工序单位能耗的计算方法、及企业吨钢可比能耗计算方法
粗钢生产工序能耗计算

粗钢生产工序能耗计算引言能耗计算是工业生产过程中的一个重要环节,通过对不同工序的能耗进行准确计算,可以帮助企业找出能耗较高的环节,进而采取相应的节能措施,提高生产效率,降低成本。
本文将针对粗钢生产过程中的不同工序进行能耗计算,以帮助企业更好地控制和优化能源消耗。
粗钢生产工序简介粗钢是指通过冶炼过程制得的未经初步加工的钢材,具有较高的含碳量和较低的纯度。
粗钢生产工序一般包括:原料准备、熔炼冶炼、钢水处理、连铸、初轧和粗轧等环节。
原料准备能耗计算原料准备环节主要包括铁矿石的破碎、磨矿、混合和配料等过程。
根据实际产量和生产数据,可以计算出原料准备环节的能耗。
原料准备能耗 = 原料准备消耗能量 / 产量熔炼冶炼能耗计算熔炼冶炼环节是将铁矿石和其他辅助材料经高温熔炼,得到钢水的过程。
熔炼冶炼能耗可以通过以下公式计算:熔炼冶炼能耗 = 燃料消耗能量 + 电能消耗能量 + 冷却水消耗能量 / 产量钢水处理能耗计算钢水处理环节是将熔炼冶炼出来的钢水经过脱硫、脱氧等处理,提高钢水的纯度和质量。
钢水处理能耗可以通过以下公式计算:钢水处理能耗 = 电能消耗能量 + 冷却水消耗能量 / 产量连铸能耗计算连铸是将钢水浇铸成连续铸坯的过程,连铸能耗可以通过以下公式计算:连铸能耗 = 电能消耗能量 + 冷却水消耗能量 + 氧气消耗能量 / 产量初轧能耗计算初轧环节是将连铸坯经过初轧机轧制成规定尺寸的厚板,并进行质量控制。
初轧能耗可以通过以下公式计算:初轧能耗 = 电能消耗能量 + 冷却水消耗能量 / 产量粗轧能耗计算粗轧环节是将初轧后的厚板不断轧制,降低其厚度,最终得到要求尺寸的薄板。
粗轧能耗可以通过以下公式计算:粗轧能耗 = 电能消耗能量 + 冷却水消耗能量 / 产量结论通过对粗钢生产工序的能耗计算,可以帮助企业找出能源消耗较高的环节,并针对性地采取节能措施,提高能源利用效率,降低生产成本。
在实际应用中,还应考虑到设备能效、操作参数等因素对能耗的影响,以实现更精确和全面的能耗计算和优化。
工业企业单位产品能耗指标计算方法
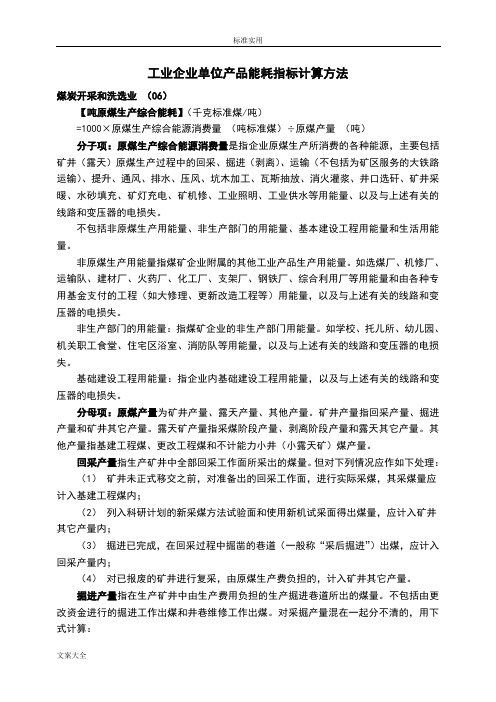
工业企业单位产品能耗指标计算方法煤炭开采和洗选业(06)【吨原煤生产综合能耗】(千克标准煤/吨)=1000×原煤生产综合能源消费量(吨标准煤)÷原煤产量(吨)分子项:原煤生产综合能源消费量是指企业原煤生产所消费的各种能源,主要包括矿井(露天)原煤生产过程中的回采、掘进(剥离)、运输(不包括为矿区服务的大铁路运输)、提升、通风、排水、压风、坑木加工、瓦斯抽放、消火灌浆、井口选矸、矿井采暖、水砂填充、矿灯充电、矿机修、工业照明、工业供水等用能量、以及与上述有关的线路和变压器的电损失。
不包括非原煤生产用能量、非生产部门的用能量、基本建设工程用能量和生活用能量。
非原煤生产用能量指煤矿企业附属的其他工业产品生产用能量。
如选煤厂、机修厂、运输队、建材厂、火药厂、化工厂、支架厂、钢铁厂、综合利用厂等用能量和由各种专用基金支付的工程(如大修理、更新改造工程等)用能量,以及与上述有关的线路和变压器的电损失。
非生产部门的用能量:指煤矿企业的非生产部门用能量。
如学校、托儿所、幼儿园、机关职工食堂、住宅区浴室、消防队等用能量,以及与上述有关的线路和变压器的电损失。
基础建设工程用能量:指企业内基础建设工程用能量,以及与上述有关的线路和变压器的电损失。
分母项:原煤产量为矿井产量、露天产量、其他产量。
矿井产量指回采产量、掘进产量和矿井其它产量。
露天矿产量指采煤阶段产量、剥离阶段产量和露天其它产量。
其他产量指基建工程煤、更改工程煤和不计能力小井(小露天矿)煤产量。
回采产量指生产矿井中全部回采工作面所采出的煤量。
但对下列情况应作如下处理:(1)矿井未正式移交之前,对准备出的回采工作面,进行实际采煤,其采煤量应计入基建工程煤内;(2)列入科研计划的新采煤方法试验面和使用新机试采面得出煤量,应计入矿井其它产量内;(3)掘进已完成,在回采过程中掘凿的巷道(一般称“采后掘进”)出煤,应计入回采产量内;(4)对已报废的矿井进行复采,由原煤生产费负担的,计入矿井其它产量。
3能耗指标体系的分类计算

能耗指标体系的分类钢铁企业能耗指标主要有吨钢综合能耗、吨钢可比能耗、主要产品的工序能耗、主要产品的实物单耗(如炼铁焦比、炼焦煤耗等)以及产值能耗、增加值能耗等等。
能源分析评价指标中,包括企业内部能源加工转换指标和企业损失指标。
按钢铁企业能耗经济技术指标体系可分为:(1)企业级能源技术经济指标:如吨钢综合能耗、万元产值能耗、吨钢耗新水、吨钢电耗、损失率等。
(2)工序级能源技术经济指标:如炼钢工序能耗、炼铁工序能耗等。
(3)耗能设备级能源技术经济指标:加热炉燃耗、高炉焦比、制氧机电耗等。
按钢铁企业能效对标指南中能耗指标体系可分为:(1)综合性指标:如企业级能源消耗总量、工序级能源消耗总量、各类能源介质消耗总量、企业能源亏损量等指标。
(2)单耗性指标:如吨钢综合能耗、企业吨钢可比能耗、工序单位产品能耗。
(3)经济性指标:万元产值能耗、万元增加值能耗等。
2.能耗指标的范围及计算钢铁制造流程是由多个不同的生产工序组成的,前一道工序的产品为下一道工序的原料,这是钢铁工业的特点,由于其复杂性,因此,统计范围和指标定义必须规范,以便于对标,找出节能潜力,提升企业效益。
(1)吨钢综合能耗范围及计算综合能耗是规定的耗能体系在一段时间内实际消耗的各种能源实物量按规定的计算方法和单位分别折算为标准煤后的总和。
吨钢综合能耗(comprehensive energy consumption ):吨钢综合能耗是企业生产每吨粗钢所综合消耗的各种能源自耗总量;也就是每生产一吨钢,企业消耗的净能源量。
其计算公式为:吨钢综合能耗=企业钢产量企业自耗能源量(吨标准煤/吨钢,千克标准煤/吨;tce/t ,kgce/t )式中,企业自耗能源量即报告期内企业自耗的全部能源量。
统计上报按企业全部耗能量。
企业自耗能源量= 企业购入能源量 ± 库存能源增减量 - 外销能源量= 企业各部位耗能量之和 + 企业能源亏损量作为行业对标,吨钢综合能耗的统计范围可按照企业生产流程的主体生产工序(包括原料储存、焦化、烧结、球团、炼铁、炼钢、连铸、轧钢、自备电厂、制氧等动力厂)、厂内运输、燃料加工及输送、企业亏损等消耗能源总量,不包括矿石的采、选工序,也不包含炭素、耐火材料、机修、石灰、精制及铁合金等非钢生产工序的能源消耗量。
6钢铁企业吨钢可比能耗计算方法

规模以上工业统计报表制度 —1—6.钢铁企业吨钢可比能耗计算方法工序 部位工序单位能耗 吨标准煤/吨产品(1)钢比或铁比 吨产品/吨钢(铁)(2)可比能耗的组成 吨标准煤/吨钢 (1)×(2)备 注焦化Aa =(烧结、球团、炼铁)耗焦量/全铁折合产量A ·aa b c 为折算铁比系数,只适用于能耗指标计算烧结 Bb =烧结矿消耗量/全铁折合产量B ·b球团 Cc =球团矿消耗量/全铁折合产量C ·c炼铁D =炼铁工序能耗/全铁折合产量D 1=炼铁工序能耗/全铁产量E = A ·a+ B ·b+ C ·c+ De :吨钢耗生铁量 E ·eD :炼铁工序折合全铁单位能耗;D 1:炼铁工序全铁单位能耗;E :企业吨铁单位能耗;转炉 电炉 其他炉 连铸F 1 F 2 F 3 F 4f 1转炉钢率 f 2电炉钢率 f 3其他炉钢率 f 4连铸钢率 (f 1+ f 2+ f 3=1)F= F 1·f 1+ F 2·f 2 + F 3·f 3+ F 4·f 4连铸能耗属炼钢工序开坯G :初轧单位能耗g ·[1— (连铸坯量+直接成材耗锭量)/ (初轧耗锭量+连铸坯量+直接成材耗锭量)]M=初轧开坯累计耗能量/(初轧耗锭量+连铸坯量+直接成材耗锭量)1.式中连铸坯量系企业直接成材消耗的连铸坯量;2.在特钢企业用钢锭成材时,生产的锻钢件(材)可按直接成材处理;3.M=G ·g ·[1— (连铸坯量+直接成材耗锭量)/ (初轧耗锭量+连铸坯量+直接成材耗锭量)]g.初轧钢坯成坯率轧材H=轧材耗能量/企业最终钢材产量h: 企业由钢到材的综合成材率 H ·h机车I=运输能耗量/企业钢产量燃气加工与输送J=燃气加工与输送耗量/企业钢产量 企业能源亏损K=企业能源亏损量/企业钢产量 企业吨钢可比能耗L=E ·e+F+M+ H ·h +I+J+K。
工序能耗计算方法

工序能耗计算方法
工序能耗计算方法:
①明确计算边界包括直接消耗能量如燃料电力以及间接消耗如蒸汽压缩空气等并确定计算周期通常以生产批次或固定时间段为准;
②收集所有相关设备运行参数比如电机功率加热炉温度冷却水流量等记录开始结束时间计算实际工作时长;
③计算单台设备能耗使用公式耗能量等于功率乘以时间单位转换成标准形式如千瓦时或兆焦耳;
④对于非直接测量项目如蒸汽消耗量通过热量平衡法估算根据蒸汽压力温度查表得出焓值再乘以流量换算成能量形式;
⑤将所有单个设备耗能量汇总得出整个工序总耗能量如果存在多个工序则分别计算各自能耗再相加得到系统总能耗;
⑥考虑到能源转换效率不同能源形式之间需要按照等价值原则进行折算例如电力转换系数通常取值为3.6MJ/kWh以便比较分析;
⑦分析工序中各环节能源利用效率识别能源浪费环节比如无效散热不必要空转等提出改进措施降低能耗;
⑧建立能源基准即在当前技术水平和操作条件下达到最佳能效状态时所消耗的能量用于评估未来改进效果;
⑨利用生命周期评估LCA方法考虑原材料获取加工运输安装使用废弃处置等全生命周期阶段能量消耗情况综合评价工序整体能效;
⑩应用能源管理系统如ISO50001标准持续监测关键能源使用区域定期审核能源绩效确保长期维持高效状态;
⑪结合历史数据分析季节性变化规律预测未来能耗趋势为节能减排提供决策支持;
⑫最后通过持续改进措施不断优化能源使用结构提高能源利用效率实现绿色低碳生产目标。
吨钢可比能耗限额与计算方法
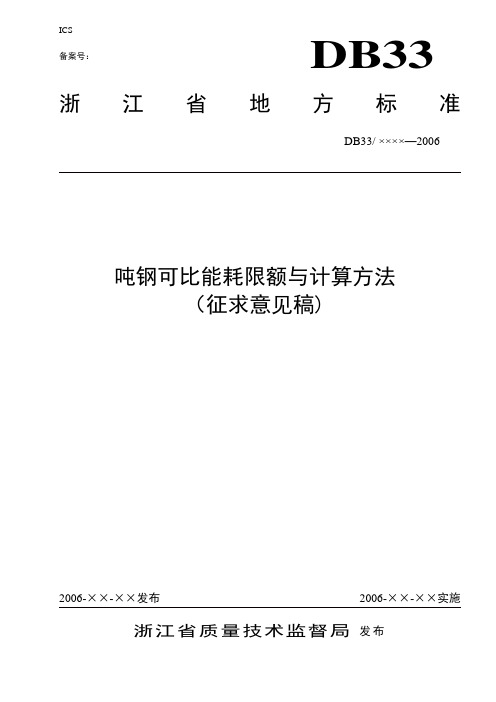
ICS备案号:DB33吨钢可比能耗限额与计算方法(征求意见稿)浙江省质量技术监督局 发布前言本标准由浙江省经济贸易委员会提出并归口。
本标准起草单位:浙江省节能协会。
本标准主要起草人:吨钢可比能耗限额与计算方法(征求意见稿)1 范围本标准规定了钢铁联合企业吨钢可比能耗限额及计算方法。
本标准适用于钢铁联合企业。
2 规范性引用文件下列文件中的条款通过本标准的引用而成为本标准的条款。
凡是注日期的引用文件,其随后所有的修改单(不包括勘误的内容)或修订版均不适用于本标准,然而,鼓励根据本标准达成协议的各方研究是否可使用这些文件的最新版本。
凡是不注日期的引用文件,其最新版本适用于本标准。
GB 17167-2006《用能单位计量器具配备与管理通则》;GB/T 6422《企业能耗计量与测试通则》;GB33/××××-××××《用能单位能源消耗量化管理要求》;《关于颁发〈钢铁企业能源平衡及能耗指标计算办法的暂行规定〉的通知》冶金工业部(82)冶能字第551号;《关于统一钢铁企业能源统计报表中各类能源折算系数的通知》冶金工业部(84)冶能办字第005号;《主要行业产品能源消耗指标培训材料》主编单位:国家统计局工交司、中国钢铁工业协会等,2006年8月。
3 定义吨钢可比能耗是指钢铁企业在报告期内,每生产一吨粗钢,从炼焦、烧结、炼铁、炼钢直到企业最终钢材配套生产所必须的耗能量及企业燃料加工与运输、机车运输能耗及企业能源亏损所分摊在每吨粗钢上的耗能量之和。
不包括钢铁工业企业的采矿、选矿、铁合金、耐火材料制品、炭素制品、煤化工产品及其它产品生产、辅助生产及非生产的能耗。
4 吨钢可比能耗的限额本限额适用期限为2006年~2010年。
指标名称计量单位指标限额吨钢可比能耗千克标准煤/吨 6305 吨钢可比能耗的计算方法钢铁企业可参照本标准引用文件中相关文件的规定,定期编制《钢铁企业能源平衡表》,并依照以下计算方法计算吨钢可比能耗,见表1。
工业企业单位产品能源消耗指标计算方法

工业企业单位产品能源消耗指标计算方法(按统计局的统计口径计算)【选煤电力单耗】(千瓦时/吨)=100×选煤生产过程耗电量(万千瓦时)/入选原煤量(吨)分子项:选煤生产过程耗电量按电业部门结算的电量计算,不包括选煤厂向外转供电量,以及与选煤生产无直接关系的各种用电量(如居民生活用电、基建工程用电、文化福利设施用电等)。
分母项:入选原煤量指从入厂毛煤中拣出的不计原煤产量的大块(一般指50毫米以上)矸石后进入选煤过程,进行加工处理的原煤量。
无机碱制造(2612)【单位烧碱生产综合能耗】(千克标准煤/吨)=1000×液体烧碱综合能源消耗量(吨标准煤)/液体烧碱产量(折100%)(吨)分子项:烧碱综合能源消耗量是指用于烧碱生产的各种能源折标准煤后的总和。
包括烧碱生产工艺系统耗能量和为烧碱生产服务的辅助系统和附属生产系统耗能量。
烧碱生产系统耗能量的统计范围,从原料投入开始,包括盐水制备、整流、电解、蒸发、蒸煮至成品烧碱包装入库为止的所有工艺用的电解用交流电、动力用电、蒸汽、油、煤等实际消耗量。
烧碱生产的辅助和附属系统耗能量的统计范围包括:电槽修理、阳极组装、石棉绒回收、炭极加工、以及车间检修、车间分析、车间办公室、休息室、更衣室等各种耗能量。
分母项:烧碱产量折成100%计算。
氢氧化钠(烧碱)(折100%)包括由盐水电解法或由纯碱(或天然碱)苛化法生产的液体氢氧化钠。
也包括氢气干燥和本企业其他产品自用的合格烧碱。
不同方法生产的各种烧碱,经检验符合国家标准(GB209-93),方可统计产量。
产量中不包括在使用烧碱过程中回收的烧碱和生产烧碱过程中自用的电解碱液、浓缩碱液、回收盐液中的含碱量。
企业填报烧碱产量,应将不同的生产方法(水银法、隔膜法、离子膜法、苛化法)生产的液碱折成100%计算产量。
【单位烧碱生产耗交流电】(千瓦小时/吨)=100×交流电消耗量(万千瓦时)/液体烧碱(100%)产量(吨)分子项:交流电消耗量以电业局安装的直流耗交流电度表为准。
粗钢生产工序能耗计算

②高炉煤气的折标量:当月高气消耗量115.09万立方米×1.30038 (当月煤热值
÷7000)=149.67吨标煤
③焦炉煤气的折标量:当月焦气消耗量180.02 万立方米×6.20457(当月煤热值
÷7000)=1116.95吨标煤
技术要求(限额准入值) v 当电力折标准煤系数采用等价值0.404kgce/(kw·h)
时,新建或改扩建烧结机生产设备烧结工序单位产 品综合能耗限额准入值应不大于60kgce/t。 v 当电力折标准煤系数从等价值0.404kgce/(kw·h)改 为当量值0.1229 kgce/(kw·h) 时,新建或改扩建烧 结机生产设备烧结工序单位产品综合能耗限额准入 参考值应不大于51kgce/t。
v 本标准适用于钢铁企业进行烧结工序(不含球 团)、高炉工序、转炉工序和电炉工序单位产品 能耗的计算、考核,以及新建设备的能耗控制 。
粗钢生产工序能耗计算
二、标准规范性引用文件
v 下列文件中的条款通过本标准的引用而成为 本标准的条款。凡是注日期的引用文件,其 随后所有的修改单(不包括勘误的内容)或修订 版均不适用于本标准,然而,鼓励根据本标 准达成协议的各方研究是否可使用这些文件 的最新版本。凡是不注日期的引用文件,其 最新版本适用于本标准。
v 企业应定期对粗钢生产的几个主要工序能耗情况进行考核, 并把考核指标分解落实到各基层单位,建立用能责任制度。
v 企业应按要求建立健全能耗统计体系,建立能耗计算和考核 结果的文件档案,并对文件进行受控管理。
v 企业应根据GB 17167的要求配备能源计量器具,并建立能 源计量管理制度。
v 树立系统节能、管理节能的大局意识,从完善工艺操作流程 、提高系统的综合生产能力、产品合格率、设备作业率、利 用系数等方面开展综合节能工作;结合生产工艺改造、扩建 、新建,实现生产设备大型化,提高产能规模。
- 1、下载文档前请自行甄别文档内容的完整性,平台不提供额外的编辑、内容补充、找答案等附加服务。
- 2、"仅部分预览"的文档,不可在线预览部分如存在完整性等问题,可反馈申请退款(可完整预览的文档不适用该条件!)。
- 3、如文档侵犯您的权益,请联系客服反馈,我们会尽快为您处理(人工客服工作时间:9:00-18:30)。
二、其它能耗计算方法的资料
中国8个钢铁企业产量达千万吨
近几年中国钢铁工业生产规模明显扩大,年产钢1000万吨以上的企业已有8家,年产钢500万吨以上的共有1 7家,年产钢300万吨以上的有30多家。
2005年产钢1000万吨以上企业由2000年的1家(宝钢)上升到8家(宝钢、鞍钢、唐钢、武钢、首钢、沙钢、济钢、莱钢),合计产钢万吨,占全国钢产量的%。
产钢大于500万吨小于1000万吨企业由2000年的3家(鞍钢、首钢、武钢)上升到2005年的9家 (马钢、华菱钢铁、包钢、邯钢、攀钢、安阳钢铁、太钢、酒钢、建龙钢铁),合计产钢万吨,占全国钢产量的17. 17%。
产钢300万吨以上企业共30家,合计产钢万吨,占全国钢产量的%。
据介绍,中国钢产量已由2000年的亿吨上升到2005年的亿吨,钢产量占世界钢产量的比例由2000年的%上升至2005年的%。
标准煤系数就是把某一能源品种的实物量折合成标准量时所采用的系数,换句话说,就是单位能源的实际发热值与7000千卡的比率:即:
单位能源的实际发热值
=该能源品种折标准煤系数
7000千卡
例如:1公斤焦炭的平均低位发热量为6800千卡,其折标准煤系数为:6800千卡÷7000千卡=。
也就是说,1公斤焦炭相当于0.9714公斤标准煤,1000吨焦炭相
当于吨标准煤。
在企业内部同一能源品种,由于到货时间、供货单位的不同,其实际发热值也不一样。
在此情况下,确定企业标准煤系数,一般采用“加权算术平均数”的计算方法,加权算术平均数是反映次数结构影响的算术平均数,它的计算方法是总体各标志值(变量值)乘以相应的次数(权数)之和与总次数(总权数)的比。
例如:某企业2002年5月份先后从枣庄、肥城、山西、兖州等地购入原煤的实际数量分别为150吨、175吨、250吨、250吨,每次到货后实测发热值分别为4910千卡/公斤、4509千卡/公斤、5101千卡/公斤、5250千卡/公斤,这些原煤在本月全部消耗,那么该企业5月份消耗煤炭折标准煤吨,折标准煤系数为。
即:折标准煤=150×4910+175×4509+250×5101+250×5250
7000
=(吨)
折标准煤系数=错误!=
计算折标准煤系数时可将上两步合为一步求得:即
折标准煤系数=150×4910+175×4509+250×5101+250×5250
7000
÷825=错误!=
由此可以得出计算任一能源品种在某一时期内折标准煤系数的一般计算公式为:
某一时期任一能源品种折标准煤系数 =
∑〔
某一批能源
品种购入量
×
该品种能源平
均低位发热量
〕
7000千卡
÷该能源某一
时期内购入量之和
能源品种折标准煤系数的确定
(一)煤炭折标准煤系数的确定
可按下列顺序依次确定:l、由实测计算确定。
2、如不具备实测条件,可用煤矿发货单上的发热量计算出。
3、按照当年能源统计制度规定的参考系数。
(二)焦炭折标准煤系数的确定
有条件的单位应实测计算,否则用当年统计制度规定的参考系数计算。
(三)天然气折标准煤系数的确定
有条件的单位应按气田天然气、油田伴生气、煤田天然气(即煤矿瓦斯气)分别实测计算,否则以当年统计制度规定的折算系数折标(即每立方米天然气折1.3300公斤标准煤,每万立方米天然气折吨标准煤)。
(四)热力折标准煤系数的确定及其换算
热力主要指蒸汽和热水量。
蒸汽分为饱和蒸汽和过热蒸汽。
热力的计算单位现行统计报表制度要求统一换算为“百万千焦”或“万百万千焦”。
其换算关系为:以“卡”作单位转换为以“焦耳”作单位及其折标准煤系数。
1千卡=千焦,
1百万千卡=百万千焦=吨标煤
1万百万千卡=万百万千焦=万吨标煤。
以“焦耳”作单位转换为以“卡”为单位及折标准煤系数。
l千焦=千卡
1百万千焦=百万千卡=吨标煤
1万百万千焦=万百万千卡=万吨标煤
各种能源折标准煤参考系数
注:此表平均低位发热量用千卡表示,如需换算成焦耳,只需乘上即可。
吨钢综合能耗
包括从铁水(原料)进厂到钢锭(坯)出厂全部工艺过程中所消耗的一次和二次能源。
铁水预处理、连铸工艺、炉外精炼、电除尘设备等的燃料(含煤气、燃油)消耗及服务于炼钢的各种蒸汽、压缩空气、电力等动力消耗,都要计入炼钢工序能耗中,按其平均低位发热量折算标准煤。
计算公式为:
吨钢综合能耗(千克标准煤/吨)
=炼钢燃料
消耗量
+
动力
消耗量
-
转炉煤气余热
回收外供量
(千克标准煤)
钢产量(吨)
注:为方便计算,规定子项单位为吨标准煤,母项单位为吨。
计算结果乘以1000。
吨钢可比能耗(联合企业)
指企业每生产一吨钢,从炼铁、炼钢直到成材配套生产所必需的耗能量及企业燃料加工与输送、机车运输能耗及企业能源亏损量之和,折算成标准煤。
计算列于下表:
钢铁企业吨钢可比能耗计算方法
L=E·e+F+M+ H·h
+I+J+K
.钢铁企业吨钢可比能耗计算方法
工序
部位
工序单位能耗
吨标准煤/吨产品
(1)钢比或铁比
吨产品/吨钢(铁)
(2)可比能耗的组成
吨标准煤/吨钢
(1)×(2)
备注
焦化
A
a=(烧结,球团,炼铁)耗焦量/全铁折合产量
A・a
a b c为折算铁比系数,只适用于能耗指标计算烧结
B
b=烧结矿消耗量/全铁折合产量
B・b
球团
C
c=球团矿消耗量/全铁折合产量
C・c
炼铁
D=炼铁工序能耗/全铁折合产量
1=炼铁工序能耗/全铁产量
E= A・a+ B・b+ C・c+ D
e:吨钢耗生铁量
E・e
D:炼铁工序折合全铁单位能耗;
D1:炼铁工序全铁单位能耗;
E:企业吨铁单位能耗;
转炉
电炉
其他炉
连铸
F1
F2
F3
F4
f 1转炉钢率
f2电炉钢率
f3其他炉钢率
f4连铸钢率
(f 1+ f2+ f3=1)
F= F1・f 1+ F2・f2
+ F3・f3+ F4・f4
连铸能耗属炼钢工序
开坯
G:初轧单位能耗
g・[1― (连铸坯量+直接成材耗锭量)/ (初轧耗锭量+连铸坯量+直接成材耗锭量)] M=初轧开坯累计耗能量/(初轧耗锭量+连铸坯量+直接成材耗锭量)
1.式中连铸坯量系企业直接成材消耗的连铸坯量;
2.在特钢企业用钢锭成材时,生产的锻钢件(材)可按直接成材处理;
=G・g・[1― (连铸坯量+直接成材耗锭量)/ (初轧耗锭量+连铸坯量+直接成材耗锭量)]
g.初轧钢坯成坯率
轧材
H=轧材耗能量/企业最终钢材产量
h: 企业由钢到材的综合成材率
H・h
机车
I=运输能耗量/企业钢产量
燃气加工与输送
J=燃气加工与输送耗量/企业钢产量
企业能源亏损
K=企业能源亏损量/企业钢产量
企业吨钢可比能耗
L=E・e+F+M+ H・h0+I+J+K
―― 规模以上工业统计报表制度
规模以上工业统计报表制度――。