB spacing reduces to <5 μm no regular cell bands are seen[9]and irregular subgrains are found, because when the crystal fragment size reduces below a certain level slip becomes less well defined with respect to the macroscopic shear stress, due to grain to grain interactions. A similar result has been reported fordeformation structures in fine grained materials by Jazaeri and Humphreys[21].2.2 Shear bandsIn the dilute alloys studied, microshear bands werenot seen in the first pass. In the second pass with ECAE processing there is always a strain path change which depends on the die angle and processing route[8]. Except for deformation in route C, it represents a Bauschinger type reversal and involves a rotation of the idealized shear plane and the activation of latent slip systems.For route A, the theoretical shear planealterna tes byπ-2φevery cycle and should thus intercept the cell bands by 60(°) or 90(°) , with the 120(°) and 90(°) dies respectively. Such strain path changes are known to promote shear banding as the collapse of the lamellar DDWs barriers forming the cell bands, when subjected to an orthogonal shear, can lead to transient flow softening[22]. In Fig.2 after the 2ndECAE pass microshear bands, only one cell in width, can now be seen cutting through the cell band structure aligned closely with the die’s theoretical shear plane in both dies. Their average misorientation thickness and spacing are given in table 1. The cell band substructure has rotated towards the extrusion direction 25(°) and 15(°) to ED for the 120(°) and 90(°) die respectively, from the expected 60 and 45 degrees, due to the highly localized shear within the microshear bands, but the alignment is spread and depends on the local shear band intensity. The cell band misorientations have remained at only 4~6(°) . Some microshear bands were seen in packet s of two, to five, bands and extended across grain boundaries, although theydid not generally propagate across the whole sample. It can thus be considered that there is a mixture of inter-granular microshear bands and microshear packets that are developing into trans-granular macroshear bands. In comparison in the same alloy.Single microshear bands are more commonly observed in rolling at similar strains, due to the lower intensity of the shear, and lack of an abrupt strain path change[19]. Substantial lattice rotationsoccur within the shear bands of 6~30(°) (table 1) around TD towards the extrusion direction,which readily generates new HAB segments across their boundaries. The microshear bands were more regularly distributed and slightly higher in misorie ntation with the 90(°) than the 120(°) die, which reflects the higher strain intensity each pass. More intense and regular microshear bands were found within larger stable crystal volumes, that often coincided with when a {111} crystallographic plane aligned with the dies shear plane, compared to areas subdivided by more closely spaced deformation bands, which reduces the intensity of intergranualmicroshear bands by restricting the slip line length.The microshear bands have mediummisorientations and are permanent features of the deformation structure.Once formed, with route A, they undergo a rigid-body rotation towards the extrusion direction on subsequent cycles and their spacing is compressed[9,12]. This process, along with orientation splitting, is eventually responsible for the formation of lamellar boundary structures and the elongated “ribbon grains” observed at high strains[9,12]. At intermediate strains it causes a complexmicrostructure to develop by subsequent micro/shear bands kinking the rotated cell bands and earlier microshear bands. Micro/shear bands are also observed to form by route Bc, but their comparative intensity has not yet been quantified. However, they are less likely to form with processes where there is a direct Bauschinger strain path reversal[22], as typified by route C. The importance of micro/shear bands to grain refinement in ECAE,at low strains, can be seen from the much higher rate of HAB area generation in a single phase alloy(Fig.3a), relative to that in an Al-0.2%Sc alloy, where theirformation is suppressed because of slip homogenisaiton due to the presence of a high density of non-shearble fine particles (Fig.2d)[16].Coarse macroscopictrans-billet shear banding can also be observed to occur in ECAE under unstable deformation conditions[6]. This particularly occurs in aluminium alloys when the material has been heavily work hardened and contains high levels of Mg. Ultimately, this results in fracture of the billet, and can not thus be exploited to produce a homogeneous ultra-fine grain structure.Diffuse trans-granular shear bands at high strains havealso been observed to contribute to the breakup of ribbongrains,produced by route A, into ultrafine grains[9,12].2.3 Orientation splittingThe formation of deformation bands in unstable grains, which subdivide into slab morphology volumes and rotate towards diverging end orientations, that define the deformation texture for a given deformation mode, is a well-known phenomenon[23]. The pattern of deformationbanding within a given grain appears to become established at relatively low strains, and occurs in ECAE during the first pass as a grain enters the dies deformation zone (Fig.4a). High angle misorientationsare generated between each band and typically alternate for regular bands as shown Fig.4c. In the first pass the DDWs that make up the cell band boundaries remain aligned with the shear plane, but where they coincide with steep orientation gradients narrow transition bands form between the deformation bands with high HAB segments. This can occur irregularly and form closely spaced parallel HAB segments as can be seen in area C in Fig.4a. The misorientation features of these HAG segments can be seen in Fig.4d. Typically, two length scales of deformation banding were found (table 2), coarse primary deformation bands that have high misorientations of 30~55(°)(Fig.4a A and B) and a spacing of 20~30 μm (after the first pass) and much finer secondary deformation bands, that can form within the primary bands in some grains with spacin gs as fine as 5 μm (Fig.4a C). In subsequent passes with route A, these regions rapidly develop into local bands containing a high density of lamellar HABs. In the current work sufficient statistical data has not yet been obtained to correlate general crystal orientations to grain stability in such regions. However, both regular coarse and irregular fine deformation bands were found to rotate towards a stable orientation defined by the end texture of the material, which is (111)[-211] for both 90(°) and 120(°) dies. Fig.4b shows that deformation bands A, B and C all evolve towards (111)[-211], regardless of their initial orientations. However, theoretical analysis by Barnett andMontheillet[24]has suggested that, due to the material spin in simple shear, which results in no truly stable final deformation texture, orientation splitting is more significant than in other deformation modes, such as plane strain.Despite reorientation of the shear plane, on subsequent ECAE passes by route A the pattern of deformation banding formed in the first pass does not appear to change, (i.e. no more subdivision occurs), although the band width does reduce due to continued element distortion, and the misrorentation across bands increases resulting in the formation of continuous HABs at secondary bands. Similarly, with route Bc where there is no continuous element distortion, again the pattern of deformation banding developed after the first pass appears to largely remain during subsequent passes, unless the structure is destroyed by intense shear banding, such as that seen in high Mg content alloys. Crystal plasticity simulations have shown similar results, in that the pattern of orientation subdivision is generally determined at relatively low strains[13].Cell bands can also develop HABs in regions near grain boundary surfaces and triple points, in the original grain structure, due to high local orientation gradients resulting from grain-grain interactions[9]. New HABs can also be promoted by orientation gradients associated with coarse second phase particles, within their deformation zones and through particle stimulated deformation bands. This greatly increases the rate of grain refinement and reduces the strain required to produce an ultra-fine grain structure[17], as can be seen from Fig.3a.2.4 Importance of geometric boundary compressionIn most conventional deformation processes continuous distortion of a material element occurs. This leads to an increase in grain boundary area simply due to the geometric shape change imposed on a grain[23]. In ECAE deformation continuous element distortion does take place by route A and BA, but not by Route Bc or C. The grain subdivision mechanisms of orientation splitting,and repeated micro/shear banding at low strains and transgranularshear banding at high strains,on alternate shear planes, are therefore primarily responsible for grain refinement by Route BC. With route A, as well as orientation splitting and shear banding resulting in grain subdivision there is also an increase in HAB area due to the geometric requirements of shear associated with the development of a fibrous deformation structure, which results in a lamellar HAB structure at strains grater than 3~4. At higher strains of 5~7 the lamellar boundary spacing approaches the subgrain size and ribbon grains are formed which subsequently breakup and reduce in aspect ratio to form submicron grains at ultra-high strains[8,12]. In Fig.3b the measured increase in HAB area with strain,for different original grain sizes, is compared to that calculated from the geometric increase in HAB area, based on the theoretically distortion of grains that deform homogenously. From Fig.3b it can be seen that at low strains the geometric increase in HAB area becomes extremely important when the initi al grain size reduces below 5 μm, and at high strains all the data converges with the predicted behaviour for an initial grain size of 10 μm. Jazaeri and Humphreys[25]have shown that in rollingall new HAB area can be attributed to the geometric increase in boundary area for grain sizes below 10~15 μm. However, for smaller initial grain sizes the reduction in HAB spacing falls below that expected from the geometrical requirements of strain, which suggests a minimum HAB spacing is approached that is controlled by dynamic recovery. An effective limit to grain refinement is also observed in ECAE processing, when the grain size converges with the subgrain size, as will be shown below.2.5 Severely deformed microstructuresWithdeformation paths that do not involve a net element shape change, such as route BC, if deformation occurs homogeneously there is no geometric requirement for a compression of the boundary spacing, or increase in HAB area with strain. However, grain subdivision processes will still result in grain refinement and a geometric increase in boundary area can still occur locally if deformation occurs heterogeneously within intense macroshear bands.Thus, at ultra high strains by ECAE, both routes A and BCcan produce ultra-fine grained materials, but result in distinctively differentdeformation structures, examples of which are given in Fig.5. Materials produced by route A,with continuous element distortion, (Fig.5a, b) have fibrous ultra-fine grain structures, which tend to be quite homogeneous in the transverse direction, but have a lower average boundary misorientation in the grain elongation direction and still contain surviving long ribbon grain fragments. With route BC, shear banding on alternate planes and the lack of an overall compression of the structure with strain, results in a more chaotic microstructure, which contains lowermisorientationsubgrain islands within a matrix of ultra-fine grains (Fig.5c). These submicron grains are frequently finer in scale and elongated within shear bands created in the last pass.If a mechanism of grain subdivision, such as micro/shear banding is suppressed by the inclusion of high densities of dispersoids, which are frequently used in superplastic alloys[16], both route A and route BCresult in more heterogeneous structures. However, route BCis much more significantly affected due to the lack of any general geometric boundary extension. With route A larger unrefined fibrous grains are retained (Fig.5b), which correspond to volumes with more stable orientations, which are no longer subdivided by micro/shearbanding[16]. But, with route BC, due to the suppression of shear banding, the material can no longer be described as submicron grained and contains only 45% HABs (Fig.5d). In contrast, materials produced by any deformation route can be made more homogenous by including coarse second phase particles, which encourages matrix orientation divergence at low strains and breaks up lamellar HAB structuresat high strains[17].2.6 Steady state and dynamic recoveryIf the deformation conditions are maintained constant, ultimately a steady state must be approached in severe deformation where there is no further grain refinement. An example of this behaviour can be seen in Fig.6a, where statistical data obtained by EBSD shows little significant difference in the fraction of HAB area, and a negligible reduction in grain width, in the strain range 8~17, using route A. At this stage the grain width hasconverged with the cell size. There is, however, still a noticeable reduction in average grain length. This occurs due to the breakup of the final remaining long fibrous ribbon grain fragments, resulting in an increase in homogeneity of the material.Due to the geometric requirements of the imposed shear, the grain width should be reducing with strain at a much higher rate, although this is less significant than in plane strain where a similar limiting grain width has been observed by Jazaeri et al.[25-26]. This is illustrated in Fig.6a where the theoretical grain width is geometrically required by shear to reduce by the order of 0.1-0.02 μm per extrusion cycle in this strain range.If a constant grain width is maintained dynamically, with a ram speed of 50 mm/min and deformation zone width of 2 mm, this corresponds to a boundary migration velocity of 0.01~0.04 μm·s-1. The conventional thermally activated migration rate of a boundary is given by[18]:If the average driving force for boundary migration P is equivalent to 3γ/d, using typical measured values ofγ=0.3 J·m-2, a grain sized0.7 μm,M0~0.1 m4·J-1·s-1, and an activation energy of 130 kJ·mol-1[26], this gives, assuming a deformation temperature due to plastic work of ~50 ℃ a velocity of 1×10-10μm·s-1, which is too lowby a factor of 108to maintain a constant grain width.However estimated, unrealistic values of P would be required to greatly increase V. In comparison an effective activation energy and a value of 80 kJ·mol-1will result in the required migration rate. Similar values of Q have been reported for static grain growth at low temperatures in severely deformed alloys, using TEM measurements, but these resultsare generally confusing as they can also be attributed to misinterpretation resulting from the heterogeneous nature of the deformation structures[27]. However, overall the data suggests that a limiting grain size is achieved due to dynamic grain boundary migration occurring at a far higher rate than for conventional static annealing. This could result from the interaction of dislocations with HABs, a higher vacancy concentration, and higher local driving pressures due to non-equilibrium boundary configurations.It is also apparent that limited dynamic boundary migration could contribute to the grain refinement process at high strains once the HAB spacing in local bands reduces to the subgrain sizeand, for example, facilitate some spheroidisationandthe break up of thin ribbon grains in a manner similar to that observed during static annealing of lamellar HAB structures at higher temperatures[27]. Simulations have shown this occurs becauseeven low angle transverse boundaries exert a large resolved surface tension at nodal points in lamellar boundary structures. A strongly developing texture can also reduce the HAB density during deformation, but the texture is generally relatively weak in ECAE[12]. Further grain refinement can thus only be achieved by increasing the Zener-Hollomon parameter. The remarkable effect of reducing the deformation temperature is illustrated in Fig.6b, where the Al-0.1Mg alloy after processing by ECAE at 20 ℃ temperature toεeff=10 (Fig.5a) has been subsequently deformed in plane strain compression in liquid nitrogen to a further strain ofεtrue=2, resulting in thin ribbon grains of 100 nm in width.Grain refinement in high stacking fault energy aluminum alloys during severe deformation processes,such as ECAE, occurs predominantly by orientation splitting, micro and macroshear banding, and the geometric requirements for high angle boundary area to increase with strain. The deformation structure evolution is strongly affectedby the processing route, die geometry, and material parameters. Both cell bands and microshear bands show alignment with the dies shear plane, corresponding to the maximum resolved stress but irrelevant of the crystallographic slip systems of the material. Micro/shear bands are promoted by changes in the shear plane orientation in each extrusion cycle. The geometrically required increase in boundary area and compression in boundary spacing with strain is an important aspect of the formation of fibrous ultra-fine grain structures with route A, and increases in significance with smaller initial grain sizes. The introduction of fine non-shearable second phase particles results in a reduction in the rate of grain refinement by the homogenization of slip which results, when combined with processing routes that involve redundant strains (e.g. Route BC), in materials that predominantly contain subgrains. In contrast, coarse second phase particles accelerate the rate of grain refinement and increase homogeneity of the final grain structure. At high strains a steady state is achieved, due to dynamic boundary migration occurring at far higher rate than under static conditions, resulting in a constant minimum grain size. Dynamic boundary migration also contributes to the grain refinement process at high strains when the HAB spacing approaches the subgrain。
等径角挤压工艺中变形与挤压载荷研究
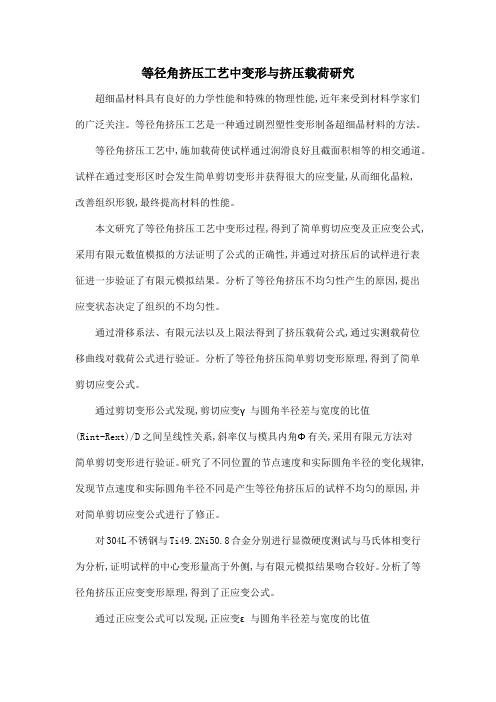
等径角挤压工艺中变形与挤压载荷研究超细晶材料具有良好的力学性能和特殊的物理性能,近年来受到材料学家们的广泛关注。
等径角挤压工艺是一种通过剧烈塑性变形制备超细晶材料的方法。
等径角挤压工艺中,施加载荷使试样通过润滑良好且截面积相等的相交通道。
试样在通过变形区时会发生简单剪切变形并获得很大的应变量,从而细化晶粒,改善组织形貌,最终提高材料的性能。
本文研究了等径角挤压工艺中变形过程,得到了简单剪切应变及正应变公式,采用有限元数值模拟的方法证明了公式的正确性,并通过对挤压后的试样进行表征进一步验证了有限元模拟结果。
分析了等径角挤压不均匀性产生的原因,提出应变状态决定了组织的不均匀性。
通过滑移系法、有限元法以及上限法得到了挤压载荷公式,通过实测载荷位移曲线对载荷公式进行验证。
分析了等径角挤压简单剪切变形原理,得到了简单剪切应变公式。
通过剪切变形公式发现,剪切应变γ与圆角半径差与宽度的比值(Rint-Rext)/D之间呈线性关系,斜率仅与模具内角Φ有关,采用有限元方法对简单剪切变形进行验证。
研究了不同位置的节点速度和实际圆角半径的变化规律,发现节点速度和实际圆角半径不同是产生等径角挤压后的试样不均匀的原因,并对简单剪切应变公式进行了修正。
对304L不锈钢与Ti49.2Ni50.8合金分别进行显微硬度测试与马氏体相变行为分析,证明试样的中心变形量高于外侧,与有限元模拟结果吻合较好。
分析了等径角挤压正应变变形原理,得到了正应变公式。
通过正应变公式可以发现,正应变ε与圆角半径差与宽度的比值(Rint-Rext)/D之间呈线性关系,斜率仅与模具内角Φ有关。
当Rext-Rint=D,或者模具内角角度为180°时,理论计算的正应变为0,即不发生正应变。
采用有限元模拟结果验证了正应变理论公式,并用实际节点圆角半径代替模具内外角圆角半径,完善了正应变的理论公式。
通过304L奥氏体不锈钢金相结果及显微硬度结果证明了正应变的存在。
大体积超细晶金属材料的剧烈塑性变形法制备技术
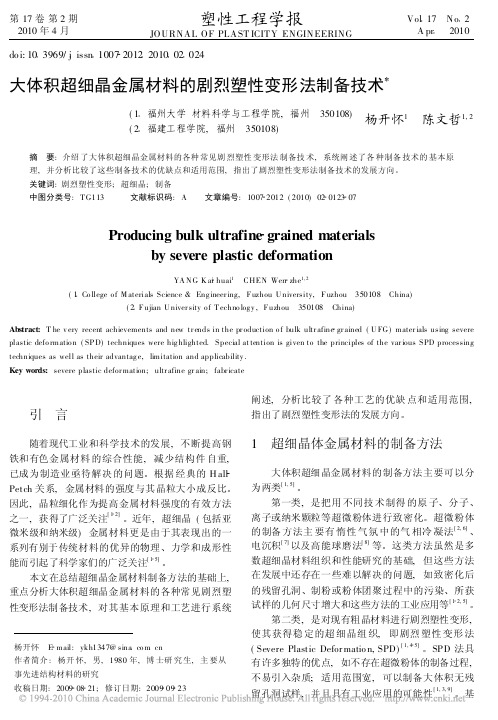
第17卷第2期2010年4月塑性工程学报JOURNAL OF PLAST ICITY ENGINEERINGVol 17 No 2A pr 2010doi:10 3969/j issn 1007 2012 2010 02 024大体积超细晶金属材料的剧烈塑性变形法制备技术*(1 福州大学材料科学与工程学院,福州 350108)(2 福建工程学院,福州 350108)杨开怀1 陈文哲1,2摘 要:介绍了大体积超细晶金属材料的各种常见剧烈塑性变形法制备技术,系统阐述了各种制备技术的基本原理,并分析比较了这些制备技术的优缺点和适用范围,指出了剧烈塑性变形法制备技术的发展方向。
关键词:剧烈塑性变形;超细晶;制备中图分类号:T G113 文献标识码:A 文章编号:1007 2012(2010)02 0123 07Producing bulk ultrafine grained materialsby severe plastic deformationYA N G K ai huai 1 CHEN Wen zhe 1,2(1 Co llege o f M aterials Science &Eng ineer ing,F uzhou U niversity,F uzhou 350108 China)(2 F ujian U niver sity o f T echno log y ,F uzhou 350108 China)Abstract:T he v ery recent achievements and new tr ends in the pr oduction o f bulk ultr afine gr ained (U FG )mater ials using severe plastic defo rmatio n (SP D)techniques were hig hlighted.Special at tention is given to the principles of the var ious SPD processing techniques as well as their advantag e,limitation and applicability.Key words:severe plastic defor mation;ultr afine gr ain;fabr icate杨开怀 E mail:ykh1347@sina co m cn作者简介:杨开怀,男,1980年,博士研究生,主要从事先进结构材料的研究收稿日期:2009 08 21;修订日期:2009 09 23引 言随着现代工业和科学技术的发展,不断提高钢铁和有色金属材料的综合性能,减少结构件自重,已成为制造业亟待解决的问题。
强烈塑性变形超塑材料研究进展

ie
w
;u l t r a
fin
e
-
r i g a
n e
d
m e
ta s ; a lu m l
in
u m
a
llo ys
晶粒 尺 寸 对 超 塑 性 材 料 而 言
。
是
一
个非常重要 的
、
等径 角 挤 压 (E C A P )r
7- - ”
。
高压 扭 转 工 艺 的 基 本 原 理 如
,
结 构 参数
。
晶 粒 尺 寸 的减 小 可 以 使 材 料 在 更 低 温 度
typ ic a
ity
,
Xi
’
a n
7 10 0 7 1 Ch i n
,
a
)
l a
r
v e re a a
p l a s t ic d e f o r m
a
tio
n
is
a n
s u
e
e c s
i t
v e
to
.
to
de
v e
lo p
r
u
e
-
g r a in
e
d
s
m e
o
ta
ls
.
n a s u
d
o n e
重庆维普
第3l 卷
200 8 车
第4 期
7 月
兵 器 材料科 学与工 程
0 R D N A N C E M A T E 砒 A L S C IE N C E A N D E N G I N E E R IN G
V o I.l 3
细化晶粒
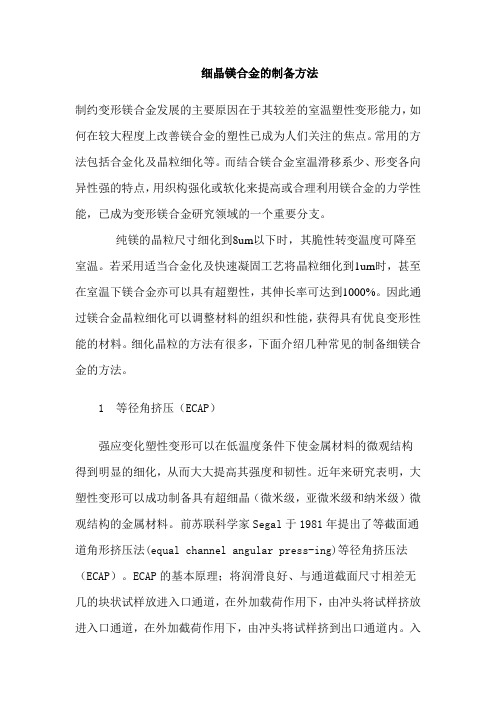
细晶镁合金的制备方法制约变形镁合金发展的主要原因在于其较差的室温塑性变形能力,如何在较大程度上改善镁合金的塑性已成为人们关注的焦点。
常用的方法包括合金化及晶粒细化等。
而结合镁合金室温滑移系少、形变各向异性强的特点,用织构强化或软化来提高或合理利用镁合金的力学性能,已成为变形镁合金研究领域的一个重要分支。
纯镁的晶粒尺寸细化到8um以下时,其脆性转变温度可降至室温。
若采用适当合金化及快速凝固工艺将晶粒细化到1um时,甚至在室温下镁合金亦可以具有超塑性,其伸长率可达到1000%。
因此通过镁合金晶粒细化可以调整材料的组织和性能,获得具有优良变形性能的材料。
细化晶粒的方法有很多,下面介绍几种常见的制备细镁合金的方法。
1 等径角挤压(ECAP)强应变化塑性变形可以在低温度条件下使金属材料的微观结构得到明显的细化,从而大大提高其强度和韧性。
近年来研究表明,大塑性变形可以成功制备具有超细晶(微米级,亚微米级和纳米级)微观结构的金属材料。
前苏联科学家Segal于1981年提出了等截面通道角形挤压法(equal channel angular press-ing)等径角挤压法(ECAP)。
ECAP的基本原理;将润滑良好、与通道截面尺寸相差无几的块状试样放进入口通道,在外加载荷作用下,由冲头将试样挤放进入口通道,在外加截荷作用下,由冲头将试样挤到出口通道内。
入口通道与出口通道之间存在一个夹角。
在理想条件下,变形是通过在两等截面通道交截面(剪切平面)发生简单的切变实现的。
经角径角挤压后,试样发生简单切变,但仍保持横截面积不变,挤压过程可以反复进行,从而在试样中实现大塑性变形。
通过这项技术,可以不依赖粉末冶金和复杂的形变热处理而制备大体积块状细晶材料。
2 添加适当的合金化元素根据合金化原理,明确各种元素在镁中产生的作用,针对不同的需要对镁合金中添加适当的微量合金元素,并进行显微组织和结构设计,引人固溶强化、沉淀强化或弥散强化等机制,可以达到细化晶粒,调整镁合金组织,提高和改善合金性能的目的。
基于剧烈塑性变形的超细晶中碳钢制备技术

基于剧烈塑性变形的超细晶中碳钢制备技术
汪建敏;陆晋;周孔亢;许晓静;姜银方
【期刊名称】《农业机械学报》
【年(卷),期】2006(37)12
【摘要】用实验方法研究了中碳钢两相组织在等通道角挤压过程中的强烈塑性变形行为和组织演化过程.实验结果表明,用Bc挤压路径经过4道次变形后开始出现纳米级晶粒.中碳钢两相组织的变形行为和组织演化过程为:前两道ECAP,强烈剪切变形集中发生在铁素体内,使铁素体原始晶粒中产生了大量位错缠结和位错胞,随挤压道数的增加,珠光体也开始参与剪切变形,渗碳体由原来的条状被剪切断裂而被细化,成为颗粒状,其粒状平均尺寸至1μm,同时所形成的高密度位错铁素体显微组织逐渐演化变成等轴显微组织.挤压四道次后,位错胞崩塌形成大角度晶粒,其铁素体平均晶粒尺寸至200 nm.
【总页数】4页(P209-212)
【作者】汪建敏;陆晋;周孔亢;许晓静;姜银方
【作者单位】江苏大学材料科学与工程学院 212013 镇江市;江苏大学电气信息工程学院;江苏大学汽车与交通工程学院;江苏大学机械工程学院;江苏大学机械工程学院
【正文语种】中文
【中图分类】TG1
【相关文献】
1.剧烈塑性变形后超细晶粒耐蚀钢的强度 [J], O.V.Rybal;郭湛(译);浦玉梅(校)
2.基于剧烈塑性变形法制备块体超细晶材料和力学性能的研究综述 [J], 刘博;郑丽;卢振华
3.基于温变形的超细晶中碳钢制备工艺 [J], 汪建敏;陆晋;姜银方;周孔亢;潘励
4.基于等通道角挤压工艺制备超细晶中碳钢 [J], 汪建敏;陆晋;李新城;程晓农;许晓静
5.大体积超细晶金属材料的剧烈塑性变形法制备技术 [J], 杨开怀;陈文哲
因版权原因,仅展示原文概要,查看原文内容请购买。
ECAP法超细晶制备纯铝

本文首先是通过有限元模拟,发现挤轧变形时样品的推进长度、推进速度等因素对挤轧变形过程有很大的影响,模拟后得出最佳的实验条件,然后根据模拟结果改进实验装置以及实验条件。最后本文所采用装置推进长度为20mm,推进速度为5mm/s时,可以使纯铝试样顺利地发生挤轧变形,使得材料晶粒发生明显细化。模拟结果表明,在推进压力一定的条件下,样品挤轧变形速率仅和样品与轧辊间的摩擦系数有关,与轧辊的转速无关。挤轧变形及热处理实验结果表明,当挤轧道次为4道次,退火温度为200℃,退火时间为10min时,所获得的晶粒尺寸细小均匀,晶粒细化效果最好。
铝的低密度与耐腐蚀,是其性能的两大突出特点。铝的密度很小,虽然它比较软,但可制成各种铝合金,如硬铝、超硬铝、防锈铝、铸铝等。这些铝合金广泛应用于飞机、汽车、火车、船舶等制造工业。此外,宇宙火箭、航天飞机、人造卫星也大量使用铝及其合金。同时铝的导电性仅次于银、铜和金,虽然它的导电率只有铜的2/3,但密度只有铜的1/3,所以输送同量的电,铝线的质量只有铜线的,一半。铝表面的氧化膜不仅有耐腐蚀的能力,而且有一定的绝缘性,所以铝在电器制造工业、电线电缆工业和无线电工业中有广泛的用途:。铝是热的良导体,它的导热能力比铁大3倍,工业上可用铝制造各种热交换器、散热材料和炊具等。铝有较好的延展性(它的延展性仅次于金和银),在100℃~150℃时可制成薄于0.01 mm的铝箔。这些铝箔广泛用于包装香烟、糖果等,还可制成铝丝、铝条,并能轧制各种铝制品。铝的表面因有致密的氧化物保护膜,不易受到腐蚀,常被用来制造化学反应器、医疗器械、冷冻装置、石油精炼装置、石油和天然气管道等。铝粉具有银白色光泽(一般金属在粉末状时的颜色多为黑色),常用来做涂料,俗称银粉、银漆,以保护铁制品不被腐蚀,而且美观。
- 1、下载文档前请自行甄别文档内容的完整性,平台不提供额外的编辑、内容补充、找答案等附加服务。
- 2、"仅部分预览"的文档,不可在线预览部分如存在完整性等问题,可反馈申请退款(可完整预览的文档不适用该条件!)。
- 3、如文档侵犯您的权益,请联系客服反馈,我们会尽快为您处理(人工客服工作时间:9:00-18:30)。
The development of NanoSPD as an important area of materials science
The interest in SPD processing was subsequently stimulated by the recognition that it may be used to produce exceptional grain refinement in bulk solids and thus it is a processing tool for achieving unusual and beneficial properties.
Bulk UFG materials:
Additional requirements: fairly homogeneous and reasonably equiaxed microstructures, with a majority of the grain boundaries having high angles of misorientation.
Modern Types of Nanostructured Materials
Two approaches to produce bulk nanostructured materials
1. Bottom-up
由小到大的合成法
Consolidation of nanograins (particles)
一. Introduction
Ultrafine-grained (UFG) materials
Ultrafine-grained (UFG) materials:
polycrystals having very small grains with average grain sizes less than ~1 μm. Thus, the grain sizes of UFG materials lie within the submicrometer (100 –1,000 nm) and nanometer (less than 100 nm) ranges.
Why SPD? To Refine/Homogenize the Microstructure To Strengthen the Material To Enhance the Properties
Examples: Work Hardening Grain Refinement Development of Special Microstructures Development of Special Textures
2. Top-down
Inert gas condensation (惰性气体凝聚原位加压)
– Process • vapour phase of metal • condensed on a cold surface • particles of up to 50 nm in size • consolidation of particles
Segal and coworkers in Minsk, former Soviet Union, 1980s: the technique of equal-channel angular pressing (ECAP) was first introduced in a form that is essentially identical to the procedure now used in many laboratories around the world.
成语:百炼成钢 ancient SPD technique to make good steel. repetitive fold and forgings.
East Han 30 LIAN steel Knife
Thin elongated silicate inclusions in array, indicating the layered microstructure from deformation in the East Han 30 LIAN steel knife.
The development of NanoSPD as an important area of materials science
Severe plastic deformation (SPD) processing has a long history, dating back to the metalworking of ancient China.
As a consequence of this early work, there was a general recognition in the 1990s that SPD processing was becoming an important research area having a significant potential for use in a wide range of industrial applications.
首先制备出纳米颗粒,然后通过原位加压、热等静压、热挤压等 方法制备块体纳米材料。理论上凡是能够获得纳米颗粒的制备方ndensation (Gleiter, 1984) • Electrodeposition (Erb et al, 1989) • Consolidation of nanopowders (Koch,1990) 由大到小的细化法 Decreasing the grain size of already bulk materials • Severe plastic deformation (SPD) (Valiev et al, 1991)
Bulk ultrafine-grained materials processed by severe plastic deformation
郑明毅
哈尔滨工业大学 材料科学与工程学院 2008, 06
Outline
1. Introduction 2. Techniques for SPD Processing 3. Equal channel angular pressing (ECAP) 4. Microstructural features of SPD-processed materials 5. Properties of UFG materials processed by SPD 6. Applications of UFG materials processed by SPD 7. Future prospects for UFG materials by SPD
– Limitations • slow • thin layer (<100 μm)
High energy mechanical milling(高能球磨法)
– Process • metallic particles milled by steel spheres at room or cryogenic T • severe plastic deformation in individual particles • average grain sizes 10-20 nm • consolidation of particles
– Limitations • long time • surface contamination • residual pores in consolidated material • possible coarsening during consolidation
Severe plastic deformaation (SPD)
High Pressure Torsion Equal Channel Angular Pressing (from R.Z. Valiev, Nature Materials 3, 2004)
Why SPD?
Unique feature of SPD processing :
the high strain is imposed without any significant change in the overall dimensions of the workpiece, the shape is retained by using special tool geometries that prevent free flow of the material and thereby produce a significant hydrostatic pressure. overcoming of a number of difficulties connected with residual porosity in compacted samples, hazardous nano-powders, impurities from ball milling, processing of large scale billets, practical application of the given materials.
Tremendous current interest in SPD processing One of the most active and developing fields in modern materials science: Bulk ultrafine-grained (UFG) materials processed by severe plastic deformation (SPD).
The development of NanoSPD as an important area of materials science