硅溶胶失蜡精密铸造
失蜡法铸造工艺流程

失蜡法铸造工艺流程失蜡法铸造,又称蜡失法铸造,是一种常用的精密铸造工艺,其工艺流程主要包括模具制作、蜡模注塑、蜡模组装、砂型制作、烧蜡、熔炼、浇注、冷却、脱蜡、清理等环节。
下面将详细介绍失蜡法铸造工艺的具体流程。
首先,模具制作是失蜡法铸造的第一步。
模具的设计和制作直接影响到最终铸件的质量和形状,因此需要精心设计和制作。
通常采用硅胶模具或金属模具,根据铸件的形状和尺寸来选择合适的模具材料和制作工艺。
接下来是蜡模注塑。
在模具制作完成后,需要将熔化的蜡注入模具中,冷却后取出蜡模。
蜡模的成型质量直接关系到后续工艺的顺利进行,因此在注塑过程中需要严格控制温度和压力,确保蜡模的成型质量。
蜡模组装是将蜡模组合成完整的铸件模型,通常需要将多个蜡模组合在一起,形成完整的铸件模型。
在组装过程中需要注意蜡模之间的连接和定位,确保组装后的模型符合设计要求。
随后是砂型制作。
将蜡模组装好后,需要在其表面涂覆一层特制的砂浆,形成一层砂壳。
砂型的质量和结构对最终铸件的质量和表面光洁度有着重要影响,因此需要在砂型制作过程中严格控制涂覆厚度和砂浆的配比。
烧蜡是将蜡模中的蜡烧掉,使模型内部留下空腔。
通常采用加热或蒸发的方式,将蜡模中的蜡完全烧掉,留下空腔用于浇注金属。
接下来是熔炼和浇注。
将金属材料熔化后,通过浇注的方式将熔融金属注入到砂型中,填充蜡模留下的空腔。
在熔炼和浇注过程中需要控制好温度和浇注速度,确保金属充分填充砂型,避免产生气孔和缺陷。
冷却是指待浇注的金属在砂型中冷却凝固。
冷却速度和方式对铸件的组织结构和性能有着重要影响,因此需要在冷却过程中控制好冷却速度和温度,确保铸件的质量。
脱蜡是指在金属冷却后,将砂型中残留的蜡烧掉,以便取出成品铸件。
脱蜡过程需要控制好温度和时间,确保砂型中的蜡完全烧掉,不留任何残留物。
最后是清理。
在脱蜡后,需要清理砂型表面和铸件表面的残留物,通常采用喷砂或化学清洗的方式进行清理,以确保铸件的表面光洁度和质量。
硅溶胶精密铸造的工艺

硅溶胶精密铸造的工艺一、蜡模制作蜡料处理工艺操作守则蜡料处理流程:(静置桶I中)静置脱水→(除水桶中)搅拌蒸发脱水→(静置桶II中)静置去污1 工艺参数静置桶I静置温度85-90℃静置时间6-8h除水桶搅拌温度110-120℃搅拌时间10-12h静置桶II 静置温度80-85℃静置时间>12h保温箱保温温度54±2℃保温时间>24h2 操作程序2.1 检查设备、温控仪表是否处于正常工作状态。
2.2 将脱蜡釜回收的旧蜡液倒入过滤槽中过滤;再送到静置桶I中,在低于90℃下静置6-8h。
2.3 静置完毕把沉淀水放掉后,将蜡液倒入除水桶中。
2.4 除水桶中的蜡液,在110-120℃保温并搅拌,使残留水分蒸发,到目视蜡液表面无泡沫为止。
2.5 将除完水的蜡液,经过<60目筛网过滤再放入<90℃的静置桶II中,保温静置12h 以上。
2.6 各除水桶、静置桶应定期性的放掉其底部的残留水和脏杂物。
2.7 把静置桶II中处理好的回收蜡液送到模头压蜡机保温桶中,用于主产模头(浇道)。
2.8 根据旧腊料性能和腊料消耗情况,不定期的在静置桶II中适量加新蜡,一般在3%-5%左右。
2.9 将合格的蜡液灌入保温箱内的蜡缸中,为减少蜡缸内蜡液中的气体,先保持一段高温时期80℃/2h后降至54℃。
在54±2℃下保温24h后,方可用于压制蜡模。
3 注意事项3.1除水桶,静置桶均应及时排水、排污。
3.2经常检查各设备温控仪表的工作状况,防止失控,尤其应防止温度过高造成蜡料老化。
3.3每月检查一次蜡处理设备各导热油的液面位置,油面应距设备顶面200㎜左右,防止油溢出。
并注意检查设备有无渗油现象。
3.4经常检查环境状态,避免灰尘及外来物混入蜡料中。
压制蜡模工艺操作守则1 工艺要求室温24±3℃蜡缸温度54±2℃(大件应根据工艺要求设定)射蜡嘴温度57-64℃压射压力 4.2Mpa(42kgf/cm2)保压时间5-15s冷却水温度<10℃2 操作规程2.1 检查压蜡机油压、保温温度、操作按钮等是否正常。
硅溶胶精密铸造工艺.doc

硅溶胶精密铸造工艺焦作市恒辉精密制造有限公司企业标准特种合金熔模铸造工艺规程QQ/HH C4.1-20131适用范围1.1本规程适用于特种合金硅溶胶熔模铸造。
1.2其他合金硅溶胶熔模铸造可参照执行。
2特殊合金熔模铸造工艺流程图3控制要求3.1特殊合金熔模铸造生产过程的成型、组合、制壳、脱蜡、熔化和浇注、清洗、热处理和精修复,应制定各过程的通用工艺规程。
检验包括在检验规范中。
熔炼和浇注被确认为特殊过程。
3.2对于每个铸件,需要一个工艺规范。
3.3铸件的整个生产过程应严格按照工艺规程和工艺规程的要求进行。
根据工艺规程的要求,实施过程控制,并做好过程的原始记录。
焦作市恒辉精密制造有限公司企业标准特种合金熔模铸造工艺代码蜡模生产QQ/HH C4.2-1.2其他合金硅溶胶熔模铸造可参照执行。
2特殊合金熔模铸造工艺流程图3控制要求3.1特殊合金熔模铸造生产过程的成型、组合、制壳、脱蜡、熔化和浇注、清洗、热处理和精修复,应制定各过程的通用工艺规程。
检验包括在检验规范中。
熔炼和浇注被确认为特殊过程。
3.2对于每个铸件,需要一个工艺规范。
3.3铸件的整个生产过程应严格按照工艺规程和工艺规程的要求进行。
根据工艺规程的要求,实施过程控制,并做好过程的原始记录。
焦作市恒辉精密制造有限公司,企业标准特殊合金熔模铸造工艺代码蜡模制作QQ/Hhhc4.2:(在蒸馏桶内)蒸馏脱水→(在移除桶内)搅拌蒸发脱水→(在蒸馏桶内)蒸馏去污1.2工艺参数a .蒸馏桶蒸馏温度85-90°c .蒸馏时间6-8小时c .移除桶搅拌温度110-120°c .搅拌时间10-12小时e .蒸馏桶蒸馏温度80-85°c .蒸馏时间> 12小时g 1.3.2将脱蜡釜回收的旧蜡液倒入过滤罐中过滤;然后送入静置桶中,将脱蜡釜回收的旧蜡液倒入过滤罐中过滤至85-1 . 3 . 2;然后送至立筒中细化晶粒,消除魏氏组织,铸造应力低于85%。
精密铸造常识及详解

6.铸件后清理
将清理好的铸件按照客户的包装要求进行包装
入库即可
Copy Right By ZYC
11
What Shall We Talk…? 主要内容
Copy Right By ZYC
28
4
铸件尺寸影响因素分析
熔化收缩(焙烧和凝固)
1、模壳的焙烧温度和时间 2、浇注温度 3、浇注速度 4、补浇冒口操作 5、合金成分 6、浇后冷却方式 7、出壳到浇注结束的时间 8、合金的净化处理质量 9、环境温度
Copy Right By ZYC 29
5
铸件冶金质量影响因素分析
Copy Right By ZYC 17
3绍
3 三种蜡料系统和三种粘结剂系统介
三种蜡料系统
1、低温蜡料 以蜡基模料为主。熔点小于70度,主 要用于小件和尺寸及表面要求不高的零 件,膏状压制,能回用。与水玻璃粘结 剂多一起使用。用热水直接脱蜡。
Copy Right By ZYC
18
3绍
3 三种蜡料系统和三种粘结剂系统介
脱除。脱出的蜡料经回收处理后可重复使用。
Copy Right By ZYC
8
4.焙烧
为了进一步去除型壳中的水分、残蜡及其它杂
质,在金属浇注之前,必须将型壳送入加热炉内加热
到950℃左右进行焙烧2h左右。通过焙烧,型壳强度
增高,型腔更为干净。
Copy Right By ZYC
9
5.浇铸
为提高合金的充型能力,防止浇不足和冷隔缺
硅溶胶精密铸造工艺流程
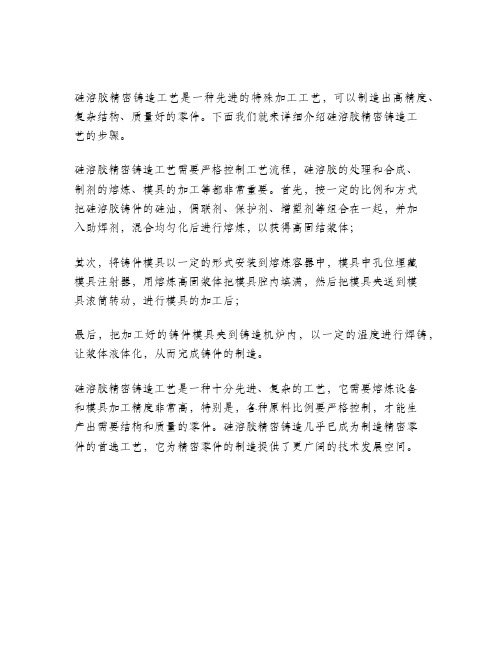
硅溶胶精密铸造工艺是一种先进的特殊加工工艺,可以制造出高精度、复杂结构、质量好的零件。
下面我们就来详细介绍硅溶胶精密铸造工
艺的步骤。
硅溶胶精密铸造工艺需要严格控制工艺流程,硅溶胶的处理和合成、
制剂的熔炼、模具的加工等都非常重要。
首先,按一定的比例和方式
把硅溶胶铸件的硅油,偶联剂、保护剂、增塑剂等组合在一起,并加
入助焊剂,混合均匀化后进行熔炼,以获得高固结浆体;
其次,将铸件模具以一定的形式安装到熔炼容器中,模具中孔位埋藏
模具注射器,用熔炼高固浆体把模具腔内填满,然后把模具夹送到模
具滚筒转动,进行模具的加工后;
最后,把加工好的铸件模具夹到铸造机炉内,以一定的温度进行焊铸,让浆体液体化,从而完成铸件的制造。
硅溶胶精密铸造工艺是一种十分先进、复杂的工艺,它需要熔炼设备
和模具加工精度非常高,特别是,各种原料比例要严格控制,才能生
产出需要结构和质量的零件。
硅溶胶精密铸造几乎已成为制造精密零
件的首选工艺,它为精密零件的制造提供了更广阔的技术发展空间。
硅溶胶精密铸造

未知驱动探索,专注成就专业
硅溶胶精密铸造
硅溶胶精密铸造是一种利用硅溶胶作为模具材料进行铸造
的加工方法。
硅溶胶具有高温稳定性、高精度、高强度和
化学稳定性等优点,可以制作出精密复杂的铸造件。
硅溶胶精密铸造的工艺流程包括模具制作、溶胶浸涂、回
填砂料、烘烤固化、脱模和烧结等步骤。
首先根据铸件的
形状和尺寸,制作相应形状的硅溶胶模具。
然后将模具浸
入硅溶胶浆料中,使模具表面均匀涂覆一层硅溶胶,形成
模具壳体。
接着将硅溶胶模具填充砂料,使铸件的轮廓形成。
随后,将模具放入烘烤室中进行固化处理,使硅溶胶
完全烘干和固化。
固化后,进行脱模处理,得到铸件。
最
后将铸件放入高温炉中进行烧结,使其成为坚固的陶瓷材料。
硅溶胶精密铸造具有制造成本低、生产周期短、尺寸精度高、表面质量好等优点。
它广泛应用于航空、航天、冶金、军工等领域,制造精密复杂的零件和工艺件。
1。
硅溶胶在精密铸造中的运用
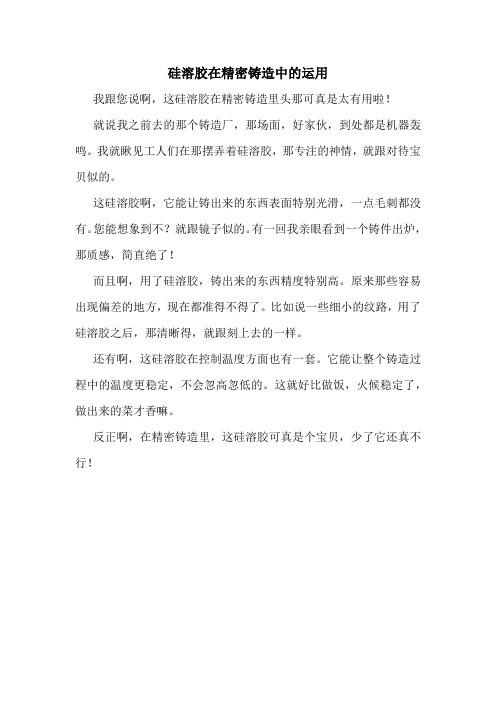
硅溶胶在精密铸造中的运用
我跟您说啊,这硅溶胶在精密铸造里头那可真是太有用啦!
就说我之前去的那个铸造厂,那场面,好家伙,到处都是机器轰鸣。
我就瞅见工人们在那摆弄着硅溶胶,那专注的神情,就跟对待宝贝似的。
这硅溶胶啊,它能让铸出来的东西表面特别光滑,一点毛刺都没有。
您能想象到不?就跟镜子似的。
有一回我亲眼看到一个铸件出炉,那质感,简直绝了!
而且啊,用了硅溶胶,铸出来的东西精度特别高。
原来那些容易出现偏差的地方,现在都准得不得了。
比如说一些细小的纹路,用了硅溶胶之后,那清晰得,就跟刻上去的一样。
还有啊,这硅溶胶在控制温度方面也有一套。
它能让整个铸造过程中的温度更稳定,不会忽高忽低的。
这就好比做饭,火候稳定了,做出来的菜才香嘛。
反正啊,在精密铸造里,这硅溶胶可真是个宝贝,少了它还真不行!。
硅溶胶精密铸造基本工艺流程
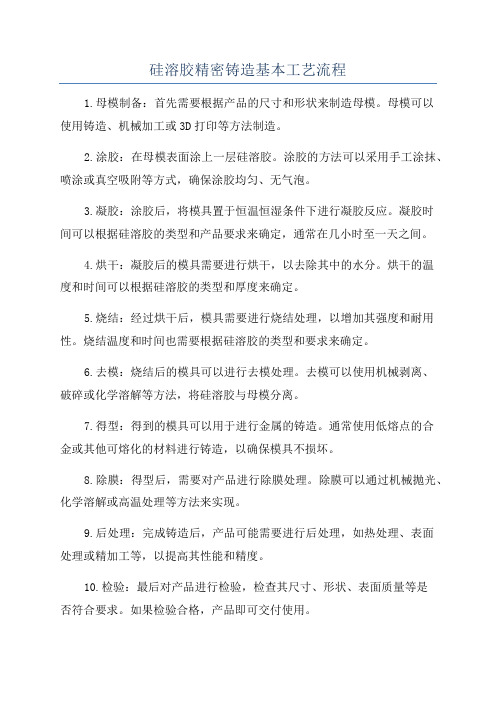
硅溶胶精密铸造基本工艺流程
1.母模制备:首先需要根据产品的尺寸和形状来制造母模。
母模可以
使用铸造、机械加工或3D打印等方法制造。
2.涂胶:在母模表面涂上一层硅溶胶。
涂胶的方法可以采用手工涂抹、喷涂或真空吸附等方式,确保涂胶均匀、无气泡。
3.凝胶:涂胶后,将模具置于恒温恒湿条件下进行凝胶反应。
凝胶时
间可以根据硅溶胶的类型和产品要求来确定,通常在几小时至一天之间。
4.烘干:凝胶后的模具需要进行烘干,以去除其中的水分。
烘干的温
度和时间可以根据硅溶胶的类型和厚度来确定。
5.烧结:经过烘干后,模具需要进行烧结处理,以增加其强度和耐用性。
烧结温度和时间也需要根据硅溶胶的类型和要求来确定。
6.去模:烧结后的模具可以进行去模处理。
去模可以使用机械剥离、
破碎或化学溶解等方法,将硅溶胶与母模分离。
7.得型:得到的模具可以用于进行金属的铸造。
通常使用低熔点的合
金或其他可熔化的材料进行铸造,以确保模具不损坏。
8.除膜:得型后,需要对产品进行除膜处理。
除膜可以通过机械抛光、化学溶解或高温处理等方法来实现。
9.后处理:完成铸造后,产品可能需要进行后处理,如热处理、表面
处理或精加工等,以提高其性能和精度。
10.检验:最后对产品进行检验,检查其尺寸、形状、表面质量等是
否符合要求。
如果检验合格,产品即可交付使用。
以上就是硅溶胶精密铸造的基本工艺流程。
这种工艺流程能够满足各种复杂形状和高精度要求的产品的制造,已广泛应用于航空航天、汽车、电子、医疗等领域。
- 1、下载文档前请自行甄别文档内容的完整性,平台不提供额外的编辑、内容补充、找答案等附加服务。
- 2、"仅部分预览"的文档,不可在线预览部分如存在完整性等问题,可反馈申请退款(可完整预览的文档不适用该条件!)。
- 3、如文档侵犯您的权益,请联系客服反馈,我们会尽快为您处理(人工客服工作时间:9:00-18:30)。
硅溶胶失蜡精密铸造
silica sol lost wax precision casting
铸造范围:壁厚≥2mm,重量0.01kg-200kg
Casting range : thickness≥2mm , weight 0.01-200kg
铸造材质:不锈钢、低合金钢、普碳钢、耐热钢等
Casting material : stainless steel , alloy steel , carbon steel, heat resistant steel , etc.
铸造标准:GB, ISO, DIN, ASTM, AISI, BS, NF, AS, JIS
Casting standard : GB, ISO, DIN, ASTM, AISI, BS, NF, AS, JIS
加工方式:来图加工、来样加工、OEM加工等
Processing methods : according drawing , according sample, OEM , etc.
7-10天,交货期:20-60天
Tooling time : 3-10 days , sample
time : 7-10 days , delivery time :
20-60 days
Drawing/Sample Process design Tooling making Wax parts <inspecting> Shelling Cleaning <cutting> Melting and pouring<material testing> Shell roasting Lost wax
Heat treatment CNC machining <inspecting> Surface process Testing Packing ,transport
silica sol lost wax precision casting
Casting range : thickness≥2mm , weight 0.01-200kg
Casting material : stainless steel , alloy steel , carbon steel, heat resistant steel , etc.
Casting standard : GB, ISO, DIN, ASTM, AISI, BS, NF, AS, JIS
Processing methods : according drawing , according sample, OEM , etc.
Production time :Tooling time : 2-10 days , sample time : 5-10 days , delivery time : 20-60 days。