滚珠丝杠驱动的加工中心
加工中心z轴原理

加工中心z轴原理
加工中心的Z轴原理是指加工中心在加工工件时,Z轴方向(垂直于工作台的方向)的运动原理。
Z轴通过控制系统,通过电动驱动装置和导轨滚动装置实现。
在加工中心中,Z轴的运动主要由电动驱动装置实现。
这种电动驱动装置通常为伺服电动机,通过控制系统发出指令,调节伺服电动机的运转,从而控制Z轴的运动。
伺服电动机将电能转化为机械能,推动导轨滚动装置,使工件在Z轴方向上进行升降运动。
导轨滚动装置是实现Z轴运动的关键部件。
它通常由导轨、滑块和滚珠螺杆组成。
滚珠螺杆将旋转运动转化为直线运动,滑块沿导轨滑动,使工件在Z轴方向上移动。
导轨滚动装置具有较高的刚性和准确度,能够保证加工中心在工件加工时的稳定性和精度。
通过控制系统对Z轴的运动进行精确控制,可以实现加工中心在加工过程中的Z轴位置调整。
根据不同的加工要求,可以通过控制系统设定Z轴的加工深度和速度,完成加工中心对工件的切削加工、孔加工和螺纹加工等操作。
加工中心的Z轴原理保证了加工过程中Z轴运动的准确性和稳定性,能够提高加工精度和加工效率,广泛应用于机械加工和零部件制造行业。
龙门加工中心丝杠辅助支撑系统的设计

渤
4
偏心 量
o.g/
装置结构 1.径 向顶丝 2.滑架 油封 3.传 动 箱 4.偏 心轴
5.斜齿轮轴套 6.通轴 7.限位盘 8.限位螺钉
Байду номын сангаас
平 时 液 压 缸 处 于 托 起 状 态 , 当 丝 杠
图2 液压原理 1.油箱 2.吸油过滤器 3.变量叶片泵 4.精过滤器 5.单向阀 6.测压垫板 7.减压阀
螺 母 接 近 托 8.换向阀 9.油路块 lO.风冷却器 11掖位发讯器
起 点 时 ,发 信 开 关 发 信 并 通 过 系 统 换 向 阀 换 向 ,
2.解决方案 为 了 解 决 大 行 程 丝 杠 驱 动 过 程 中的 丝 杠 下 垂 问题 , 我 们 设 计 了一 套 解 决 方 案 ,利 用 液 压 缸 及 导 向 ,在 丝 杠 的 中 段 取 一 个 或 两 个 点 ,作 为 托 起 点 , 目的是减 少在此位置的变形 。如 图2所 示液压 原理 ,如果是一个点的话 ,就通过一个发信开关发 信 。 两 位 四 通 电磁 阀 8得 电 电磁 阀 换 向 。该 托 起 液 压系统工作原理是通过 变量 叶片泵3提供 系统工作
心 运 动 ,进 而 带 动 通 轴 6进 行 偏 心 振 动 。 当 需 要 调 整 偏 心 量 时 , 可 先 松 开 限 位 螺 钉 8,转 动 偏 心 轴 4, 当斜 齿 轮 轴 套 5与 偏 心 轴 4圆 心 重 合 时 ,偏 心 为 零 ,反 之 则 产 生 偏 心 。调 整 好 后 ,将 限 位 螺 钉 旋 紧 顶 在 限 位 盘 7上 (限 位 盘 圆 周 有 沟 槽 可 定 位 ) 。
加工中心40刀刀库(链式刀库)-说明书
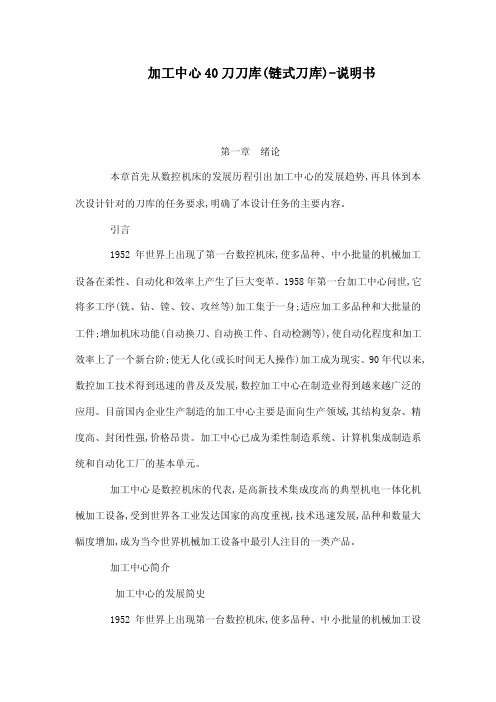
加工中心40刀刀库(链式刀库)-说明书第一章绪论本章首先从数控机床的发展历程引出加工中心的发展趋势,再具体到本次设计针对的刀库的任务要求,明确了本设计任务的主要内容。
引言1952年世界上出现了第一台数控机床,使多品种、中小批量的机械加工设备在柔性、自动化和效率上产生了巨大变革。
1958年第一台加工中心问世,它将多工序(铣、钻、镗、铰、攻丝等)加工集于一身;适应加工多品种和大批量的工件;增加机床功能(自动换刀、自动换工件、自动检测等),使自动化程度和加工效率上了一个新台阶;使无人化(或长时间无人操作)加工成为现实。
90年代以来,数控加工技术得到迅速的普及及发展,数控加工中心在制造业得到越来越广泛的应用。
目前国内企业生产制造的加工中心主要是面向生产领域,其结构复杂、精度高、封闭性强,价格昂贵。
加工中心已成为柔性制造系统、计算机集成制造系统和自动化工厂的基本单元。
加工中心是数控机床的代表,是高新技术集成度高的典型机电一体化机械加工设备,受到世界各工业发达国家的高度重视,技术迅速发展,品种和数量大幅度增加,成为当今世界机械加工设备中最引人注目的一类产品。
加工中心简介加工中心的发展简史1952年世界上出现第一台数控机床,使多品种、中小批量的机械加工设备在柔性、自动化和效率上产生了巨大变革。
它用易于修改的数控加工程序进行控制,因而比大批量生产重使用组合机床生产线和凸轮、开关控制的专用机床有更大的柔性,容易适应加工件品种的变化,进行多品种加工。
它用数控系统对机床的工艺功能、几何图形运动功能和辅助功能实行全自动的数字控制,因为有更高的自动化程度和加工效率,大大改变了中小批量生产中普通机床占整个机械加工的状况。
数控机床能实现两坐标以上联动的功能,其效率和精度比用手工和样板控制加工复杂零件要高得多。
1958年第一台加工中心在美国卡尼、特雷克(Kearney&Trecker)公司问世。
现代加工中心的内容是什么?第一,它是在数控镗床或数控铣床的基础上增加自动换刀装置,可使工件在一次装卡中,能够自动更换刀具,自动完成工件上的铣削、钻孔、镗孔、铰孔、攻丝等工序的数控机床。
SKM25-B数控加工中心

SKM25-B数控加工中心适用范围:木工行业:各种门,窗,橱柜,工艺木门,免漆门,屏风,工艺扇窗,波浪板加工等各种家具,木艺的加工。
广告行业:广告标牌,标示制作,广告用料切割,吸塑制模,LED 霓虹灯制作等多种材料广告装饰产品的制作。
工艺品行业:可在木质,竹,人造大理石,有机板,双色板,水晶等材料上进行各种精美图案和文字的雕刻。
适用材料:各种木质材料;铝板,铝塑板,塑料板;PVC、亚克力、双色板、密度板、水晶板等广告材料;及人造软大理石等非金属及轻金属材质。
雕刻效果:可以雕刻各种浮雕,影雕,透雕,平面雕刻,切割,洗底等各种效果。
性能特点:◆床体钢结构无缝焊接,坚固耐用,不易变形。
◆Z轴采用德国产滚珠丝杠,进口直线导轨,精度高更耐用。
X.Y轴采用齿条传动,速度更快,更好的提高效率,节省成本。
◆软件兼容性强,可兼容type3/artcam/castmate/文泰等多种CAD/CAM设计制作软件,具有刀具补偿、中文显示、后台编辑、主轴多点定位、模拟操作显示、故障显示功能。
◆台湾宝元(新代)控制系统.操作更简单,斗笠式自动换刀系统,。
意大利进口换刀主轴驱动系统采用日本安川伺服驱动电机,驱动器,功能齐全性能稳定,精度更高◆自动油路润滑系统,维护、保养更方便。
真空吸附台面,加工异性工件更加轻易自如,喜力更强,可达160立方/小时◆拥有断点续雕、断电恢复、加工时间预测等功能。
◆设计更加人性化,不论大力切割还是精雕细琢都能得心应手。
技术参数:型号SKM25-B 进料高度300mm床体结构钢结构主轴速度24000r/min雕刻范围1300*2500mm冷却方式风冷(意大利进口HSD)平台尺寸1440*3040mm雕刻指令G代码,HPGL,U00,mmg,plt分辨率0.01mm吸尘功能有主轴功率9KW吸附功能真空吸附工作电压AC380V/50HZ操作系统台湾宝元(新代)最大运行速度70m/min刀柄直径φ3.175-φ12.7刀库个数8个工作方式伺服。
桥式龙门说明629

桥式数控龙门车铣加工中心技术说明中传重型机床有限公司2013-61.机床概述桥式数控龙门车铣加工中心是中传重型机床有限公司在吸收了当今国际上先进的数控龙门镗铣床制造技术,自行研发的龙门车铣加工中心。
该机床采用优化设计手段,三维立体造型、CAM模拟仿真、有限元分析及模块化设计等方法,配置国内、外先进的功能部件,精心设计的专用产品,是集电气、液压控制和现代机械设计等多学科、多门类精密制造技术于一体的机电一体化机床产品。
机床主要应用了滚柱导轨导向系统,双驱同步驱动技术,高精度车铣转台技术等;并配置了西门子840Dsl数控系统和海德汉公司的位置检测系统,确保机床具有刚度好、效率高,可靠性强,功能稳定、操作方便、安全环保。
机床配备两数控轴万能铣头能够在一次装夹中,对一个零件内外五个不同表面进行钻孔、镗孔、切沟槽、以及平面的銑削加工。
机床配有数控车铣工作台可实现回转零件的车削和銑削的分度定位功能。
机床可选配延伸铣头、直角铣头、窄直角铣头等。
机床设有链式刀库和附件头库,并能实现自动更换,从而缩短了辅助时间、大幅度提高了生产效率。
机床的组成:机床采用分离传动;配有固定工作台、数控车铣工作台、龙门移动式结构布局。
1.1主运动主传动采用滑枕内置主电机,带有双速齿轮箱,变速驱动附件铣头的旋转运动。
主运动挡内无级调速。
1.2进给运动X轴-龙门架沿床身导轨水平纵向移动。
Y轴-滑座沿横梁导轨水平移动。
Z轴-滑枕沿滑座导轨垂直运动。
C轴-回转工作台回转分度运动。
A轴-万能铣头主轴的摆动运动。
C1轴-万能铣头的回转运动。
2.主要技术参数2.1固定工作台面宽度 1600 mm2.2固定工作台面长度 3000 mm2.3固定工作台承重 5000kg/m2.4两立柱间的最大距离 2200 mm2.5最大工件高度 1000 mm2.6滑枕端面至工作台面最大距离 1700 mm2.7龙门架纵向工作行程(X轴)3050mm2.8龙门架纵向总行程 5195 mm2.9滑座水平行程(Y轴)±1375mm2.10滑枕垂直行程(Z轴) 1000mm2.11龙门架纵向进给速度(X轴) 0-8000mm/min 2.12滑座水平进给速度(Y轴) 0-8000mm/min 2.13滑枕垂直进给速度(Z轴) 0-6000mm/min 2.14龙门架纵向快速移动速度(X轴) 8000mm/min2.15滑座水平快速移动速度(Y轴) 80000mm/min 2.16滑枕垂直快速移动速度(Z轴) 6000mm/min2.17方滑枕尺寸 360×360mm 2.18主轴最高转数 3000r/min2.19主电机功率 35kW2.20数控万能铣头功率 17 kW转速 11890r/min扭矩 13.7NmA轴±120°C1轴+90°/-450° 2.21数控回转工作台工作台最大扭矩 19kNm工作台转速级数(机械二档)档内无级工作台转速范围车削 2.5-250r/min銑削 0-5r/min2.22 数控系统 SIEMENS840Dsl2.23数控轴数主轴加6数控轴2.24联动轴数 4轴联动2.25机床所需压缩空气气压0.6Mpa2.26 机床总重量约(不含附件铣头)76 t2.27机床外形尺寸(长×宽×高)9250×5150×5800mm机床精度定位精度X轴全行程定位精度0.040mmY轴全行程定位精度0.022mmZ轴全行程定位精度0.012mm重复定位精度X轴的重复定位精度0.01mmY轴的重复定位精度0.008mmZ轴的重复定位精度0.008mm3.机床主要结构及性能机床为工作台固定、龙门架移动式、并配备数控回转工作台,实现车铣功能。
JCS018加工中心研究特选
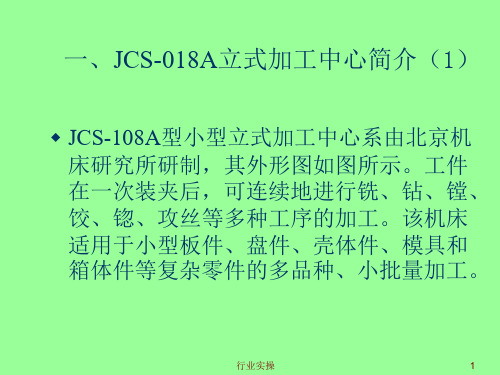
行业实操
17
五、典型部件结构(3)
自动换刀装置(ATC)(2)
刀套下转90° 本机床的刀库位于立柱左侧,刀具在 刀库中的安装方向与主轴垂直,如图7-24所示。换刀 之前,刀库2转动将待换刀具5送到换刀位置,之后把 带有刀具5的刀套4向下翻转90°,使得刀具轴线与主 轴轴线平行。
具有自动装卸刀具的机械手 在加工中心机床上 刀具的自动更换,多数借助机械手来进行。
具有主轴准停机构、刀杆自动夹紧松开机构和 刀柄切屑自动清除装置 这是加工中心机床主轴 部件中三个主要组成部分,也是加工中心机床 能够顺利地实现自动换刀所需具备的结构保证。
具有自动排屑、自动润滑和自动报警的系统等。
行业实操
28
五、典型部件结构(9)
机械手结构 (3)
抓刀动作结束时,齿条17上的挡环12压下位置开关14, 发出拔刀信号,于是液压缸15的上腔通压力油,活塞 杆推动机械手臂轴16下降拔刀。在轴16下降时,传动 盘10随之下降,其下端的销子8插入连接盘5的销孔中, 连接盘5和其下面的齿轮4也是用螺钉联接的,它们空 套在轴16上。当拔刀动作完成后,轴16上的挡环2压 下位置开关1,发出换刀信号。这时液压缸20的右腔 通压力油,活塞杆推着齿条19向左移动,使齿轮4和 连接盘5转动,通过销子8,由传动盘带动机械手转 180°,交换主轴上和刀库上的刀具位置。
轨迹控制方式
直线/圆弧方式或空间直线/螺旋方式
纸带代码
EIA/ISO
程序格式
写地址式可变程序段
脉冲当量
0.001㎜/脉冲
立式加工中心主轴部件设计
引言装备工业的技术水平和现代化程度决定着整个国民经济的水平和现代化程度,数控技术及装备是发展高新技术产业和尖端工业(如:信息技术及其产业,生物技术及其产业,航空、航天等国防工业产业)的使能技术和最基本的装备。
制造技术和装备是人类生产活动的最基本的生产资料,而数控技术则是当今先进制造技术和装备最核心的技术。
当今世界各国制造业广泛采用数控技术,以提高制造能力和水平,提高对动态多变市场的适应能力和竞争能力。
此外世界上各工业发达国家还将数控技术及数控装备列为国家的战略物资,不仅采取重大措施来发展自己的数控技术及其产业,而且在“高精尖”数控关键技术和装备方面对我国实行封锁和限制政策。
数控机床技术的发展自1953年美国研制出第一台三坐标方式升降台数控铣床算起,至今已有很多年历史了。
20世纪90年开始,计算机技术及相关的微电子基础工业的高速发展,给数控机床的发展提供了一个良好的平台,使数控机床产业得到了高速的发展。
我国数控技术研究从1958年起步,国产的第一台数控机床是北京第一机床厂生产的三坐标数控铣床。
虽然从时间上看只比国外晚了几年,但由于种种原因,数控机床技术在我国的发展却一直落后于国际水平,到1980年我国的数控机床产量还不到700台。
到90年代,我国的数控机床技术发展才得到了一个较大的提速。
目前,与国外先进水平相比仍存在着较大的差距。
总之,大力发展以数控技术为核心的先进制造技术已成为世界各发达国家加速经济发展、提高综合国力和国家地位的重要途径。
1 绪论1.1 加工中心的发展状况1.1.1 加工中心的国内外发展对于高速加工中心,国外机床在进给驱动上,滚珠丝杠驱动的加工中心快速进给大多在40m/min以上,最高已达到90m/min。
采用直线电机驱动的加工中心已实用化,进给速度可提高到80~100m/min,其应用范围不断扩大。
国外高速加工中心主轴转速一般都在12000~25000r/min,由于某些机床采用磁浮轴承和空气静压轴承,预计转速上限可提高到100000r/min。
HMS125p型精密卧式加工中心
精密 卧式加 工中心 , 具有高精 度 、 高速度 、 高刚性 、 大扭 矩等特
点 , 合 于 零 件 多 工 作 面 的铣 、 、 、 、 丝 、 维 、 维 曲 适 钻 镗 铰 攻 二 三
面等多下序加 j 【,能够 在一次 装夹 中完 成箱体 孔系 和平 面多
序 的精 密 加 工 , 箱 体 、 体 等 零 部 件 高 精 、 效 加 的 理 是 壳 高 想 设 备 , 泛 适 用 于 国 防 军 工 、 车 、 船 、 具 、 用 机 械 等 广 汽 造 模 通
() I整机结构对称 ’ 冈 陛好 , 受力 、 受热均匀 , 精度稳定 , 整机
及 重 要零 、 件 经 有 限元 软 件 分 析 和 优 化 设 计 , 有 较 高 的 动 、 部 具
静态 性 能 。
图 1 H 15 MS 2 p型 精 密 卧式 加 中心 结 构 示 意 图
冷却 圆筒机改进后的运行 表明, 设备运转平稳 , 流程连续稳 定, 密封效果 明显改善 , 现场环境 大大改观 , 劳动强度得到降低 ,
.
彻底解决了冷却圆筒 机在运行过程 中出现的问题 , 效果 良好 。
排 料装 置
W 1 . -2 1 04 4
筒 体
作者通联:白银有 色金属 集团公 司第三冶炼厂
行业 。
1 床结 构 和特 点 . 机
机床总体 布局 ( 1 为横 、 图 ) 纵床身组成 T字型结构 , 回转工
作 台在横床身上做 向运动 , 立柱在纵床 身上做 z向运 动 , 主轴
箱 沿 立 柱 做 Y向运 动 , 作 台绕 回转 中心 做 30 范 围 的 曰 轴 连 工 6。 续 转 动 , 可 与 、, 并 l、 联 动 控 制 。 机 床设 有 刀 库 和 双 交 换 工 z轴 作 台 , 成 刀具 及 工作 台 的 自动 交 换 , 完 以缩 短 加 工辅 助 时 间 , 提 高 工 作效 率 。机 床 的结 构 特 点 和技 术 性 能 如 下 。
vmc1000立式加工中心参数
vmc1000立式加工中心参数VMC1000立式加工中心是一种高精度、高效率的数控机床,具有良好的加工性能和广泛的应用领域。
下面将详细介绍其参数。
1.加工范围:VMC1000立式加工中心的X轴行程为1000mm,Y轴行程为600mm,Z轴行程为600mm,工作台尺寸为1100mm×600mm,能够满足不同尺寸的零件加工需求。
2.主轴:该加工中心配备一台功率为11/15kW的主轴,主轴最高转速可达8000转/分钟,可根据不同材料和加工要求进行调节。
主轴垂直于工作台,使得加工更加稳定。
3.控制系统:VMC1000立式加工中心采用国内外知名品牌的数控系统,具有简单易用的操作界面和丰富的加工功能。
用户可以通过操作面板或计算机进行程序输入和调整。
4.自动工具变换系统:该加工中心采用多台自动刀库,可容纳不同类型的刀具,实现自动的刀具变换功能。
工具变换速度快,节省了切削刀具更换的时间,提高了加工效率。
5.进给系统:VMC1000立式加工中心采用伺服电机驱动的直线导轨和滚珠丝杠,具有高速、高精度的进给性能。
进给速度可调,能够满足不同加工要求。
6.切削液系统:为了保证切削过程的稳定和工件表面的质量,VMC1000立式加工中心配备了切削液系统。
该系统能够及时对切削区域进行冷却和润滑,有效延长刀具使用寿命。
7.安全保护系统:在加工过程中,为了保障操作人员的安全,VMC1000立式加工中心配备了多种安全保护措施,如门锁、限位开关、紧急停机按钮等,可以有效避免因操作不当而导致事故的发生。
8.应用领域:VMC1000立式加工中心广泛应用于机械制造、汽车零部件、航空航天、模具制造、电子仪器等领域。
它能够加工各种材料,如铝合金、钢材、铜材等,可实现多种加工工艺,如铣削、钻孔、镗削等。
总结:VMC1000立式加工中心是一台高精度、高效率的数控机床,具备多种优秀的加工性能和功能。
它的参数从加工范围、主轴、控制系统、自动工具变换系统、进给系统、切削液系统、安全保护系统等方面进行了详细介绍。
HSM600U型5轴高速铣削加工中心故障处理1例
分析设备运转状况记 录,设备运行温度一直 比原厂交付使 用后 的 5 6 0 0 h 平均高 5 ~ 1 5 ℃。维修安装后运行 4 8 h左右 , 振动 筛 轴承箱就开始漏油 , 操作工补加润滑油 。每次出现故障前 , 轴
复 自由状 态 ,因此
轴 承压盖 带 轮 皮 带
十微米 , 每次漂动值完全 随机 , 与 轴停放位置也无关 系。故障
出现后 , 系统没有误差监控报警 , 加工工件精度也正常 。
2 . 故 障 处 理
图 1 加工 中心 轴结构
最初判断故障 由光栅 尺和编码器引起。按机床操作面板上
母、 丝杠右端轴承支撑不在 同一条线上 , 导致丝杠弯 曲。 机床门关 闭 ,门保护开关 闭 合, 驱 动上 电, 螺母
要 回到 系 统 原来 位
置 ,系统驱动电机
运 转 , 因此 显示 器
上 轴 坐 标 变 化 几十微米 。门打开 后 ,门保护开关 断 开 ,驱动和电机相 继断 电,丝杠要恢
M P 1 1 0 . 0 ( 该参数设置为 0 , 关 闭光栅尺 ; 设置 为 x1 , 轴光栅尺
电缆插 在主计算 机 m c 4 2 2的 x1 接 口;设置为 X 2 , X轴光栅尺 电缆插在 主计算机 m c 4 2 2的 X 2接 口) , 按“ E N T ” 键确认 , 搜 索 参 数。将参数 MP 1 1 0 . 0的值由 2 0 1 改为0 , 屏蔽光栅尺状态 。按
型号 2 Y H 2 1 6 0双层 双 振 幅振 动筛 装 机运 行 5 6 0 0 h后 ,
轴承 温度升 高至 1 1 0 ℃, U形 密封环 失效 漏油 , 导致 轴承抱 死
给激振 器主轴 两端 的轴承 , 瞬 间增 大轴 承 负荷 。当振 动筛 下 筛 面物 料铺满 时 ,振 动筛 承重在 1 0 0 0 k g ,再 加上 比原来 多 了一个 筛面 的负荷 , 振 动筛 总承 重超 过 2 5 0 0 k g , 在1 l m m 的 振 幅下 , 将 所有 势 能作 用在 轴承 上 , 对 轴 承来 说 使 用条 件 恶
- 1、下载文档前请自行甄别文档内容的完整性,平台不提供额外的编辑、内容补充、找答案等附加服务。
- 2、"仅部分预览"的文档,不可在线预览部分如存在完整性等问题,可反馈申请退款(可完整预览的文档不适用该条件!)。
- 3、如文档侵犯您的权益,请联系客服反馈,我们会尽快为您处理(人工客服工作时间:9:00-18:30)。
滚珠丝杠驱动的加工中心目录1 引言 (1)1.1 加工中心的发展状况 (1)1.1.1 加工中心在国外的发展 (1)1.1.2 主轴部件的研究进展 (2)1.2 课题的目的及容 (3)1.3 课题解决的关键问题 (3)1.4 解决上述问题的策略 (4)2 方案拟定 (5)2.1 加工中心主传动系统的组成 (5)2.2 机械系统方案的确定 (5)2.2.1 主轴传动机构 (5)2.2.2 主轴进给机构 (6)2.2.3 主轴准停机构 (6)2.2.4 刀具自动夹紧机构 (6)2.3 加工中心主轴组件总体设计方案的确定 (8)3 主轴组件的主运动部件 (10)3.1 主电机选型 (10)3.2 主轴 (10)3.2.1 主轴的结构设计 (10)3.2.2 主轴受力分析 (16)3.2.3 主轴的刚度校核 (20)3.2.4 主轴的强度校核 (21)3.3 主轴组件的支承 (22)3.3.1 主轴轴承的类型 (22)3.3.2 主轴轴承的配置 (24)3.3.3 主轴轴承的预紧 (25)3.3.4 主轴支承方案的确定 (26)3.3.5 滚动轴承的精度与配合 (27)3.3.6 主轴轴承设计计算 (27)3.4同步带的设计计算 (29)3.5主轴组件的润滑与密封 (32)3.5.1 主轴组件的润滑 (32)3.5.2主轴组件的密封 (32)3.5.3 本课题的润滑与密封方案的确定 (34)3.6 主轴上键的设计与计算 (34)3.7 液压缸的设计计算 (35)结论.......................................................... 错误!未定义书签。
参考文献. (37)致谢.......................................................... 错误!未定义书签。
1引言1.1加工中心的发展状况1.1.1加工中心在国外的发展对于高速加工中心,国外机床在进给驱动上,滚珠丝杠驱动的加工中心快速进给大多在40m/min以上,最高已达到90m/min。
采用直线电机驱动的加工中心已实用化,进给速度可提高到80~100m/min,其应用围不断扩大。
国外高速加工中心主轴转速一般都在12000~25000r/min,由于某些机床采用磁浮轴承和空气静压轴承,预计转速上限可提高到100000r/min。
国外先进的加工中心的刀具交换时间,目前普遍已在1s左右,高的已达0.5s,甚至更快。
在结构上,国外的加工中心都采用了适应于高速加工要求的独特箱中箱结构或龙门式结构。
在加工精度上,国外卧式加工中心都装有机床精度温度补偿系统,加工精度比较稳定。
国外加工中心定位精度基本上按德国标准验收,行程1000mm以下,定位精度可控制在0.006~0.01mm之。
此外,为适应未来加工精度提高的要求,国外不少公司还都开发了坐标镗精度级的加工中心。
相对而言,国生产的高速加工中心快速进给大多在30m/min左右,个别达到60m/min。
而直线电机驱动的加工中心仅试制出样品,还未进入产量化,应用围不广。
国高速加工中心主轴转速一般在6000~18000r/min,定位精度控制在0.008~0.015mm 之,重复定位精度控制在0.005~0.01mm之。
在换刀速度方面,国机床多在,无法与国际水平相比。
虽然国产数控机床在近几年中取得了可喜的进步,但与国外同类产品相比,仍存在着不少差距,造成国产数控机床的市场占有率逐年下降。
国产数控机床与国外产品相比,差距主要在机床的高速、高效和精密上。
除此之外,在机床可靠性上也存在着明显差距,国外机床的平均无故障时间(MTBF)都在5000小时以上,而国产机床大大低于这个数字,国产机床故障率较高是用户反映最强烈的问题之一。
1.1.2主轴部件的研究进展图1.1立式加工中心结构图1-切削箱 2-X轴伺服电机 3-Z轴伺服电机 4-主轴电机5-主轴箱 6-刀库 7-数控柜 8-操纵面板9-驱动电柜 10-工作台 11-滑座 12-立柱13-床身 14-冷却水箱 15-间歇润滑油箱 16-机械手典型加工中心的机械结构主要有基础支承件、加工中心主轴系统、进给传动系统、工作台交换系统、回转工作台、刀库及自动换刀装置以及其他机械功能部件组成。
图1.1 所示为立式加工中心结构图。
主轴系统为加工中心的主要组成部分,它由主轴电动机、主轴传动系统以及主轴组件成。
和常规机床主轴系统相比,加工中心主轴系统要具有更高的转速、更高的回转精度以及更高的结构刚性和抗振性。
随着电气传动技术(变频调速技术、电动机矢量控制技术等)的迅速发展和日趋完善,高速数控机床主传动的机械结构已得到极大的简化,取消了带传动和齿轮传动,机床主轴由装式电动机直接驱动,从而把机床主传动链的长度缩短为零,实现了机床主运动的“零传动”。
这种主轴电动机与机床主轴“合二为一”的传动结构形式,使主轴组件从机床的传动系统和整体结构中相对独立出来,因此可做成“主轴单元”,俗称“电主轴”。
由于当前电主轴主要采用的是交流高频电动机,故也称为“高频主轴”。
由于没有中间传动环节,有时又称它为“直接驱动主轴”。
电主轴是一种智能型功能部件,不但转速高、功率大,还有一系列控制主轴温升与振动等机床运行参数的功能,以确保其高速运转的可靠性与安全。
1.2课题的目的及容主轴组件是机床的执行件。
它的功用是支承并带动工件或刀具,完成表面成形运动,同时还起传递运动和扭矩、承受切削力和驱动力等载荷的作用。
由于主轴组件的工作性能直接影响到机床的加工质量和生产率,因此它是机床中的一个关键组件。
主轴组件是由主轴、主轴支承以及安装在主轴上的传动件组成。
主轴组件的设计,其实主要就是这三个部件的设计,但它们既是独立的,又是互相联系而不可分割的,因此设计时需要全面、综合地加以分析。
本课题的目的是进行立式加工中心主轴组件的结构设计,主轴组件作为立式加工中心的执行元件,它确保带动刀具进行切削加工、传递运动、动力及承受切削力等,并满足相关的技术指标要求。
本课题涉及的主要技术指标有:(1)主电机采用FANUC交流主轴电机,功率5.5KW。
(2)主轴转速:标准型22.5~2250rpm;高速型:45~4500rpm.(3)主轴锥孔为7:24,BT—45,大端直径Φ57.15.1.3课题解决的关键问题各类机床对其主轴组件的要求,主要是精度问题,就是要保证机床在一定的载荷与转速下,主轴能带动工件或刀具精确地、稳定地绕其轴心旋转,并长期地保持这一性能。
主轴组件的设计和制造,都是围绕着解决这个基本问题出发的。
为了达到相应的精度要求,通常,主轴组件应符合以下几点设计要求:(1)旋转精度旋转精度是指机床在空载低速旋转时,主轴前端安装工件或刀具部位的径向和轴向跳动值满足要求,目的是保证加工零件的几何精度和表面粗糙度。
(2)刚度指主轴组件在外力的作用下,仍能保持一定工作精度的能力。
刚度不足时,不仅影响加工精度和表面质量,还容易引起振动,恶化传动件和轴承的工作条件。
设计时应在其它条件允许的条件下,尽量提高刚度值。
(3)抗振性指主轴组件在切削过程中抵抗强迫振动和自激振动保持平稳运转的能力。
抗振性直接影响加工表面质量和生产率,应尽量提高。
(4)温升和热变形温升会引起机床部件热变形,使主轴旋转中心的相对位置发生变化,影响加工精度。
并且温度过高会改变轴承等元件的间隙、破坏润滑条件,加速磨损。
(5)耐磨性指长期保持其原始精度的能力。
主要影响因素是材料热处理、轴承类型和润滑方式。
根据本课题的设计任务要求,由于主轴的转速并不是很高,所以在抗振性、温升等方面不必重点考虑,而应重点考虑加工中心的旋转精度和刚性。
但是在设计时仍应综合考虑以上几项要求,注意吸收新技术,以获得满意的设计方案。
1.4解决上述问题的策略旋转精度主要取决于主轴、支撑轴承、主轴箱上轴承座等的制造、装配和调整精度。
显然,若要保证主轴组件的旋转精度,则必然对主轴支承轴颈的圆度、轴承滚道及滚子的圆度、主轴及其上的回转零件的动平衡度、止推轴承的滚道及滚动体的误差,以及对主轴的主要定心面的径向跳动和轴向窜动等提出较高的整体要求,特别是提高支承轴承的精度等级。
要保证旋转精度,通常应尽量满足以上要求。
而对于主轴组件的刚度,实际上市主轴、轴承、轴承座等加工设计的综合反映。
主轴自身的结构形状和尺寸,滚动轴承的配置形式(背靠背、面对面、同向、混合等)、数量、类型、预紧等,以及支承的跨距、主轴前端的悬身量等都将直接影响其刚度。
为了保证机床的主轴具有足够的刚度,通常应尽量使主轴前端的悬身量缩短,主轴直径增大,并通过计算求出支承轴间的最佳跨距、进行预紧、采用合理的轴承及相应的配置形式等措施。
采用以上各种措施必然会使机床的刚性及旋转精度大幅度提高,但是,若盲目地全部采纳上述措施,则一定会使机床的制造难度增大,成本增加。
所以,在设计的时候,要综合各项因素考虑。
2方案拟定2.1加工中心主传动系统的组成主传动组件是由主轴、主轴支承、装在主轴上的传动件和密封件等组成的。
主轴的启动、停止和变速等均由数控系统控制,并通过装在主轴上的刀具参与切削运动,是切削加工的功率输出部件。
主轴是加工中心的关键部件,其结构的好坏对加工中心的性能有很大的影响,它决定着加工中心的切削性能、动态刚度、加工精度等。
主轴部刀具自动夹紧机构是自动刀具交换装置的组成部分。
2.2 机械系统方案的确定2.2.1 主轴传动机构对于现在的机床主轴传动机构来说,主要分为齿轮传动和同步带传动。
齿轮传动是机械传动中最重要的传动之一,应用普遍,类型较多,适应性广。
其传递的功率可达近十万千瓦,圆周速度可达200m/s,效率可达0.99。
齿轮传动大多数为传动比固定的传动,少数为有级变速传动。
但是齿轮传动的制造及安装精度要求高,价格较贵,且不宜用于传动距离过大的场合。
同步带是啮合传动中唯一一种不需要润滑的传动方式。
在啮合传动中,它的结构最简单,制造最容易,最经济,弹性缓冲的能力最强,重量轻,两轴可以任意布置,噪声低。
它的带由专业厂商生产,带轮自行设计制造,它在远距离、多轴传动时比较经济。
同步带传动时的线速度可达50m/s(有时允许达100m/s),传动功率可达300kW,传动比可达10(有时允许达20),传动效率可达0.98。
同步带传动的优点是:a)无滑动,能保证固定的传动比;b)预紧力较小,轴和轴承上所受的载荷小;c)带的厚度小,单位长度的质量小,故允许的线速度较高;d) 带的柔性好,故所用带轮的直径可以较小。
其主要缺点是安装时中心距的要求严格。
由于齿轮传动需要具备较多的润滑条件,而且为了使主轴能够达到一定的旋转精度,必须选择较好的工作环境,以防止外界杂物侵入。