铜及铝板带轧制过程中轧机不稳定因素探讨
板带材轧机中辊系误差对轧制精度的影响研究

板带材轧机中辊系误差对轧制精度的影响研究概述板带材轧机是一种常见的金属加工设备,广泛应用于钢铁、有色金属等行业。
在板带材的轧制过程中,轧机中辊系的精度对于产品的成形质量具有重要影响。
因此,研究板带材轧机中辊系误差对轧制精度的影响,对于优化生产工艺、提高产品质量具有重要意义。
一、轧机中辊系误差类型及对轧制精度的影响轧机中辊系误差主要包括凸度误差、偏心误差和直线误差等。
这些误差会直接导致板带材在轧制过程中出现形状和尺寸方面的变化,严重影响产品的成形质量。
1. 凸度误差凸度误差是指辊子在轧制过程中出现的弯曲凹凸现象。
这种误差会导致板带材在轧制过程中受到非均匀的应变,从而影响产品的尺寸和形状。
若凸度误差较大,会导致板带材出现弯曲或塑性变形,严重影响产品的成形质量。
2. 偏心误差偏心误差是指轧机辊子的旋转轴线与材料的轧制轴线不重合所引起的误差。
当偏心误差较大时,会导致轧机在轧制过程中施加的压力不均匀,从而使板带材出现尺寸不匀或形状偏斜的问题,影响产品的外观和质量。
3. 直线误差直线误差是指辊子表面的直线度偏离理论直线度的程度。
辊子的直线度与板带材成形的直线度密切相关,直线误差过大会导致轧制后的板带材出现波浪形状,影响产品的平整度和表面质量。
二、轧机中辊系误差的产生原因板带材轧机中辊系误差的产生主要有以下几个原因:1. 制造误差:轧机辊子的制造和安装过程中存在一定的误差。
例如,加工辊子的磨床或研磨机床的几何精度不足,或者安装过程中的定位误差,都会导致辊子的几何形状不理想,进而引发辊系误差。
2. 磨损和变形:轧机辊子在长时间的使用过程中,由于受到高压和高温的影响,会产生磨损和变形。
这些磨损和变形会导致辊子的几何形状发生变化,进而引发辊系误差。
3. 温度变化:板带材轧机在工作过程中,由于材料的变形和摩擦产生的热量,会导致辊子的温度发生变化。
这种温度变化会导致辊子的物理性质发生变化,进而引发辊系误差。
4. 油膜效应:轧机中的油膜是保证辊子与板带材表面之间形成薄膜的一种润滑方式。
轧机状态对轧制稳定性的影响

750
298.5
297.6
-0.008
0.050
0.9
是
F4
750
-0.037
0.050
4.1
是
290
285.9
F5
500
255.3
265.1
0.072
0.050
-9.8
否
F6
500
-0.039
0.050
5.8
是
276.9
271.1
F7
500
0.032
0.050-ຫໍສະໝຸດ .8是271.6276.4
2,同步性 设备系统旳同步性是确保稳定生产旳最基本旳条件,
例如:精轧机组两侧弯辊缸旳同步性、两侧压下系统 (AGC)旳同步性、侧导板两侧动作旳同步性。设备系 统同步性旳好坏主要取决于设备本身固有旳特征。
3,一致性 实际生产过程中轧机体现出来旳一致性,是衡量轧机
状态旳主要原则,它能够直接反应轧机目前旳状态是否 稳定。
辊缝弹跳
辊缝弹跳差 差(原则 )
刚度差(DSOS)
是否达标
F1
750
305.5
304.3
-0.010
0.050
1.2
是
F2
750
312.0
307.8
-0.033
0.050
4.2
是
F2
750
297.7
298.6
0.008
0.050
-0.9
是
F3
750
298.0
288.7
-0.081
0.050
9.3
否
F3
时间、材质横截面积旳大小、灌浆旳质量、地脚螺 栓直径及拉拔力旳大小等。 影响辊系刚度旳原因
最新整理铜及铝板带轧制过程中轧机不稳定因素探讨.docx

最新整理铜及铝板带轧制过程中轧机不稳定因素探讨在铜及铝板带轧制过程中难免会发生不稳定现象,导致这种现象的原因较多,其问题主要集中在轧机上,从而对带材高精度生产造成严重影响。
于有色金属板的性能区别于钢铁的性能,因此对轧机的要求有所不同。
本研究中,笔者对轧机轧制过程中不稳定现象从工艺、设备等的角度进行分析,以供同行工作者参考。
当前,随着科学技术的日益发展,在有色金属的加工技术中,对板带材精度和质量随之提出了更高的要求。
为确保轧机轧制在板带轧制过程中的稳定性,消除外扰因素很重要,只有认真发现铜及铝板带轧制过程中存在的一些问题,才能消除于这些不稳定因素的发生导致产品质量出现问题的现象。
轧机系统稳定性受轧制材料的质量的影响1.1轧制过程中发生辊颤与材料相关采用铸轧坏料在铝粗轧机进行轧制的调试时,通常采用轧制速度及压下量等常规轧制工艺参数,整个轧机有时会发生颤动的现象,这使工艺参数的调整受到影响。
出现这种现象主要是因铸轧坯料铸轧后表面氧化膜化厚,其主要因放置时间较长所致,材料表面性能及其内部组织在长时间后均会发生变化,使轧材与辊面的摩擦系统不断降低,再加上摩擦力与咬入力小较,而导致打滑的现象发生,而导致轧辊颤振。
1.2来料偏差不宜过大一般试验过程中经常采用厚度偏差不同的带坯,而轧制厚度偏差的带坯为0.1~0.12mm时,相比0.15mm的轧制厚差带坯,轧机稳定性较高。
轧机系统稳定性受工艺润滑剂的影响经常发生辊颤还有一个重要原因是于润滑剂与所选择的工艺参数不匹配,对于轧机系统的振动因被轧金属与辊缝处辊面之间的摩擦因素而受到影响主要体现在以下几个方面:(1)在轧机系统的垂直运动中辊缝的润滑油膜能起到一定的阻尼作用,其阻尼作用在油膜摩擦系数越低的情况下越小,则会降低系统的稳定性质,轧机在外部等量扰动的情况下极易发生振动;(2)在充分润滑的条件下,会减小辊缝摩擦,而在干扰因素不稳定的情况下,辊缝状态的波动会增大,则会严重影响到系统的稳定性;(3)辊缝的摩擦系数越小,轧机轧制压力所受到的摩擦压力也就越小,轧制压力受到轧制张力的影响也就越大,从而会降低轧机系统的稳定性,使轧机容易发生振动。
铜带轧机调试过程中的问题及解决办法
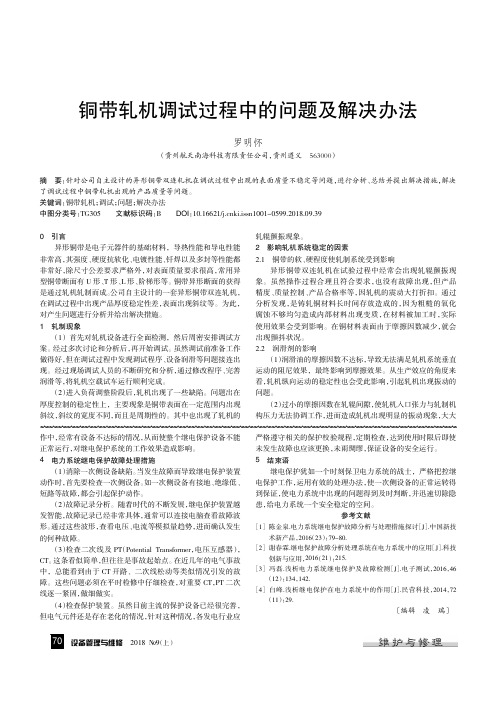
设备管理与维修2018翼9(上)铜带轧机调试过程中的问题及解决办法罗明怀(贵州航天南海科技有限责任公司,贵州遵义563000)摘要:针对公司自主设计的异形铜带双连轧机在调试过程中出现的表面质量不稳定等问题,进行分析、总结并提出解决措施,解决了调试过程中铜带轧机出现的产品质量等问题。
关键词:铜带轧机;调试;问题;解决办法中图分类号:TG305文献标识码:BDOI :10.16621/ki.issn1001-0599.2018.09.390引言异形铜带是电子元器件的基础材料,导热性能和导电性能非常高,其强度、硬度抗软化、电镀性能、钎焊以及多封等性能都非常好,除尺寸公差要求严格外,对表面质量要求很高,常用异型铜带断面有U 形、T 形、L 形、阶梯形等。
铜带异形断面的获得是通过轧机轧制而成。
公司自主设计的一套异形铜带双连轧机,在调试过程中出现产品厚度稳定性差,表面出现斜纹等。
为此,对产生问题进行分析并给出解决措施。
1轧制现象(1)首先对轧机设备进行全面检测,然后周密安排调试方案。
经过多次讨论和分析后,再开始调试。
虽然调试前准备工作做得好,但在调试过程中发现调试程序、设备润滑等问题接连出现。
经过现场调试人员的不断研究和分析,通过修改程序、完善润滑等,将轧机空载试车运行顺利完成。
(2)进入负荷调整阶段后,轧机出现了一些缺陷。
问题出在厚度控制的稳定性上,主要现象是铜带表面在一定范围内出现斜纹,斜纹的宽度不同,而且是周期性的。
其中也出现了轧机的轧辊颤振现象。
2影响轧机系统稳定的因素2.1铜带的软、硬程度使轧制系统受到影响异形铜带双连轧机在试验过程中经常会出现轧辊颤振现象。
虽然操作过程合理且符合要求,也没有故障出现,但产品精度、质量控制、产品合格率等,因轧机的震动大打折扣。
通过分析发现,是铸轧铜材料长时间存放造成的,因为粗糙的氧化腐蚀不够均匀造成内部材料出现变质,在材料被加工时,实际使用效果会受到影响。
在铜材料表面由于摩擦因数减少,就会出现颤抖状况。
有色金属轧制设备常见故障及其维护研究

有色金属轧制设备常见故障及其维护研究【摘要】由于有色金属轧制设备所处的工作条件复杂,这就导致轧机出现故障的种类较多,严重影响了轧制的质量和效率。
本文主要介绍有色金属轧制设备主要部件的常见故障及其日常维护保养措施,以便更好地对其进行维护,提高有色金属轧制设备使用寿命和工作性能。
【关键词】有色金属;轧制设备;检修;维护有色金属轧制设备中最主要的就是轧机,它是使轧件在转动的轧辊间产生塑性变形,轧出所需断面形状和尺寸的钢材。
主要由轧辊、轧辊轴承、机架压下装置、轨座和导位装置等组成。
由于其所处的工作环境往往是伴随着高温、潮湿、摩擦、粉尘、重负载等等,,这些因素使轧机的各部件容易产生种种故障。
如不及时发现和处理,不仅会影响正常生产,造成企业重大经济损失,甚至会酿成灾祸。
1 常用的轧制设备故障检测方法(1)机械测量法。
是利用机械器具对对被测物理量进行直接测量。
如用杠杆应变计测量应变,用机械测振仪测量轧机振动参量等。
(2)光测法。
是利用光学的基本理论,用实验的方法去研究物体中的应力、应变和位移等力学问题。
如光弹法、云纹法、红外测温仪测温以及激光扫描测径仪测量轧辊直径等。
(3)声测法。
是利用声波或超声波在介质中的传播速度和波形衰减情况估价被测物质的质量。
如超声波测量仪来检测轧机部件的抗拉强度和内部缺陷等。
(4)电测法。
是先将被测物理量转换成电量,再用电测仪表进行测量的方法。
如用电阻应变仪表测量应力应变,用热电高温计测温度,用涡流检测仪检测轧辊内部缺陷等。
2 轧制设备轧辊的故障检修及维护措施轧辊是轧制设备的重要组成部件,其主要用于轧制过程中使有色金属产生塑性变形,以生产不同尺寸的有色金属板带材产品,轧辊正常稳定的运行对提高产品的数量和质量都起着至关重要的作用。
因此,对其故障进行高效检修和维护显得十分重要2.1 轧辊常见故障及其产生原因轧辊常见的失效方式主要有辊身表面出现崩坑或裂纹、辊体断裂、辊体硬度衰变等三个方面。
铝轧机板形等质量问题分析及采取措施

铝轧机板形等质量问题分析及采取措施一、板形不良.1、冷轧机:(1)每三个月由钳工检查一次喷杆梁的减振喉是否损坏.及时更换(2)每两个月由操作手和电工一起检查喷嘴是否有堵塞或者在轧制时,操作手发现板形明显不良或者喷嘴喷油异常时,马上对喷嘴进行测试检查.(3)针对不同宽度,不同厚度,操作手及质检作好记录,并及时通知设备部进行一起分析,是否需要对板形目标曲线进行更改及试验(不同的板形目标曲线会对喷淋产生一定的影响). (4) 有些薄板,建议操作手可以进行手动喷淋干预,总结分析板形不良原因.(5)所有辊系检测每季度一次,由技术组完成,水平度及平行度。
2、粗轧机:(1)建议要求厂家增加手动调节喷淋功能(因为粗轧机不能对局部喷油进行手动干预,其不良板形只能通过弯辊,倾斜等手段进行辊型控制).(2)定期检查压平辊平行及水平度.1次/季度。
(3)每两个月由操作手和电工一起检查喷嘴是否有堵塞或者在轧制时,操作手发现板形明显不良或者喷嘴喷油异常时,马上对喷嘴进行测试检查.(4)工艺道次合理安排,张力合理使用,轧辊凸度建议尝试支承辊凸度0.02mm;工作辊凸度0.05-0.07mm.3、精轧机:(1)定期检查喷杆梁喷嘴.(2)定期检查压平辊平行及水平度.1次/季度(3)喷射梁及板型仪备品备件要尽快订货,因为膜片及滤芯都是消耗品需定期更换。
(4)工艺道次合理安排,张力合理使用,轧辊凸度建议尝试支承辊凸度0.02mm;工作辊凸度0.05-0.07mm.针对以上情况,将对三台轧机定期作以下的检查和测试:(1)定期对入口张紧辊进行检查辊系.(2)定期对板形辊平行度,水平度进行检查.(3)定期对工作辊辊隙进行检查.(4)定期对轧制线进行检查.(5)对薄板的局部板形不良,操作手是否可以采用手动调节喷淋,对相同的铝卷进行持续跟踪和比较.二、打底印.1、目前对部分变形的套筒进行车削,保证套筒的外圆一致。
2. 生产要加强套筒管理严格区分退火用套筒和非退火用套筒,决不能混用3、合理使用张力速度,匹配要合理.三、铝粉堆积1、入口可增加板面清洗装置.2,加强板式过滤器维护,确保过滤能力满足生产需求3,定期换纸,严格执行硅藻土及白土纤维素的添加工艺,搅拌箱内不能吸空4,每班要对轧制油透光率进行检测设备部2017-4-18。
轧制缺陷及质量控制
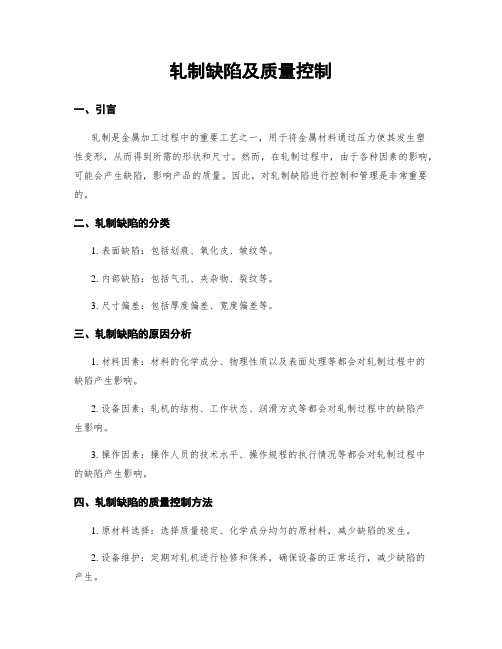
轧制缺陷及质量控制一、引言轧制是金属加工过程中的重要工艺之一,用于将金属材料通过压力使其发生塑性变形,从而得到所需的形状和尺寸。
然而,在轧制过程中,由于各种因素的影响,可能会产生缺陷,影响产品的质量。
因此,对轧制缺陷进行控制和管理是非常重要的。
二、轧制缺陷的分类1. 表面缺陷:包括划痕、氧化皮、皱纹等。
2. 内部缺陷:包括气孔、夹杂物、裂纹等。
3. 尺寸偏差:包括厚度偏差、宽度偏差等。
三、轧制缺陷的原因分析1. 材料因素:材料的化学成分、物理性质以及表面处理等都会对轧制过程中的缺陷产生影响。
2. 设备因素:轧机的结构、工作状态、润滑方式等都会对轧制过程中的缺陷产生影响。
3. 操作因素:操作人员的技术水平、操作规程的执行情况等都会对轧制过程中的缺陷产生影响。
四、轧制缺陷的质量控制方法1. 原材料选择:选择质量稳定、化学成分均匀的原材料,减少缺陷的发生。
2. 设备维护:定期对轧机进行检修和保养,确保设备的正常运行,减少缺陷的产生。
3. 工艺控制:严格控制轧制工艺参数,如轧制温度、轧制速度等,以减少缺陷的发生。
4. 检测手段:采用先进的无损检测技术,如超声波检测、X射线检测等,及时发现并排除缺陷。
5. 操作培训:加强操作人员的培训,提高其技术水平和操作规范性,减少人为因素对缺陷的影响。
五、轧制缺陷的质量控制效果评估1. 缺陷检测率:通过统计检测到的缺陷数量和总产量,计算缺陷检测率,以评估质量控制的效果。
2. 缺陷修复率:通过统计修复的缺陷数量和检测到的缺陷数量,计算缺陷修复率,以评估质量控制的效果。
3. 产品合格率:通过统计合格产品的数量和总产量,计算产品合格率,以评估质量控制的效果。
六、案例分析以某钢铁公司的轧制生产线为例,该公司采用了上述的质量控制方法,并进行了持续的改进。
经过一段时间的实践,缺陷检测率从原来的10%降低到了5%,缺陷修复率从原来的50%提高到了80%,产品合格率从原来的80%提高到了95%。
铜板带在粗轧完以后经常在边部看到一条明显的起皮是什么原因?

铜板带在粗轧完以后经常在边部看到一条明显的起皮是什么原因?铜板是一种常用的金属材料,被广泛应用于建筑、电子、航空等多个领域。
然而,在生产过程中,铜板带在粗轧完以后经常会出现边部起皮的情况,这会降低铜板带的品质和使用寿命。
本文将从铜板的制造工艺、材料特性、轧制参数等多个方面来探讨铜板带起皮的原因,并提出相应的解决办法。
制造工艺铜板的制造工艺包括锭化、浇铸、轧制、退火等多个环节。
在轧制过程中,将铜锭放入轧机中进行轧制,使其逐渐变薄。
这个过程通常需要经历多道工序,每道工序会将铜板带的厚度减少一定的比例。
在每道工序中,都要对轧制参数进行调整,以确保铜板带能够顺利地通过轧机,并且保持良好的表面质量。
边部起皮可能与轧制工艺有关。
在轧制过程中,铜板带会经过拉伸、弯曲等多个力学变形过程,这会导致边部应力过大,从而引起边部起皮。
同时,在冷轧过程中,由于金属的韧性有限,边缘区域较易产生硬化,这也可能是边部出现起皮的原因。
材料特性铜板的高导电性、高热传导性以及良好的可加工性是其重要的特性,但这些特性也可能会影响铜板在冷轧过程中的表现。
在冷轧过程中,铜板会发生较大的塑性变形,因此,其晶粒会被极大地拉长。
在铜板晶粒拉长的同时,它的位错密度也会随之增加,这会使得边部区域的应力和位错密度比中心区域高得多。
同时,铜板的金属组织和化学成分也会影响铜板在冷轧过程中的表现。
如果铜板的化学成分不均匀,或者含有过多的杂质,都有可能导致钢材硬化不均匀,从而引起边部起皮。
轧制参数轧制参数是决定铜板带品质的重要因素。
在冷轧过程中,轧制的质量和轧制参数的选择对铜板带的品质有着直接影响。
轧制参数如轧制压力、轧制速度、辊缝等参数都会对铜板带的品质产生重要影响。
辊面的状况也会影响边部的起皮情况。
如果辊面粗糙,那么在铜板带经过辊面时就会容易产生起皮现象。
因此,高质量、平整的辊面是确保铜板带表面质量的重要保障。
解决办法为确保铜板带的品质,可以采取以下几种措施:1.加强材料检测:在生产过程中,对铜板的化学成分、金属组织等进行严格检测,确保铜板的质量符合标准。
- 1、下载文档前请自行甄别文档内容的完整性,平台不提供额外的编辑、内容补充、找答案等附加服务。
- 2、"仅部分预览"的文档,不可在线预览部分如存在完整性等问题,可反馈申请退款(可完整预览的文档不适用该条件!)。
- 3、如文档侵犯您的权益,请联系客服反馈,我们会尽快为您处理(人工客服工作时间:9:00-18:30)。
铜及铝板带轧制过程中轧机不稳定因素探讨
Revised by Hanlin on 10 January 2021
铜及铝板带轧制过程中轧机不稳定因素探讨在铜及铝板带轧制过程中难免会发生不稳定现象,导致这种现象的原因较多,其问题主要集中在轧机上,从而对带材高精度生产造成严重影响。
由于有色金属板的性能区别于钢铁的性能,因此对轧机的要求有所不同。
本研究中,笔者对轧机轧制过程中不稳定现象从工艺、设备等的角度进行分析,以供同行工作者参考。
当前,随着科学技术的日益发展,在有色金属的加工技术中,对板带材精度和质量随之提出了更高的要求。
为确保轧机轧制在板带轧制过程中的稳定性,消除外扰因素很重要,只有认真发现铜及铝板带轧制过程中存在的一些问题,才能消除由于这些不稳定因素的发生导致产品质量出现问题的现象。
轧机系统稳定性受轧制材料的质量的影响
1.1轧制过程中发生辊颤与材料相关
采用铸轧坏料在铝粗轧机进行轧制的调试时,通常采用轧制速度及压下量等常规轧制工艺参数,整个轧机有时会发生颤动的现象,这使工艺参数的调整受到影响。
出现这种现象主要是因铸轧坯料铸轧后表面氧化膜化厚,其主要因放置时间较长所致,材料表面性能及其内部组织在长时间后均会发生变化,使轧材与辊面的摩擦系统不断降低,再加上摩擦力与咬入力小较,而导致打滑的现象发生,而导致轧辊颤振。
1.2来料偏差不宜过大
一般试验过程中经常采用厚度偏差不同的带坯,而轧制厚度偏差的带坯为0.1~0.12mm时,相比0.15mm的轧制厚差带坯,轧机稳定性较高。
轧机系统稳定性受工艺润滑剂的影响
经常发生辊颤还有一个重要原因是由于润滑剂与所选择的工艺参数不匹配,对于轧机系统的振动因被轧金属与辊缝处辊面之间的摩擦因素而受到影响主要体现在以下几个方面:(1)在轧机系统的垂直运动中辊缝的润滑油膜能起到一定的阻尼作用,其阻尼作用在油膜摩擦系数越低的情况下越小,则会降低系统的稳定性质,轧机在外部等量扰动的情况下极易发生振动;(2)在充分润滑的条件下,会减小辊缝摩擦,而在干扰因素不稳定的情况下,辊缝状态的波动会增大,则会严重影响到系统的稳定性;(3)辊缝的摩擦系数越小,轧机轧制压力所受到的摩擦压力也就越小,轧制压力受到轧制张力的影响也就越大,从而会降低轧机系统的稳定性,使轧机容易发生振动。
从上述分析中可以看出:轧机在辊缝摩擦系数较小的情况下容易发生振动。
轧机系统稳定性受轧制速度的影响
厂在调试一台冷轧机过程中,可看到轧机有严重的辊颤现象。
对轧机各部分性能进行检查,发现问题出现在轧制时轧机速度上,如将速度设定在4m/s时,其始终保持着3.9~4.1的传动速度,期间有出现周期性摆动,而导致轧机辊颤,并且有带材厚薄不均的现象。
通过对轧机主传动和卷取机电气反复调整后,在速度稳定的情况下,消除了辊颤的现象。
轧机系统的稳定性及其外部的扰动能量决定着其是否会发生自激振动,轧机系统会受到轧机轧制速度高低的影响,其主要体现在:(1)在轧制速度不断提高的情况下,轧机周围会有越来越多的扰动因素,并且扰动强度也越来越高,那么要确保其平稳就必须保证其速度较低;(2)轧制速度较低时,轧机谐振频率会高于外扰频率,不容易出现共振;而当轧制速度越高的情况下,其工作辊入口张力变化与运动的关系将越紧密,系统的自激关系也就越强烈,从而会增强各种外扰频率,轧机系统稳定性越差的情况下,便容易出现振动。
此外,轧机辊缝中的润滑情况也会受到轧制速度的影响。
润滑液膜在速度越高的情况下厚度越大,因此在辊缝一定时,带材的厚度公差会直接受到速度高低的影响。