精铸硅溶胶型壳工艺的改进
硅溶胶型壳常见缺陷及防止措施
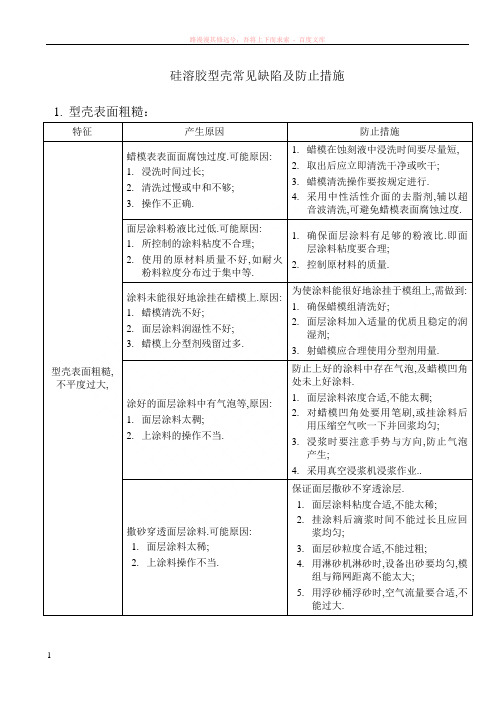
硅溶胶型壳常见缺陷及防止措施1.型壳表面粗糙:特征产生原因防止措施型壳表面粗糙,不平度过大, 蜡模表表面面腐蚀过度.可能原因:1.浸洗时间过长;2.清洗过慢或中和不够;3.操作不正确.1.蜡模在蚀刻液中浸洗时间要尽量短,2.取出后应立即清洗干净或吹干;3.蜡模清洗操作要按规定进行.4.采用中性活性介面的去脂剂,辅以超音波清洗,可避免蜡模表面腐蚀过度. 面层涂料粉液比过低.可能原因:1.所控制的涂料粘度不合理;2.使用的原材料质量不好,如耐火粉料粒度分布过于集中等.1.确保面层涂料有足够的粉液比.即面层涂料粘度要合理;2.控制原材料的质量.涂料未能很好地涂挂在蜡模上.原因:1.蜡模清洗不好;2.面层涂料润湿性不好;3.蜡模上分型剂残留过多.为使涂料能很好地涂挂于模组上,需做到:1.确保蜡模组清洗好;2.面层涂料加入适量的优质且稳定的润湿剂;3.射蜡模应合理使用分型剂用量.涂好的面层涂料中有气泡等,原因:1.面层涂料太稠;2.上涂料的操作不当.防止上好的涂料中存在气泡,及蜡模凹角处未上好涂料.1.面层涂料浓度合适,不能太稠;2.对蜡模凹角处要用笔刷,或挂涂料后用压缩空气吹一下并回浆均匀;3.浸浆时要注意手势与方向,防止气泡产生;4.采用真空浸浆机浸浆作业..撒砂穿透面层涂料.可能原因:1.面层涂料太稀;2.上涂料操作不当.保证面层撒砂不穿透涂层.1.面层涂料粘度合适,不能太稀;2.挂涂料后滴浆时间不能过长且应回浆均匀;3.面层砂粒度合适,不能过粗;4.用淋砂机淋砂时,设备出砂要均匀,模组与筛网距离不能太大;5.用浮砂桶浮砂时,空气流量要合适,不能过大.2.型壳面层裂纹:特征产生原因防止措施型壳表面层出现不规则的裂纹,或出现极细小的龟状裂纹这些裂纹是型壳干燥时产生的,主要是由于面层干燥过快,或涂料干燥收缩过大引起的,或由于蜡模热膨胀使面层型壳被胀裂.及型模焙烧不当引起.具体产生原因:1.环境相对湿度太低2.面层干燥时间过长3.空气流动不均匀而且过大4.环境温度变化过大5.壳模焙烧不当.1.面层干燥区相对湿度宜在RH60~70%之间.2.面层干燥时间以4~6h为宜,特殊产品不要超过10h.3.风不要正对模组吹,应降低直接吹到模组上的气流量.4.制壳间温度应严格控制,保持在22~25℃之间.5.脱蜡后壳模应在至少4h后装炉焙烧.尽量避免高温-低温-高温焙烧及二次焙烧.3.型壳面层鼓裂:特征产生原因防止措施型壳面层局部与蜡模分开向外鼓起(图a),或鼓起后破裂导致背层涂料流到蜡模和面层之间,但未将空隙填满(图b、图c)., 1.面层型壳与蜡模间附着力太差1.确保蜡模清洗好.2.面层涂料润湿剂加入量合适.2.面层型壳外表面干燥过度、内表面干燥不足.1.控制好环境相对湿度、面层干燥时间和风速,确保面层型壳外、内表面干燥合适.2.应使面层涂料厚合适,不要过厚.3.面层型壳湿强度不足,特别是在蜡模锐角处其强度低1.保证面层型壳湿强度.为此,要保证硅溶胶和耐火材料的质量,按工艺规范保持涂料正确配方,配制方法及确保涂料性能合格.2.要保证蜡模锐角处有一定厚度的涂料,且涂料不要滴得过干.4.制壳间温度不均匀保持制壳间温湿度均匀.4.型壳内孔搭桥:特征产生原因防止措施内孔、凹槽处的型壳不致密,局部有未上好涂料,未撒上砂使该处型壳存在孔隙搭桥. 1.第一层或背层涂料太稠.2.孔洞或狭缝处浸浆不足.3.撒砂过粗,以致孔洞或狭缝处很快就被塞住.4.孔洞或狭缝处松散砂粒在浸下层浆时未被清除掉.5.内孔或凹槽处型壳干燥不足.1.控制好第二层和背层涂料粘度.2.细致地上孔洞或狭缝处的涂料.3.撒砂使用较细的砂,防止孔洞或狭缝处过早被塞住.4.注意将孔洞或狭缝处松散的浮砂吹除,再上下层涂料.5.注意内孔或凹槽处型壳干燥情况,不干时不能制作下层模壳.5.型壳面层剥落:特征产生原因防止措施型壳型腔尺寸变大,表面不光洁. 面浆与蜡型的附着力太差1.改善蜡模蚀刻清洗,利用溶剂轻微腐蚀蜡模表面以增强其与浆层的吸附力.2.破坏宽大之平面,在宽广平面上加上若干凸出物或筋,减少平面宽广程度,以利浆附着.3.在型蜡中添加一些亲水性物质,改善蜡的亲水性,也可有效增强面浆与蜡型的吸附力.面层在制下层型壳过程中剥落,这是由于面层还没有干燥就制第二层型壳,硅溶胶发生回溶现象,使面层型壳剥落.控制好环境相对湿度、温度、风速和干燥时间,确保面层干燥后再做第二层.面层干燥过快或过度增加面层干燥区的的湿度,一般为RH60~70%,但在特殊有深穴如盒状铸件内部不易干燥的状况,甚至相对湿度设定为70~80%.减少空气的流速,避免内外速率相差太大,外部本就较易干燥,若再加风吹,则外部已干燥过度,而内部尚未干燥,因此减少空气流动,对拉动内外干燥一致有较大助益.相对湿度愈高,风速愈小,则室内的干湿球温差愈小,如此,可避免壳型在干燥初期,因为快速干燥蒸发水汽,温度急降而使蜡型收缩,待干燥后,蜡型又因吸收室内温度而而升温膨胀,如此缩胀,轻则龟裂,重则剥落.温度变化不均确保除湿间的绝热性与温度的均衡性.型壳脱蜡时面层剥落.原因是面层和第二层型壳间结合力太差而赞成的.1.面层太太厚.2.第二层涂料粘度太大,难于渗入面层.3.面层撒砂太细,一二层很难形成牢固的镶嵌结构.4.撒砂中粉尘量及含水量过大,造成分层.5.面层撒砂过慢等引起撒砂未能嵌入涂层内部.而是浮贴在涂层上,或根本未撒上砂子形成涂料与涂料接触,产生分层.6.上第二层涂料前未去除面层型壳上松散的浮砂.7.未使用预湿剂,导致个别地方涂挂不良. 1.面层太厚的原因导之于面浆过浓,粘砂时,耐火材料仅在浆的表面而无法深入浆层,失去键销阻绝大面收缩的效果,使浆层干燥后产生微裂,因此,可适当降低浆液的浓度.2.第二层涂料粘度不能太大.3.砂粒不应太细,以形成粗糙的背面,使一二层镶嵌紧密.4.控制砂的质量,将粉尘含量列入管制标准.撒砂中粉尘含量与水的含量均应低于0.5%.5.滴回浆不可过干,撒砂不应过慢.6.在制第二层型壳前以柔和风吹去表面松散砂粒.7.制第二层型壳前,把模组浸入硅溶胶预湿剂中(不超过2S),取出甩干或滴干(表面无明显滴落胶液),再上第二层涂料.焙烧时型壳面层剥落,则是由于两涂层间热胀系数不同而造成的. 尽量使面层和二层的材料热膨胀系数相近.6.型壳强度低:特征产生原因防止措施型壳强度不足1.硅溶胶质量差,如胶体粒径过大,胶体结构不不致密,杂质多等.1.选用质量好而稳定的硅溶胶,同时强化进料检验.2.硅溶胶中SiO2含量低. 2.确保硅溶中SiO2质量分数.3.耐火材料质量差,如耐火材料矿物组成不符合要求,杂质量含高等.3.保证耐火材料质量好而稳定.4.涂料质量不好,如涂料配比不合理,配料时未按照规范进行.4.严格控制涂料配比和配制工艺,保证涂料质量.5.制服壳同操作不当,发涂料上得不匀,涂层过薄;撒砂粒度不合适等等.5.严格按照制壳工艺规范进行制壳作业.6.型壳干燥不透,这常是硅溶胶型壳强度不高.的主要原因.6.控制好制壳间的温度、湿度、风速和干燥时间,确保型壳干透.7未上预湿剂,或上预湿剂不当.预湿剂起强化型壳的作用,是防止型壳分层的重要措施. 7.按型壳大小等正确规定上预湿剂的规范.8.型壳层数不够. 8.应根据铸件大小等,正确选择型壳层数.7.型壳裂纹:特征产生原因防止措施型壳开裂,浇出的铸件有一规则的毛刺、飞边. 1.脱蜡时蜡模膨胀大于型壳膨胀,而型壳湿强度又低,使型壳开裂.1.脱蜡前型壳应存放在恒温的制壳间,脱蜡时运到脱蜡处.立刻装车入脱蜡釜脱蜡,不允许型壳过长时间放在脱蜡间中.2.脱蜡蒸汽压力上升要快,14S内必须升到0.6kg.3.组树方案正确,以保证蜡易流出.4.型壳应有足够的透气性,对有的铸件应设透气孔.5.采取各种措施保证型壳强度(见本表型壳强度低缺陷的防止措施).6.防止组树时蜡模间距离太近,使型壳不易干燥,造成型壳强度低.7.铸件上平面大时,应设法增加型壳强度.8.气泡、毛刺:特征产生原因防止措施壳模制作不紧实,浇铸后因钢水穿透而形成毛刺. 浆的浓度太高浆的浓度太高时,流动性自然较差,浆液无法进入蜡型的死角位置仍被空气占据,为一气泡形态,解决方法:先用含有湿润剂预浸液(硅溶胶溶液或较稀的浆液)预浸蜡树,使死角处的空气被预浸液挤排除去,浸浆时,浆液将顺着预浸液进入死角而避免了气泡的产生.不正确的浸浆作业当浸浆时,预湿液已经干燥或流失,则死角地区仍被空气占据,失去预浸功能,因此,应训练作业人员的回浆作业手法,在浸浆之前,应用回浆手法使预湿液能均匀的占据蜡型(或壳型)的每一个角落.挤除空气并预湿表面.浆内气泡太多配制浆料后,必须要经过4h以上的浸润浆料及排除气泡,湿润剂在过度的搅拌下也会产生气泡,故需对搅拌速度进行适当设定.虽然一切均无问题,浆液中仍会因混入空气而有小气泡,故在浆液中要加入少量的消泡剂辅助去除气泡.浆的浓度太低当浆的浓度太低时,面层浆自然会太薄,且粉料太少会使面层有许多的小孔隙,而且因面层太薄,后面耐火砂堆集的孔隙,对浆层无支撑力,当铸造时,金属会穿入这些孔隙中形成痱子状的尖刺(毛刺),此时,应在沾浆作业时多沾一次浓度较高的浆液,并回浆均匀后再沾耐火砂.耐火砂粒度太粗面层用的耐火砂过粗时,粒间空隙太大,对面层而言无支撑力,会使金属液穿刺而形成痱子,故可选用较细的耐火砂做面浆的支撑.9.未润湿:特征产生原因防止措施蜡模组表面挂浆性不佳,个别位置出现露出蜡面或涂挂层太薄,可见蜡色过多的离型剂(脱模剂)训练射蜡作业员正确的离型剂喷涂方法.清洗不确实用溶剂清洗时,可能溶剂效能已降低,浸洗时间没有相应延长,致清洗不完全.若用中性介面活性剂的去脂剂清洗时,同样亦会因使用一段时间后,效能降低.故在此状况下,均以延长浸洗时间来解决,倘仍不能解决,则只能更换清洗剂.面浆内的湿润剂不够不同厂牌的湿润剂,效果不同,其用量亦不相同,应各自试用恰当的用量,不可过多,否则会产生过多的气泡.另外醇基湿润剂会挥发,故隔一段时间后应继续追加.10.壳模破裂:特征形成原因防止措施壳模局部位置表面出现一定深度的裂痕,严重者则为自内而外穿透性裂缝. 脱蜡前陶壳破裂浸浆室及干燥区的温度不稳定,造成蜡型热胀,使陶壳胀裂。
对熔模铸造现行制壳工艺

对熔模铸造现行制壳工艺的改进和讨论黄炳荣1,景宗梁2(1. 无锡鹰普精密铸造有限公司,江苏无锡 214028;2. 郑州大禹化工产品有限公司,江苏无锡 214035)摘要:中温模料硅溶胶制壳工艺是目前国内、国外的主流工艺,用于生产精密铸件。
然而,面临制壳生产周期长、因面层型壳缺陷导致铸件缺陷的困扰。
提出面层浆料加入防裂剂、面层大风力干燥、面层采用大粒径硅溶胶、取消涂二层前预湿、取消涂面层前沾硅溶胶的工艺举措,从而提高面层型壳的强度,减少面层型壳的缺陷,缩短涂层干燥时间,提高铸件一次性合格率。
关键词:防裂剂;干燥时间;预湿;胶粒径•The current system of investment casting shell process of thinking and discussHUANG Bing-rong1, JING Zong-liang2(1. Wuxi Impro Precision Casting Co., Ltd., Wuxi 214028, Jiangsu,China; 2. Zhengzhou Dayu Chemical Products Co., Ltd., Wuxi 214035,Jiangsu, China)Abstract:WenMo silicon sol material in the shell is the current domestic and foreign technology process for the production of the mainstream, precision castings. However, faced with the shell long production period, because the surface defects casting mold shell to defect problems. Put forward the surface crack size to join agent, facing big wind dry, facing the large particle size silicon sol, cancel besmear before the second floor surface coating, prewettingcancelled before the process with silicon sol measures, so as toimprove the strength of the road surface mold shell, reduce thesurface defects, shorten the mold shell coating drying time, improve casting one-time qualified.Key words:Guards against the crack agent; Drying time; The wet;Glue size熔模铸造中温蜡全硅溶胶结壳工艺适合生产表面粗糙度值小、尺寸精度高的精密件,已经成为主流工艺被广泛应用。
熔模铸造型壳强度与硬化工艺改进(李海树)

熔模铸造型壳强度与硬化工艺改进(李海树)制造型壳是熔模铸造工艺中的一个关键工序,它不仅决定着铸件的尺寸精度和表面粗糙度,而且直接影响铸件的制造成本和生产效率。
多年的实践证明,由于型壳残留强度大,给铸件清砂与碱煮工序带来困难,我厂每年碱煮工序消耗蒸气4 688.6 t(费用达25.79万元),烧碱26.8 t(费用达9.28万元),制壳工序消耗结晶氯化铝162.14 t(费用达42.16万元),占用了大量的生产资金。
因此,对影响型壳强度性能的结晶氯化铝硬化工艺进行了改进,应用氯化铵与结晶氯化铝混合硬化工艺,并取得较好的经济效果。
1型壳强度与硬化剂的关系分析从制壳、浇注到清理的不同工艺阶段,型壳有三种不同的强度指标,即常温强度、高温强度和残留强度。
三种强度之间有一定的关系,但形成机制和影响因素不完全相同。
例如:若常温强度不足,在制壳过程中易掉件,在脱蜡过程中易变形或破裂;若高温强度不足,在焙烧和浇注过程中会发生型壳变形和跑火(漏钢);若残留强度过高,直接影响型壳的脱壳性和铸件清砂的难易程度。
如何调整型壳三种强度间的关系,使其具有高的常温强度、足够的高温强度和尽可能低的残留强度是我们所希望的。
根据制壳工艺的现状,在粘结剂和耐火材料不变的情况下,对常用硬化剂的分析与改进十分必要。
1.1氯化铵硬化剂的特点分析氯化铵作为水玻璃型壳的硬化剂,其硬化反应式如下:2NH4Cl+Na2O.mSiO2.nH2O→mSiO2.(n-1)H2O+2NaCl+2NH3↑+2H2O反应结果生成的SiO2胶体将型壳中的石英粉和砂粒牢固地粘结在一起,使型壳获得强度。
氯化铵是应用最早的水玻璃型壳硬化剂,其主要优点是扩散硬化速度快,制壳周期短,型壳残留强度低,脱壳性好。
同结晶氯化铝硬化剂相比,型壳高温强度差,存放期间容易生茸毛,硬化反应时析出氨气污染空气,劳动条件差,设备腐蚀比较严重。
1.2结晶氯化铝硬化剂的特点分析结晶氯化铝作为水玻璃型壳的硬化剂,在硬化过程中,氯化铝与水玻璃是相互中和、相互促进水解的过程;在此过程中,水玻璃的p H值下降、稳定性降低而析出硅凝胶。
精密铸造4种制壳工艺特点分析及改进方向探讨
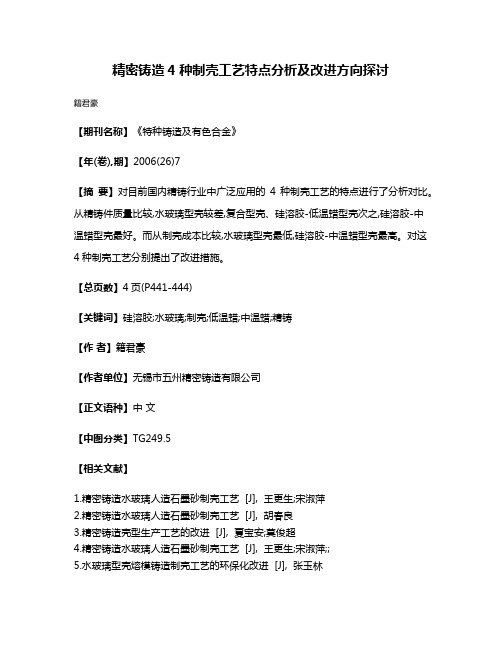
精密铸造4种制壳工艺特点分析及改进方向探讨
籍君豪
【期刊名称】《特种铸造及有色合金》
【年(卷),期】2006(26)7
【摘要】对目前国内精铸行业中广泛应用的4种制壳工艺的特点进行了分析对比。
从精铸件质量比较,水玻璃型壳较差,复合型壳、硅溶胶-低温蜡型壳次之,硅溶胶-中温蜡型壳最好。
而从制壳成本比较,水玻璃型壳最低,硅溶胶-中温蜡型壳最高。
对这4种制壳工艺分别提出了改进措施。
【总页数】4页(P441-444)
【关键词】硅溶胶;水玻璃;制壳;低温蜡;中温蜡;精铸
【作者】籍君豪
【作者单位】无锡市五州精密铸造有限公司
【正文语种】中文
【中图分类】TG249.5
【相关文献】
1.精密铸造水玻璃人造石墨砂制壳工艺 [J], 王更生;宋淑萍
2.精密铸造水玻璃人造石墨砂制壳工艺 [J], 胡春良
3.精密铸造壳型生产工艺的改进 [J], 夏宝安;莫俊超
4.精密铸造水玻璃人造石墨砂制壳工艺 [J], 王更生;宋淑萍;;
5.水玻璃型壳熔模铸造制壳工艺的环保化改进 [J], 张玉林
因版权原因,仅展示原文概要,查看原文内容请购买。
熔模铸造制壳工序的几点体会
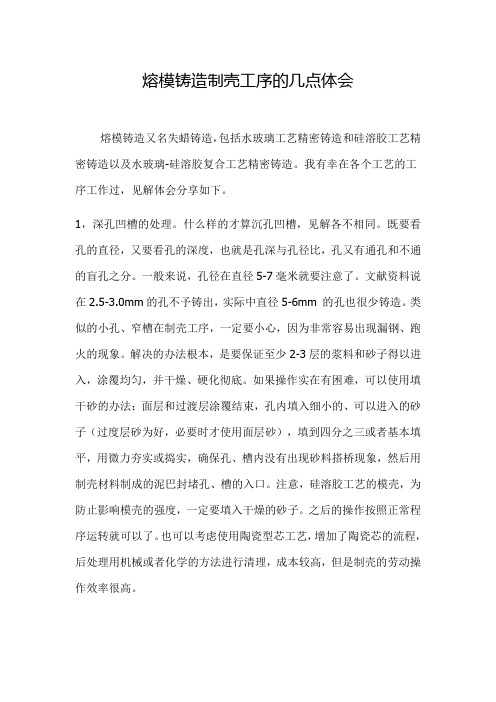
熔模铸造制壳工序的几点体会熔模铸造又名失蜡铸造,包括水玻璃工艺精密铸造和硅溶胶工艺精密铸造以及水玻璃-硅溶胶复合工艺精密铸造。
我有幸在各个工艺的工序工作过,见解体会分享如下。
1,深孔凹槽的处理。
什么样的才算沉孔凹槽,见解各不相同。
既要看孔的直径,又要看孔的深度,也就是孔深与孔径比,孔又有通孔和不通的盲孔之分。
一般来说,孔径在直径5-7毫米就要注意了。
文献资料说在2.5-3.0mm的孔不予铸出,实际中直径5-6mm 的孔也很少铸造。
类似的小孔、窄槽在制壳工序,一定要小心,因为非常容易出现漏钢、跑火的现象。
解决的办法根本,是要保证至少2-3层的浆料和砂子得以进入,涂覆均匀,并干燥、硬化彻底。
如果操作实在有困难,可以使用填干砂的办法:面层和过渡层涂覆结束,孔内填入细小的、可以进入的砂子(过度层砂为好,必要时才使用面层砂),填到四分之三或者基本填平,用微力夯实或捣实,确保孔、槽内没有出现砂料搭桥现象,然后用制壳材料制成的泥巴封堵孔、槽的入口。
注意,硅溶胶工艺的模壳,为防止影响模壳的强度,一定要填入干燥的砂子。
之后的操作按照正常程序运转就可以了。
也可以考虑使用陶瓷型芯工艺,增加了陶瓷芯的流程,后处理用机械或者化学的方法进行清理,成本较高,但是制壳的劳动操作效率很高。
2,孔、槽产品的水玻璃精密铸造的硬化。
水玻璃精密铸造采用液体硬化,靠水玻璃中的硅酸钠和水玻璃中的二氧化硅的化学反应进行硬化,所以确保硬化液体浸入到所有和浆料接触,需要硬化的部位,以便和水玻璃发生化学反应是保证硬化效果的关键,孔、槽部位也不例外。
特别注意的是,盲孔、深的凹槽,在浸入硬化液体时,一般来说会有气泡冒出,要注意观察并确保气体能全部排出来,使硬化液能彻底进入孔、洞、操的深处。
如果孔、槽的角度和组树方式所限,气体不能自缢而出,要改变模组入池的角度,或者其他方法,总之要想方设法使空气溢出的目的。
3,孔、槽产品硅溶胶工艺的风干。
硅溶胶工艺的硬化是干燥硬化,和空气中的水分含量、空间温度高低有直接关系,还由于制壳间属于恒温恒湿的必备条件,所以空气的流动性成为关键因素。
精铸硅溶胶型壳工艺的改进电子教案

5.由表十一,十二及十三实验结果得出以下结论:
⑴.在表面层涂料中加入少量“分散剂”能改变硅溶胶涂料的流变特性,增
加涂料的屈服值从而可提高涂挂性和覆盖性(涂层平均厚度)3可提高15-25%。同时由于
“分散剂”作用能使粉料“分散”不易“结团”。使平均粒径减小因而3增加。虽然粉液比
n略有下降,但致密性k%仍在要求范围之内(表七)。涂料的均匀性,悬浮性,涂挂性和流 平性均有提高。“板结”“老化”时间延长(稳定性提高)。
1.美国在2006年前面层涂料的典型工艺是在锆英粉中掺加5-10%(质量)的熔融石英粉。
其主要目的是:降低成本,提高铸件尺寸精度和改善脱壳性、透气性。国外重点工艺改进方 向是:充分利用熔融石英纯度高,杂质少,密度和热膨胀系数小,加上高温“析晶”,低温
“相变”的特点,使型壳在高温时保持高强度而在低温时因相变产生剧烈收缩(-3.7%)致
精铸硅溶胶型壳工艺的改进
前言:
众所周知,全球精铸界通用的硅溶胶型壳工艺存在三大缺点:
1.成本高。2.制壳周期长。3.铸件脱壳性差(型壳残留强度高)。
据统计,表面层型壳通用的耐火料锆英石砂、粉占型壳原辅材料成本的48%占总生产成本
的10%(平均值)[1]。优质锆英石资源稀缺,因而寻找它的代用品或减少其消耗量是当今 国内外精铸界共同关心,重点研究的课题之一。
2.混合涂料用粉料粒度要求应符合表五规定。
注:1•采用GSL-101BI型“激光颗粒度测定仪” 测定(丹东市辽宁仪器仪表研究所生产)
2.粒度判定以DV90, DV50及Wo三项指标为主要依据。DV98 DV84为参考指标。
3.无粒度检测条件时,可将待测粉料与“标准”硅溶胶配制成“标准”涂料来判定
硅溶胶在熔模精密铸造中的应用

粘结 ,且在室温配制涂料时又不会引起料浆胶凝 。常
使用粒径为 0. 075 mm 左右的氧化铝 、氧化锆 、莫来
石 、铝矿石及石英玻璃粉 ,为了改善涂料的浸涂性 ,往
往还要加入悬浮剂 、矿化剂 、渗透剂 、流平剂等辅助材
料 。稀释剂常用去离子水或酒精 。粉料的加入必须是 边加入边搅拌 ,防止局部粉料过多吸水导致硅溶胶胶 凝 。选定配方后 ,涂料的性能由其粘度和密度来决定 。 表 2 列出铸造镍基高温合金定向凝固铸件用壳型涂料 的典型配方及其性能 。
随着涂料浸渍使用 ,其性能必然发生变化 。水分 蒸发减少 ,粘度提高 ,故需按计算量补加少许硅溶胶和 去离子水 ,以保证原涂料 SiO2 含量及粘度 。冬季使用 硅溶胶粘结剂时 ,如果室内温度过低 ,配制涂料时粘度 会偏高 ,易产生气泡而影响型壳品质 。
表 2 定向凝固壳型涂料的典型配方及性能[3 ] Tab. 2 Typical component and properties of shell casting for di2
我国从 60 年代起开始生产和使用硅溶胶 ,近年来 用于熔模铸造的国产硅溶胶 ,品质日趋稳定并逐步向 国际商业品类靠拢 。北京航空材料学院从60年代末
收稿日期 :2001206220 ; 修订日期 :2001207218 作者简介 :肖 克 (19622 ) ,北京人 ,工程师 ,工学学士 1
作为熔模铸造壳型粘结剂的硅溶胶的性能指标包 括 SiO2 含量 、密度 、稳定剂的含量 、p H 值 、SiO2 粒径 。 表 1 列出熔模铸造行业常用的硅溶胶及其性能 。
表 1 熔模铸造行业常用的硅溶胶[1 、3 ] Tab. 1 Silica sol using for investment cast vocation
水玻璃精铸工艺升级方案探讨与实践

摘要:针对传统水玻璃熔模精铸高污染问题,进行了工艺升级方案探讨,确认硅溶胶薄壳工艺为最佳方案,该工艺从模料、组树、制壳和蜡回收处理方面进行优化升级,彻底消除了酸雾、钠盐的污染,同时也提升了铸件品质。
关键词:水玻璃熔模精铸污染工艺升级硅溶胶型壳中图分类号:U466文献标识码:BDOI :10.19710/ki.1003-8817.20190085水玻璃精铸工艺升级方案探讨与实践蓝勇王永华李锐(东风精密铸造有限公司制造技术研究所,十堰442714)作者简介:蓝勇(1973—),男,高级工程师,硕士学位,研究方向为熔模铸造新材料与新工艺。
1前言熔模铸造是一种近净成形工艺,比较适合于中小型复杂精铸件的生产。
按涂料粘结剂的类型分,熔模铸造可分为水玻璃型壳、硅溶胶型壳和硅酸乙酯型壳等3种主要工艺,其中前2种是目前国内精铸企业广泛采用的主流工艺。
水玻璃粘结剂熔模铸造(简称水玻璃精铸)工艺在我国工业化应用已经有近60多年的历史[1],期间虽然在制壳材料、硬化剂及过程工艺控制方面进行了大量改进和创新,但其高污染的问题一直没有得到根本性解决。
水玻璃精铸工艺环保性差主要体现在以下方面。
a.主体模料以石蜡、硬脂酸为主,使用过程容易发生皂化反应,回收通常采用盐酸进行处理,氯化氢酸雾污染严重;模料耐热性差、强度较低导致制壳过程掉件率高,废弃模壳排放量大。
b.制壳过程的化学硬化产生大量的钠盐和氯化氢酸雾污染,用氯化铵硬化还额外增加氨气污染。
用氯化镁代替氯化铝或氯化铵作硬化剂,环保性并没有得到改善,硬化过程同样产生钠盐,焙烧过程中残留的氯化镁会分解出高腐蚀性的氯化氢气体。
c.型壳中氧化钠含量高,高温强度低,通过增加厚度保证总体强度导致制壳耐火材料消耗量大、焙烧能耗高。
d.脱蜡时采用氯化铵或盐酸补充硬化,存在氨气或氯化氢酸雾污染。
e.当前氯化铵硬化水玻璃型壳工艺已经被国家列为落后工艺,盐酸在很多地方也被禁止使用,随着环保压力的增加,传统水玻璃型壳工艺的转型或升级势在必行。
- 1、下载文档前请自行甄别文档内容的完整性,平台不提供额外的编辑、内容补充、找答案等附加服务。
- 2、"仅部分预览"的文档,不可在线预览部分如存在完整性等问题,可反馈申请退款(可完整预览的文档不适用该条件!)。
- 3、如文档侵犯您的权益,请联系客服反馈,我们会尽快为您处理(人工客服工作时间:9:00-18:30)。
精铸硅溶胶型壳工艺的改进一. 前言:众所周知,全球精铸界通用的硅溶胶型壳工艺存在三大缺点:1.成本高。
2.制壳周期长。
3.铸件脱壳性差(型壳残留强度高)。
据统计,表面层型壳通用的耐火料锆英石砂、粉占型壳原辅材料成本的48%,占总生产成本的10%(平均值)[1] 。
优质锆英石资源稀缺,因而寻找它的代用品或减少其消耗量是当今国内外精铸界共同关心,重点研究的课题之一。
“快干”硅溶胶的推广应用和真空干燥设备的逐步完善,缓解了制壳周期长的缺点。
由于硅溶胶型壳高温强度高(是水玻璃型壳的6.7倍),其相应的残留强度也高(是水玻璃型壳的2.8倍),因而铸件的脱壳性能比水玻璃差得多。
加之大部分生产的精铸件是结构复杂的中小件,型壳残留强度高会严重影响后处理工序生产效率和增加材料工时成本、降低铸件表面质量,延误交货期。
我们通过学习国内外同行的先进经验,经过多年的努力研究和实践,在降低硅溶胶型壳生产成本和改善脱壳性方面取得了一定成效,特向精铸界同仁作一介绍,以期达到抛砖引玉的目的。
二. 表面层制壳工艺的改进:〈一〉. 锆英石粉料的代用—长期以来锆英石是全球精铸业首选的型壳表面层耐火料。
正如2007年美国精铸学会(I CI)第54届年会论文所言:“锆英石与多种合金反应低、密度高、热化学性能好,要寻找替代用品是困难的”。
[2]1. 美国在2006年前面层涂料的典型工艺是在锆英粉中掺加5-10%(质量)的熔融石英粉。
其主要目的是:降低成本,提高铸件尺寸精度和改善脱壳性、透气性。
国外重点工艺改进方向是:充分利用熔融石英纯度高,杂质少,密度和热膨胀系数小,加上高温“析晶”,低温“相变”的特点,使型壳在高温时保持高强度而在低温时因相变产生剧烈收缩(-3.7%)致使型壳残留强度大大降低,从而使铸件脱壳性、透气性、尺寸精度提高。
自2007年起,通过技术改进美国已有80%的精铸企业表面层涂料中的熔融石英粉掺入量已提高至50%(按体积比为68.7%)。
其中更有20%工厂其石英掺入量高达75%(按体积比86.8%,锆粉仅占14.2%)[3]2. 我们根据分析和试验证实其工艺改进的关键技术要点有两方面:a.通过采用高致密度即优良级配的粉料提高了表面层涂料的工艺性能。
其中主要是“覆盖性”(涂层平均厚度δ)和致密性(粉液比n或粉料在涂料中的体积浓度k%)两项。
以往进口原包装澳大利亚锆粉配制的涂料其粉液比多为:n=3.2-3.7(ηΦ4=40±5s)而近年来已提高到n=3.9-4.6。
国内加工的锆粉则仍大部分为n=2.5-3.7。
b.在表面层涂料中加入少量(0.1%-0.2%占硅溶胶质量)“分散剂”。
它可在不影响涂料其他工艺性能前提下提高了涂料平均厚度(δ)15-25%(表三)。
同时还能改善涂料的均匀性,悬浮性。
使涂挂性和均匀性很差的熔融石英在锆英粉—硅溶胶涂料中掺入量有原5-10%提高到50%-75%。
试验和生产实践充分证明了上述结论。
从表一、二、三、四试验结果得出下列结论:1. 要提高混合涂料(锆英粉—熔融石英粉硅溶胶涂料)中熔融石英的掺入量,应采用较高致密度(n=3.9-4.6)的锆英粉(表一)及熔融石英粉(n=1.5)。
这两种粉料配制的混合涂料(锆粉70%+熔融石英粉30%)其致密性n=2.5-3.0(k=44-48.5%),ηΦ4=40±5(s),δ=0.08-0.09(表七),才能满足生产工艺要求。
2. 混合涂料用粉料粒度要求应符合表五规定。
注:1.采用GSL-101BI型“激光颗粒度测定仪”测定(丹东市辽宁仪器仪表研究所生产)。
2.粒度判定以DV90,DV50及Wo%三项指标为主要依据。
DV98,DV84为参考指标。
3.无粒度检测条件时,可将待测粉料与“标准”硅溶胶配制成“标准”涂料来判定粉料粒度大小及组成是否符合(表七)各项工艺性能指标规定。
3. 砂粉料(锆英石及熔融石英石)的物理化学性能要求:⑴.锆英石砂粉的物理性能应符合“中国铸造协会精密铸造分会”标准CICBA/C02.09-1999规定,但应确定砂、粉中游离铁(磁性物)含量。
即加工过程中混入的磁性物杂质(表九)。
⑵.熔融石英砂、粉,我国尚无精铸业内标准,参考国外资料结合我国生产厂具体情况暂按表八验收。
4.为改善混合涂料的工艺性能,提高熔融石英的加入量,涂料严格选用优质的粉料和合理进行两种粉料的级配外,加入适量的“添加剂”是不可缺少的措施[6] 。
实验证实:无论在锆英粉,熔融石英粉或两者配制的混合涂料中加入少量的“分散剂”能较大幅度地提高涂料的屈服值。
使涂料覆盖性(涂层平均厚度)提高,这正是国外精铸界能使锆英粉—硅溶胶涂料中熔融石英粉掺入量由原来5-10%提高到50-75%的主要原因和重要措施之一。
5.由表十一,十二及十三实验结果得出以下结论:⑴.在表面层涂料中加入少量“分散剂”能改变硅溶胶涂料的流变特性,增加涂料的屈服值从而可提高涂挂性和覆盖性(涂层平均厚度)δ可提高15-25%。
同时由于“分散剂”作用能使粉料“分散”不易“结团”。
使平均粒径减小因而δ增加。
虽然粉液比n略有下降,但致密性k%仍在要求范围之内(表七)。
涂料的均匀性,悬浮性,涂挂性和流平性均有提高。
“板结”“老化”时间延长(稳定性提高)。
⑵.由表十三可见:混合涂料中熔融石英粉掺入量可由原30%提高到50%,主要是通过“分散剂”加入后得到的效果。
⑶.“分散剂”的作用原理是:高分子长链会形成网状结构使涂料中细粉质点不易按触合并成大颗粒。
使粉料在涂料中分布更分散和均匀。
细粉(0.2-10μm)含量增加δ增厚提高了硅溶胶涂料的屈服值,不仅提高了涂料工艺性能,而且对稳定和提高铸件(型壳)表面质量和增加型壳透气性有利。
粉液比适当减小,涂料成本也能降低,但应控制在合格范围内(表七)。
<二>.表面层涂料加“锆砂”工艺[5]为了提高面层型壳(涂料)的致密性。
我们在表面层涂料中外加入10%的锆英砂(1 00/200目)(占锆粉质量)。
其效果是由于“砂粒”的掺入,提高了面层型壳干燥时抗拉强度,硅溶胶在失水、干燥收缩时可防止面层型壳产生裂纹。
这对于大平面或外表面积较大和铸件结构复杂、内外壁干燥速度差别大的铸件特别有效。
长江厂生产的“容积器”壁厚5m m,净重15kg,内腔深200mm。
过去表面层型壳须自干12小时以上,往往外表面已出现裂纹,铸件60-80%出现“飞翅”或“流纹”(线性缺陷)。
在表面层涂料中加砂后,多批生产260件,无一出现这类缺陷。
混合涂料中不宜加入密度太小的熔融石英砂,否则会在搅拌机底部及四周沉积。
而加入密度大的锆砂无此现象。
全锆粉或混合硅溶胶涂料加锆砂后均能改善涂料工艺性能,提高其致密性、流动性、流平性和均匀性。
减少了由涂料在复杂型腔内堆积而造成的“铁豆”,穿钢等缺陷。
尤其可降低型壳开裂的风险,其作用犹如在大平面水泥路上掺入砂、石,可防止水泥浆在失水干燥收缩时开裂的原理一样。
实践证实,细砂在涂料中加入量未影响铸件表面粗糙度。
当然,砂粒的粒度不宜过粗,以常用的100/200目或140/270目为宜(粒径d=0.075-0.10mm为最佳)不宜超过涂料层厚度。
目前这一工艺已为多家硅溶胶型壳和水玻璃型壳精铸应用。
效果良好。
综上实验及一年生产实践关于表面层涂料(不论是全锆粉或混合涂料)中加入锆英砂10%这一工艺措施,其主要特点如下:1.涂料加砂后除涂料致密性k%提高了4%左右,而其他工艺性能均未改变,但涂料的流平性,均匀性得到提高,表面层型壳强度(抗裂性)有所提高,硅溶胶在失水胶凝后的收缩应得以分散使表面层型壳开裂倾向降低,这对于大平面件,尤其是复杂型腔内外干燥不均匀的铸件最有价值,可大大减少表面产生飞翅(披锋)或“流纹”缺陷。
2.型壳表面致密性的提高,铸件表面质量相应提高,致密而光洁,使外观缺陷减少。
3.这一工艺同样适合于水玻璃型壳。
适合于涂料工艺性能较差的混合涂料。
(锆粉—熔融石英粉)硅溶胶,或白刚玉—硅溶胶涂料)。
<三>.锆英砂的代用——生产中表面层撒砂料消耗量和成本略高于粉料。
美国精铸业虽然大部分用熔融石英粉取代了锆英粉,但95%的工厂仍采用锆英石撒砂料。
只有少量企业用熔融石英粉或雷马斯砂(相当于我国的烧结铝矾土)国内精铸厂已有许多工厂已在上产中批量投产试用优质的电熔白刚玉砂,完全取代了锆英砂。
实践证明,只要选用纯度高、杂质少、游离铁(Fe O%)及含量低的精铸用电熔白刚玉撒砂料。
不会造成型壳残留强度高,铸件脱壳性恶化的问题。
表面层型壳、撒砂料只有密度高才能顺利进入复杂型腔、小孔、窄孔内固定涂层。
因而生产复杂件,目前只有刚玉砂可以替代锆砂。
较低密度的高岭石和熔融石英均难以应用(碳钢件,简单件例外)。
撒砂料的粒度应符合表十四规定(参照CICA标准)测定,商品代号为80/120目的精铸用砂,实际大多为100/200目。
撒砂粒度过粗易造成型壳“蚁孔”,铸件产生“毛刺”缺陷。
过细则会造成表面层型壳“分层”或“裂纹”。
铸件表面生成“流纹”或“飞翅”缺陷。
故其粒径应在d=0.08-0.15mm为宜,即100/200目(表十四)。
其含粉量<0.2%(过300目即d<0.045mm)表面层撒砂的粒径分布的要求是:相对集中,适度分散<四>.目前我们厂精铸件表面层型壳生产工艺为:1.表面层制壳工艺—①.涂料配比:锆英粉70%+熔融石英粉30%,外加10%锆英砂(占锆粉质量)(300-400目) (200-270目)②.撒砂:100%电熔白刚玉(100/200目)(郑州三星白刚玉厂)2.锆英砂物化性能:按CICBA/C02-09-1999,粒度按表五或表七验收。
FeO则应符合表九规定。
涂料中加锆砂粒度按表十四。
3.表面层型壳用电熔白刚玉砂的物化性能同锆英石可查标准。
4.目前我们正在小批试用涂料中加“分散剂”,尽早采用锆粉50%+熔融石英粉50%的表面层混合涂料,力争早日达到国外先进工艺水平。
5.据统计,表面层涂料熔融石英粉掺入量30%,撒砂100%改用电熔白刚玉砂,工艺改进后,型壳材料成本每月可降低2.3万元,年节约达27万元。
三.背层制壳材料的选用及工艺改进:(一)砂粉料合理选用:硅溶胶型壳三大缺点之一是型壳残留强度过高,铸件脱壳性差。
不仅与表面层或过渡层有关,还常和背层型壳耐火材料的合理选择关系密切。
背层型壳耐火砂、粉料虽在其单价成本比面层低得多(只有锆英石的1/10以下),但因层数多,每吨合格铸件约须消耗1.2吨耐火料,因而其在生产成本中也占相当大的比例,国内不少精铸企业在背层耐火料的选用上常将价格因素放在第一位,选购“价廉、质次”的砂粉料,其后果往往是铸件返修率、报废率和型壳破损、漏钢率增加,后处理成本大幅增高,铸件生产综合成本往往高过耐火料差价,结果是得不偿失。