模具设计与制造方案
模具设计与制造

第二章模具设计与制造在大型工业生产中,人们为了提高生产力,使工业用零件生产快捷、批量生产、外形美观、简洁、品质稳定及零件有预定的功用和使用寿命,故人们为此而设计了该零件外形可开合、多次重复使用的模腔,称之为模具。
第一节常用设备及工具一、常用设备:CNC加工中心、计算机铣床、计算机3D抄数机、车床、铣床、磨床、钻床、镗床、手提打磨机、砂轮机、磨刀机、手提砂轮机、吊钻机、电葫芦、线切割机、攻牙机、电焊机、氧焊机、氩焊机、手动压力泵、空气压缩机、锯床、雕刻机、灯箱、粹火炉、无心研磨床、拋光机等等二、常用工具:钳子、虎口钳、铁钻、扳手、六角匙、起子、铁锤、研磨石、手锯、锉刀、卡尺、千分尺、高度尺、分度尺、直尺、直角尺、角度尺、厚薄规、塞规、塞尺、外圆规、内圆规、R规、硬度测试仪、光洁度测试仪.第二节合金模和塑料模的主要区别:一、模具主要区别:二、适用啤注材料的区别:第三Array节工模的基本结构及各部分的常用材料一、模具常用部件名称及定义:1、上哥\下哥:上哥为嵌入上内模的镶件,下哥为嵌入下内模的镶件.2、上/下模镶针:嵌入上/下内模的销子叫上/下模镶针,用来制作工件上的盲孔或通孔等.3、行位/斜鸡/行位油板/斜鸡油板/斜边/压条:行位即滑块,行位的工作面为工件料位,有两面为滑动面,一面贴斜鸡(又名压座、压块)滑动,中间穿有斜边(又名斜导边、斜导销),起推动行位的作用.另外在行位的工作面和斜鸡的滑动面都嵌有油板(即耐磨块).4、方铁(垫脚)/底板:方铁在底板(又名底部固定板,下模板、C板)与下模框之间用来固定间隔距离,提供顶出啤件的行程,为弹簧提供行程范围.5、弹簧杆:又名弹簧柱,穿在弹簧中心,固定在面针板上,弹簧压缩复位时在下模的孔中行走.6、直边(导柱)/托司(导套)/直司(直套):直边穿入托司或直司,沿内孔行走,使上下模作相对运动,对上下模作配位固定.7、面针板(顶针固定板)/管针(销钉、暗销)/托板(顶针托板)/底针板(推板、脱模板):面针板用来固定顶针,顶针用管针固定在面针板上,底针板在压力机作用下将顶针和面针板推动,使顶针顶出工件.底针板、面针板和顶针在弹簧和回针的作用下复位.8、垃圾钉(限位钉):为了保证不让可能掉下来的啤料垃圾影响顶针板的行程,在底板上装有垃圾钉,使托板与底板之间保持一定的距离.9、顶针(起模杆)/托针(有托顶针)/垃圾顶针:顶针、托针和垃圾顶针都是用来将工件顶出的,顶针和托针直接顶工件,不同的是托针下部要粗一些.垃圾顶针不直接顶工件,而是通过工件边上小水口流入垃圾钉孔口的啤料将工件顶出.10、司筒(顶杆套、顶管、推管)/司筒针:司筒中间有一根固定的销子,司筒顺销子运动,顶出工件.中间的销子为司筒针.11、大水口/细水口:流体流入内模的水口,开在工件边上的为大水口,开在工件中间的点浇口为细水口.12、单托唧咀(A型浇套)/双托唧咀(B型浇套):唧咀又名为水口司,浇道套,位于上模的中心,起浇道套筒的作用,与压力机的喷料咀连接,液态材料经此喷入内模.13、分流锥(用于合金模):分流锥又名为浇道分流器,水口分配器,喷入的液料由此分流出去.14、唧咀中心线:唧中心线与压力机喷料咀中心线重合.15、喉塞(管塞):用来堵塞运水道的堵头.16、水口板(浇道脱模板):用来顶出浇道啤料.17、勾针:用来将上模唧咀段的啤料拉到下模.18、定位圈(法兰):使压机喷料口,内模,唧咀成一线的定位圈.另外还有水口边、隔片、滑动锁、杯司(衬套)、O型圈(密封圈)、撑头(支柱)、球掣、锁扣、限位块、摇臂、拉板(拉杆)、推杆(剑身)、加速顶针机构、活动臂、回针(复位销)、提前回针、复位机构,提前复位机构、粗框、压板(面板、工字板、上模板)、分型面(分模线)、模具镶块、下模板(托板)、上模板、铜公、杯头螺丝(内六角螺丝)、平头螺钉、无头螺钉等.第四节模具设计注意事项:一、模图设计与绘制:模图设计就是依据客人要求制造产品的件数(即一模几头),将产品在模具上进行排位,然后将模具结构用图纸的形式表示出来的过程; 绘好模图后,还要做加工工艺资料,来指示模具各部分的加工方法、加工要求等;最后还要对模图进行审核,才能正式做模. 有关模图的审核一般应考虑以下几点:1.检查一些料位过细且难走齐胶的产品零件是否离主流道太远,一些小件、薄型件、跳级多的件应尽量排在离唧咀较近的水道边.2.检查水口是否幵在适当的地方,水口应幵在能迅速填满型腔而不昜产生缩水或夹水纹的地方。
《模具设计与制造》教案

《模具设计与制造》教案第一章:模具设计基础1.1 模具概述介绍模具的定义、分类和应用领域讲解模具在制造业中的重要性1.2 模具设计基本原则讲解模具设计的要求和流程介绍模具设计中的常见问题和解决方法1.3 模具设计常用软件介绍模具设计常用的CAD/CAM软件讲解软件的选择和使用方法第二章:模具制造工艺2.1 模具制造概述介绍模具制造的定义和流程讲解模具制造的关键环节和技术要求2.2 模具制造常用材料介绍模具制造常用材料的分类和性能讲解材料的选用原则和加工方法2.3 模具制造工艺过程讲解模具制造的各个工艺过程介绍常用的模具制造工艺方法和设备第三章:模具设计实例分析3.1 模具设计案例一:塑料注射模设计分析塑料注射模的设计要求和步骤讲解模具结构设计要点和注意事项3.2 模具设计案例二:冲压模设计分析冲压模的设计要求和步骤讲解模具结构设计要点和注意事项3.3 模具设计案例三:压铸模设计分析压铸模的设计要求和步骤讲解模具结构设计要点和注意事项第四章:模具制造实例分析4.1 模具制造案例一:模具零件的加工分析模具零件的加工方法和工艺流程讲解加工要点和质量控制方法4.2 模具制造案例二:模具装配分析模具装配的要求和步骤讲解装配要点和调整方法4.3 模具制造案例三:模具调试与验收分析模具调试的目的和步骤讲解调试要点和验收标准第五章:模具设计与制造的创新发展5.1 模具设计创新介绍模具设计创新的含义和重要性讲解模具设计创新的方法和案例5.2 模具制造技术创新介绍模具制造技术创新的含义和重要性讲解模具制造技术创新的方法和案例5.3 模具设计与制造的发展趋势分析模具行业的发展趋势讲解模具设计与制造的发展方向和挑战第六章:模具管理与维护6.1 模具管理讲解模具管理的重要性介绍模具管理的方法和工具6.2 模具维护与保养分析模具磨损的原因讲解模具维护和保养的步骤与注意事项6.3 模具的修复与改造讲解模具修复与改造的技术和方法分析模具修复与改造的经济效益第七章:模具安全与质量控制7.1 模具安全介绍模具安全的重要性讲解模具安全的设计要求和措施7.2 模具质量控制分析模具质量的影响因素讲解模具质量控制的方法和工具7.3 模具质量的检测与评价介绍模具质量检测的方法和设备分析模具评价的内容和指标第八章:模具设计与制造的现代技术8.1 计算机辅助设计(CAD)介绍CAD技术在模具设计中的应用讲解CAD软件的选择和使用方法8.2 计算机辅助制造(CAM)介绍CAM技术在模具制造中的应用讲解CAM软件的选择和使用方法8.3 数字化制造技术讲解数字化制造技术的基本概念分析数字化制造技术在模具行业中的应用前景第九章:模具设计与制造的前沿技术9.1 高速模具设计与制造介绍高速模具设计与制造的特点和优势分析高速模具设计与制造的应用领域9.2 精密模具设计与制造讲解精密模具设计与制造的要求和方法分析精密模具设计与制造的发展趋势9.3 绿色模具设计与制造介绍绿色模具设计与制造的基本概念分析绿色模具设计与制造在可持续发展中的作用第十章:模具设计与制造的职业素养与职业道德10.1 模具设计师的职业素养讲解模具设计师应具备的技能和素质分析模具设计师的职业发展前景10.2 模具制造工人的职业素养讲解模具制造工人应具备的技能和素质分析模具制造工人的职业发展前景10.3 模具设计与制造的职业道德介绍模具设计与制造的职业道德规范分析职业道德在模具行业中的重要性重点和难点解析本文主要介绍了模具设计与制造的基础知识、工艺流程、实例分析、创新发展、安全管理、现代技术以及前沿技术。
模具设计与制造毕业设计
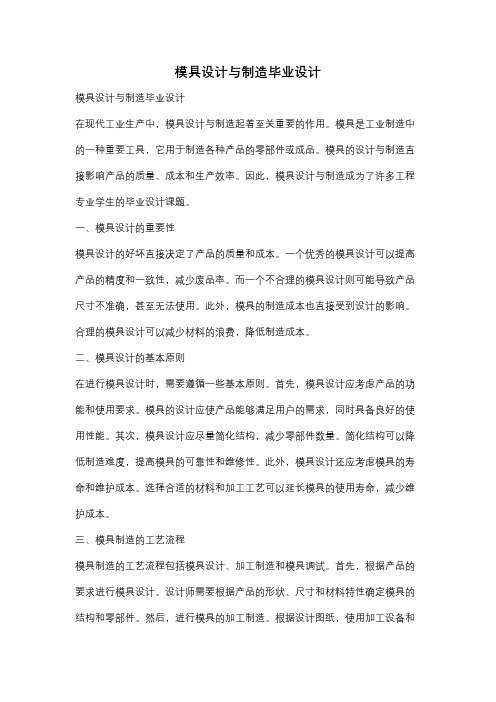
模具设计与制造毕业设计模具设计与制造毕业设计在现代工业生产中,模具设计与制造起着至关重要的作用。
模具是工业制造中的一种重要工具,它用于制造各种产品的零部件或成品。
模具的设计与制造直接影响产品的质量、成本和生产效率。
因此,模具设计与制造成为了许多工程专业学生的毕业设计课题。
一、模具设计的重要性模具设计的好坏直接决定了产品的质量和成本。
一个优秀的模具设计可以提高产品的精度和一致性,减少废品率。
而一个不合理的模具设计则可能导致产品尺寸不准确,甚至无法使用。
此外,模具的制造成本也直接受到设计的影响。
合理的模具设计可以减少材料的浪费,降低制造成本。
二、模具设计的基本原则在进行模具设计时,需要遵循一些基本原则。
首先,模具设计应考虑产品的功能和使用要求。
模具的设计应使产品能够满足用户的需求,同时具备良好的使用性能。
其次,模具设计应尽量简化结构,减少零部件数量。
简化结构可以降低制造难度,提高模具的可靠性和维修性。
此外,模具设计还应考虑模具的寿命和维护成本。
选择合适的材料和加工工艺可以延长模具的使用寿命,减少维护成本。
三、模具制造的工艺流程模具制造的工艺流程包括模具设计、加工制造和模具调试。
首先,根据产品的要求进行模具设计。
设计师需要根据产品的形状、尺寸和材料特性确定模具的结构和零部件。
然后,进行模具的加工制造。
根据设计图纸,使用加工设备和工具进行模具的加工和装配。
最后,进行模具的调试。
通过试模和调整,确保模具能够正常运行,满足产品的要求。
四、模具设计与制造的挑战模具设计与制造面临着许多挑战。
首先,随着科技的发展,产品的形状和尺寸越来越复杂,对模具的设计和制造提出了更高的要求。
其次,模具设计与制造需要综合运用多学科知识,如材料科学、机械工程、自动化技术等。
这对设计师和制造工程师的综合素质提出了更高的要求。
此外,模具设计与制造还需要不断创新和改进,以适应市场需求的变化。
五、模具设计与制造的发展趋势随着科技的不断进步,模具设计与制造也在不断发展。
模具设计与制造专业建设方案
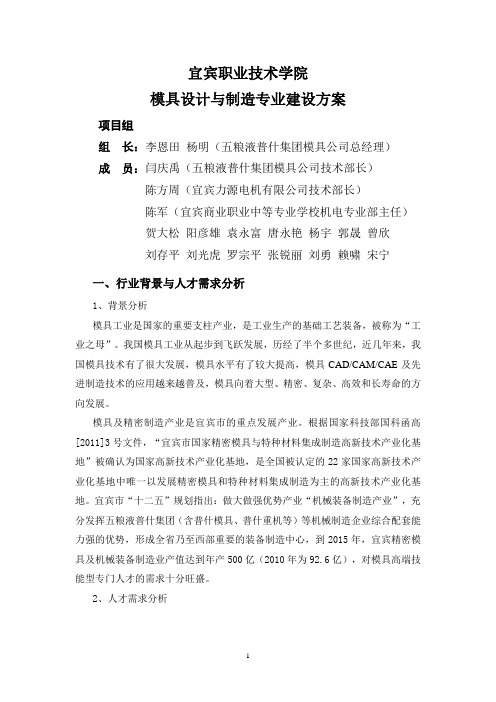
宜宾职业技术学院模具设计与制造专业建设方案项目组组长:李恩田杨明(五粮液普什集团模具公司总经理)成员:闫庆禹(五粮液普什集团模具公司技术部长)陈方周(宜宾力源电机有限公司技术部长)陈军(宜宾商业职业中等专业学校机电专业部主任)贺大松阳彦雄袁永富唐永艳杨宇郭晟曾欣刘存平刘光虎罗宗平张锐丽刘勇赖啸宋宁一、行业背景与人才需求分析1、背景分析模具工业是国家的重要支柱产业,是工业生产的基础工艺装备,被称为“工业之母”。
我国模具工业从起步到飞跃发展,历经了半个多世纪,近几年来,我国模具技术有了很大发展,模具水平有了较大提高,模具CAD/CAM/CAE及先进制造技术的应用越来越普及,模具向着大型、精密、复杂、高效和长寿命的方向发展。
模具及精密制造产业是宜宾市的重点发展产业。
根据国家科技部国科函高[2011]3号文件,“宜宾市国家精密模具与特种材料集成制造高新技术产业化基地”被确认为国家高新技术产业化基地,是全国被认定的22家国家高新技术产业化基地中唯一以发展精密模具和特种材料集成制造为主的高新技术产业化基地。
宜宾市“十二五”规划指出:做大做强优势产业“机械装备制造产业”,充分发挥五粮液普什集团(含普什模具、普什重机等)等机械制造企业综合配套能力强的优势,形成全省乃至西部重要的装备制造中心,到2015年,宜宾精密模具及机械装备制造业产值达到年产500亿(2010年为92.6亿),对模具高端技能型专门人才的需求十分旺盛。
2、人才需求分析宜宾地区精密模具设计与制造类技能应用人才紧缺。
随着宜宾国家精密模具与特种材料集成制造高新技术产业化基地建设的逐步展开,以及宜宾以五粮液集团普什模具有限公司为首的模具产业集群的发展,本地区对于精密模具设计与制造相关岗位的模具类高技能应用型人才的需求急增,而宜宾地处川滇黔结合部的地域特点,决定了该专业需求的人才主要依靠本地培养。
因此,培养一批稳定的模具高端技能型专门人才成了首要解决的问题,加强我院模具设计与制造专业的建设也就成了首选。
《模具设计与制造》教案

针对不同类型的模具和问题,采用不同的调试方法和技巧 ,如调整模具结构、改变温度和压力等参数、使用特殊工 具等。
调试记录与总结
在调试过程中,应做好记录并进行分析总结,以便于后续 的模具改进和优化。
模具装配与调试实例分析
实例选择
选择具有代表性的模具 作为实例,如注塑模、 压铸模等,对其装配和 调试过程进行详细分析 。
主流模具设计软件介绍 讲解目前市场上主流的模具设计软件,如AutoCAD、 SolidWorks、Pro/Engineer等。
软件操作基础
介绍软件界面、工具栏、菜单栏等基本操作,以及二维绘图和三维 建模的方法。
软件应用实例
通过具体实例演示如何使用软件进行模具设计,包括零件建模、装 配、工程图生成等。
检查与紧固
检查模具各部件是否松动,紧固关键部位。
防锈处理
采用防锈剂或防锈纸,防止模具生锈。
模具维修实例分析
案例一
注塑模具维修实例
案例二
冲压模具维修实例
案例三
压铸模具维修实例
案例四
锻造模具维修实例
THANKS
感谢观看
模具设计实例分析
典型模具设计案例
01
选取具有代表性的模具设计案例,如注塑模、压铸模、锻模等
,进行详细的分析和讲解。
案例中问题与解决方案
02
针对案例中可能出现的问题,提出相应的解决方案,并解释原
因。
案例总结与经验分享
03
总结案例中的经验和教训,分享模具设计师在实际工作中积累
的经验和技巧。
03
模具材料与热处理
模具设计与制造的基本流程
设计阶段
根据产品需求,进行模具结构 设计、选择适当的材料和热处
制造工艺中的模具设计与制造技术创新案例

制造工艺中的模具设计与制造技术创新案例模具设计与制造技术在制造工艺中占据着重要的地位。
它们直接关系到产品的质量、生产效率以及生产成本。
随着科技的不断发展,模具设计与制造技术也在不断创新与演进。
本文将介绍几个在制造工艺中的模具设计与制造技术创新案例,以展示技术进步对制造工艺的重要作用。
1. 案例一:3D打印模具传统的模具设计与制造通常需要经过多个环节,耗费大量的时间与人力成本。
然而,随着3D打印技术的兴起,模具制造行业发生了巨大的改变。
通过3D打印技术,可以将模具的制造过程简化为从设计到生产的一体化,大大提高了制造效率。
同时,使用3D打印技术还能够实现个性化定制的模具设计,更好地满足客户的需求。
2. 案例二:数字模具设计与仿真数字模具设计与仿真技术是另一种在制造工艺中的重要创新。
传统的模具设计通常需要进行多次试验与修改,耗费大量的时间与资源。
而借助数字模具设计与仿真技术,设计师可以通过计算机模拟,准确地预测模具设计的效果,降低设计风险。
此外,数字化设计还能够快速生成模具图纸,加快产品的研发周期。
3. 案例三:高性能材料应用在模具设计与制造中,材料的选择至关重要。
传统的模具材料通常存在耐磨性、耐腐蚀性等方面的不足。
而随着材料科学的发展,新型高性能材料逐渐应用于模具制造中。
例如,使用高强度合金材料可以提高模具的使用寿命,使用耐高温材料可以适应高温环境下的制造工艺。
这些高性能材料的应用,不仅提高了模具的性能,还有效地减少了生产成本。
4. 案例四:智能化模具设计与制造随着人工智能技术的发展,智能化模具设计与制造也成为制造工艺中的一个重要方向。
智能化模具可以通过传感器监测和收集数据,实现自主感知与自我调整。
例如,智能模具可以根据生产数据预测模具损耗情况,并主动通知维修与更换。
这种智能化的模具设计与制造技术,不仅提高了制造的自动化程度,还极大地减少了生产成本和人力资源的浪费。
总结:模具设计与制造技术的创新对于制造工艺具有重要的影响。
模具设计与制造专业人才培养方案
模具设计与制造专业人才培养方案执笔人:邴起航审核人:宁玲玲审批人:钮平章实施时间:2010.81.【模具设计与制造】《模具设计与制造》5801062.【教育类型及学历层次】高等职业教育、大专3.【入学要求条件】高中毕业或同等学力者4.【学制】三年5.【培养目标】本专业主要面向培养德、智、体、美等方面全面发展,具有良好的职业素质,面向制造行业,从事模具设计、模具加工工艺编制、冲压和塑料成型加工、数控机床的操作以及生产管理等工作的高素质技能型专门人才。
6.【职业面向及职业能力要求】(1)职业面向主要就业单位:模具设计与制造企业、冲压与塑料成型机械制造企业、精密零件件加工企业。
主要就业部门:生产部、售后服务部、销售部、工艺工程部、质检部或技术开发部。
12(2)能力结构及要求(3)职业资格证书必须取得下列职业资格证书之一:37.【典型工作任务及其工作过程】8.【培养方案体系】(1)体系框架与课程路线4(2)课程方案说明:职业能力拓展课8个学分,学生可在第4、5学期对学校开设的职业能力拓展课程进行选修。
5(3)学分与学时安排6(4)集中实践教学环节安排9.【考核总体要求】(1)考核可以根据不同课程的特点和要求采取笔试、实操、作品展示、成果汇报等多种方式进行。
(2)考核要以能力考核为核心,综合考核专业知识、专业技能、方法能力、职业素质、团队合作等方面。
(3)各门课程应该根据课程的特点和要求,对采取不同方式、对各个方面的考核结果,通过一定的加权系数评定最终成绩。
710.【教师队伍基本要求】(1)专任授课教师具备本专业或相近专业大学本科以上学历(含本科);(2)专任实训教师要具备数控技术专业中级以上的资格证书或工程师资格;(3)本专业专任教师“双师”资格的比例要达到60%以上;(4)专任教师与学生比例1:20左右,其中企业兼职教师占教师总数的比例不低于30%;(5)专任教师应具有高等院校教师资格证,具有开发职业课程的能力。
模具设计与制造实训教案
一、教案基本信息教案名称:模具设计与制造实训教案课时安排:45分钟教学目标:1. 使学生了解模具设计与制造的基本概念和流程。
2. 培养学生掌握模具设计的基本方法和技巧。
3. 提高学生实际操作能力,使其能够熟练使用相关软件和设备。
教学方法:1. 讲授:讲解模具设计与制造的基本概念、流程和方法。
2. 演示:展示模具设计实例和操作过程。
3. 实践:学生动手操作,进行模具设计实践。
教学内容:1. 模具设计与制造的基本概念。
2. 模具设计的流程和方法。
3. 模具设计软件的使用。
4. 模具制造的工艺和设备。
5. 模具设计的注意事项。
教学准备:1. 计算机及相关软件。
2. 模具设计实例。
3. 模具制造设备。
教学过程:1. 导入:介绍模具设计与制造的基本概念,激发学生兴趣。
2. 讲解:讲解模具设计的流程和方法,引导学生理解并掌握。
3. 演示:展示模具设计实例和操作过程,使学生直观感受。
4. 实践:学生动手操作,进行模具设计实践,巩固所学知识。
5. 总结:强调模具设计的注意事项,提醒学生在实践中注意。
二、模具设计与制造的基本概念教学目标:使学生了解模具设计与制造的基本概念。
教学方法:讲授教学内容:1. 模具的定义及分类。
2. 模具设计的作用和意义。
3. 模具制造的工艺和方法。
教学准备:无教学过程:1. 导入:引导学生思考模具在生产中的重要性。
2. 讲解:讲解模具的定义、分类、作用和意义,以及模具制造的工艺和方法。
3. 互动:学生提问,教师解答。
三、模具设计的流程和方法教学目标:使学生掌握模具设计的流程和方法。
教学方法:讲授、演示教学内容:1. 模具设计流程:需求分析、方案制定、设计、制造、调试与改进。
2. 模具设计方法:二维绘图、三维建模、模具设计软件。
教学准备:计算机及相关软件教学过程:1. 导入:回顾上一节课的内容,引导学生了解模具设计的重要性。
2. 讲解:讲解模具设计的流程和方法,展示相关实例。
3. 演示:演示模具设计软件的使用,让学生直观感受模具设计过程。
毕业设计:模具设计与制造毕业设计
毕业设计:模具设计与制造一、引言模具设计与制造是机械工程领域中重要的一项技术,广泛应用于各个行业。
随着工业的快速发展,模具在产品制造中的地位日益重要。
本文将介绍模具设计与制造的基本概念、流程和技术要点,并通过实例说明其在工业生产中的应用。
二、模具设计与制造的基本概念2.1 模具的定义模具是指为了在工业生产中批量制造产品而设计和制造的设备。
它包括模具的结构和零部件,以及模具的加工和组装工艺。
2.2 模具的分类根据不同的划分标准,模具可以分为多种类型,常见的有:压力模具、塑料模具、冲压模具、注塑模具等。
每种模具都有其专门的设计和制造要点。
2.3 模具设计与制造的流程模具设计与制造的流程分为:需求分析、结构设计、零部件设计、加工制造和试模调试等几个阶段。
在每个阶段,都需要注意不同的技术要点和问题。
三、模具设计与制造的技术要点3.1 结构设计要点模具的结构设计是模具设计过程中最重要的一环。
要考虑到产品的形状、尺寸、材料等因素,确定合适的结构形式。
同时,还要充分考虑模具的可制造性和可维修性。
3.2 零部件设计要点模具的零部件设计涉及到模具的各个部分,如模座、模具芯、滑块等。
在设计零部件时,要保证零件之间的配合精度,以及零部件的可拆卸性和易于维修。
3.3 加工制造要点模具的加工制造包括模具零部件加工和组装。
在加工过程中,要选择合适的加工工艺和设备,确保零部件加工的精度和质量。
在组装过程中,要注意零部件的装配顺序和配合要求。
3.4 试模调试要点模具的试模调试是模具设计与制造的最后一步,也是最关键的一步。
在试模调试过程中,要通过实际操作,不断优化和调整模具的结构和参数,以确保模具在实际生产中的良好运行。
四、模具设计与制造实例分析4.1 塑料注塑模具设计与制造以塑料注塑模具为例,介绍模具设计与制造的实例分析。
包括模具结构设计、零部件设计、加工制造和试模调试等方面。
通过实例分析,展示模具设计与制造的全过程和技术要点。
《模具设计与制造》教案
《模具设计与制造》教案一、教学目标1. 了解模具设计与制造的基本概念、分类及应用领域。
2. 掌握模具设计与制造的基本原理和方法。
3. 熟悉模具设计与制造的工艺流程。
4. 了解模具行业的发展趋势和前景。
二、教学内容1. 模具概述1.1 模具的定义与作用1.2 模具的分类1.3 模具的性能与选用2. 模具设计2.1 模具设计原则2.2 模具设计步骤2.3 模具结构设计2.4 模具零件设计3. 模具制造3.1 模具制造工艺3.2 模具制造设备3.3 模具制造过程3.4 模具制造常见问题及解决方法4. 模具装配与调试4.1 模具装配原则4.2 模具装配过程4.3 模具调试与验收5. 模具的使用与维护5.1 模具的使用注意事项5.2 模具的维护与保养5.3 模具的修复与改造三、教学方法1. 采用讲授、案例分析、讨论相结合的教学方式。
2. 使用多媒体课件、实物展示等教学手段,增强学生对模具设计与制造的理解。
3. 组织实地考察,使学生更好地了解模具行业的发展和应用。
四、教学安排1. 课时:45分钟/节,共15节。
2. 授课方式:理论讲解与实践操作相结合。
3. 实践环节:安排模具设计与制造的实操课程,让学生亲自动手操作,提高实际操作能力。
五、教学评价1. 平时成绩:包括出勤、课堂表现、作业完成情况,占总评的30%。
2. 实操成绩:包括模具设计与制造的实际操作能力,占总评的30%。
3. 期末考试:包括书面考试和实际操作考试,占总评的40%。
六、模具的材料与热处理6.1 模具材料的分类与性能6.2 常用模具材料及应用6.3 模具材料的选择原则6.4 模具热处理工艺及性能七、模具CAD/CAM技术7.1 CAD/CAM技术概述7.2 CAD/CAM软件及其应用7.3 模具CAD/CAM设计流程7.4 模具CAD/CAM技术的发展趋势八、塑料模具设计8.1 塑料模具概述8.2 塑料模具设计原则8.3 塑料模具结构设计8.4 塑料模具零件设计九、金属模具设计9.1 金属模具概述9.2 金属模具设计原则9.3 金属模具结构设计9.4 金属模具零件设计十、模具制造工艺与设备10.1 模具制造工艺概述10.2 模具制造工艺流程10.3 模具制造设备及选用10.4 模具制造新技术与发展趋势十一、模具装配与调试11.1 模具装配概述11.2 模具装配过程11.3 模具调试与验收11.4 模具装配中常见问题及解决方法十二、模具的使用与维护12.1 模具的使用注意事项12.2 模具的维护与保养12.3 模具的修复与改造12.4 模具的使用寿命及提高措施十三、模具行业现状与发展趋势13.1 模具行业概述13.2 模具行业现状13.3 模具行业发展趋势13.4 我国模具行业的发展策略十四、模具设计与制造实例分析14.1 塑料制品模具设计实例14.2 金属制品模具设计实例14.3 复杂模具设计实例14.4 模具制造实例十五、课程总结与展望15.1 模具设计与制造课程总结15.2 模具设计与制造技能的重要性15.3 模具行业发展前景15.4 学生就业方向与职业规划教学安排、教学方法、教学评价等请参考前五个章节的内容。
- 1、下载文档前请自行甄别文档内容的完整性,平台不提供额外的编辑、内容补充、找答案等附加服务。
- 2、"仅部分预览"的文档,不可在线预览部分如存在完整性等问题,可反馈申请退款(可完整预览的文档不适用该条件!)。
- 3、如文档侵犯您的权益,请联系客服反馈,我们会尽快为您处理(人工客服工作时间:9:00-18:30)。
模具设计与制造方案
材料:Q235钢
一、冲压件工艺性分析
工件有冲孔、内孔翻边、落料三个工序。
材料为Q235钢,具有良好的冲压性能,适合冲裁。
工件的尺寸全部为自由公差,可看作IT14级,尺寸精度较低,普通总裁即可满足要求。
二、冲压工序方案的确定
工件包括三个基本工序,这里采用级进模生产。
级进模生产只需
一副模具,生产效率高,操作方便,工件精度也能满足要求。
三、主要设计计算
1.排样方式的确定及其计算.
因工件的形状较为复杂,排样采用直
排。
搭边值取1.5和1.8,送料采用导轨形式
得料宽为:
B=(L max+2a+2b)=110mm+3.6mm+4mm=117.6mm
b—板料进入导轨宽度。
A—搭边余量。
L max—条料宽度方向冲(注:
裁件的最大尺寸。
)步距27.9mm,一个步距的材料利用率=A/B S⨯100%=(1020.5/3375)%=30.4%(A一个冲裁伯的面积;B —条料宽度;S—步距。
)
2.冲压力的计算
模具采用级进模,选择弹性卸料、下出件。
冲裁力:F=F落+F冲=KL tτ(L-零件总的周长,包括零件外轮廓和内孔。
)F=KL tτ=1.3⨯350.25⨯1⨯380=173023.5N
卸料力:F X=K X F=0.04⨯173023.5=6921N
冲压工艺总力:F Z=F+F X=173023.5N+6921N=179944.5N
落料所需冲裁力: F落=KL落 tτ=271.2⨯1⨯380=133972.8N 落料部分所需卸料力:F X落=K X F落=0.04⨯133972.8N=5359N
冲孔所需冲裁力: F孔=KL孔 tτ=79.05⨯1⨯380=39050.7N 冲孔部分所需卸料力:F X孔=K X F孔=0.04⨯39050.7N=1562N
3.翻边工艺的分析及翻边力的计算
由零件图可以反应出内孔的翻边为变薄翻边,且是在平板料上的翻边。
由图上给出的尺寸可知预冲孔的大小未知,因而要判断预冲孔的大小。
4.工作零件刃口尺寸计算
零件采用自由公差因而可取公差值为IT14根据材料及板厚查得冲裁间隙Z min=0.100mm,Zmax=0.140mm.各工作零件的刃口尺寸计算如下:
冲孔凸模与凹模尺寸的计算
1)计算56mm⨯16mm孔的凸模与凹模刃口尺寸:
冲孔时: d T=(d min+ X∆)0-δT d A=(d T+Z min)0+δA
查得56mm的∆=0.74 δT=δA=0.185 X∆=0.370尺寸转换为560+0.74得: d T=(56+0.37)0-δT=56.370-0.185mm
d A=(56.37+0.100)0+δA=56.470+0.185mm
查得12mm的∆=0.43 δT=δA=0.110 X∆=0.220尺寸转换为160+0.43得: d T=(12+0.220)0-δT=12.220-0.110mm
d A=(12.22+0.100) 0+δA=12.320+0.110 mm
2)计算7mm⨯2mm孔的凸模与凹模尺寸:
查得 7mm 的∆=0.360 δT=δA=0.090 X∆=0.180 尺寸转换70+0.360得: d T=(7+0.180)0-δT=7.180-0.090mm
d A=(7.18+0.100)0+δA=7.28 0+0.090mm
查得2mm的∆=0.25 δT=δA=0.060 X∆=0.130尺寸转换为20+0.060得: d T=(2+0.130)0-δT=2.130-0.060mm
d A=(2.13+0.100)0+δA=2.230+0.060mm
3)计算φ2.5孔的凸模与凹模尺寸:
查得φ2.5孔的∆=0.25 δT=+0.008 δA=-0.006 X=0.75尺寸转换为φ2.500.25得:d T=(2.5+0.25⨯0.75)0-δT=2.6880-0.080mm
d A=(2.688+0.100)0+δA=2.7880+0.060mm
落料凸模与凹模尺寸的计算
落时:D A=(D max- X∆)0+δA D T=(D A-Z min)0-δT
首先判断凸模与凹模的加工方法,根据对零件的分析,易采用配
作法加。
因为是落料所以取凹模作为基准件进行加工
其次判断哪些尺寸是受落料模影响的,从图中可以看出受落料模影响的尺寸主要有:R62.5、7.0、9.0、26.9、2.9。
查得 7mm 的∆=0.360 δT=δA=0.090 X∆=0.180 尺寸转换70-0.360得: D A=(7-0.180)0+δA=6.820+0.090mm
D T=(6.82-0.100) 0-δT=6.72 0-0.090mm
查得9.0mm 的∆=0.360 δT=δA=0.090 X∆=0.180 尺寸转换90-0.360得: D A=(9-0.180) 0+δA=8.820+0.090mm
D T=(8.82-0.100)0-δT=8.72 0-0.090mm
查得26.9mm 的∆=0.520 δT=δA=0.130 X∆=0.260 尺寸转换
26.900.52得: D A=(26.9-0.26)0-δT=26.630+0.130mm
D T=(26.63-0.100)0+δA=26.53 0-0.130
查得 2.9mm 的∆=0.250 δT=δA=0.060 X∆=0.130 尺寸转换
2.90-0.250得: D A=(2.9-0.130)0+δA=2.770+0.060mm
D T=(2.77-0.100) 0-δT=2.67 0-0.060mm
查得R62.5mm的∆=0.74 δT=+0.008 δA=-0.006 X∆=0.130 尺寸转换R62.50-0.740得: D A=(62.5-)0+δA=62.770+0.060mm
D T=(2.77-0.100) 0-δT=62.67 0-0.060mm
5.卸料弹簧的设计
根据模具安装位置先4个弹簧,每个弹簧的预压力为F预=F X/n(N) (n-为弹簧的个数,这里n取4。
)弹簧在F0作用下的预压缩量
∆H 0F 0/F 2∆H 2,
根据上面对各工序的卸料力的计算,取其中最大的那个F X 进行弹簧预压力的计算。
得:F 预=(5359/4)N =1340N 因需要的负荷较大,而安装位置受到限制,不易采用普通弹簧。
因而可采用弹力大的强力弹簧h 预=
Fj
hj
F 预 四、 模具的总体设计
1. 模具类型的选择
由冲压工艺分析可知,采用级进冲压,所以选择的模具类型为冲孔—翻边—落料级进模。
2. 因为该模具使用的是条料,所以导料采用导料板,送进步距采用导正销控制。
3. 卸料、出件方式的选择
因工件料厚为1mm ,相对较薄模具采用弹性卸料,采用弹性元件为弹簧,它与卸料杆配合使用实现卸料的过程。
4. 导向方式的选择
为了提高模具的寿命和工件质量,方便安装调整,该级进模采用中间导柱的导向方式。
5.φ
2.5的冲孔凸模强度的钢度校核
由于φ
2.5冲孔凸模与材料厚度相近,故要验证其钢度,则 小凸模d 的纵向总压力p ,
p=p1+q1
冲裁力p=lt σ 推件力Q=NKP=1.3 lt σK
根椐公式:
P∑
F≥
A
即πdd/4≥σπdt(1+nk)/ []σ
d≥4σπt(1+nk) / []σ
=4x420x3.14x1x(1+5x0.055)/1350
≈6.7mm
所以强度符合要求。
翻边的计算:
查表可得该材料的最小拉深系数k=0.5
所以由公式d=kD
=7.1X0.5
≈3.5mm
故可以一次成形。
五、主要零件的结构设计
工件采用的是级进冲裁,考虑到模具的价格较贵和更换的方便,凹模做成组合式。
由于工件上孔较多且大小不一致,其中还有一些是小孔,因而在设计凸模的结构时考虑到其强度和钢性我们将凸模做成阶梯式的,且尺寸较大的凸模在长度方向上要大于小尺寸凸模一个t的值。
(这样,各凸模冲裁力的最大峰值不同时出现从而达到降低冲裁力的目的。
)
1.凸模长度方向的尺寸计算
凸模的长度L=h1+h2+t+h (L—凸模长度,h1凸模固定板厚度,h2卸料
板厚度,h增加长度,t—材料厚度。
)
2.模架及其他零部件的选用
垫板尺寸 L⨯B⨯H=250mm⨯200mm⨯8mm
导柱d/mm⨯L/mm=φ32⨯190
导套d/mm⨯L/mm⨯D/mm=φ32⨯105⨯45
该模具的闭合高度:
H闭=H上模+H垫+L+H+H下模-h2=(50+8+45+25+50-3)mm=165.5mm, 六、模具总装图
通过以上设计分析,可得到模具总装图。
模具上模主要由上模板、垫板、凸模固定板及卸料板等组成。
卸料方式采用弹性卸料,以弹簧作为弹性元件。
下模部分主要由下模座、凹模板、导料板等组成。
条料送进时采用导正销进行定距,,从而保证了送料的精度。